
13 minute read
TECHNOLOGY IN CONSTRUCTION
the majority of our sites in Cardiff This system uses residual heat from a shower’s wastewater to pre-heat incoming cold water, meaning less energy is used to get the shower to the required temperature
Another example is the Allume SolShare, being trialled at Brookfield Drive in Cardiff, which equally distributes the electricity generated from solar panels on an apartment block to each individual affordable tenant
Technologies already exist and it is up to the residential sector, alongside local authority partners, to harness them and ultimately benefit from their potential
Low carbon tech in action
In Cardiff, the Council has ambitions to be carbon neutral by 2030 And, as we deliver our Cardiff Living development programme to provide 1,500 new homes across the city over 10-years, we ’ re helping them to achieve this goal
The Aspect Place development, for example, has been designed and constructed using Passivhaus principles to create healthier, more thermally efficient homes that will cost residents and the planet less to heat
By carefully designing the fabric of the buildings, as well as using Mechanical Ventilation Heat Recovery (MVHR), the latest hydrogen ready combi boilers and triple glazing, the houses are effectively protected from the elements, meaning they are far better insulated than a typical UK property and less reliant on the standard heating systems which make up a large proportion of the residential sector’s emissions
At Aspen Grove, a development of 214 homes, the Council has made use of lowcarbon technologies, including electrical vehicle charging points, solar panels, lithium-ion batteries and ground source heat pumps, to achieve CO2 emissions around 90% lower than an average home and 80% lower than a new-build
Not only this, but the homes are also connected by a state-of-the-art monitoring system to help residents understand how they can reduce the amount of energy being used on an ongoing basis, such as for heating and hot water, and to take excess power from the grid At the same time, this allows them to make sure they are creating an environment that is comfortable for them and reduces fuel bills
Modern methods of construction
As an industry, we also need to pay close attention to the emissions created during the construction of a building By working with partners to manufacture houses offsite, local authorities have an opportunity to minimise the resources required at the construction site and to deliver more energy-efficient buildings by maximising the performance of the materials that make up the fabric of the building itself
Modular homes delivered for Cardiff at Crofts Street are 90% more energy-efficient than standard homes built to current Building Regulations and in recognition of their environmental credentials have achieved Grade A in Energy Efficiency and Environmental Impact (CO2) ratings Solar panels and MEV Heat Recovery with electric heating elements mean they’re not required to connect to the mains gas service and will therefore emit significantly less CO2 than a standard home
As an added bonus, modern methods of construction have allowed the Council to build and install new homes for local people in record time At Crofts Street, residents moved into their new homes within weeks of them being lowered onto the site
Tackling these challenges together
Building more homes and tackling climate change might seem at odds with each other, but both are crises we must urgently address And, by investing in new technologies be those new methods of building, renewables or smart digital tech we can make this possible Building homes can be part of the solution as we move towards net zero n More information on Wates Group here www.rdr.link/lak017 n More information on the Wates Innovation Network here www rdr link/lak018


Modern methods of construction apprenticeship programme

Technology in facilities management
New research from Watco has revealed that almost half (45%) of facilities managers think that their organisation could become unviable in the next couple of years if it doesn’t improve its digital technologies and skills The study found that 72% of facilities managers (FMs) admit that their business is slow to embrace digital innovation and 18% said that their biggest priority over the next year will be upskilling and training employees on new technologies
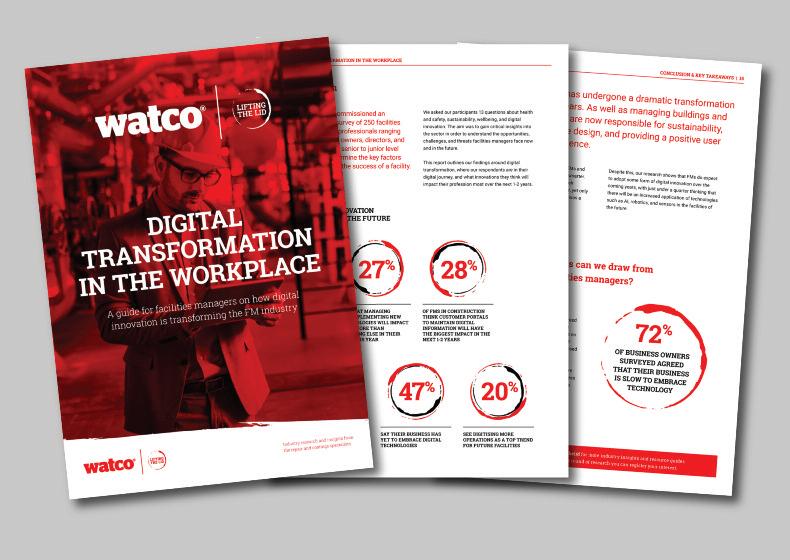
Leading UK offsite timber frame manufacturer, Donaldson Timber Systems (DTS), has partnered with West Herts College to offer an apprenticeship programme in support of the next generation of talent in the construction industry for timber frame construction The partnership originated with DTS’ appointment to the Hertfordshire OSM framework, which included the commitment to engage with the local College The 2 5-year programme was open to students on the College’s Level 2 City and Guilds carpentry course
The apprenticeship will include four days per week on-site, delivered by one of DTS’ service level agreement partners, Bedfordshire-based S E Carpentry One day per week the apprentices will attend the College to work on in-class modules, including an additional module that will focus on modern methods of construction (MMC) for timber frame that was developed in partnership with DTS This covers an understanding of construction technology; health and safety; an introduction to MMC; and understanding construction information, materials and the installation process, together with site/project communications
Simon Horn, Technical Development Manager at DTS, says: “Supporting skills development in the next generation is crucial to the ongoing evolution of the UK construction industry, and is something we ’ re committed to at DTS, so working with the College to grow and support talent was a great fit This apprenticeship programme is a pilot project for DTS and is something we would like to roll out in more areas, with more partners, in time ”
Sian Williams, Curriculum Director at West Herts College, comments: “We’re excited to partner with DTS on this programme to give our learners an opportunity to receive hands-on training and develop their understanding of Modern Methods of Construction It has been fantastic to work closely with DTS to develop MMC modules that incorporate new design and technologies that enable our learners to gain the most current and update knowledge and skills linking into a variety of curriculum courses ”
Spencer Earl, Managing Director of S E Carpentry, adds: “We’re proud to partner with DTS and West Herts College to provide two apprentices with the opportunity to learn from our team and develop their skills It’s also unquestionably a great benefit for our business, as we will have two qualified installers at the end of the programme who are trained to work on DTS’ timber frame build systems ” n More information can be found at www.rdr.link/lak019
The research also found that some innovations have already risen in popularity In fact, 33% of FMs say that they are using customer portals, and almost a quarter (21%) said that customer portals will be the digital tool that will have the most significant impact on the sector in the next 12 months This is because customer portals help to maintain a ‘golden thread’ of maintenance information, which is something that is set to become enshrined into law under the Building Safety Act, which is due to come into force in October this year
On top of this, 55% of FMs are considering introducing resource and management software in the next two years This software can help to schedule and plan maintenance activities, allocate resources more efficiently, and monitor equipment and facility performance in real time
On top of this, 55% of FMs are considering introducing resource and management software in the next two years The survey of 250 facilities management professionals revealed the five key technologies that FMs think will have the biggest impact on their role are customer portals to maintain a digital ‘golden thread’ of information; sensor technology (e g to understand; temperature & air quality metrics); robotics (e g for cleaning tasks); resource and workforce management software and Internet of Things (IoT)
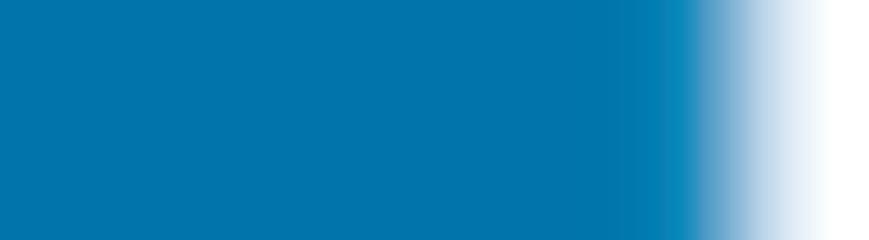
Swansea Council and the Welsh School of Architecture won the Domestic Project of the Year category at this year's CIBSE Building Performance Awards for the energy efficiency retrofit of six bungalows. The project builds on the learning from similar retrofit schemes undertaken by the school, as Juliet Rennie of CIBSE explains.
As residential energy efficiency retrofits go, the results of a collaboration between Swansea Council and Cardiff University's Welsh School of Architecture (WSA) in refurbishing a terrace of six council bungalows are impressive. The home's carbon emissions are down 94%; average annual energy consumption is only 5MWh, significantly lower than the UK average of 15MWh; and the home's Energy Performance Certificate rating has improved from a G (the worst) to an A (the best).
This is a refurbishment that demonstrates what is possible when retrofitting local authority homes for energy efficiency. Particularly when you consider that the retrofits were carried out using offthe-shelf materials and technologies.
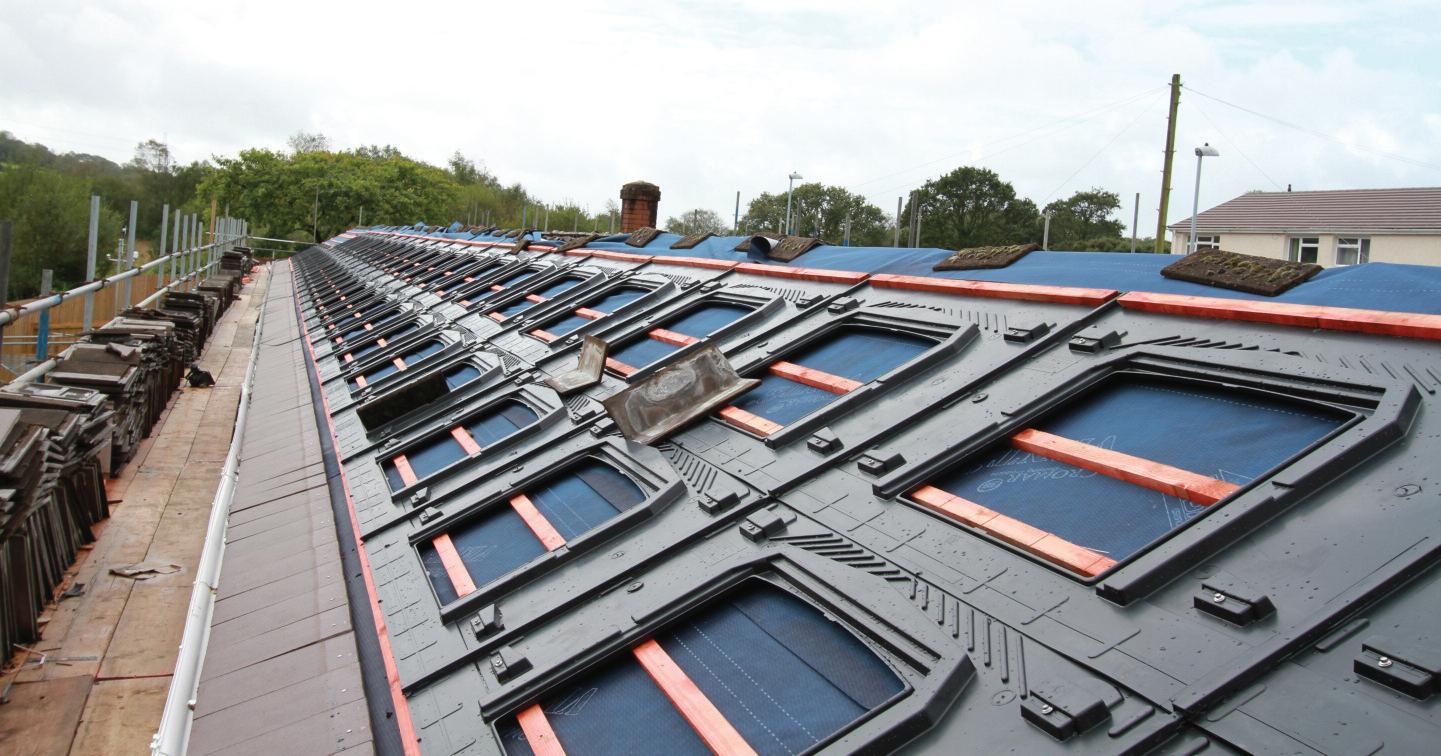
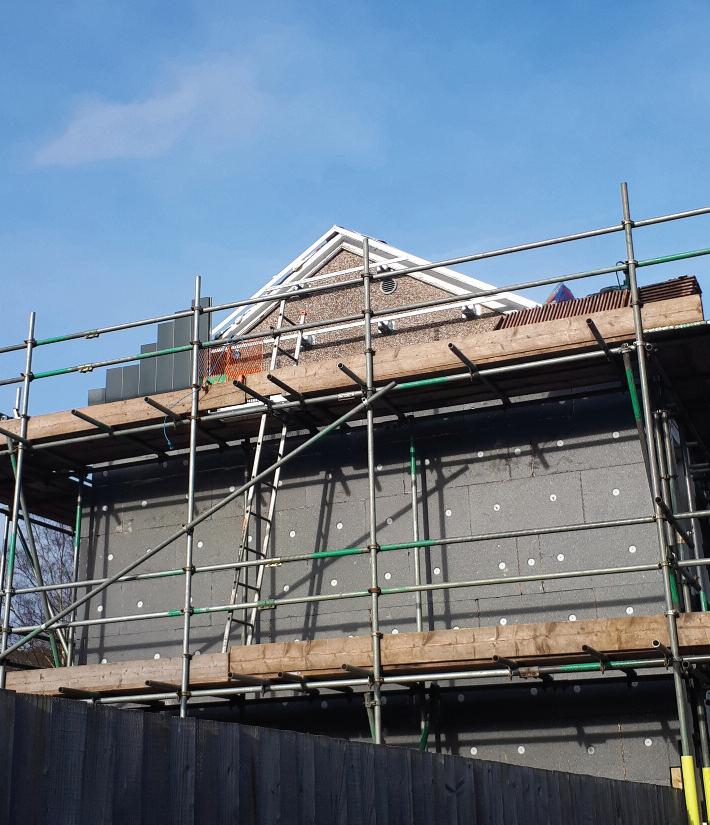
What is more, the homes tackled under this scheme were not exceptionally bad; in fact, they are described by the WSA as being "typical of many Welsh homes" in that they are off the gas grid and have been constructed with poorly insulated windows, walls, and roofs, making them expensive to heat and prone to damp and mould.
Unsurprisingly, the refurbishment won Project of the Year – Domestic, at this year's Chartered Institute of Building Services Engineers (CIBSE) Building Performance Awards. The judges were clearly impressed with the approach taken by the WSA saying it "will have far-reaching impacts in Wales and beyond".
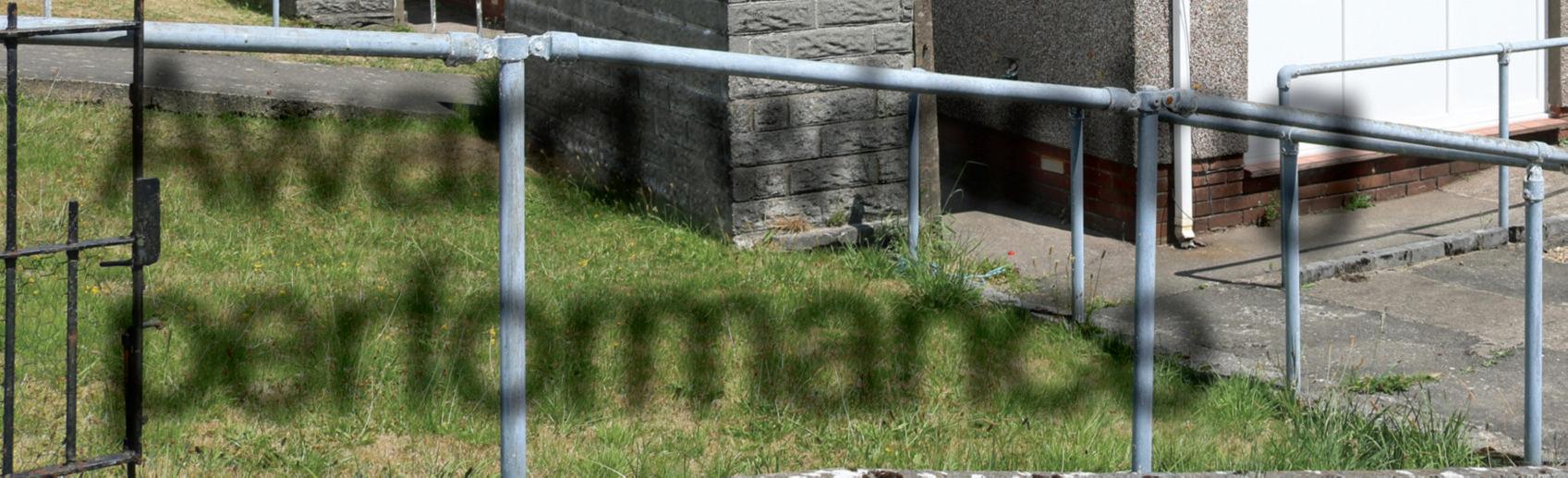
Whole house approach
The WSA's approach builds on learning from earlier residential retrofits, including work the school had undertaken in collaboration with Wales and West Housing

(another CIBSE award winning project) where it developed its integrated approach to energy efficiency improvements. This ensures retrofit decisions are based on the most appropriate interventions for each home by considering how a mix of technologies and interventions perform as an entire system.
Professor Joanne Patterson, Professorial Research Fellow at WSA, terms this "a whole house approach". She says its success depends on data-driven decisions.
“To h e l p r e s i d e n t s u s e t h e t e c h n o l o g i e s e ffe c t i ve l y, t h e
W S A p ro d u c e d a s i m p l e u s e r g u i d e a n d S wa n s e a
C o u n c i l ' s e n e rg y ma n a g e r a l s o s p e n t t i m e e x p l a i n i n g t h e o p e ra t i o n o f t h e t e c h n o l o g i e s t o r e s i d e n t s . ”
WSA's starting point for each residential retrofit is its Practical Retrofit Early Stage Survey (PRESS) This is a systematic method of collecting information developed by the school to help it understand how residents use their home and the level of comfort they expect
Data model
Crucially, PRESS is supported by a detailed study and monitoring of the building fabric This is used to identify existing performance issues; it includes airtightness testing, fabric U-value measurement, and the use of a thermal imaging camera to identify areas of excessive heat loss that may need additional treatment
Data obtained from the monitoring is used by the WSA to calibrate a digital model of the home The model allows the school to virtually test different combinations of fabric improvements and technologies to assess how these perform holistically The home's energy use, carbon emissions, and cost of energy is calculated for each combination of measures Outputs from the model enable potential energy savings to be assessed against capital costs
In determining which interventions are appropriate, the school first focuses on improvements to the building fabric through the addition of internal or external insulation to minimise heat losses before considering the most appropriate heating system Finally, the impact of adding photovoltaic panels (PVs), a mechanical ventilation system with heat recovery (MVHR) and the benefit of energy storage batteries are assessed
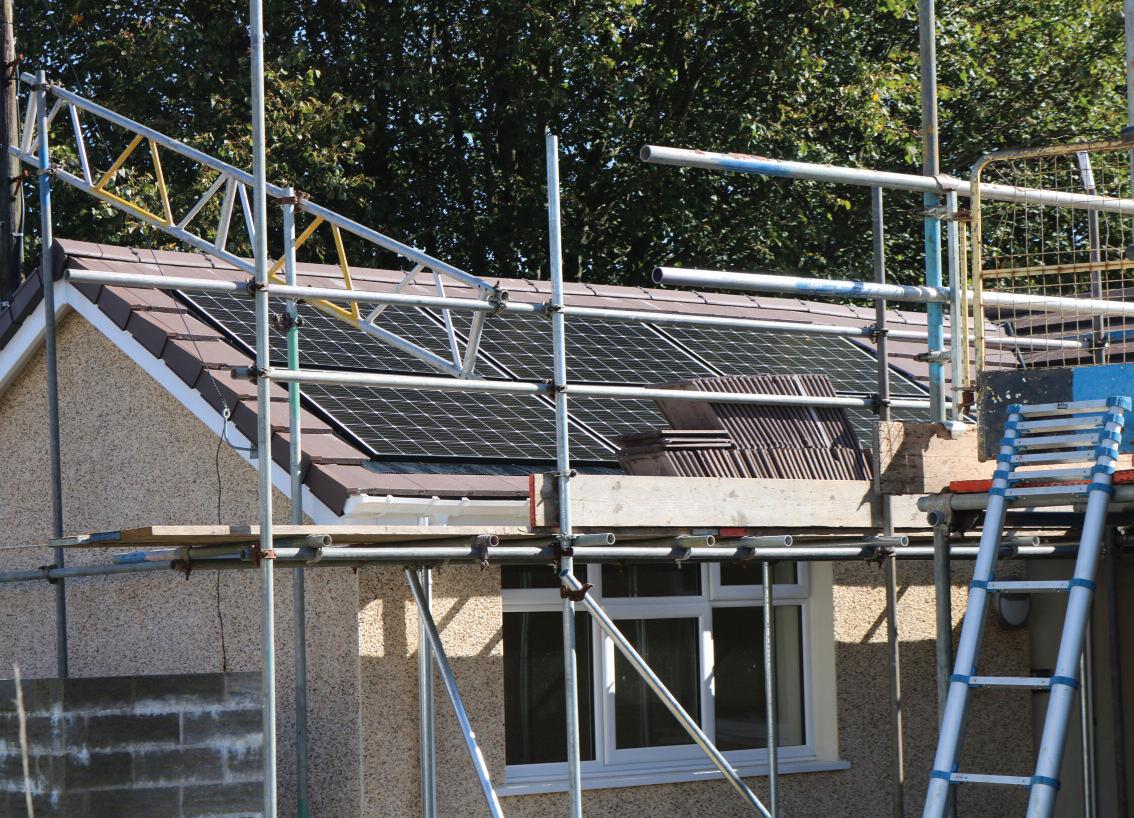
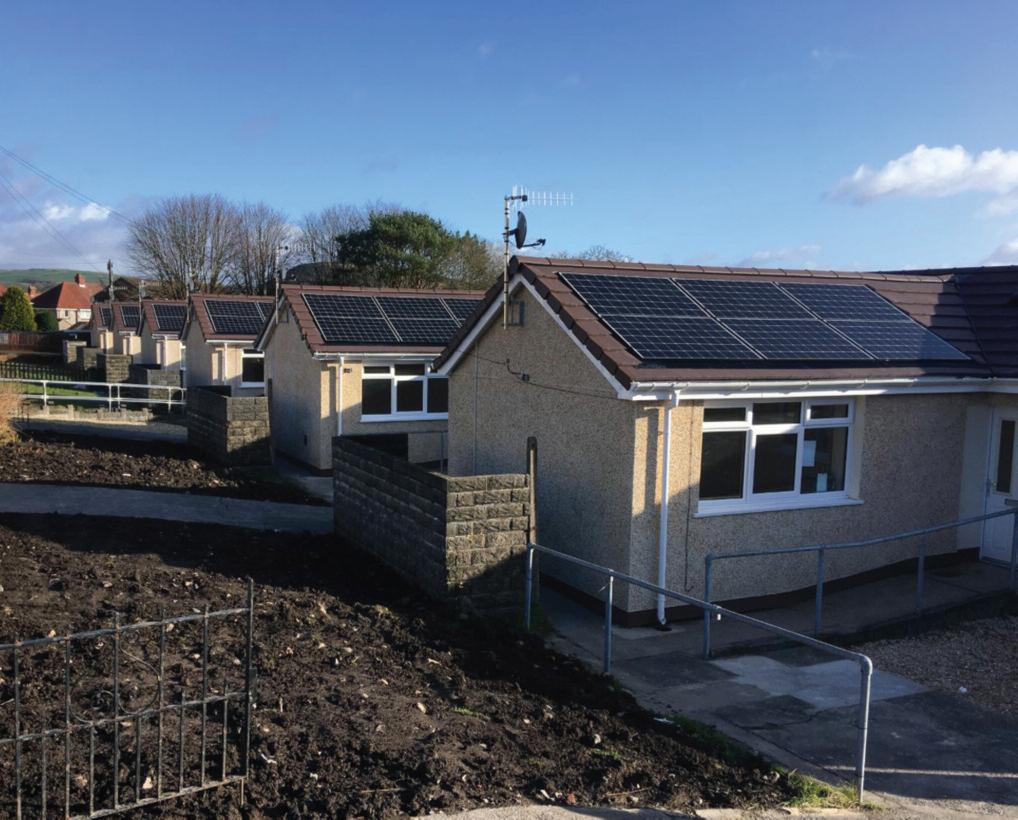
Property improvements
In Swansea, fabric energy efficiency improvements to the bungalows included external wall insulation, a reduction in the glazed area, installation of high specification double-glazed windows and the addition of loft insulation Technological additions included: a ground source heat pump (GSHP), photovoltaic panels on the roof and a large battery capable of storing surplus electricity generated by the PVs The properties were also fitted with an MVHR system to provide a constant source of energy efficient ventilation
Retrofitting this quantity of energy efficiency improvements can be very intrusive for residents So, to help minimise the impact of the works, the teams from Swansea Council and WSA decided to implement the retrofit in two phases: fabric efficiency improvements took place over one winter with the installation of the energy supply and storage technologies the following year
Post-retrofit monitoring by the WSA ensured the technologies were working as predicted, that they had been commissioned correctly and that their operation had been optimised In addition, to help residents use the technologies effectively, the WSA produced a simple user guide and Swansea Council's energy manager also spent time explaining the operation of the technologies to residents
Resident feedback
Following completion of the works, residents were interviewed for their perceptions on the impact of the retrofit Overall feedback was positive with thermal comfort in both summer and winter scoring top marks; the availability of daylight also received top marks, that despite an increase in the depth of the window reveals because of the addition of external wall insulation However, the issue of noise from the new GSHP compressor and the new MVHR system were both identified as audible, although neither was considered by residents to be intrusive
In terms of energy use, post retrofit monitoring over two years by WSA showed that from March to September (out of heating season and when days are longer) 95% of the home's energy was provided by the combination of PVs and battery, which meant that once standing charges had been excluded, resident's energy bills for the supply of electricity and heating hot water were just £3 00 per month No wonder the CIBSE awards judges were impressed n More information on the CIBSE Building Performance Awards here www.rdr.link/lak021

L o w c a r b o n c o n s t r u c t i o n w i t h s t r u c t u r a l t i m b e r
Housing associations and local author ities face numerous challenges, including the ongoing quest to help the UK achieve net zero by 2050 Here, Andrew Orr iss of the Str uctural Timber Association, explores why str uctural timber presents the greatest oppor tunity for low carbon constr uction, and how organisations are implementing it into their constr uction plans.
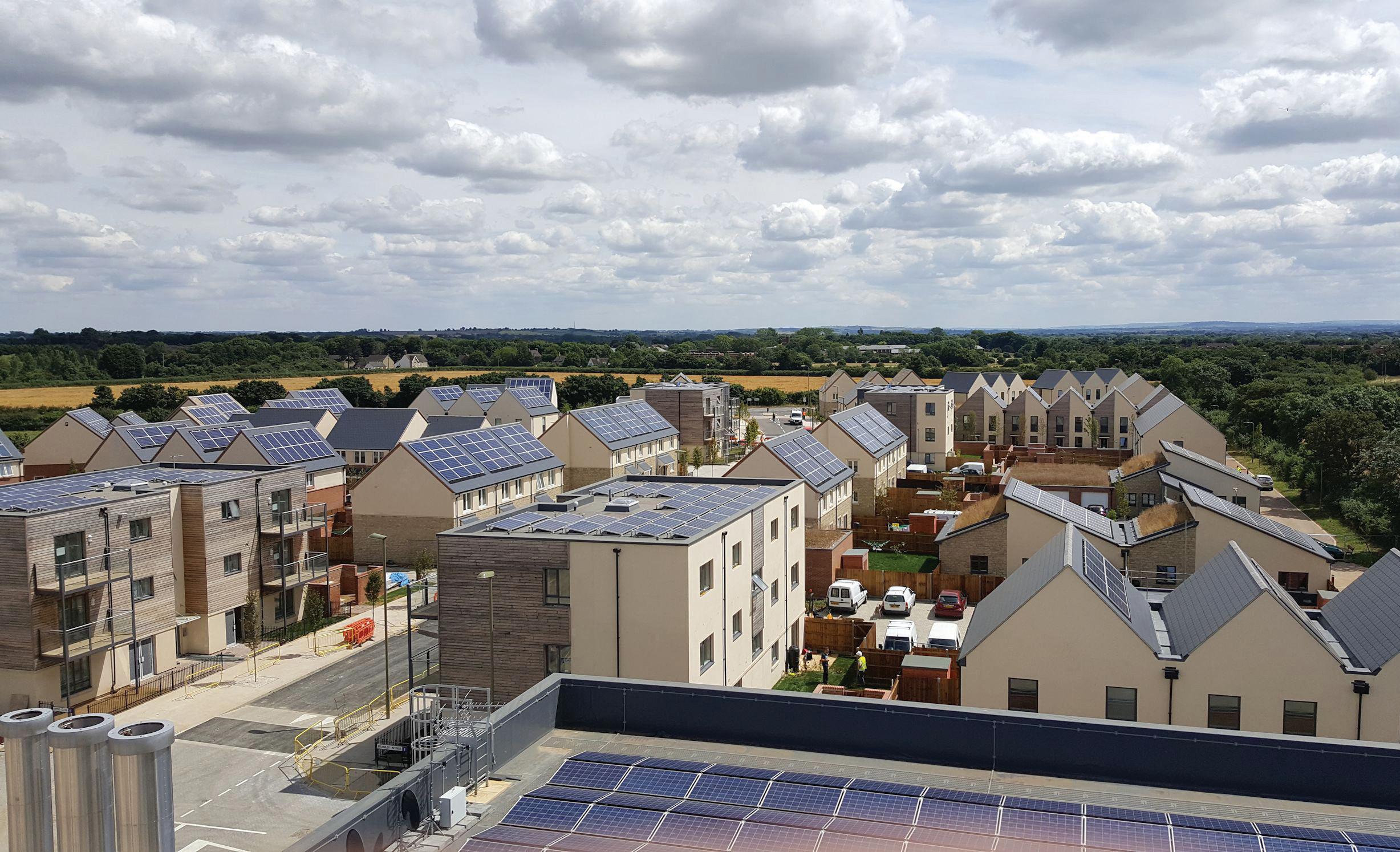
Offsite construction is considered by many as the future Timber itself is perfectly suited for offsite construction for several reasons Firstly, it is lighter than other traditional materials, making the transportation of fabricated components to site much simpler and quicker with excellent vehicle utilisation with enough panels for an entire house fitting on a single vehicle
Meanwhile, the controlled factory environment leads to minimal defects and an overall higher quality build with less waste This high precision manufacturing improves the overall airtightness of the build, which will increase the energy efficiency of the home A timber frame structure has larger capacity cavities, enabling the installation of more insulation, thus reducing heat loss and further bolstering energy efficiency Overall, offsite construction helps to alleviate tight project deadlines, overcome skills shortages and reduce the environmental impact of construction w h o l e - l i f e c o s t s a n d l o w c a r b o n f a c t o r s , w h i c h w a s o n e o f t h e r e a s o n s i n t h e i r d e c i s i o n t o c h o o s e t i m b e r f r a m e, a s w e l l a s t h e i r d e t e r m i n a t i o n t o e m b r a c e M o d e r n M e t h o d s o f C o n s t r u c t i o n ( M M C ) a n d o f f s i t e
Timber systems suit eco town policy
c o m m i t t e d t o p r o c u r e m e n t b a s e d o n
An additional consideration is how offsite manufacture can reduce the cost of construction by reducing the amount of time spent onsite through precision engineering This was demonstrated at another Donaldson Timber Systems project for Bicester Eco Town the UK’s first eco town designed to achieve high standards of environmental sustainability
Road To Zero Carbon
The A2Dominion development sought to deliver the most sustainable living in the UK for its residents, along with ensuring the homes were as affordable as possible
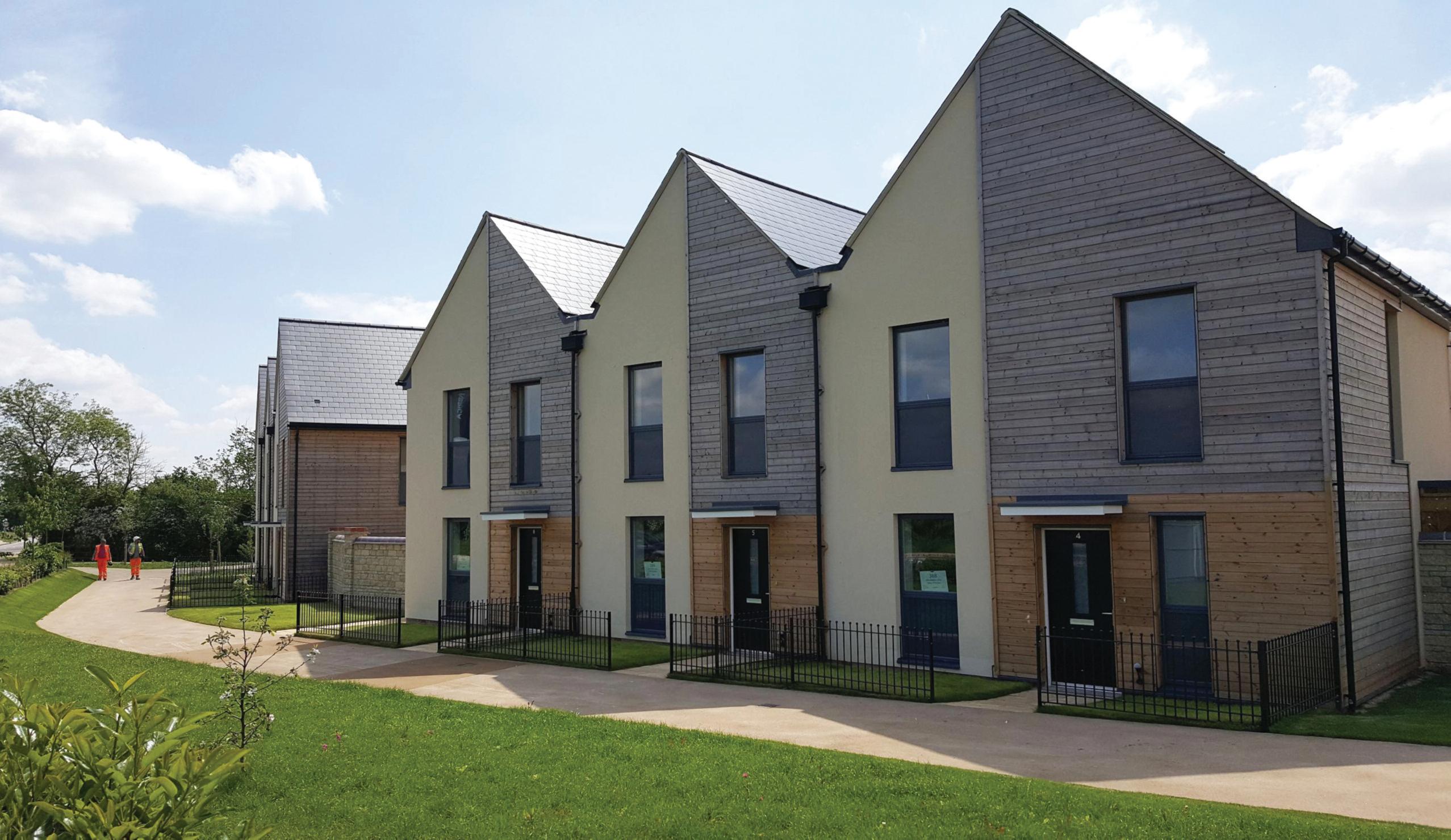
The pre-assembled flat roof modules and insulated floor cassettes meant a pair of semi-detached homes that are fully insulated and watertight were completed in just 72 hours, while also achieving reduced costs on preliminary site preparation This will be a huge consideration for housing associations across the industry, along with ensuring homes are future-proofed through achieving maximum energy efficiency
Achieving optimal insulation with SIPs Using Structural Insulated Panels, or SIPs in a recent large-scale project, SIPCO successfully manufactured and delivered 24 high-quality, affordable homes across four streets designed for modern community living in the Manchester area SIPs are an advanced method of construction that exploits composite panel techniques to deliver a structure that boasts exceptional thermal characteristics, while also enabling highvolume, fast-build and high-performance houses that can be built offsite
The increased use of structural timber presents an opportunity to transition towards a more sustainable and carbonefficient method of construction The environmental benefits are vast, from possessing the lowest embodied carbon of any building material to its increased energy-efficiency both in construction and operational carbon output
Arguably one of the most important factors about timber, is that it is the only truly renewable and sustainable building resource Providing forests are properly maintained and managed, timber will remain a sustainable and endless material, with typically five trees being planted for every tree farmed
The STA work tirelessly to increase the safe use of structural timber in construction, and we do this through education, research and by ensuring our members uphold the highest standards We achieve this through our STA Assure Quality Assurance scheme, which offers firm reassurances that STA members are supplying products and systems to an audited quality scheme, meeting or even exceeding current legislation and regulatory requirements STA Assure ensures that our members keep on top of the constantly increasing industry expectations on quality and competency, and as legislation continues to evolve, the technical support offered by the STA is invaluable n Find out more about the STA here www.rdrlink/lak022
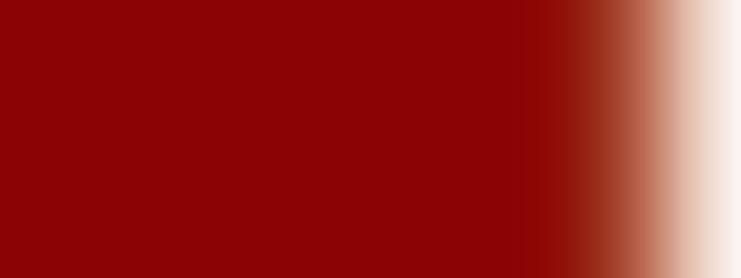
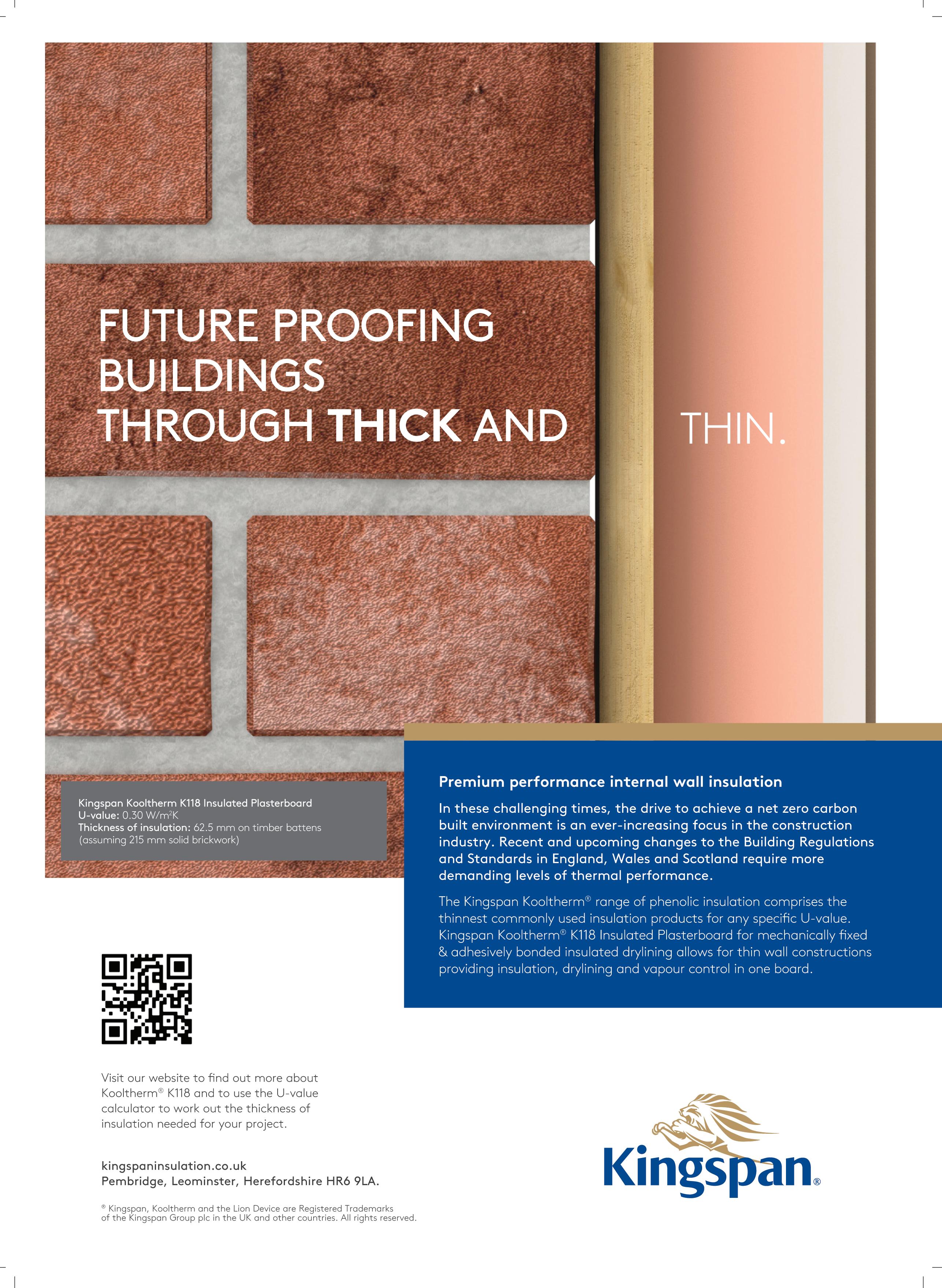