23 minute read
News
Next Article
Ligna 2021 moves to the autumn – clashing with The W Exhibition
Ligna has moved its May 2021 event to an autumn slot, from 27th September to 1st October 2021 – a timing which conflicts with the UK’s leading event for the furniture and joinery sector, The W Exhibition.
Following discussions, and in view of the current Covid-19 situation, Ligna organisers Deutsche Messe and the German association VDMA have jointly decided to push the Ligna event forward by five months.
“Due to the ongoing pandemic, increasing restrictions and the renewed lockdown, there is great uncertainty in the market. We take this very seriously,” emphasises Deutsche Messe managing board member, Dr Andreas Gruchow.
“The decision to postpone Ligna was a very difficult one for us,” he explains, “but it is the only consistent measure to give all those involved planning security and the necessary lead time for preparations. To ensure that Ligna, the world’s leading trade show for the sector, can live up to this expectation, suppliers and visitors alike must be given sufficient planning security for participation – and this is significantly higher for September/October than for May 2021”.
It will not have escaped the notice of many readers, but the timing of the rescheduled Ligna event is directly head-on with The W Exhibition, organised at the NEC in Birmingham during the exact same timeslot. With the W already 85% booked up, what will Ligna’s move mean for the UK’s key biannual event?
F&JP spoke with organiser Montgomery for a response. Commenting on Ligna’s postponement, The W Exhibition MD Nickie West says: “We have been made aware, alongside the rest of the market, that Ligna has announced the postponement of its May showcase to a new dateline of 27th September to 1st October 2021.
“Whilst The W Exhibition is very much a UK domestic show, meaning that we do not rely on international visitors, we will obviously explore the ways in which we can minimise any logistical challenges for our exhibitors.
“We do not yet know how foreign travel will be affected in 2021 by any continued Covid-19 restrictions, and the consequences of this on Ligna remains to be seen. What we do know is that there is a huge appetite for a UK show.
“This support has already been demonstrated across the industry, with The W Exhibition 2021 already 85% sold and an engaged visitor audience who are eager to reconnect with the market and see the latest products after
Deutsche Messe’s Dr Andreas Gruchow
an extended period of restricted face-to-face contact,” explains Nickie.
“We are in the process of conducting extensive discussions with the market and all of our stakeholders to help in any way possible to plan through any potential logistical challenges.
“Our exhibitors’ return on investment, along with the protection of The W Exhibition brand, are of paramount importance to us. We, in partnership with all our stakeholders, shall, as always, endeavour to make the right decisions for a successful exhibition, both now and in the future.”
F&JP understands that initial telephone discussions with key stakeholders have been coming back with positive responses.
www.ligna.de
Ironmongery Direct partnership
Leading ironmongery specialist supplier Ironmongery Direct has partnered with Checkatrade, a leading UK website for finding tradespeople, offering exclusive benefits for both new and existing Checkatrade members and Ironmongery Direct customers.
CSIL new online mattresses market report
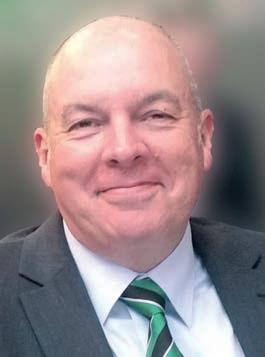
A new CSIL research report into ecommerce in the mattress industry offering a detailed analysis of the online mattress market, with a particular focus on three world areas – the Americas, Europe and Asia Pacific is now available.
January Furniture Show delayed
Event organiser, Clarion Events has rescheduled the country largest furniture trade show to 25-28th April 2021.
New Joinery Network website
As the growth of The Joinery Network continues, a new website has been launched to support UK joinery manufacturers looking to manufacture PAS 24:2016 Document Q-ready timber windows and doors. The new website has information on The Joinery Network’s range of fully tested, accredited timber windows and doors, Lignum, and is live at www. thejoinerynetwork.co.uk.
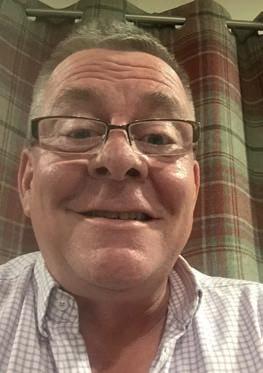
OBITUARY Kevin Lovell
It is with great sadness and heavy hearts that the team at Weinig UK confirm the sudden and unexpected death of our colleague Kevin Lovell. Kevin died peacefully in his sleep at home on Wednesday 22nd October, aged 59.
We, and many others, will miss him greatly. During a long career in the industry, Kevin established himself as a respected and trusted sales manager with a depth and breath of knowledge that enabled him to provide invaluable advice to many companies in the UK. His legacy will live on for many years.
Kevin was a private individual who genuinely enjoyed his life as a bachelor. Golf was an important part of his life outside of work, and he often told us his handicap was in single figures – “well, nearly,” he would say, with a wry smile so characteristic of his dry sense of humour.
OBITUARY Kevin Wright
Leadermac UK MD Kevin Wright sadly passed away on 22nd October.
Kevin was born in Walthamstow in London in 1964. He started work at Wadkin in London in the tooling room, moving to Wadkin Bolton in 1988 as a sales representative.
In 1991, he went to work in Singapore for six months as a sales manager, and on returning went to work at Calder Wilkinson in Sowerby Bridge as a sales manager.
Eventually, Kevin became sales director for Calder Wilkinson, and then in 2001 he left and established Leadermac UK.
Kevin will be missed by his wife Joanne and family, Tracey and the rest of the team at Leadermac UK. Fred, Kevin’s son, started working for Leadermac UK in 2019, and will continue to follow in his dad’s footsteps.
Leadermac UK would like to take this opportunity to thank everyone for their kind thoughts.

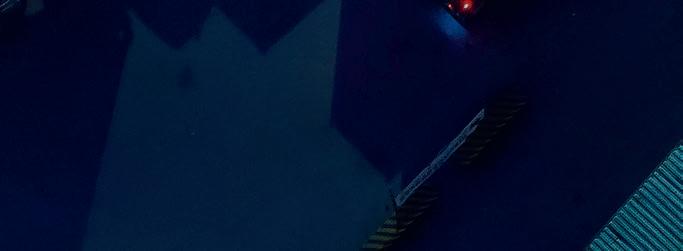
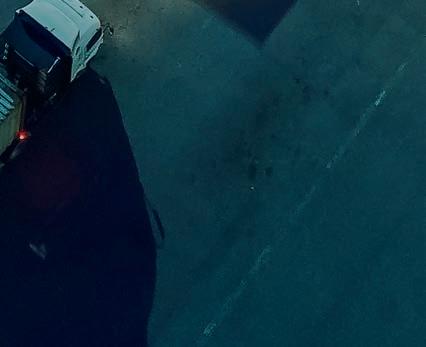
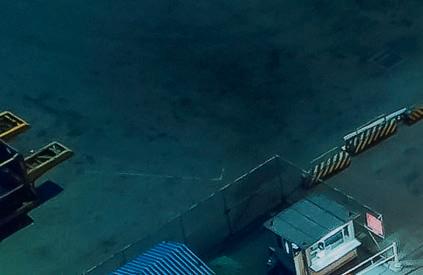

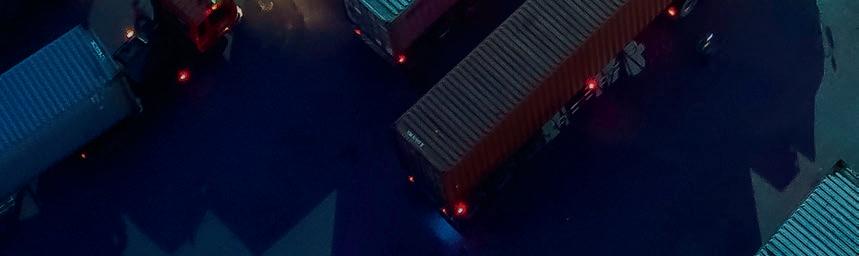
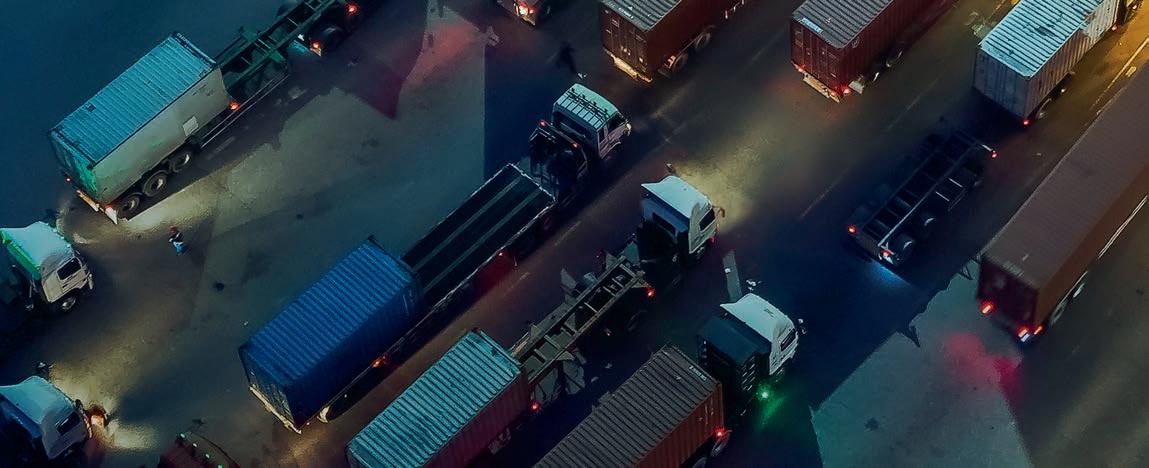

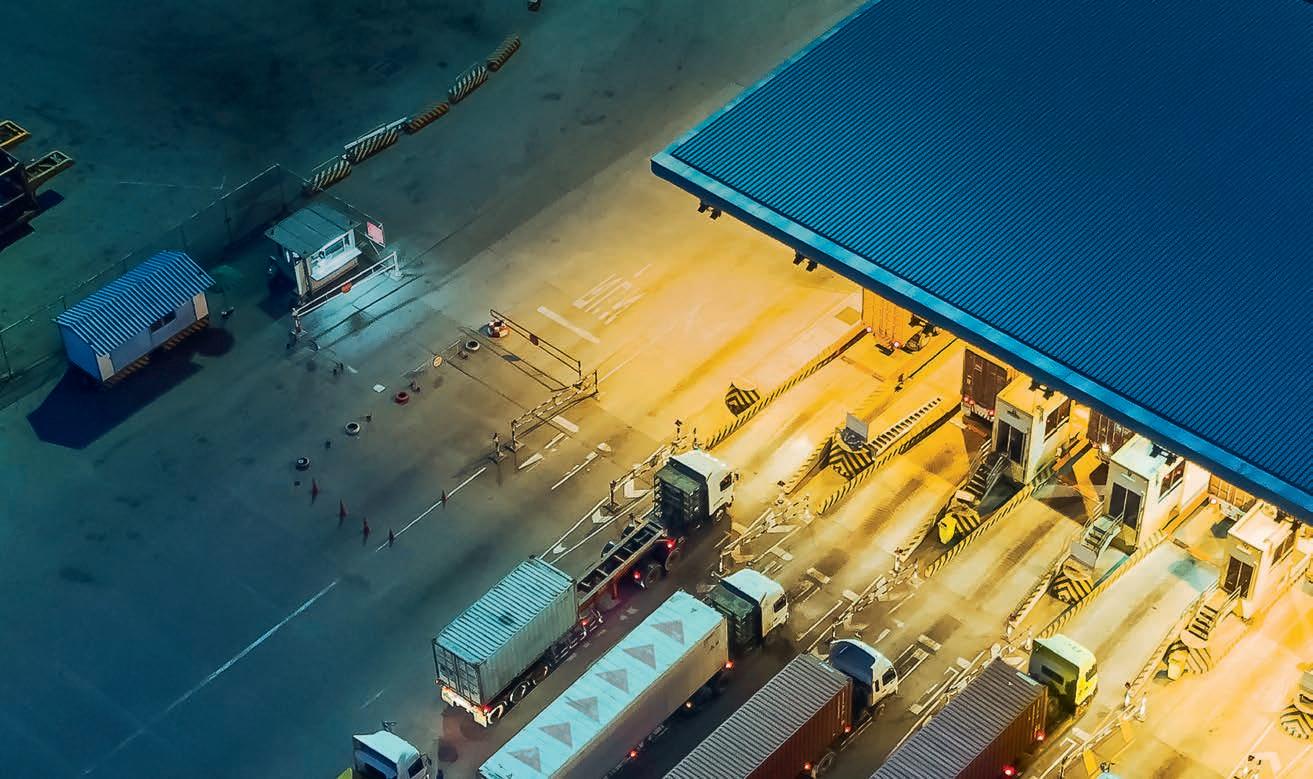
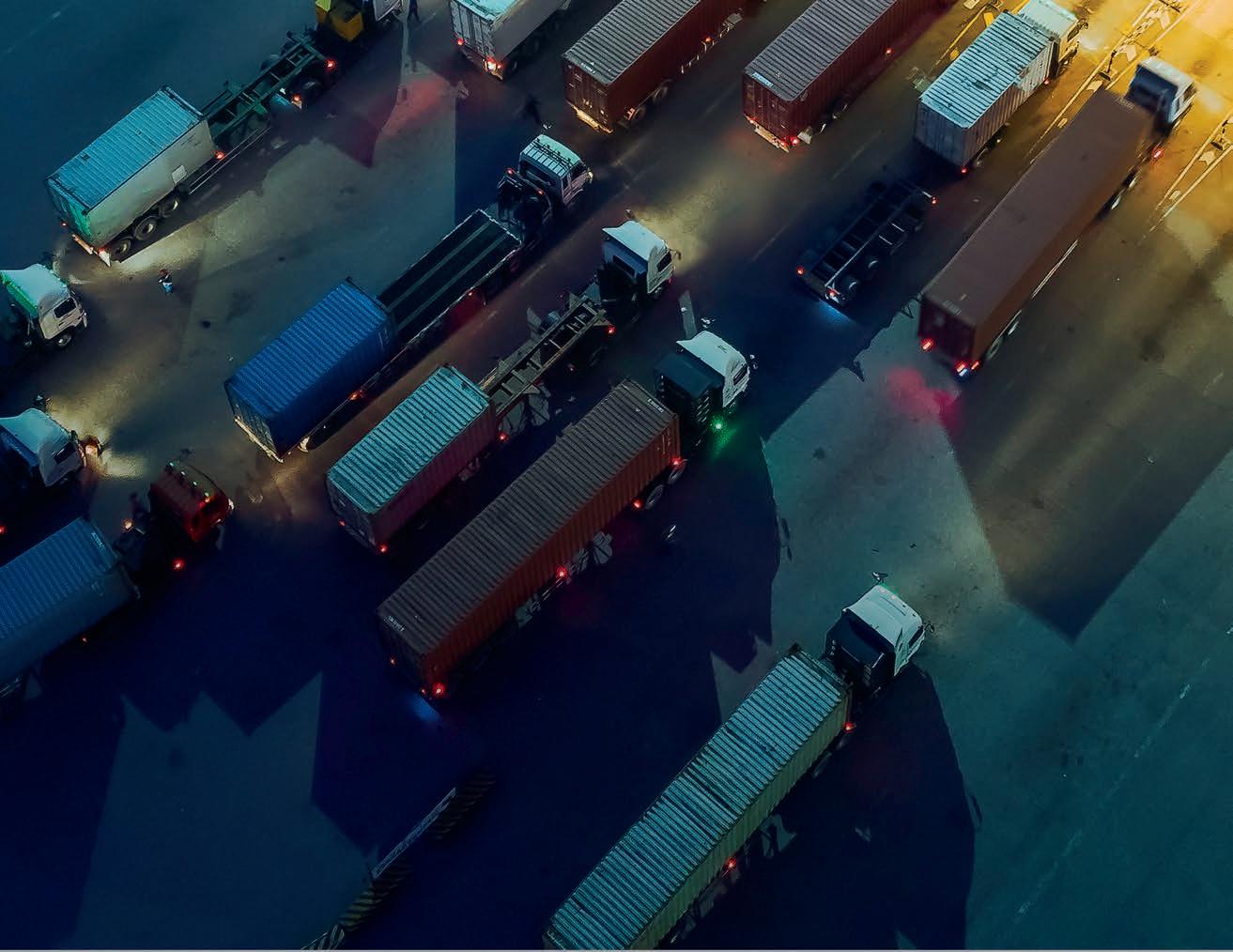
Gowercroft Joinery joins the Made in Britain campaign
Multi award-winning timber window and door manufacturer Gowercroft Joinery is teaming up with Made in Britain to celebrate its success as a UK business delivering high-quality timber windows and doors to its customers.
The Made in Britain campaign group was formed in 2011 with the aim of supporting British manufacturers, encouraging sustainable growth and helping consumers, buyers and specifiers identify genuinely UK-made products.
“We’re delighted to be part of this growing community of British manufacturers, dedicated to high standards of quality and performance,” said Andrew Madge, MD of Gowercroft Joinery.
Since it was formed in 1998, the company has gone from strength to strength, developing marketleading ranges of timber windows and doors, which combine state-of-the-art technology and high-performance materials with a traditional style of joinery and craftsmanship that is “perfectly suited” to UK homes and architecture.
The success of the company’s core range of Classic windows and doors has been followed by the launch of its award-winning Heritage range, developed for the UK building conservation sector, and the pioneering new Frontier range, designed specifically for the future-build market.
“As the UK window and door market has always been distinct to that of continental Europe, we believe it is all the more important that it is serviced locally, with product designs and detailing that reflect the unique heritage and architectural styles of the British Isles,” says Andrew. “Over the past decade, imports have taken a large share of the UK market, and this is threatening the authenticity and character of UK housing stock and the built environment.
“We are proud of our 22 years of uninterrupted trading in Derbyshire. Made in Britain membership is a demonstration of our commitment to high-quality British design and to the local and national economy, as well as a way of celebrating our success as a home-grown company.”
In recent years, the company has been recognised in several industry awards, including the Best Windows category of the 2017 Build It Awards and the prestigious 2019 British Woodworking Federation’s (BWF) Woodworking Project of the Year award, for its part in the restoration of Templeton House, Sir Winston Churchill’s former home in Roehampton.
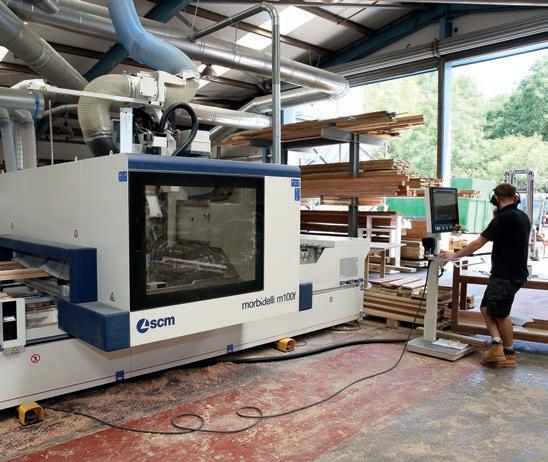
Mirka’s decade of tooling evolution
Mirka’s award-winning power tools division celebrated its 10th birthday in October. In the last decade, this team has been at the cutting edge of technology advancement, and has created the DEROS sanders, which it says are two of the most ergonomic and easy-to-use sanders on the market, and are amongst Mirka’s bestselling products.
The division, founded after the success of the CEROS in 2009, highlighted to Mirka that a dedicated power tools division was required to help anticipate and fasttrack the development process of future products.
Caj Nordström, product development manager, Mirka, says: “Developing new products and working with new technology has
Following the recent announcement from the UK Government and the World Health Organisation on Covid-19, TM Machinery thought it was important to update the industry on the actions it is taking to support its colleagues and customers over the next four weeks.
With strict health and safety procedures in place, it is “business as usual” at TM Machinery Sales and TM Services, whose machinery sales and serving division will remain open, and whose engineers will continue to install and service machinery in line with the latest Government guidelines, says the supplier.
This includes asking customers to respect social distancing measures when its engineers are always been my passion. Mirka is well known for manufacturing abrasives, but abrasives are only a part of the complete picture when it comes to sanding. They are best matched with tools that have been designed for them to give the best possible result, and as our engineers are not just theoretical people, we like to use the products ourselves.”
The power tools division has won many awards for its products over the past decade. Caj says: “Winning our first award told us we had gotten the design right. But the most important feedback, of course, comes from end users, who work with our power tools every day. The tool must be perfect for the user.”
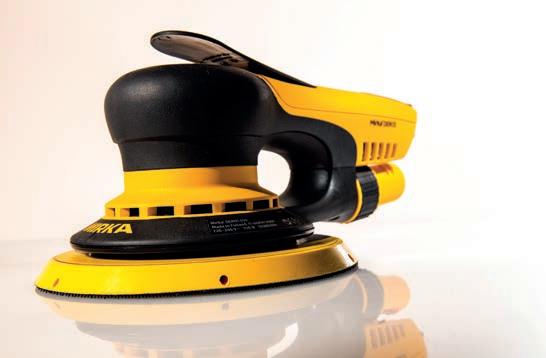
As with many innovative furniture and joinery manufacturers across the UK, Gowercroft regularly upgrades its capability as it responds to new market opportunities, and is proud to join the Made In Britain campaign
01773 300510 www.gowercroft.co.uk
TM Machinery – Covid-19 update
www.mirka.com
on-site, wearing face coverings, adhering to all hygiene advice and taking advantage of the company’s remote customer support offering wherever possible.
“We are dedicated to doing our part to help tackle this pandemic and, going forward, we will continue to adapt our procedures wherever necessary to keep our colleagues, customers and suppliers safe, whilst continuing to offer our customers the high level of customer service they expect,” says a spokesperson.
“We would like to thank you for demonstrating extra care and consideration at this time, and we will continue to monitor the Covid-19 situation closely and keep our customers up to date with any ongoing changes to our business.”
sales@tmservices.co.uk
Novel Vorasurf Silicone Surfactants combine performance and sustainability for bedding and furniture foam
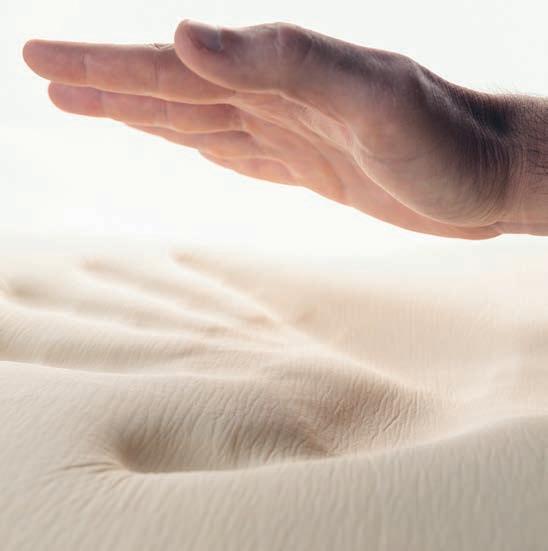
Flexible polyurethane foam formulators now have access to a set of higher-performing surfactant options for mattresses and other upholstered furniture, with an improved sustainability profile. Dow, one of the world’s leading materials science companies, has introduced the next generation of low-cyclics, low-volatile silicone Vorasurf Surfactants.
“Flexible polyurethane foam formulators around the world are facing growing demands from brand owners and consumers for improved physical performance and ergonomics, as well as enhanced health and sustainability profiles for their foams,” says Justin Weare, North America marketing manager for polyurethane additives at Dow.
“This new series of novel Vorasurf Surfactants is a testament to Dow’s commitment to bringing high-quality, profitable polyurethane surfactant technology to the foam industry that addresses both the latest market trends and technical requirements.”
Vorasurf Polyurethane Surfactants empower formulators with an enhanced level of control over the physical properties of their foam, helping them meet the latest specifications on volatile content and emissions required by leading brand owners – such as IOSMAT-0010.
These new-generation additives also allow formulators to easily comply with demanding regulatory and sustainability requirements around the world, helping ensure safe and compliant furniture products. The new Vorasurf Surfactant series includes: Vorasurf DC 5951LV Additive, an innovation primarily aimed at EO-rich, polyol-based MDI/TDI systems and low- to medium-density conventional foams, including those based on auxiliary blowing agents; Vorasurf FF 5959 Additive, a new-generation surfactant offering finer control over cell size and foam recovery properties in flexible foam applications; and Vorasurf DC 5906LV, Vorasurf DC 5950LV, Vorasurf DC 198LV Additives – all low-cyclics, low-volatile grades of globally recognised industry standards for bedding and furniture, including medium-high density conventional foams, MDI viscoelastic foams, and applications requiring excellent flame retardancy.
www.dow.com/vorasurf
The Joinery Network’s new website goes live
As the growth of The Joinery Network continues, a new website has been launched to support UK joinery manufacturers looking to manufacture PAS 24:2016 Document Q-ready timber windows and doors.
The new website has information on The Joinery Network’s range of fully tested, accredited timber windows and doors, Lignum, and is live at thejoinerynetwork.co.uk.
Owen Dare of O T Dare Joinery Consultants, one of the founder directors of The Joinery Network, says: “We launched the new website to make it easy for joinery manufacturers to see the range of tested timber windows and doors available, exclusively, for them.
“There is also lots of information on which tests our product range has passed. With this information, joinery manufacturers can choose the products they need, get licences for each product against each test result, and cascade the data to use as their own. This transparency means that both big and small joiners – offering a full or selective range – can fully comply with regulations without worrying about falling foul of the law.”
The new website comes after the launch of the exclusive Lignum range from The Joinery Network. Lignum is the first complete UK timber window and door system with full PAS 24:2016, Document
Following the latest announcement from the UK Government on Covid-19, Weinig UK is remaining open during the next phase of restrictions.
Continuing to adhere to its coherent in-house Covid-19 policy and the ongoing guidelines set out by the Government, Weinig UK’s sales, service and aftercare teams will continue to operate normally during the next four weeks. Engineers will also continue to install and maintain machinery, with site visits being assessed individually and machinery demonstrations taking place by appointment only.
Remote support continues to be offered to customers, with a technical hotline and online support Q, BS 6375: 1. Document L1B, and Document M certification, available to joinery manufacturers.
Owen continues: “Lignum is the exciting new window system for the timber window and door industry. Fully accredited and designed for UK homes, Lignum is perfect for joiners as a low-cost entry system through The Joinery Network licences.
“They also don’t have the expense of spending upwards of £60,000 on testing products themselves, as The Joinery Network has already made that investment. It’s an easy way for joiners to show that their products comply with Building Regulations, and win more sales.”
“We’ve carefully selected our founder partners and affiliates to offer expertise through every step of the supply chain. Many of them offer exclusive benefits to The Joinery Network licence holders, which we’ve featured on www. thejoinerynetwork.co.uk,” adds Owen.
Joiners can find out more at
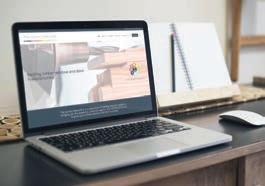
Business as usual for Weinig UK
www.thejoinerynetwork.co.uk
services readily available, and a newly launched webshop for quick and easy ordering of spare parts around the clock.
Malcolm Cuthbertson, MD of Michael Weinig (UK), says: “Weinig UK remains committed to ensuring the ongoing health and safety of our staff, customers and suppliers. By introducing a strict Covid-19 policy and continuing to assess and adapt our procedures wherever necessary, we are doing our utmost to stop the spread of the virus, whilst continuing to offer ongoing support and vital services to our customers. We thank everyone for adhering to these measures and for demonstrating extra care and consideration at this time.”
www.weinig.co.uk
Make UK calls on manufacturing to help kickstart young careers
Businesses who think they cannot take advantage of the government’s new £2 billion Kickstart training scheme can still take part through a gateway body, says Make UK, the manufacturers’ organisation.
The Government Kickstart Scheme will provide funding to employers to create job placements for 16-24 year olds. The scheme will create new six-month placements for young people who are currently on Universal Credit and at risk of long-term unemployment.
A business can only sign up to the Kickstart scheme if they have a minimum of 30 job placements to offer - however approved gateway organisations, such as Make UK, can apply on the behalf of a business if they require less than 30 placements.
Stephen Mitchell, (below) director of apprentices and technical training at Make UK’s Technology Hub in Aston, Birmingham, said: “We know manufacturing, and understand that right now it may be difficult for employers to take on an apprentice. But these fullyfunded work placements provide manufacturing extra support that they may currently need and a young person a chance to develop skills and experience they need to find work after completing the scheme.
“Working with a gateway organisation such as Make UK has multiple benefits - you don’t need
Emuca is promoting its growth by increasing the size of its logistics centre at its central headquarters in Valencia, by acquiring a new 7000m2 warehouse adjacent to it.
With this new facility, Emuca will increase its size to 32,000m2, with a total capacity of more than 35,000 pallets, combined with the logistics centre in Padua (Italy).
Emuca has made this investment in order to continue providing the best service to all its customers and to continue adding capacity to its logistics operations. This investment will enable Emuca to cover the increase in orders and customers in its key markets Italy, to have 30 placements, and we can make the process a lot easier and do much of the groundwork, including supporting you through the selection process, providing training and working with the young person to help them into a job or apprenticeship after the placement. We understand the requirements of manufacturing and how to get the best out of a young person.” The government will fully fund each ‘Kickstart’ job, paying 100% of the age-relevant National Minimum Wage, National Insurance and pension contributions for 25 hours a week. Once a job placement is created, it can be taken up by a second person once the first successful applicant has completed their six-month term.
For more information on the Kickstart program, call Make UK on 0121 344 7903 or email kickstart@makeuk.org
France, the UK, Poland, Portugal, the Benelux and Spain.
Emuca firmly believes in the development of its digital transformation process, having achieved two important milestones – 70% of its customers’ orders are received through its B2B platform, and, reinforcing the internationalisation of the brand through its digital channels, its YouTube channel has reached two million views.
Emuca is aware that the current and future challenges would not be possible to confront without a multidisciplinary, professional and involved team like the one it boasts.
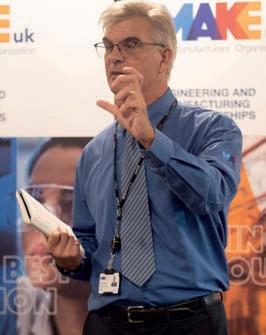
In February this year, Cleaf and Egger presented together at Euroshop in Düsseldorf
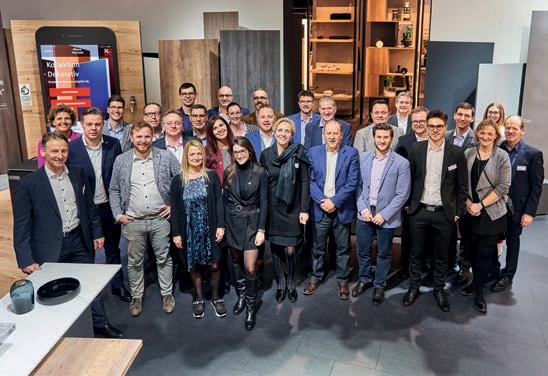
Enhanced co-operation – Egger to acquire minority stake in Cleaf
Cleaf and Egger, two manufacturers globally active in the sector of surface materials for furniture and interior design, enhanced their co-operation, with the signing of an acquisition agreement in September (expected to close this month), in which the Austrian Egger Group will acquire a 27.5% stake in the Italian Cleaf.
Cleaf and Egger entered into a partnership about a year ago as an expression of a common vision and mutual respect between the two family businesses. As previously announced, the sales partnership will now be followed by the next step – Egger will acquire a minority stake of 27.5% in Cleaf. The parties agreed not to disclose the value of the transaction.
“We have always pursued the vision of broader co-operation. Our co-operation in sales has shown that together we can offer our customers the best of two worlds,” comment both companies. The majority shareholding in Cleaf will continue to be held by the Caspani family. Egger emphasises that it does not intend to acquire a majority stake in Cleaf in the future.
Successful sales partnership
About a year ago, the two companies announced the ‘Cleaf presented by Egger’ collection for six European markets. Since its launch together with the Egger Decorative Collection in February 2020, customers in Germany, Austria, Switzerland, Poland, the Czech Republic and Slovakia have shown great interest in this range. The two companies also presented themselves at the Euroshop in February in Düsseldorf, on directly
Emuca expands logistics centre at its headquarters
connected exhibition stands.
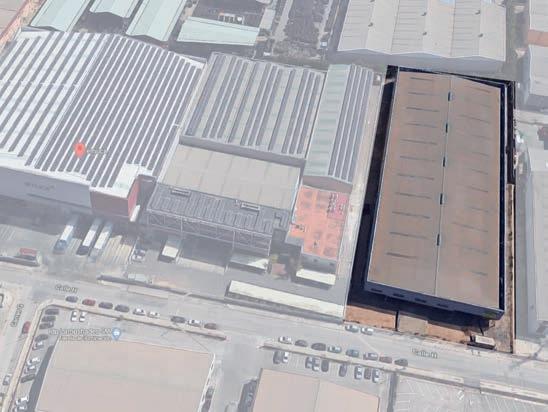
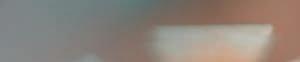
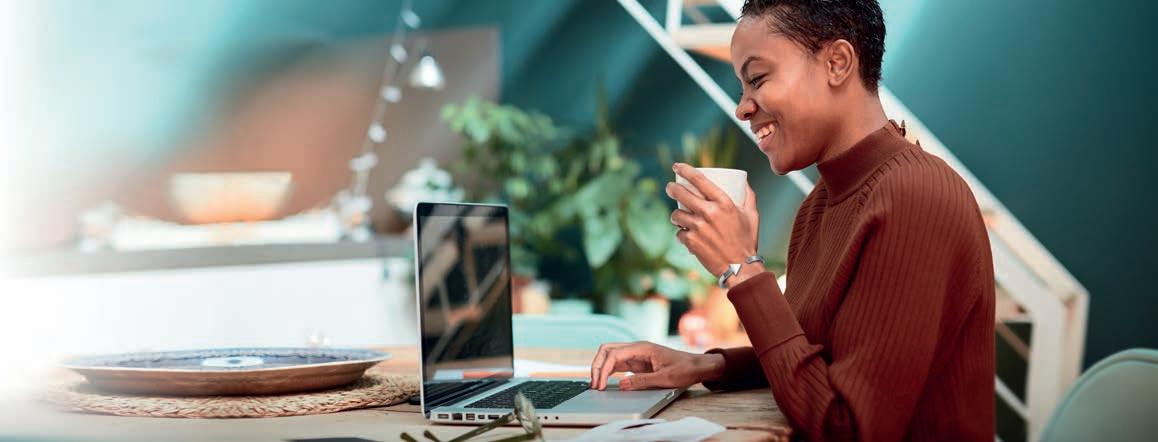
Hypnos achieves ISO standard for quality management
Royal warrant holder and award-winning British bedmaker, Hypnos, has announced that its Castle Donington site has achieved compliance with ISO 9001, the international standard that specifies requirements for an effective Quality Management System (QMS).
This ISO 9001 accreditation is further proof of the company’s commitment to top-class design and craftsmanship, and to ensuring its operations are run with high-quality systems and assurance in place.
The standard means that the company’s Castle Donington site delivers to a consistently high-quality level and standard, and continually measures and improves every aspect of its operations.
Darren Machin, quality and facilities manager at Hypnos, says: “Delivering the most comfortable beds, made in an environmentally and socially responsible way, has been at the heart of what we do for over a decade.
“By gaining ISO 9001 accreditation and assurance, we can prove to our customers that we always strive for our products and service to meet the highest expectations and consistency in our sustainable designs and production. So, whether it’s pushing the
Due to restrictions across the UK and the re-imposition of lockdown in England through to December has led January Furniture Show organiser, Clarion Events, to reschedule the event to 25-28th April 2021.
Cleere Scamell, event director, says:,
“The furniture show at the NEC is the most powerful UK trade event of its kind. Over the past months we have been working towards
January, determined to deliver the strong show the sector needs. The large footprint of the show, combined with a very targeted professional audience, means that we remain
UKAS-accredited testing house, FIRA International, has launched E-TIC HUB, a new portal designed to give customers more control over their testing.
The E-TIC HUB allows customers to: request quotes for all types of furniture testing with FIRA International; accept quotes and arrange for samples to be booked in; follow the progress of specific tests, with full visibility of where the sample is in the testing process, with 24/7 access to check progress and alerts as each testing stage begins/ends; access and direct download of test reports; and instant messaging with the experts at FIRA International.
Furthermore E-TIC HUB is GDPR compliant, boundaries of bedmaking to achieve the best possible design, considering the environmental impact of everything we do, or caring about the people we work with, our customers can have the utmost confidence that they will truly have a comfortable bed made with the utmost integrity when they purchase from us.
“Our dedication to crafting quality mattresses confident in being able to fully implement the Government’s All Secure Standards guidance for event safety.
“However, recent developments, combined with the necessarily long lead times exhibitors need to prepare and present their products, mean that it is important for us to be realistic, and put safety first at this stage. Additionally, after a turbulent year globally there are significant supply-side issues in parts of the furniture sector, and this move will allow more time for material supplies to normalise.”
Cleere continues: “Over the past few weeks and Quality System Compliant with BS EN ISO/ IEC 17025:2017, in line with UKAS requirements.
Howard James, testing and technical manager at FIRA International, says: “E-TIC HUB forms part of our overall strategy of improving our operational excellence, and developing a bespoke hub was an improvement a number of our clients had requested to enable them to gain more control over their testing, and to simplify how they work with our testing experts.
“I’d like to thank our clients who supported us as we developed E-TIC HUB – their feedback was invaluable in shaping the hub to ensure it delivers what the industry needs regarding testing, which can be complex at times due the and beds has been at the heart of our business for over 100 years and it’s this ongoing commitment that has seen us collaborate with suppliers to source more traceable and certified materials in our products.
“Qualifications such as this really do play such an important role in the development of a business, helping to drive training and learning, and reinforcing rigorous inspection standards by the quality team. It very much aligns with the dedication, care and authentic craft of bedmaking that our entire workforce has, so we’re very proud to have achieved it.
To gain the accreditation, which reinforces the trust Hypnos has earned from supplying homes, hotels and palaces around the world, the company had to assess every area of its hospitality business and manufacturing processes at the Castle Donington site, and develop formal procedures to continuously improve its operations and ensure excellence at every level.
As a result of this ongoing attention to detail and quality, Hypnos is able to assure consistency across its sustainable designs and its methods of production.
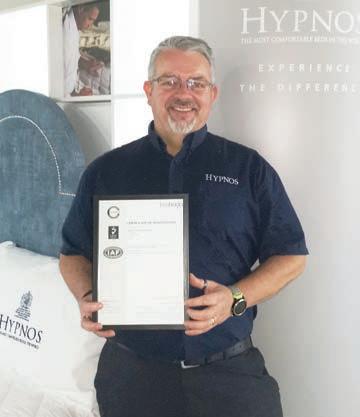
January Furniture Show postponed until April 2021
www.hypnoscontractbeds.com
we have been surveying furniture and interiors buyers across the sector, and I am pleased to share that we have had a very strong and positive response from regular visitors, who are in favour of moving to April. 84% of buyers say they will certainly attend, and a further 13% plan to attend when they have more details about the practical Covid measures in place.
“We are also in the process of connecting with exhibitors, visitors and other industry stakeholders, and this will continue over the course of the next few weeks as we finalise
FIRA International launches new portal to simplify testing
plans for Furniture Show Birmingham in April.” standards and regulations which govern the furniture market.
“This is just the first-phase launch for the hub – we’re already working hard behind the scenes on the next release, which will include a full reporting suite with details on test times and results analysis, the opportunity to schedule tests direct to machines in advance and invoicing functionality via the hub.”
To request a login, FIRA International customers should contact info@fira.co.uk. The hub can be accessed via https://portal.fira.co.uk.
FIRA also confirmed that it would be running MS Teams sessions to support users new to the hub, with details on request via info@fira.co.uk.
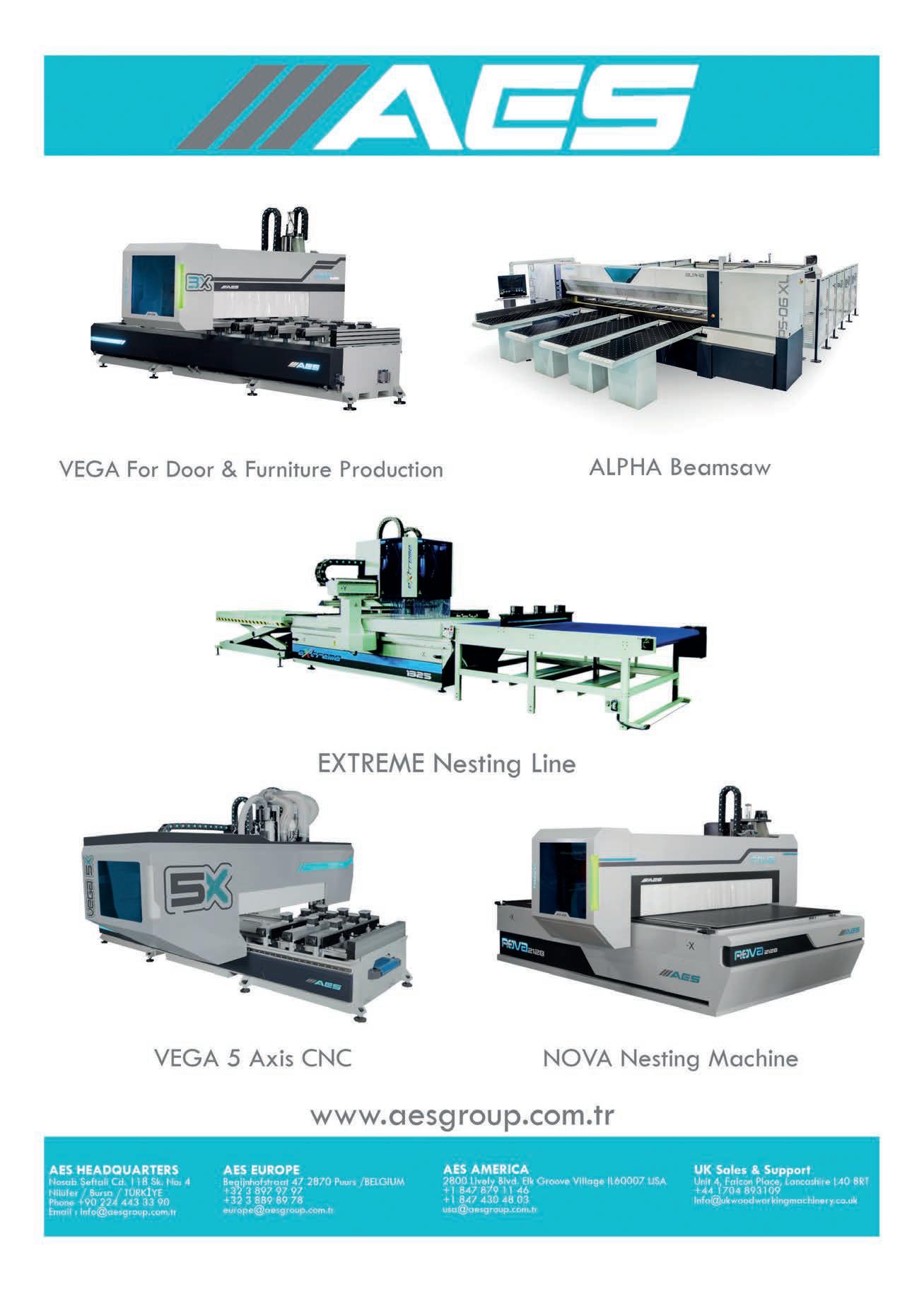