5 minute read
5 falhas que prejudicam o sucesso na armazengem grãos - Nathan Levien Vanier
Nathan Levien Vanier
Professor na FAEM-UFPel Especialista na área de Pós-Colheita, Industrialização e Qualidade de Grãos nathanvanier@hotmail.com
Cada operação realizada nas etapas de pré-armazenamento, armazenamento e conservação dos grãos pode interferir direta ou indiretamente na qualidade dos grãos que serão comercializados ao final do período de armazenamento. Quanto maior a discrepância entre a qualidade inicial dos grãos armazenados e a final (na expedição), maiores serão os prejuízos ao armazenista.
A seguir estão apresentadas de forma resumida cinco falhas muito comuns que prejudicam o sucesso no armazenamento de grãos. Cabe destacar que estas não são as únicas e que cada uma delas é um tema extenso e com muitas particularidades.
Erros nas determinações de umidade e de matérias estranhas e impurezas
O registro de volume das cargas na entrada e na saída das unidades armazenadoras de grãos tem como fator de correção o teor de matérias estranhas e impurezas e o grau de umidade. Este é o primeiro ponto de alerta: errar nestas determinações implica em falhas no registro de volume de grãos que compõem as cargas que ingressaram e/ou foram expedidas da unidade armazenadora.
É premissa básica que as operações de amostragem e análises sejam tecnicamente bem conduzidas. Além dos equívocos que podem ocorrer na aferição do volume armazenado, erros nessas determinações levam à falta de precisão nas estimativas de quebra técnica e de quebra de umidade no armazenamento.
Especificamente em relação à determinação de umidade, equipamentos adequadamente aferidos devem ser utilizados por secadoristas para definir os momentos de retirada de cargas dos secadores e de realização do carregamento de silos ou graneleiros.
Errar meio ponto percentual pode levar a uma tomada de decisão equivocada, que agrava a quebra técnica e causa sérios prejuízos financeiros ao armazenista.
Ausência ou erros de estratégia para segregação de lotes
Um dos critérios bastante utilizados para segregar lotes a partir da recepção é a faixa de umidade. Desta forma, a operação de secagem ganha tanto em eficiência como em uniformidade de umidade do lote ao final do processo, que terá reflexos na conservabilidade dos grãos armazenados.
O teor de defeitos dos grãos talvez seja o fator mais importante para segregação e que muitas vezes não é levado em consideração. A identificação de lotes mais propensos a perdas também é feita no setor de recepção dos grãos. Essa prática é mais comum em soja, onde lotes que ultrapassem determinado limite de grãos partidos, picados, fermentados ou mesmo ardidos e mofados são segregados de lotes mais sadios. Neste item também é premissa básica que as operações de amostragem e análises sigam as recomendações técnicas.
A correta identificação de defeitos na classificação dos grãos e a integração desta informação com os setores de secagem e armazenamento permitem que operadores segreguem lotes conforme a programação de expedição, previamente acordada junto à equipe de gestão da empresa.
Para unidades armazenadoras que operam com arroz, cevada, feijão e/ou trigo, a segregação pode levar em consideração outros critérios além da faixa de umidade e do teor de defeitos. Para estas culturas é comum utilizar a cultivar como um dos fatores de segregação; outros fatores particulares à uma ou outra cultura são: teor de micotoxinas, tempo de cozimento, cor dos grãos, teor de proteína bruta, número de queda, força de glúten, entre outros.
Capacidade de movimentação subdimensionada
Além dos aumentos em área cultivada e em produtividade observados em nosso país ano após ano, é notório o aumento na capacidade de colher maior volume de grãos em menor tempo. Há exemplos de fazendas em que alguns anos atrás a safra (colheita) demorava 45 dias e hoje leva apenas 10.
Soma-se a este aspecto o fato de que muitas unidades são projetadas para capacidade de movimentação inferior ao que precisarão em um curto espaço de tempo. Como exemplo, existem unidades com capacidade para movimentar 60 toneladas por hora que na verdade deveriam ser projetadas para 120.
A operação que geralmente trava o fluxo operacional nas unidades é a secagem. Para acelerar o fluxo de recebimento tem sido comum o emprego da secagem escalonada, em duas etapas. O espaço de tempo entre a primeira e a segunda etapa varia conforme a cultura. Grãos mais ricos em lipídeos, como a soja, requerem complementação em espaço de tempo bem menor do que cereais, como o arroz.
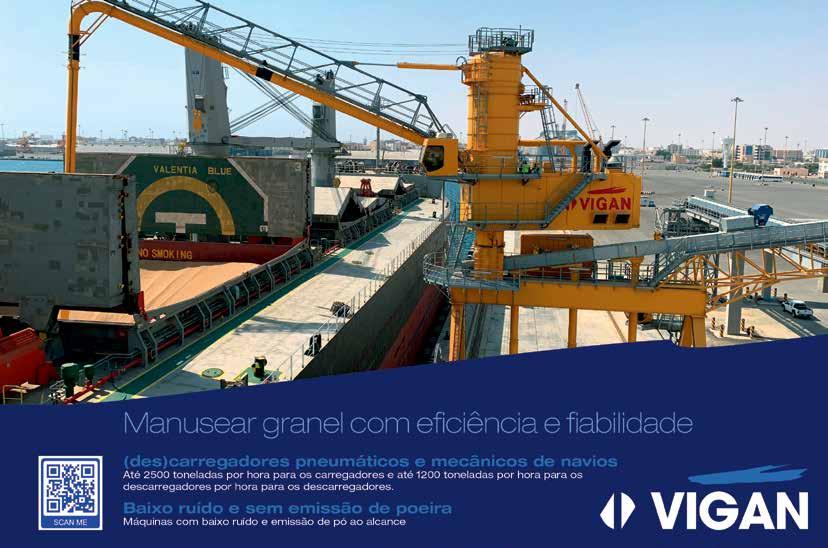
Falta de programação de comercialização ou industrialização
Saber qual produto comercializar primeiro ou qual lote industrializar em determinada situação é tão importante quanto a segregação adotada na chegada dos lotes na unidade armazenadora.
Para fins de qualidade de produtos e processos na etapa de industrialização, empresas armazenadoras e que também realizem o beneficiamento do arroz devem compatibilizar a escolha do lote armazenado com o padrão de qualidade desejado no lote industrializado.
Falhas na seleção dos lotes oneram processos, desgastam equipamentos, sobrecarregam equipes e aumentam riscos de não atendimento ao padrão do lote industrial.
Ausência ou precariedade de equipamentos e ferramentas para monitorar e gerir a unidade
A existência de sistemas de (a) amostragem, análises e registro de entrada e saída de cargas, (b) de acompanhamento de temperatura do ar na secagem, (c) de controle de fluxo nas operações, (d) de termometria, exaustão e aeração dos grãos armazenados e (e) de controle de pragas é requisito básico para monitoramento e gestão das unidades armazenadoras.
Existem opções para modernização e melhoria de cada operação. Um exemplo clássico é a utilização da termometria digital (em substituição aos termopares) e de maior número de sensores por área do silo ou graneleiro, medidas estas que aumentam a precisão no monitoramento de temperatura dos grãos armazenados.
Algumas unidades carecem de maior número de sensores de temperatura. Considerando que grãos são maus condutores de calor, muitas vezes quando se verifica aumento de temperatura em determinado sensor da termometria, na realidade a temperatura em ponto “cego”, entre sensores, pode ser bem superior.
Dados de inteligência artificial, associada a automação de processos, permitem que os sistemas de mediação das variáveis climáticas, de aeração, de termometria, de medição de umidade intersticial e de medição dos níveis de dióxido de carbono operem integrados, auxiliando (e muito) os responsáveis técnicos no manejo da conservação dos grãos armazenados.
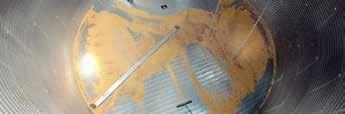
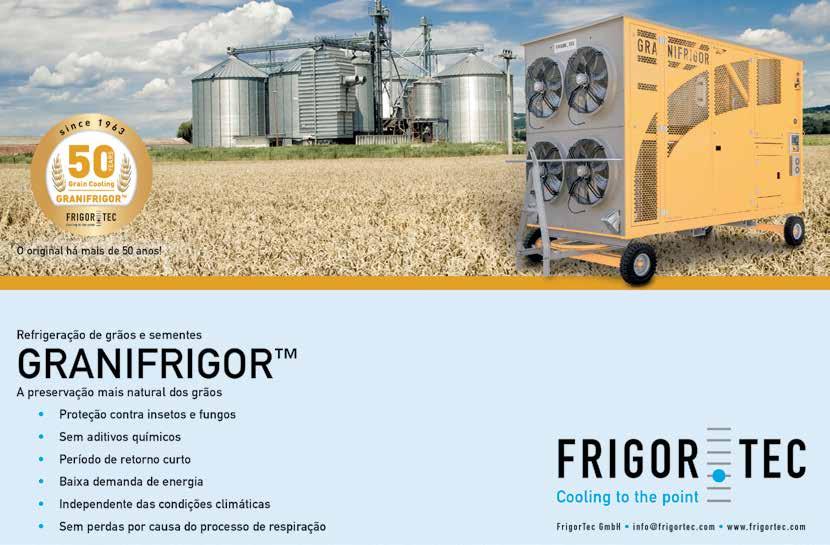