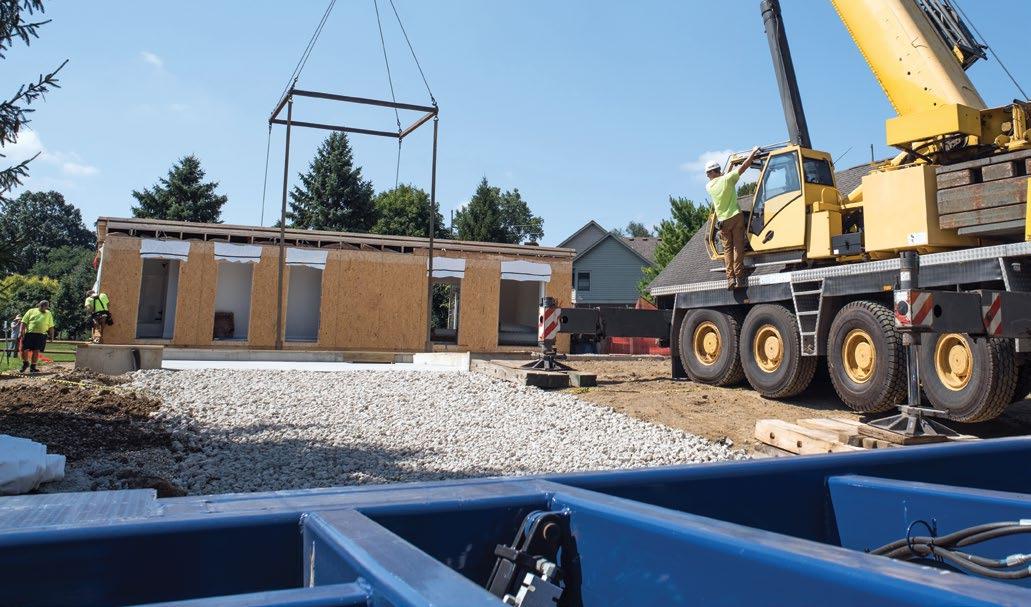
4 minute read
IS THE FUTURE OF CONSTRUCTION MODULAR?
FEATURE FEATURE
IS THE FUTURE OF CONSTRUCTION
Advertisement
MODULAR?
Winter is never a great time to be out at a job site. One week you're dealing with a muddy site, and the next, you're shovelling snow and running through HotHands like they were candy. That's not to mention coping with freezing portable toilets.
By Alex Kinsella
We all want to avoid construction in the winter—and NRB Modular Solutions may have figured out how. With plants in Grimsby and Cambridge, NRB Modular Solutions has taken some of the best practices from manufacturing and applied them to construction. From design to build, NRB's modular construction process has been one of the most significant advancements in construction since the first drywall use over 100 years ago. NRB has completed projects at the Bruce Power nuclear plant, a major pharmaceutical manufacturer, a steel plant, and other industrial and commercial applications. Touring NRB's plant and seeing projects in the field has us asking if modular construction is the future of our industry. Scott van Rooy, director of operations at NRB Modular Solutions, has worked in manufacturing for nearly 30 years and joined NRB in 2019. He said awareness and understanding of modular construction are starting to grow, but there is still much customer education needed to show the advantages over traditional construction.
NRB does not produce prefabricated buildings. Instead, it designs to spec and manufactures what van Rooy described as Lego blocks that get assembled at a site. "As we're building the blocks, the foundation is being poured and the site is being prepped. We ship the blocks and it is erected on site. You go from a blank slate with a foundation and within 12 to 15 days, you've got a three-storey building," van Rooy said. Tying the modules together and completing site finishes typically takes six to eight weeks, depending on the project's scope. For most projects, van Rooy said you could have occupancy of a building within nine to ten months. NRB has been producing modular buildings for over 40 years. The company originally started with smaller buildings, including kiosks and portable classrooms and now produce buildings for commercial, industrial, healthcare, and other applications. Van Rooy said that NRB's Grimsby plant makes more than 200 portable classrooms a year.
The City of Toronto is working with NRB to use modular construction for one of its affordable housing projects. Van Rooy said the feedback from the nonprofits operating the housing projects has been fantastic. "You're getting people off the streets faster—that's the beauty of modular. It gets the building done faster. Gets people off the street faster. Toronto Mayor John Tory is a big advocate of it. He's been through our facilities a few times and loves the modular concept because of that speed," van Rooy said. One of modular construction's most significant advantages is hiring and retaining skilled workers. Since the construction of its modular buildings happens inside, NRB can offer a climatecontrolled environment for its staff.
"Typically you'd be out in the mud right now. At NRB, you're indoors on a steady shift. We're on public transit, we have plenty of parking. Some sites in downtown Toronto, you'd be lucky to find parking within blocks of where you're working," van Rooy said. With work happening inside, NRB operates year-round without stops due to inclement weather. Van Rooy said this benefits NRB in two ways. First, they can plan out projects while avoiding weather delays. Second, they can offer steady work to skilled workers throughout the year, which improves the retention rate. "We still have some turnover, but it definitely minimizes it," van Rooy said. Despite these advantages, van Rooy said NRB still faces many of the same challenges in attracting and retaining skilled trades workers as traditional construction. He said there is still a significant gap in the number of young people pursuing a trade career due to misconceptions about the work and earning potential. "We've really got to start selling the math. Graduating university with a four-year degree, you may make $60,000 a year. Going into trades, you're going to make that much along the way as opposed to paying $80,000 after graduating," van Rooy said. Another major misconception is that modular construction means cheaper construction costs. Van Rooy said lumber costs are the same whether in the factory or on-site. NRB also deals with the same supply chain challenges that traditional construction companies face. Van Rooy said they are looking at 12 to 14-week backorders on basics like windows and doors.
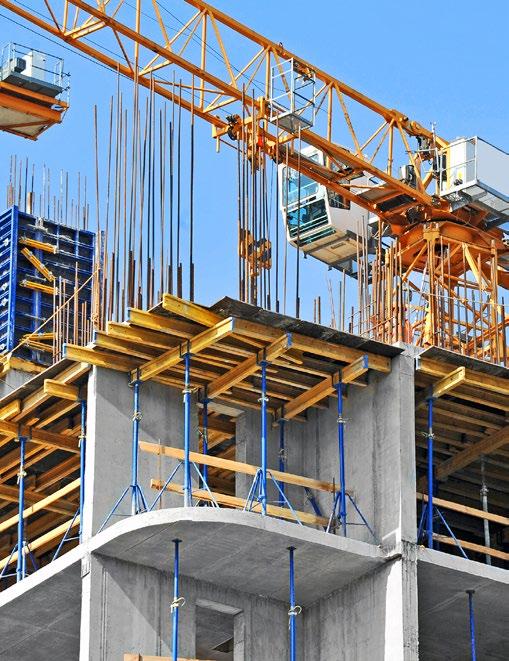
"When we're trying to sell speed, we have to think ahead on that kind of thing," he said. As for whether modular construction is the future, van Rooy said he sees the needle moving forward in 2023. "You've got a lot of old school guys that stick with 'this is the way we've always done it.' But we're on the cusp of something here. It's no different than the electric car was 10 years ago."