40 minute read
News
Lathams moves to address ‘lack of carbon understanding’ in industry
Timber and materials supplier James Latham has released a ‘carbon calculator’ designed to direct customers towards more sustainable products.
Built in partnership with the BioComposites Department at the University of Bangor, it is based upon detailed research into the embodied and biogenic carbon impacts of the products that it supplies.
The calculator covers just over 70% of the total Lathams range, and focuses on timber products. In time, it will also incorporate composite materials that were out of scope for the first phase.
Ewa Bazydlo, environmental manager at Lathams, says: “Reducing the environmental impact of our buildings is one of the key issues of our time. However, the understanding around sustainability is not consistent across the industry.
“We’ve developed the calculator to help our customers to better understand the sustainability of the materials they choose as well as the expected performance levels that they offer.”
The tool calculates environmental impact by looking at the carbon footprint of products, from production through to delivery to Lathams’ depots. It also looks at how much carbon is stored within the wood’s structure, known as biogenic carbon.
Each product then receives a rating from 1-4 (one being the highest, four being the lowest), based on the confidence that Lathams has in the data used for the calculations. The higher the score, the higher the quality of the data points that have been reviewed, for example an audited and published EPD (Environmental Performance Declaration).
Lathams will be adding the carbon data to all invoices, delivery notes, and other key documentation to increase visibility around this issue.
It is a move that Campbell Skinner, senior lifecycle assessment analyst at BioComposites Centre, argues is a positive step forward: “Companies have used eco-labels before, but the approach taken by Lathams is really innovative. For the first time that I’m aware, the confidence with which these footprints are presented is rated and placed foremost in the labelling.
“Latham’s customers are being given a clear indication of the transparency with which suppliers are reporting their carbon footprints and this will surely nudge more companies towards independently verified reporting schemes, such as EPDs.”
Ewa adds: “We needed a mechanism to rank our products and make it quick and easy for our customers to be able to specify more carbon conscious materials. As a large distributor, we have the relationships with the supply chain, which improves our ability to source and analyse the relevant data and make recommendations.
“We hope that others in the industry follow our lead and improve the transparency around these products so that we can work together to reduce construction’s impact on the environment.”
To complement the calculator and share some of the insights from its research, Lathams will be publishing a Think You Know Carbon? guide. It will include an overview of the main issues in sustainability, a glossary of key terminology and steps that architects and specifiers can take to be more sustainable in their designs.
It will also include highlights of some of the most sustainable products Lathams stocks, from manufacturers such as Accsys Technologies, which produce modified timber Accoya, and UPM Plywood, home to WISA plywood products. Find out more at www. lathamtimber.co.uk/about-us/ carbon-calculator.
Management buyout at ATA
Following a management buyout in November, ATA Engineering Processes has changed its trading name to ATA Engineering Products – and Mark Whitbread is now be the owner and MD of the new company.
Having earned its stripes supplying tools for the aerospace Industry, ATA has built a first-class reputation for supplying CNC laser cutters, router cutters and woodworking machines.
In a statement, Mark said: “We will continue to sell the same extensive selection of products and hope that we can continue our mutual beneficial working relationship with our customers.
“I would also like to thank ATA customers in advance for their continued support and look forward to working with them all and growing our businesses together.”
The company’s contact details remain the same. 01442 264411 sales@ataeng.com www.ataeng.com www.lathamtimber.co.uk
AkzoNobel receives royal seal of approval as a leader in sustainability
AkzoNobel is proud to be one of the first recipients of the Terra Carta Seal, which was launched at COP26 by His Royal Highness The Prince of Wales.
The Terra Carta Seal is a major new award which recognises global companies that are driving innovation and demonstrating their commitment to – and momentum towards – the creation of genuinely sustainable markets. It is part of the Terra Carta, a recovery plan for nature, people and planet which was introduced early this year through HRH The Prince of Wales’ Sustainable Markets Initiative.
As the only paints and coatings manufacturer to receive the prestigious honor, AkzoNobel is among an elite group of companies which have been acknowledged for holding a leadership position within their industry, and which have credible transition roadmaps underpinned by globally recognised, scientific metrics for achieving net zero by 2050 or earlier.
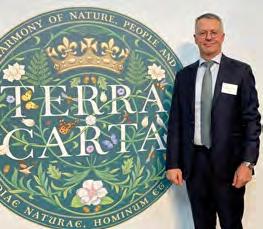
CAD/CAM/CIM SOFTWARE FOR WOODWORKERS
Streamline your design to manufacturing workflows
Powered by
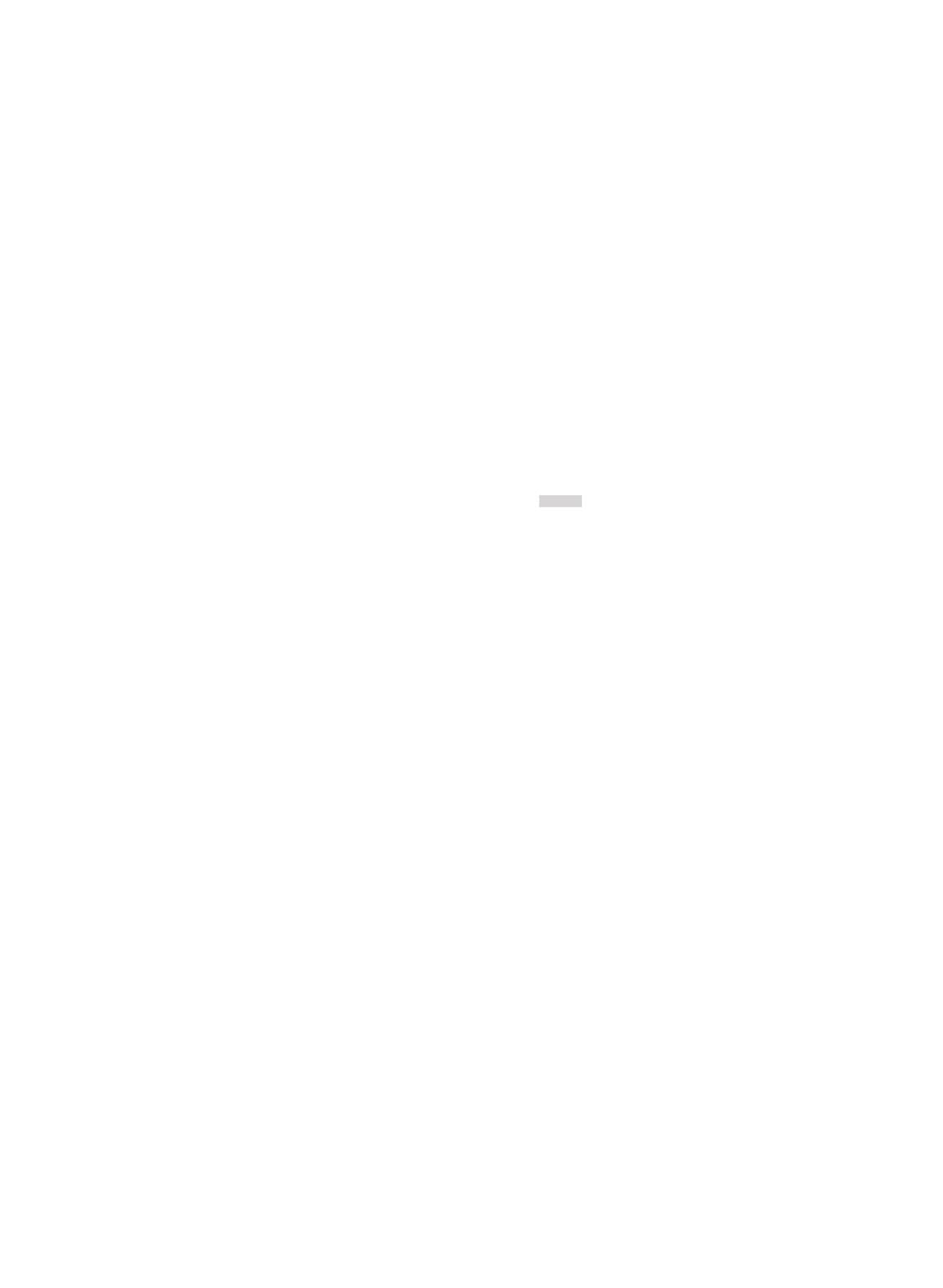
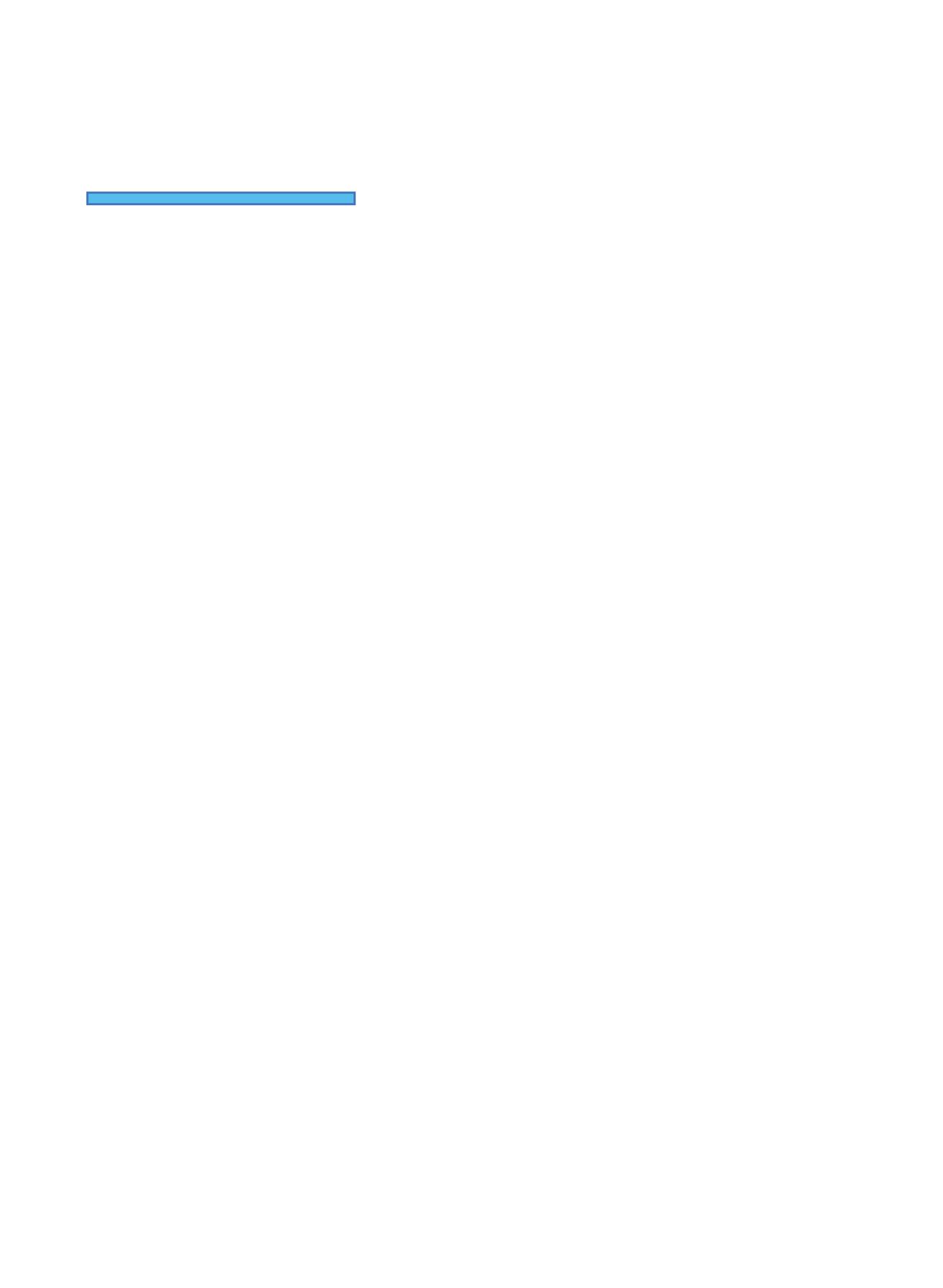
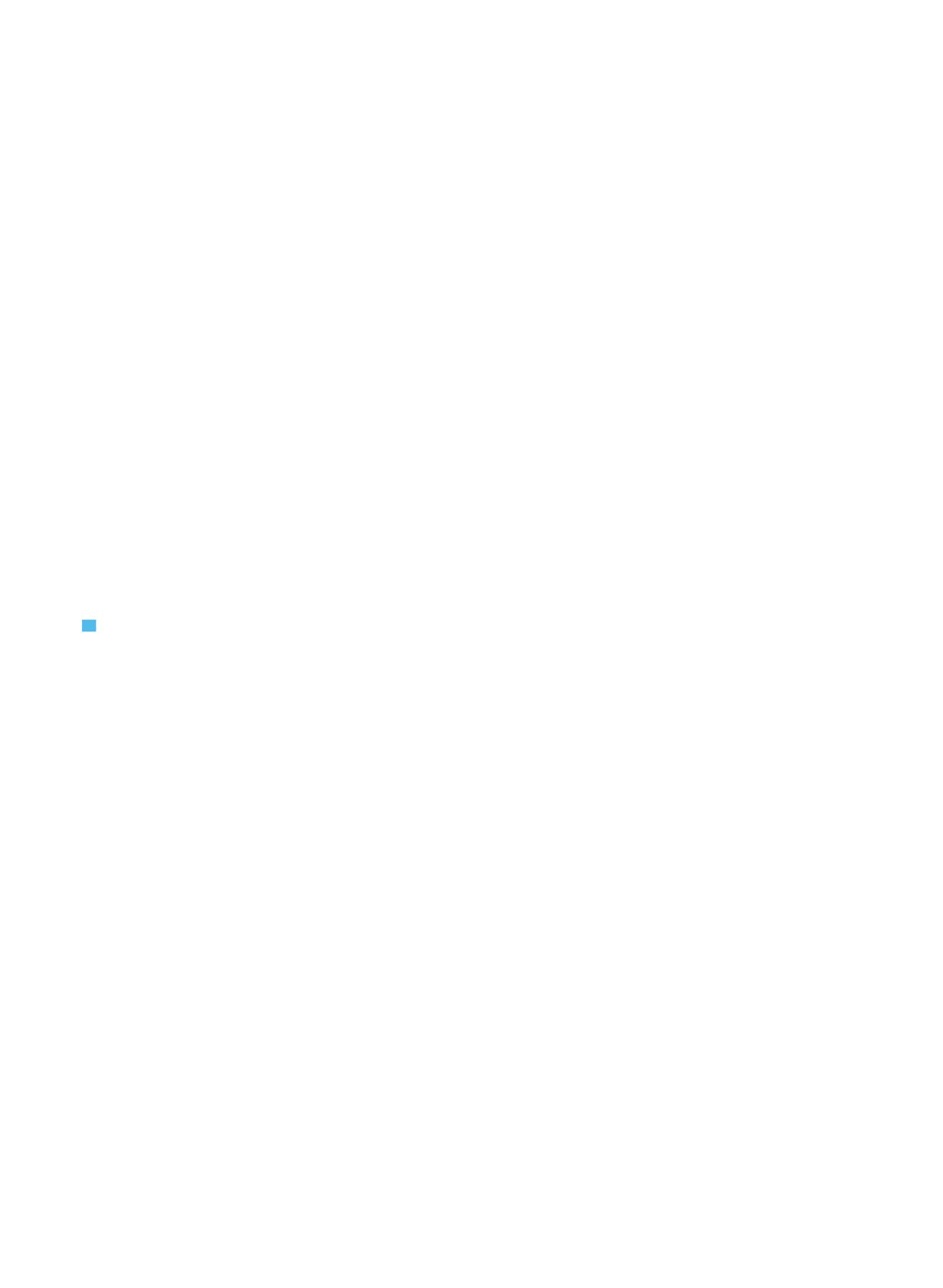
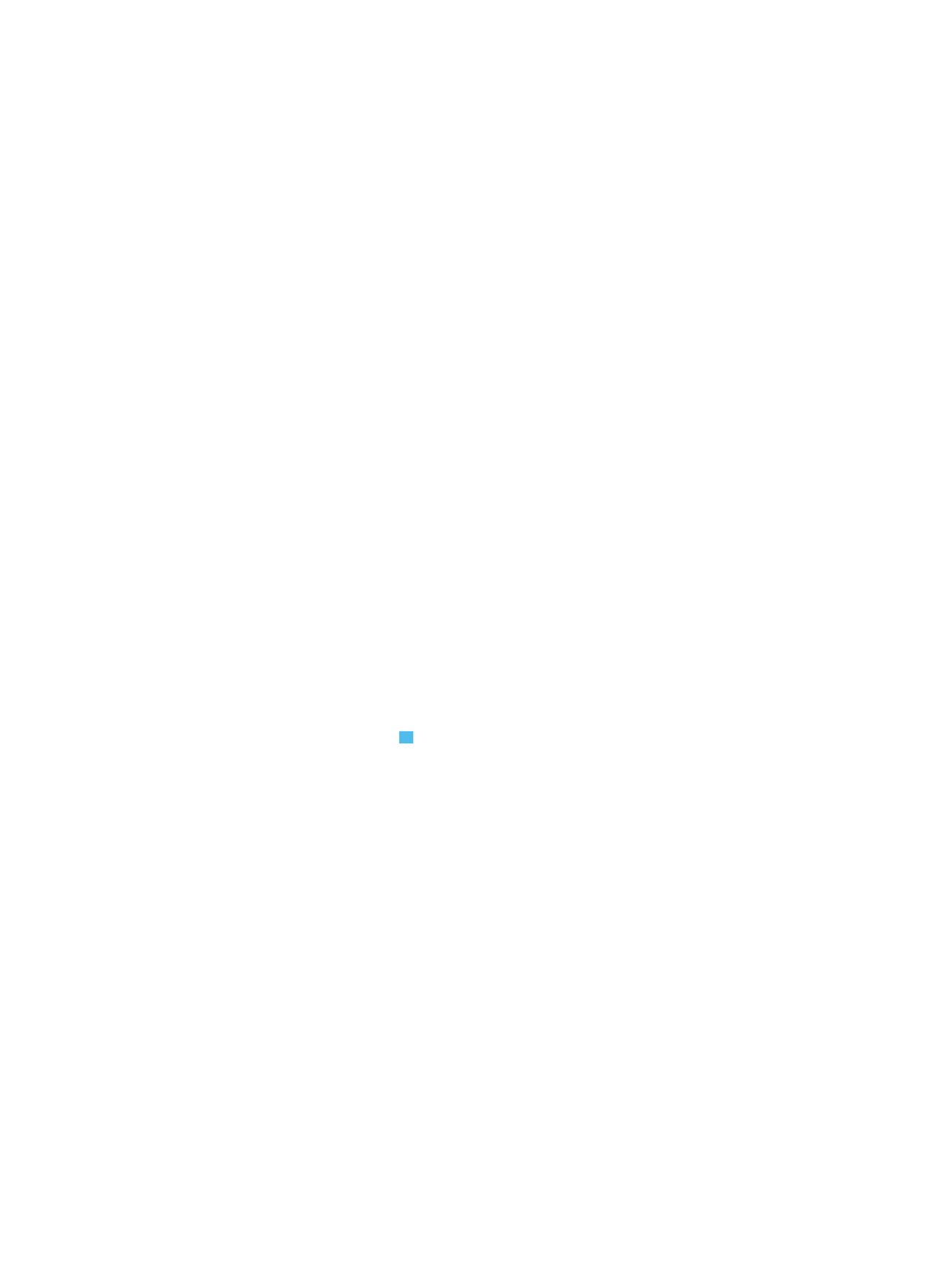
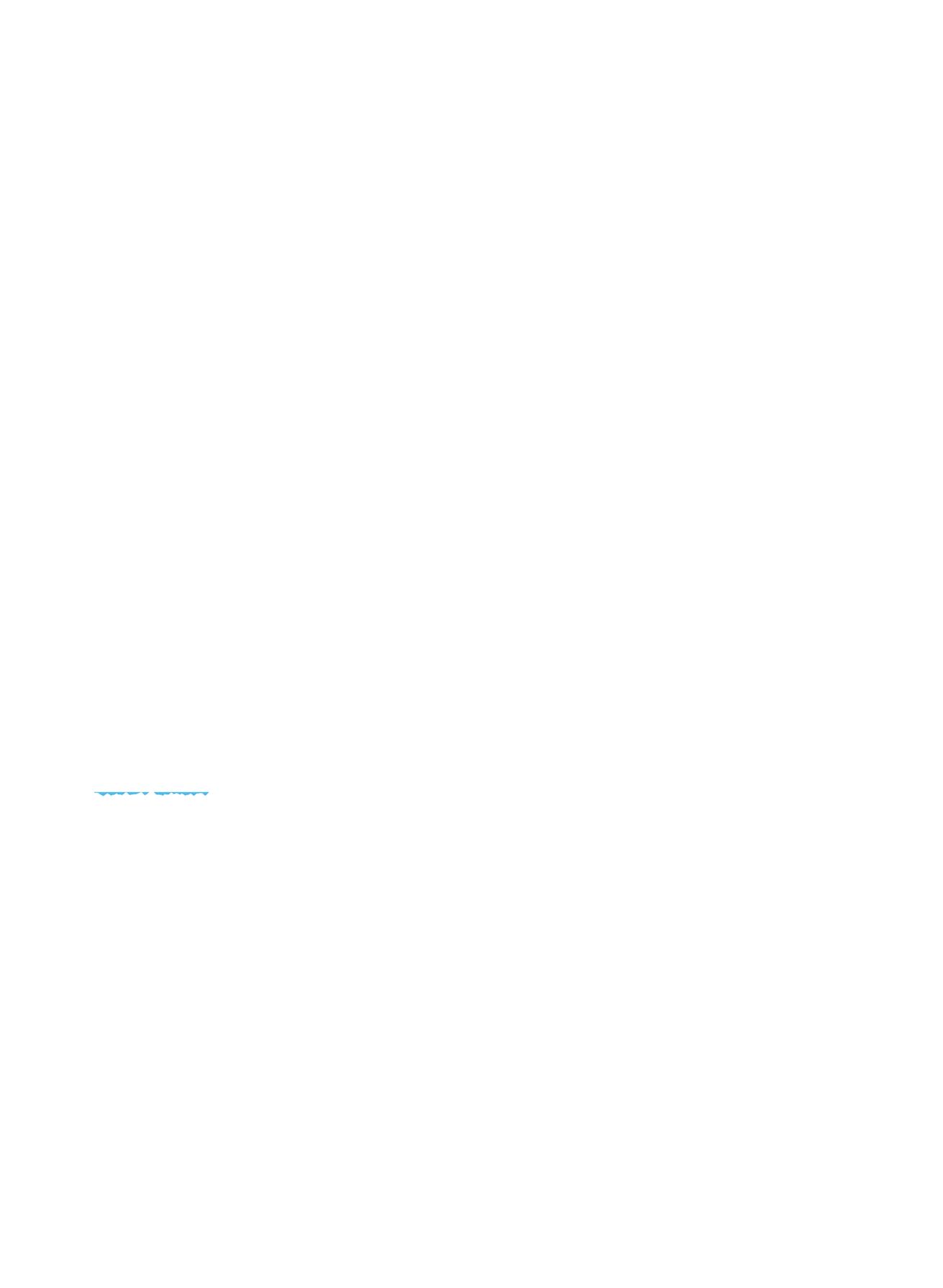
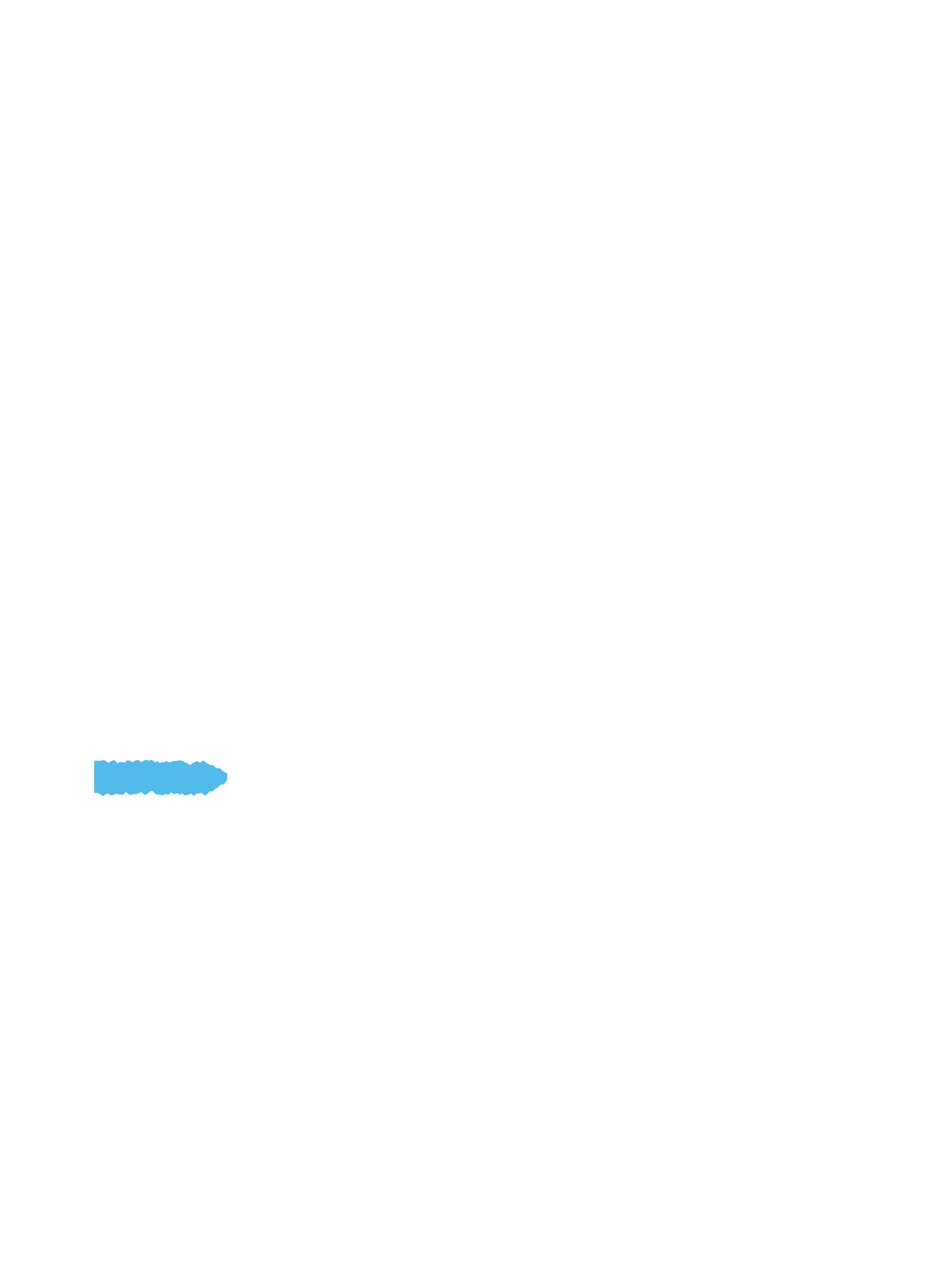
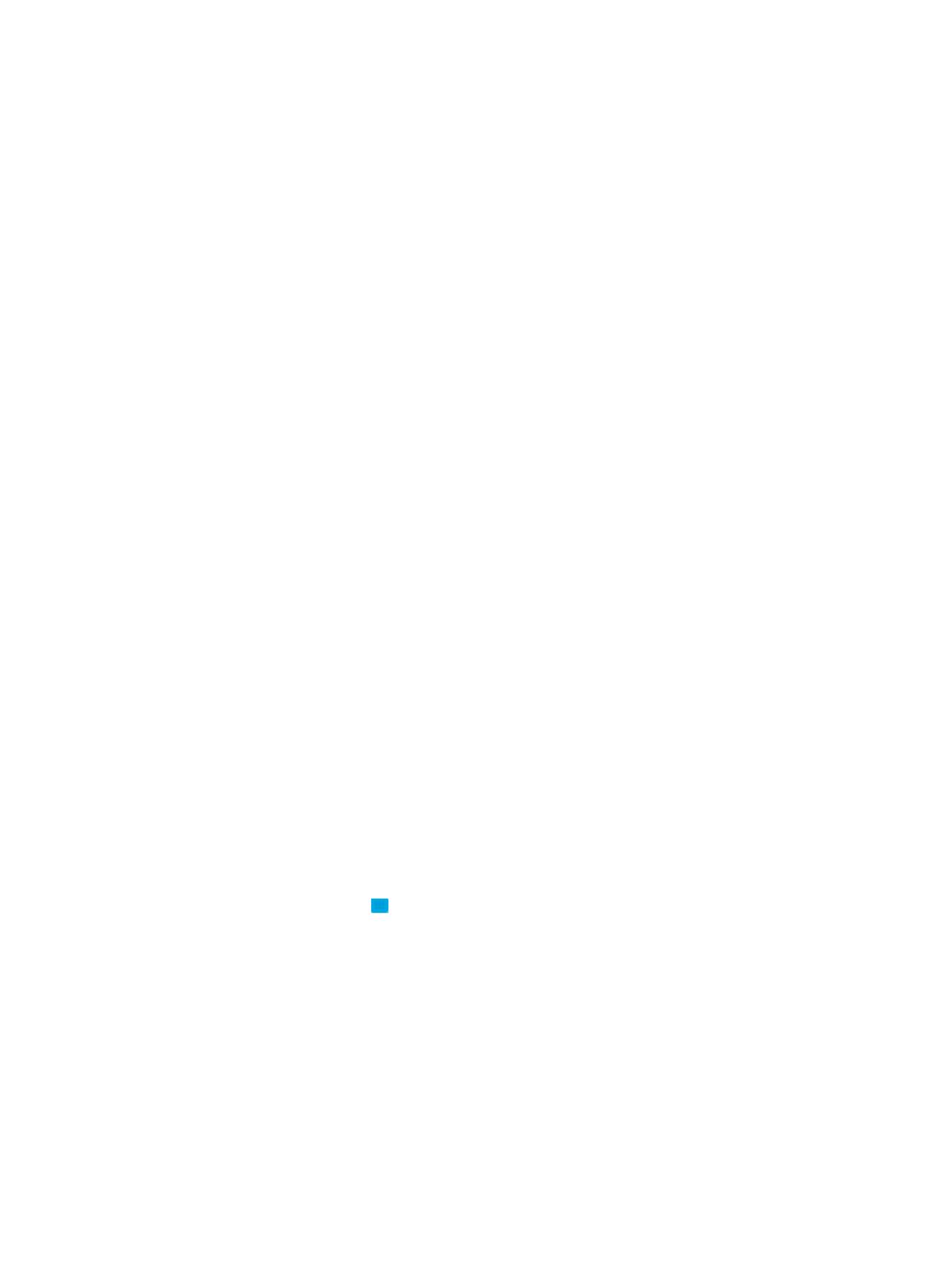
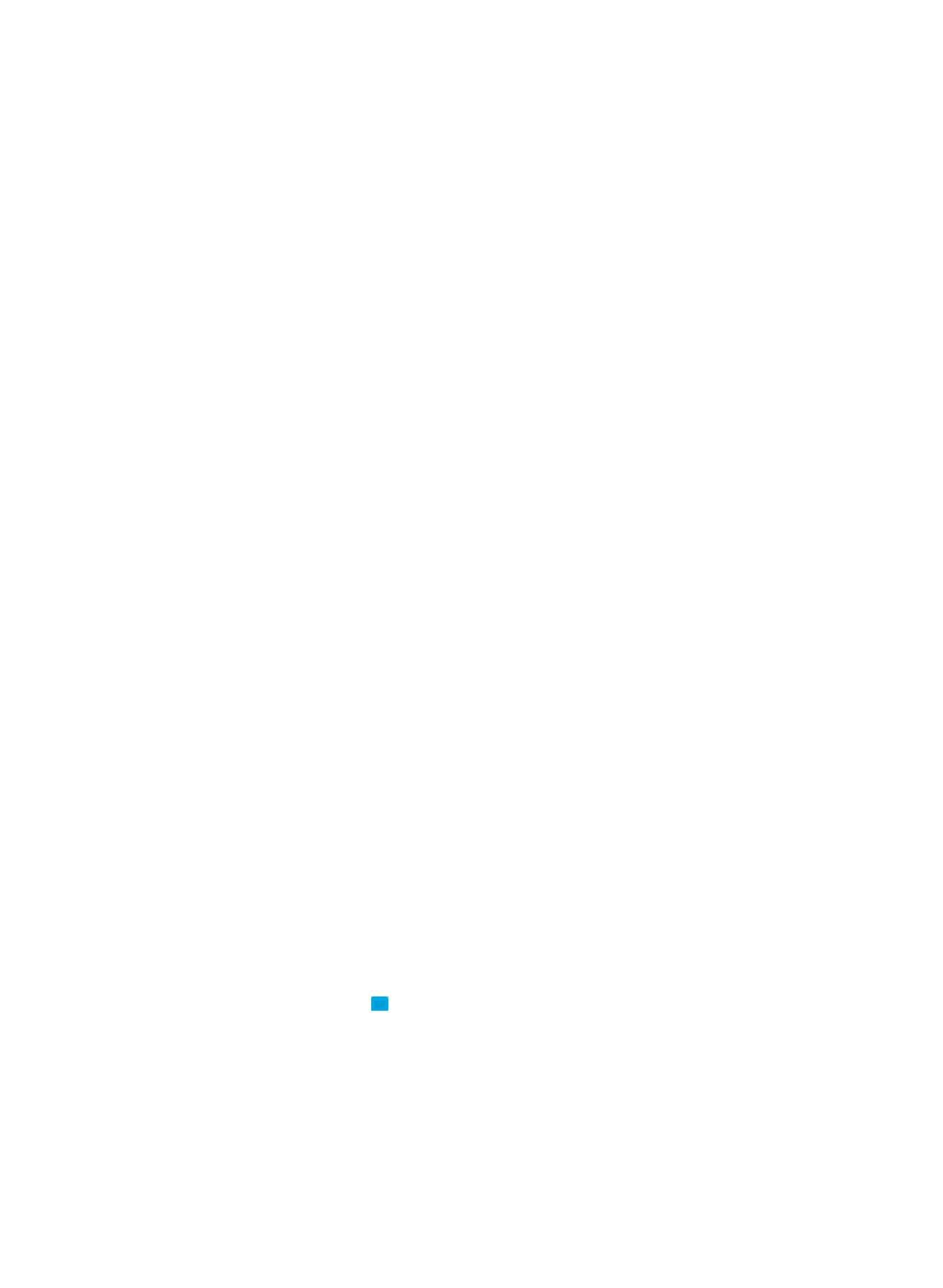
Microvellum has changed the way we do business. Their staff in the UK have not only assisted me to get the best out of my software and machinery but their extensive knowledge of manufacturing has helped us to be more professional and efficient. ” Scott Purdom
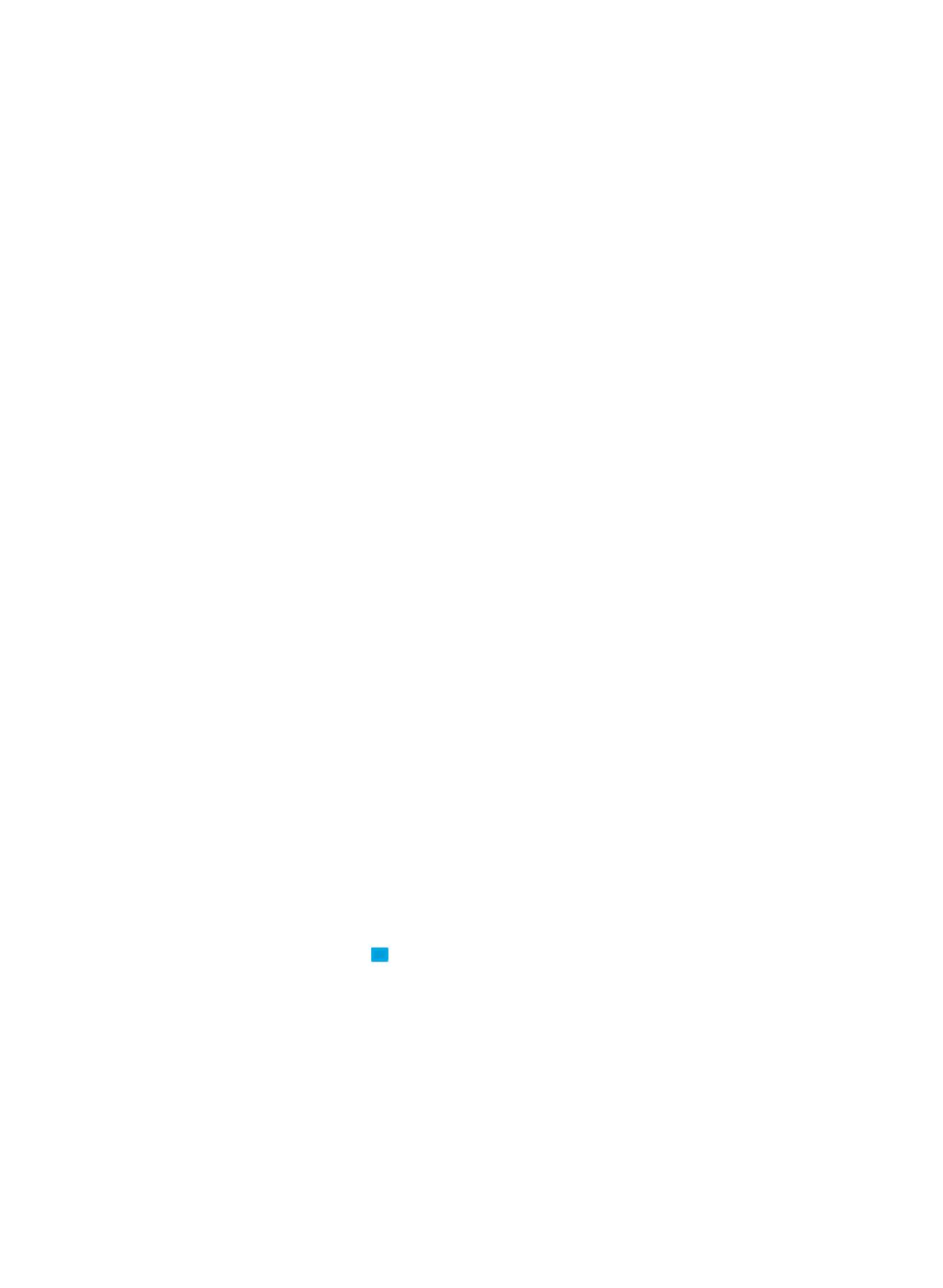
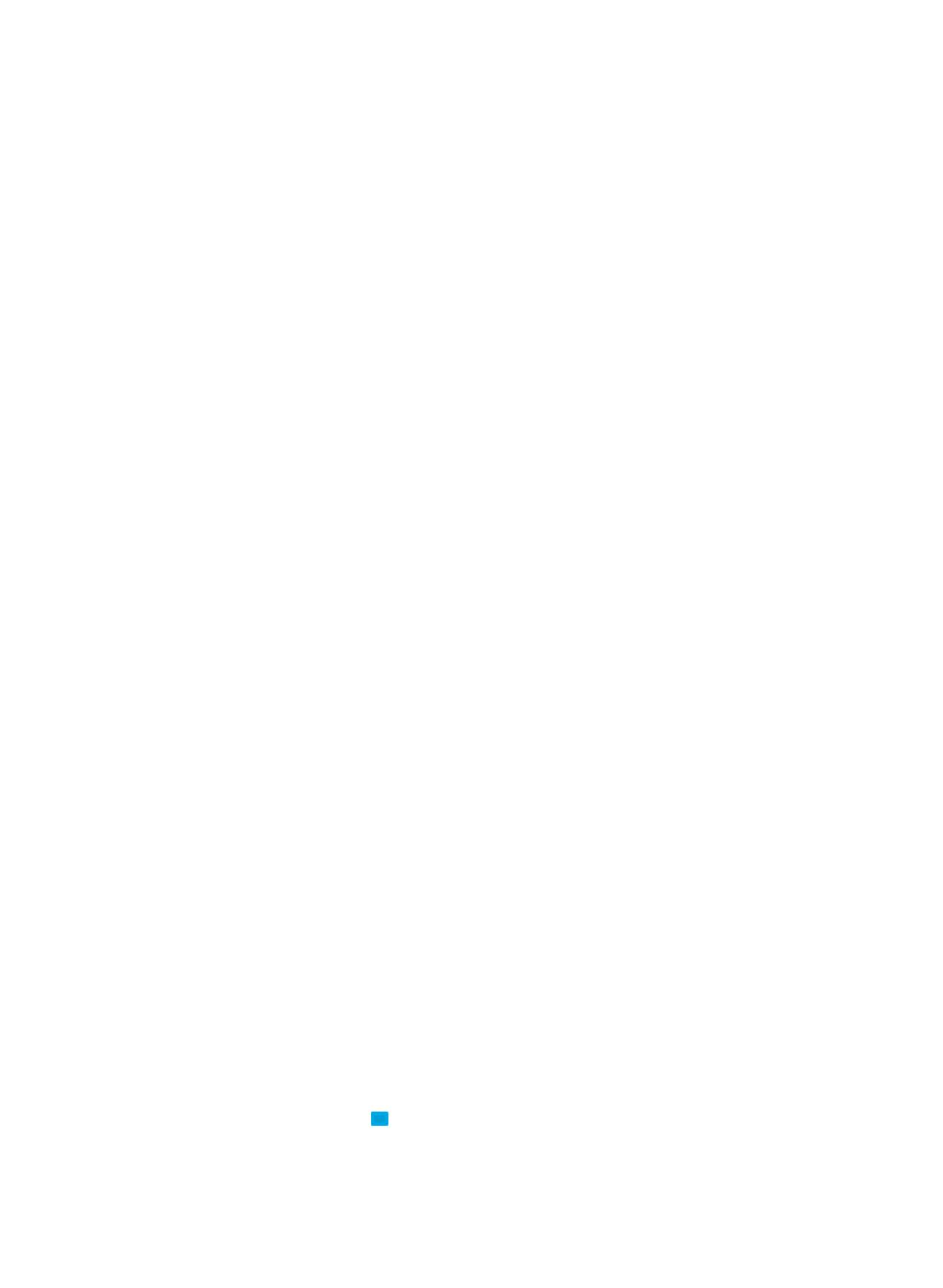
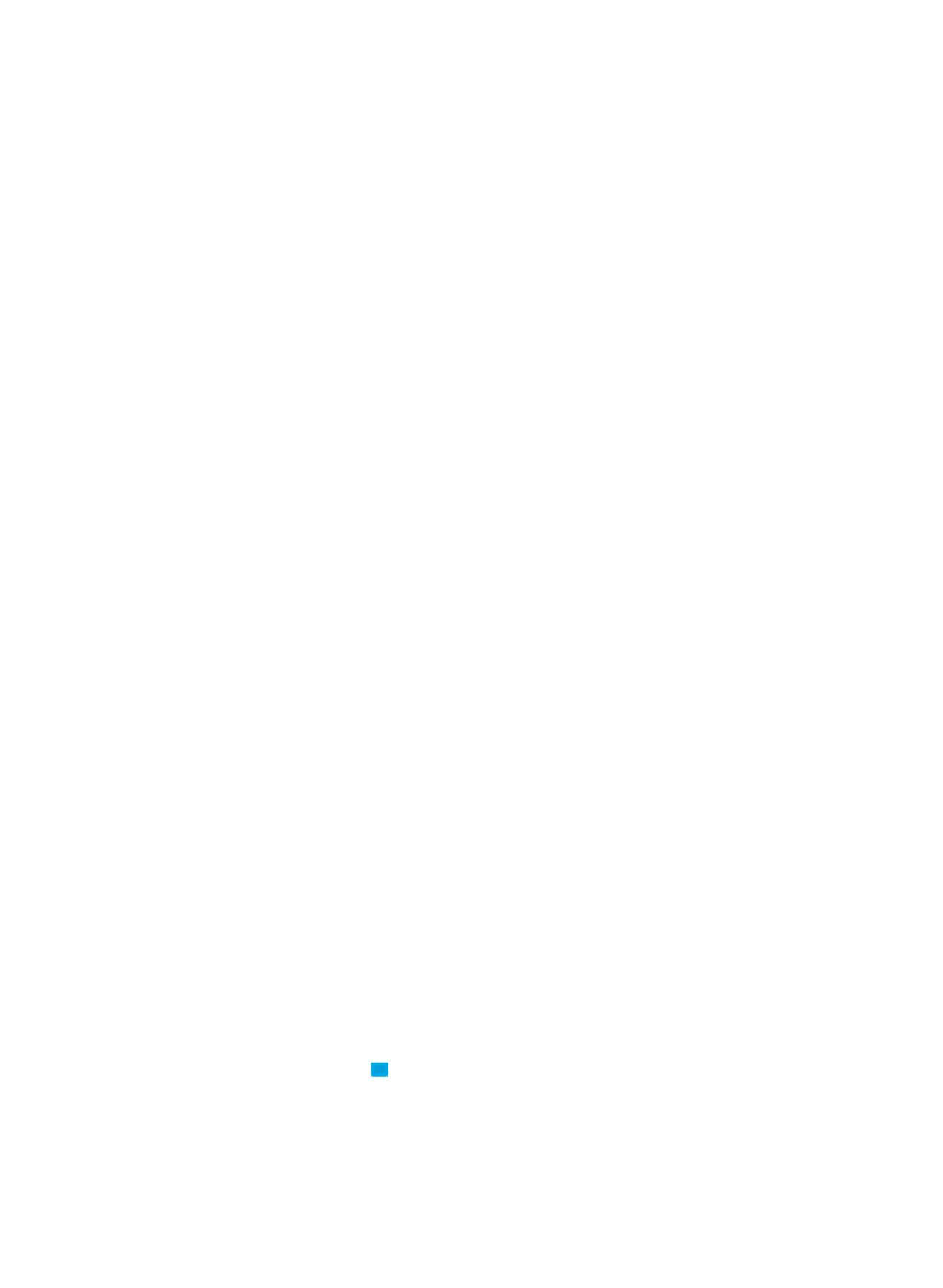
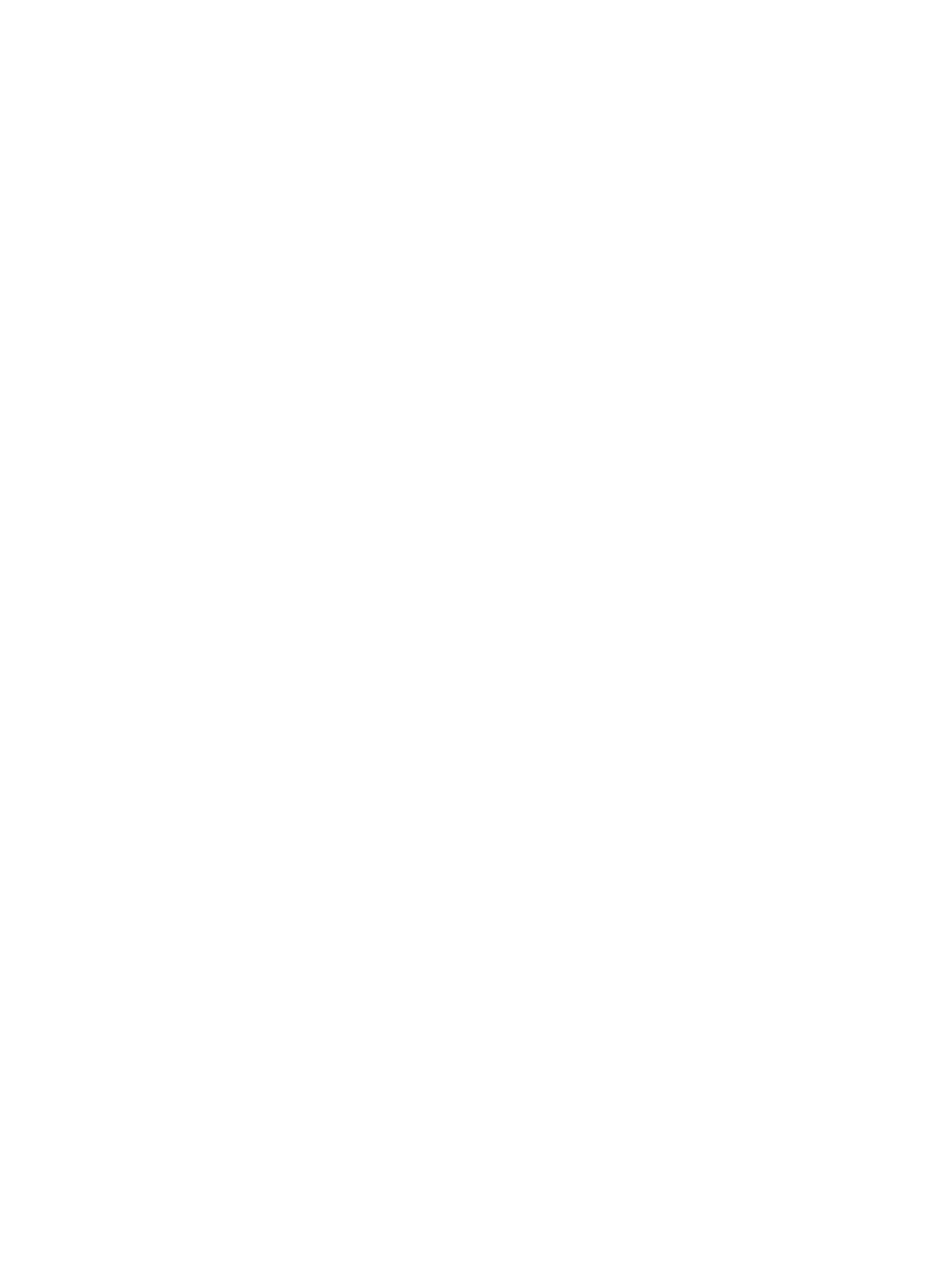
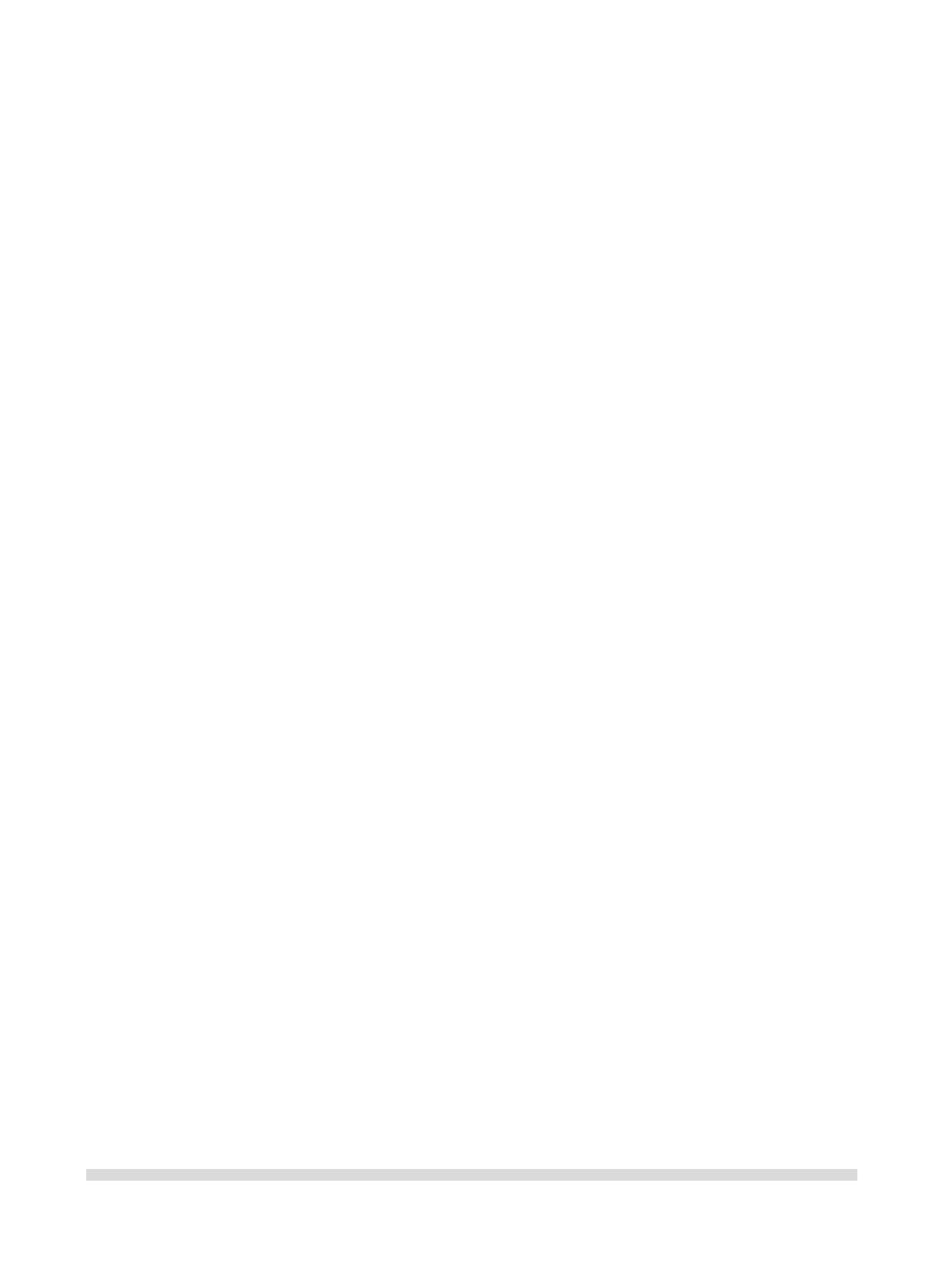

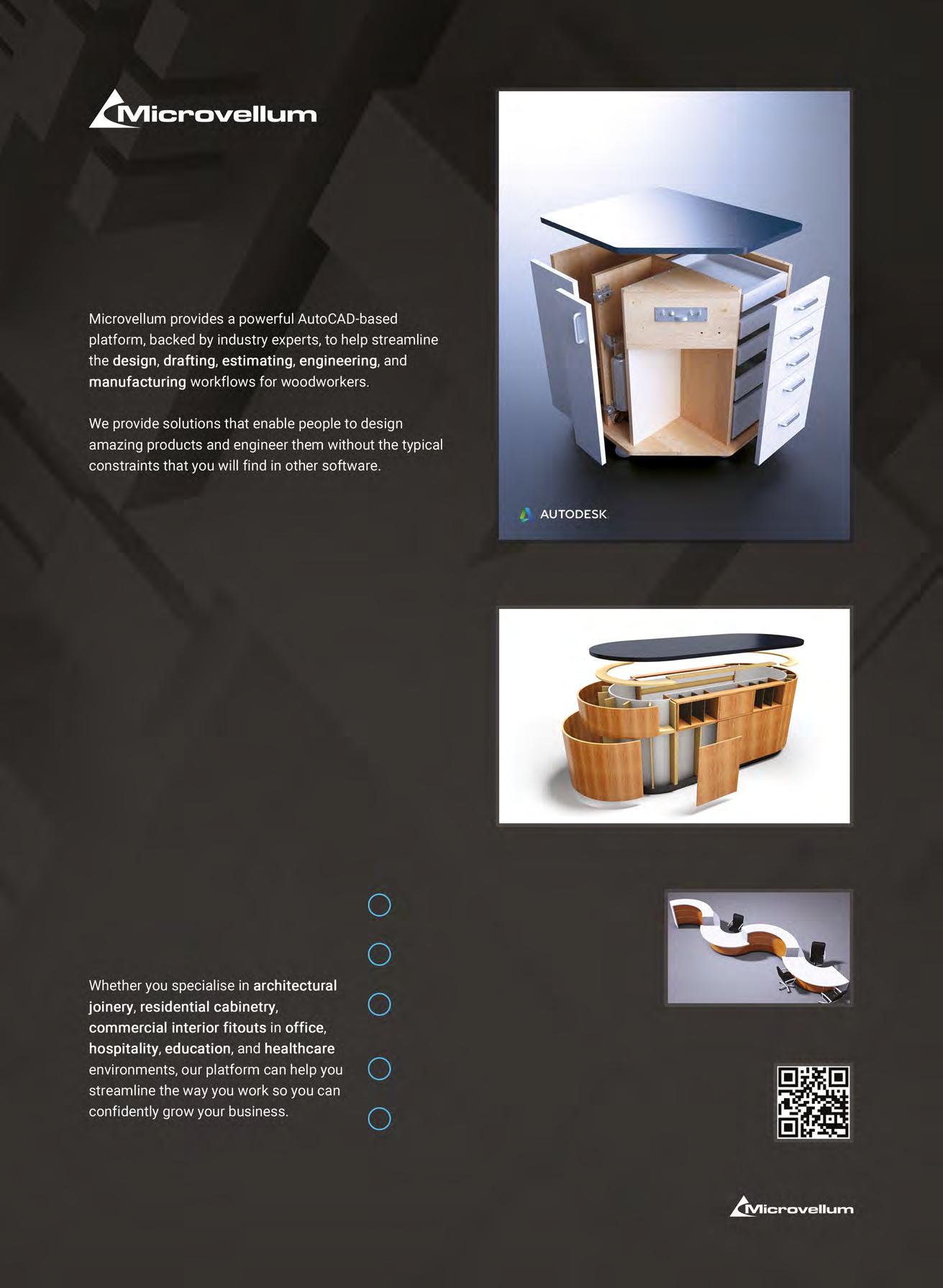
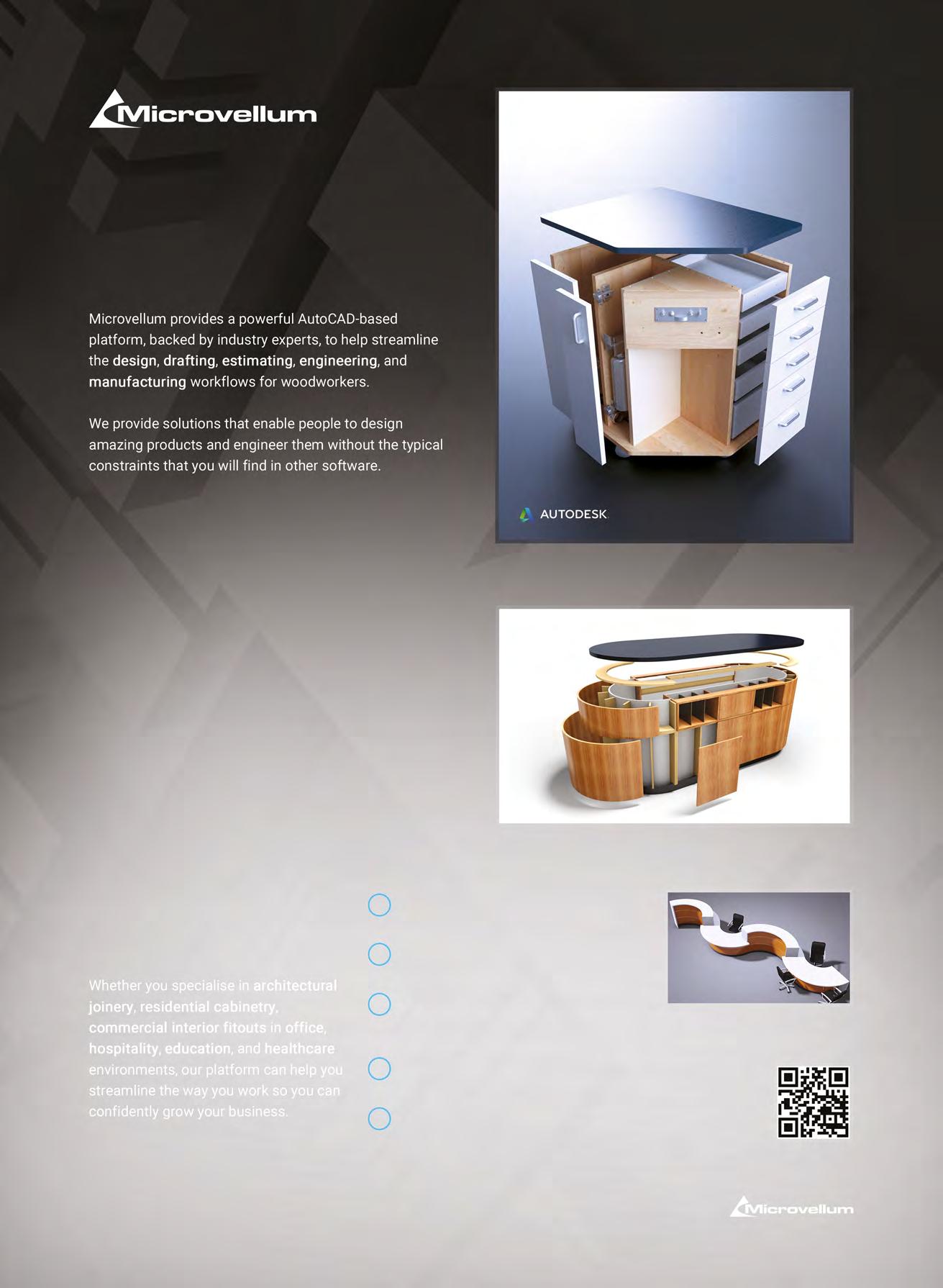
Lamin8 Scotland / Robe Lamin8 Scotland / Robert Sinclair Interiors
Confidently grow your business
Professional design and drafting tools built for woodworkers.
Predict your time, material and labour costs with confidence.
Limitless engineering possibilities allowing you to grow beyond simple cabinetry.
Helping you get the right data, in the Helping you get the right data, in the right place, at the right time.
A streamlined solution for design to CNC manufacturing
Four medals for skilled Blum workers at EuroSkills 2021
At EuroSkills 2021, the European vocational skills championship, young skilled professionals from across Europe came together in Graz to demonstrate their various skills. The four participants from Blum showcased their talent and took home one silver and three bronze medals.
At the seventh European vocational skills championship, which was the first to be held in Austria, Kevin Emhofer (CNC Turning), Mike Fink (CNC Milling), Lukas Schwärzler (Industrial Mechanics) and Lucas Dolinar (CAD Design) were the four young professionals to take part from Blum. And the result is certainly something to be proud of – the quartet from Graz took home one silver and three bronze medals.
Silver medal for Kevin Emhofer
The 22-year-old from Hoechst beat some tough competition in the CNC Turning category to take home the silver medal. “At first I was just looking at my workpiece and thinking, how am I supposed to do this in the time I have? But then I just started to put into practice what I’ve learned, step by step,” says Kevin, giving an insight into the competition. As he had just completed his national service, there was little time for him to prepare: “That’s why I never expected to come away with silver. The team spirit with the coaches and the other candidates was invaluable. It took the pressure off me and meant that I was never alone throughout the long competition. It feels really good to have the medal around my neck now,” says the European championship silver medallist in CNC Turning.
Three bronze medals round off a marvellous result
“We spent months preparing. The level at EuroSkills is really high and the three days of competition are very challenging. It feels fantastic to know that all the work was worth it and I’m happy that we were able to showcase our skills. The medal is the perfect reward,” says Mike Fink with a smile, as he reflects on his bronze medal in CNC Milling.
Lucas Dolinar also secured third place in CAD Design: “The long and intense training that I did to prepare paid off and everything went to plan for me at EuroSkills. I just wanted a medal. I didn’t mind whether it was bronze, silver or gold. This made the feeling of actually going up onto the podium even sweeter,” explains the 22 year old. The fourth member of the Blum team also impressed in the Industrial Mechanics category of the international competition and took home a bronze medal: “It wasn’t always plain sailing during the competition. I really had to keep a cool head. Right up until the end, I wasn’t sure if I’d done enough. Getting a medal is an indescribable feeling,” says Lukas Schwärzler.
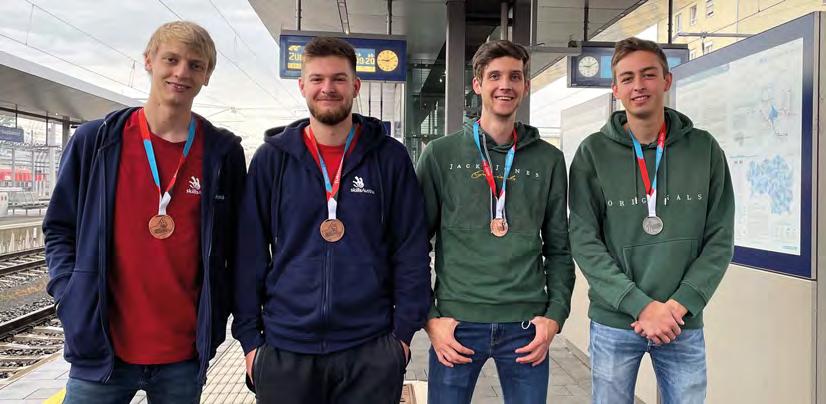
The four medal winners from Blum, from left: Lucas Dolinar (CAD Design), Mike Fink (CNC Milling), Lukas Schwärzler (Industrial Mechanics) and Kevin Emhofer (CNC Turning)
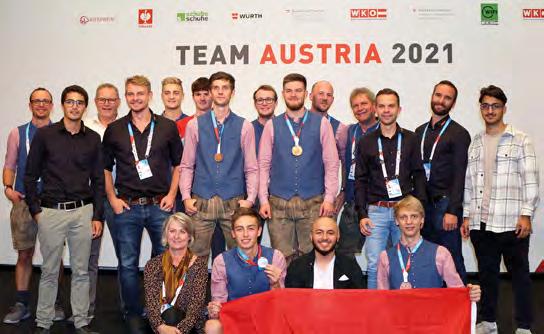
Right: Blum’s head of vocational training Dieter Hämmerle was more than happy with the performance of the competitors at EuroSkills 2021
Exceptional performances by apprentices and instructors
An international competition is always an exciting challenge for apprentices and instructors alike. “We are extremely proud of all our competitors and overjoyed by their outstanding achievements,” stresses Dieter Hämmerle, head of vocational training at Blum. “The best of the best compete at EuroSkills. The right frame of mind, nerves of steel and tolerances of a thousandth of a millimetre are crucial here.
“Our intensive preparation, which includes mental coaching and team-building exercises, has definitely paid off,” explains Dieter, adding: “We are delighted that EuroSkills 2021 took place – despite all the setbacks.
“This international competition is very important to us, as a company that believes in training and apprenticeships, because it also puts the quality of our vocational training to the test time and time again. Everyone is talking about the shortage of skilled professionals. These kinds of competition are all the more reason to help counteract this. Next time, I hope that we can compete with even more participants – and perhaps some female competitors too.”

Additional participants from Vorarlberg in Graz
Two more apprentices from Blum, Jonas Brunner and Marc Domig, were able to participate without official scoring, using the event as an opportunity to prepare for the upcoming national championship. Four coaches and three experts from the Blum team of instructors were on hand at the big event and supported the young, skilled professionals.
‘Team Vorarlberg’ was completed by three other participants and one jury member from the Vorarlbergbased company.
A total of 450 competitors across 45 professions took part – from 23rd-25th September 2021, competing for the coveted title of European champion in their categories.
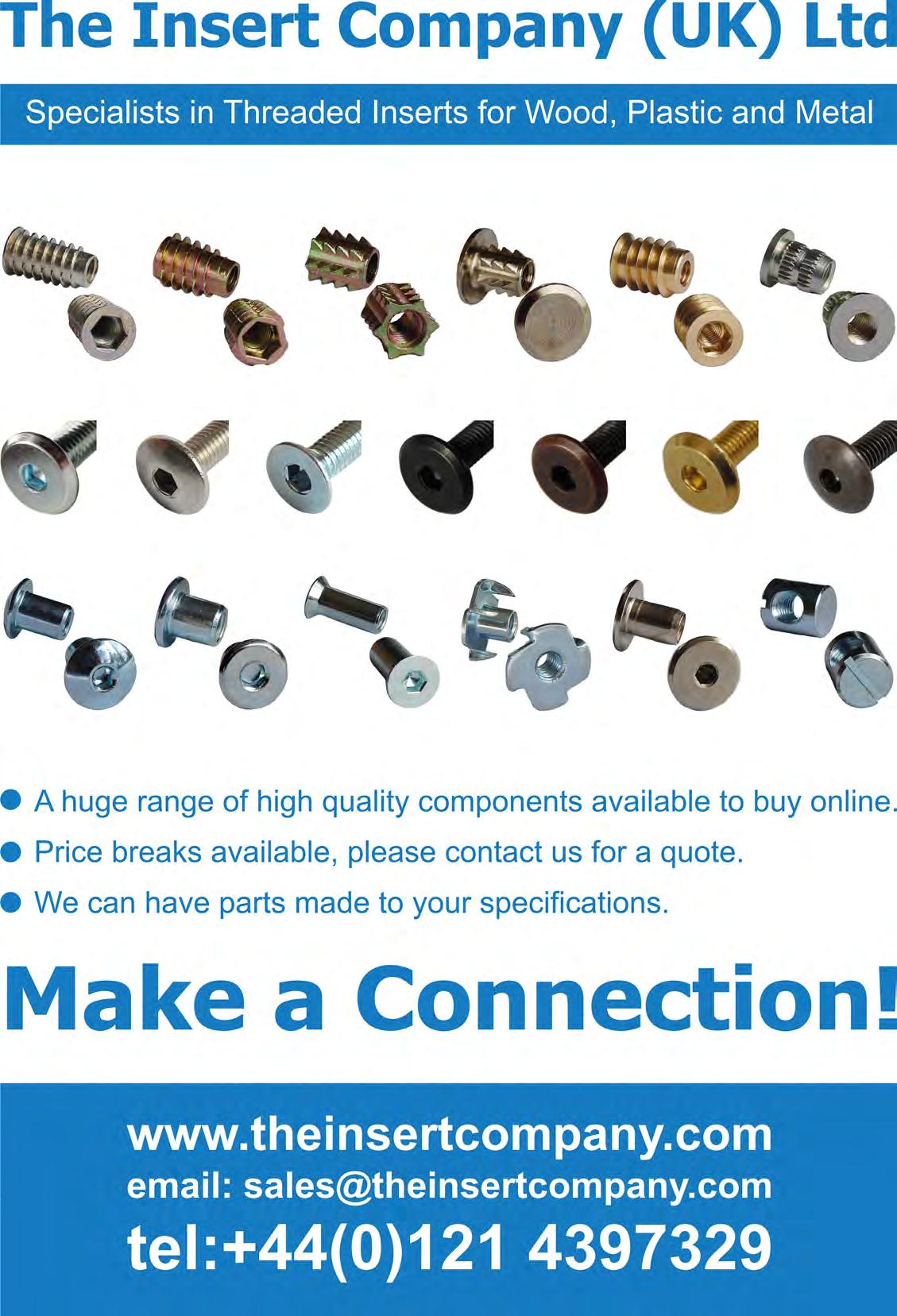
IDS extends website to include Minerva and Maia premium solid-surface worktops
Surface materials distributor IDS has updated its website to enable customers to purchase the Minerva and Maia ranges of premium solid-surface worktops by Sylmar at their convenience.
Trade customers who have signed up to use IDS’ website to purchase products now have the flexibility to buy Minerva and Maia products in a huge depth and breadth of sizes and decors 24/7, by logging on to www.idsurfaces.co.uk
Website customers can log in to their trade account at any time to place their orders, track their status and manage their account.
In addition to the Minerva and Maia ranges, customers can also purchase surfacing solutions from IDS’ expansive range, including flooring, worktops, bathroom wall panelling, high-pressure laminate, solid-surface and decorative panel, as well as sinks and taps.
Minerva and Maia solid-surface worktops offer a high-performance surface material with extensive design and fabrication flexibility. Within the Minerva worktop range there is a choice of 18 designs in a variety of sizes along with matching upstands, breakfast bars, splashbacks and prefabricated sink modules.
Maia offers 15 worktop designs in several sizes and thicknesses alongside breakfast bars, island units and sink modules. Both ranges are hand finished and ready for easy installation without specialist fabrication, and carry a 10-year guarantee. www.idsurfaces.co.uk
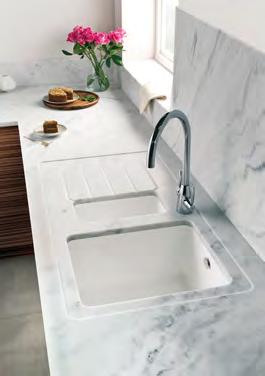
IDS has extended its website to include the addition of the Minerva and Maia ranges of premium solidsurface worktops by Sylmar
Technical paper aims to ‘set the standard’ for measuring embodied carbon in timber construction
Timber Development UK is bringing clarity on how to account for embodied carbon in timber construction, with a newly released technical paper.
‘Assessing the carbon-related impacts and benefits of timber in construction products and buildings’ explains how to account for carbon in timber buildings and Environmental Product Declarations (EPDs) by rigorously applying the latest British/European standards. This will prove useful for building designers, clients and contractors when assessing the embodied carbon associated with buildings and other structures, as well as product manufacturers and suppliers in demonstrating the carbon impact of their products.
Charlie Law, sustainability director at Timber Development UK, says: “The construction and built environment sector is responsible for nearly 40% of global CO2 emissions, and a significant proportion of this is through embodied carbon accumulated within the construction and manufacturing process. “Regulatory and professional focus has for the past four decades largely focused on operational carbon, such as heating in buildings, while embodied carbon emissions have been overlooked – but this is beginning to change. “Across the built environment professions there is a rising wave of awareness that if we are to build to net-zero carbon, we need to tackle how we account for embodied carbon. “This paper seeks to help unify how we account for embodied carbon within timber buildings and structures so we can better understand, measure, and address these emissions in order to reduce their environmental impact. “Along with the likes of Part Z and the Climate Emergency Design Guide, this paper seeks to help build understanding and drive forward low-carbon construction, and set the standard for measuring embodied carbon in timber construction.” Timber Development UK worked with Jane Anderson of ConstructionLCA to develop this paper, the first technical paper from this newly formed membership organisation which is aiming to bring together the entire timber supply chain. Timber Development UK was formed in 2021 by the merger of the Timber Trade Federation (TTF) and the Timber Research and Development Association (TRADA). By combining the membership of these two organisations, Timber Development UK has more than 1500 members, which extend all the way from sawmill to specifier.
This paper is free to download from the TTF website – https://ttf.co.uk/download/tduktechnical-paper/
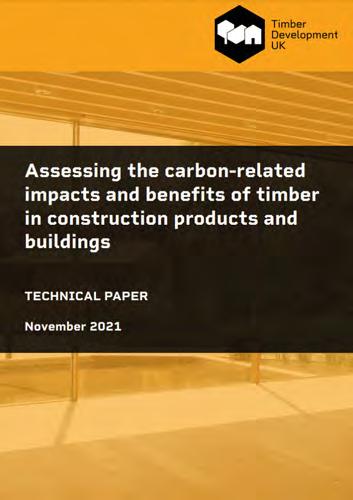
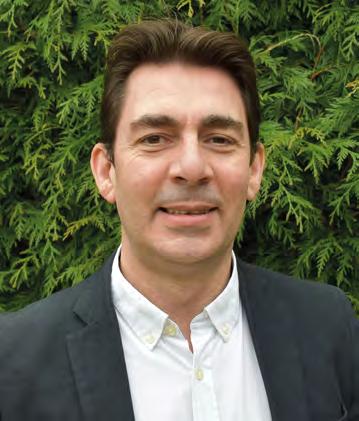
Charlie Law, sustainability director at Timber Development UK
‘This paper seeks to help unify how we account for embodied carbon within timber buildings and structures so we can better understand, measure and address these emissions in order to reduce their environmental impact’
Timber import patterns shift rapidly to meet high demand in Q3
New area sales manager appointed at Weinig UK
The market has proved responsive to high demand for timber in the UK, with imports sourced from a far broader range of supplying countries in Q3.
Demand for timber and panel products during the summer months of 2021 was at record levels, with import volumes over 3.2 million m3 in these three months alone.
August became the third consecutive month when import volumes exceeded one million cubic metres, with softwood imports surging to meet the uplift in construction demand.
Softwood imports in June, July and August 2021 were +33% higher than the same months in 2020, when demand for softwood began to recover during the first lockdown. A broader spread of countries have also been supplying this softwood to the UK in these three months compared to the same period in 2020.
Softwood import volumes significantly increased from many countries, including from Latvia by +53% (+175,000m m3), Germany by +93% (+120,000m3), and Canada by +195% (+12,000m3).
Other product groups followed similar trends, with hardwood imports rising by +30%, with substantially higher volumes arriving from the Baltics, Croatia and Hungary.
However, it was softwood plywood imports which saw the most radical change in Q3, with an increase in supply from China by +372% (29,800m3). David Hopkins, CEO of the Timber Trade Federation (TTF), says: “The timber industry has gone through a period of unprecedented demand through the summer as people invested in home improvements and maintenance.
“The changing trade patterns seen here show a resilient and innovative timber supply chain that is capable of harnessing new markets to satisfy the high domestic demand seen throughout the summer.
“As mentioned in our recent market statement, we expect demand to slow further in Q4 and in the new year as colder weather and post-Covid restriction spending habits ease demand for RM&I and private housing.
“It is likely however that demand for timber will remain strong as the Government looks to achieve climate targets, particularly as they emerge from COP26 with firm international commitments. “Timber is essential to building low-carbon in the UK, and this is reflected in the recent Net-Zero Strategy, with the Government endorsing a policy plan to increase the use of wood in construction.”
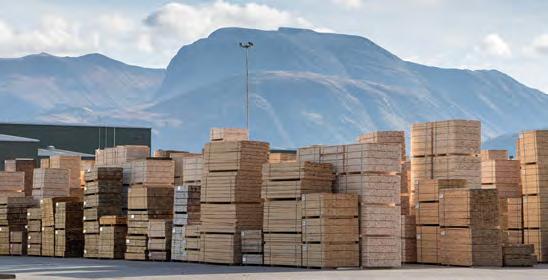
Andy Morgan has been appointed as the new area sales manager for leading woodworking machinery manufacturer, Weinig UK. Taking over the role from Dean Grimbley who, after 35 years with the company is moving on to pastures new, Andy will be responsible for Weinig machinery sales in the Midlands.
With over 20 years of experience as a bench joiner and woodworking machinist – and more recently, a software configurator and trainer for the woodworking industry – Andy’s interest in bespoke joinery and carpentry, combined with his comprehensive knowledge and technical understanding of woodworking machinery, makes him the ideal person to strengthen sales and develop key relationships with new and existing customers in his area.
“My background sees me approach things differently,” says Andy. “I’ve been a Weinig customer myself – spending seven years operating and maintaining Weinig’s Conturex machines – and during that time, I worked closely with Weinig’s aftersales and technical support team.
“I built great working relationships with them, and the support was the best I’ve ever encountered. Because of this, I firmly believe in Weinig’s product and service offering. I can be open and honest about the build and performance of Weinig’s machinery and the support that comes with it because I’ve experienced it first-hand. This was a huge driving force behind my decision to work for Weinig, and I’m excited to be working for a company that is so well respected in the woodworking industry.”
Malcolm Cuthbertson, MD of Michael Weinig (UK), adds: “Andy is a time-served wood machinist with a detailed understanding of the mechanics behind our machines. This, plus his experience working outside the manufacturing industry – helping joinery companies integrate control software into their production processes – makes Andy a great fit for Weinig, and I’m confident his skillset will make him a valuable asset to the Weinig team.
“I’d also like to take this opportunity to thank Dean for his 35 years of service, and the whole team wish him all the best in his next position.”
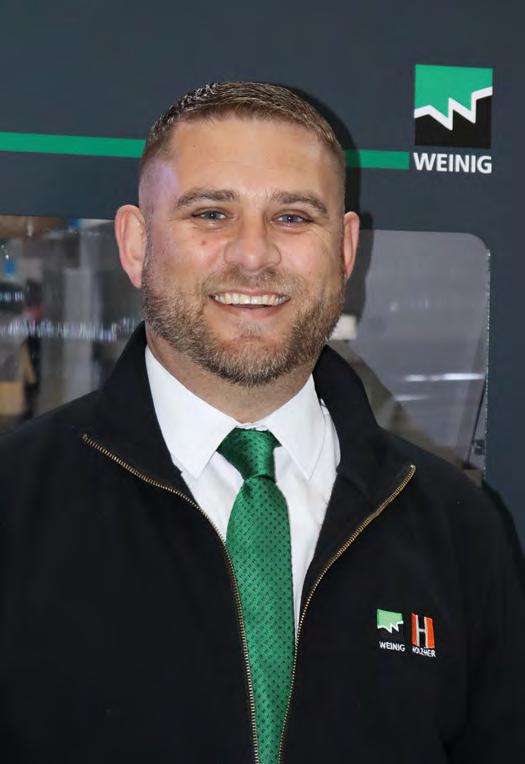

Global Forests need Global Governance – Tropical Timber Accord launches at COP26
A major new initiative to tackle illegal deforestation and strengthen legal governance frameworks in tropical forest producer countries and within international timber supply chains was recently launched at COP26.
Billed as a ‘call to action’ from the global private sector involved in forest management and timber production globally, the Tropical Timber Accord - ‘Global Forests need Global Governance’ highlights that strong, inclusive legal frameworks are essential for the sustainable management of tropical forests, which underpins all other climate policy ambitions. The paper proposes a new governance approach for the global tropical forest sector, based on national standards within an international framework. Crucially, it also proposes supporting an international secretariat to administer and oversee the development of this framework. Produced from a series of workshops with trade associations and businesses throughout the tropical production belt and facilitated and led by the UK Timber Trade Federation (TTF), the Accord is supported by associations in consumer nations including China, Europe and the UK. Vel Gnanendran, climate and environment director of the Foreign, Commonwealth & Development Office, says: “We really welcome this call to action that the TTF has facilitated. We have to be able to support growth in countries across the world where the forests are an important economic resource, but at the same time, protect and support our climate-change objectives.” Sheam Satkuru, director of operations of the International Tropical Timber Organisation, says: “Protecting and growing our global forests cannot be left to ‘one-sided’ approaches, but must be within a continual dialogue which supports sustainable production and shares the cost of enforcement.
“The tropical timber sector has a key role in achieving the forest management and conservation goals of COP26, and this requires the private sector, governments and civil society coming together to promote governance and sustainable management of resources.” David Hopkins, chief executive of the UK Timber Trade Federation (pictured), adds: “This is the first time that the global private sector of the forestry management and timber production industry has come together to speak with one united voice to advocate for greater global governance and enforceable legal frameworks in supply chains and within producer forest
countries. Now we need to start to put some of the detail behind those pledges into action, with a far stronger global legal framework governing the management of forests and the trade through the supply chains.”
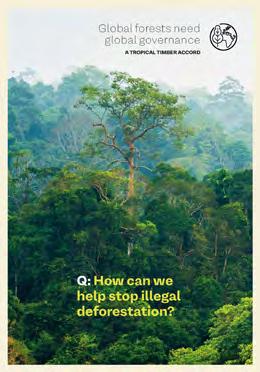
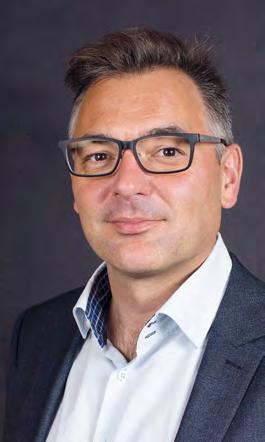
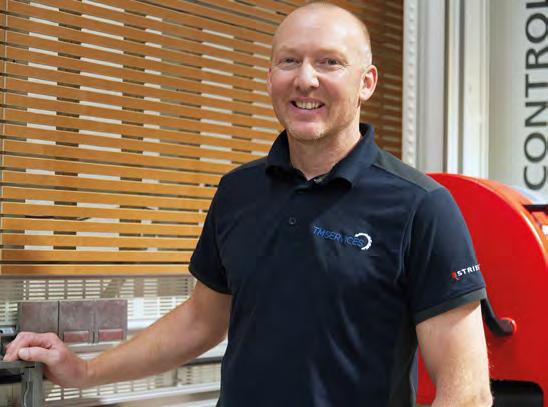
Meet the team – Darren Ismay, service engineer at TM Machinery
Meet Darren Ismay. While you may not recognise his face, if you have bought a reconditioned woodworking machine from TM Machinery in the last five years, you are sure to have experienced his work first-hand …
A self-proclaimed motorbike enthusiast and former racer with decades of experience working in manufacturing and motor mechanics, Darren joined TM Machinery in 2016 as an in-house engineer with responsibility for coordinating all machinery shipments going in and out of the warehouse, and refurbishing a wide range of used machinery. In the last six months, Darren has completed his level 3 apprenticeship, and is now a fully qualified engineer.
“Refurbishing machinery is a big part of my job and an area I take great pride in,” says Darren, 50. “I am currently working on five machines, each needing varying levels of refurbishment. It’s my job to get them looking and working like new.
“Every machine is thoroughly cleaned before being stripped down, with parts serviced and replaced. The machine is then set up and fully tested before being shipped to its new home.
“No job is ever the same and I really do love that – it keeps me on my toes. You also need to be a real problem solver, be open to approaching each project differently and have an eye for detail to get the job done well.”
Darren admits that he knows the machines he works on well – he’s even able to pick up on some faults through the tone of the motor – but this is where his technical abilities and passion for the industry shines though. This is not just a job for Darren, it is his hobby. This is a man that spends his weekends maintaining and prepping bikes for racing events and rebuilding models that date back to the 1970s. “The job is a good fit for me,” says Darren, and it is clear to see why.
His recent qualification has built on his existing skillset, with assessments in technical drawing, electrical testing, pneumatics, hydraulics and advanced maths for engineers. “It’s been over 30 years since I last stepped inside a classroom,” admits Darren, “but it’s been a brilliant experience.”
“It was always going to be a challenge, but my enthusiasm and experience working at TM has contributed massively to my development. It feels really good to work for a company that wants to invest in its staff and values the work we do. Because of TM Machinery, I’m now able to complete on-site machinery installations and offer on-site maintenance and repairs to our customers, while continuing to refurbish machinery. I get great job satisfaction out of my work, and knowing that I have a great team around me really adds to this.”
Made Smarter creates 60 digital leaders
Furniture manufacturers prepare for the challenges of a digital future with leadership programme
Two furniture manufacturers are among 60 firms pursuing smarter manufacturing through Made Smarter’s innovative leadership programme.
Pendle Doors, based in Darwen, Lancashire, and Inscape Interiors, a manufacturer of commercial cubicles, washrooms and fitted furniture, based in Chorley, Lancashire, were among the trailblazing businesses to embark on the programme.
Sixty digital leaders now have the vision and the skills after five cohorts of managers and directors at SME manufacturing companies completed the Made Smarter Leadership Programme through the Lancaster University Management School (LUMS), the University of Liverpool (UoL) and Manchester Metropolitan University (MMU).
The programme encourages current and future leaders to develop a new way of looking at their business and create a clear strategy to enable the adoption of digital technology, including how that can drive the net-zero agenda.
It uses a blend of workshops delivered by academics and experts in digital and leadership, site visits to SME manufacturers which are already on the journey of adopting digital technology, facilitated-learning sessions, and special project ‘sprints’ to test new ideas.
The programme also uses peer-to-peer coaching to create a trusted network of leaders, many of whom have remained in close contact.
With 60 SME leaders now empowered to transform their businesses, manufacturers across the North West are now being encouraged to register their interest for the next
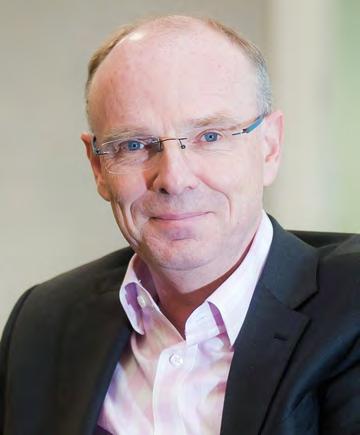
Professor Angus Laing, Dean of Lancaster University Management School
cohort intake, which started on 10th November at Lancaster University.
Reflecting on the success of the programme, Donna Edwards, director of the Made Smarter Adoption Programme in the North West, says: “I am delighted that the leadership programme has helped create 60 new digital leaders by giving them time out of their business to reflect on the bigger picture and share ideas and experiences alongside their peers in manufacturing, and then return to their own business and develop a digital strategy to create growth and efficiencies.
“They are among hundreds of manufacturers in the region grasping the opportunities offered by Made Smarter, which include expert, impartial technology advice, digital transformation
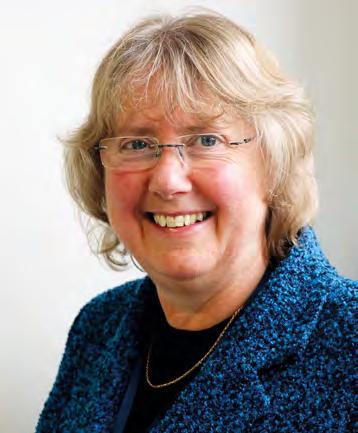
Donna Edwards, director of the Made Smarter Adoption Programme in the North West
workshops to help take that first step to transform a business, funded digital technology internships, and support with technology adoption projects.
“I would encourage SME manufacturers to make contact with Made Smarter to find out how we can help with leadership development, skills, and how to adopt technology the right way.”
The programme, which takes place over eight months, includes seven workshops led by both academics delivering leading-edge thinking and business practitioners demonstrating adoption in real business settings. Delegates will also embark on ‘sprints’ where they will test their ideas with other business leaders to build engagement and learn from each other.
>>
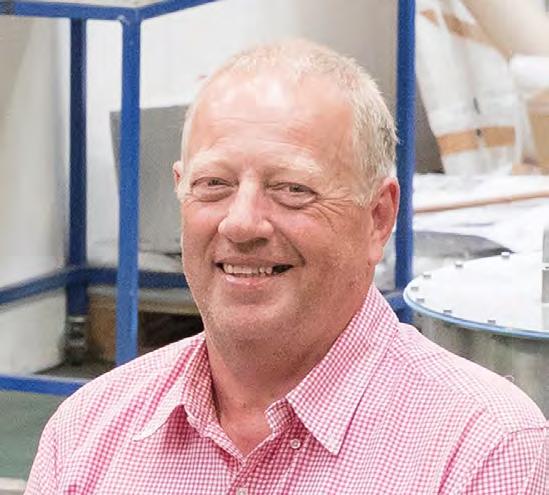
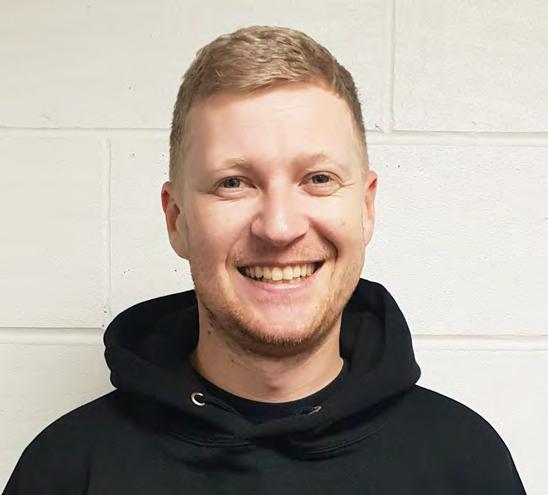
>>
Professor Angus Laing, Dean of Lancaster University Management School, says: “When we co-created the leadership programme with Made Smarter, our hope was to create a space for leaders to build their confidence, capacity and capability, to identify, test and adopt new technologies.
“It is clear from the feedback from so many of the leaders from the five cohorts who have now embarked on this programme that they have reaped great benefit from taking vital time away from the business to develop a strategy to adopt hi-tech and digitally based manufacturing techniques into their own production processes, while bringing employees and other stakeholders along on their digital transformation journey.” Registration for the next leadership programme is now open. www.madesmarter.uk
“I would encourage SME manufacturers to make contact with Made Smarter to find out how we can help with leadership development, skills, and how to adopt technology the right way”
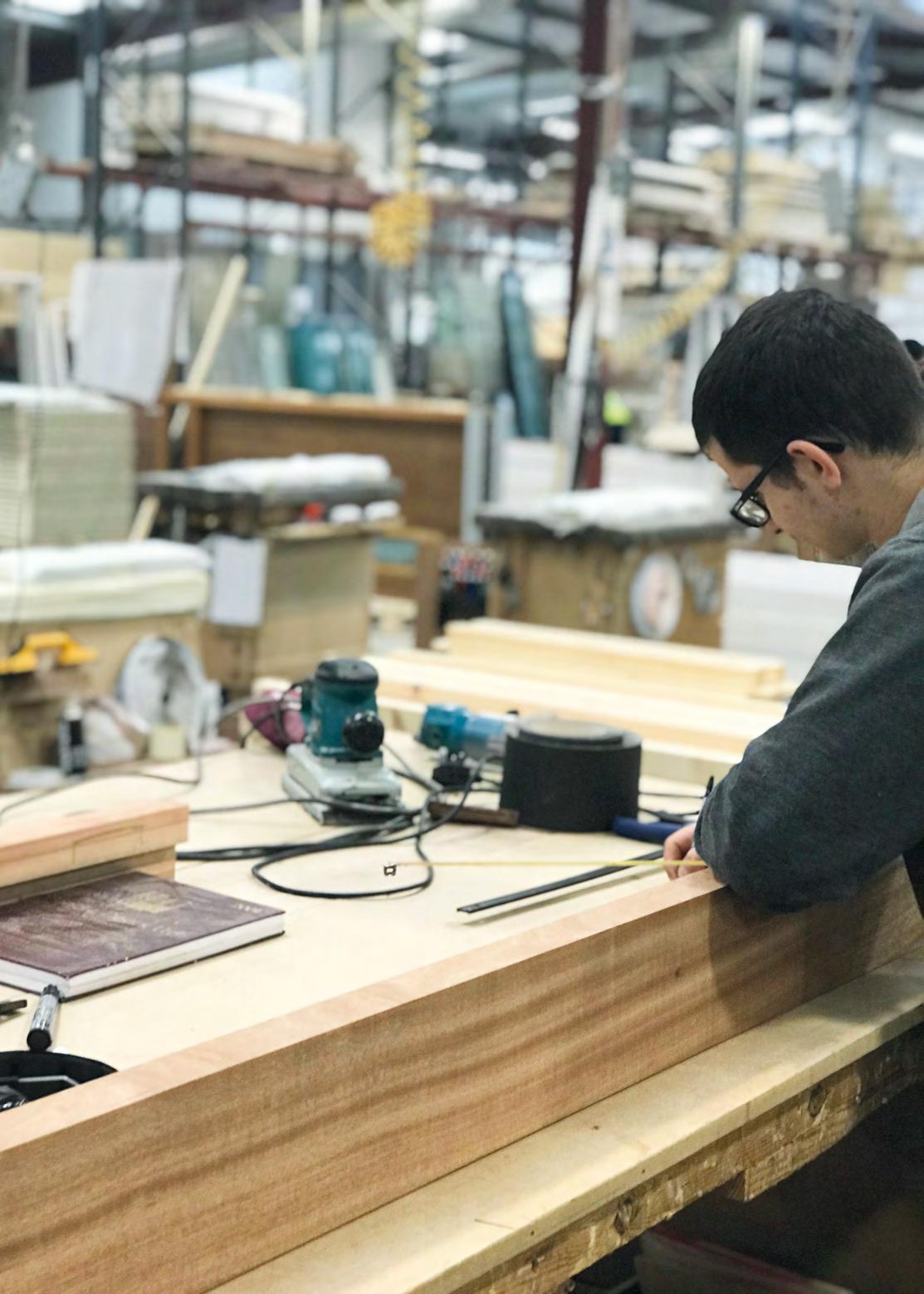
New HOMAG woodWOP software makes wood processing effortless
With the release of the latest generation of woodWOP in Q4 2021, HOMAG has dramatically improved the functionality of its market-leading CNC programming software. This most recent edition is branded woodWOP 8.
Unparalleled success story
The woodWOP success story began with its launch in 1991 and its development now spans over 30 years. The success of the woodWOP software is arguably unparalleled within the wood processing industry. Since its launch, more than 30,000 CNC machines have been equipped with woodWOP and 60,000 licenses have been sold to satisfied customers.
At the heart of this easy-to-use software is the innovative large graphic area in which the workpiece is displayed in three dimensions. Trimming and drilling or saw cuts are programmed quickly and easily by entering the machining parameters and are displayed realistically in the graphic.
Significant development leap made in collaboration with professional carpenters
HOMAG has always excelled at involving its customers in the improvement of its products. This collaboration has been continued with the further enhancements of the woodWOP software. HOMAG’s product development team worked closely with professional carpenters to evaluate the developmental requirements of the software to produce woodWOP 8.
The newly developed software now provides woodworkers with practical wizards for easier processing. This has made working with the woodWOP software more convenient, userfriendly and ultimately faster than working with its predecessor.
Key innovations of woodWOP 8 at a glance 1. Contour wizard provides improved support for beginners
New workpieces can be programmed more conveniently. For example, template files will be stored for circles, L-shapes or other curved components. This has a significant advantage in terms of time savings and it reduces novice operator problems.
2. Feature recognition for the automatic attribute identification
With the feature recognition technology holes, grooves and slots are directly recognised in a 3-D workpiece model. The appropriate machining macro is generated for automatic subsequent machining. This represents a significant acceleration in the conversion from CAD import to the machining program. The optimal use of existing data is also ensured.
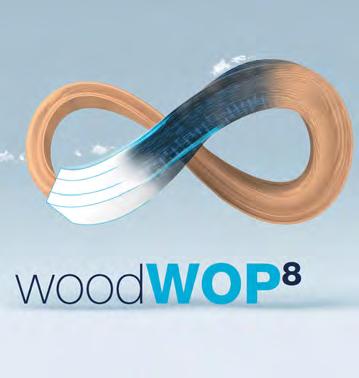
3. Formula view and additional help graphics to simplify operation
The woodWOP 8 programming process is faster and easier than before, with incorrect operation minimised. The software’s variable table has also been extended and upgraded to deliver new operational possibilities.
Minimum and maximum values can be defined, selection lists can be created and help graphics can be stored for illustration. New properties such as ‘Hide’ (hide line) and ‘Boolean’ (input via checkbox) along with two views – the list view and form view – make programming clearer.
4. Glueing wizard for efficient edgebanding
The glueing wizard is integrated directly into woodWOP 8. With this wizard, all work steps for edgebanding are generated automatically after defining the contours and corners.
The revised technology database provides support for situation-dependent inputs, C-angles and heating power. The import of edge images from external CAD systems is also possible with the new wizard. So an even faster creation of programs with edge glueing is ensured.
5. Formula wizard for the easy creation of complex formulas
The new formula wizard makes creating formulas extremely easy. The user has everything in view in the multi-line formula field. Building blocks such as mathematical functions, variables and conditions are at the user’s fingertips for assembling his formulas.
The formula components are highlighted in colour. This means that even complex formulas are clearly displayed. In addition to the formula result, partial results can also be calculated. These useful features support the simple creation of extensive and variable programs.

Mass changes to macros for quick and easy adjustments
With the transfer of parameter values, mass changes to macros can be made quickly and easily in just four steps, as outlined below: 1. Make changes in a macro. 2. Transfer one or all parameters to the parameter clipboard. 3. Select all other macros to be changed. 4. Insert the parameter value(s).
Significant improvements and added value
Commenting on the new software, Simon Brooks, HOMAG UK’s managing director said: “The development of the woodWOP software has been incredibly well thought out. The new and updated functions of the software make wood processing operations safer, easier and quicker.
“The latest version brings great added value and, like all previous editions of woodWOP, is intuitive to use. A notable increase in functionality, along with time-saving operation characterise the new woodWOP 8 software.”
For more information on woodWop 8, visit the news section of the HOMAG UK website to watch the presentation video and download the product brochure. Alternatively, contact Adele Hunt at HOMAG UK. 01332 856424 www.homag.com
Looking back on a record year
Considering the obstacles and challenges that seemed to constantly pop up in 2020, the fact that forklift manufacturer Combilift had a record year is a cause for celebration and proof that certain sectors are experiencing healthy growth. Company CEO and co-founder Martin McVicar attributes some of this success to the relentless rise of ecommerce – already noticeable pre-pandemic but which has mushroomed in the last year or so.
For some manufacturing and retail sectors, working from home drove demand for certain products, as did the lack of opportunities to travel, which saw rising spending on home comforts and garden accessories, which in turn had a knock-on effect on Combilift’s order books. “In 2020 we produced a record 6830 units, and our predicted truck order intake for 2021 is at an all-time high,” says Martin.
A quick look back over 2021 proves that, as ever, the engineers and the R&D department in Monaghan were busy.
In February the launch of the new AME-OP order picker was announced, and this variant of the Aisle Master articulated forklift will be much appreciated by companies that are under pressure to get orders processed, picked and delivered as quickly as possible.
This is a stand-on electric powered truck, a main feature of which is the step-through operator compartment. The low floor height of just 280mm enables convenient, single-step access from both sides of the truck, which speeds up order picking compared to the operator having to get in and out from a seated position.
Crucially, for maximum versatility, the AME-OP offers all the key advantages of the conventional Aisle Master – indoor/outdoor operation for loading/offloading and for stock replenishment at other times during shifts when order picking is not required.
As reported throughout the year, many Combilift users are switching to electric fleets for environmental and sustainability reasons, and Combilift’s expanding range of electric models is helping customers to reduce their carbon footprint. The first electric C-Series truck was built over 18 years ago, and now more than 60% of the manufactured units are electric, with availability in almost all models across the range.
The new Combi-XLE was launched in September, and this multi-directional forklift with up to five-ton lift capacity combines quiet, emission-free operation with powerful performance for a wide range of industries and applications. Since electric-powered trucks do not have traditional combustion engines, or hydraulic transmissions, there is no longer any need to check and top up engine fluids/ lubricants, resulting in longer intervals between services, ultimately saving costs.
Looking forward now and not back, Combilift is exhibiting at W22 in February, so at long last there will be an opportunity to catch up once again with the team at the NEC – stand G700 – and to check out new Combilift products up close and personal. www.combilift.com
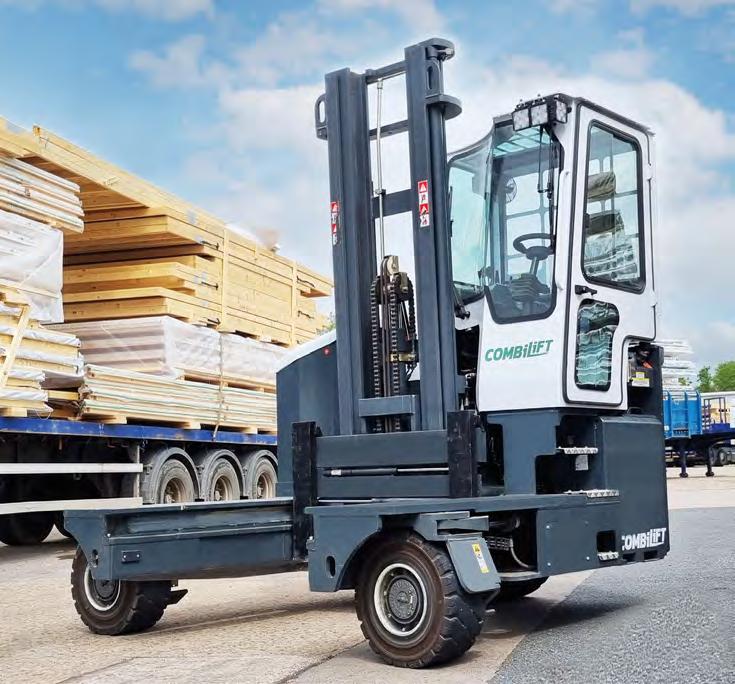
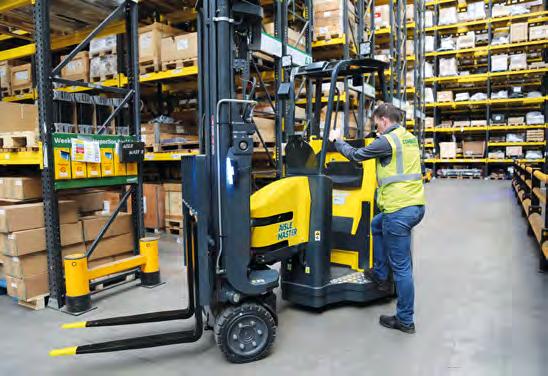
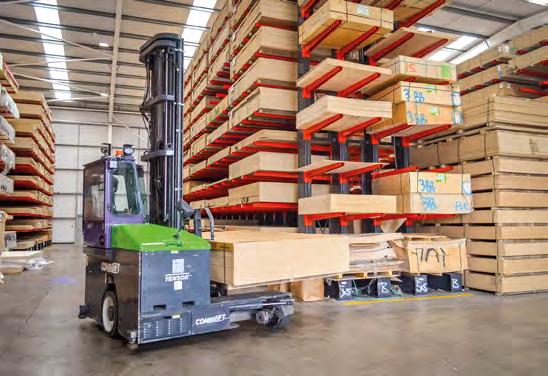
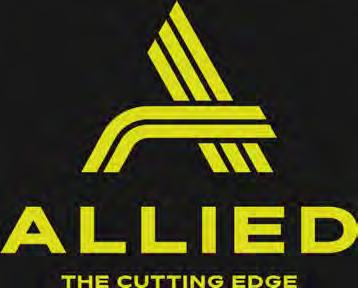
A new age for nesting with CLF Compression Spirals After the successful launch of our CLF and CLF+ Compression Spirals in 2020, we have now extended the range with; diameters from 4mm - 20mm, 2 different geometries dependant on machine orientation, Z2+2 & Z3+3 and now available with our internally developed ‘Slick’ coating. A new age for nesting with CLF Compression Spirals After the successful launch of our CLF and CLF+ Compression Spirals in 2020, we have now extended the range with; diameters from 4mm - 20mm, 2 different geometries dependant on machine orientation, Z2+2 & Z3+3 and now available with our internally developed ‘Slick’ coating. A new age for nesting with CLF Compression Spirals After the successful launch of our CLF and CLF+ Compression Spirals in 2020, we have now extended the range with; diameters from 4mm - 20mm, 2 different geometries dependant on machine orientation, Z2+2 & Z3+3 and now available with our internally developed Our CLF+ Compression Spirals can reach feed rates as high as 50 M/Min when nesting. This feed rate combined with our *‘Slick’ coating offers the end user reduced cycle times and reduction in downtime. Our CLF+ Compression Spirals can reach feed rates as high as 50 M/Min when nesting. This feed rate combined with our *‘Slick’ coating offers the end user reduced cycle times and reduction in downtime. ‘Slick’ coating. Our CLF+ Compression Spirals can reach feed rates as high as 50 M/Min when nesting. This feed rate combined with our *‘Slick’ coating offers the end user reduced cycle Whilst others are imitating, we are innovating! Whilst others are imitating, we are innovating! times and reduction in downtime. Whilst others are imitating, we are innovating!
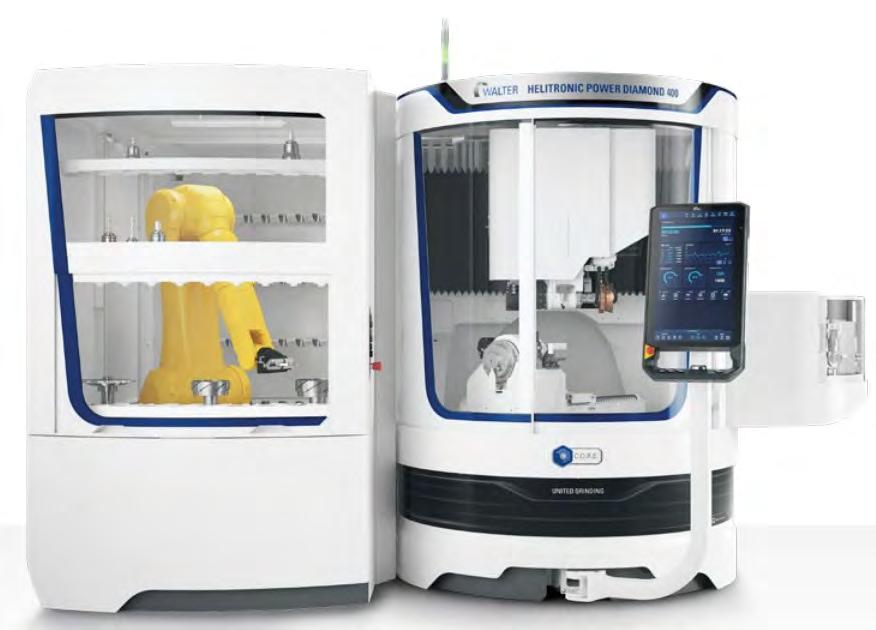
*With an sp3 content of 80 – 90%, our ‘Slick’ *With an sp3 content of 80 – 90%, our ‘Slick’ coating reaches a hardness of over 5000 HV. coating reaches a hardness of over 5000 HV. The thin, smooth, and extremely hard coating is designed to maintain maximum cutting edge sharpness in machining abrasive materials. The thin, smooth, and extremely hard coating is designed to maintain maximum cutting edge sharpness in machining abrasive materials. *With an sp3 content of 80 – 90%, our ‘Slick’ coating reaches a hardness of over 5000 HV. The thin, smooth, and extremely hard coating is designed to maintain maximum cutting edge Continued Investment in PCD Erosion In September 2021 we took delivery of our 4th PCD Erosion Machine. This time we invested with Walter by ordering their Helitronic Power Diamond 400 with Tool Studio. This Tool Studio, operated by a Fanuc Robotic Arm, has the capacity to hold up to 80 PCD Tools. Continued Investment in PCD Erosion In September 2021 we took delivery of our 4th PCD Erosion Machine. This time we invested with Walter by ordering their Helitronic Power Diamond 400 with Tool Studio. This Tool Studio, operated by a Fanuc Robotic Arm, has the capacity to hold up to 80 PCD Tools. Continued Investment in PCD Erosion In September 2021 we took delivery of our 4th PCD Erosion Machine. This time we invested with Walter by ordering their Helitronic Power Diamond 400 with Tool Studio. This Tool Studio, operated by a Fanuc Robotic Arm, has the capacity to hold sharpness in machining abrasive materials. The Walter accompanies our 2x existing Vollmer QXD 250’s with 27 tool carousels. With 4x PCD Erosion Machines, operating 24/7, we can now offer the end user an unrivalled service. The Walter accompanies our 2x existing Vollmer QXD 250’s with 27 tool carousels. With 4x PCD Erosion Machines, operating 24/7, we can now offer the end user an unrivalled service. up to 80 PCD Tools. The Walter accompanies our 2x existing Vollmer QXD 250’s with 27 tool carousels. With 4x PCD Erosion Machines, operating 24/7, we can now offer the end user an unrivalled www.alliedtooling.com sales@alliedtooling.com service. +44(0)1202 675767 www.alliedtooling.com sales@alliedtooling.com +44(0)1202 675767 www.alliedtooling.com sales@alliedtooling.com +44(0)1202 675767
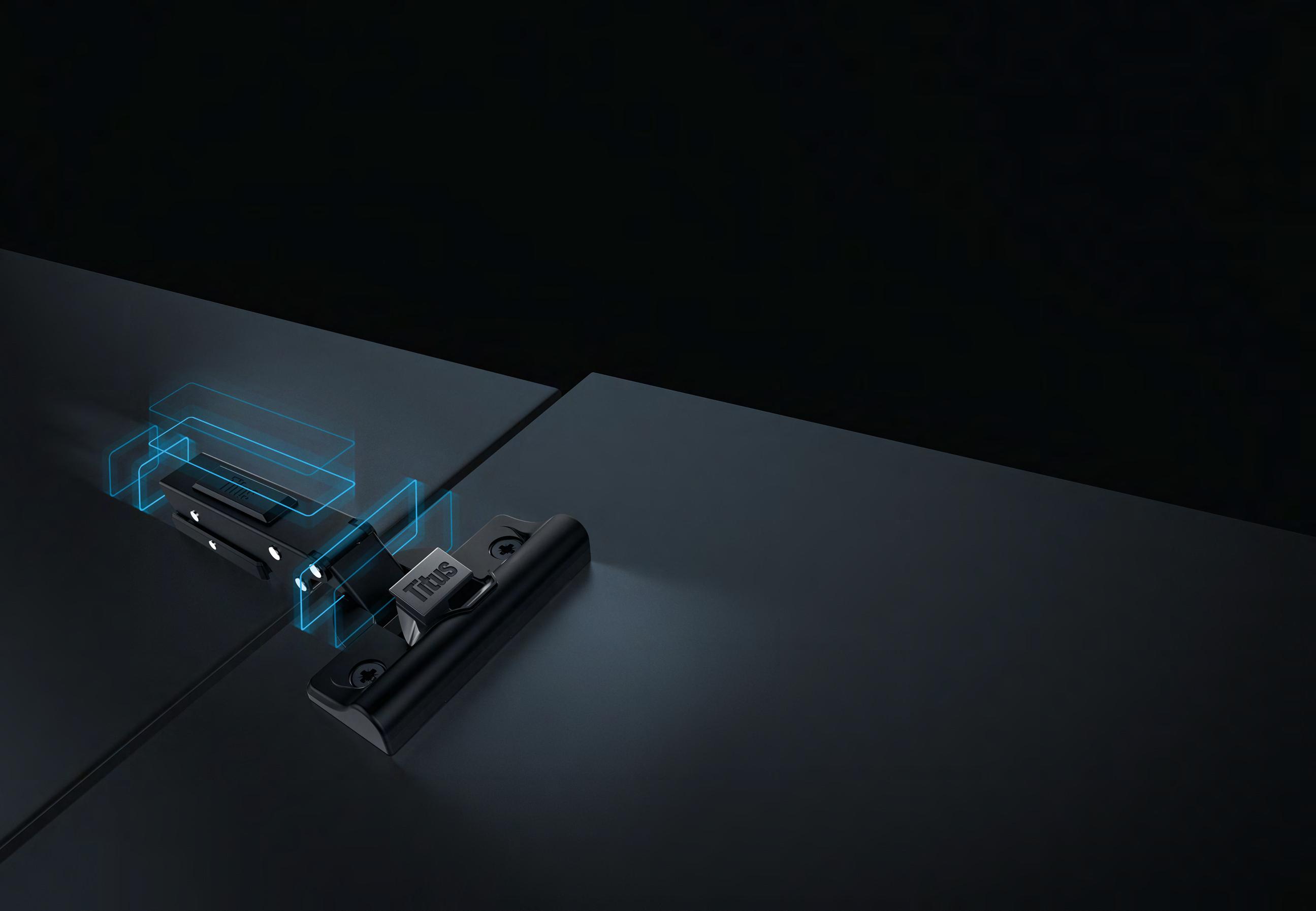
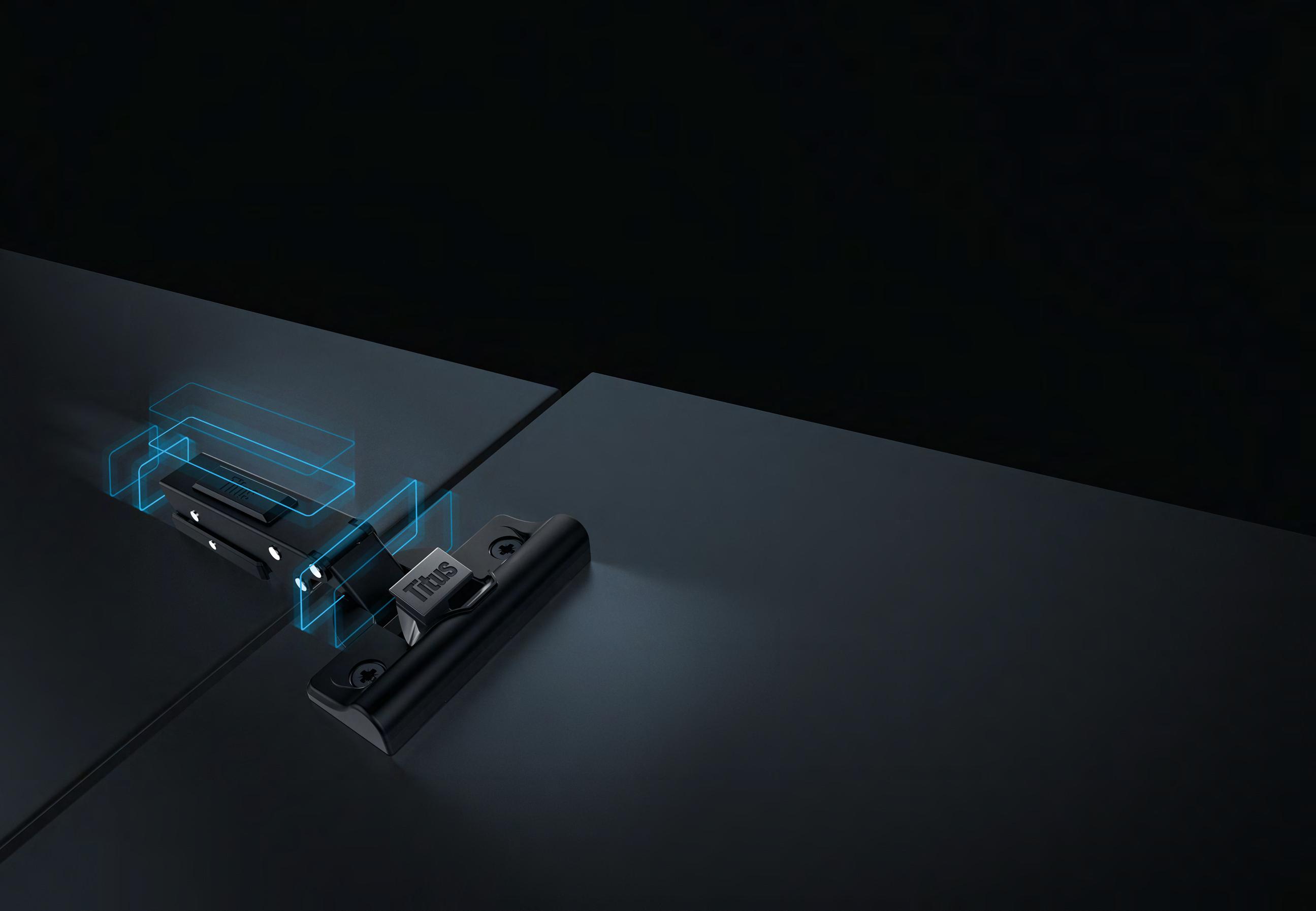
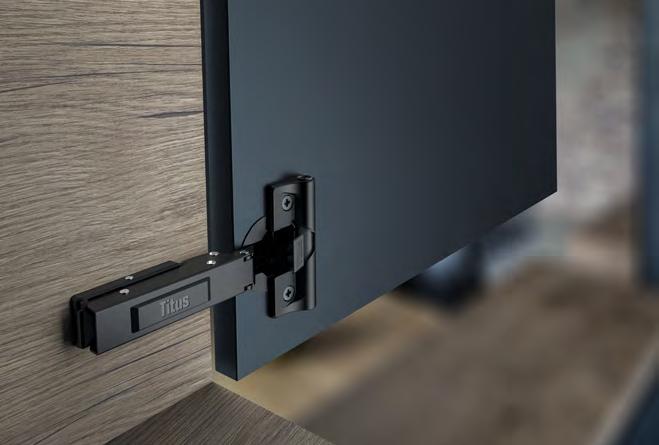
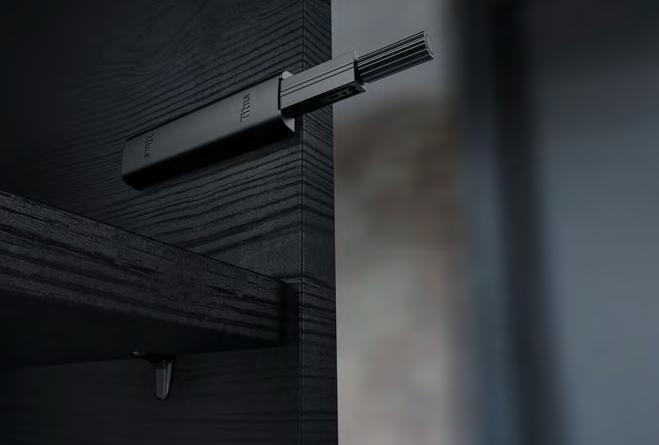
Business Sentiment Index (BSI) – optimism at record levels
The Close Brothers Asset Finance Business Sentiment Index (BSI) has continued to rebound, rising to record levels as confidence returns to key sectors – most notably in manufacturing, which broke through the 40-point mark for the first time, in spite of the well-publicised supply chain delays, slower new order growth and rising material and labour shortages.
According to the monthly purchasing managers’ index, manufacturing production increased for the 16th consecutive month, and jobs growth was registered for the ninth month running.
Manufacturers remained positive for the year ahead, with nearly two thirds of firms predicting their output would increase during the coming 12 months, compared to 6% expecting a contraction. This confident outlook was attributed to recoveries in both domestic and global markets, reduced difficulties from supply chains, Covid-19 and Brexit, and planned new product launches.
Challenges facing manufacturers include production schedules being disrupted by a combination of input shortages, longer supplier lead times and capacity constraints, including difficulties with staff shortages and hiring staff with the required skills.
Average vendor lead times also increased significantly because of delays to air, land and sea freight, staff shortages, COVID-19 and Brexit disruptions, a lack of delivery drivers, and port delays.
About the BSI
The BSI is calculated and based on business owners’: • appetite for investment in their business in the coming 12 months • access to finance and whether they have missed a business opportunity through lack of available finance • views about the UK’s economic outlook, and • thoughts on their likely performance in the coming 12 months
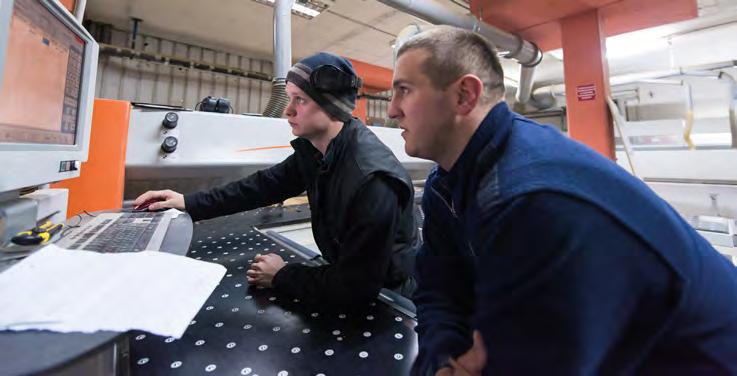
Appetite for investment
Firms’ appetite to invest increased strongly, returning the sector’s strongest figures ever recorded for this measure. More than three quarters of respondents indicated that they plan to seek funding for business investment in the coming 12 months.
Looking ahead at potential headwinds, 65.3% of manufacturers have pinpointed Brexit as a cause of concern, saying it has made it both more difficult to buy from – and sell to – the EU.
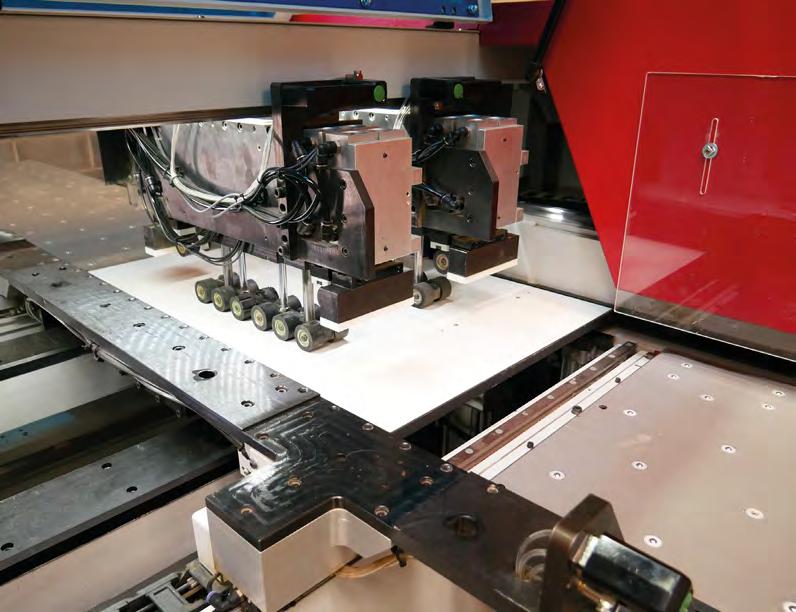
Missed opportunities
Nearly half of manufacturing firms have missed a business opportunity because of a lack of available finance, despite the availability of Government-backed loans. Many businesses now require additional finance to enable them to invest in growth and continue their recovery.
Cashflow is, by some distance, the biggest concern manufacturers currently have, with 34% selecting the option. This is followed by competitive pressure, late payments (both 14%) and the lack of skills staff (10%).
Economic outlook
Positivity about the economic outlook continued to rebound after a strong increase earlier in the year.
Over half of manufacturers (52%) expect the economy will continue to grow, while a further third anticipate a ‘slow path to prosperity’. Only 7% feel there has not been any real economic growth.
Predicted business performance
After a surge in business growth confidence in April, 44% of manufacturers predict their operations will expand, up from 39%. Nearly half (46%) think they will ‘stay the same’ into 2022 – only 9% foresee a contraction. www.closeassetfinance.co.uk
Ergonomic handling solutions from TAWI

TAWI is a market leader in manual handling solutions. Proud to claim that it designed the first-ever vacuum lifting aid in 1989, TAWI has been constantly innovating new solutions ever since to provide customers with the newest and most reliable technology. The equipment is beautifully versatile, with different mounting options and interchangeable feet to allow easy lifting and turning of panels of all shapes and sizes.
Designed with ergonomics and comfort in mind, TAWI’s manual handling aids remove 100% of the weight of goods from the operator. This allows them to achieve optimum levels of productivity and precision, in turn reducing production errors and workplace injury.
LG Collection has 40 years’ experience in manufacturing panels in various materials, including wood and laminated panels. After complaints from employees experiencing shoulder and back pain due to repetitive lifting, the decision was made to invest in one TAWI system.
Bjorn Skoglund, production leader at LG Collection, describes how the team went from one unit to 20 after realising the benefits that it was experiencing through its new investment: “Employees can keep an even pace throughout the whole day without straining their bodies,” he says. “The amount of sick leave has reduced significantly and employee satisfaction has been noticeably better, as employees can now avoid pain and physical tiredness.”
Andy Longrigg, area sales manager at TAWI UK, adds: “We are seeing more enquiries nowadays after a bad accident has happened, or because health and safety requirements
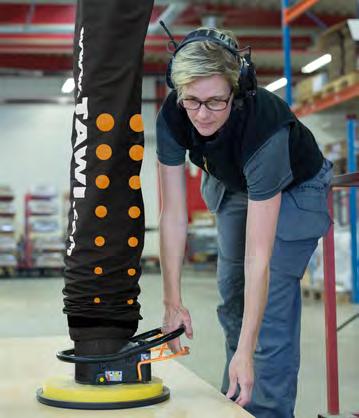
LG collection
are becoming stricter. These accidents are avoidable, and by proactively introducing aids such as these, staff injury and stress can be massively reduced.
“We will always ensure that you have the best possible solution for you and your staff, and we offer a free visit to site to discuss your requirements and view the space you and your team are working in.
“Once installed, we have a dedicated aftersales team who will keep the equipment safe and up to date for its lifetime. We value the relationships we build with our customers, and we will make sure you have the full support of the entire team throughout your working relationship with TAWI UK.” www.tawi.com
LG collection

Edging Supplies

Edging Supplies was formed in July 2018 by Kal Sandhu and Derrick Gray. Based in Malvern, Worcestershire, the company was set up to supply the furniture manufacturing industry with edgebanding and ancillary products.
With over 25 years’ involvement in this market and a good customer base built up over many years, Kal and Derrick were well placed to set themselves up – so long as they had a good supplier base behind them.
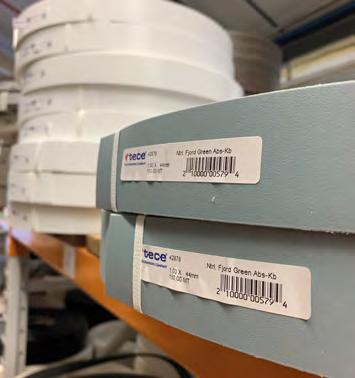
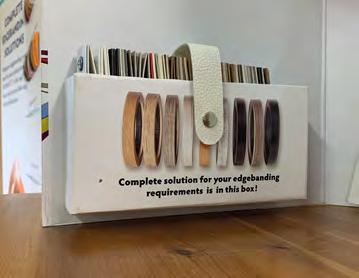
Edging Supplies’ major supply partner is TECE, based in Turkey. TECE, which was established in 1987 and is known as a major producer and supplier of edgebanding worldwide, has supported Edging Supplies since its conception.
It is with suppliers like TECE and many more that the business is able to give such a high level of service and support to its customer base. Edging Supplies’ ethos of quality, service and reliability is closely aligned with its suppliers in this ever-demanding world.
Edging Supplies has a comprehensive range of edgebandings and ancillary products which it stocks at its warehouse in Malvern. There are over 400 product lines and more than two million metres of edgebanding, all available on a nextday delivery. Edging Supplies holds a range of products, from ABS, PVC, melamine, and veneer edgebandings to ancillary products such as selfadhesive cover caps, repair waxes, edgebander adhesives and panel cleaners. sales@edgingsuppliesltd.co.uk www.edgingsuppliesltd.co.uk
Kal Sandhu
07384 810271 kal@edgingsuppliesltd.co.uk
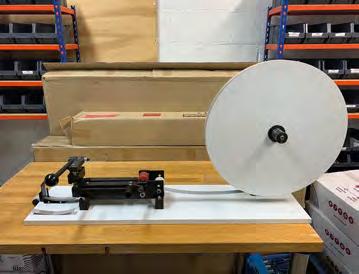