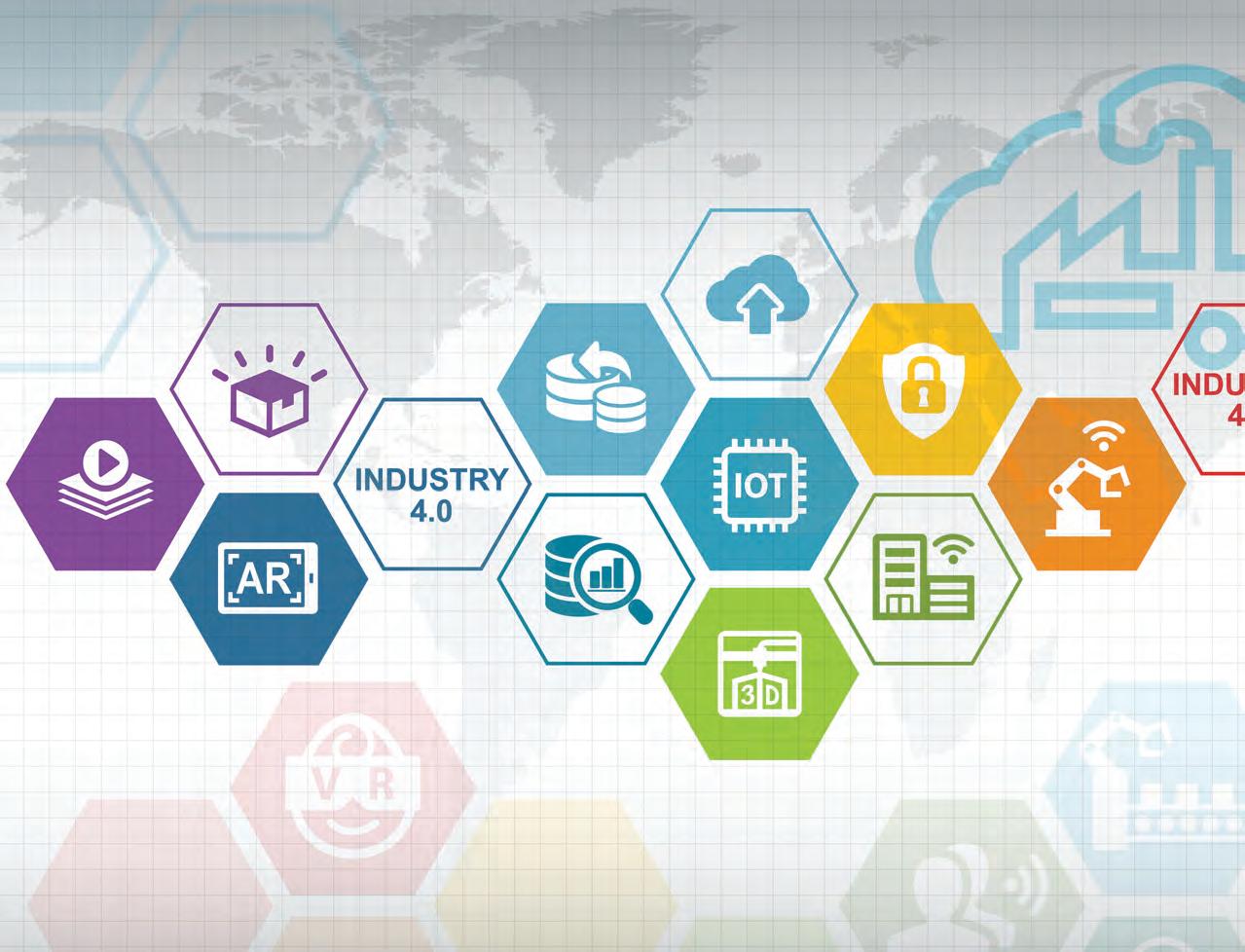
15 minute read
Maintenance 101
INDUSTRY 4.0 AND THE FUTURE OF MAINTENANCE
The future of maintenance departments and the way they perform their maintenance activities are changing quickly, and technology is taking them in a completely new direction. BY PETER PHILLIPS
Most of the people that read MRO magazine are on the front line of maintenance and have seen many great changes over the past number of years. COVID-19 has certainly changed the way we conduct our maintenance activities. There was a shortage of manpower with the virus spreading within the maintenance department and many facilities did not allow maintenance contractors on site due to COVID-19 protocols. This created a major labour hour shortage and caused facilities to fall further behind on planned maintenance activities that included preventive maintenance, plant outages, equipment repairs, maintenance trainings, and the list goes on as critical activities were canceled or postponed.
In general, this affected equipment reliability in a big way, and it made companies think about the future, and prompted corporations to look closely at their maintenance strategies; to looks critically at maintenance regimes and to seek solutions that can predict equipment reliability without totally depending on the human intervention of trades people.
Companies are turning to alternate ways to predict and perform maintenance for several reasons:
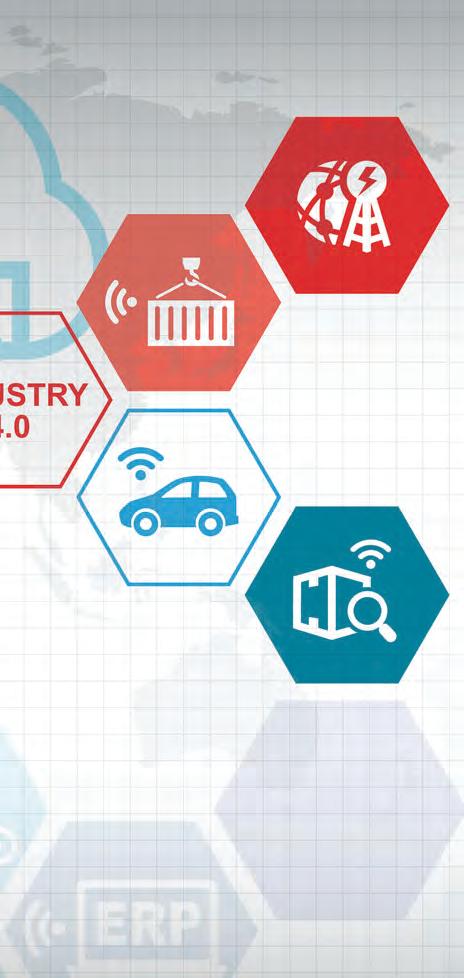
• The shortage of skilled labour through Canada and the U.S. is at unprecedented levels. North America has millions of job openings at this very moment, notably in the skilled trades. This shortfall is expected to continue for the next decade, as colleges and trade schools have fallen behind with the demand. • Technology is advancing quickly and is becoming more affordable for companies to implement. • Demand for products has risen sharply, companies need more reliable equipment, and there is less time available for equipment repair and unscheduled breakdowns.
Because of these factors over the next five years, most maintenance departments in large industrial manufacturing facilities are going to see a big change in how maintenance activities are triggered and executed. Preventive maintenance will be done based on equipment health that will be determined by technology instead of set maintenance frequencies. Right now, the vast majority of maintenance departments has twice as many hours of PMs to be completed than the number of maintenance hours they have available to complete them. In conjunction with the shortage of skilled tradespeople and maintenance departments who are fighting a losing battle.
Maintenance management at the corporate level see these factors and are aggressively looking for solutions to maintain the equipment in such a way that planned and scheduled maintenance activities are achieved on schedule.
How will this be achieved?
Maintenance monitoring is at the top of the list. As an example, real-time temperature and vibration monitoring technology is now available from a variety of vendors and at very affordable pricing. Variations in temperature and vibration is detected and reported as soon as they happen. Periodic vibration measurements and analysis of the data are being replaced with real-time sensors. Problems are detected immediately, and repairs can be scheduled well ahead of time. Many companies have applied thermal vibration sensors on every motor and gearbox on the production line. Historical preventive maintenance on these units barely exist as maintenance monitoring technology has replaced these labour-intensive activities where equipment needed to be shut down, guards removed, a visual inspection completed and then re-assembled.
Industry 4.0 technologies that include artificial intelligence and machine learning will further enhance the monitoring and predicting of equipment health. The integration of industrial systems and combined data from previously standalone systems will not only monitor and analyze equipment health, but it will also offer solutions to maintenance staff of what needs to be done to solve the issue. Industry 4.0 digital industry technology will transform the way we are currently doing things and allow us to work alongside the machine in new and highly productive ways.
In case you are not fully familiar with Industry 4.0 technologies, here is some additional information of how it integrates with maintenance and equipment.
Industry 4.0 is built on nine technology pillars. These innovations bridge the physical and digital worlds and make smart and autonomous systems possible. Businesses and supply chains already use some of these advanced technologies, but the full potential of Industry 4.0 comes to life when they’re used together.
1. Big data and AI analytics: In Industry 4.0, Big data is collected from a wide range of sources, from factory equipment and IoT devices, CMMS, equipment sensors, equipment and work order historians, etc. Analytics powered by artificial intelligence and machine learning are applied to the data in real time – and insights are leveraged to improve decision-making and automation in every area of equipment health and reliability. 2. Horizontal and vertical integration:
The backbone of Industry 4.0 is horizontal and vertical integration. With horizontal integration, processes are tightly integrated at the “field level” – on the production floor, across multiple production facilities, and across the entire supply chain. With vertical integration, all the layers of an organization are tied together – and data flows freely from the shop floor to the top floor and back down again. In other words, maintenance and production equipment and processes are tightly integrated
Industry 4.0 is built on nine technology pillars. These innovations bridge the physical and digital worlds and make smart and autonomous systems possible. Businesses and supply chains already use some of these advanced technologies, but the full potential of Industry 4.0 comes to life when they’re used together.
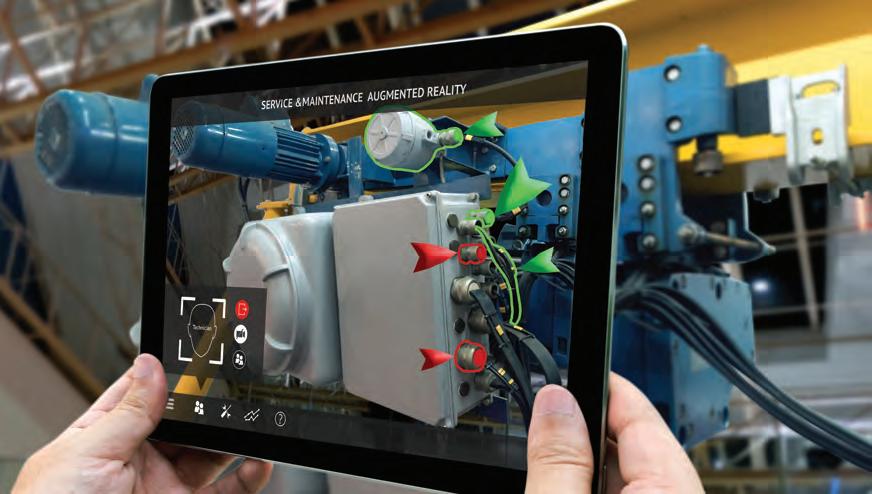
– and previously stand-alone data systems and knowledge silos are a thing of the past. 3. Cloud computing: Cloud computing is the “great enabler” of Industry 4.0 and digital transformation. Today’s cloud technology goes way beyond speed, scalability, storage, and cost efficiencies.
It provides the foundation for most advanced technologies – from AI and machine learning to the IoT, and gives businesses the means to innovate. The data that fuels Industry 4.0 technologies resides in the cloud, and the cyber-physical systems at the core of Industry 4.0 use the cloud to communicate and coordinate vital equipment data. 4. Augmented reality (AR): Augmented reality, which overlays digital content on a real environment, is a core concept of Industry 4.0. With an AR system, employees use smart glasses or mobile devices to visualize real-time IoT data, digitized parts, repair or assembly instructions, training content, and more when looking at a physical thing – like a piece of equipment or a product. AR is still emerging, but has major implications for maintenance, service, and quality assurance as well as technician training and safety. 5. Industrial Internet of Things (IIoT): The Internet of Things (IoT) – more specifically, the Industrial Internet of
Things – is so central to Industry 4.0 that the two terms are often used interchangeably. Most physical things in
Industry 4.0 – devices, robots, machinery, equipment, products – use sensors and RFID tags to provide real-time data about their condition, performance, or location. This technology lets companies run smoother, prevent equipment downtime, track spare part inventory, and much more. 6. Additive manufacturing/3D printing:
Additive manufacturing, or 3D printing, is another key technology driving Industry 4.0. 3D printing was initially used as a rapid prototyping tool, but it now offers a broader range of applications, from mass customization to distributed manufacturing. With 3D printing, for example, parts and products can be stored as design files in virtual inventories and printed on demand at the point of need – reducing both transportation distances and costs. 7. Autonomous robots: With Industry 4.0, a new generation of autonomous robots is emerging. Programmed to perform tasks with minimal human intervention, autonomous robots vary greatly in size and function, from inventory scanning drones to autonomous mobile robots for pick and place operations.
Equipped with cutting-edge software,
AI, sensors, and machine vision, these robots are capable of performing difficult and delicate tasks – and can recognize, analyze, and act on information they receive from their surroundings.
Crafts people will need to have specific knowledge and skills to maintain these complex machines. 8. Simulation/digital twins: A digital twin is a virtual simulation of a real-world machine, product, process, or system based on IoT sensor data. This core component of Industry 4.0 allows businesses to better understand, analyze, and improve the performance and maintenance of industrial systems and products. An asset operator, for example, can use a digital twin to identify a specific malfunctioning part, predict potential issues, and improve uptime. 9. Cybersecurity: With the increased connectivity and use of Big Data in
Industry 4.0, effective cybersecurity is paramount. By implementing a Zero
Trust architecture and technologies like machine learning and blockchain, companies can automate threat detection, prevention, and response – and minimize the risk of data breaches and production delays across their networks.
It can be easily concluded that the future of maintenance will be very high tech. Of course, there will still be a need for trades people to turn wrenches, change parts and repair equipment. However, knowing when that work needs to be done will often be prescribed by technology.
In the future, we will see fewer maintenance tradespeople in our departments, as historic ways of doing maintenance will be replaced with technology that provides the real-time condition of the equipment. Tradespeople will be highly trained to interpret and react to technology-based equipment monitoring. In reality, that will significantly change the way we do maintenance and it upon us, and we must learn and adapt starting now. MRO
Peter Phillips is the owner of Trailwalk Holdings Ltd., a Nova Scotia-based maintenance consulting and training company. Peter has over 40 years of industrial maintenance experience. He travels throughout North America working with maintenance departments and speaking at conferences. Reach him at 902798-3601 or peter@trailwalk.ca.
WHAT’S NEW IN PRODUCTS For more product news, visit www.mromagazine.com/products
WON linear bearings and rails
AutomationDirect WON linear bearings generate lower friction, which means less power is required to move a load, and higher speeds can be achieved. WON linear bearing blocks are available in a range of sizes. The H series offers four rows of continuously circulating ball bearings and comes in a flanged or rectangular form factor, and the M and MB series offer two rows and come in either a rectangular or long rectangular form factor. Linear rail in lengths up to 1000 millimetres and matches the series of bearing blocks that is selected. All bearing/ rail systems provide four-direction equal load sharing in any direction for lower friction and smooth motion.
www.automationdirect.com
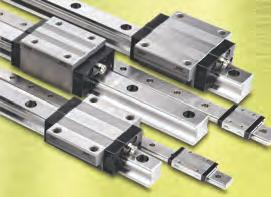
UHF RFID patient ID wristband
SATO UHF RFID direct thermal wristband for identification, verification and tracking of patients in hospitals. Designed for comfort and optimal reads within hospital location systems. The UHF RFID wristband and compact four-inch printer, the CT4-LX UHF, can be integrated into a complete ID and tracking system with third party readers and antennas. Readers can be positioned around the hospital so staff can be alerted immediately of any unexpected movement.
With a SATO AEP (application enabled printing) compatible printer, users can both encode wristbands and develop custom apps to streamline their work processes.
www.sato-global.com

Sandvik Coromant’s CoroCut QI grooving tools
Sandvik Coromant launched CoroCut QI, a range of internal and face grooving inserts designed for smaller diameters.
CoroCut QI provides a selection of tools for numerous parting and grooving applications, designed specifically for smaller diameters. All inserts fit both internal and face grooving tool holders.
CoroCut QI is divided into internal grooving and face grooving application areas, and is an upgrade of the T-max Q-Cut 151.3 program. The design allows for greater chip control, a 10 per cent productivity increase, and a 20 per cent improved tool life aided by tighter edge-rounding tolerances and internal coolant for both internal and face grooving tools.
Key features of the CoroCut QI include a tip seat angle for lighter cutting action and cutting forces that aid vibration-free machining, and a rail insert seat for a stable insert position.
The insert geometries include -GF, a ground sharp insert for internal grooving, -TF with direct pressed geometry for face grooving and internal grooving and turning, and -RM, for non-linear turning such as internal and face profiling.
www.sandvik.coromant.com
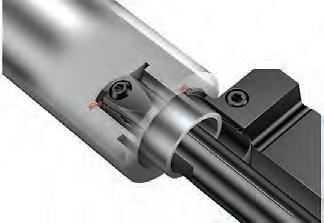
Teledyne FLIR Neutrino SX8 mid-wavelength infrared (MWIR) camera module and four Neutrino IS Series models designed for integrated solutions requiring HD MWIR imagery with size, weight, power, and cost (SWaP+C) constraints for commercial, industrial, defense OEMs, and system integrators. Based on Teledyne FLIR HOT FPA technology, the Neutrino SX8 offers 1280×1024 HD MWIR imagery for ruggedized products. The SX8 and the Neutrino IS series models are for integration with small gimbals, airframes, handheld devices, security cameras, targeting devices, and asset monitoring applications. Neutrino IS products include a Teledyne FLIR CZ lens integrated with a Neutrino SWaP Series camera module (VGA or SXGA).
www.flir.com
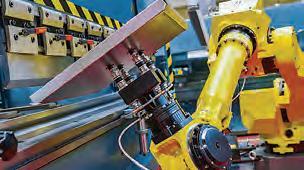
Tough Gun TT4A and TT4E reamers
Tregaskiss Tough Gun TT4A (analog) and TT4E (ethernet) reamers offer a.95HP motor and 236 pounds of lifting force at 95 psi. The cutter blades are resistant to breaking, chipping or cracking.
Features: durable valves and cylinders rated for 10M+ cycles and a wire cutter that can run 1M+ cycles without requiring maintenance. The reamers feature a motor that lasts up to 18M cycles at 80+ psi.
An anti-spatter reservoir with 20-ounce capacity reduces the need for frequent refills to improve productivity, while a low fluid level indicator sends an alert to the PLC/robot when anti-spatter solution is low. The reservoir includes a tethered cap and easy-clean filter to protect against anti-spatter contamination, which can also lead to weld quality issues.
www.tregaskiss.com

The Podcast for MRO Professionals
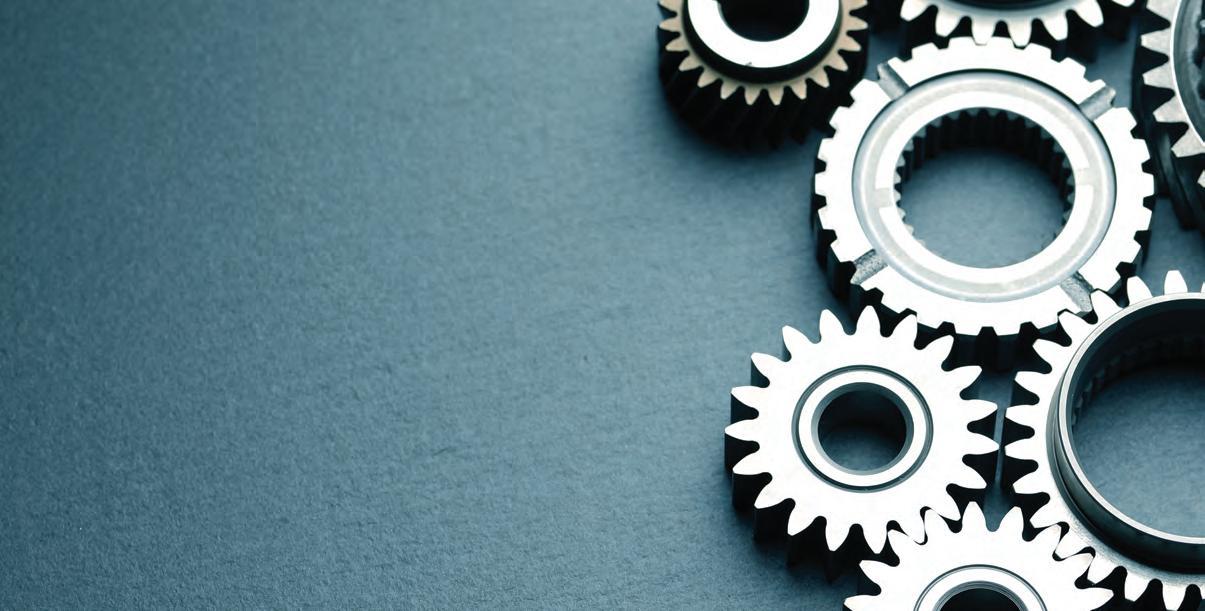
The podcast features conversations with industry experts about maintenance, reliability, repair, asset management, safety and operations. Topics that are of utmost importance to MRO readers.
Previous guests and topics have included:
• Scott MacKenzie, Senior National Manager of External
Affairs, Toyota Motor Manufacturing Canada –
Maintenance at TMMC Plants with a Focus on the
Environment; • Martha Myers, Founder and Owner, Martha Myers
Consulting Service – Importance of Networking and
Education in Maintenance; • Doc Palmer, Managing Partner, Richard Palmer and
Associates Inc – Focus on Scheduling and Planning of
Maintenance; • James Reyes-Picknell, President, Conscious Asset –
Managing Maintenance and Reliability; • Shawn Casemore, President, Casemore and Co Inc –
Engaging Your Employees in a Safety Culture; and
• Steve Richmond, CEO, Projetech Inc - How the
expansion of 5G networks can benefit maintenance and repair operations MRO
Mr. O’s Tip
Increase affordability and efficiency with cloud-based EAM systems
It’s never been more important for companies to manage assets effectively in order to scale in the best way possible. Just having a better product or service is no longer adequate in today’s world; organizations are now expected to develop their product better, faster, and cheaper, meaning they need to maximize the productivity of their assets and equipment to really succeed.
Companies are now faced with the choice between installing enterprise asset management (EAM) Cloud or EAM On-Premise systems with modern applications to reach these goals. It was only a decade ago when the most typical way to deploy an EAM system was through an on-site data centre, but things have changed.
On-premises installations that are hosted and controlled internally by IT departments are now being outperformed by software-as-aservice (SaaS) and cloud-based alternatives. Most EAM technologies are now cloud-based SaaS models, and they offer some significant advantages, especially when it comes to increasing affordability and efficiency.
Affordability:
Perhaps the best thing about an EAM Cloud system is the amount of money you can save upfront. Their minimal start-up costs also make cloud EAM apps popular with smaller businesses. Cloud-based SaaS models eliminate the need for upfront capital investments, and you only pay for what you use. They give you the freedom to scale up or down your service based on your monthly requirements, and you also get seamless automated software upgrades and backups.
On the other hand, on-premise systems require a significant initial expenditure because you must acquire and maintain the gear required to run the EAM software. You’ll end up spending more in the long run, and these costs can add up quickly. If affordability is your focus, go with an EAM Cloud system for the most bang for your buck.
Efficiency:
In a side-by-side comparison for efficiency, an EAM Cloud system is going to be far more superior to an EAM On-Premise system. With SaaS or cloud-based EAM systems, upgrades are handled automatically by the vendor, enabling workers to do other tasks and effectively outsource the technical expertise required with EAM maintenance. Updates are also performed regularly by software providers to improve software stability typically overnight, which allows for as little disruption as possible.
With an on-premise system, you’ll be faced with big challenges if your physical premise is ever damaged by a natural disaster or power loss, which is not a problem when you store critical EAM data in the cloud. Aside from having to spend time maintaining and troubleshooting expensive on-site hardware, an on-premise system also doesn’t offer efficient capabilities for your maintenance staff to access asset data via the cloud from any device, anywhere, instead of having the data on a single computer.
Choosing the appropriate EAM for your business is no easy task. First and foremost, you must examine your organization’s needs, finances, data, and scalability constraints. However, most companies are going to find more benefits from an EAM Cloud system, especially when it comes down to affordability and efficiency.
- Steve Richmond, CEO and Founder, Projetech, Inc.


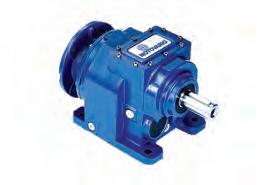
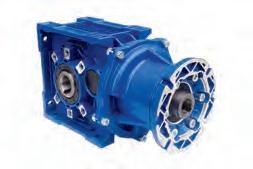