9 minute read
SCM
Next Article
SCM’s seven decades on the leading edge
SCM celebrates 70 years of edgebanding alongside state-of-the-art companies in the furniture and design industries
SCM has been an authentic edgebanding specialist for 70 years – a historical and reliable partner to globally renowned, prestigious companies that keep a close eye on the latest furniture and design trends.
SCM’s range of edgebanding and squaring-edgebanding machines is vast, and capable of meeting any production demand – from the artisan company keen to ensure quality machining, to important industries requiring high-automation solutions to handle processes that are increasingly becoming faster while still being flexible.
The main new entries for 2020, and key players in the recent SCM Live Show event, clearly reflect this extensive variety of technological solutions, within the reach of the entire woodworking industry: increasingly more sophisticated productivity, thanks to the integration of the edgebander or squaring-edgebander in cells and plants fitted with rollers, panel return devices, automatic loading and unloading systems, assisted by robots and fitted with IoT sensors to provide instant feedback on the machine’s functioning, in line with Industry 4.0 requirements; a unique machining accuracy and quality on any kind of panel, even the most delicate ones and with more complex materials, thanks to a new Round 2 Servo rounding unit and RT-X grinding unit and the latest optimised devices for an accurate line of glue; and a close focus on the continually evolving demands around matters of softforming and J-shape, areas in which SCM has made its mark in providing easy-touse solutions that provide equally top-quality results.
Stefani Rocket – edgebanding and squaring-edgebanding line to handle high volumes with maximum ease
The Stefani Rocket line, made up of two single-sided edgebanders and squaring-edgebanders and an interconnection/servo automation system, allows for both high-volume mass customisation production and equally simple management of the entire process.
The automatic feed system with roller allows for panels to be loaded without having to match or align them. This leads to a considerable saving in time and, more than anything, means the line can be controlled without the assistance of specialised operators.
The different configuration options can adapt to the spaces available, adjusting accurately to the already existing production situation.
The line is even available in the non-squaring version, to integrate into processes with the presence of panels that have already been squared.
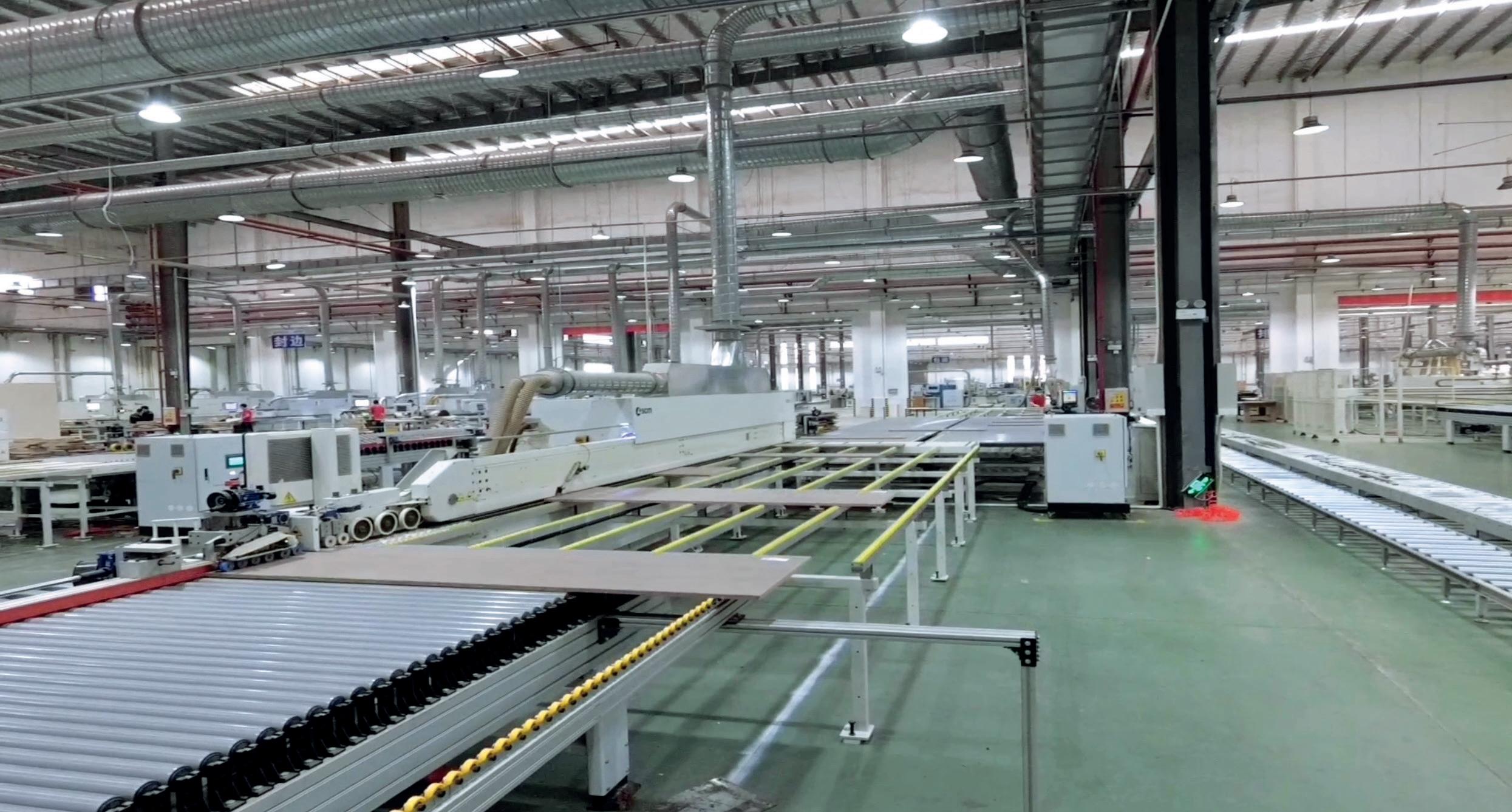
Flexible Stefani cell edgebanding solutions for batch 1
Flexibility, integration and automation – these are the cornerstones of the new Stefani cell range, designed and developed to fully interpret and meet the demands for efficiency, high production and customisation from today’s market.
The edgebander or squaring-edgebander is integrated into cells and plants fitted with rollers, panel return devices, automatic loading and unloading systems, assisted by robots and fitted with IoT sensors to guarantee instant digital services as back-up support to the optimal functioning of the machine.
Stefani cell is the new generation of flexible cells with an edgebanding or squaringedgebanding machine for batch 1 machining, with high-tech solutions requiring minimum investment: the Stefani cell E, to machine panels that have already previously been squared; the Stefani cell S to machine panels with squaring-edgebanding function and semi-automatic feed; and the high-productivity Stefani cell H/H+, to machine panels with or without squaring-edgebanding function and with automatic feed.
The range’s software has also been modernised with Maestro active edge and Maestro active watch – a new supervisor with an HMI interface and structure shared with all the SCM machines. In particular, the new Edge Store Manager function means the change of edge and machining can be handled automatically, as well as rapidly and intuitively. This is done using a combination system between the program and edge via a barcode reader and QR code.
Of fundamental importance is also the integration with the Maestro connect IoT platform, the system for collecting and analysing data from SCM technologies which, thanks to the constant analysis of the data being produced by the machines, provides instant access to a wide range of services such as remote technical support with augmented reality (AR) glasses, the purchase of spare parts online, predictive maintenance and numerous other services that considerably increase the effectiveness and efficiency of a production plant.
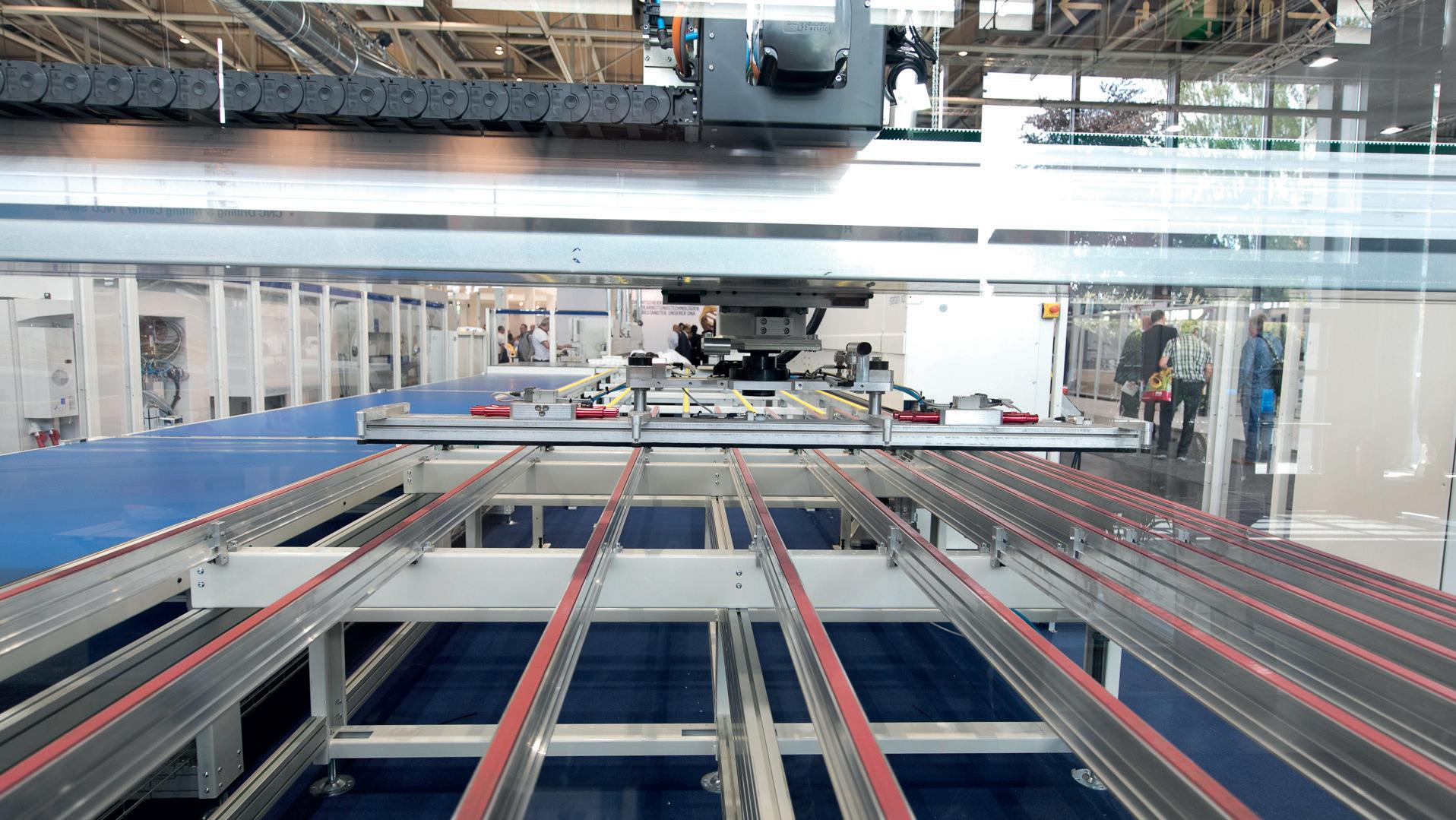
Stefani Cell E
Stefani cell E is the entry-level cell in the range, for edgebanding previously squared panels. It combines the advantages of customised production and large volumes with a compact overall design and, above all, with an accessible investment level – even for SMEs.
The multiple configurations available allow
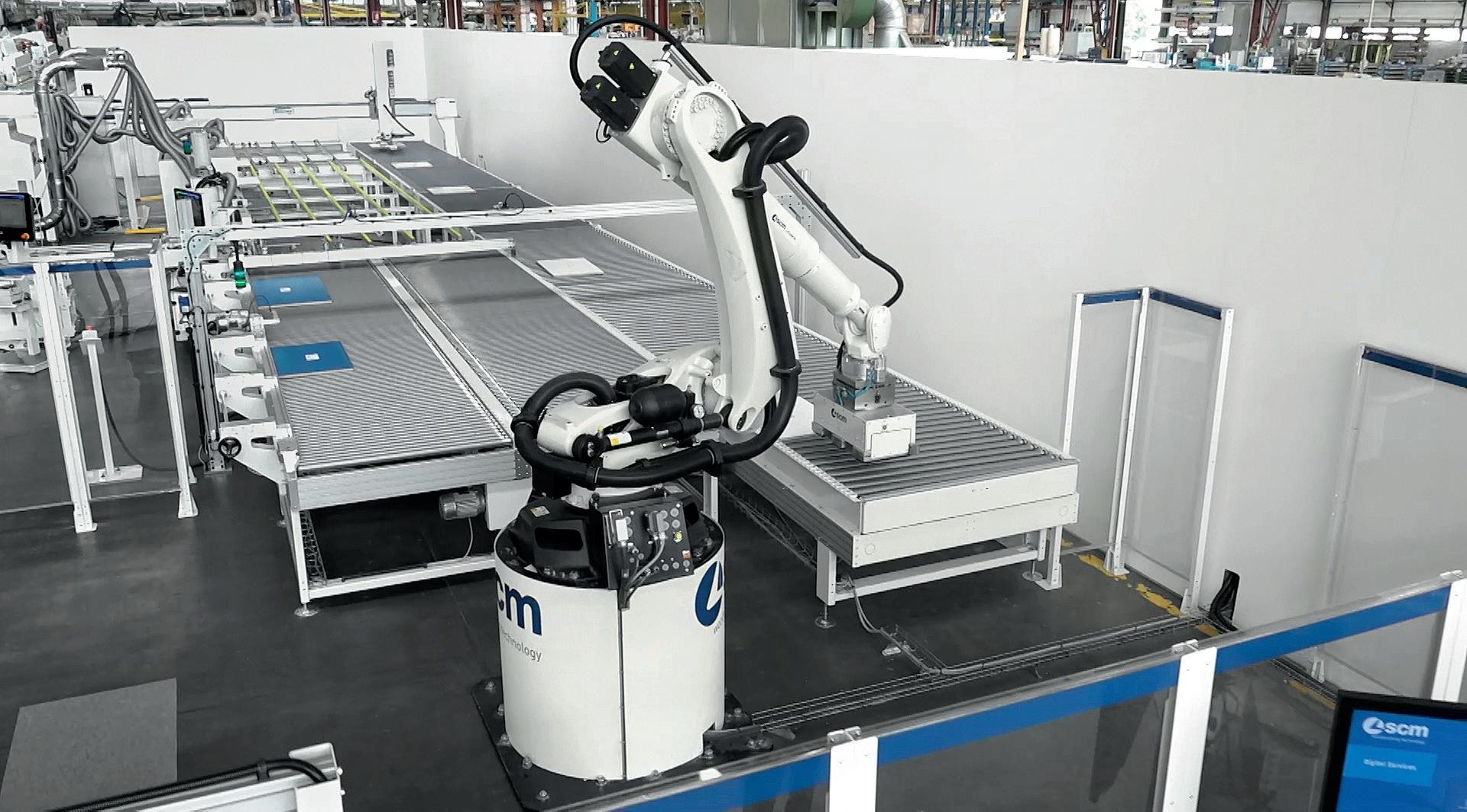
for each specific need to be covered in terms of productivity and machining. Feeder, Robot or additional movements can be combined to offer maximum flexibility and customisation.
In particular, in the Robot Loop version, the Stefani cell E is configured with the anthropomorphic robot for the complete automatic management of the panel loading/ unloading work. It also features: – Fast-axis high technology, in line with future market scenarios. Type, colour, edge thickness, position and mortise depth, handling of the protective film and panel dimensions – the highly versatile Stefani cell E means the user can continually feed-in and change all these parameters as part of the production flow without it being interrupted. – Simple, integrated and versatile, the multiple configurations available (reloop with robot or reloop with motorised belts) mean all specific needs in terms of production and ››
machining are met. Feeder, robot or additional movements can be combined to offer maximum flexibility. – Whether it be in self-learning mode, with barcode/QR code or with supervisor, Stefani cell E is programmed to be set at any level of logical and physical integration. – New automation to accelerate business – with the new fast, reliable pickback gantry panel-return system, the panel is automatically rotated, to speed up the next in-feed. It will also be possible to unload at the end of the cycle in masked time with the next loop load. – No errors, and a guarantee of always feeding in the panels in the right direction, thanks to the Side Finder technology, which shows how to position the panel from a display in the operator’s area, so that it can be correctly machined.
Stefani Cell S
Stefani cell S is the all-in-one square-edging cell designed for mid-range investments, with the aid of a single operator to provide clear business advantages from the outset – especially companies focusing on semiintensive production and/or with varying production batches. – Compact and performing, Stefani cell S allows for the machining of parts from the premeasured and squared nesting cycle and sheet cutting, and which require the parallelism/ squaring to be reset. This occurs thanks to the innovative semi-automatic feeder device with panel squaring, which facilitates and allows for longitudinal and transversal feeding, even of large panels. – Modular and efficient, the Stefani cell S is designed to be easily integrated into different operating situations, thanks also to its integration with the new Pickback gantry panel return system, which automatically unloads the machined panels into a stack. This brings with it considerable advantages in logistics terms and overall machining times, with full automation for the return of the panel as far as
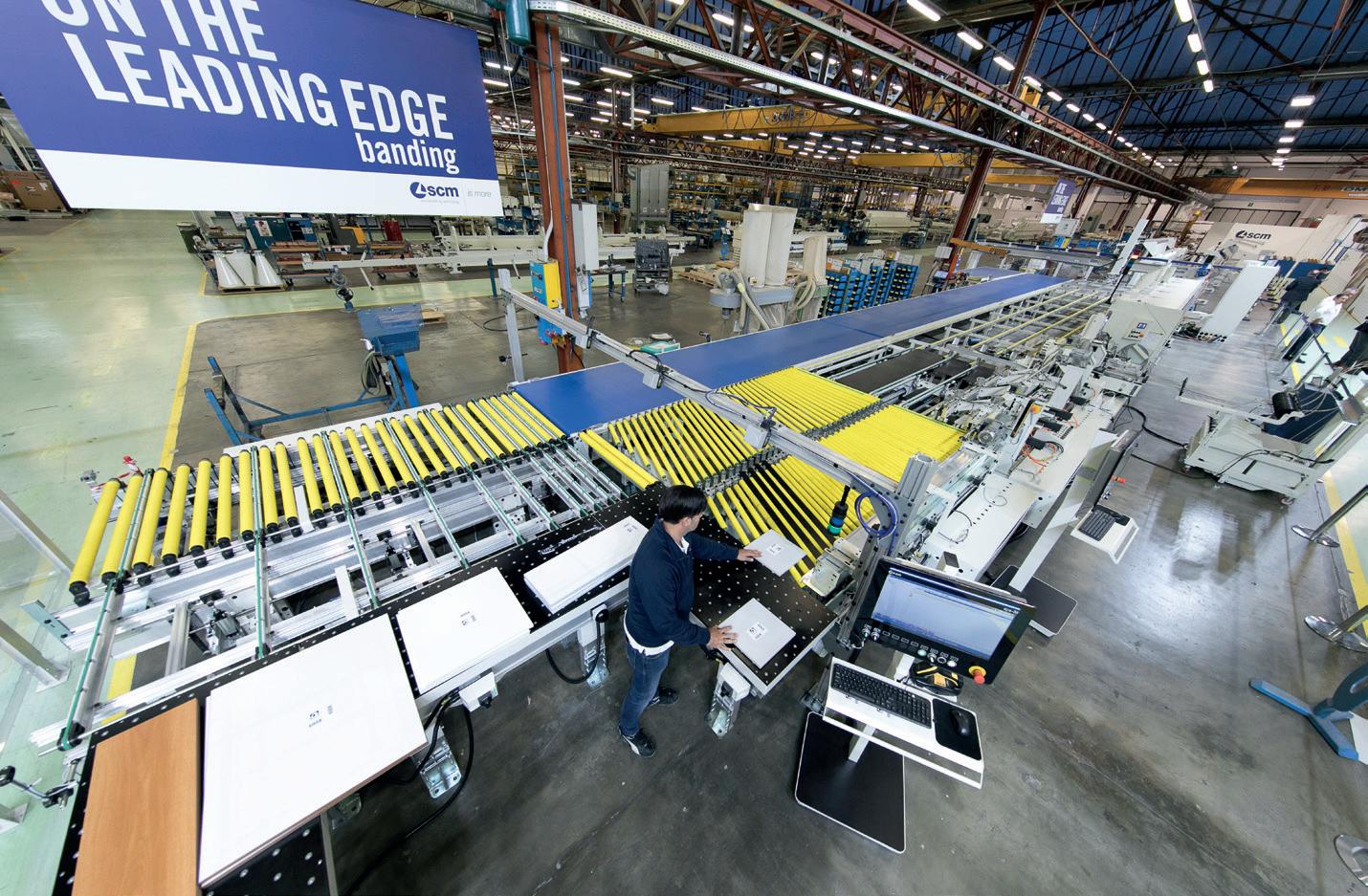
the operator loading area. – Exact and dynamic, the specific technical solutions provided guarantee maximum quality at the final assembly stage of all the furniture parts – even the largest pieces like the sides and cupboard doors. Repeatability and machining accuracy become a safe added value for each component in a piece of furniture.
Stefani Cell H and Stefani Cell H+
Boasting maximum customisation, high productivity levels and impressive machining quality, Stefani cell H and Stefani cell H+ are the new edgebanding and square-edging cells capable of bringing together all these advantages within one solution. The cells can be configured with different kinds of panel-feeder systems – semi-automatic or fully automatic – are structured according to technical solutions, level of investment and efficiency, and are designed to guarantee both industrial level production volumes as well as maximum diversification of the production batch.
Stefani cell H/H+ ensures 100% efficient machining of components for furniture items for every part of the home (kitchens, living rooms, bedrooms, bathrooms, wardrobes and studies), bringing with it considerable advantages. – Instant production, and financially advantageous, both for batches with single panels as well as for average standard stacks, without the need to stop production for the change of format, thickness, ornamentation or gluing quality which occur on a regular basis during a machining shift. – Instant availability, even on mobile devices, of the machining information relating to each single panel – wherever it is in the cycle – thanks to the continuous tracking provided by the supervision software. – Panel flow and movement optimisation handled and synchronised with company network data.
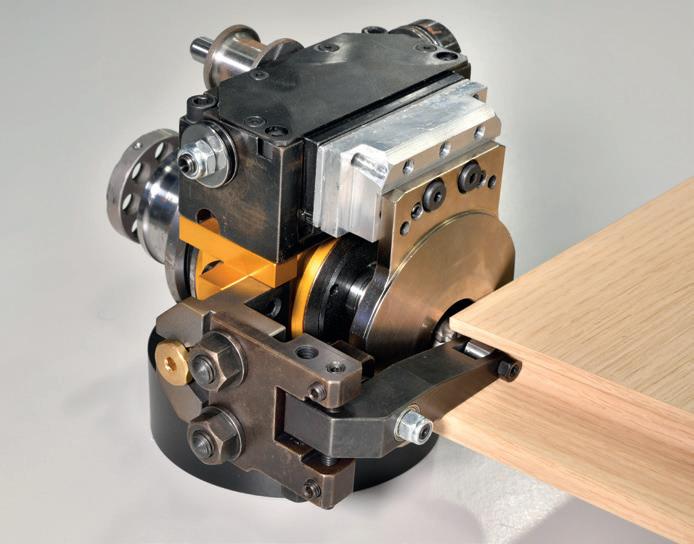

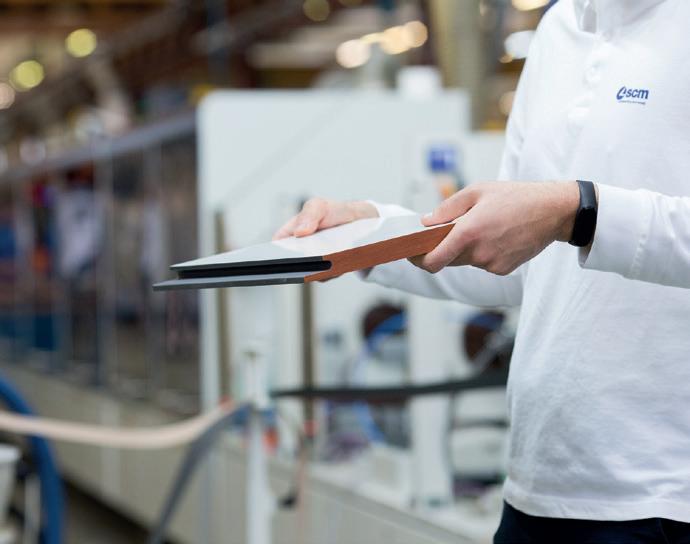
The best of softforming for J-Shape type profiles
As part of SCM edgebanding, a great deal of attention is also paid to market demands on softforming and J-shape, with the state-of-theart Stefani models.
The J-side kit, in particular, has been designed to solve the problem of complex profiles, so the straight edging lines up perfectly with the shaped edging, without gaps or projections. There is no longer any need to carry out this machining manually or with an additional procedure, thanks to this exclusive SCM solution.
An edgebander equipped like this means any kind of edgebanding problem can be resolved while work continues, without any interruption, exactly as though it were working on a normal straight edge.
This is a significant step forward in being able to extend the creative potentials of softforming to a growing number of companies, a solution which is effective with any kind of edge and with different thicknesses that can be applied and worked without interruption, concludes SCM.
www.scmgroup.com
STEFANI KD THE BEST IS AT YOUR FINGERTIPS
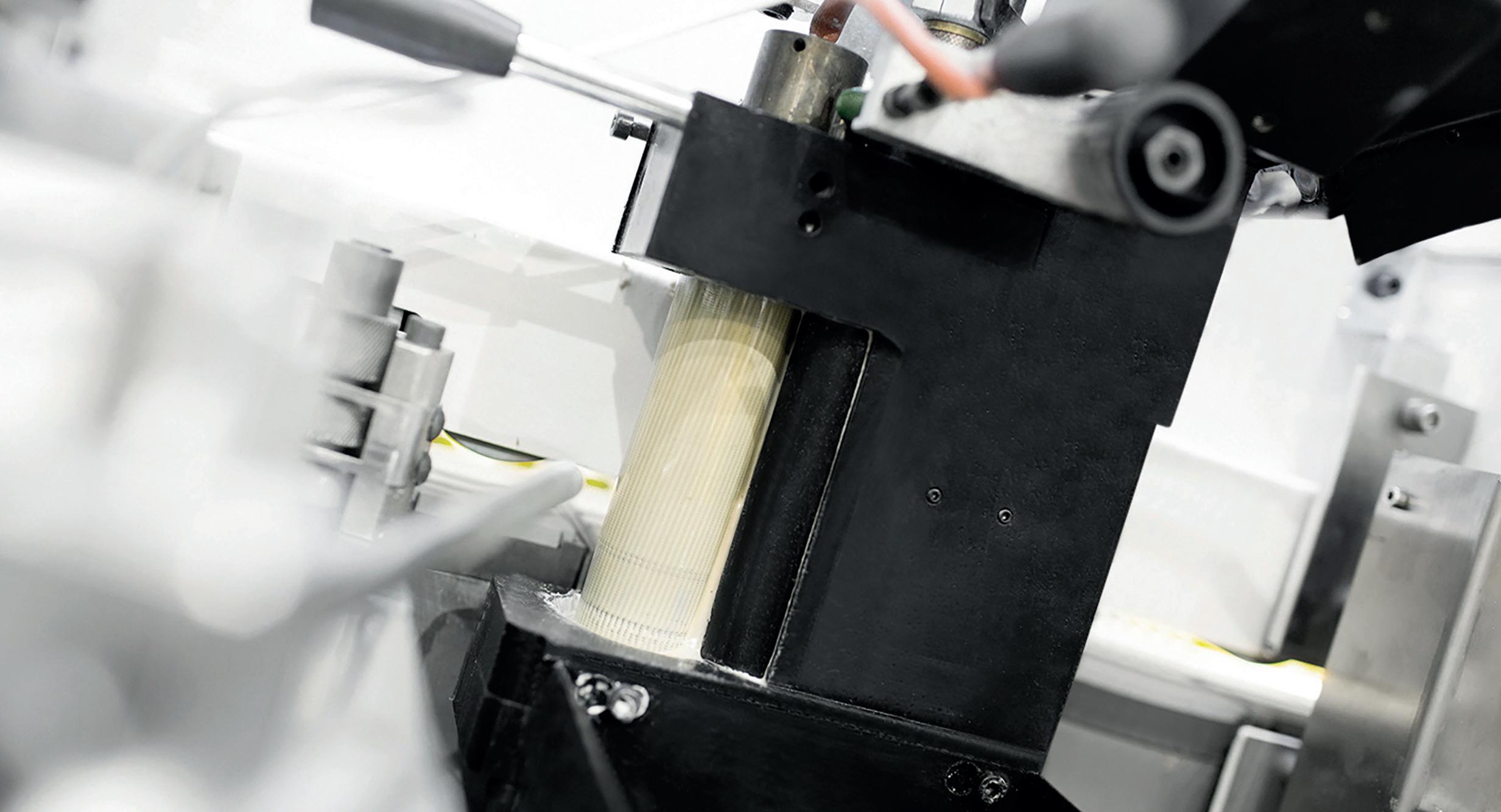
Continuous and versatile solutions for quality machining are the distinctive features of stefani kd.
•
Automatic machine set up for processing 2 different radii, infinite thin edges and solid wood up to 12 mm
Use of Polyurethane and Eva glue for the production of high quality panels thanks to the SGP glue pot allowing a fast and simple glue changeover
“Zero” glue line between panel and edge thanks to the AirFusion+ technology
Fast and error-free production with the new Maestro pro-edge HMI and the eye-M 21.5” multitouch consolle with 3D preview of the processed panel.
New top pressure belt particularly suitable for processing delicate panels
High production levels thanks to the machining speed up to 20 m/min
Great efficiency with the “Fastback” panel return device allowing the complete edgebanding process managed by a single operator
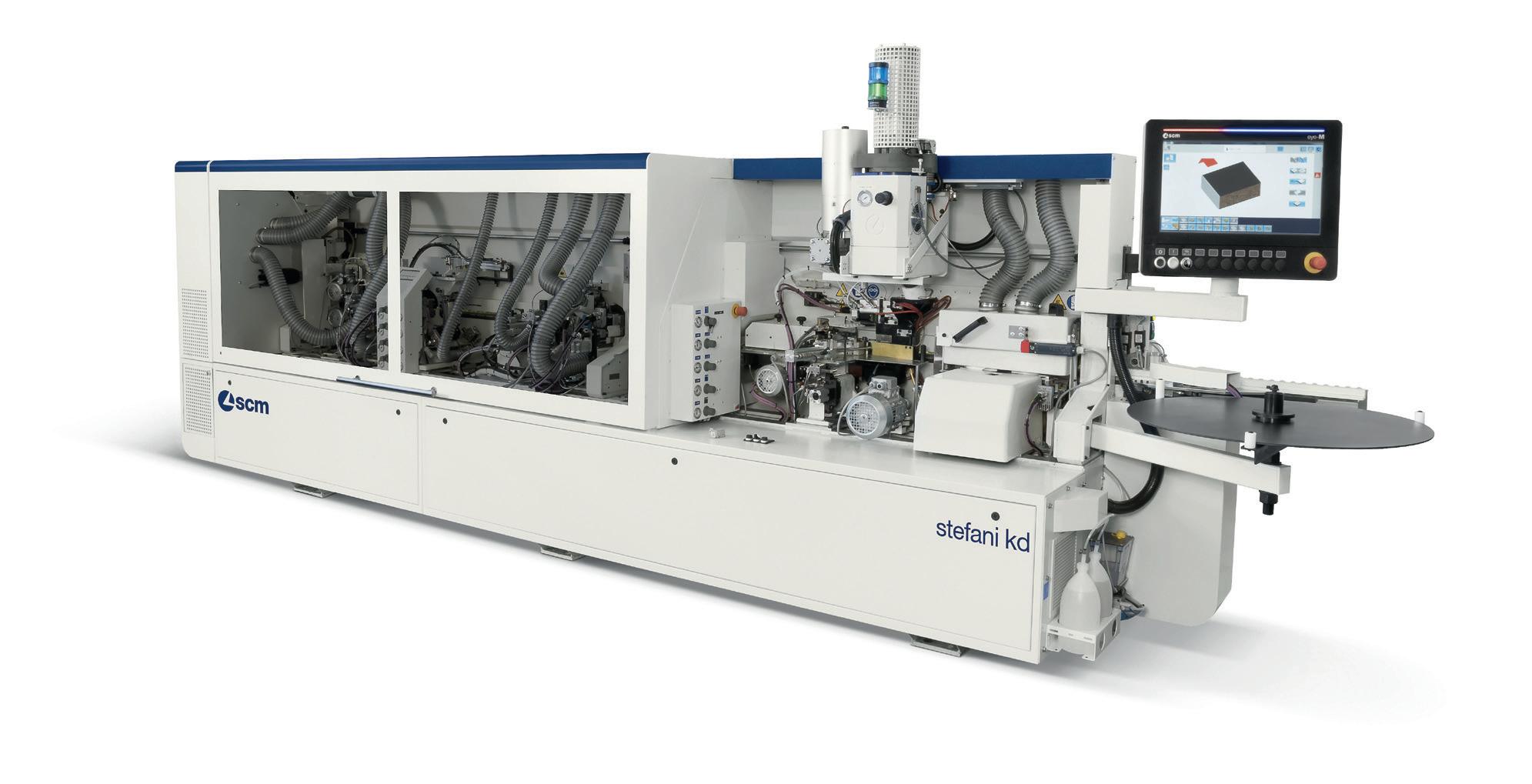