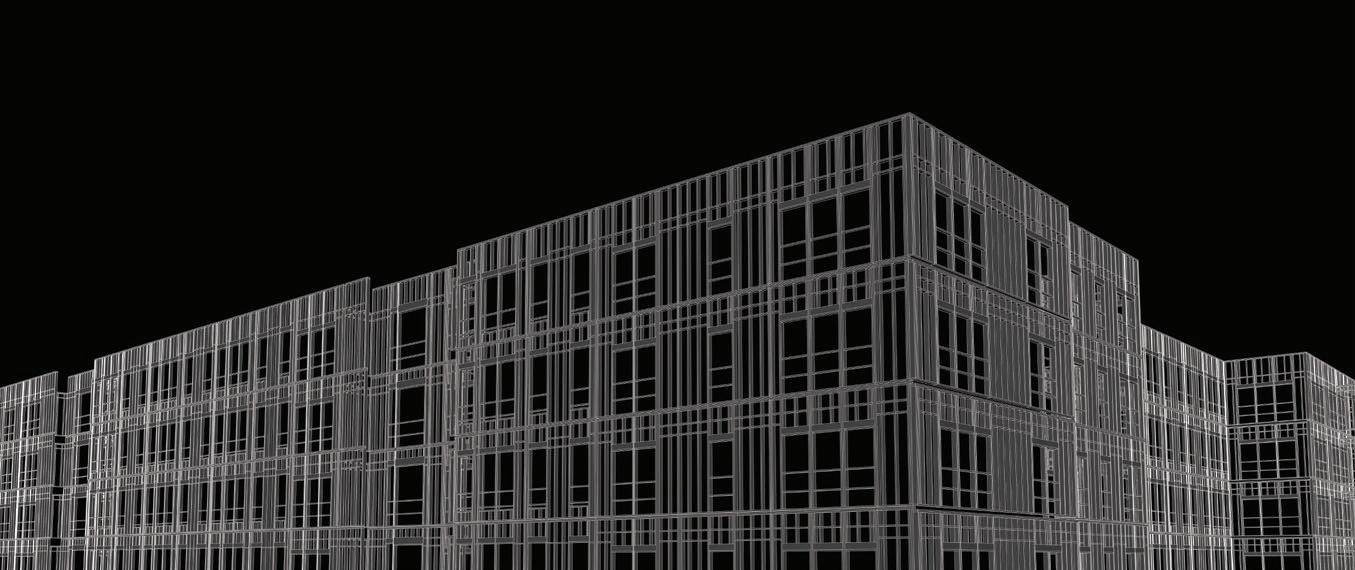
5 minute read
Technical Framing Solutions
AN AFFILIATE COMPANY OF COLT BUILDERS
When asked about his favorite part of the job, Jamie Howard, director of manufacturing for Technical Framing Solutions, answers quickly. “The best part of the job is being able to solve problems,” he says. “Coming up with new or improved processes that save people time and energy—that’s what I love to do.”
Advertisement
a BuildinG BaCKGrOund
Technical Framing Solutions is a sister company to Colt Builders and specializes in designing wall panels and floor trusses for many of their wood-framed buildings. Wall panels are a relatively new addition to the framing industry in some markets, offering an alternative to more traditional stick framing. Jamie, as director of manufacturing, oversees the design center and manufacturing process and credits his diverse background for preparing him for this unique role.
Like many people across Colt Builders and its sister companies, Jamie grew up in a construction family. His father worked as a building and remodeling contractor, so high school and college summers were spent learning the trade from his dad. Jamie decided to leave construction work and attend university to earn a degree in mechanical engineering. A few years later though, he found himself working in the framing industry once again. In the early 2000s, Glen Yates, who would become president of Colt Builders a decade later, offered Jamie a job, and for the next several years, Jamie worked in various construction-related positions. In 2012, Jamie joined Colt Builders as a project manager and assisted in the initial setup of some of the necessary programs for safety, estimating, and preconstruction.
PrOVidinG suPPlY tO meet demand
As Colt Builders grew to new markets, the demand for panels in the Northeast expanded. The company soon realized that it couldn’t keep up with demand for wall panels unless they started producing the product themselves. In diversifying their production line, the company was able to design and manufacture the panels off site and deliver them ready-to-assemble to each project location. “Traditional stick framing is much more time consuming,” Jamie explains. “Raw lumber shows up to a site, and the framing crew measures it, cuts it, and then nails it together. With wall panels that are manufactured off site, the field crew just has to stand a wall that’s already nailed together.”
Jamie and his teams craft their designs for the wall panels based on interpretations of the blueprints provided by engineers and architects. Design projects can take anywhere from a few days to a year to complete depending on the size of the project, but without the work Technical Framing Solutions provides, much more time is spent in the field interpreting and analyzing the plans.
the PartnershiP BetWeen sustainaBilit Y and innOVatiOn
In order to make a building a reality, reducing the time between an initial drawing to completion of a build is critical, and sustainability is the key component in that effort.
“Our goal in manufacturing is to ensure that the design is optimized and correct per plan. When optimized, it reduces the amount of extra, wasted material. When plans are followed in detail, there are fewer errors and no wasted time fixing mistakes in the field,” Jamie explains. “And when we make things efficient, the overall quality of the product is better, which is the biggest benefit.”
Minimizing architectural or engineering mistakes through detailed design isn’t the only way that Technical Framing Solutions is focused on making the entire construction process smoother. Technical Framing Solutions utilizes top-of-the-line
Nicknamed “The LEON”
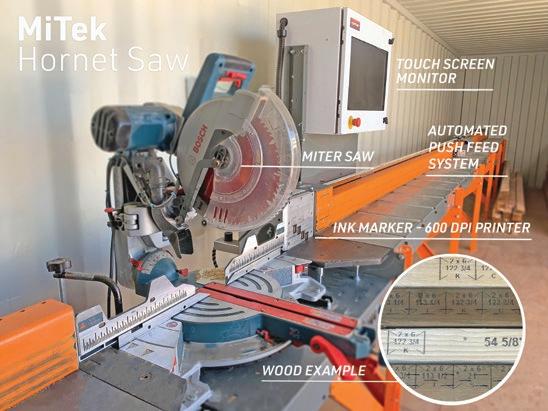
tools that embrace the advances of the digital age to help create modern solutions for age-old problems.
One of the most prominent ways that Jamie and his teams do this is by using a Hornet Saw, a recently developed tool that uses computer design and an automated machine to cut wall panel plates to the correct length, noting stud locations and openings for things like windows and doors. The pusher lines up the plates to be cut at the correct location while an inkjet printer then reads the design and prints out the markings.
“Traditionally, marking out the plates is usually done by hand with one layout person and a tape measure,” says Jamie. “And it’s one of the hardest parts of the job. By designing a computer model and exporting file that we can upload into a machine, we ensure the markings are as accurate as possible—less room for human error.”
By using the Hornet, Jamie estimates that the time his team spends marking and cutting the wall panels to match design specifications is cut by more than 90 percent. The machine is also small enough to transport from plant to plant, meaning no matter where the walls are being framed, the Hornet can make its way there.

a teCh-driVen future
Jamie is optimistic about where Technical Framing Solutions is headed in the next few years, and innovation in machinery is only part of a bigger picture. Training new members to eventually create robust design and estimating teams that can provide Colt Builders and the other companies the control and the support they need is also something he’s looking forward to. Because of his background in developing safety protocols and operation processes for Colt Builders, Jamie is excited for Technical Framing Solutions to teach and mentor young designers who will join the team in the future. This will be important as the trade grows, especially if the industry continues its trend toward a more technology-based approach. Jamie sees this as inevitable, and he’s ready to face it head on.
“The biggest benefit of technology is the efficiency it provides to the design,” he emphasizes again. “By providing our clients with 3D modeling and other kinds of innovative approaches, we’re able to complete quicker, faster projects where a lot of the answers and coordination with other trades are figured out ahead of time. Technical Framing Solutions is looking forward to providing more and more of that kind of benefit to Colt Builders.”
—JAMIE HOWARD, DIRECTOR OF MANUFACTURING
Technical Framing Solutions team