6 minute read
Insight
Next Article
What type of racking do I need?
For over 55 years, family-run firm Stakapal has produced storage and racking for warehousing and manufacturing industries across the UK. Nick Betteley, technical director at Stakapal, advises what to consider when choosing racking for your warehouse.
When it comes to selecting the correct storage option there can be numerous challenges. In furniture and joinery manufacturing there are many different lengths and quantities of products which are difficult to store. From panel products and sheet materials to softwoods and hardwoods, you need to maximise the available space in your building, increase throughput and also minimise stock damage. You need to consider the type of mechanical handling equipment you are using, plus the available storage options for any handloaded product ranges.
Stakapal’s own in-house design and project teams have provided a range of turnkey solutions for the industry. We are the only manufacturer to produce cantilever racking and pallet racking, as well as a full range of warehouse racking systems, from within the UK.
Whatever you are storing we offer a solution: Cantilever racking
When storing long lengths of product, cantilever racking offers the perfect solution. This type of racking consists of vertical upright columns with arms attached at variable heights. Arms can be adapted to accommodate specific load bearing requirements and designed to suit any pack size to fully maximise the available area.
Single-sided racks can fit flush against the wall, while double-sided configurations create storage on either side of the central column. Our full range includes conventional, free path and guided aisle cantilever racking.
Pallet racking
Our Stakrak SR2000 series pallet racking offers a low budget alternative for storing low volumes of panel products and sheet materials. Our comprehensive range of rack frames and beams ensure that there is a solution for any storage challenge. system stores vertically with the item’s length resting on a sloped frame shaped like an ‘A’. It can be configured as single-sided for storing against a wall or double-sided if you have available floor space.
Pigeon hole racking
For relatively small, hand-loaded quantities, our pigeon hole racks make it easy to access specific product ranges which are stored horizontally in separate compartments. The pigeon holes are divided by vertical beams which can either be fixed in place or adjustable dependent upon storage needs.
Safety first
The manufacturing industry is safety conscious, and we support this through our membership with SEMA (Storage Equipment Manufacturers Association) – a leading voice within the warehouse industry.
As full members of SEMA, our products are independently tested, which guarantees they have been designed, manufactured, and installed to rigorously defined standards.
Stakapal’s commitment to safety continues by ensuring that our in-house installers working on your site are registered and put through SEIRS (Storage Equipment Installers Registration Scheme) – a unique initiative from SEMA which trains on the safe and correct way to install racking.
Racking systems qualify as work equipment and, under PUWER, it is your responsibility to ensure they are in good working order. The HSE recommends using a SEMA Approved Racking Inspector (SARI) who is trained and continually assessed to industry standards. Following the installation of our racking, our own in-house SARI’s offer this facility to our customers on an annual basis. We visit each site to undertake a comprehensive inspection and prepare a detailed report. 01543 278123 sales@stakapal.co.uk www.stakapal.co.uk
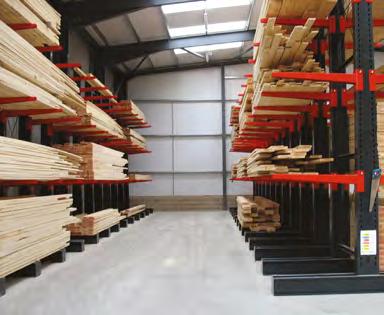
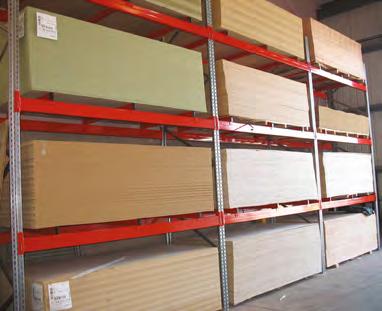
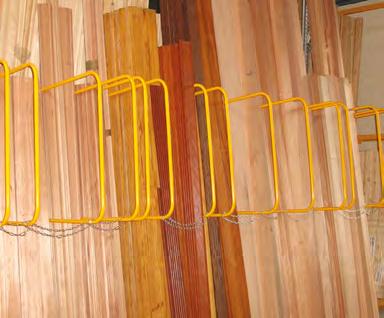
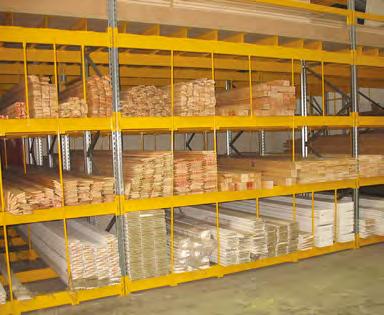
Simplify your design to manufacturing workflow with Microvellum
In such a fast-paced world, homeowners and architects have come to expect quick turn arounds on projects – not only do they want their projects done ahead of schedule, but they also expect you, as a manufacturer, to respond quickly to their changes and demands for mass customisation. According to Daniel Mesecke, account manager for Microvellum, many manufacturers rely on several different design and manufacturing software applications. For some, it can be difficult to keep up with change requests and remain profitable.
“I speak with a lot of manufacturers that depend on multiple steps to complete a project, utilising several different software applications and processes,” says Daniel. “This may involve creating estimates in one software, drawing projects in CAD software such as AutoCAD, engineering products in a separate cabinet or modeling software, creating CNC machine programs in yet another disconnected CAM program and relying on other software or manual processes to fill in the gaps before products can make their way into assembly.
“For some, this system may work, but most will admit they don’t have the power to accelerate the way they need to grow their company.”
Microvellum specialises in helping woodworkers streamline the way they work with one solution. Users of Microvellum’s AutoCADbased software rely on one platform for the entire design to manufacturing process. All project data is stored in one central database that can be accessed for estimating, design, drafting, engineering, production data and reporting.
“Imagine a solution where your team is all working from the same data,” continues Daniel. “Your drafting team is using the products that your estimators configured and included in “When you align your team behind one platform that has the power to streamline the way your team works, you remove friction, lower risk and increase your profits”

their bid – the same ones your engineers built for mass customisation. Now, imagine being able to advance the projects to your factory for production from one application. This is what you get with a Microvellum solution.
“And when that inevitable request to change one or more a product sizes or configurations comes, imagine having a platform where all your changes are kept in sync automatically – 2D drawings and sections required for architects or homeowner approval are updated, 3D models are modified so you can visually verify that your modifications are what your client expected, machine tool paths have been adjusted and all other data needed for reporting and production is updated. All you need to do is reprocess the project.
“Now, think about what would need to happen to make those same modifications when you use three, four, or possibly five separate applications.”
Microvellum’s platform combines the power of AutoCAD® and the flexibility of Excel® – enabling users of the system to have complete control over the parametric intelligence built into every product – features such as 2D drawings and sections, 3D models, construction options, machining, hardware and warning messages. Users can make use of the extensive cabinet, wardrobe, fixtures, toilet partition and office furniture libraries as is or choose to customise or build their own unique products.
“I like to tell people that, remaining profitable is about lowering risk,” concludes Daniel. “When you align your team behind one platform that has the power to streamline the way your team works, you remove friction, lower risk and increase your profits.”
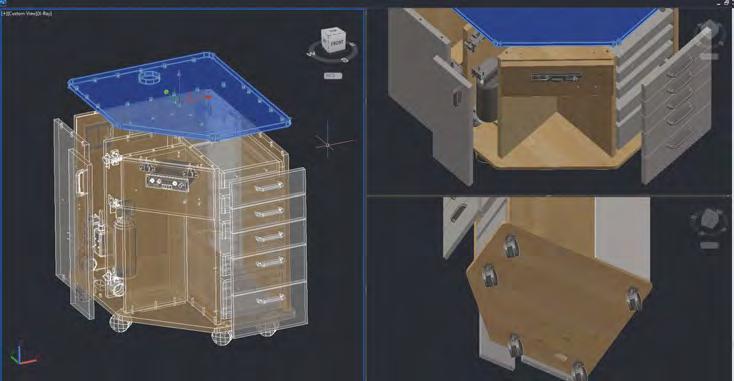
To learn more about Microvellum or to request a free assessment of your design to manufacturing workflows, visit www. Microvellum.com.