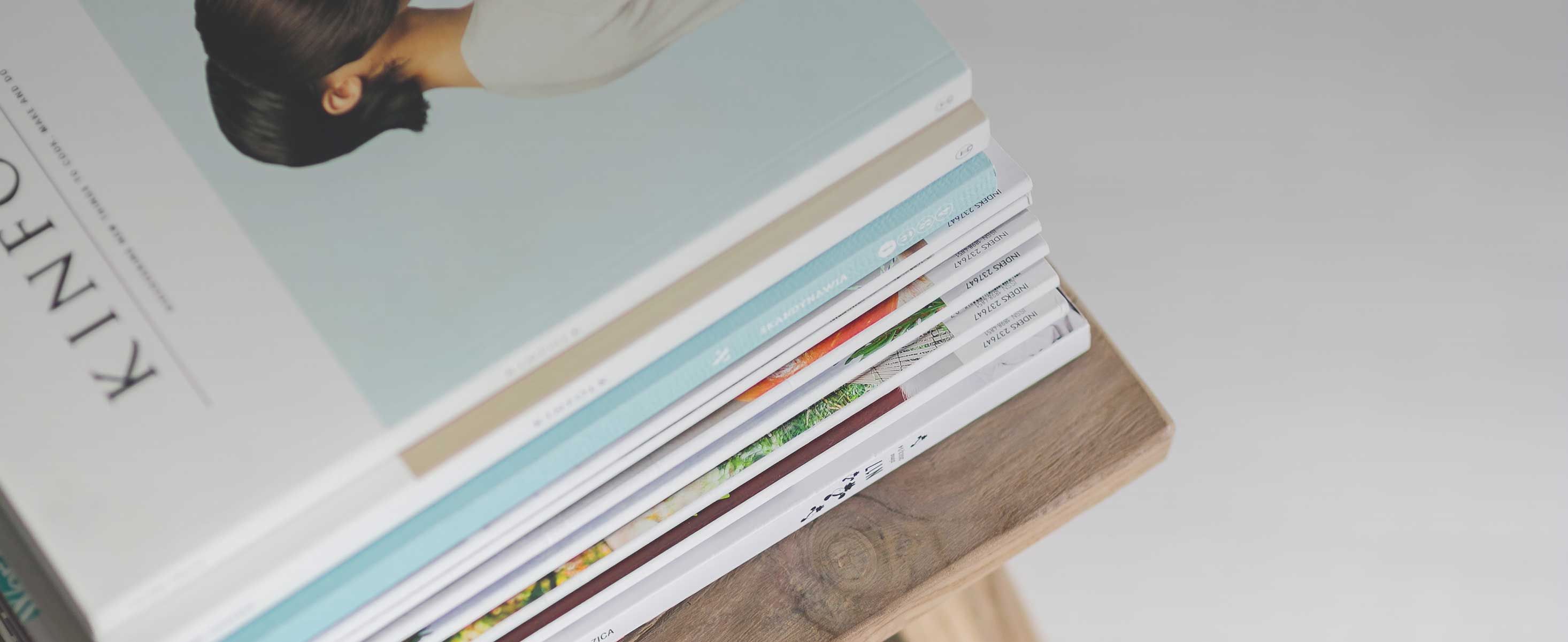
2 minute read
STEINMÜLLER AFRICA: STEAM GENERATION EXPERT REACHES A 60-YEAR MILESTONE
Inside Mining talks to Moso Bolofo, Director at Steinmüller Africa, about the company’s 60-year legacy and its ongoing service offering to boiler- and process-steam operators in South Africa and across the wider continent.
Steinmüller Africa has been in South Africa since 1962 and as such has a 60-year legacy – largely in the power generation sector. The steam generation expert started with the now-old stations of Grootvlei and Hendrina, then went on to the other baseload stations of Kriel, Duvha, Tutuka and Majuba. “In recent times, Steinmüller Africa has been a subcontractor to Hitachi for the fabrication of the Medupi and Kusile boilers, which are supercritical boilers that operate at main steam conditions of 240 bar at 560°C, with reheat temperatures up to 570°C. This requires Level 1 high-pressure pipework, which is an area of expertise for us,” Bolofo tells Inside Mining
Advertisement
Steinmüller Africa also operates in other industries that use steam in their production processes – such as the pulp and paper or sugar industry – or for the generation or reticulation of that steam in the petrochemical plants and the fuel refineries. From doing all the fabrication and following up with the installation and commissioning of several early boilers, the company has progressed to become a key service provider for ongoing plant maintenance. Steinmüller Africa also assisted in the mothballing and de-mothballing of the return-to-service plants at the Camden, Grootvlei and Komati power stations.
Well-equipped facilities and a dream team
“Our large-scale facilities in Pretoria West have worldclass fabrication equipment, such as our steam headers, and the Cojafex Induction Bending Machine for pipe spools – both of which are unique to the African continent,” explains Bolofo. The company’s Pretoria facilities have 50 000 m2 of under-roof fabrication workshops, with a lifting capacity of up to 50 t. Its bays are up to 35 m wide and 700 m long, and have a pressure component production capacity of 1 million hours per year. Its Piping Division is a true one-stop shop for all induction bending requirements, offering bending of pipes 48-850 mm in diameter and a maximum wall thickness of 120 mm, with a maximum radius of 4 600 mm.

The team also provides shop fabrication after bending, which entails heat treatment, pipeend preparation, spool fabrication, surface preparation and packing. The advantages of the bending facilities are high dimensional accuracy, custom-made individual bends and fewer buttwelds using complex 3D bend geometry. Based on the requirements and application of the material, certain alloys may require post-bend heat treatment.
Steinmüller Africa has furnaces with accurate temperatures up to 1 200°C. “We also specialise in electrical post-weld heat treatment, which is crucial to the quality and integrity of welding on highpressure parts and pipelines,” Bolofo explains.
Steinmüller Africa’s history proves the claim of being an end-to-end service provider that really does look at the whole life cycle of a plant – from conceptual design, manufacture and installation to maintenance and through the entire service life, until decommissioning or lifetime extension.