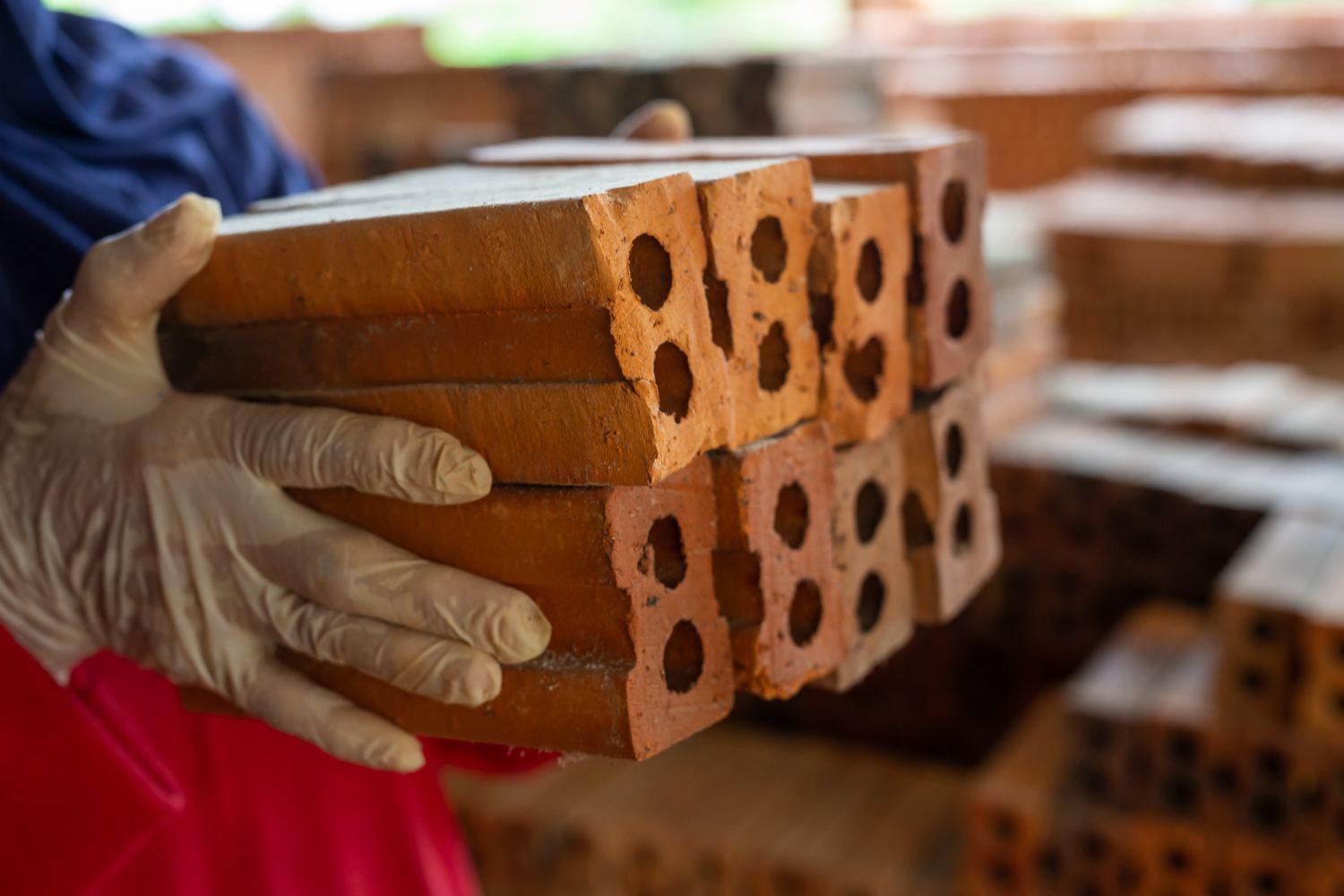
2 minute read
PURPOSE OF REFRACTORY MATERIALS
FOR CHEMICAL INDUSTRY:
Refractory material plays a major role in the chemical manufacturing industry.The chemical company has heavily relied on high-temperature equipment like refractory materials for many of its big operations. In addition, such machines are exposed to harsh materials and excessive temperatures. In order to reduce the damage and effective running process, the chemical plant demands refractory materials. The use of refractories is essential for minimizing the negative effect and improving performance resulting in a long life span.Although refractory materials help chemical manufacturing industries reduce carbon footprint and save energy costs.
Advertisement
HIGH-TEMPERATURE REFRACTORYMATERIALS FOR CHEMICALINDUSTRY:
There are different types of refractory materials available in the market suitable for various industries. Here we have listed out the best refractory materials for the chemical industry that make chemical manufacturer tasks easier.
Boiler
Boiler refractory is one type of high-temperature equipment that is designed to line the boiler and prevent heat retention. Refractory boilers are composed of a wide range of materials like bricks, tiling, castables and other mixtures.Achemical manufacturing process uses an industrial boiler to produce heat and power, which reduces the retaining heat when the boiler is not in use.
Kilns
Arefractory kiln can gather out all heating elements with an insulated shell to practice tasks like quick-drying, improving strengths, and generating chemical actions and reactions. However in some scenarios, these high operating temperatures are prone to damage the kiln, hence refractory is used in the chemical industry
Furnace
There are different types of furnaces available in the chemical manufacturing industry, and a good quality furnace can withstand high temperatures. Furnaces are widely spread in the chemical industry and such refractory materials offer great insulation and protection against excessive heat and chemical attacks.
Incinerators
Incinerators can prolong the equipment’s life and ease maintenance requirements. Incinerators are additionally subjected to intense operation and high temperatures. Therefore, efficient heat transfers are necessary for combustion chambers and rotary furnaces.The right incinerator refractory could solve this by protecting against harsh conditions.
Castables
Refractory castables are majorly used for chemical kiln systems due to their convenience and flexible features. Further, it is one of the common refractory materials for the chemical industry. Whether it’s about fixing the complex structure of the chemical kiln preheater system or other factory systems. Low refractory castables will never fail to meet chemical manufacturing industry demands.
Refractoryfirebricks
Fire Brick is another name for refractory bricks. Fire bricks are made using the same dry-press, tough, smooth casting, and hot-pressing processes as building bricks. Fire brick is capable of withstanding high temperatures without melting or fusing. Fire bricks are commonly made from silicon dioxide and aluminium oxide. In order to improve the efficiency of chemical implants, select the best manufacturer of refractory material and get standard-quality refractory firebricks
Silicarefractory
In the chemical manufacturing industry, silica bricks come in various forms.
At least 93% of the SiO2 in silica brick makes it a refractory material. Silica brick is very strong mechanically at temperatures close to its actual fusing point. The behaviour of this material contrasts with that of several other refractories, such as aluminium silicates, which start to fuse and creep at much lower temperatures than their fusion points.