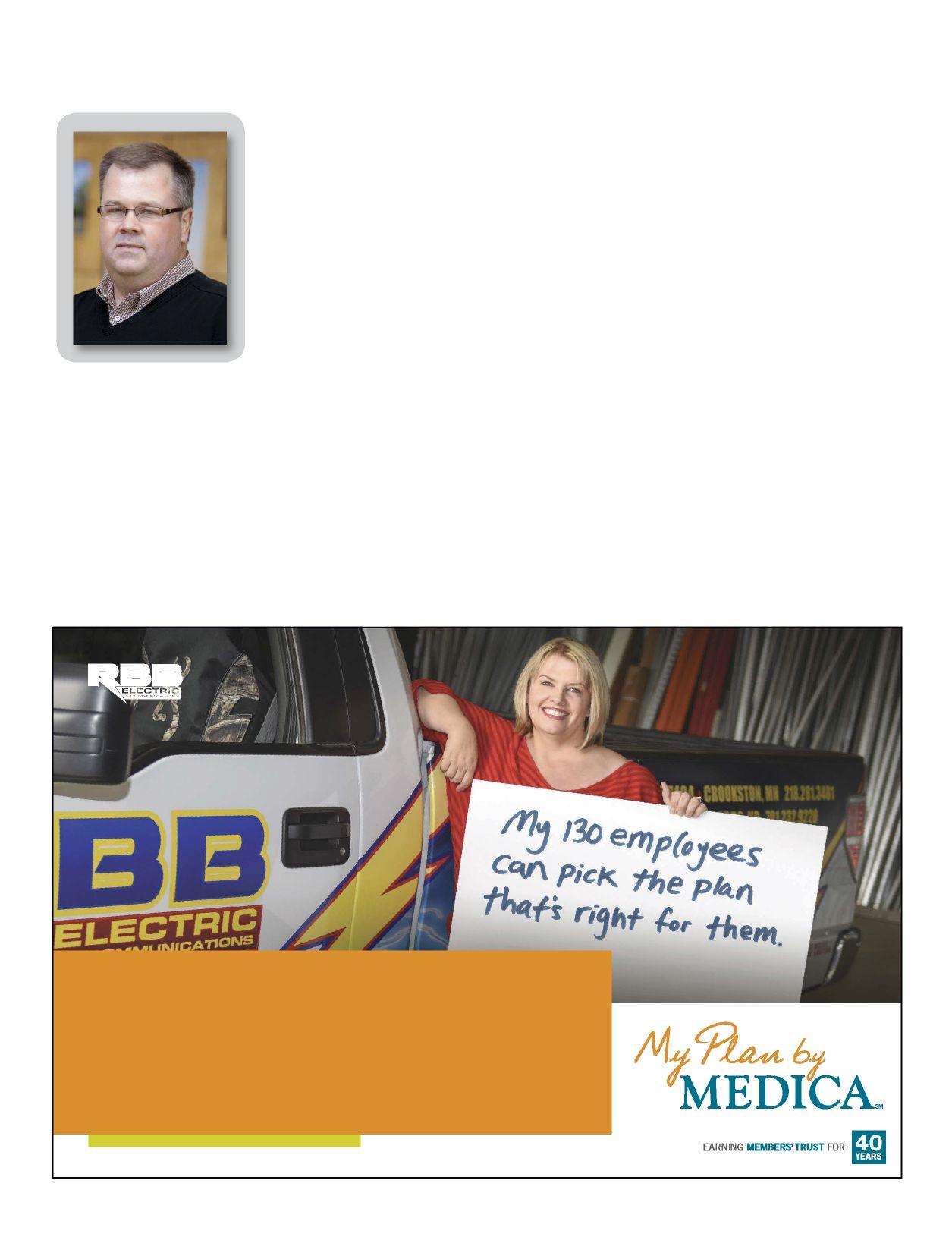
2 minute read
Identify and Eliminate ‘Waste’
BY CHAD FROST
When introduced to the idea of the popular Lean Management System, many organizations I have worked with respond, “I thought that only worked in the automotive industry,” or my all-time favorite, “We don’t make cars here, so this really doesn’t apply to our company.”
After we get past the usual resistance-to-change barriers everyone uses when confronted with new and strange ideas, many people begin to understand whatever they do in their careers or day-to-day jobs almost always involves a process or sequence of steps. Lean is first and foremost a management system and focuses heavily on the concept of improving flow and reducing or eliminating waste in a process. So the question becomes after this initial discussion, “Do you think Lean could help us with our process?” The answer is unequivocally, “Yes.”
Recently at EAPC, we introduced Lean training to our architectural team and heard, “How can I use Lean? I’m an architect.” We overcame these concerns by first asking the architects about their core processes at their jobs, day in and day out. (In Lean, these are called value streams.) Immediately, they started to map out how they completed their projects and saw how the project was just a long chain of steps, which, at the end of the day, finally produced an architectural design process.
Once we agreed on the process, we started to talk about the flow. Flow is how easy the service or product moves through the various steps – it can be choppy and interrupted with stops and waits or it can be uninterrupted and smooth. Regardless, if the process flow is poor, it’s obvious to employees and customers — a good example is long lines at a restaurant.
My Plan by Medica helps employers control health insurance costs while offering employees more options. Your employees are able to pick a plan that fits their needs. For RBB Electric, My Plan sparked major enthusiasm. My Plan is easy to implement without creating more work. Just ask Robin. She’ll tell you all about RBB Electric’s experience with My Plan and why change was good at medica.com/privateexchange. For more information about My Plan call your broker or Medica at 952-992-3055.

Smooth, uninterrupted flow is a key factor to a Lean process, and to ensure the process continues to improve, the waste slowing that flow must be identified. Interestingly, wastes are defined by our customers and are based on the concept of value to the customer. A simple rule of thumb: If the customer is not willing to pay for it, it should be considered a waste in our process.
Once the team of architects started to view their work as a process and assessed the process from the viewpoint of the customer, they were able to quickly identify wastes and put together plans to reduce or eliminate them. At the end of the day, the team of architects asked the question, “What can’t you apply Lean to?” Mission accomplished.
Chad Frost Director of Business Excellence, EAPC Architects Engineers chad.frost@eapc.net
Do you know a woman at the top of her eld who deser ves recognition?
The 25 Top Women in Business edition of Prairie Business celebrates creative, successful women who have made a signi cant impact in their businesses or industries. Beyond business talents, these honorees share their skills through community service, mentoring and balancing wor k and family.
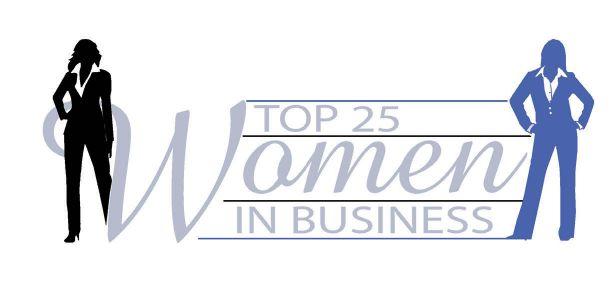