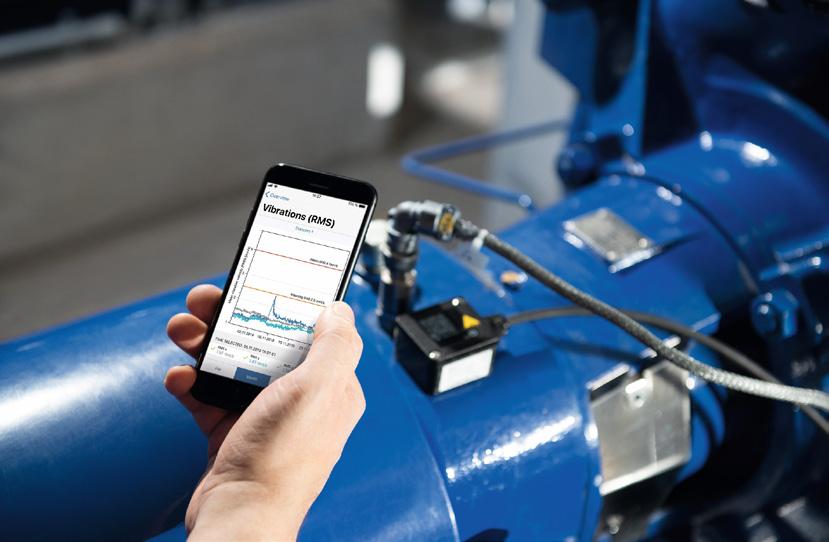
4 minute read
Energy efficient pumps
by 3S Media
As the mining industry in Southern Africa continues to grow, there is an increasing need for pumps and valves that are bigger, more energy-efficient and sustainable.
KSB Pumps and Valves, a leading manufacturer of pumps and valves, has been at the forefront of this movement, designing and manufacturing pumps specifically built to meet the needs of the mining industry. With a focus on sustainability, KSB is leading the charge when it comes to providing equipment that can handle a variety of mining conditions, is easy to maintain, and can provide a long wear life.
Advertisement
“In addition to our focus on sustainability, KSB also dedicates time and energy to minimising downtime on our mining pumps, which is achieved through a range of measures, including the use of highquality materials and manufacturing processes, as well as extensive testing and quality control procedures,” says Rob Bond, area manager: Mining in Southern Africa, KSB Pumps and Valves. This in turn ensures that KSB pumps are built to last, with minimal need for maintenance or repairs.
Global expertise and customer centricity
But when issues do arise, KSB’s aftersales service is there to provide support and assistance. With a global network of service centres and technicians, “KSB can provide rapid response times and quick repairs, minimising downtime and ensuring equipment is up and running as quickly as possible,” says Bond. This commitment to after-sales service is a key part of KSB’s approach to sustainability, as it helps to extend the life of their pumps and reduce the need for replacement or disposal.
“One of the biggest challenges facing the mining industry is the need to operate in a sustainable and environmentally friendly manner. To meet this challenge, we have focused on developing pumps and valves that are designed to reduce energy consumption and minimise the environmental impact,” Bond adds. By using the latest technology and materials, KSB has been able to produce pumps that are more energy-efficient, while still delivering the level of performance the mining industry demands. KSB’s after-sales service is also focused on preventative maintenance, with a range of services available to help customers keep their pumps and valves in top condition.
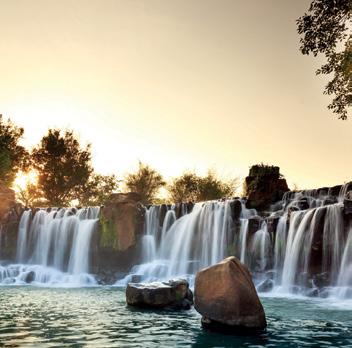
From regular inspections and maintenance schedules to training and technical support, KSB’s aftersales service is designed to help customers get the most out of their equipment, while also reducing the environmental impact of their operations.
“We have 37 production sites in 18 countries and nine foundries on three continents. Plus, we have over 3 500 worldwide service staff ready to assist you wherever you may be. KSB Mining has proven it is well equipped to offer our partners a complete package of products and services. We use our expertise to make our customers’ experience easy and successful. We provide exceptional and unparalleled customer service,” he concludes.
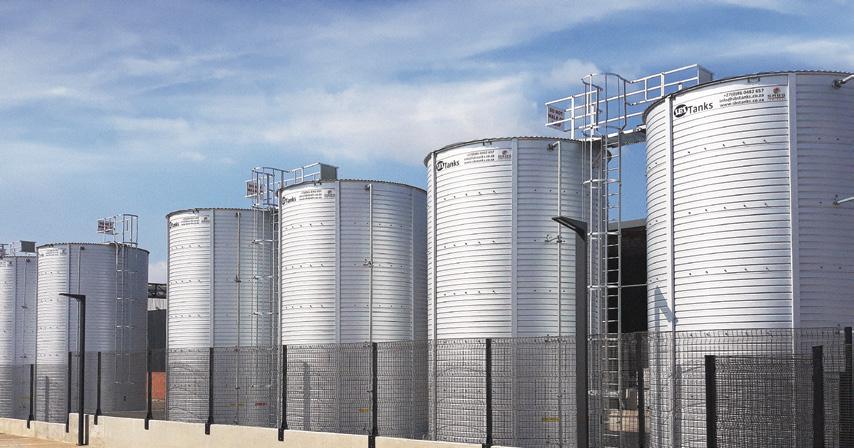
Water management is key to the automotive sector’s sustainability
Electric motors, CO2 emission reduction and lightweight construction are key issues for the automotive sector, but what about water? Automotive manufacturers use thousands of litres of water each day – making this an ideal cost-saving and sustainability focus.
By Chris Ashmore, GM, Watericon Group
Water conservation is becoming an issue of growing importance in sustainable vehicle manufacturing – not to mention the cost savings associated with sustainable water usage. Around the world, automotive manufacturers and suppliers are collaborating in their efforts to improve the environmental performance of their organisations.
Unfortunately, the true cost of using water is often misunderstood across industries, resulting in poor management choices regarding how water is used and treated.
For example, the automotive sector is a major consumer of water, which is a critical component in various production processes, including paint spray booths, surface treatment and coating, hosing, rinsing and washing.
Of the various automotive production processes that use water, metal finishing operations are notorious for high water consumption, but it is in the paint shop that water consumption is most significant. The painting process itself uses considerable water volumes, and processing equipment used
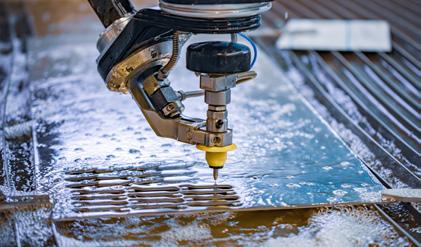
Chris Ashmore, GM, Watericon Group
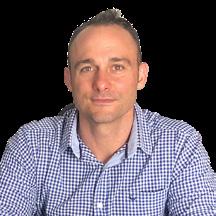
for automotive coatings must be cleaned regularly.
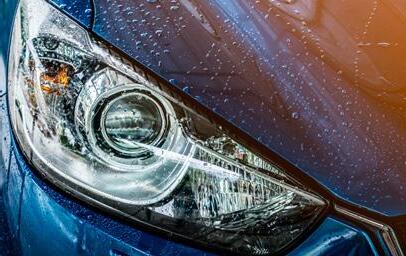
In addition to the use of water for these processes, there is also the matter of wastewater, which needs to be treated to high standards to meet environmental regulations.
So, how do automotive manufacturing plants ensure sustainability, improve their environmental footprint and save costs when their processes rely on using thousands of litres of water each day?
Reducing waste, reusing water and saving costs
Watericon is a South Africa-based water treatment company that provides a full range of water treatment services for the industrial, municipal and residential sectors. Specifically, Watericon assists its customers in the automotive industry to become more sustainable, while simultaneously saving on costs and allowing them to focus on what they do best.
For example, one manufacturer’s plant used municipal water as a rinse water source in its paint shop (Zone 11); however, effluent from a different part of the plant (Zone 8) was not utilised, resulting in wasted water that could be reclaimed.
Watericon’s solution was to build a water treatment plant that could treat the effluent water from Zone 8, so that this water could then be used as supply rinse water to Zone 11. This eliminated the use of municipal supply in the circuit, reducing water costs and boosting sustainability by reclaiming and reusing wastewater.
Similarly, a competitor’s plant generates a noticeable volume of paint water effluent, which, if left untreated, is unsuitable for reuse.
The solution was to build a water treatment plant to treat the paint water effluent to a level where it becomes suitable for use in the existing reverse osmosis unit, thus eliminating the need for municipal water.
Since implementing the new treatment system, the plant has had the benefit of reusing the treated paint water effluent, a decreased reliance on municipal water usage, and decreased effluent disposal costs. Each solution is custom-built for the needs of the specific plant.
Responsible for the installation of over 20 anaerobic digestors in Africa, Talbot has extensive experience in building, designing as well as operating biogas plants, and is beginning to see an increase in biogas projects.
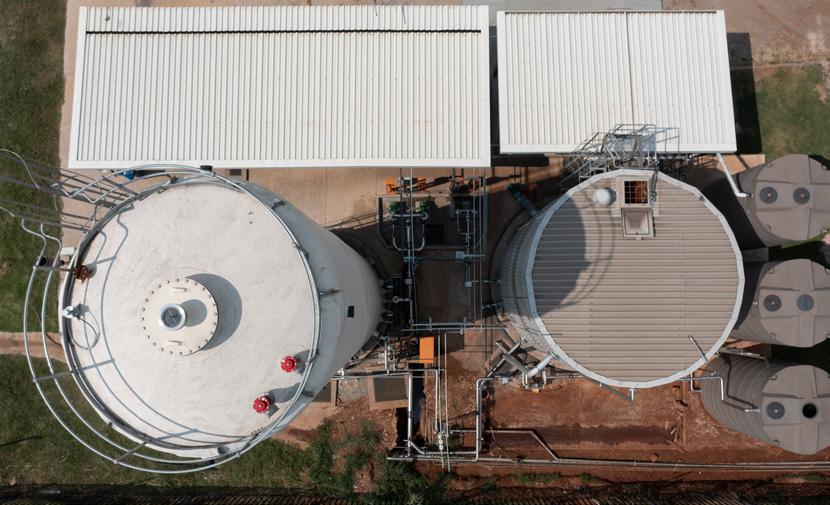

By Kirsten Kelly