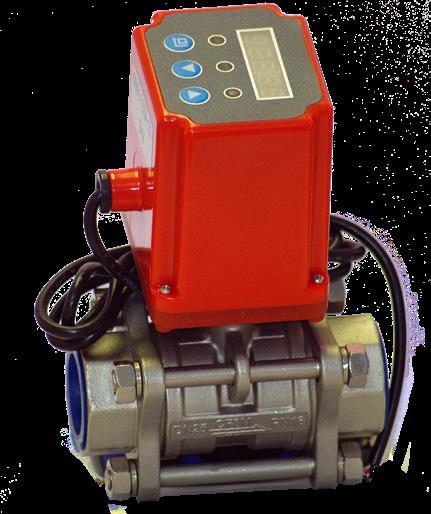
3 minute read
FAST AND EFFICIENT WATER TREATMENT SOLUTION
by 3S Media
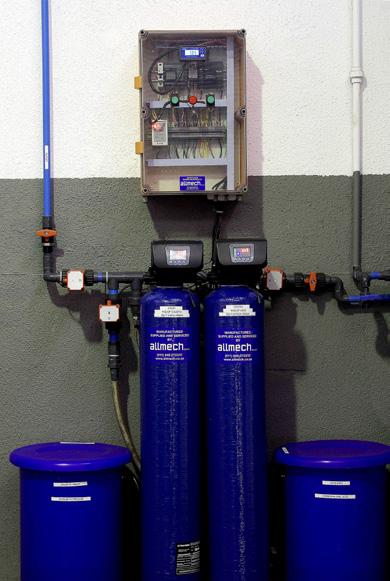
Demineralisation refers to the removal of dissolved solids from feedwater and process streams. By definition, it is the near-total removal of inorganic salts from water. In most industrial process water treatment applications, the removal of dissolved solids from feedwater and process streams is accomplished through ion exchange.
Advertisement
Demineralisation (demin) plants are widely used for industrial and scientific purposes such as in laboratory applications and testing, computer chip manufacturing, lead-acid batteries, cooling systems, high-pressure boiler feeds, laser cutting, steam irons and steam raising, pharmaceutical manufacturing, cosmetics, aquariums, and fire extinguishers. They require a lower capital investment than reverse osmosis plants and remove both cationic (positive) and anionic (negative) contaminants:
• Cations: calcium, iron, magnesium, manganese, potassium, sodium.
Allmech offers compact units that can be resized easily. The company caters for plants up to 15 m3/h of water, from raw water with a conductivity of 400 microsiemens
• Anions: chloride, nitrate, sulfate. How it works A demin plant typically consists of two vessels: one containing cation and the other containing anion exchange resins. Raw water enters first through the cation resin, where mineral contaminants are replaced by hydrogen ions, and next through an anion resin, where mineral contaminants are replaced by hydroxyl ions, which combine with the hydrogen ions to form pure water. A demin plant then needs to be regenerated with hydrochloric acid and sodium hydroxide when necessary. Allmech offers compact units that can be resized easily. Unlike other suppliers, Allmech caters for plants up to 15 m 3/h of water, from raw water with a conductivity of
400 microsiemens. Their control valves interlink and ceramic ball valves can be used with the control valves. These control valves are chemical-resistant and reliable, while the ball valves do not cause water hammer.
Allmech also offers a programmable logic controller (PLC) system that works with its in-house developed software to run the ion exchange demineralisation.
Regeneration
Regeneration is carried out using a municipal or raw water supply. The full regeneration process is estimated at 2.5 hours.
When the product water’s total dissolved solids (TDS) exceeds a set point, the demin plant commences with regeneration. The first vessel cation bed is regenerated by using a calculated volume of hydrochloric acid, followed by the second resin vessel anion bed regenerating using a calculated volume of sodium hydroxide. Water must be ‘decationised’ to regenerate the anion column. When the anion unit has completed the regeneration cycle, the plant returns to service mode and is ready to provide treated water. The Runxin ceramic electronic ball valve is used to return the demin plant to service from the regeneration cycle. Thereafter, the system does a rinse and the TDS is measured – if it is not within spec, the system will repeat the regeneration before going into an alarm state and shutting off automatically so as not to waste water.
Three Runxin ceramic electronic ball valves (three-wire) 12/24 V DC units are used in the setup. The regeneration process makes use of hazardous chemicals that create a waste product that must be disposed of. During the regeneration process, water production stops, affecting plant production. If the system does not shut off after unsuccessful regeneration due to a lack of available chemicals, it has the potential to waste a lot of water. A demin plant cannot run indefinitely – it needs downtime and manual inputs for regeneration to take place and resin replacement at approximately 10 years of use.
Flexibility
Some flexibility in the configuration of a demineralisation system is required in order to optimally meet various process conditions and purity goals. In designing a demineralisation system, consideration should be given to the changeability of the feedwater, level of purity needed, system footprint, tolerance for ion leakage (especially sodium and silica), and chemical feed requirements. The total dissolved solids (TDS) of the incoming water and required output are most important.
The size of the demin plant is dependent on the volume of water needed, the incoming TDS and the required TDS outcome. The maximum size is limited by the maximum vessel size that valves can be mounted on.
With the addition of the new PLC, Allmech’s demin plant is even more easily customisable through the programming of the various inputs. It also offers alarm functionality to flag when water quality does not meet standards, which ensures the water is not needlessly dumped through backwashing and alerts the user to potential issues in the system.
Considerations
Pre-treatment of water may be required. This will depend upon the nature of the incoming water and the type of demin plant.
Examples include:
• A demin plant operated on low-conductivity municipal water where significant levels
Allmech also offers a programmable logic controller system that works with its in-house developed software to handle ion exchange demineralisation of organics are present may need an organic scavenger or carbon filter for pre-treatment.
• A rinse water recovery demin plant system may also need carbon pre-filtration if there are high rates of organics or the presence of free chlorine.
• Multimedia filtration might also be used in this instance, where suspended solids (possibly resulting from metal hydroxide precipitation) could be present. Allmech can supply the pretreatment plants, filter plants and water storage facilities to help with the process.