
5 minute read
BIGEN delivers safe, reliable water to Palapye
Bigen was appointed as lead engineering, procurement and construction (EPC) designer on the Palapye Water Treatment Works Expansion Project that boosted the current treatment plant with a capacity of 18 Mℓ/day to 58 Mℓ/day that will service the area for at least another 20 years.
The contract was awarded in June 2019 with a project duration of 30 months. The letter of acceptance was issued on 28 June 2019 with access to site on 12 July 2019.
Advertisement
Expansion of the current treatment plant
A 40 Mℓ/day plant was constructed in two modules that operate in parallel. The project was completed within the contract period and within budget, even while experiencing the full impact of the Covid-19 pandemic and its related restrictions.
The new plant processes were carefully developed to follow the same process train and design aspect of the existing 18 Mℓ/day plant to allow operators, familiar with the old plant, the ease of understanding and operation the new plant.
The 40 Mℓ/day plant includes the following process elements:
• inlet works
• flow measurement
• pre-chlorination with chlorine dioxide
• pre-liming
• blending tank
• coagulant dosing and coagulation
• pulsator clarifiers (two off)
PROFESSIONAL TEAM
Client: Botswana Water Utilities Corporation (WUC)
Contractor: Stefanutti Stocks/ Heinsite Joint Venture
EPC lead designer: Bigen
Local subconsultant partner (minor works): Mmowe Consulting
• rapid gravity sand filters (10 off)
• post disinfection by chlorine dioxide dosing
• modifications to the existing sludge handling facility
• modifications to the washwater recovery facility.
Contract Values
Client budget: P450 000 000 (Pula)
Tender amount: P345 472 296
Final cost: P386 841 038
Budget saving: 14%
Continuous improvements and alternative construction methods were applied to optimise the design of the treatment plant.
The pulsating clarifier structure was extremely complex, with suspended overflow launders and settling hoppers with submerged concrete inlet channel sections. Various members were redesigned as precast members and a precast yard was established onand off-site to construct these members concurrent to the main construction activities. This reduced the construction period significantly and resulted in substantial cost and time savings.
A jointing system using expansion joints, water bars, bandage systems and sealants on all structures was changed to an in-fill strip system, whereby separate panels (walls and floors) were cast and allowed to complete the normal concrete shrinking process, after which the 1 m wide in-fill sections between panels were cast.
This required extensive planning between the contracting and design teams as the waiting period for shrinkage impacted significantly on the construction duration. These design changes proved to be highly successful as the quantities of reinforcing steel were reduced significantly, which resulted in cost and time savings. The success of this construction method was evident when the various sections of the water-retaining structures underwent watertightness testing without any failures.
As the new plant is located on an area next to the existing plant (with shallow rock), various design-level changes had to be made on the various structures to minimise rock excavation and save time and costs.
The existing sludge lagoons were used for the final dewatering of the sludge. An additional 20% hydraulic capacity was provided to enable the treatment plant to operate at an increased capacity of 58 Mℓ/ day when there is peak demand.
The hydraulic head available through the plant was limited, as the new 40 Mℓ/ day plant had to tie in with process infrastructure on the old 18 Mℓ/day plant. There needed to be careful planning as structures were raised and/or lowered while excavation proceeded to identify rock formations under the various structures. Interconnection to the existing infrastructure also posed a risk, as blasting was not possible close to existing infrastructure that could be damaged as a result. The constant changes to design levels proved to be very successful, as no blasting was required on any of the structure excavations, which resulted in further significant cost and time savings.
The following ancillary infrastructure was also provided:
• construction of a control room with Scada walls, board room, offices, car ports, ablution and kitchen areas for the operators on the old and the new plant
• Scada integration between the new and old plant
• double- and single-storey accommodation units
• paving areas around operator accommodation units
• fencing of the old and the new plant
• modifications to old plant inlet works to accommodate split flow to both plants.
Automation
The design team engaged with the client operators and process personnel throughout the design and construction stages, and jointly selected reliable mechanical and electrical equipment that is locally available and supported, and known to the maintenance personnel. These included pumps, blowers, actuated valves, control and instrumentation equipment already successfully used on the existing and other plants operated by the Water Utilities Corporation of Botswana. Mechanical equipment is fully automated (with status feedback) and can be controlled via a Scada system from anywhere in the world. All processes are automatically monitored with online measuring equipment for pH, turbidity, chlorine content and flows. The high level of automation allows for only one operator to monitor and control the entire plant remotely.
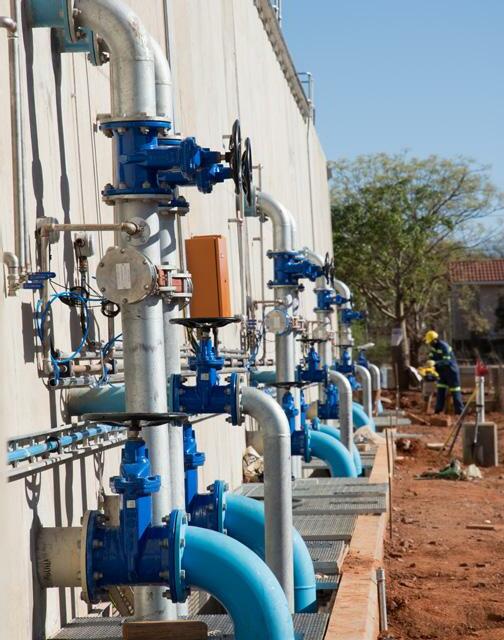
A specialist water treatment expert was employed by the design team to provide formal process and operations training during the commissioning period up to handover. The services provided by the designer include assistance during the one-year defects liability period. For this, the designer trained a local citizen employee to assist the operators during the defects period.
A remote link to the plant utilising the Scada system was provided to allow the consultant to operate and control the entire plant remotely from its offices in South Africa. This remote connection will also be used to assist the operators in fault-finding and troubleshooting. All data is recorded and available to access for information and compliance monitoring during the period of operation.
Challenges
The first challenge was to achieve a fine balance between complying with the bid specifications and competitive pricing. The EPC contracting approach places a lot of the risk on the contractor, which may lead to increased prices if the risk cannot be brought down to the minimum. To be competitive, it was necessary to complete designs at a level of detail that would eliminate completion and performance risks with associated costs. This was done under extreme time pressure and there was limited deviation from the bid stage design.
With the onset of the Covid-19 pandemic, Botswana’s government instituted travel and other restrictions. This impacted both the movement of key design and construction team personnel, as well as the supply chains for many of the construction inputs.
However, due to the national strategic importance of this project, construction work needed to continue. Once special permission had been granted, the EPC team improvised their way to creating alternative operating procedures. This included a rapid migration to virtual meetings and supervision inspections, and the use of photography for capturing construction progress.
The EPC team demonstrated their commitment to maintain productivity, as many members were forced to endure long periods away from their families as a precaution and to allow adherence to the travel restrictions.
Conclusion
The Palapye Water Treatment Expansion Project resulted in a secure, reliable and safe supply of water to an additional 500 000 people living in the towns of Palapye and Serowe, but also contributed immensely to the local economy of the region in the form of job creation, skills development and local economic expenditure.
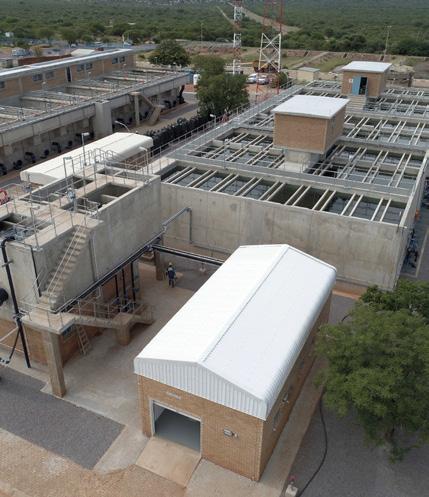
Wherever possible, most materials and resources were locally secured where possible. This included the provision of accommodation, furniture, stationery, security, electrical materials, reinforcing, cement, aggregates, formwork, steel pipes, UPVc pipes, bricks, concrete pipes and general building materials.
Fifteen subcontractors were appointed, of which only four were non-local companies. The professional project team also employed additional services from a locally owned citizen subconsultant for the full duration of the project to assist with quality and project management, especially during the Covid-19 lockdown period.
The expansion of the Morupule Power Station (Botswana’s principal domestic source of electricity, located just outside Palapye) and the establishment of the new Botswana International University of Science and Technology (situated on the Tswapong Hills, south-east of Palapye) resulted in significant expansion of the town of Palapye. This project has therefore made an immense contribution to local industries and mines, thereby improving the overall quality of life.
Bigen was fully engaged in all dry commissioning, wet commissioning, trial operation and training activities. Full commissioning and the production of compliant potable water were achieved on 17 January 2022.