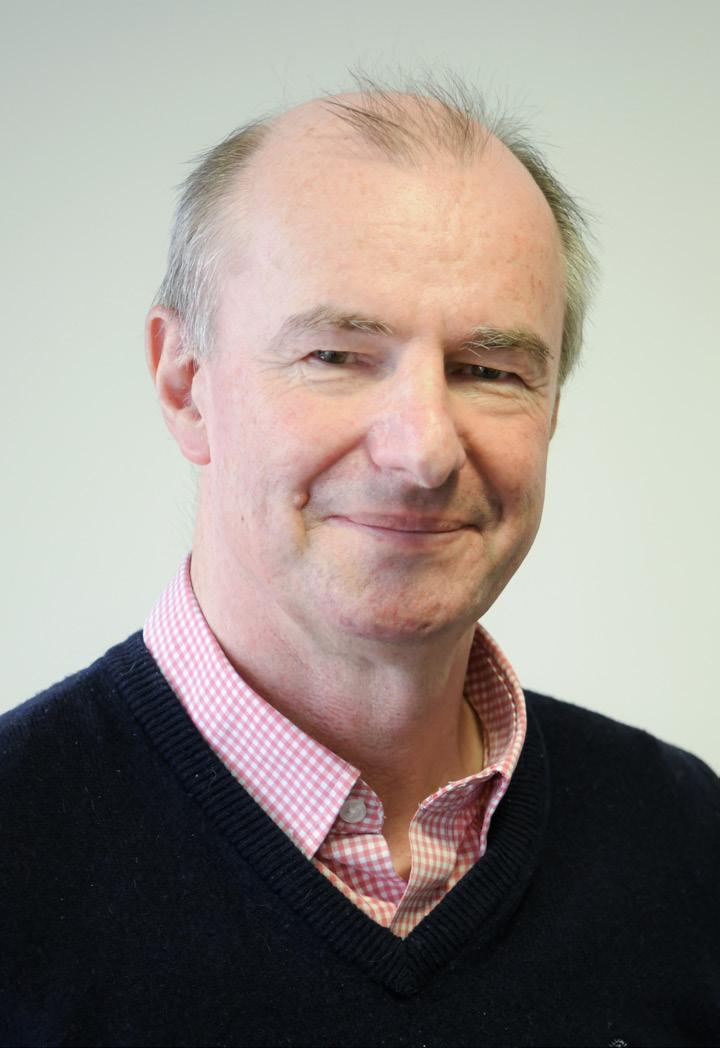
2 minute read
MARKET TALKS “2023 is the time of triple glazing for UK glass market”
- Hamish Ogilvie, Ravensby Glass CEO
Given its position in the UK market, Ravensby Glass has its finger on the pulse of both commercial and residential glass trends: two different realities that are react in different ways in this first half of 2023.
Advertisement
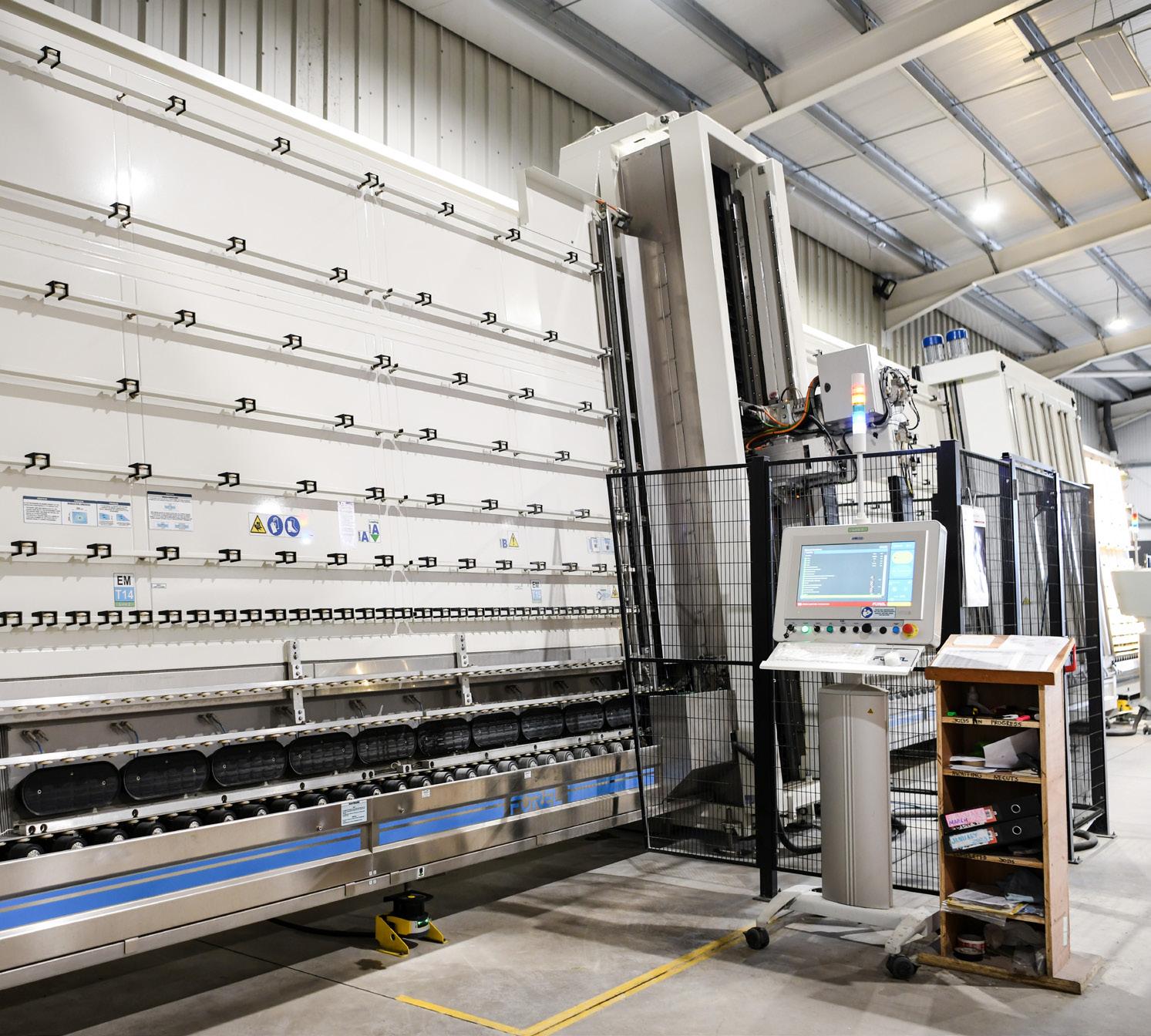
“Contrary to what might have been assumed a year ago, the demand for commercial glass shows no sign of contracting, quite the contrary” continues Mr. Ogilvie “The constructionarchitectural sector in the UK is in full swing and the need for facades, shopfronts and other installations will be a constant until and including 2024.
Despite the dampening effect we can expect due to the rising cost of raw materials, it is undeniable that there is a willingness to invest significantly in commercial glass, particularly triple glazing. In fact, in 2022, our orders were only 10% triple glazing, whereas today they are already 35%.
As for the residential market, it is stable at the moment. However, I believe that the demand for triple glazing will also increase here before long, in the wake of what is happening in other sectors. From this point of view, Ravensby is well prepared: when it comes to triple glazing, the Forel line has demonstrated really good performance”.
Flexible Spacer Applicator
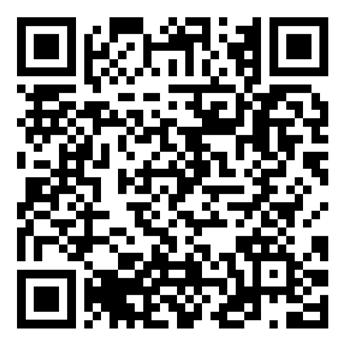
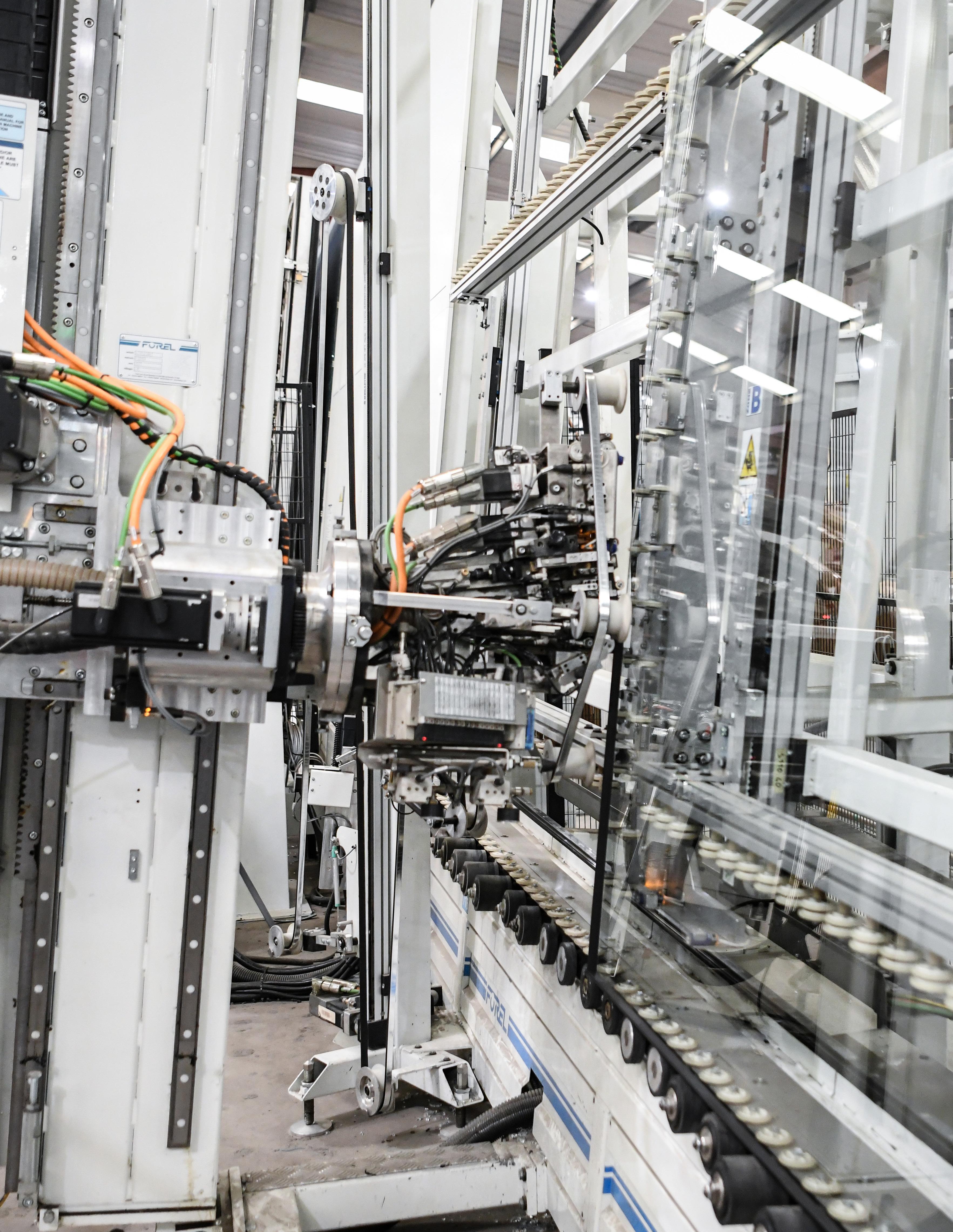
What’s going on with Insulating Glass and Thermoplastic Spacer?
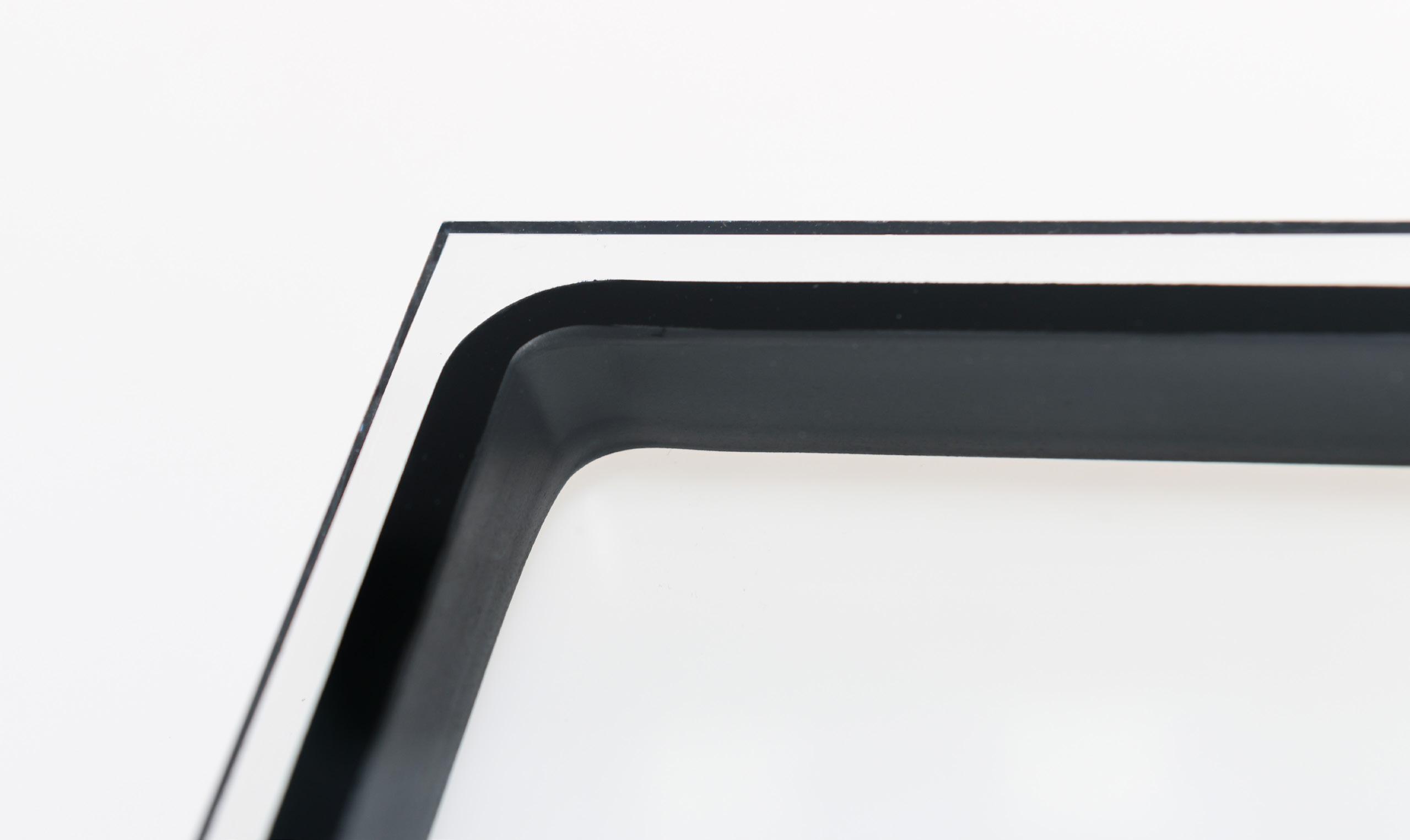
An increasingly popular solution for the production of large volume production of double and triple glazed units

The use of thermoplastic spacer products is a decidedly attractive option for all manufacturers who handle large daily production volumes of IG units, which is often the case when dealing with orders for residential and commercial glass units. The Forel High Tech IG line with thermoplastic applicator is a bivalent model, capable of processing conventional insulating glass with rigid box spacer profile. The entire solution is highly automated and can be managed via a single workstation. Following the principles of Industry 4.0, the line provides real run time production data that is linked to the companies ERP.
At the heart of the system is the Art. TA Thermoplastic Applicator, developed for the perfect extrusion and positioning of the material in a fully automatic but userfriendly way. The interface already contains the most commonly used cycles and the different options related to the use of thermoplastic spacer: “Its use is easy and intuitive”. The extruded profile thickness changes automatically relative to the production requirements and the non-stop dosing system allows for material drum changes without any loss in production. The product is constantly monitored throughout the entire extrusion circuit, thanks to multiple temperature control sensors and heater elements.
Before glass coupling but post spacer extrusion, the glass can be stationed within the new Buffer Station, which enhances the characteristics of the material and increases the overall assembly speed of the panel. The process of coupling the glass and filling with either argon, krypton, or a mix of the two, is performed by the Art. AP Automatic Press. The final inline process is entrusted to the Art. SR ‘High Tech’ Sealing Robot, already widely appreciated for its excellent performance on both residential and commercial insulating glass units.
The “High Tech” with thermoplastic spacer line is available in four formats, with maximum workable dimensions of 4000x 2000 mm, 4000x2500 mm, 5000x2800 mm and 6000x3300 mm respectively. The line can also process offset units. The maximum thickness of units assemblable with the line is 100 mm.