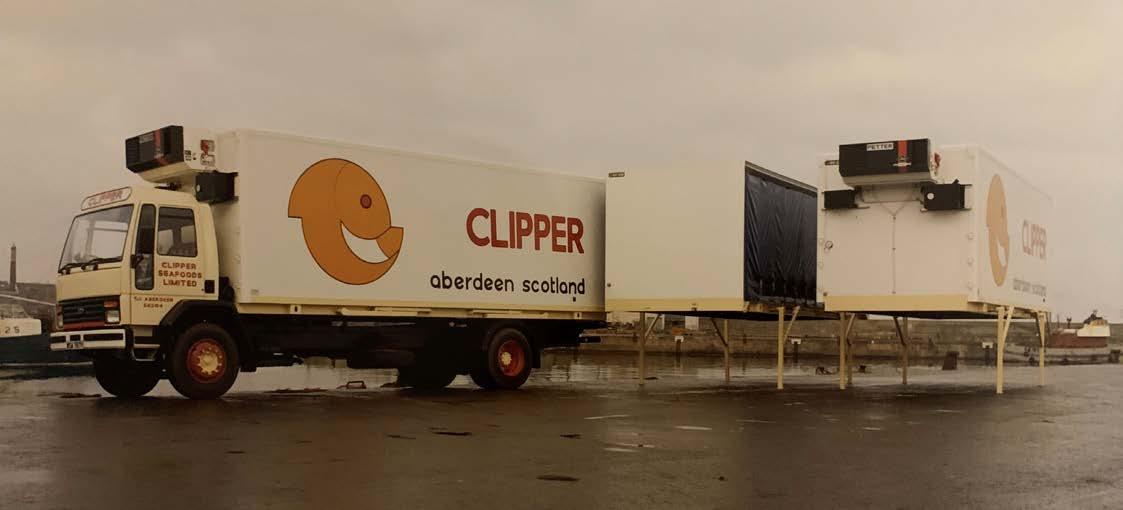
8 minute read
The Gray & Adams Story – Part Three
Following on from the spring 2023 edition (Issue 20), we pick up the history of Gray & Adams from the early 2000’s.
Further development of the former CPT buildings started again in 2000 when the third vacant building had the front area adapted to meet our storage requirements for raw materials and parts, primarily for use in chassis manufacture. The remainder of the building was set up to accept a foam injection plant specifically manufactured for our needs by Simmipianti in Italy. In preparation for its arrival, the subfloor base of the building had to be excavated to a depth of 1.5 metres to facilitate the installation of the new machines. An extension to the building was also created in order to accommodate the associated plant equipment, pumps, and bulk storage tanks for the liquid polyurethane foam. The plant comprised of a large press for the manufacture of refrigerated vehicle roofs and a smaller press located in an adjoining area for the manufacture of front bulkheads and rear doors.
Advertisement
During the course of 2002 one of the UK’s longest established transport companies, Gibb’s Transport, ceased trading. As the site was next to ours, we purchased it for future expansion. The decision was taken to dismantle their existing workshop and erect a new building which would accommodate 14 tables for panel manufacturing, effectively doubling our capabilities. We also incorporated robotic glue dispensing machines which were manufactured by Pro Hydro in Finland for our specific requirements. Once the panels were produced they would need to be trimmed to meet our customer requirements and as such a multi-functional saw was purchased from CMS Italy and modified to suit our needs. We also retained some existing machinery, primarily for the pre assembly preparation of the trailer floors.
When the new panel hall was eventually completed in 2005 we were able to produce and supply an increased number of panels, however, after a very short time, the increased capacity meant operators were under more pressure, and as such consideration was given for operator safety in this busier environment. After much thought, James J Gray suggested introducing a night shift, not in every department, just in areas of high demand. This obviously required additional employees and a recruitment programme was started to fill both day and nightshift vacancies since some existing employees expressed an interest in working the nightshift. This proved to be useful in terms of passing on the skills required and after a period of adjustment the new shift pattern began to work as anticipated and even expanded to include other departments which continues to this day.
An additional part of the extension on the former Gibb site was to create a new motor vehicle accident repair facility as we had outgrown our existing one which we have been operating from since 1966. Part of the then new facility included various car ramps, additional jigs for body repairs and, what was then state of the art, spray booths.
In 2008 a decision was taken to create a new accident repair facility for trailers which was originally going to be sited in the former Bluebird coaches building. This had a 7 bay capacity which was extended by a further 3 bays and subdivided into areas for panel pre assembly, specialist equipment and jigs purchased from Josam in Sweden for rectification of accident damaged truck chassis cabs and trailer chassis. The final bay of the building had a spray booth installed which could accommodate the longest and highest trailers we manufacture. This operated as a repair facility for a period of time, however due to an increased demand for double deck trailers the decision was taken to relocate the trailer repair facility to other existing buildings on our site. This freed up a significant portion of the building which could now accommodate a dedicated double deck completion and final inspection area. Given that double decks sit closer to the ground, portable Stertil Koni hydraulic column lifts were purchased as it wouldn’t have been practical for operators to work on or inspect the underside of the vehicles. We then took a decision to purchase a fully compliant HGV brake tester which was sited at the north end of the completion and final inspection area allowing us to brake test all vehicles manufactured or repaired on the Fraserburgh site.

To refer back to the buildings where repairs had been relocated to, these were originally used for storage and the manufacturing of smaller parts and assemblies and therefore needed to be adapted in order to accommodate all vehicle types. The buildings were extended upwards and new roof cladding and composite panels were fitted alongside new full height roller doors. The adapted building contained 6 bays, one of which contained a full length inspection pit for easy access.
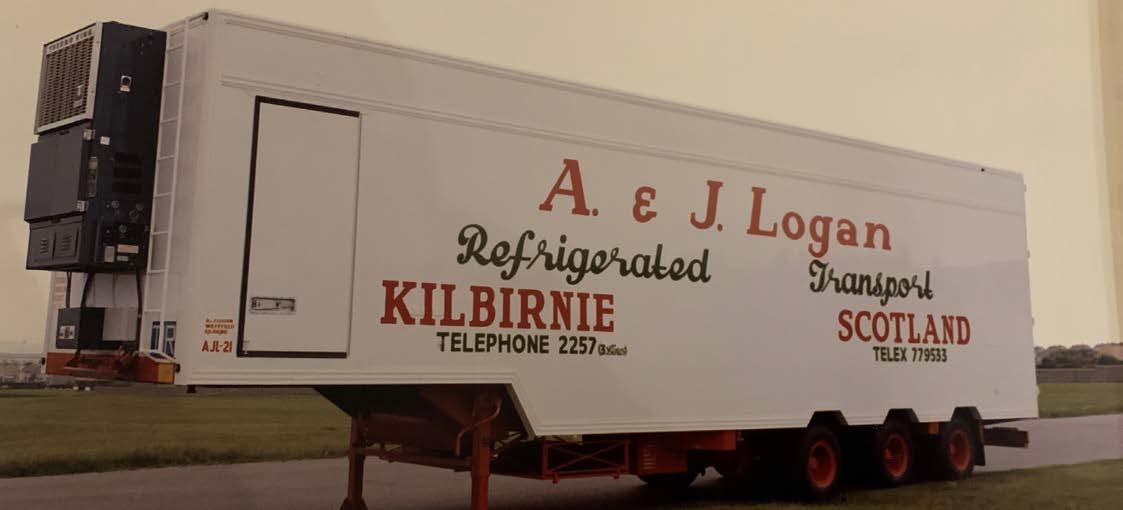
Brian Fraser
I commenced employment at Gray & Adams March 1998, having previously worked as a building surveyor with the local authority. I initially had a placement in the Sales Office in Fraserburgh but after a short period of time the company had completed the purchase of an engineering works across from the main factory, and that potentially was the start of me going back to utilising my building experience. Peter Gray was ultimately responsible for persuading me to join Gray & Adams way back then.
I have maintained relationships throughout my 25+ years, with all our major customers and key suppliers, including support for Doncaster, Dunfermline and Ireland, a role which to this day I still enjoy.
Engaging on a daily basis with James and Peter, has allowed me to achieve a wider knowledge within the group. The support I have received, and still receive, from the joint Managing Directors both on a work and personal level, is second to none.
During the earlier years, I spent a large amount of my time with Jim Gray Snr, and Lewis Gray Snr. Both vastly knowledgeable on the day to day running of the company, and this was invaluable and beneficial to my progression.
Throughout my career it is satisfying to see the younger generation progress within the company, without the younger staff members having the opportunity to enjoy their time being at Gray & Adams, the future would be very bleak indeed.
Having involvement with customer orders, and seeing these through to the final delivery process is good for morale.
Having been asked, what is the best thing about working for the company? My simple answer to that question is, it is never a thought to come to work on any given day.
Lifelong Careers (25 years) – Brian Fraser & Neil Gilland
Lifelong Careers (40 years) – Ian Senic & James Duthie
NEIL GILLAND
I started with Gray & Adams in the Drawing Office as a CAD Engineer on 13th April 1998. Ruary Campbell introduced me to the Office systems and processes and working under him, I was initially looking after the database/library drawings – adding new variants for the different builds and specifications as well as keeping the drawings up to date.
Starting in 1999, I worked with Lewis B Gray and Bob Reid to develop a refrigerated lifting floor trailer taking all the ideas and drawing them to get the project to the build stage. We built two demonstrators in early 2000 and they went into service for customers trials as soon as they were ready. I have been heavily involved in these trailers since then as we worked on the design to get where we are today. These have proved to be extremely popular with our customers and are huge part of our build numbers. In those early years I also worked a lot with Lewis and Bob on our low floor double decks with large wheelboxes and independent suspension, which we still build today.
In the early 2000s, I was involved in the early days of automation in the factory after the introduction of new CNC machines – plasma, laser and router all of which are still programmed in the Drawing Office, the Foam Injection machine also came on line at around the same and again I worked with Lewis B Gray putting his ideas on to paper for our foam injected panels to get them to the production stage.
I became the Assistant Drawing Office Manager in May 2004. It was April 2007 that I took on the role of the Drawing Office Manager that I still am today, at the same time we moved into a newly completed bright open plan office where we still are today.
The site in Fraserburgh is so much bigger now than when I started, it was only on this side of the main road and we had other businesses that we worked around but they have all gone now and we have expanded into where they were.
The Chassis Shop was next door to us but is now a much bigger building across the road and that building is now the Twin Frame Completion. We now have two buildings that were built solely for our lifting floor/double deck trailers.
I think the company has only gone from strength to stronger since James and Peter took over as joint MDs and that is including the Covid years, where I think the Directors did a magnificent job keeping everyone safe and the factory going.
No two days are ever the same with such a wide variety of projects that we cover, the time has always flown in everyday and I still cannot believe it is 25 years, it really has been a privilege to work for so many years for such a superb company and in my home town just a few minutes walk from my house. I am not alone with many years of service and I think it says a lot about the company that so many people have been here a long time not least in my Office which I have a great team.
IAN SENIC
I started at Gray & Adams on 26th May 1983 and have been here for the last 40 years. I first started in the assembly department building the refrigerated trailers. I have been in various roles, I moved from the assembly department to the door department, then to the trailer department before finishing up in my current role as a manufacturing operative where I drive the forklift collecting waste materials for recycling, which I have been doing for the last 7 years.
My career highlight at Gray & Adams is seeing the company expand over the years, from starting as a car body shop to becoming one of the largest employers in town, it’s been incredible to watch. I have had some mentors across my time at Gray & Adams with older generations teaching me skills. While I haven’t mentored anyone myself, I have always helped in other departments. My experience in various roles has meant that over the years I have been able to turn my hand at a number of roles and help put where required.
Gray & Adams has been a great local company for me to work for. There is a happy workforce with lots of camaraderie and everyone getting on. I have really enjoyed my 40 years here.

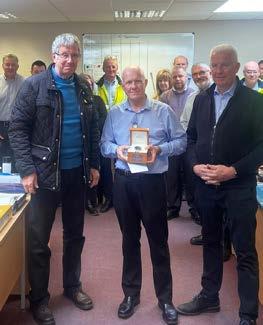
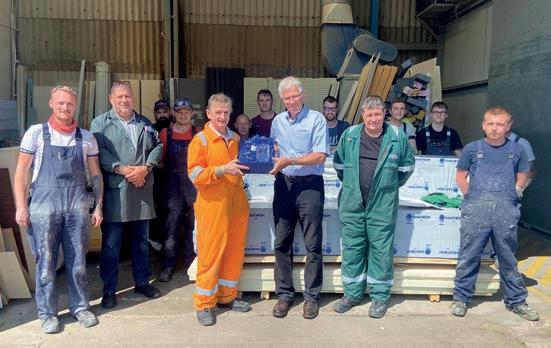
JAMES DUTHIE
I first started at Gray & Adams in May of 1983. I was due to start the week that Aberdeen were playing in Gothenburg but I was going to the game so I was able to postpone my start date to the following week.
I started my career at Gray & Adams in the assembly department putting cappings on vans, and most of my 40 years within that area of the business, before moving across to road to the foamfill department.
A career highlight for me is seeing the company grow and expand. My gaffer Kenny Burnett was always keen and helpful, sorting out problems and so on, he helped me out in the long term, so I really appreciated his mentorship.
Gray and Adams has been a really good firm to work for, it has been great for getting the work and keeping everyone in a job. I have really enjoyed seeing the business expand over my 40 years there.
“ I have really enjoyed seeing the business expand over my 40 years there.”
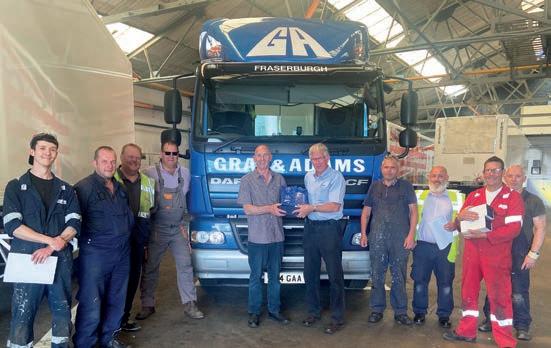