19 minute read
News
BFM issues warning over TDI shortages
National trade body the British Furniture Manufacturers (BFM) is sounding caution over the availability of foam used in upholstered furniture and mattresses.
The trade body says that TDI chemical shortages pose a threat to the supply of foam across Europe throughout autumn.
As a result, it says that retailers and customers should be prepared for unexpected delays as manufacturers face sporadic supplies.
Sean Holt, MD of the BFM, said: “There’s a significant reduction in the manufacture of TDI from the European facilities, which supply many of our members.
“The material is being imported from the US and Asia, but overseas transportation costs and the fact that not enough of it is being produced to meet demand, means manufacturers are facing unexpected sporadic supply shortages or sudden jumps in costs, which may cause disappointment and inconvenience for customers.
“The BFM is committed to encouraging consumers to buy British and appreciate the value of British-made furniture, but it also important to manage expectations.
“Manufacturers are battling extremely challenging circumstances, with national and international economic factors that are beyond their control.
“We are closely monitoring the situation and will provide members with regular updates, which will hopefully help them to navigate the situation ahead.”
Mirka achieves Gold standard with Investors in People

Mirka (UK) Ltd has been awarded the Investors in People (IIP) Gold accreditation. The IIP practitioner praised the business’ excellent relationships with all its stakeholders, ensuring continued sustainability, aided by a strong management team that inspires its staff, and delivering high business standards and performance levels.
The IIP practitioner also highlighted the company culture that brings people together within the organisation, empowering them to make autonomous and trusted decisions, and its robust structure and policies that support staff in continuous professional development and upskilling. Craig Daycock, managing director of Mirka (UK) Ltd, says, “We are absolutely thrilled to be accredited with the Gold award from the IIP. This recognition highlights how the sustained investment in the processes and structure to aid the development of our staff to support their customers and all our stakeholders has helped them grow both individually and as part of their team.
“The Mirka UK management team is committed to continuing to invest in these areas because we understand first-hand how continuous professional development benefits our customers and the business, and how it has made our staff feel empowered and trusted within the organisation.”
St Albans to Morecambe bike ride cyclists raise £27,000 for industry charity
A team of intrepid furnishing industry cyclists have completed a gruelling 300+ mile bike ride, raising £27,000 for The Furniture Makers’ Company, the City of London livery company and charity for the furnishing industry.
A 12-strong team of cyclists took part in the St Albans to Morecambe Bike Ride fundraiser, which was organised by Tony Attard OBE DL, Master of The Furniture Makers’ Company, and took place from 1216th September.
Dressed smartly in the sponsored team jersey, the peloton set off on the morning of Monday 12th September from Verulamium Park in St Albans and cycled 64 miles north, taking the riders through the beautiful Buckinghamshire countryside, and ending the day in Whittlebury. On day two, the team cycled 68 miles up through the heart of the East Midlands, negotiating the bustling streets of Leicester and Loughborough, finishing in Kegworth.
On the third day of the challenge, the cyclists headed 67 miles from Kegworth, riding through Long Eaton – the UK centre of upholstery – in the morning, followed by an exhausting afternoon climb up Snake Pass – a testing hill pass in the Derbyshire section of the Peak District – ending the day in Glossop.
The cyclists faced another tough day on day four, with climbs out of Glossop and ending the day in the beautiful Yorkshire market town of Skipton after a 58-mile ride.
On the final morning, the weary cyclists started the day with a visit to the office of the National Bed Federation, a sponsor of the team jersey. The cyclists were greeted by Andrew Mear, chairman of Skipton Business Improvement District, and Jessica Alexander, executive director of the National Bed Federation, who presented the team with a cheque. After the presentation, the team cycled the final 45 miles west from Skipton, ascending over the Yorkshire Dales and into Morecambe, Lancashire. The team were cheered over the finish line by friends and family at the Midland Hotel. Later that evening the High Sheriff of Lancashire, Martin John Ainscough DL, presented each participant with a certificate and a bottle of English Champagne.
The group’s fundraising total currently stands at a huge £27,000, but there is still time to donate, as the JustGiving page will remain live for another six weeks. The money raised from the fundraiser will support the charity’s education programme – which nurtures young people looking to build a career in the sector – and its provision of occupational welfare to people working in the industry.
The Furniture Makers’ Company would like to thank all the sponsors of the team jersey: Biesse UK, Blum UK, Bulgaro Interiors, Burbidge Kitchens, the British Contract Furnishing Association, the British Furniture Manufacturers Association, Celtheath, Furniture Village, Gresham Office Furniture, KI, the National Bed Federation, Ocee Design, Panaz, Sanderson
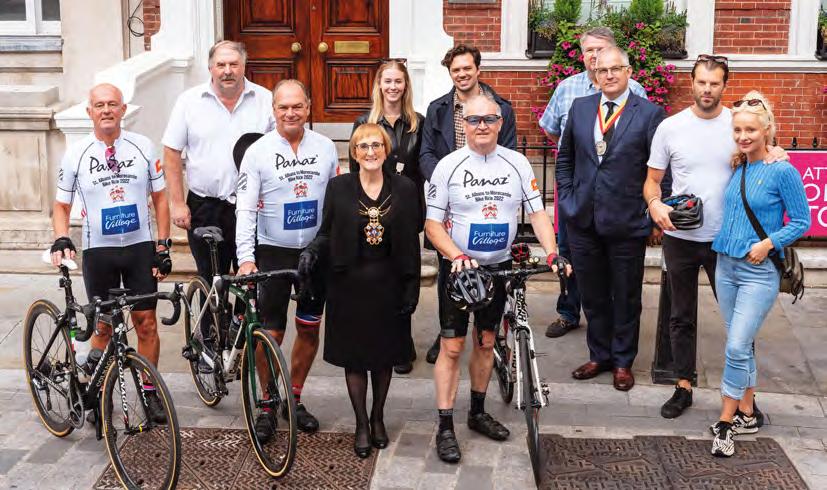

The cycle team comprised of 12 riders who joined the fundraiser for various legs of the journey:
• Rollie Attard (Days 1-5) • Tony Attard OBE DL (Days 1-5) • Ben Burbidge (Days 2-5) • Stuart Daykin (Day 2) • John Irwin (Days 1-5) • Paul von der Heyde (Days 1-5) • Stewart Linford (Days 1-5) • Andrew Sykes (Day 1) • Edward Sykes (Day 1) • Nick Westlake (Day 1) • William White (Days 2-5) • Aidan Wilson (Day 2) Design Group, SATRA and Shackletons Group.
Tony Attard OBE DL, Master of The Furniture Makers’ Company, said: “What a fantastic week we had. This was a substantial challenge for all of us with some very tough climbs throughout the week. All the participants agreed that it was a hard trip but worth it to raise the significant sum of £27,000 for our charity. I would like to express my deepest of thanks to our corporate cycle jersey sponsors as well as for all the individual donations we have received through JustGiving. There is still time to donate and help us raise more funds.”
Prior to the group’s departure, a ceremony took place at Furniture Makers’ Hall, London on Sunday 11th September, where Alison Gowman, Alderman and Sheriff of London, presented the Master with a donation towards the fundraiser and wished the team well on the trip.
Alison Gowman, Alderman and Sheriff of London, said: “It is a great initiative for the Master and livery members to undertake. I was delighted to wish them well as they set off and I know that all the hard work will result in funds that will be put to such good use.”
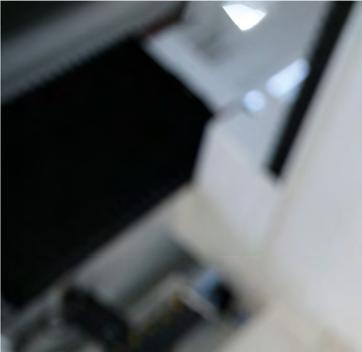
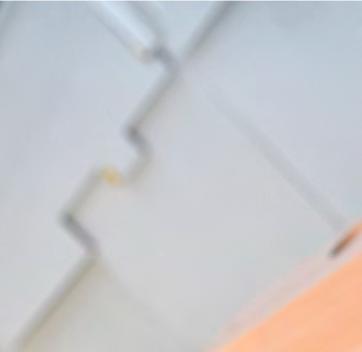
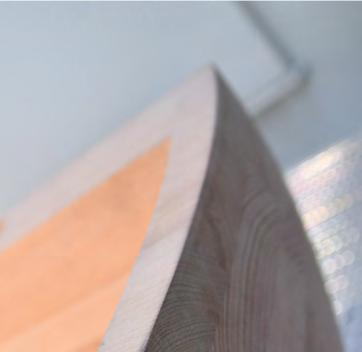
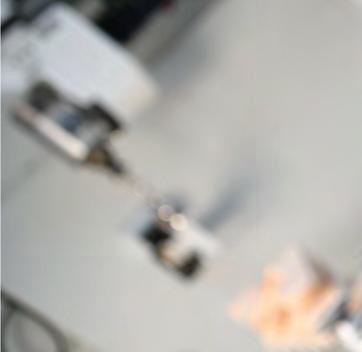
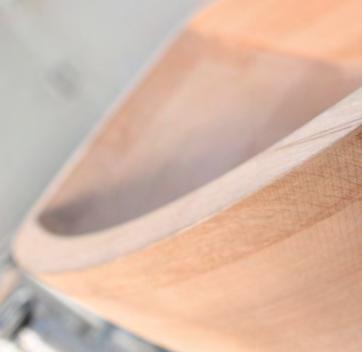
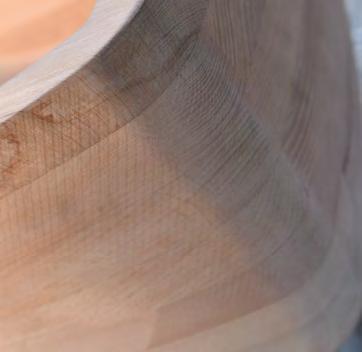

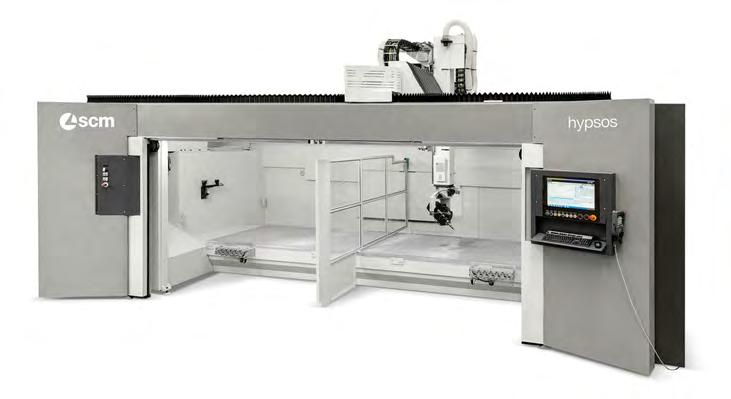
Waste not, want not
Chris Franklin, managing director of Ranheat Engineering, one of the UK’s leading manufacturers of wood-waste burning equipment. Continuing his series of articles exclusively for Furniture and Joinery Production. With the Government announcing that industry will receive help with it’s energy bills there is still a lot of uncertainty, how much and for how long?
Here at Ranheat we have seen a large increase in enquiries from both within and outside the woodworking industry. Ranheat systems can burn all types of wood and wood-based products.
This includes chipboard, OSB, plywood, melamine-faced chipboard as well as hardwood, softwood, pallets, and wood packaging. Outside the woodworking industry lots of goods and components are delivered on single use pallets that are not economical to return. Basically, Ranheat systems can turn this into useful energy.
Almost all companies in the wood working industry have some form of dust extraction system even if only simple bag extraction systems.
Companies outside the woodworking industry don’t have extraction. By using an auger feed from a wood granulator, nails and other metal fixings can be dealt with as there is no fire risk.
Some form of magnetic separator is a good idea and the steel from the nails is in quite a pure form so gets a high value as scrap metal.
With the end of the Renewable Heat Incentive, which was only applicable to boiler based systems, Ranheat has experienced increased demand for it’s warm air variants.
They are cheaper to buy and simpler to use and there is no
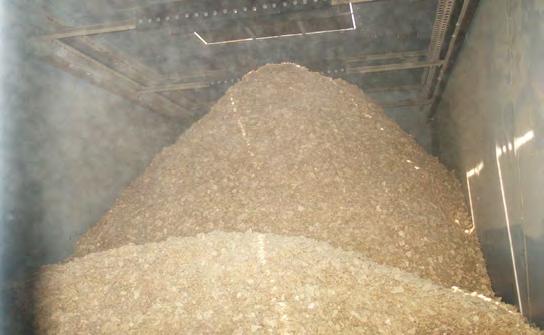
Granulate from a wood-chipper inside a bunker silo
fear of freezing the system during shutdowns such as over Christmas (most customers use them 24/7)
Warm air variants can be programmed to turn themselves down to run at much lower outputs outside of occupancy and then turn themselves up in time for workers’ occupancy.
Products manufactured from wood benefit from being kept at stable temperatures overnight and over weekends.
The warm air variants have a simple summer/winter divertor allowing the heat produced to be released to atmosphere. Still a better way to dispose of the woodwaste than sending to landfill. 01604 750005 sales@ranheat.com www.ranheat.com
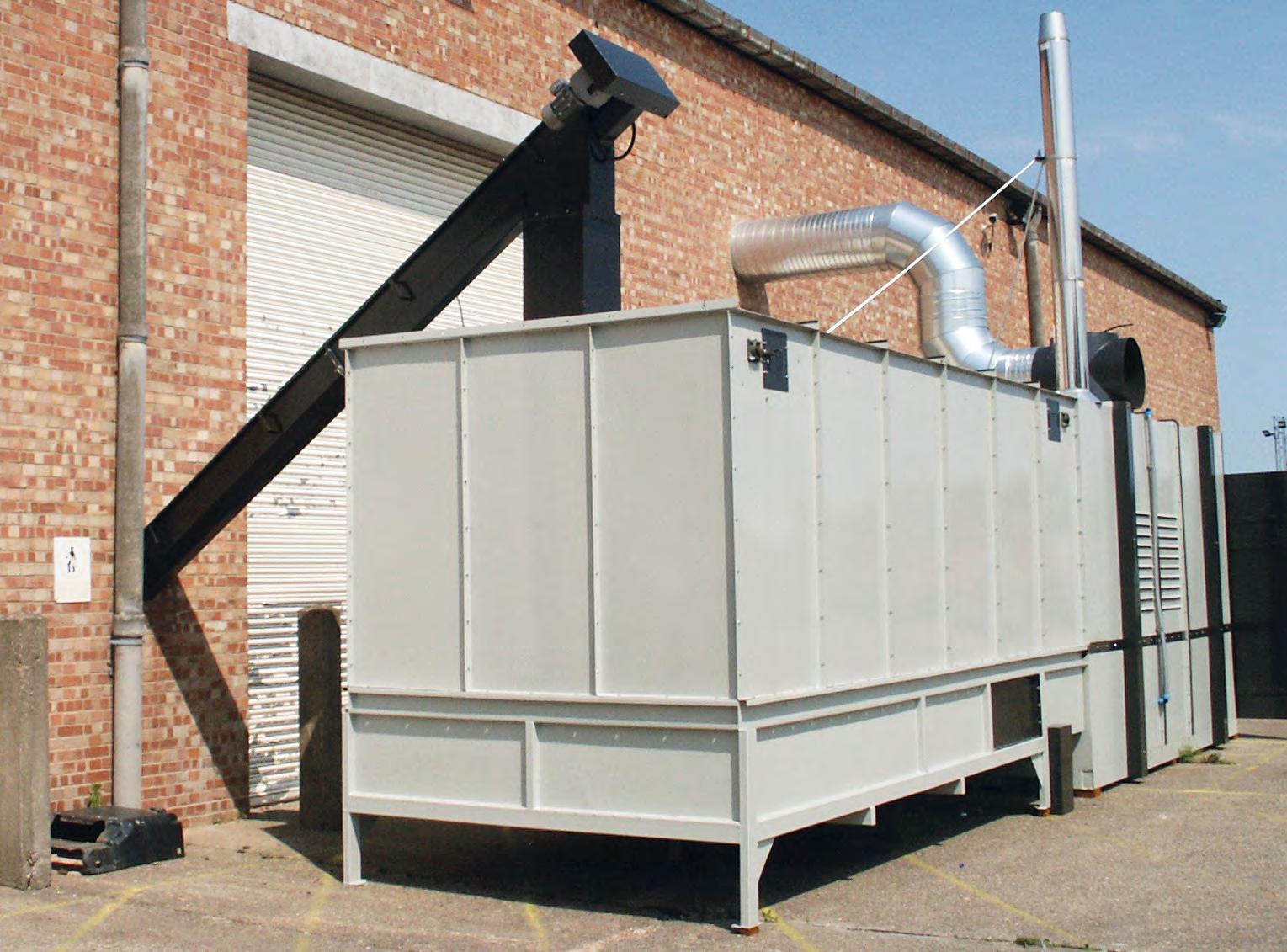
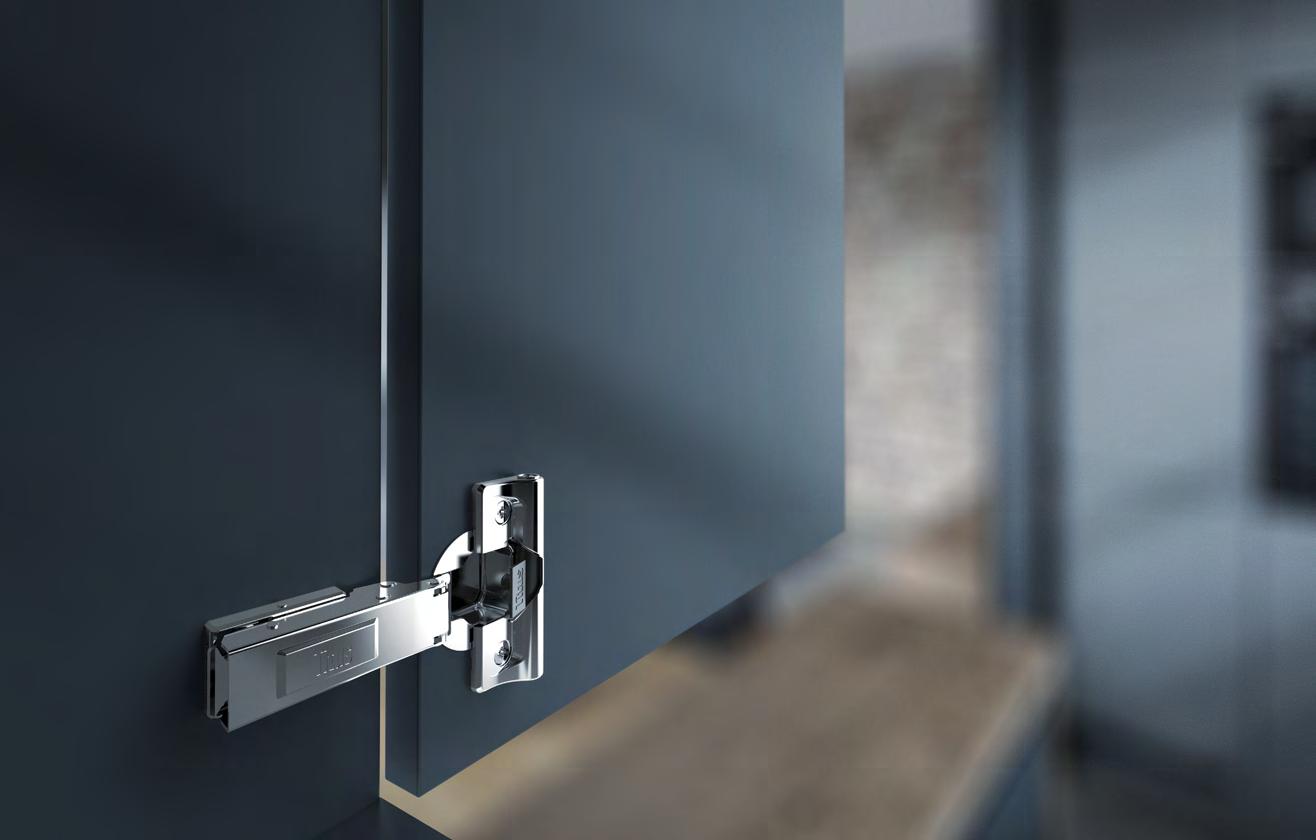
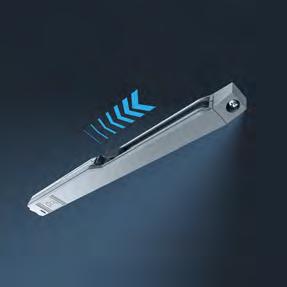
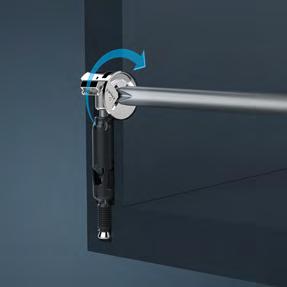

Record attendance at Daltons Wadkin Wood & Panel Machinery Show
Managing Director, Alex Dalton, is pleased to report a resounding success for this years Wood & Panel Machinery Show. A record number of companies and individuals where welcome across the three day event from all parts of the UK and Ireland.
“It was great to see so many visitors from such a wide range of industries; automotive, joinery, restoration, aerospace, rail, oil and gas, sawmilling, garden furniture, kitchen and bathroom, colleges, window and door… ”, enthuses Alex. “Customers were grateful for the opportunity to visit and discuss their individual applications. It was encouraging to gain such positive feedback on planned investment despite the media’s gloomy economic outlook”.
The Wood & Panel Machinery Show showcased the largest ever display of Salvador automatic crosscut saws in the UK. The SuperPush 200 and 250 models where of particular interest, pallet manufacturers and timber importers appreciating the overall build quality, ease of use and range of technical features included as standard. The everpopular Salvador SuperAngle 600 angle crosscut was on constant demonstration showing off its quick set, high accuracy, optimising and defecting ability.
It wouldn’t be a Daltons Wadkin show without Stenner. The ST100R band resaw remains the industry standard for customers wanting a no compromise resawing solution that will last for generations. The pitless design, high strain guidance system and automatic feed setting gives timber processors significant advantages over older models.
Elcon vertical panel saws where of great interest to panel processors, especially those cutting advanced materials such as GRP and other composites. Elcon’s patented Limpio dust capture system coupled with an iVision high powered extraction unit demonstrates how operator exposure to harmful dust can be greatly reduced.
Popular as always, the Kimla BPF industrial CNC router was running demonstrations on wood-based panels and plastics, showing how processing times and finish quality can be optimised through Kimla’s own CAD/CAM/ CNC control system. Exhibiting for the first time in the UK was the Kimla PowerCut fiber laser. “The PowerCut is of course for the sheet metal industry, but we knew many of our customers work with a wide range of materials and this too proved a popular exhibit”, comments Alex.
Sliding table panel saws from Altendorf and SCM were also on display, side by side. Visitors were able to directly compare features and specifications from these leading manufactures allowing them to make an informed decision with 100% confidence.
For all those that missed the Wood & Panel Machinery Show, fear not. Daltons Wadkin will continue to welcome visitors to their Nottingham showroom for working demonstrations on the latest technology from Europe’s leading specialist manufacturers. 0115 986 5201 www.daltonswadkin.com
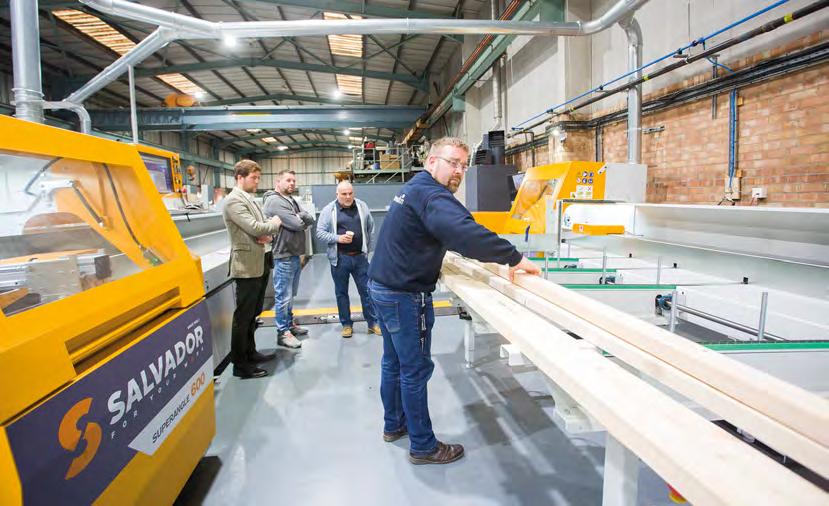
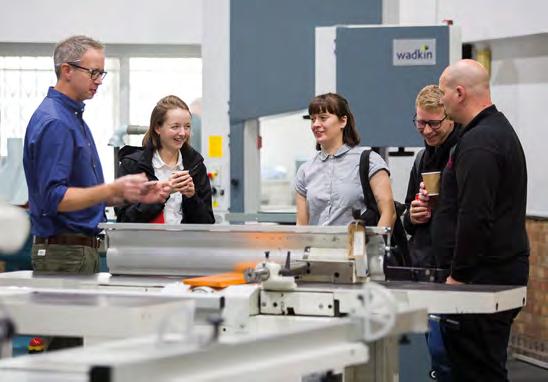
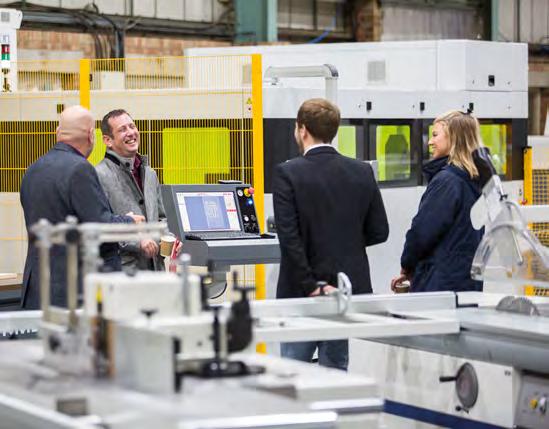
Visitor’s to Panelco’s Innovation Event treated to an array of innovative panel options
Panelco recently hosted a twoday Innovation Insight Event at its head office in Stoke-onTrent. The impressive event did not disappoint, packed full of innovative new designs and textures, many on display for the first time in the UK.
Partnering with three of Panelco’s major brands – Alvic, Egger and Unilin – this event was certainly an exclusive assemble with a considerable number of visitors from across the UK furniture manufacturing sector. The delightfully well-appointed Design Studio displayed 56 beautiful Alvic décors in large format style providing an impressive feature across the majority of the room.
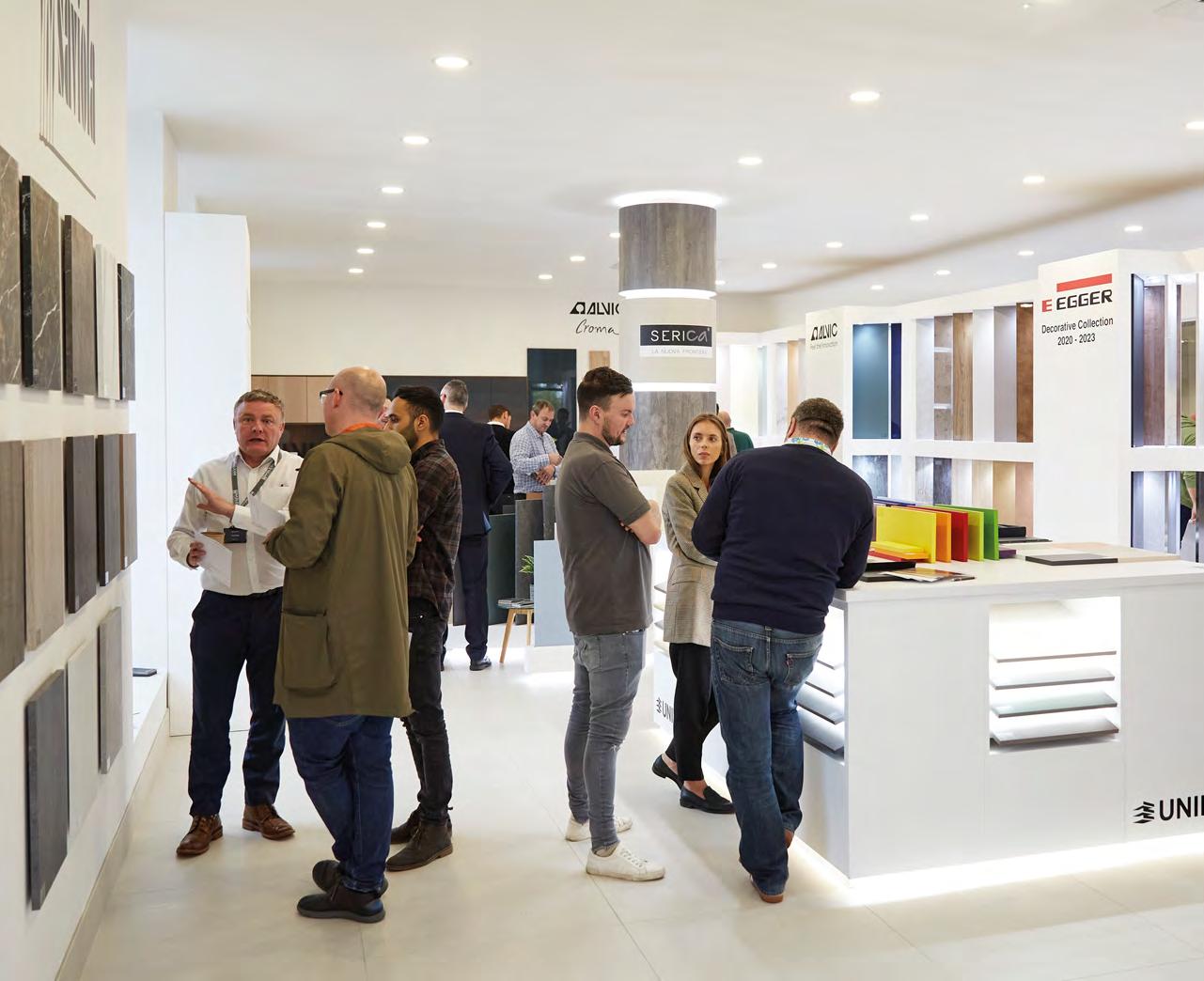
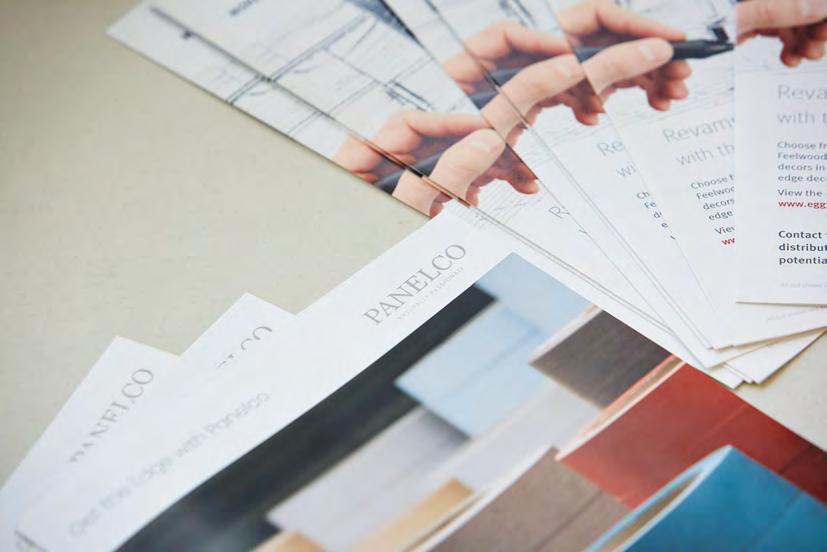
A diverse and throught-provoking range from Alvic really provides something for everyone – but not only that, there’s something unique for all. A full display of high gloss, high resistance panels, embossed surface textures, striking metallic elements and the soft, supermatt, luxury silk touch surfaces.
Across one wall the unique Croma sunset design was on show in a striking piece of furniture which really was a highlight.
Over on the other side of the Studio, Unilin displayed its UK decorative collection, comprising some 44 décors consisting of solid colours, life-like stone finishes, an intricate and highly fashionable weave texture, the singularly impressive new generation of Master Oak in various hues, and the fabulous new geometric Hive texture which – which proved a real hit with visitors.
The second Design Forum was utilised across the two days by Egger – and the room was

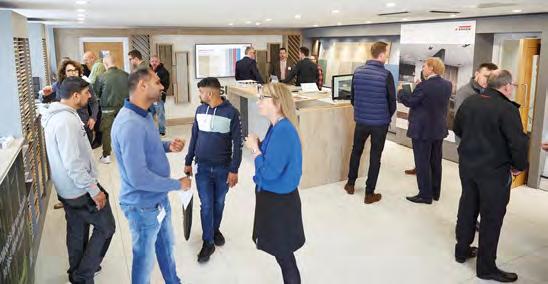
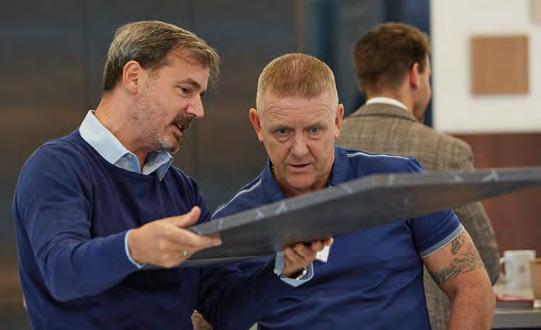
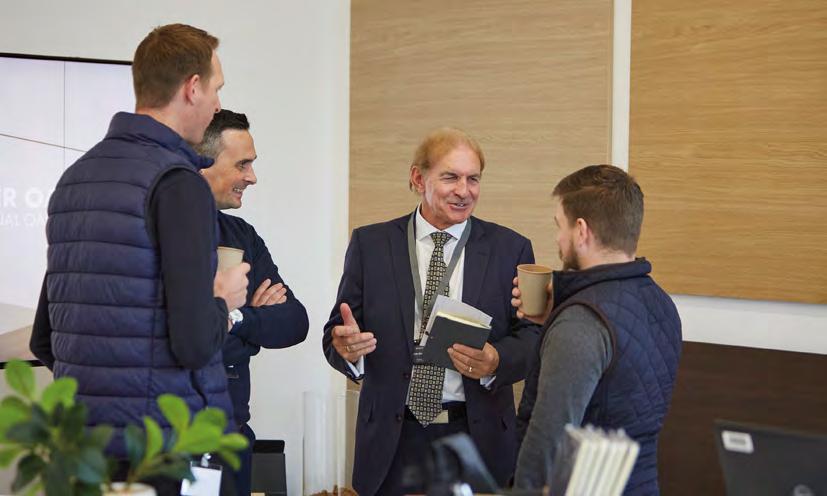
transformed with large graphics and mood boards detailing the new introductions, digital services on offer, recent upgrades in the Perfect Sense gloss laminate range, the advantages of choosing Egger’s Flammex range and an important focus on sustainability, something Egger has championed for many years.
Presentations took place across the two days where customers were shown the new additions to the decorative collection and the new TM9 Perfect Sense structure.
Panelco provided refreshments and tasty treats all day along with factory tours where customers were suitably impressed by the sheer breadth and mix of products across the site – and in such huge volumes too! And in true Panelco style, a thank-you gift bag was given to those who that attended.
The sheer hard work of the Panelco team, all the staff involved and their partners was obvious – and the event proved a considerable with meangful discussions throughout the two days. So much so that Panelco is already planning their next event in January 2023 – watch this space! www.panelco.com
£6.1m funding boost to accelerate digitalisation among furniture manufacturers
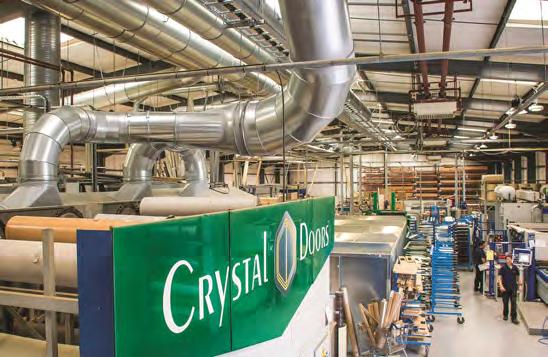
A trailblazing programme that has backed 2500 SME manufacturers to adopt new digital technology and skills to create growth and jobs has secured £6.1m funding to continue for three more years.
Made Smarter’s adoption programme in the North West has helped small and mediumsized companies start their digital journey by providing them with specialist advice and a digital roadmap to help them select the right approach, level of investment and tools for their business.
More than 250 of them, including several in the furniture sector, have invested in new technology, ranging from software and sensors to robotics and extended reality, to become more efficient, build resilience, increase their productivity and grow sustainably.
These include businesses like: Pendle Doors, based in Darwen; Crystal Doors in Rochdale; Inscape Interiors, a manufacturer of commercial cubicles, washrooms and fitted furniture, based in Chorley; and Starlight Bedrooms, based in Bolton.
As a result, Made Smartersupported manufacturers are set to create 1250 new jobs, upskill almost ,300 existing roles, deliver an additional £176m in gross value added to the region, and help the UK meet its net zero target by 2050.
Now with a further £6.1m funding from the government, Made Smarter can accelerate its drive to support hundreds more SME manufacturers to embrace the industry 4.0 movement.
Meanwhile, as a result of the trailblazing work in the North West, the national roll out of the Made Smarter adoption programme has continued, and now includes the West of England and East Midlands. They join the North East, Yorkshire and the Humber, and the West Midlands regions.
Alain Dilworth, Programme Manager for the Made Smarter Adoption Programme in the North West, said: “I am delighted that the Government has recognised the extraordinary impact that Made
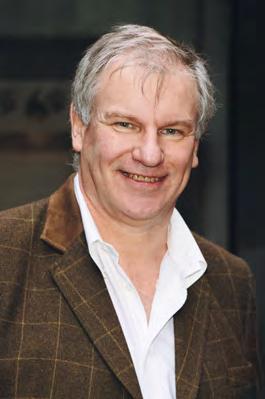
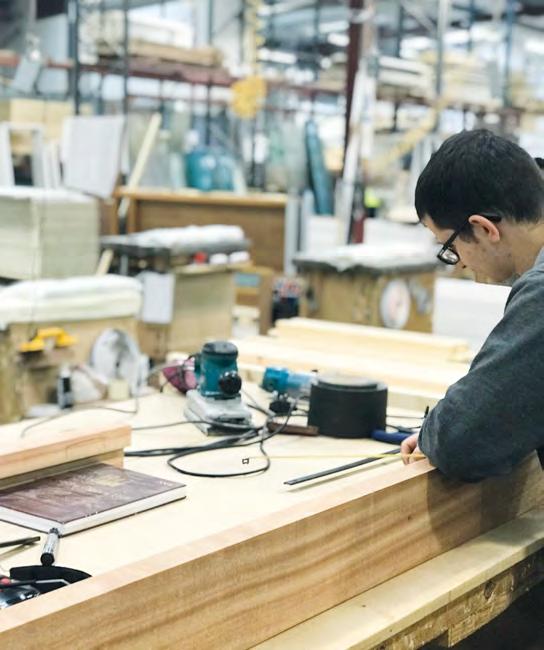
Pendle Doors, based in Darwen
Alan Dilworth, Programme Manager for the Made Smarter Adoption Programme in the North West
Smarter’s adoption programme is having on digitalisation of SME businesses and the adoption of Industry 4.0 technologies in the North West whilst continuing to fund our work for the next three years.
“While UK manufacturing navigated the pandemic and is working towards recovery, it is also bracing for further challenging times and economic bumps in the road ahead. Our rallying call to manufacturers is that digital technologies offer businesses opportunities to build resilience, innovate and transform. Digital tools can help manufacturers make marginal savings, set themselves apart from competitors in a volatile time, and make products quicker, affordable and more efficiently.
“This new funding means we can renew our ambition to reach out to the region’s SME manufacturers ‘Made Smartersupported manufacturers are set to create 1250 new jobs, upskill almost ,300 existing roles, deliver an additional £176m in gross value added to the region, and help the UK meet its net zero target by 2050’
to connect them to the tools that will make an everyday difference to their businesses, build resilience and enable them to keep up with a fast-moving industry.”
Made Smarter’s simple and straightforward approach gets quickly to the heart of a business’s challenges and supports them to take that first step in their digital transformation.
Registration takes five minutes and is followed up with a digital transformation workshop to identify core challenges and provide a bespoke digital manufacturing roadmap. Made Smarter’s team of expert advisors then pinpoint other ways that the programme can support a company’s digitalisation including skills and leadership development, and recommending the correct technology to invest in. www.madesmarter.uk
Toolfix celebrate 35 years of business
“A simple, honest and quality service that you can rely on” have been the values of Toolfix since it was first set up by Sydney Burt and his son David in the front room of David’s house in Peterborough in 1987.
The growth of the company has been on an upward trajectory ever since its inception, moving out of David’s front room to its first shop in their first year. The company quickly expanded, moving to larger premises three times with a small fleet of vans serving a local 30 mile radius, before moving to its current 10,000sq ft location in Newark Road, Peterborough in 2002.
The success of the company has been built on the foundations of hard work, providing expert advice and supplying customers as quickly as possible at the fairest prices.
The company is truly a family business with third generation Anthony the current MD along with his brother and director Nigel. They have more recently been joined by the 4th Generation of Burt family members with Carson and Conrad looking after sales and their sister Louella who is responsible for the company accounts.
While other members of the family have worked at Toolfix over the years, the growth of the company could not have been achieved without other members of staff and their contribution has helped Toolfix become what it is today.
There have been many changes since the company’s humble beginnings, the most significant of which was when Toolfix chose to serve customers further afield to become a truly national company and the decision to focus solely on the joinery industry.
This decision was made in part
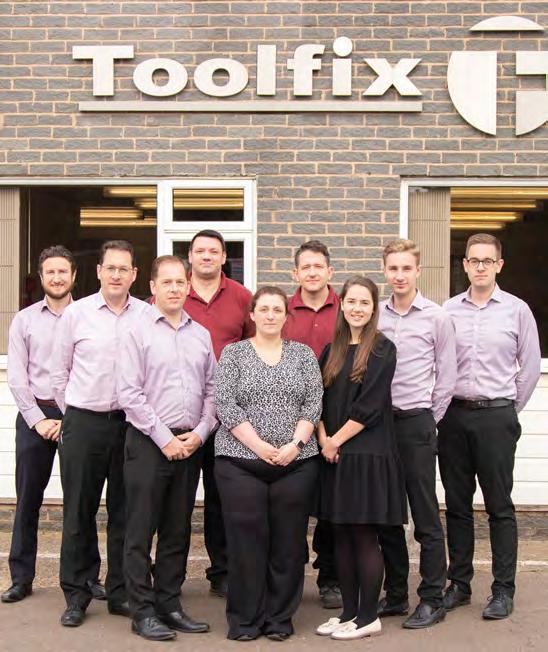
Toolfix Team Shot (L-R) Craig, Anthony, Nigel, Matt, Daniella, Marco, Louella, Conrad and Carson
Sidney and David Burt based on the wealth of experience the company had gained serving local joinery companies and it also allowed Toolfix to maximise and focus its resources, while stocking a wider range of products used specifically by the joinery industry, including door and window hardware, weather seals, cabinet and gate hardware and workshop consumables.
Today Toolfix serves joinery companies across the UK, many of which have been working with Toolfix for a number of years. One such company is Allan Brothers, one of the UK’s longest established joinery specialists.
“We like working with Toolfix as they are very reliable and prompt and they are always willing to source items that we need as a business. We find their prices very competitive, their staff are very polite and cheerful and nothing is too much trouble”
Not one to rest on their laurels, Toolfix continue to innovate and grow, most notably with the introduction of their own brands including Xylo, a range of joinery workshop consumables, Xylo-Fit, a range of cabinet fittings and Hardwick, a range of window and door hardware.
On the celebration of 35 years in business, Anthony Burt, commented “It’s our aim to lead the industry through exceptional service and innovation so that we can make it easier for our customers to do their job.
A lot has changed in the industry over the last 35 years and as a company we’ve evolved to meet the needs of our customers. As we move into the future, we will strive to continue the high standards set from when the company first started and to build on this with continuous improvements.
We don’t plan on standing still and are excited to build on our ranges of own brand products, while staying ahead of changes and trends in the industry, ensuring we continue to provide a simple, honest and quality service you can rely on.
I’d like to take this opportunity to thank all of our customers, past and present, without whom our success would not be possible.” www.toolfixservices.com
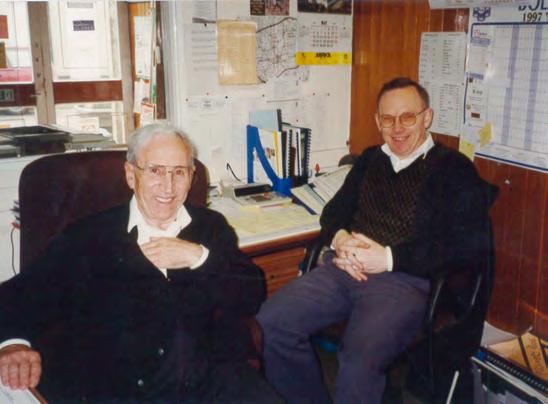
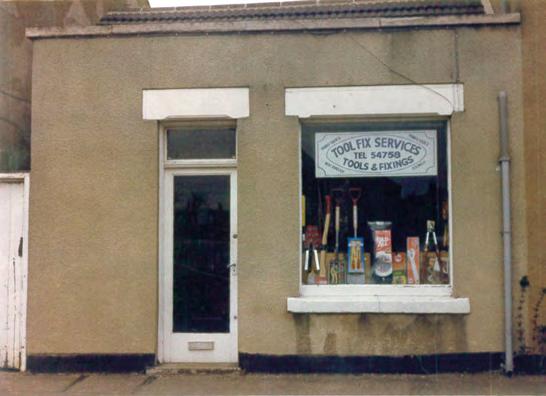