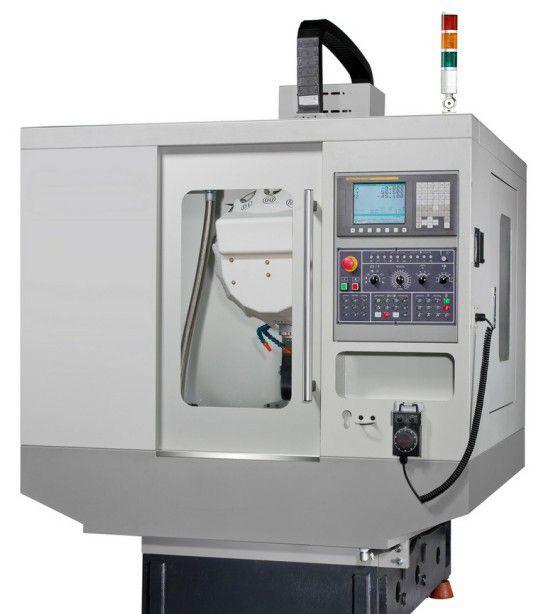
6 minute read
Machinery
£110K MACHINERY INVESTMENT TO BOOST PRODUCTION AT AT PRECISION
Leading aluminium bifold hardware supplier AT Precision has invested £110K in new machinery, in a bid to ramp up production and keep up with growing demand.
The Durham-based company has bought in a CNC vertical machining centre, an 8-head tapping machine, as well as three new saws.
Sales Director Michael Hewitt comments: “We’ve seen an increased demand for aluminium products across the board, especially for bi-folds and patio doors, meaning demand for our products has also soared. “Future proofing the business by investing in new machinery is a vital step in meeting this demand and continuing to deliver the best quality products our customers are used to, matched with excellent service and competitive lead times.” Serving to over 100 fabricators across the country, AT Precision manufactures the Everglide range of bi-fold hardware, which includes rollers, top guides, pull handles, hinges, cleats and shootbolt handles, as well as the Everseal range of wedge, captive, flipper and bubble gaskets. Both ranges are compatible with all major systems, and because they’re manufactured in-house, come at a very affordable rate.
The new suite of machinery is the latest in a series of investments at AT Precision, following the addition of plastic ancillaries, espagnolette window handles, security hardware, as well as aluminium profile, to its wide range. Michael concludes: “As a leading aluminium bi-fold hardware manufacturer, we pride ourselves on being a reliable supplier that fabricators can trust, and so it’s vital that we’re able to keep up with customer demand. “Buying in a host of new machinery will significantly boost our production speed and capacity to allow us to do just that, and has been an extremely worthwhile investment.”
www.atprecision.co.uk
ROSEVIEW WINDOWS TAKES DELIVERY OF SECOND SBA-4 VS PVC-U PROFILE MACHINING CENTRE FROM HAFFNER
Roseview Windows, the UK’s leading vertical slider manufacturer, has just taken delivery of a second SBA-4 VS PVC-U Profile Machining Centre from Haffner.
Mike Bygrave, Sales & Marketing Director at Roseview Windows, commented: “Roseview has witnessed a sharp upturn in demand in the past 18 months as a result of the continued popularity of feature-rich sash windows. Our investment in this new machine will give us a big increase in capacity and further support our continued strategy for growth.” The second machine arrives on the shop floor just 12 months after the business took receipt of their first Haffner VS machining centre. Mike commented: “We invested in our first SBA-4 VS machining centre to replace an ageing machine and upgrade efficiencies across the shop floor. It made such a huge difference to our fabrication capabilities we had no hesitation in ordering a second machine to support our business growth trajectory and maintain our quality sash window output.” The Roseview team had no hesitation in working with Haffner again either. Mike said: “We have a trusted partnership with Haffner based on cooperation and support. There was no reason to go anywhere else.” The SBA-4 VS PVC-U Profile Machining Centre is driven by technical innovation and highperformance accuracy, which makes it ideal for manufacturing both standard and mechanically jointed vertical sliders. For a company such as Roseview, which is renowned for the quality of its product and the efficiency of its operations, it is the perfect choice. Like all Roseview’s fabrication machines, the new SBA-4 VS PVC-U Profile Machining Centre has been given a name to make it easy to identify in production meetings. Mike commented: “We name all our machines after Nintendo characters. The first machine we purchased from Haffner is called Bowser. This new one is Yoshi. We also have a Mario, Luigi and Super Mario.” Serving the trade market, Roseview Windows was established in 1977 and has grown year-on-year. In 1985 it was the first company in the UK to specialise in manufacturing PVC-U vertical sliders. Based in Buckinghamshire, the company currently manufactures around 700 windows a week, with plans in place to increase output to 1,000 windows per week. With the arrival of Yoshi, or its second SBA-4 VS PVC-U Profile Machining Centre, it is well equipped to achieve this.
SAVE TIME WITH HAFFNER
Leading machinery innovators, Haffner Ltd has reported an increase in demand for their KT Assembly tables which are helping fabricators improve their efficiencies and delivering some impressive time savings too. Matt Thomas, Managing Director of Haffner, explains: “We know that automated machines provide the ability to achieve more output with less skilled manpower, which means they are a powerful way for fabricators to adapt to the current worker shortage in addition to increasing their output. But their timesaving properties cannot be overlooked as confirmed by two major industry fabricators who recently purchased our KT Assembly Tables.”
On first glance, the assembly tables are able to transform the speed of manufacture with minimal skilled manpower, but they can deliver a lot more. Matt said: “One fabricator confirmed that the automated door table can prep three hinges on a door in under 3 minutes. This has saved them around 40 minutes on each set of French Doors. They also confirmed that their new tilt and turn table will prep a tilt and turn sash in under 4 minutes too which has dramatically improved the speed of their output. Just as important is that the machines are fully automated, so they do not need to be operated by a skilled operator.” Even more impressive is the fabricator confirmed that the tables had saved the time of around four people, which is hugely beneficial for fabricators struggling to find skilled labour.
The KT Assembly Tables are designed for use on single and tilt-andturn window systems and door sashes of various dimensions. The intelligently designed machines optimise sash assembly by combining several processes at one table. And by taking these operations off a conventional machining centre means you will further increase the output of your existing machines too.
They have triple drilling for handles and milling for the espagnolette channel with easy positioning of the tools. There is a punch unit for cropping the single or tilt-and-turn espagnolettes, as well as scissor hinges, which is all done according to sash dimension and without requiring measuring. Hinge holes are also drilled automatically without an operative needing to measure for the location. The automatic screwing unit includes height adjustment for espagnolette and scissor hinges. The accuracy is far superior to traditional methods of a tape measure and jig too. CNC positioning of the frame and sash ensures all hinges are in the correct place, leaving little adjustment on the finished door. This unique measurement system allows for tolerances in welded frames and also reduces the time needed to check and adjust each door on the bench which further improves production output. Matt concluded: “We have always highlighted the benefits of automation across our various PVC-U and aluminium fabrication machines. Those benefits haven’t changed – but in the current market they’ve become even more central to fabricators’ success. So, if you’re looking for a solution to your current worker shortages, improve your output and save considerable time, our machines are the tried and tested solutions you need”. Tel: 01785 222421 www.haffnerltd.com
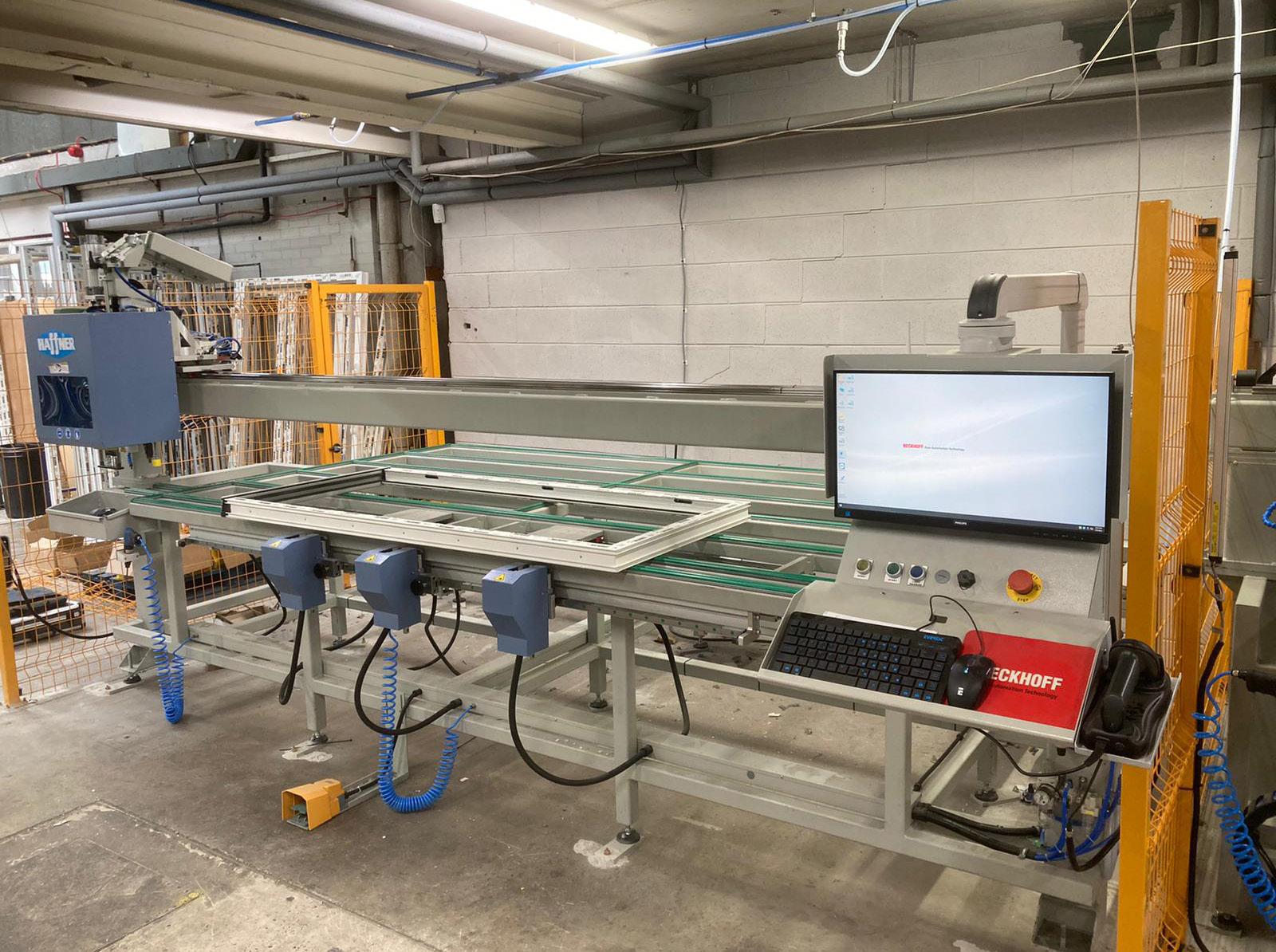