
6 minute read
CALDER GARDENS: THE LATEST ADDITION TO PHILADELPHIA’S “MUSEUM MILE”
CALDER GARDENS: THE LATEST ADDITION TO PHILADELPHIA’S “MUSEUM MILE”
BY JESSICA MATASE SLATTERY, DIRECTOR OF MARKETING | LF DRISCOLL
If there’s one thing Philadelphia does well (besides cheesesteaks), it’s museums. Modeled after the ChampsÉlysées, the city’s Benjamin Franklin Parkway boasts what is also referred to as “Museum Mile” thanks to the many cultural institutions located along the way. Philadelphia’s own LF Driscoll has led the construction of many of them, including the Barnes Foundation, Rodin Museum, Free Library, and the long-time master plan and Core Project expansions at the famed Philadelphia Museum of Art.
The team is now adding another cultural institution to this impressive list: Calder Gardens. Expected to open in 2025, Calder Gardens will serve as an 18,000sqft exhibition space for a variety of modernist sculptures created by famed artist—and native Philadelphian—Alexander Calder.
Designed by Herzog & de Meuron with Ballinger as architect of record, the planned building appears modest in size on the surface. However, as visitors enter at ground level, they will have the opportunity to descend two more levels that include galleries with a variety of art experiences. From a curved gallery that runs along the exposed concrete ceilings to a sunken gallery and smaller rooms at the lower level. “This building is like nothing else. Everything is custom,” says Jack Garrett, LF Driscoll’s senior superintendent. “We’ve assembled an expert team to make this kind of artistic vision a reality.”
The Calder Gardens building is designed to be built almost completely of exposed concrete—with walls up to 7 feet thick. That means all building systems, walls, windows, built-in benches, art displays, and other features had to be fully coordinated and meticulously planned before the concrete is poured. LF Driscoll is known for its ability to take on complex building challenges. For this project, the team leveraged virtual construction techniques and a close working relationship with the design team and subcontractors to align the many moving parts into one rock-solid plan.
The collaboration level is very high. We’re working with our subs in almost a design-assist fashion to make this vision a reality,” says Garrett. “Everything we’re doing has required detailed discussions and coordination before we begin because once the concrete is poured, it’s done.

The structural concrete was only one of the many complexities of the project. The design is intended to keep a low profile to let the artwork shine, so every detail involves a unique approach.
Finishes and formwork. Between the different types of concrete and the wood finishes here and there, accomplishing how the different finishes meet up and work with the structural concrete was no easy task. “The windows have concealed sills and frames; they are recessed behind the concrete and finished walls,” says Garrett. “That is certainly unique, so we had to work with the design team to identify the exact thickness and specs for each one.”
And because the walls and ceiling of one of the primary staircases is being built from shotcrete-applied concrete, the design team was concerned about handrails having a rough finish. So, LF Driscoll brainstormed with the team to determine what could be applied there without detracting from the aesthetic. Just outside of the main galleries is the Vestige Garden where the textured finish of the exposed concrete walls was achieved by stripping the formwork several hours after placing the concrete so that it could be “scratched” with the claw of a hammer. This created a natural, geological appearance reminiscent of a rock formation.
“If you ask me, I would say with all of the custom finishes on this project, the scratched concrete would be the most unique. That was definitely a first for all of us,” says LF Driscoll’s senior project manager Andrew Klinger.
The project also includes other unique finishes such as wood siding, venetian plaster ceilings, polished concrete floors and walls, and a very custom stainless steel metal panel façade. A mockup was built prior to building construction in which several different wood species and stainless-steel metal panels were erected. The main lobby level and portions of the galleries will be clad with wood siding to complement the board-formed cast-in-place concrete walls in the galleries. The main façade and entry canopy facing the Parkway is a custom #7 stainless-steel finish with a dulled reflection.
“The team went to great lengths to develop QA/QC guidelines for evaluating the custom stainless-steel panel finish due to the custom nature and specific aesthetic requirements of the design team,” says Klinger.
Gardens. As the name of the project would suggest, the gardens and landscaping are a main focal point of the design even beyond the artwork. The landscape was designed by world renowned landscape architect Piet Odoulf. The team has worked closely with the landscape architect and local nurseries to source the selected plantings. The dulled reflection of the custom stainless-steel façade provides a soft backdrop for the expansive gardens and almost makes the building disappear behind them.
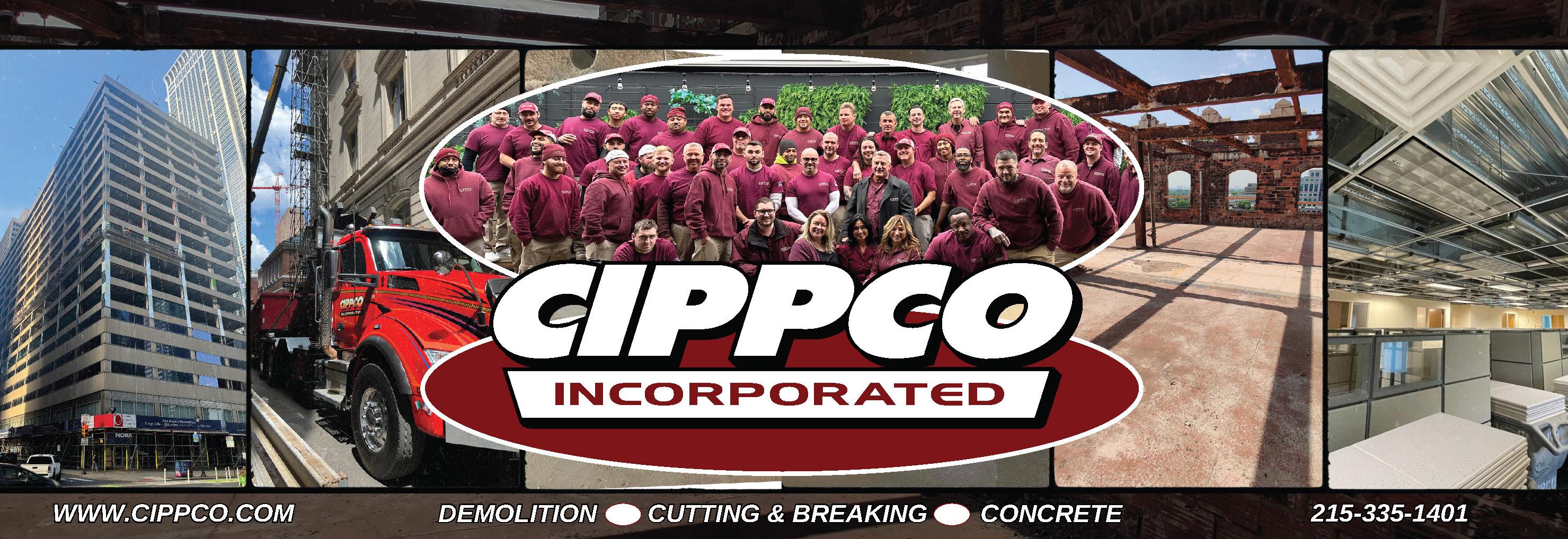
Specialty lighting. The role of light on and around art is, of course, critical. The building’s design very intentionally balances natural light with subtle lighting fixtures to control the light specifically. But as with all MEP and security system infrastructure, the lighting design had to be worked into the structural concrete. Again, the team relied on the problemsolving powers of BIM to help fish the lighting conduit and boxes into the complex, rebar-laden walls, and elevated slabs to meet the exact specifications needed.
Protecting surfaces. Because all structural concrete for the project had to be poured early but is also the finished product, the team had to find ways to protect it as the rest of construction continued. This protection plan included wetcuring the floors, which the team tested first with a mock-up. “We used a curing compound on half of the mock-up floor and wet-cured the other half with a lawn sprinkler,” Klinger says. “The team preferred the wet so that process had to be carefully staged to allow for seven full days of wet curing in each area.”
Needless to say, this one-of-a-kind artistic sanctuary will be an art piece of its own once completed. And the LF Driscoll team is excited to be part of the process.
Complexity is what we do best,” says Garrett. “We are here to figure out how to build this completely unique structure and help the City of Philadelphia add yet another world-class cultural center to its already impressive roster. We’re excited for the challenge. It’s what we do.