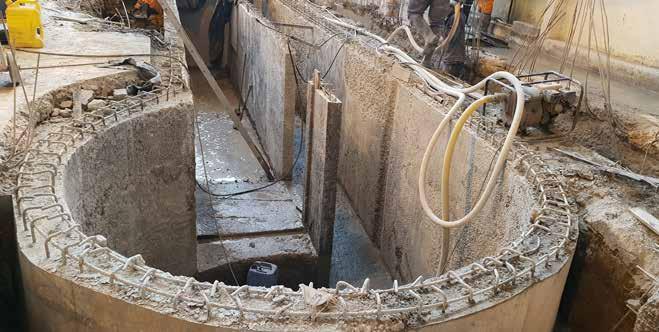
8 minute read
Repairing concrete with concrete in sewer systems
from IMIESA July 2021
by 3S Media
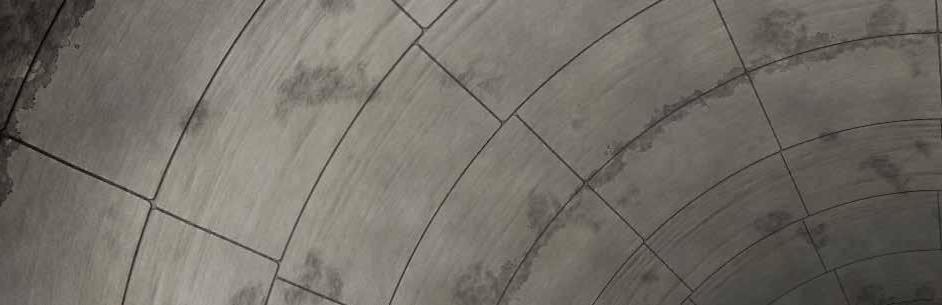
Hydrogen sulfide (H S) gas build-ups within wastewater 2 networks are the main cause of accelerated biogenic corrosion in concrete structures. Unless countered, H S 2 will significantly shorten the life of infrastructure assets, but there’s a proven solution using specialty calcium aluminate cements and aggregate products developed by French multinational Imerys, operating locally as Kerneos Southern Africa.
Advertisement
Removing spalled concrete caused by severe corrosion A refurbished section of a wastewater treatment plant sprayed with SewperCoat
Apioneer in its field, Kerneos Southern Africa registered its first patented product, Ciment Fondu® , in 1908. This calcium-aluminate-based hydraulic binder, which is supplied to this day, was the forerunner of a series of proprietary innovations in the refractory, infrastructure and general industrial sector. A groundbreaking one for the wastewater industry was the introduction of SewperCoat® in 1991, which celebrates 30 years of successful application worldwide, including South Africa – a country widely regarded as an early adopter of the technology.
SewperCoat’s unique aluminate cement and aluminate aggregate composition is a purpose-designed corrosion inhibitor and protection coating used to preserve most sewer infrastructure assets. These include iron and precast concrete pipes, manholes, pump stations, and concrete infrastructure in wastewater treatment plants. Application techniques include low-pressure wet spraying, high-pressure dry spraying, as well as rotational spinning head spraying.

BENEFITS IN A SINGLE PRODUCT 10

- Outstanding biogenic corrosion resistance - Easy monolithic installation: mixed, pumped and sprayed using conventional equipment - Readily adheres to damp concrete surfaces - Rapid return to service - Restores structural integrity - Creates an infiltration barrier - High abrasion resistance - No volatile organic compounds - Sustainable and long-lasting
“Calcium aluminates have a distinctive chemistry that makes them far more resilient than conventional Portland cement in environments where H S and other corrosive 2 elements, like acids, are present,” explains Dr Francois Saucier, Director: Infrastructure Project Specification, Imerys Building & Infrastructure, based in France.
Alumina is derived from bauxite ore – the primary source of aluminium – and aluminate cement is regarded as a niche material within the construction sector. To illustrate the point, somewhere between 2 and 3 billion tonnes of Portland cement is produced annually worldwide. This compares to some 2 million tonnes annually for calcium aluminate cement. Essentially, it’s a premium cement where the added cost more than justifies the assurance of longer-term operating life for critical assets. For SewperCoat, that’s been proven on thousands of sewers worldwide: the answer to combatting microbiologically induced corrosion – sulfuric acid being the main culprit.
Within France, a key project example was the use of SewperCoat to rehabilitate some 23 500 m2 within a 4.4 km bulk sewer line for the Greater Paris Water Authority during 2016. This was the same year that SewperCoat was first introduced to the South African market, although Kerneos Southern Africa itself has a long local history dating back to 1970 when it opened its Richards Bay factory.
Applying SewperCoat on a surface bed
Cape Town projects

“Our first major order was for a City of Cape Town project in 2017,” says Tendayi Kaitano, Africa Development, Kerneos Southern Africa. “This entailed a major pump station refurbishment where severe corrosion had been experienced. Using SewperCoat, the contractor was able to fast-track the programme and the pump station was
returned to service within a sixweek period.”
One of the key advantages of SewperCoat is that concrete gets repaired with concrete, helping to restore its structural integrity. The product also performs best when applied directly to the moist concrete surfaces
LEFT With the original corroded surface concrete layer removed, this section is now ready for a SewperCoat application
BELOW LEFT A severely corroded section of a wastewater tank section prior to refurbishment
A refurbished concrete wastewater tank after SewperCoat treatment



commonly found in sewer environments. In fact, SewperCoat needs water to hydrate, making it an optimal solution for live sewers.
Once sprayed to a specified layer thickness, this specialty cementitious mortar starts to harden rapidly, reaching 20 MPa within five to eight hours, and 40 MPa within 24 hours.
Coatings vary in thickness. For a manhole, for instance, the recommended thickness is 15 mm, and 25 mm for an interior pump station refurbishment. A rough surface is always necessary for optimum adhesion and interlocking with the bonded surface. This roughness requirement is already present to a greater or lesser extent, depending on the severity of the corrosion.
When urgent, an additional surface hardener can be applied to allow for a sewer system to return to service within one hour, but Kaitano says this is a highly specialised approach. “However, since a main sewer cannot be shut down for too long, it’s reassuring for municipalities to know that this option is available,” he explains.
In terms of current projects, the City of Cape Town has again specified the application of SewperCoat for the refurbishment of the Cape Flats 1 and 2 sewer lines, each measuring some 14 km in length. The pipe diameters range from 1.2 m to 1.8 m, and the contractor is considering using a spinning head spray system on certain sections.
“Techniques like cured-in-place pipe lining tend to work well for pipe diameters below 1 m. Above this, and for longer sections, it becomes very costly,” explains Dr Saucier. “Either way, the severest corrosion tends to occur within environments like manholes and inlet chambers, where H2S builds up in the highest concentrations.”
Every technology has its claimed advantages in terms of corrosion protection. Epoxy coatings are a prime example, which often work optimally when applied to dry concrete during the finishing stages of wastewater projects. However, studies show that they tend to work less well when epoxies need to be reapplied during a sewer refurbishment. The key challenge here is that epoxies are typically hydrophobic. When applied under normal wet operating conditions, they tend not to bond as well, so they peel off after a few years.

Accelerated corrosion
H S is certainly unforgiving on concrete, but 2 there are even more aggressive chemical compounds out there – particularly those derived as by-products of industrial processes. At times, these chemicals make their way into municipal sewer systems, chiefly because of illegal dumping.
In a recent case, Kerneos Southern Africa supplied a SewperCoat solution for a key wastewater treatment works in East London. Severe corrosion some 15 years after commissioning was significantly inhibiting process efficiencies. Industrial effluent was a contributing factor.
“Sometimes, the source of corrosion can be unexpected. Sugar, for example, is far more corrosive than H S and will easily eat away 2 200 mm to 300 mm of concrete within six months if there aren’t countermeasures in place,” Kaitano explains. “We’ve worked extensively with the South African sugar industry to address this problem, supplying our heavy-duty Fonducrete® calcium aluminate mortar. We have case studies that confirm sound concrete integrity some five years after application.”
Precast and steel pipe industry
Routine predictive and preventative maintenance interventions should always form part of an infrastructure asset management programme. The extent to which this can be minimised will also be influenced by the measure of corrosion protection in-built at inception.
“Globally, South Africa’s precast manufacturing industry stands out as one of the most progressive adopters of calcium aluminate cement and aluminate aggregate coated sewer pipes,” says Dr Saucier.
Back in 1989, the precast pipe industry established an experimental test station in Virginia, Free State, which is still active today. The setup enables the effluent flow to bypass the experimental line during inspection. Follow-up studies have been performed by Alaster Goynes from Pipeline Installation and Professional Engineering Services and Professor Mark Alexander from the University of Cape Town. With two PhDs completed on this project, there’s plenty of local data available, with four study phases conducted so far. Dr Saucier says this is a unique long-term study with an excellent body of evidence.
These Virginia tests confirm that calciumaluminate-lined pipes achieve four times the durability of Portland cement. Where manufactured test pipe sections are composed entirely of calcium aluminate, this increases to 10 times the durability.
Manufacturers within the South African steel pipe sector are also applying SewperCoat liners for sewer installations. A recent example is a project for a KwaZulu-Natal utility. This entailed the fabrication of some 0.5 km of 1.8 m diameter steel pipeline to replace an existing section, which had become heavily corroded. The internal coating thickness is between 25 mm and 35 mm, and was applied with a spinning spray device.
“Maximising the return on investment should always be top of mind for municipalities, and that boils down to best-in-class durability. SewperCoat is a premium product that will stand the test of time, maintaining the integrity of wastewater networks for decades – a fact that utilities from around the world have confirmed,” Kaitano concludes.
