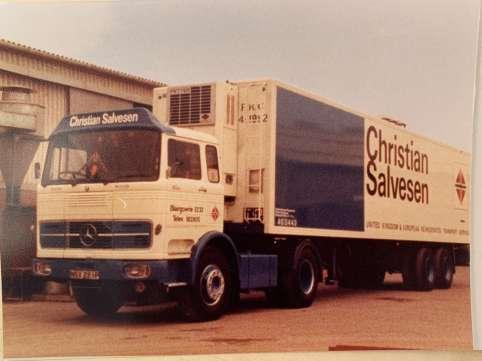
6 minute read
The Gray & Adams Story Part Two
James Gray continues with part two of the Gray & Adams story
Another major decision regarding a change of direction for the company, was being reached by the two Jim’s and Lewis Gray (Jim Gray’s brother) which was to introduce a new one-piece sandwich construction refrigerated body to the U.K. This type of construction already existed in Europe and after consulting with various manufacturers on construction techniques, a relationship soon developed with a Dutch company and shortly thereafter a small group from Fraserburgh spent two weeks with them learning more about the technology and manufacturing techniques used. The group included, W.M. Sinclair, W. Cardno, K Burnett, W. Maitland, J.J. Gray (Jim’s son) and Lewis Gray Snr and upon their return discussed what they had observed and shared the knowledge gained with other employees in order to plan the construction of the first of the new concept refrigerated chassis less Trailer. In response to the changes, it became clear that we would need the services of a draughtsman and employed Ruary Campbell, followed shortly afterwards with Charlie Buchan, the first employees of the new drawing office. G&A then sourced, from around Europe and Scandinavia the new materials required for the manufacturing techniques, which Gray & Adams had adopted, to ensure that the trailers being built would comply with these rigorous new standards. In 1978, all the hard work and planning came to fruition with the development of a new chassisless refrigerated trailer using one piece insulated panels manufactured by themselves in a new purpose built workshop.
Advertisement
Modern engineering materials, such as expanding PVC foam, structural adhesives, and continuously rolled, prepainted alloy sheeting and GRP allowed them to do away with the heavy two-member chassis and steel framed / aluminium clad panels of the earlier designs, and to build a monocoque body where the side walls, roof and floor became structural members carrying the loads along with the chassis-less chassis. (I.e. self-supporting construction).
Rumours had been circulating since 1976 that the government were considering changes in transport legislation and in January 1979, A.T.P. was finally introduced to the U.K. To obtain A.T.P., a trailer had to be sent to Warrington, where it was tested for thermal efficiency, in a special heat chamber. If it passed the test the Department of Transport would issue 30 certificates which will allow 30 trailers to be built to the same specification, then another trailer would have to be sent for the same test to get a further 30 certificates. This system was grossly unfair, because the Europeans were already getting 100 certificates per test, which meant that Gray and Adams were required to submit 3 tests for every one test of the Europeans. The two Jim’s could not take this lying down, so they challenged the DoT over this and after several fruitless meetings they contacted representatives from the European commission. Eventually the Ministry relented and brought the UK into line with the rest of Europe.
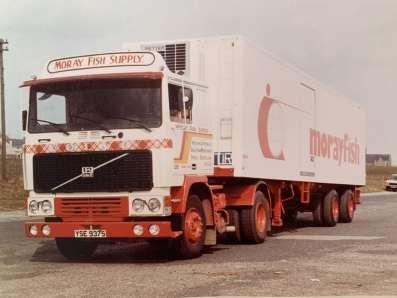
As business increased, the company found that, due to their geographical location it was difficult to expand into other areas of the country, so in 1976 a factory was acquired in Dunfermline and converted to suit their manufacturing requirements. Bob Smith was appointed as Managing Director and oversaw operations which included a service backup to customers in the Central Belt and the south of Scotland. The Directors were also aware that there was a thriving market in Ireland, which at that time was being covered, in a small way, by Montracon Trailers ( a G&A selling agent). However, they were looking to provide a better service, as well as manufacturing facilities of their own. Subsequently a green field site was purchased about ten miles outside Belfast for the construction of a purpose built factory, to produce rigid/ sliding side bodies and the servicing and repairs to rigids and trailers. The new facility began production with Harry McEwan appointed MD in Ireland.
Gray and Adams now turned their attention to the English market but, as a new factory had just been built in Ireland, it was felt the timing wasn’t right to do the same in England. It was therefore decided to appoint Atlas Refrigerated Vehicles of Nottingham, as agents and Norman Parrish heading the up the sales.
The expansion of the company and ever increasing workload led to the appointment of Jim Watt in 1979 who became the first company accountant.
In the early 1980’s, computerised systems were introduced to the sales and purchasing ledgers. Over the years the system has been continually upgraded to accommodate material purchasing and stock control, sales administration, sales ledger and salary. The design and drawing office also changed from the traditional drawing board to a computerised system with twelve full time draughtsmen and a drawing office manager. The labour recording system of manually filled out time sheets, has been replaced by a computer recording system, specifically designed to suit all companies’ requirements. Due to the number of computerised systems in operation, a full time computer technician was employed.
During 1982 the Armitage report on vehicle weights came out which resulted in an increase to the gross vehicle weight from 32.5 to 38 ton. This brought with it tri-axle steel spring suspension, side guards and latterly, spray suppression, all of which was new, not only to Gray and Adams, but to the trailer industry at large. With the Armitage report, came also much more stringent braking regulations and the introduction of an anti-lock braking system on trailers. Gray and Adams took all this in their stride and their market share continued to increase.
With the introduction of larger trailers and an increase in orders, the company again outgrew its manufacturing facilities, and in 1988, a decision was taken yet again, to extend the existing site to allow for an increase, both in production and the number of employees.
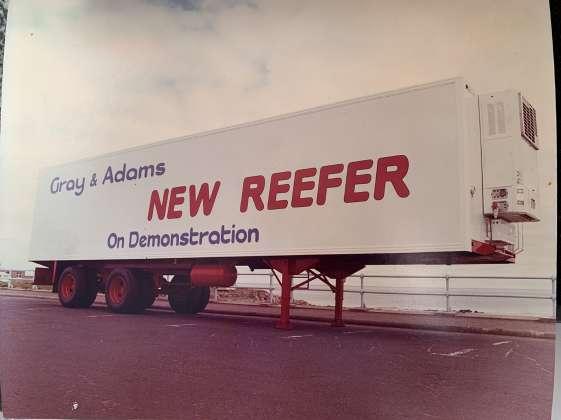
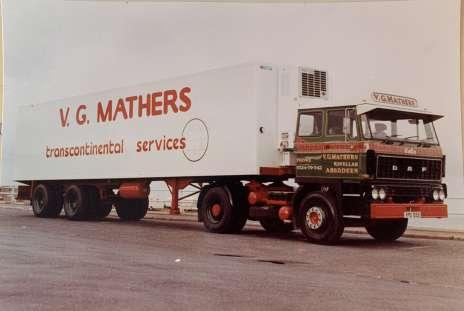
Towards the end of the 1980’s and early 1990’s, the owners of the company’s agent, Atlas Refrigerated Vehicles, indicated their intention to retire and dispose of their factory, which was on a desirable residential site. Thus in 1990, the company purchased a 5 acre site in Doncaster, which included a dilapidated building. Steve Rose was appointed MD and works began on a complete refurbished to suit the company’s requirements, being the assembly of rigid bodies and trailer and rigid repairs. This was in line with operations at the company’s other locations in Dunfermline and Ireland. Over the years, Gray and Adams have continually extended and improved facilities at the 3 locations to accommodate an increase in the manufacture of new rigid vehicles and on the repair and refurbishment of existing vehicles.
In 1991, after two years hard work reorganising, the company applied for and achieved BS 5750 part 2 and are already seeing the benefits in improved performance and manufacturing efficiency.
In 1993 when the C&U regulations changed yet again to allow 13.6mtr trailers, Gray and Adams had to take a serious look at their panel manufacturing facility as they were rapidly outgrowing it. So the Directors (still the two Jims, with Lewis and Jim Gray’s two sons, James and Peter) took the bold decision, with the country in recession, to invest in a new 46,000sq.ft. Panel manufacturing facility.
1998 saw the expansion of the trailer chassis manufacturing facilities and with no further available ground on the existing site, vacant buildings at Power Jacks, were purchased (originally CPT buildings). The existing frontage was retained but the original building was demolished to allow for a new building to be constructed to suit the chassis manufacturing requirements.
This included the purchase of new equipment, which allowed for the manufacture of the complete chassis. A CNC Plasma cutter, press brake, a full-length chassis beam welder and a fully automated shot blasting plant were purchased. Specialised chassis jigs and rotating equipment were also introduced to improve the manufacturing capability. The other buildings, which were purchased at this same time, were renovated and adapted to suit the two chassis spray booths where the chassis are painted according to the customer’s specifications. Once completed, the chassis is then moved into the brake department where it has the brakes/air suspension and electrics installed.
The first order placed for the new concept, Chassis number 1, came from a new company in Aberdeen called BonAccord transport which had recently been formed by a group of drivers and a mechanic. This was followed by one of our existing customers Moray Seafoods and was used to transport prime seafood to Spain and Portugal. Within the same year we secured and completed our largest order of 90 trailers for Christian Salvesen. Another local contractor, V.G Mathers, placed an order and we were even able to build a demonstrator which visited a number of transport companies throughout the UK in order to promote the new concept.
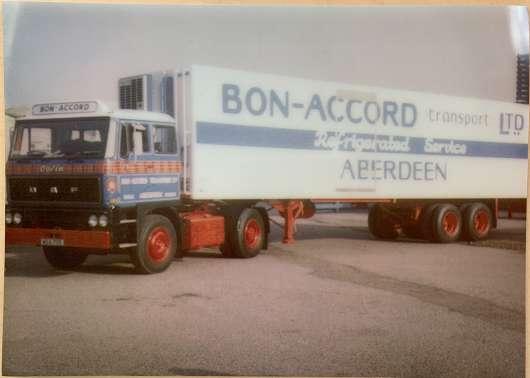