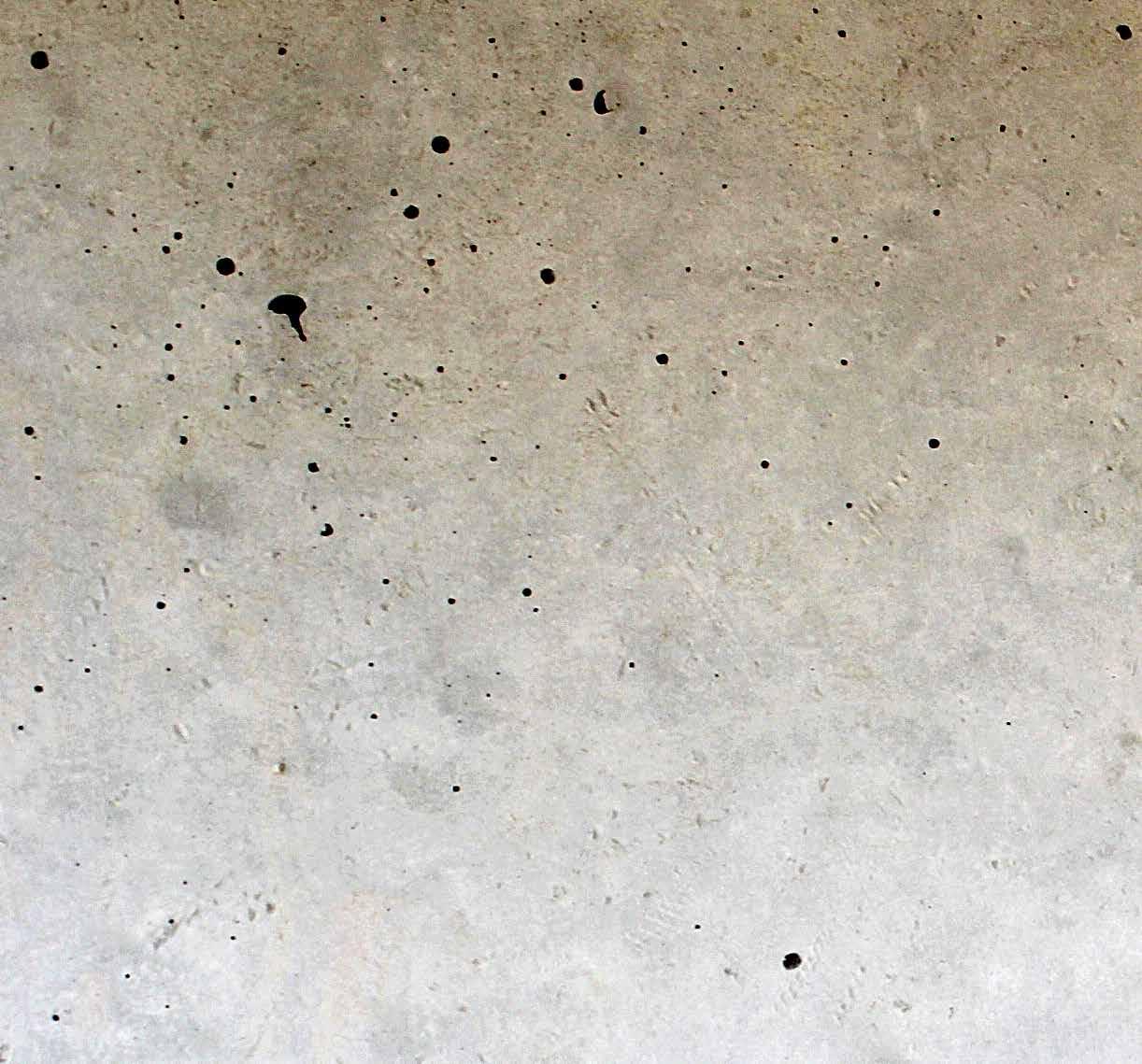
4 minute read
Minor concrete defects and their remedies
from IMIESA January 2021
by 3S Media
Bryan Perrie, managing director, TCI
The durability of concrete is exceptional and well recognised but, sometimes, operational errors or unforeseen circumstances can cause unsightly, superficial surface damage, says Bryan Perrie, managing director of The Concrete Institute (TCI).
Advertisement
The quality of any cast concrete product depends on material selection, equipment used and workmanship. Surfaces of acceptable quality and accuracy are difficult to achieve and, depending on functional and aesthetic requirements, some repairs may be necessary. Repairs may also be necessary where surfaces are damaged in service. Minor defects include: • Small cavities: such as those formed by tie-bolts and impact damage to the surface. • Honeycombing: concrete in which mortar is partially or completely absent, caused by mortar loss during placement, or segregation of the stone and mortar. • Misplaced surfaces: usually the result of incorrectly aligning or positioning
formwork, or movement of formwork during concrete placement. Under- or overfilling of formwork may also be the cause. • Blowholes: relatively small voids of roughly spherical surface shape formed against formwork or moulds, usually caused by inadequate compaction of the thin layer of concrete in contact with formwork, or the incorrect mould release agent for the formwork employed.
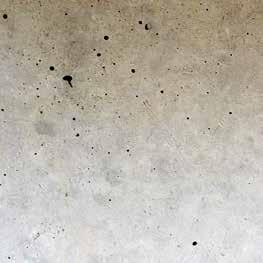
Blowholes are relatively small voids of roughly spherical surface shape formed against formwork or moulds, usually caused by inadequate compaction of the thin layer of concrete in contact with formwork, or the incorrect mould release agent for the formwork type
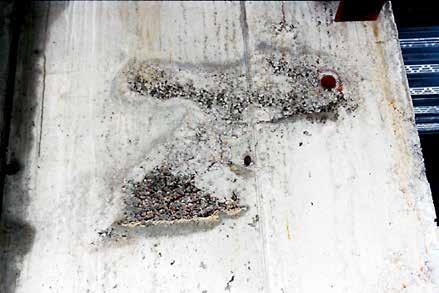
Basic types of repair materials
Repair materials are formulated to reduce the likelihood and severity of cracking. This is done by reducing potential drying shrinkage, which will reduce the tendency to crack. Two approaches are possible.
The first approach is the use of ‘semi-dry’ mixtures of cement, water and aggregate, compacted by being rammed into position. Semi-dry mixtures have low water content and therefore very low potential drying shrinkage – and a consequent resistance to cracking. But water content is critical: if too low, thorough compaction is impossible; if too high, the repair may slump or crack. These mixtures can be used only in confined spaces such as
The cause of honeycombing: concrete in which mortar is partially or completely absent, caused by mortar loss during placement, or segregation of the stone and mortar
cavities and, ideally, applied by trained, experienced and skilled operators.
The second approach is the use of plastic mixtures of cement, water, polymer emulsion and aggregate (polymer-modified mixtures) applied by trowel or spatula to reduce the amount of water required for a given consistence. The hardened material, which incorporates a 3D network of coalesced polymer, exhibits greater creep and toughness. Consequently, potential drying shrinkage is relatively low, tensile stresses resulting from restrained shrinkage reduced, and cracking significantly reduced.
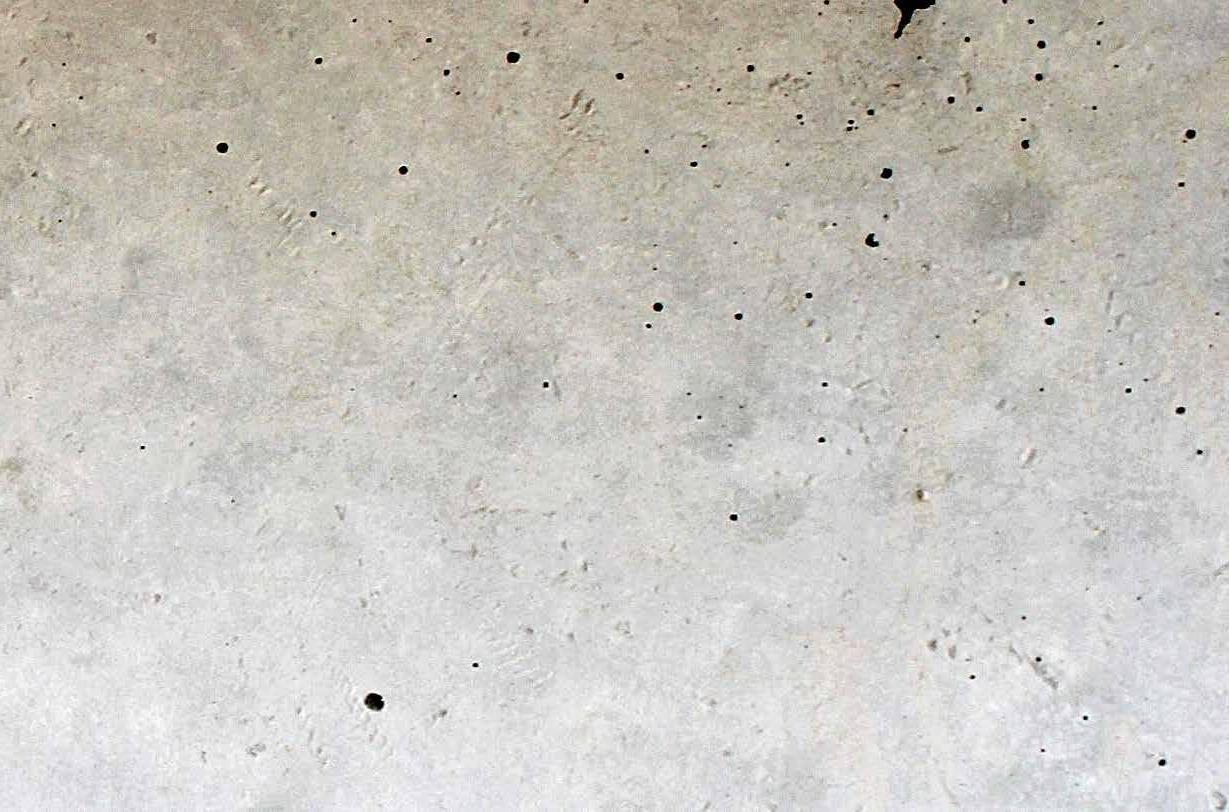
Selecting materials for repairs
Repair materials are mixtures of cement, water and aggregate, with the possible inclusion of a polymer emulsion. In all respects, it’s important to note that cement must meet the requirements of SANS 50197 for Common Cement, and the National Regulator for Compulsory Standards (NRCS) requirements as detailed in NRCS VC9085. Bags should be clearly marked with the strength grade, notation indicating composition and a Letter of Authority (LOA) number issued by the NRCS. To verify valid LOA numbers, contact the NRCS on +27 (0)12 428 5199 or www.nrcs.org.za.
Water that is potable from a municipal simply is suitable, but needs testing to establish acceptability if from other sources. Maximum aggregate particle sizes must also not exceed a quarter of the thickness (or least dimension) of the repair and, preferably, be spherical. If such materials are unavailable, particles should be rounded, roughly cubical or ‘chunky’. Flaky and elongated particles should be avoided.
Another important point to note is that sand used for repair work should have particle sizes ranging from dust to the largest size. Sands with similar-sized particles produce mixes with poor workability and a high water requirement, and should be blended with other sands to improve grading. The following aggregate types, blended where necessary, may be suitable for repair work: - Plaster sand: useful for blending with a coarser sand to improve workability or on its own for making priming slurry and filling blowholes. - Concrete sand: naturally derived pit sands or river sands and well-shaped crusher sands, with coarse particles removed by sieving if necessary and blended with a finer plaster sand. - Stone pebbles and crushed stone with well-shaped particles. - Polymer emulsions, formulated for use with cement, obtainable from specialist suppliers. Such emulsions should be based on styrene butadiene rubber or acrylic.
For more information, visit www.theconcreteinstitute.org.za or email info@theconcreteinstitute.org.za
Find our branches at www.technicrete.co.za

paving | mining | masonry | kerbs | erosion protection | retaining walls | drainage

PAVING FOR: RETAINING WALLS FOR: • Driveways • Earth embankments • Roadways • Steep channels • Pavements • Slopes • Walkways • Bridges / river banks
Technicrete is a subsidiary of ISG, a leading supplier of innovative infrastructure products to the construction and mining markets in Southern Africa.