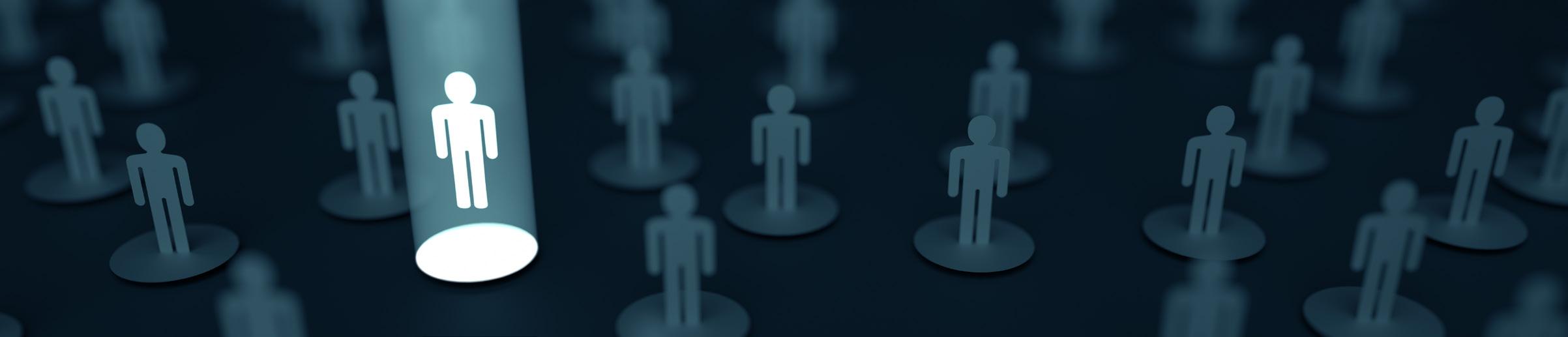
28 minute read
MEMBER SPOTLIGHT
from Pemac 2020
PEMAC Member Spotlight
By Hammad Sharif, MMP, CAMA
Hammad was born and raised in the City of Hyderabad located in Pakistan, where he finished his undergraduate degree in mechanical engineering. After 1 year with a local mining company in Pakistan, Hammad got a job working on middle-east opera¬tions through the Cairo Technical Center with the Canadian company, Lafarge Cement. Through his work with Lafarge, Hammad got a good grounding in maintenance and reli¬ability as well as a background in international engineering standards and practices. Given his developing career with a Canadian company, Hammad applied for permanent residency in Canada. Soon after being approved he accepted a position with Lafarge in British Columbia.
Shortly after arriving in Canada in 2010 the position he had taken this big risk for was ‘downsized’ due to a corporate merger. As Hammad says, “I lost my anchor point. I actively began strategizing, seeking ways and methods of finding new work so that I could continue my professional career in Canada. This is when I found PEMAC and connected with Norm Clegg [PEMAC’s 2nd Executive Director]. Norm was very kind by providing me an opportunity to volunteer so that I could meet people. He also encouraged me to enroll in the MMP program. Hammad could already boast international experi¬ence and applied knowledge of maintenance and reliability with Canadian companies, but he still saw the Maintenance Management Professional (MMP) program as a way to net-work and to get attention in the Canadian market for his skills and abilities. He took the step of enrolling in Course 1 and also applied for prior learning recognition for 3 of the subsequent courses in the program.
“Even that first module was a good jump-start for me to get familiarized with the Canadian context. Right after that I got an offer from Holcim Canada. After just a 3 month pause I was back in a maintenance and reliability role again. I am grateful for that pause because it gave me the opportunity to recognize the value of networking and to gain local creden¬tials. Later when I applied for a Reliability Engineer role with my current company, BHP, I think it helped to put me on the top of the short-list. I joined BHP in 2012 and continued my MMP studies with very good support from my supervisor until I finished in 2015.
PEMAC has helped me to connect with a lot of good people in Canadian industry. I attend MainTrain whenever possible, participating as both a delegate and a presenter, sharing what I have learned about embedding reliability in design. MainTrain provides a great opportunity to do benchmarking and to keep up to date with emerging technologies and trends. It’s good to learn from other industries represented there as well. There are different good things happening in every indus¬try in maintenance and reliability.”
In the role Hammad holds now, the higher-level Asset Management principles really come into play which is why he pursued the CAMA certification. “Actually, Asset Management was always my area of interest. During my undergraduate stud¬ies I did part-time work for Markus Evans events in Pakistan. They had a call center staffed by people with good English who could pitch conferences to the target attendees. They had a conference about Asset Management that they sold to execu¬tives. I was totally unfamiliar with Asset Management at the time but learning about the content of that conference so that I could sell it gave me a lot of insight and exposure to what it is, what the elements are, and what the benefits are. That always excited me. It’s a really cool thing to think about that now.
“Back in early 2000s Asset Management was generally considered as a theoretical concept but not very feasible to apply practically. But I always saw how it applied in practice from the ground up. I have persevered and put asset manage¬ment elements into practice associated with the design, operations and maintenance phases of lifecycle in every role, every step along the way e.g. fit for purpose equipment selection, data management, and appropriate maintenance strategy deploy¬ment. It is all important and it is necessary to integrate asset management concepts from the bottom-up. It is all relevant to addressing risk for the organization.
Hammad fully appreciates how much PEMAC and the MMP program helped him as a newcomer to translate his prior knowledge and experience into a rewarding career in Canada. It’s clear that his long-held interest in the principles and benefits of asset management, his orientation to continuous improvement and his proactive orientation to life have played a big role. With respect to his career Hammad has exemplified the PEMAC motto of “connect, learn, contribute”. He now holds a corporate role, “Principal Reliability Engineer” at BHP as well as an acting position, “Manager of Strategy and Planning” with an asset portfolio of greater than one billion dollars! Hammad lives in Saskatoon, Saskatchewan with his wife and two small children.
Powerhouse Steam Trap Maintenance Program
By Mimi Wilde
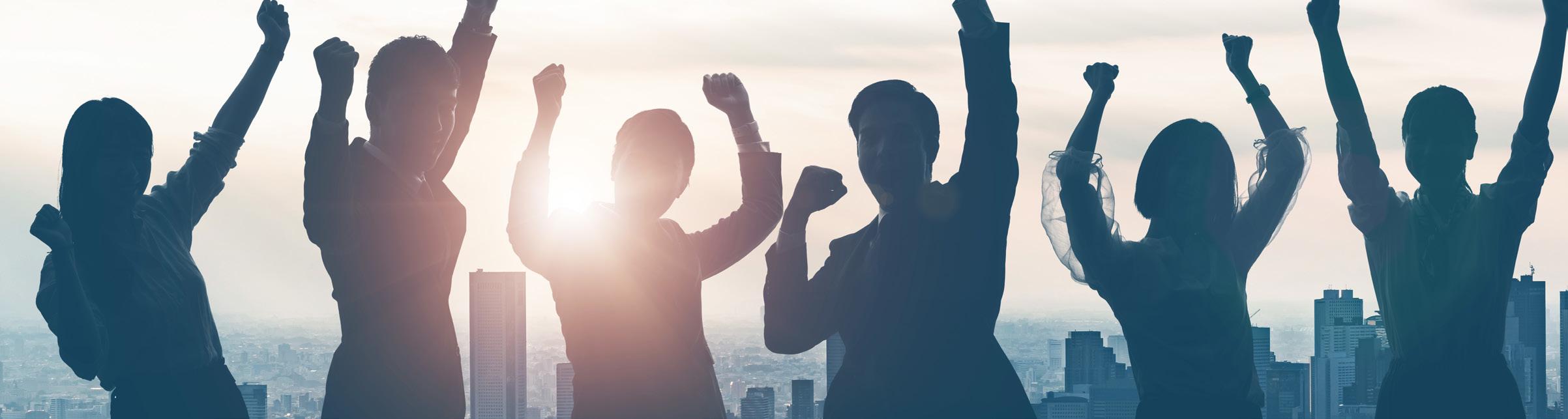
PEMAC’s Maintenance Management Professionals (MMP) have the education and applied skills to establish and sustain Asset Management for a broad range of operations. The Capstone project is the culmination of eight post-secondary level courses focused on developing maintenance management skills. PEMAC recognizes the top graduate business cases submitted by MMP Capstone participants from post-secondary institutions across Canada with two awards - MMP Capstone Award Technical Focus and MMP Capstone Award Business Process Focus.
The 2019 Awards winner for the MMP Capstone Award Technical Focus is Mimi Wilde, New Product and Services Development Specialist at Canadian Nuclear Laboratories located in Chalk River Ontario. Mimi’s project, Powerhouse Steam Trap Maintenance, exemplifies the value that can be derived from taking a fresh look at the maintenance program for a organization. Mimi’s project involved reviewing the existing preventive maintenance program, identifying which failure modes were not being addressed by it, suggesting improvements in both the condition-based monitoring technology used and the frequency of the tasks. Overall, this project aimed to improve the reliability of a critical utility system component asset, save her employer $, and engage the technicians in using technology already on hand for detecting failure in equipment. A thorough and well thought out business case.
Congratulations to Mimi Wilde! - MMP Capstone Instructor, Susan Lubell
Mimi Wilde
The Powerhouse is a support facility which provides utilities for a research laboratory located near Ottawa, Ontario. The Powerhouse delivers compressed air (for process requirements, and breathing air), water (for washrooms, fire protection, process cooling, etc.), and steam (for heating, process requirements, and sterilization) to the rest of the site, approximately 250 buildings. The Powerhouse was built in the 1950s, and was added on in the 1960s.
The Powerhouse is staffed 24 hours, 365 days a year. Each twelve-hour shift is manned by two operators (boiler operator and pump operator), and a shift supervisory engineer. In addition, two day-time maintenance staff are dedicated to the Powerhouse, with additional trades available for support for specific work requests.
Powerhouse Steam System
There are currently five operational boilers to produce steam for the site, three are natural gas while two are Bunker-C with propane back-up. Generally, one boiler is operated during the summer when demand is ~10,000 lb steam/hour, and two boilers are operated in the winter when demand rises significantly to ~100,000 lb steam/hour. The system temperature and pressure are 370°F and 105 psig, respectively.
The steam system has a requirement of fewer than three unplanned drops in pressure per year due to the many systems across site which rely on steam; there are two planned outages per year lasting one week each.
Within the Powerhouse, there are also systems which rely on steam such as turbine powered back-up for pumps in the event of
a loss of electrical power. Between these systems and the steam production system itself (chemical addition, deaerator, etc.) there are approximately 200 steam traps installed in the Powerhouse.
Opportunity
As part of the implementation of a new Equipment Reliability (ER) program, preventive maintenance (PMs) were evaluated to determine if the correct maintenance was being performed, at the most optimal frequency; this included reviewing previous year’s PMs to identify recurring issues. An annual PM on the Powerhouse steam traps was identified as an area for improvement; my MMP Capstone project “Powerhouse Steam Trap Maintenance Program” focused on the opportunity found as part of this PM review, to improve on the maintenance program for the steam traps.
The existing PM consisted of a visual check of the steam traps by one of the Powerhouse dedicated maintenance staff. Previous year’s results had the following issues: • The list of steam traps used to perform the PM was incorrect (steam traps which were no longer in service were on the list, and steam traps installed since 2015 were not on the list); • Steam traps which were identified as “Blowing” (i.e. leakage-failed) or “Blocked” (i.e. drainage-failed) appeared with the same status year over year, indicating that the traps were not replaced upon identifying the failure (impacts of failed steam traps are identified below); • The PM did not provide instructions for follow-up steps to be taken if a trap is found failed or no longer in service; • Frequent comment of “Undetermined” indicated that the visual inspection was inconclusive (up to 20 instances per
PM); and • Order of steam trap list did not allow for optimal execution of the PM (i.e. the steam traps were not grouped logically by location in order to facilitate quick identification), resulting in wasted time spent moving around the six floors of the Powerhouse.
Addressing each of these items was described in detail as part of the Capstone project. Steam traps can fail through two general modes: leakage, in which the trap continues to perform its job of removing condensate, but leaks steam; and drainage/blocked, in which the flow of condensate is blocked, preventing the removal or drainage of condensate from the system [1].
Leakage-failed steam traps can result in the pressurization of the condensate return system and in wasted energy (loss of steam for performing functional needs) which needlessly increases emissions of greenhouse gases and other pollutants. Therefore, leaking steam traps result in system inefficiencies, though they do still perform their basic task.
Drainage-failed steam traps (cold traps) can result in consequences ranging from equipment damage to personnel injury to plant shutdown due to: • Pipeline detachment from supports • Frequent steam line leaks due to water
hammer of valve packings, fittings, or erosion of pipe elbows • Atomization or process problems caused by the injection of wet steam • High operating costs due to excessive steam leaks and wasted condensate • Turbine failures • Burns from leaking steam
For these reasons, correctly identifying steam traps which have failed and quickly repairing or replacing them is critical for cost, efficiency, maintenance,
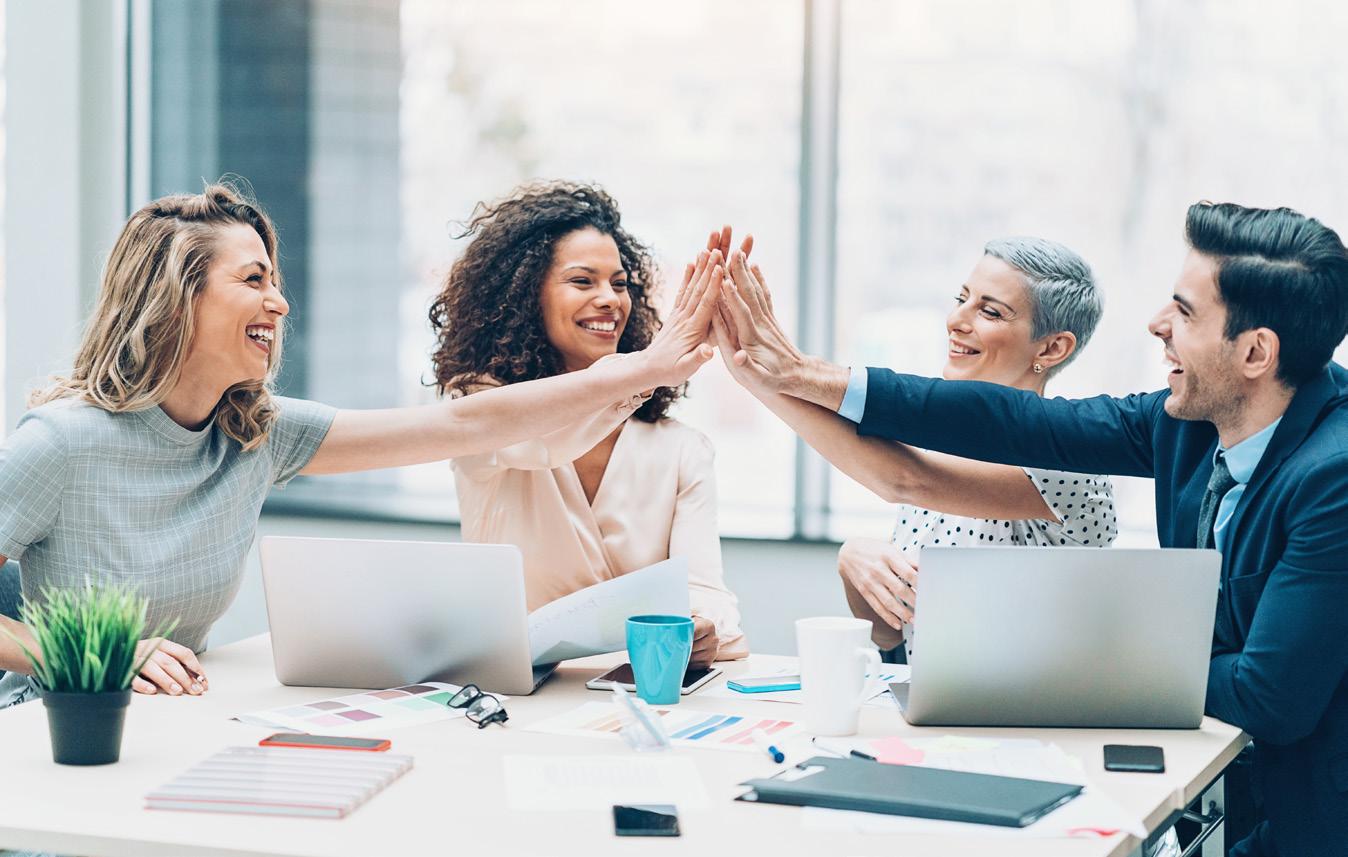
Impact of Failed Steam Traps
and safety sake.
Plan
The plan to improve upon the existing steam trap maintenance program focused on four main areas: • Technology: improving accuracy of diagnosis by implementing industry best practice of both thermography and ultrasonic technology for testing, including training of staff on new technology; • PM Details: updating the steam trap list to ensure all traps in operation are tested, optimizing frequency so that failed traps are identified in a reasonable time frame, and providing an efficient order of testing to avoid wasted man-hours; • Documentation: providing instruction on how to update steam trap list, initiate replacement of failed traps (open new work request), and provide written guidance on how to use the new technology; and • Resources and Engagement: mindset
shift to prioritize the replacement of failed traps in a timely manner, including providing resources to execute the improved PM and to initiate the replacement of failed traps.
Schedule
The schedule for implementation of the changes followed the site required gating and sanctioning process, in which management approval is required to proceed to the next activity. The schedule assumed approval to proceed at each gate, did not account for scheduling conflicts (i.e. delays in gate meetings), and assumed training availability. Assuming this “best case” scheduling scenario, the whole project was anticipated to take 17 weeks.
Costs
Since the project was in the “Identification” stage at the time of the Capstone, some assumptions were made in relation to the costs and PM frequency: • Costs associated with a failed trap: $800 annually per trap [1], 16 per cent failure rate; • Costs associated with replacement of a failed trap: $400 per trap [2]; • Costs associated with misdiagnosis $600 per trap [2], ~10 per cent per year; and • Optimal frequency assumed as quarterly (every three-months), to be further refined.
While the first-year costs to implement the described changes were significant (training, equipment purchases, updating procedures, etc.), a savings of nearly 68 per cent compared to the status quo was projected by the end of the 6th year, with a payback period of 15 months. A significant partition of the savings is as a result energy savings from replacing steam traps in a timely manner.
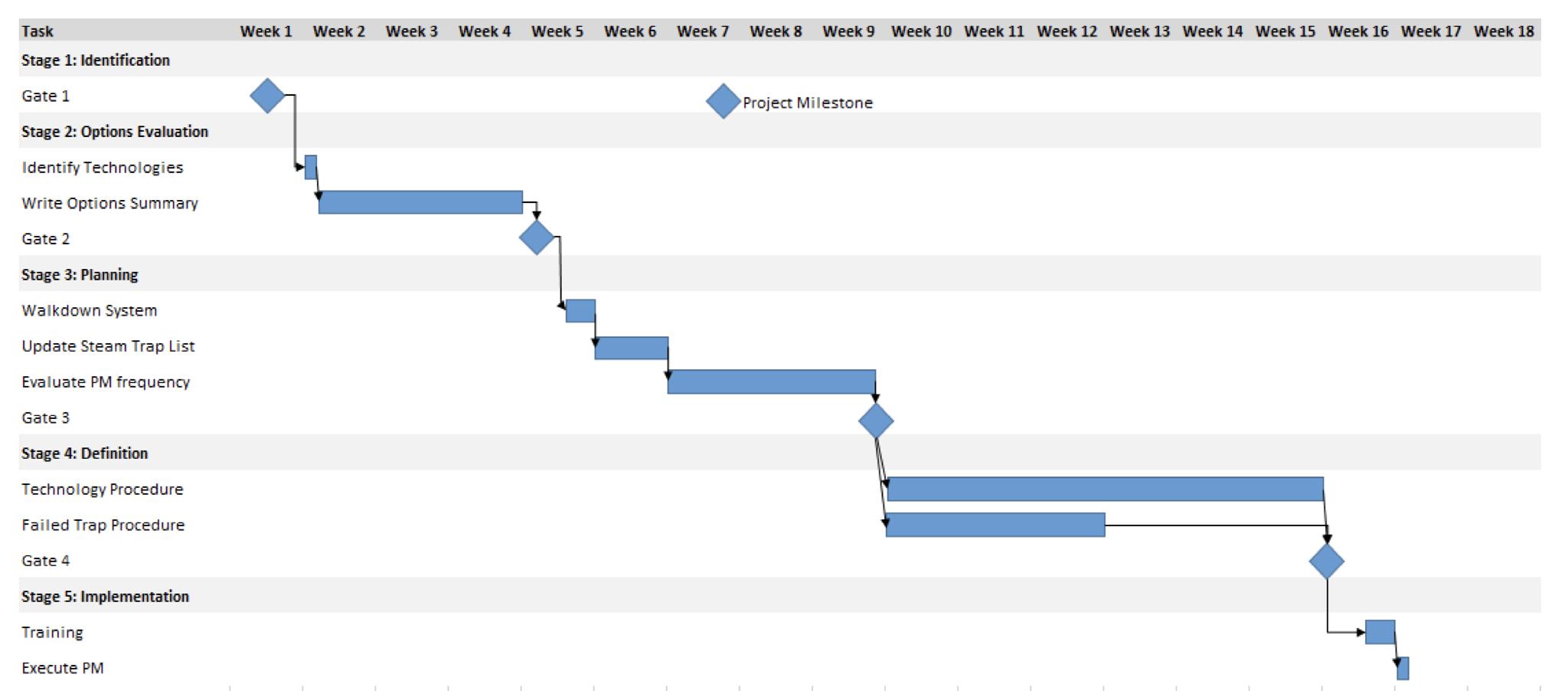
Identifying Success
In the short term, it was identified that the number of “undetermined” results should reduce from the baseline of 10 per cent to a target of one per cent in the first year. In addition, the number of steam traps identified as “blowing” or “blocked” on two or more consecutive PMs should be reduced. If that is not the case, this could be an indication that a process issue is causing premature failure of the trap, or that there are insufficient resources to execute the replacements, which would need management resolution. Both of these could be identified by reviewing the PM results the year after implementation.
In the long term, as a result of improved condensate discharging (from replacement of failed traps), boiler makeup feedwater chemical costs should reduce over time, as well as equipment and piping failures where the root cause is waterhammer or corrosion due to carbonic acid formation. Note that costs of these failures were not included in the cost evaluation.
In addition, this steam trap maintenance program could be used as a proof of concept to be implemented across the site steam system, resulting in even more cost savings.
Implementation
While the site is making significant improvements by upgrading/building new facilities and implementing improved maintenance programs, the focus at the Powerhouse in the past few years has been on upgrading other aspects of the steam system, including the boiler fuel system upgrades. This has meant that the steam trap maintenance program as presented in my Capstone report has been on hold while resources are focused on these other value-add tasks.
Having said that, the Powerhouse has implemented some aspects of the proposed plan separately including: • Reviewing the equipment list for accuracy; • Creating an ultrasound analysis program for bearing lubrication and early bearing failure detection, which could easily evolve to include steam traps since the staff are trained and familiar with the technology; and • Using infrared thermography for electrical PMs (across site), which could also transition to using this technology for steam trap maintenance.
References 1 Beware of the Dangers of Cold Traps,
Chemical Engineering Progress, pg 50-53, 2013 February 2 Implement a Sustainable Steam-Trap
Management Program, Chemical
Engineering Progress, pg 43-49, 2014
January
Asset Management for a Company
By Mark Boomer
When Mark presented his Capstone project, it was clear that he had looked at his organization through the holistic asset management lens. He provided the bigger business picture for the organization and then focused in on the critical assets that would provide value in achieving the strategic objectives. Mark made the connections that are necessary for good asset management and, if they could be improved upon, he suggested how that might be achieved. I’m sure that if his employer uses Mark’s project and suggestions as a template for moving forward, they will move quickly along the path to effective Asset Management.

Introduction by the instructor, Cliff Willliams.
Hello, my name is Mark Boomer and I want to start with my history and journey to completing my CAMP (Certified Asset M a n a g e m e n t Program) and Capstone project.
I currently live in Fort Nelson and I started work for Westcoast Energy at the local gas plant as a Maintenance Planner in 2000. I always had an interest in facility Maintenance and how we could plan and execute activities cost effectively and always learn from the past jobs to do things better in the future. In 2016 our company name was Spectra Energy and I was first introduced PEMAC and began the CAMP program. I worked though Humber College to complete all the courses with a number of excellent instructors. I was fascinated to study ISO standards and excited to learn how other companies adopted a SAMP (Strategic Asset Managing Plan). Instead of me putting into practice improvements that I learned in my company, I could learn best practices from other companies all over the world. In 2017 Spectra Energy joined a larger company and we became Enbridge. Lastly Enbridge sold the gathering and processing facilities to a brand new Canadian investment company Brookfield and called it NorthRiver Midstream Inc. The EAM (Enterprise Asset Management) Leadership team for this new company gave us the limitless opportunity to contribute to its SAMP and Asset Maintenance Management. This motivated me to create a Capstone that incorporated everything I learnt throughout my CAMP and experience of 4 predecessor companies over the last 20 years.
In my Capstone the first thing I did was to ensure it was holistic and included everything I have learnt over the previous CAMP program. Next I focused on what are the most critical parts of a Maintenance Strategy and the aspects that I felt needed the most attention. The content of my Capstone focused on the four most important aspects that my organization needed, which are:
Critical Assets, Organizational Alignment, SAMP, and knowing how to operate assets for value.
The first aspect is in knowing your critical assets and how they contribute to the strategic objectives. Our critical asses are: Gas Processing Facilities; Gas Processing Facilities; Facility and
Field Employees; Central Leadership and Support Services Employees; and Corporate Leadership Team and Business Sustainability Employees. Gas Processing Facilities are physical assets of pumps, processing systems and equipment. The strategic objectives of these critical assets are to remove any contaminates and process natural gas for public use based on the customers’ expectations and needs. The commodity is then transported via pipelines to hubs where it is transported and sold. Facility and field employees are human assets that operate and maintain the pipeline and facility assets. The strategic objectives of these critical assets ensure qualified and competent individuals are available and capable of managing the facility and field assets. Central leadership and support services employees are human assets that field employees report to and their specialized industry support advisors. The strategic objectives of these critical assets provide leadership and support to field employees so that they are efficient and effective. Corporate leadership team and business sustainability employees are human assets that set the expectations and direction of the corporation. Each corporate business unit reports into this group in Houston. The strategic objectives of these critical assets provide corporate sustainability, determine the strategic goals and direction the corporation will take as shareholders expect.
The second aspect I focussed on was alignment within the organization and set up the framework for success. Alignment has to set up from the top to the front line. I learned in “Good to Great” that all organization could develop a strategy at the top level, however great companies can implement strategies throughout. This is probably the hardest part as you need engagement and alignment from all the different departments within the organization and they all don’t understand how they contribute.
The SAMP was the third aspect of my Capstone and it is really the foundation. Strategic Asset Management Plan: Defines the organization’s strategic approach to asset management; Aligns asset objectives with the business objectives; ensures assets are managed for value to optimize the total cost of ownership; Provides a common framework for

the organization to develop and execute asset management plans (includes maintenance strategy/plans).
The fourth Capstone aspect I focussed on was the operation of assets for value through maintenance management. You have to ask yourself , “Are the current maintenance activities actually delivering what the organization needs?” The maintenance activities must support the strategy. Recognize where you are in you journey and how do we get to the next level of maintenance.
In summary the goal of my Capstone was to drive organizational alignment in asset management to realize value and balance risk, cost and performance. The next steps from here follow the PDCA Improvement cycle: • Create a “Center of Excellence” team to develop and agree on an asset strategy • Draft an Asset Management Policy,
SAMP, for senior level approval • Develop Asset Plans to deliver the strategy • Ensure transitional activities (ERP, Org structure, capability, systems) support the long term Asset Management goals • Monitor and review the progress to ensure results. (Plan → Do → Check →
Act)
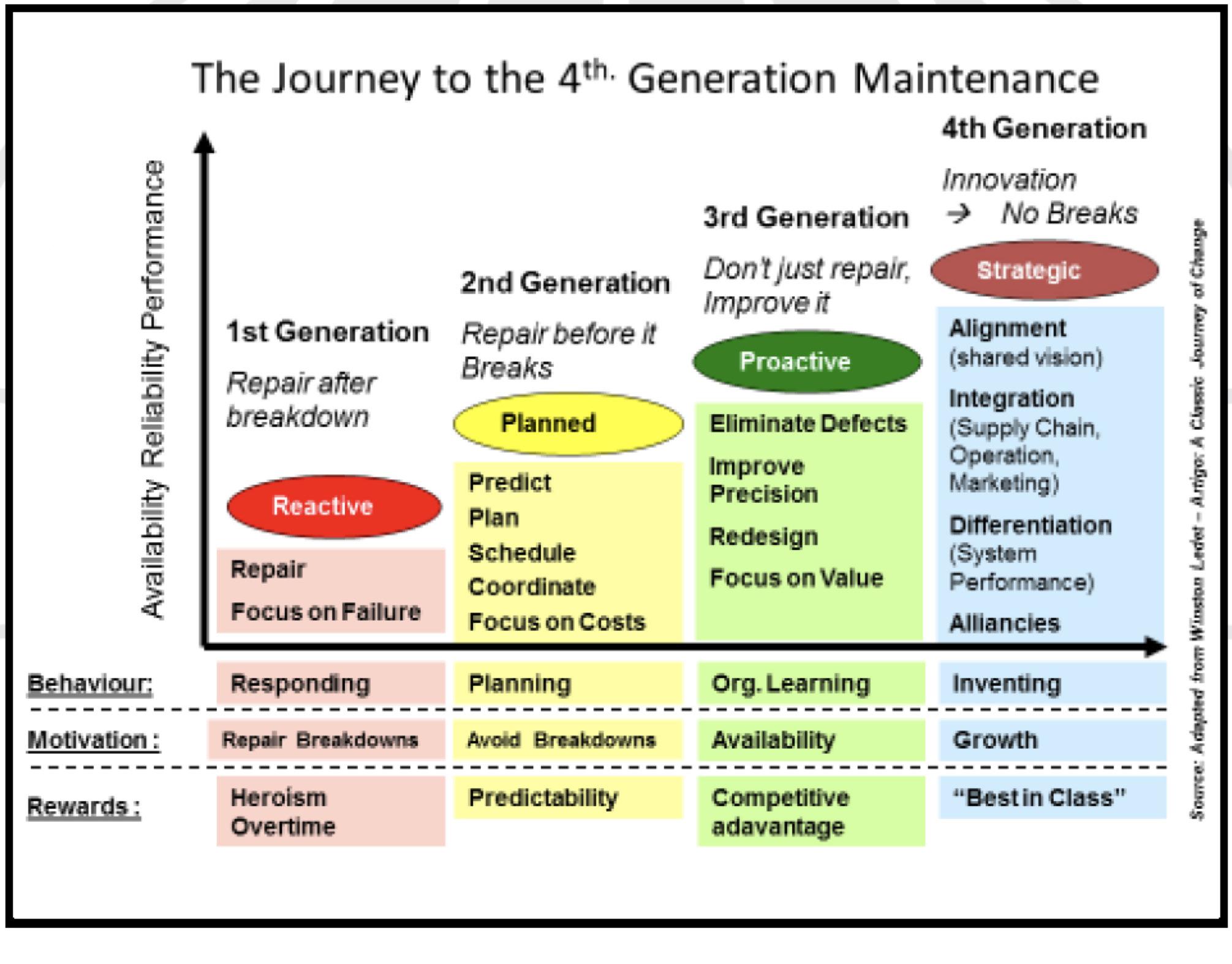

Change Management – That’s Easy! Cliff Williams, MMP, CAMP
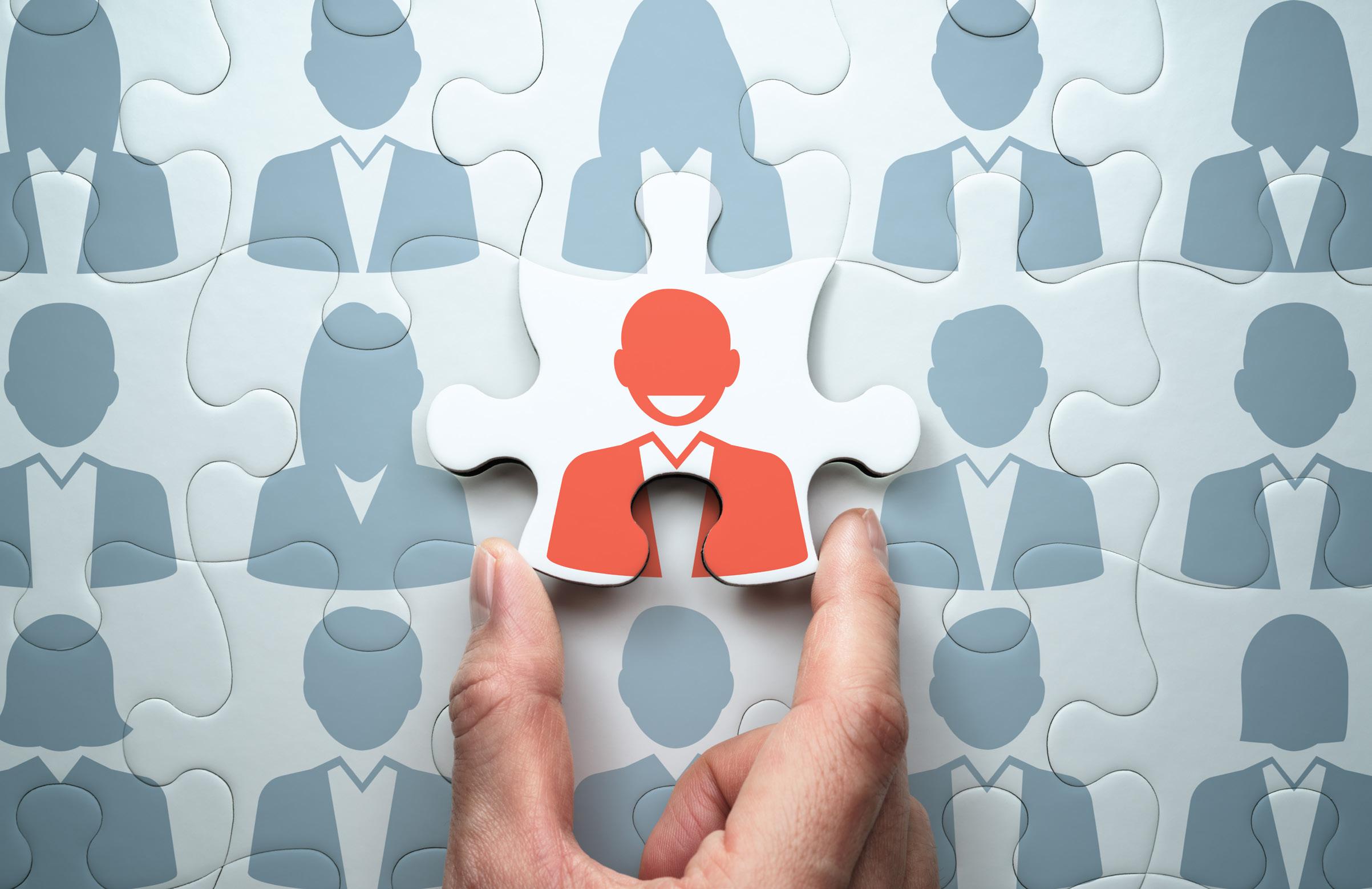
Recently I was facilitating a leadership seminar with a group of maintenance and reliability leaders. Everyone had finally agreed that, to improve performance there had to be change, because as Albert Einstein said, “If you do the same things every day and expect different results then that’s the definition of insanity!’ This led us to a discussion around perhaps the most maligned and forgotten management tool available – Change Management. We had an interesting discussion that got a little heated when I suggested that change was really easy – you simply stop doing one thing and start doing another. The group was a little puzzled as to why I would bring up the topic as being much maligned and then tell them it was easy. That was until I explained that the difficult part of Change Management is the transition of behaviours from the old way to the new way – getting the transition, and so the behaviours you want, is the challenge. I used a work order as an example of what I was saying – if the goal is to change from paper work orders to electronic work orders – the change is fairly simple – you stop using paper work orders! The transition may not be so easy – when you used paper work orders, the tradespeople would give great feedback and suggestions on the work order and allowed for continuous improvement, but after the change to electronic all you get is What needs to happen is that you enable, encourage and support the early adopters – all the while ensuring that their exuberance doesn’t get to be considered ‘over the top’ by the fence sitters.
‘complete’ on the bottom of the form. Is that the behavior that you wanted? If not, what went wrong? We talked about the many reasons why the transition didn’t turn out the way we wanted and suggested that things like ageing workforce who didn’t have confidence with computers, people not understanding the benefit of the new system or not being part of the development of the new system might have come into play.
This led us to talk about what is required to make the transition successful and I went over the factors such as explaining the need, educating how it will happen, engaging the group in developing the change and empowering them to do so. It was at the empowering point that the question that prompted this article was raised – ‘What do you do about the immovable objects – you know, the guys who just don’t want to change?” There was some consternation when I suggested ‘Nothing or very little’ – so I explained that in most changes you are going to have three different groups of individuals. • The first is the early adopters – the ones who want to run with the change, are enthusiastic and don’t mind taking the risk • The second are the fence sitters who really want to see how things pan out before they
come down off the fence and this group has a wide range from firmly entrenched on the fence to will fall off at the slightest touch. • Third are those immovable objects – they just don’t want to budge, throw roadblocks in the way constantly state ‘it will never work’ or ‘they’ll never do that’ when talking about what is necessary for the change.
The break out is usually in the 20 per cent - 60 per cent - 20 per cent range although this varies based on the culture and the skills of the ‘Change Manager’.
So why did I say do nothing or very little? Quite simply if your focus is the 20 per cent immovable objects then the 20 per cent adopters will get frustrated and start to wane and the more numerous (and so more important) 60 per cent fence sitters are going to hear the immovables’ comments more and more and they will start to give them credence.
What needs to happen is that you enable, encourage and support the early adopters – all the while ensuring that their exuberance doesn’t get to be considered ‘over the top’ by the fence sitters. This way the fence sitters will see that you are committed to the change, that you are leading the change and you will help them with the change. Remember it’s the fear of the unknown that causes the fence sitters to stay on the fence. The 60 per cent represent the critical mass that will allow the change or transition to be successful – without them you will find yourself in the all too familiar situation where things are worse after the change than they were before the change.
Now I did say, “do nothing or very little with

the immovables” but I went on to explain to the group that there really is one thing that you must do for them and that is – listen to them. Much can be gained when you listen to their complaints and even more if you can figure out the real reasons behind the complaints. If they say that ‘they’ll never do it’ go out of your way to do it – by enabling the adopters you will nullify the ‘it will never work’ by showing them that it will. One of my favourite tactics involved purchases – when the change involved new tools or in the case of work orders – computers - and the immovables loudly state that you will never get them, I have gone out of my way to ensure that whoever is sponsoring the change understands how critical these purchases are to the success of the change. It only takes two or three incidents of proving the immovables wrong in what they say before the fence starts to lean towards acceptance. So in essence you are not really doing that much with or about the immovables but you are moving the change and transition forward.
I mentioned earlier that it’s good if you can figure out the reasons behind the stance of the immovables – they may not be the same for each individual. This is crucial because when you have made enough progress and gained enough momentum, you want to go back and, off at the side, figure out how you can move the immovables. But that’s a whole other article!
2019 Maintenance Team of the Year
Edmonton Airports

Edmonton Airports was the winner of the PEMAC 2019 Maintenance Team of the Year Award for a large organization (>150 employees). The team was officially acknowledged at PEMAC’s Annual Awards Banquet on September 18, 2019 at Fort Edmonton Park.
“It has been quite the journey so far. The opportunity to submit for this award made us pause, and take a look back at where we were compared to where we are today, and celebrate that accomplishment,” says Nick Jensen, Director of Asset Management, Edmonton International Airport Maintenance Team.
In order to be considered for the Maintenance Team of the Year Award, an application must be submitted by a hopeful team. The application includes the back-story of an improvement effort as well as a self-assessment against a “Maintenance Maturity Grid”. These
applications are reviewed and ranked by the committee members. Based on the ranking, visits are carried out by PEMAC representatives to confirm whether the self-assessment was accurate.
The winners of the award this year, Edmonton Airports Maintenance Team, became involved with PEMAC in early 2019 when two employees enrolled in PEMAC’s Asset Management Professional (AMP) program. Another staff member had previously completed the PEMAC Maintenance Management Professional (MMP) program.
The team felt ready to submit an application for the Maintenance Team of the Year Award primarily due to their achievements in two categories. They have: 1. Initiated work on a maintenance improvement plan which is on schedule 2. Reorganised for effectiveness and efficiency
“We have an integrated maintenance management system with a clear line of sight to the performance, cost and resourcing requirements for all of Edmonton Airports infrastructure assets. Our people are engaged and have the information at hand to make informed decisions,” says Nick.
In early 2016, Edmonton Airports initiated a new Computerized Maintenance Management System (CMMS) project – DAXeam, which was finished in August 2017.
As part of their Core Business Systems Replacement (CBSR) plan, they replaced outdated financial and asset management systems with integrated systems, improving efficiencies in time, financials, and effort.
After a gap analysis of each functional area in March 2018, they determined that implementing a planning and scheduling team would have the most impactful result. Prior to Project DAXeam, maintenance work that was found was not prioritised and was worked on as soon as it was identified.
“Today we have a dedicated planning and scheduling team that has implemented an annual Preventive Maintenance (PM) plan, 28 day schedule forecast, 7 day schedule review and firming, and a daily observation review meeting,” says Nick.
Following this analysis, they prioritised and executed an improvement initiative, with a projected end date of December 2019.
Additionally, Edmonton Airports combined their two largest employee groups, Operations and Infrastructure, in 2018. This better aligned the work of both teams with the overarching efficiency goals of the organisation.
Recently, Edmonton International Airports rolled out a mobile app for all their maintenance workers to allow them to record their observations in the field. The key features of the app are: • Ease of use • Realtime observations (work requests) entry • Electronic checklists with ability to add values and meter reads • Ability to provide work order feedback and progress notes • Offline capabilities
Left to right: PEMAC Awards committee member, Jim Reyes-Picknell. Then Edmonton Airports team: Nick Jenson, Peter Agnew, Gary Lamb, Dean Ervine. Far right: PEMAC Awards committee chair, Alan Cox.

At the time of their submission, one and a half years after installation, the results were: • Planned work orders increased -from 67 per cent - ` 73 per cent • Preventive Maintenance (PM)
Templates increased from 837 – 2,753 • PM program inspections increased from 9,100 – 29,904 • Assets being tracked increased 8,041 – 11,408 • Backlog work orders reduced 413 – 186 • Annual facilities maintenance spending reduced by $254,026, compared to the previous period.
Congruent with an award-winning team, Edmonton Airports is looking ahead to continued improvement, by achieving the measures of success established for the project from 2017 to 2020: • Reduce maintenance labor and material expenditures by 10 per cent • Improve the availability of equipment and system performance 10 per cent • Achieve a Planned versus Reactive
Maintenance activity ratio of 80/20
In the next five years Edmonton Airports maintenance team intends to focus on: • Materials management improvement project • Moving towards a reliability centred maintenance program • Utilising technology and IoT • Implement asset management framework • Implementing enhancements to our
GIS System • Development of Asset Management
Plans for critical asset classes
And over the next 10 years their work will contribute increasingly to: • Operational excellence • Digital transformation • Further asset management plan development
When asked how it has affected the team’s morale to be part of this journey Nick replied, “Maintenance work is planned days in advance, and employees know what to expect. The comment from the staff is that their day is not as chaotic as it once was. They are experiencing the power of the information, and are enhancing work plans.”
I want to thank the PEMAC organisation for the recognition of our team. As I look to the future, I see many more great accomplishments ahead for this team,” notes Nick on behalf of his team at Edmonton Airports.
To learn more about PEMAC Award winners visit www.pemac.org/awards.
Photos with captions: https://www. pemac.org/recognition/awards/2019- maintenance-team-year-large-organization