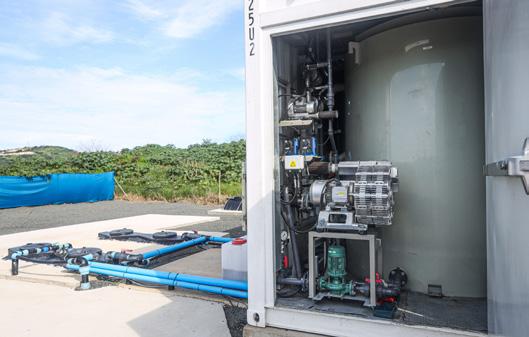
6 minute read
trialled by eThekwini Municipality PIONEERING WASTEWATER TECHNOLOGY
The technology models the functioning of the human lung. Lungs absorb oxygen and pass it on to the blood stream. Similarly, MABRs treat wastewater by passively supplying dissolved oxygen through a semipermeable membrane onto an aerobic biofilm.
“This is a fabulous aeration system where only oxygen can pass through the membrane to the biofilm –without the formation of bubbles. The biofilm performs as an active barrier that consumes oxygen, supporting anoxic conditions in the bulk liquid. It constantly removes contaminants from the wastewater,” says Lunga Patso, process engineer at MEB, the exclusive representative of Fluence Corporation in South Africa.
Advertisement
Counter-diffusion of oxygen and substrates
MABRs are especially effective for total nitrogen removal, due to the countergradient diffusion of substrates.
On the one side of the membrane, there is a low stream of air that is continuously supplied by a standard blower that works at very low air pressure. Oxygen passes through the semi-permeable membrane to the biofilm (where microorganisms are active) on the other side of the membrane. Here, the nutrients diffuse from the bulk liquid to the biofilm, where nutrients are reduced, and COD (chemical oxygen demand) is almost fully absorbed (bio-absorption) by the suspended growth.
The dissolved oxygen concentration is highest at the attachment surface and drops to low levels in the bulk liquid as it is consumed by the biofilm.
“Nitrifying bacteria are exposed to high dissolved oxygen levels, leading to higher nitrification rates. At the same time, the outer biofilm and bulk liquid are anoxic, allowing the heterotrophic bacteria to reduce nitrates with influent biological oxygen demand (BOD) as an electron donor. This makes MABR technology unique, as there is simultaneous nitrification, denitrification and BOD removal within a single biofilm," explains Patso.
MABR module
The activated sludge wastewater treatment process typically requires multiple chambers (anaerobic-anoxicaerobic), but MABR performs the actions in a single tank, since the membrane can achieve aerobic and anoxic conditions in the same basin. This smaller footprint is especially useful in urban areas.
The MABR module is a spiral-wound sleeve of oxygen-permeable material. An air spacer is inside the sleeve to allow for low air pressure flow. There is also an external water spacer that controls the water volume that is in contact with the membrane.
It is submerged in the biological reactor where intermittent mixing from diffusers causes the wastewater to circulate through the spiral. A short mixing duration is sufficient to homogenise the contents of each stage of the spiral reactor. In a four-stage spiral reactor, nutrients are removed in a onepass process without internal circulation.
The aerobic biofilm develops on the surface of the membrane and its thickness is well controlled; it cannot grow beyond 300 microns.
Patso adds that it is important to note that the wastewater is not filtered through the membrane. “The membrane provides optimum conditions for biology in wastewater. Therefore, there is no membrane clogging and fouling, no need to replace membranes every few years and no need for regular chemical maintenance. This reduces the operating expenditure of the plant. The MABR module is constructed from durable materials, ensuring more than a 20-year life expectancy.”
MABRs can be used in packaged plants and as a retrofit in existing conventional activated sludge (CAS)/AxO wastewater treatment plants.
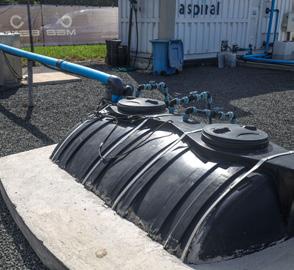
Additional benefits
Furthermore, MABR technology is extremely energy efficient due to
About Meb
The activated sludge wastewater treatment process typically requires multiple chambers (anaerobic-anoxic-aerobic), but MABR performs the actions in a single tank its passive aeration. By using low air pressure, the bubbleless aeration system reduces energy consumption by up to 90% compared to conventional technologies. On average, 0.25 kWh of energy is consumed per m3 of wastewater treatment.
“Its effective oxygen permeability leads to a high nitrification rate. Wastewater is treated to irrigation standards, BOD and nutrients are removed within a single basin, and this reduces the need for mixers required for the anoxic stage in the conventional activated sludge process.
The MABR module therefore has fewer electromechanical components, making the entire system easy to operate,” says Patso.
MABR’s low odour and noise levels make the technology ‘neighbourhood friendly’. A side benefit of the MABR design is the
MEB is a global company, operating in South Africa since 2010. It has 20 years’ experience worldwide in the fields of oil and gas, water, telecommunications, and power and energy. The MEB core business in Africa is water and wastewater, namely decentralised, modular, pre-engineered, sustainable and energy-efficient solutions.
The company has its head office in Umhlanga, KwaZulu-Natal, and offices in Maputo, Mozambique.
MEB has provided engineering, procurement and construction (EPC), as well as maintenance, management, operation and support to several water and wastewater projects in Africa, including:
• 10 Mℓ/day seawater desalination plant, Richards Bay, South Africa
• 30 Mℓ/day freshwater plant, Maputo, Mozambique ability to achieve up to 90% phosphorous removal without a dedicated anaerobic zone and chemical addition for this purpose. This drives down the operating expenditure on chemicals and manpower. Of course, chemicals for disinfection are needed just like any other wastewater treatment.
• solar farm and brackish water plant, Chigubo, Mozambique.
“This is not a new technology. Fluence is one of three global suppliers of MABR technology, and they have over 340 installations worldwide. MEB decided to showcase the technology in eThekwini, KwaZulu-Natal, South Africa, as a platform to demonstrate the effectiveness of MABR under local conditions,” states Patso.
eThekwini Municipality case study
The Aspiral™ S1 System – a full packaged plant containing fine screening, one MABR module, aerobic volume, secondary clarifier, disinfection and
Mabr Configurations Plant Capacity Features
Aspiral™ Micro – on-site decentralised sewage treatment plant, smallest product, includes a clarifier and pre-screen
Aspiral™ – packaged plant where MABR modules are submerged in a containerised reactor, includes a clarifier and pre-screen
Aspiral™ Plant – end-to-end wastewater solution, covering all stages (pre-treatment, primary, secondary, and tertiary) of wastewater treatment
Aspiral™ Modules – integrate MABR into existing solutions that require improved efficiency
SUBRE Plant – concrete MABR plant that is suitable for greenfield operations
SUBRE Upgrade – retrofit CAS/AxO plants using MABR to increase capacity without expanding footprint and/or improve the quality of the effluent
5 m3/day
50-120 m3/day
300 m3/day
• Scalable, modular system
• Can be moved from one location to another
• Treats wastewater for communities from 1 household to 35 000 households
• Pre-engineered pre-packaged wastewater solution
• Fast deployment
• Ideal for small towns, residential communities, resorts, hotels and commercial buildings
• Suitable for greenfield wastewater treatment plants
• Upgrade CAS/AxO centralised wastewater treatment plants for larger communities
• Eliminate delays for costly new builds
2 000-200 000 m3/day
• SUBRE towers are submerged within existing aeration basins with a minimum depth of 1.5 m
• Retrofits are done quickly with minimal disturbance to existing operations
As a fully automated system, the Aspiral™ S1 can be accessed from any location. This feature provided value during the Covid-19 pandemic and when there was civil unrest in KwaZulu-Natal where the site could not be physically accessed for a period of two weeks, yet the system could be monitored, operated and optimised remotely.
Pre-treatment is done through coarse screening and grit removal systems. A fats, oils and grease (FOG) trap is only required for oily wastewater with FOG concentration higher than 60 mg/ℓ control cabinet in a 20 ft container – was installed at a wastewater treatment plant in 2020.
“This is the first phase of a wastewaterto-drinking-water pilot that is intended to be scaled up for comprehensive reuse for potable water quality applicatio ns. Currently, the effluent produced can be used for non-potable uses, such as the flushing of toilets or for irrigation purposes,” adds Patso.
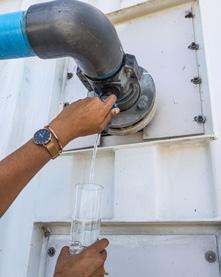
Due to the pre-packaged plant design and the limited amount of civil work needed (only concrete slabs), the entire system was installed within one week.
Pre-treated wastewater is pumped from an equalisation tank through a perforated 1 mm fine pre- screening and flows into the Aspiral™ S1 system where a submerged MABR module will allow for simultaneous nitrification and denitrification process, removing organic matter and total nitrogen pollutants from the wastewater.
"MEB is working with an independent, accredited laboratory that samples the treated effluent and provides results. As seen in the results in Table 1, the biofilm process protects from load shocks, low temperatures and even power disruptions,” states Patso.
The effluent from the MABR stage flows into the secondary clarifier unit where it is separated into two streams: clean, high-quality effluent and sludge. Most of the produced sludge is recirculated back to the MABR process (RAS) while the rest (WAS) is periodically discharged to the sludge holding tank. In the second phase of the project, tertiary treatment processes will be added to produce drinking water that meet SANS 241:2015.