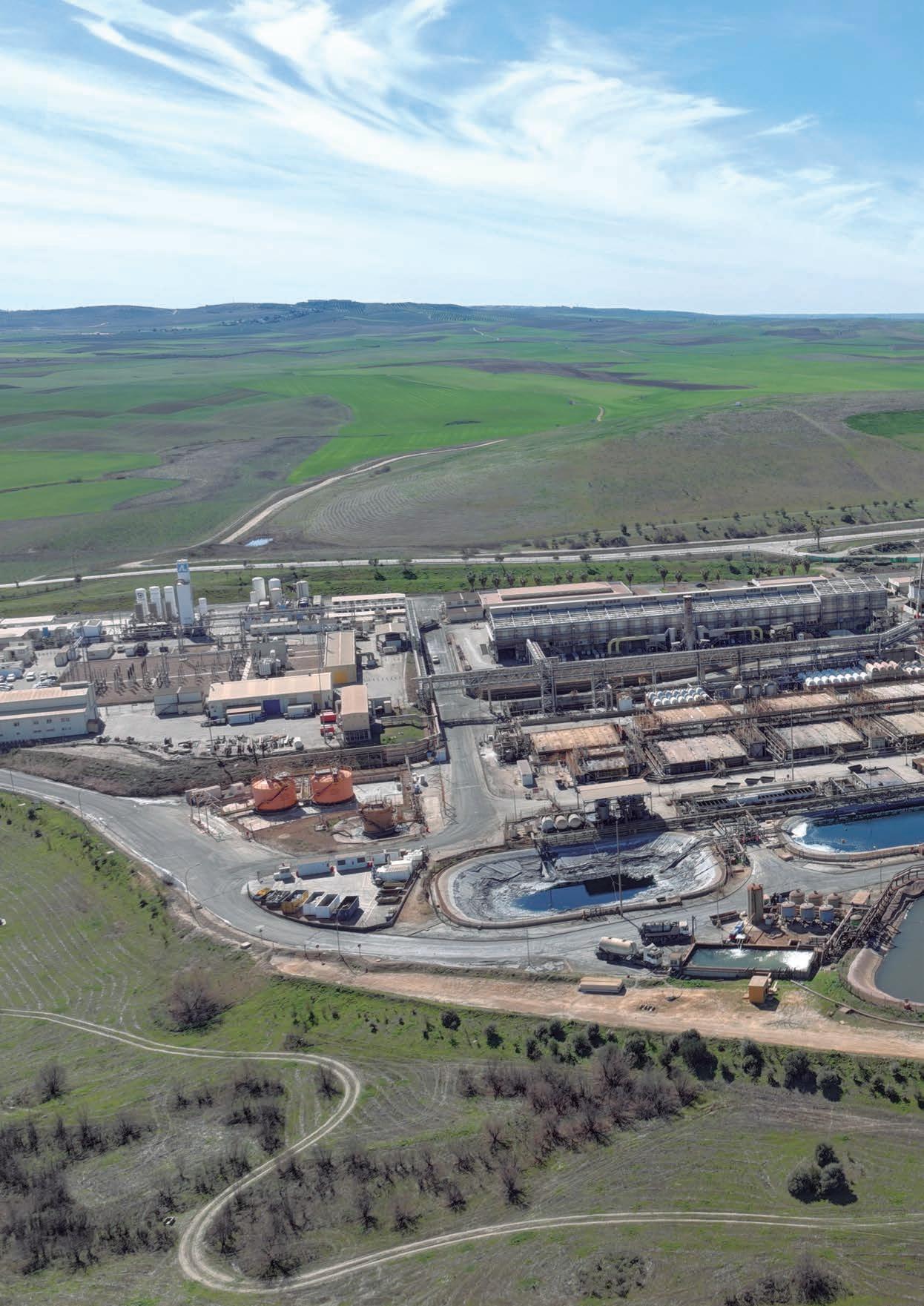
19 minute read
LA PLANTA DE TRATAMIENTO DE COLAS DE COBRE LAS CRUCES
La explotación minera de Cobre Las Cruces, perteneciente a la compañía multinacional canadiense First Quantum Minerals, comenzó su actividad extractora de cobre en Gerena, Sevilla, en 2009, beneficiando sulfuros secundarios con alta ley de cobre hasta el año 2020, que se agotaron las reservas que podían extraerse mediante minería a cielo abierto. Por otro lado, Cobre Las Cruces proyecta en sus instalaciones actuales, y mediante minería subterránea, extraer y procesar mineral polimetálico para producir metal refinado de cobre, zinc, plomo y plata, estratégicos para la industria y la transición energética, un proyecto en un estadio avanzado que, una vez entre en operación, prevé generar 2.400 puestos de trabajo, entre directos, indirectos e inducidos, y una inversión de 677 millones de euros.
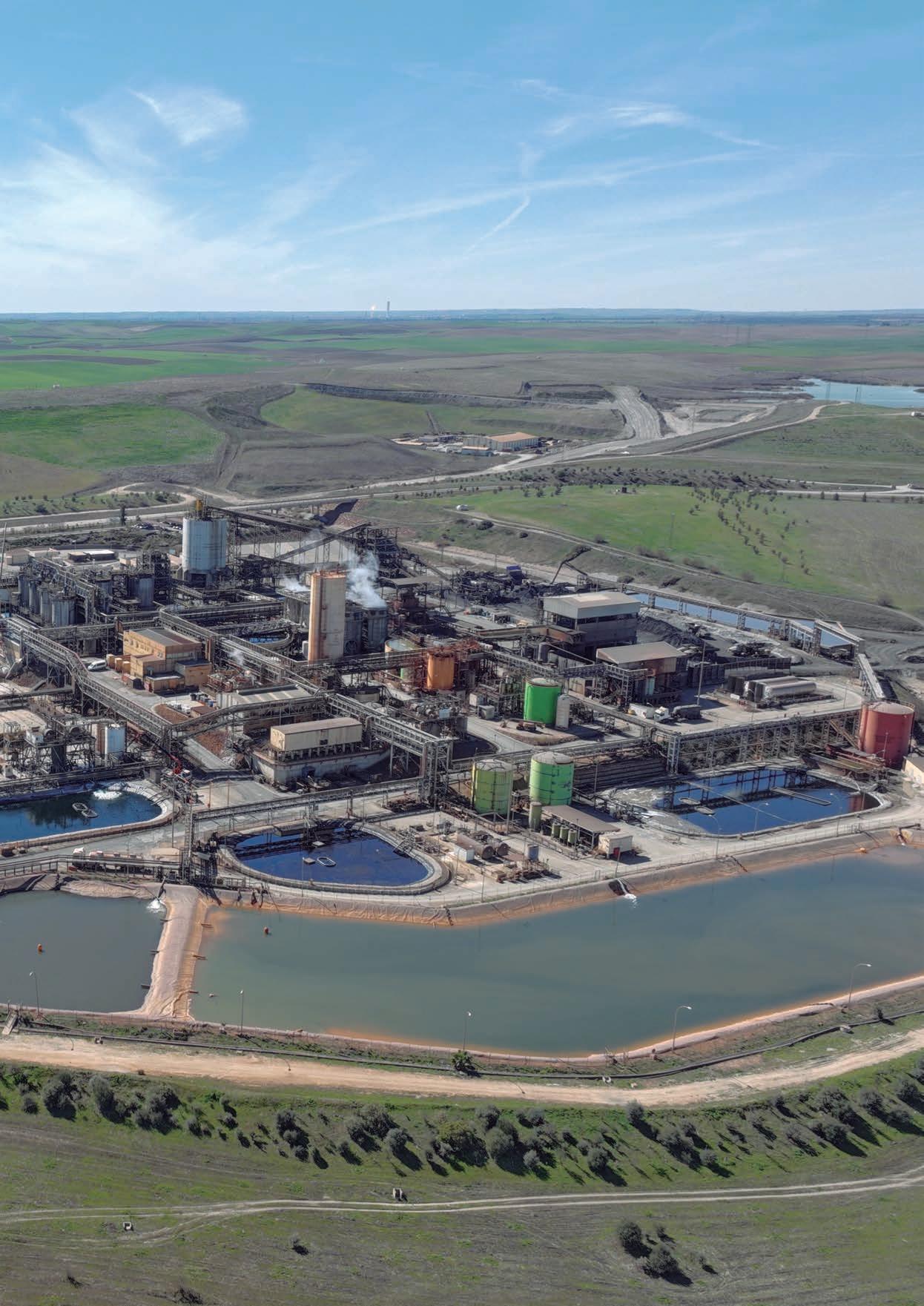
Advertisement
Sin embargo, Cobre Las Cruces no se ha quedado sin actividad entre sus operaciones a cielo abierto y su futuro inminente mediante minería de interior. Las colas, también conocidas como estériles de tratamiento, o tailings en idioma anglosajón, están siendo el puente entre el mineral secundario de cobre extraído a cielo abierto y el mineral polimetálico (cobre, plomo, cinc y plata) que se extraerá a futuro mediante minería subterránea.
Cuando la actividad minera y metalúrgica comenzó en el año 2009, la planta de tratamiento fue ajustándose hasta el año 2012, que alcanzó sus valores nominales. Por aquel entonces, el mineral que se procesaba contaba con leyes muy elevadas y,
El proyecto Tailings, como se ha bautizado al reprocesamiento de las colas ricas en cobre en CLC, comenzó a desarrollarse en 2019 y su operación en planta dos años más tarde, periodo en el cual se realizó una batería de trabajos orientada a examinar y evaluar su viabilidad técnica y económica, que concluyeron con el arranque del proyecto en 2021 por lo tanto, los residuos lixiviados generados fueron almacenados en un depósito de estériles, contando con un alto volumen de cobre. Se trata, por lo tanto, de un material rico en cobre que hace viable su reprocesamiento actual en planta para la obtención de mineral de calidad.
El proyecto Tailings, como se ha bautizado al reprocesamiento de las colas ricas en cobre en CLC, comenzó a desarrollarse en 2019 y su operación en planta dos años más tarde, periodo en el cual se realizó una batería de trabajos orientada a examinar y evaluar su viabilidad técnica y económica, que concluyeron con el arranque del proyecto en 2021.
Extracci N De Las Colas
Las colas generadas desde el año 2009 al 2020 se fueron almacenando en un área específica en superficie, la instalación de estériles de tratamiento, diseñada buscando una geometría que ayudara a minimizar el impacto paisajístico de la zona. Los estériles filtrados en la planta de proceso se fueron depositando progresivamente, cubriéndose con margas y sustrato vegetal, que garantizará su sellado y revegetación posterior.
En el proyecto Tailings, lo primero que se hizo fue un estudio de la cantidad de cobre que contenían las diferentes fases, acreditándose que la primera fase era la más rica e iba descendiendo en las fases sucesivas, algo totalmente lógico si se tiene en cuentan que la planta hidrometalúrgica fue ajustándose en el tiempo hasta alcanzar su valor nominal.


A partir de ahí se hizo un estudio de viabilidad, donde se planteó la extracción de entre 2,7 y 3 millones de toneladas de estériles de tratamiento cupríferos con un contenido medio del 1 % en Cu, por medios mineros convencionales, y su envío a planta, para, una vez acondicionados, ser procesados en la misma línea de Cu, adaptando el proceso para tratar este material. “Se creó un modelo para trabajar en las tres
EL NUEVO PROYECTO DE LAS CRUCES: UNA MINA, CUATRO METALES
Cobre Las Cruces proyecta en la provincia de Sevilla la construcción de una nueva mina subterránea y una refinería polimetalúrgica, la primera de sus características en el mundo, que supondrá una inversión de 500 millones de euros (además de otros 177 millones en instalaciones de energía renovable) y generará 2.400 empleos entre directos, indirectos e inducidos, durante un periodo de al menos 18 años.
La actual mina de cobre a cielo abierto se transformará en una explotación subterránea, lo que supondrá una operación con menor impacto visual. Se extraerá mineral polimetálico, que se transportará mediante un sistema eléctrico a la superficie y se tratará en una nueva planta industrial para convertirlo en metal puro de cobre, zinc, plomo y plata, metales estratégicos para la industria europea, la transición energética y la economía digital.
Se trata de una tecnología única en el sector minero, desarrollada y patentada internacionalmente por CLC, conocida como PMR (polymetallurgical refinery), que permite completar todo el proceso ‘de la mina al metal’ en las mismas instalaciones, de forma más eficiente y sostenible.
El proyecto PMR incorpora la última tecnología en metalurgia, así como las mejores técnicas en materia ambiental: uso sostenible del agua, rresiduos mineros espesados, filtrados y encapsulados (en CLC no hay balsas de lodos), un 90% de reducción de la huella de carbono (gracias al procesamiento del mineral in situ, sin necesidad de transportarlo a una fundición), suministro eléctrico y térmico mediante energías renovables, así como la rehabilitación ambiental progresiva de todos los espacios afectados por la operación minera.
La nueva planta tendrá el potencial de procesar mineral procedente de otras explotaciones mineras andaluzas, una capacidad que permitiría ampliar sustancialmente el horizonte del nuevo proyecto, tanto en producción como en años de operación.
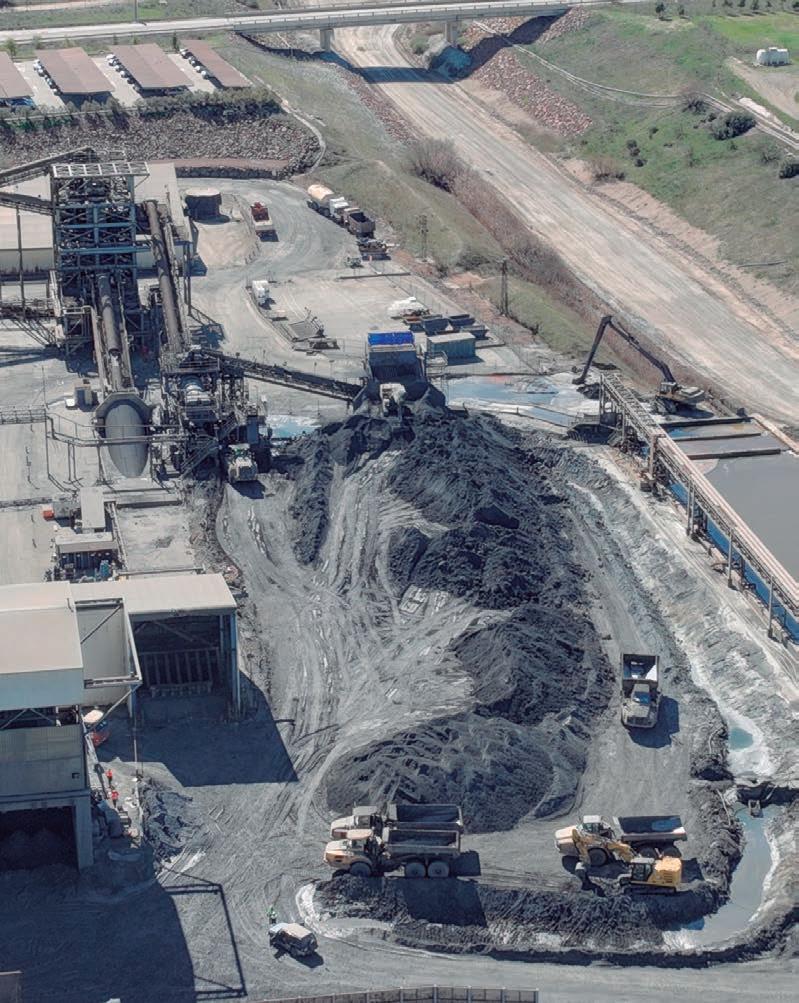
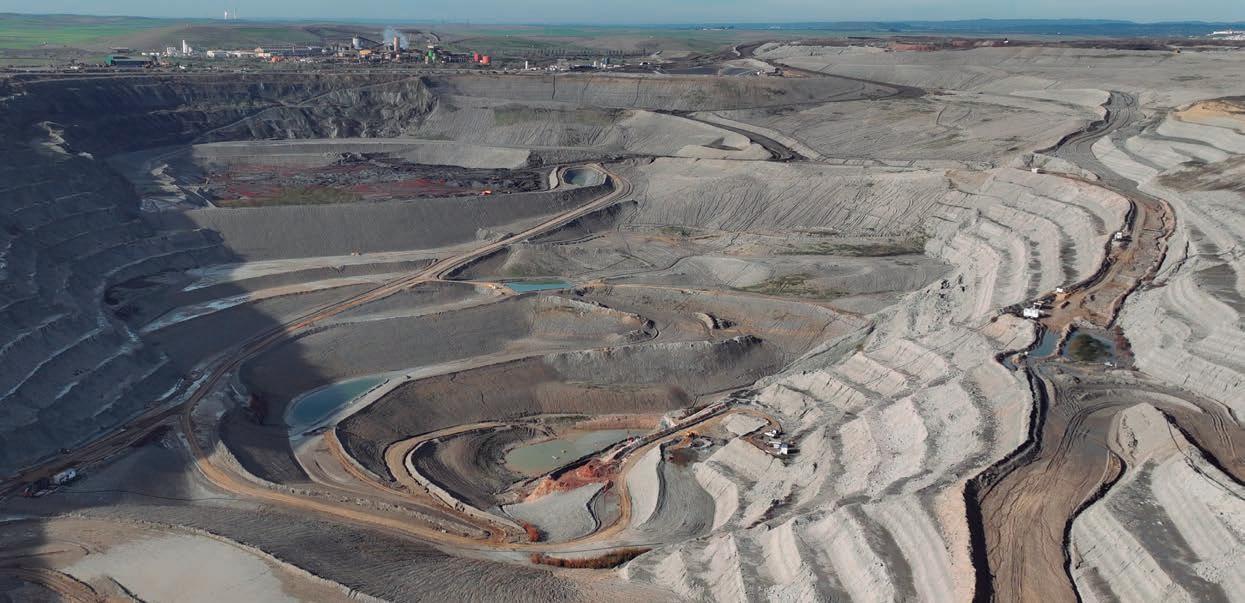
En estos momentos, el proyecto cuenta ya con todos los permisos de la Junta de Andalucía, así como los correspondientes a la Confederación de Guadalquivir (CHG), tanto mineros como ambientales, que acreditan que cumple los parámetros más exigentes en cuanto a seguridad, excelencia operacional y gestión responsable del entorno natural.
Una vez se inicie la construcción de las nuevas instalaciones, se prevé generar 1.200 nuevos puestos de trabajo directos. En la fase de operación, serán 900 empleos directos y 1.500 indirectos e inducidos.
fases, buscando siempre conocer la ley de material extraído y así alimentar de forma homogénea a la planta de tratamiento de colas”, explica Juan Manuel Escobar, jefe de geología en Cobre Las Cruces.
Una vez obtenida la autorización pertinente para esta actividad, y durante el año 2020, se realizó el desmonte inicial de la cobertera de marga existente encima de estos estériles, con un volumen estimado de unos 900.000 m3, dejando expuesto el material a procesar. Así, una vez que se terminó con el tratamiento de los minerales secundarios procedentes de la corta minera, se continuó con la obtención de cobre a partir de las colas, consiguiendo de esta forma una continuidad en la producción.
Tratamiento De Tailings
Si en algo se diferencia el proceso de tratamiento del material procedente del frente de corta a los estériles de tratamiento es que estos últimos no necesitan procesos de conminución. La trituración y molienda desaparecen, al tratarse de unos productos de desecho ya procesados que vuelven a la etapa metalúrgica para la extracción del cobre residual.
El proceso desarrollado y utilizado por CLC para el tratamiento del todo-uno procedente de la corta tras la voladura, con tamaños entre 0 y 500 mm, comprendía diferentes etapas de reducción (trituración y molienda) hasta conseguir un tamaño concreto para poder alimentar a las etapas posteriores del proceso, las cuales se llevan a cabo con pulpas, es decir, con una mezcla de líquido y sólidos muy finos, con dimensión menores a las 120 micras aproximadamente. El proceso finalizaba con la filtración del material sin cobre económicamente susceptible de ser extraída para ser finalmente enviada a un depósito de estériles de planta en seco. Este material tratado por este método constituye la materia prima para el proyecto Tailings, es decir, los estériles de tratamiento que ahora se están reprocesando para la extracción del cobre.
El proyecto Tailings desarrollado por CLC para el retratamiento de los estériles de planta permite el manejo de materiales muy finos, que ya han sido triturados, molidos, lixiviados en planta y filtrados, y que han estado almacenados durante mucho tiempo en el depósito de estériles.
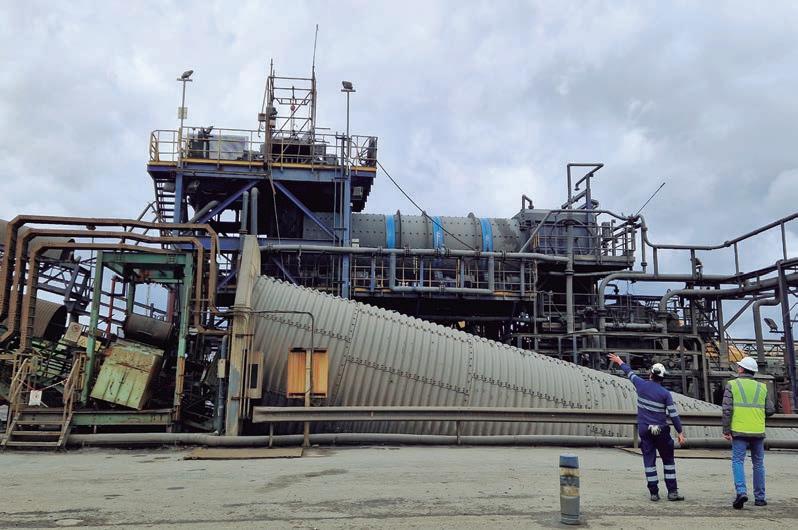
Pese a que, como se ha comentado anteriormente, el proceso para el retratamiento de colas no requiere las etapas de reducción física de tamaño (trituración y molienda), sí es necesario un proceso de limpieza de gruesos y de repulpeo, a fin de eliminar posibles materiales de mayor tamaño que hubieran sido incorporados durante la manipulación de las colas y la preparación de la pulpa necesaria para las etapas siguientes.
Por otra parte, hay que tener en cuenta que el tratamiento de las colas conlleva una reducción en el nivel de producción de cobre fino, por cuanto el contenido de cobre o ley del material se reduce de una ley del 5% de cobre fino con que contaba el mineral originariamente a un 1% aproximadamente de contenido en los tailings, lo cual significa que la producción de cobre catódico, al tratar una tonelada de estériles, es un 20% de lo obtenido con una tonelada de mineral. Es decir, si lo normal es que la planta produjera 70.000 t de cobre al año, con el tratamiento de las colas la producción se reduce a 12.000 t en el mejor de los casos, ya que depende de la ley de cobre de los tailings alimentados.
El cambio de proceso y la calidad del material tratado implicaron una revisión de todos los recursos que se necesitaban en los diferentes aspectos para la gestión de planta, entre los que destacan los equipos, insumos y la organización de la planta.
Flujo De La Planta Del Tratamiento De Colas
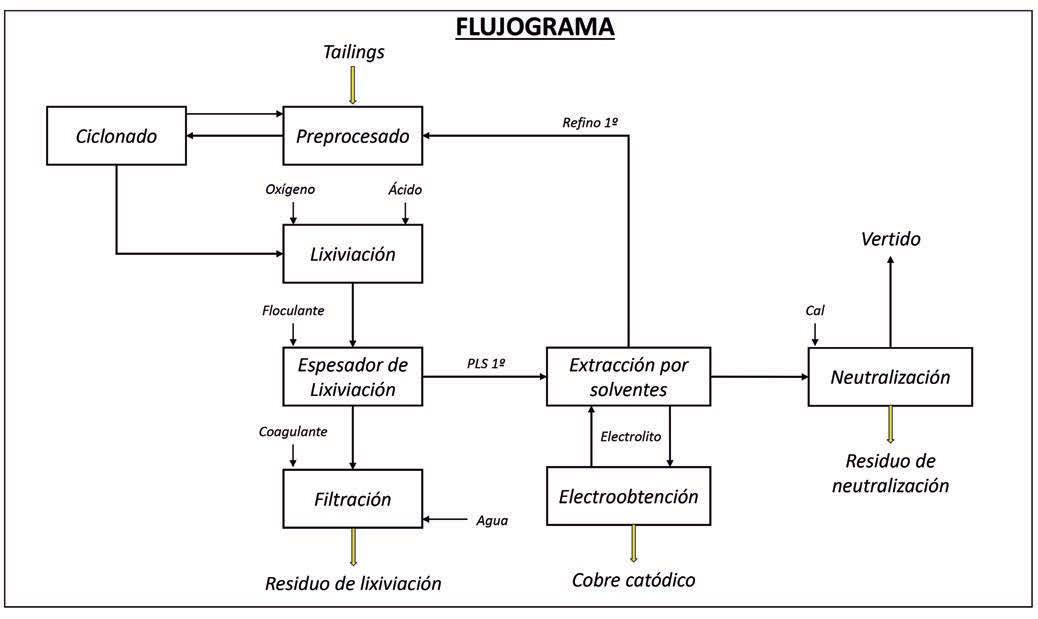
Tal y como se ha comentado anteriormente, el material procedente del estéril de tratamiento, al no necesitar procesos de conminución, comienza con una etapa de disgregación y repulpeo.
El proceso de disgregación es absolutamente necesario si se tiene en cuenta que, debido a su almacenamiento en seco a lo largo de varios años, los tailings pueden estar aglomerados, formando terrones, que es necesario romper y disgregar previamente a la etapa de repulpado. Estos materiales pueden contener sólidos de mayor tamaño, los que también deben ser retirados, para ser finalmente bombeados a las etapas posteriores (reactores de lixiviación) en forma de pulpa.
Para ello, el material de alimentación, en función de su estado, es transportado a unas cribas vibrantes móviles sobre cadenas para su clasificación por tamaños, o si tienen un tamaño más reducido, ser enviado directamente a la planta de tratamiento de colas. El material procedente de ambos procesos termina
Para ello, el material de alimentación, en función de su estado, es transportado a unas cribas vibrantes móviles sobre cadenas para su clasificación por tamaños, o si tienen un tamaño más reducido, ser enviado directamente a la planta de tratamiento de colas. El material procedente de ambos procesos termina acopiado en una zona específica donde una cargadora de ruedas es la responsable de ir cargando dicho material en la tolva que alimenta, mediante un transportador de banda, a un trómel lavador acopiado en una zona específica donde una cargadora de ruedas es la responsable de ir cargando dicho material en la tolva que alimenta, mediante un transportador de banda, a un trómel lavador.
El material se acopia en esta campa en función del porcentaje de cobre con que cuenta, dato que se conoce pormenorizadamente de cada celda de las que se extraen los tailings. La misión de la cargadora, además del suministro a la planta, es ir mezclando los diferentes acopios para intentar obtener en la medida de lo posible un porcentaje medio de un 1% en cobre.
El transportador que sale de la tolva dispone de un sistema de pesaje continuo, para el control de la cantidad de material introducido en el proceso, un detector de metales y un separador magnético, todo ello con idea de eliminar los elementos metálicos previamente a su entrada en el trómel lavador.
Una vez que los talings se encuentran en el trómel lavador, comienza su desplazamiento durante unos minutos en su interior, donde tiene lugar la disgregación del material generado por la energía de impacto como consecuencia del giro del cilindro. Además, en su interior se inyecta refino para la creación de la disolución.
En la parte final del trómel, se encuentra una virola perforada con una luz de paso de 10 mm que corta el material. El pasante va directamente a la zona de rebombeo, donde se envía al tanque de alimentación del proceso de lixiviación, mientras que el rechazo, es decir, el material con tamaños superiores a 10 mm, cae en una criba vibrante, cuya función es la eliminación de las partículas de gran tamaño que puedan suponer atascos en el proceso aguas abajo.
El pasante de la criba se envía igualmente al proceso de lixiviación, mientras que el rechazo se almacena en un troje de hormigón armado y, conjuntamente con los estériles generados en el proceso de la planta, son enviados al depósito de estériles de la corta.
n Ciclonado
Antes de comenzar los procesos de lixiviación, el material procedente del tanque de alimentación a lixiviación pasa por la etapa de ciclonado, un proceso que genera una clasificación del material, donde lo que se busca es separar el tamaño superior a 500 micras, medida que los agitadores de los reactores no son capaces de tratar.

El material en el interior del ciclón se separa generando una fracción inferior a 500 micras que sale por la parte superior, conocida como tobera de rebose o diafragma, en una proporción igual o superior al 95%, que es enviada directamente a lixiviación, mientras que la fracción superior a las 500 micras es evacuada por la parte inferior del ciclón, denominada boquilla, y se envía a una criba, donde se corta de nuevo el material a 500 micras, recuperándose la fracción fina de la misma (ineficiencia del funcionamiento del ciclón), devolviéndola al trómel lavador, mientras que la fracción superior a 500 micras es enviada al stock del área de preprocesado.
n Lixiviación
Tras las diferentes etapas de clasificación, el material con un tamaño igual o inferior a 500 micras pasa a lixiviación, una etapa que comprende los reactores de lixiviación, los espesadores y las torres de enfriamiento.
En esta etapa se disuelve el cobre contenido en el mineral con prensa se encargan de deshidratar el material sin cobre o pobre en pobre precedente del espesador de lixiviación. sulfato férrico en una serie de tanques y reactores conectados en serie en forma de cascada. El ión férrico se regenera continuamente mediante reacción con oxígeno y ácido sulfúrico en la solución, mientras que la reacción de lixiviación también disuelve algo de pirita (FeS2), la cual provee hierro, ácido y calor para la totalidad de la reacción.
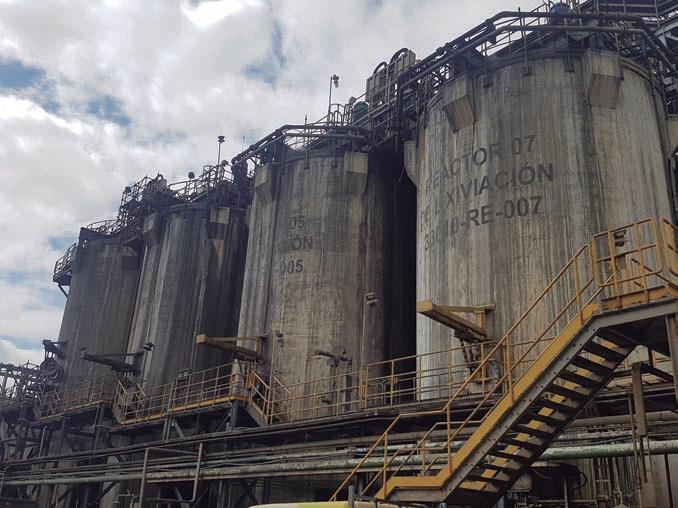
En el interior de alguno de los reactores de lixiviación (dos prereactores de 1.000 m3 cada uno y 8 reactores de 350 m3 cada uno) existe una serie de intercambiadores de calor para usar el propio calor generado durante el proceso de lixiviación (reacciones exotérmicas) en el precalentamiento de las corrientes de alimentación al sistema, ahorrando así consumo de gas natural.
Una vez separado el líquido rico en cobre, la pulpa procedente de los reactores, es decir, el material ya sin cobre, es bombeado a dos torres de refrigeración para reducir su temperatura. A continuación, pasa a una etapa de filtración donde se obtiene un sólido seco (mineral y yeso), que se mezcla con las tortas de neutralización para su depósito en la instalación de estériles de corta en condiciones adecuadas de humedad.
n Extracción con disolventes de cobre (SX)
La solución de lixiviación rica obtenida en la anterior etapa de lixiviación se bombea a los tanques de almacenamiento y de ahí se bombea a la planta de extracción por solventes. El cobre será extraído selectivamente en varias etapas conectadas en serie.
El cobre es transferido desde la solución de lixiviación rica en cobre a la fase orgánica, mientras que el refino, es decir la solución pobre en cobre, es enviada de nuevo al proceso de lixiviación.
La fase orgánica es una solución compuesta por un reactivo extractante en una base de queroseno. El cobre es transferido al extractante desde la solución lixiviada de más baja acidez y liberada de vuelta a la fase acuosa cuando entra en contacto con la solución electrolito de mayor acidez. La solución orgánica cargada se envía a un tanque especialmente diseñado para la fase orgánica cargada, lo que mejora la coalescencia y la recuperación de la fase acuosa que haya sido arrastrada durante el proceso de extracción.

n Neutralización y planta de cal
Las soluciones finales resultantes, principalmente refino secundario de la etapa de extracción por solventes, son tratadas en la etapa de neutralización con lechada de cal en tres reactores aireados para generar compuestos estables y neutralizados que posteriormente son separados del efluente tratado en un espesador (equipo separación sólido-líquido).
En el proceso de colas, no hay cambios en el tratamiento de las aguas finales y la preparación de la lechada de cal, por cuanto el tonelaje anual de material tratado se mantiene.
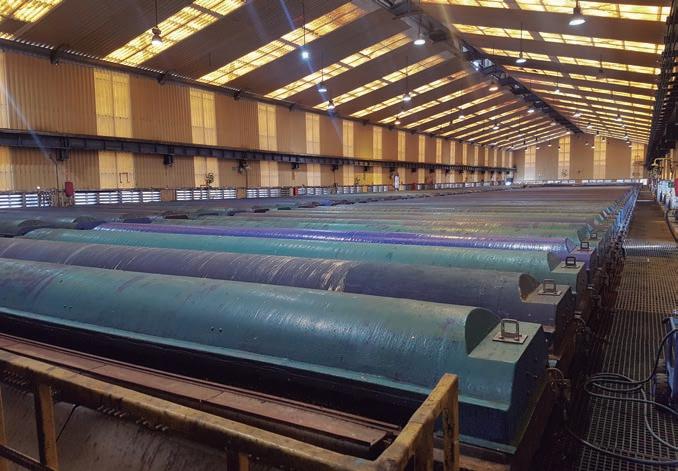
n Electroobtención
El electrolito rico procedente de la etapa de extracción por solventes se bombea a una serie de celdas electrolíticas, dosificando una serie de aditivos específicos para suavizar la superficie del cátodo y proteger la superficie del ánodo.
Con la aplicación de corriente continua en las celdas electrolíticas el cobre disuelto en solución se reduce a cobre metálico en las placas catódicas, mientras que el agua se descompone en iones hidrógeno y
Con este proceso de tratamiento de colas, Cobre Las Cruces ha sabido seguir obteniendo cobre mientras se tramitaban todos los permisos para su nuevo proyecto minero y metalúrgico, por el que operará una nueva mina subterránea y una refinería polimetalúrgica de cobre, zinc, plomo y plata oxígeno en los ánodos. Por ello, el contenido de ácido sulfúrico se incrementa en esta solución resultante y se libera oxígeno. El electrolito pobre de las celdas se retorna al tanque de circulación y de ahí a la etapa de extracción por solventes para comenzar de nuevo el ciclo.
El cobre es separado de los cátodos mediante una máquina lavadora y despegadora de cátodos. Las láminas de cobre son apiladas formando paquetes que son pesados y flejados, almacenándose en el patio de cátodos para su posterior expedición. Las placas madres de los cátodos son retornadas a las celdas electrolíticas.
La neblina de ácido generada por el oxígeno liberado se captura mediante campanas móviles dispuestas sobre cada una de las celdas enviándose a un sistema de lavado de gases (scrubbers) mediante tiro forzado de extracción.
n Filtración de estériles
En el proceso de tratamiento de colas, el estéril o el material sin cobre o con una proporción muy baja se envía a la etapa de filtrado, donde una batería de filtros prensa deshidratan el residuo de lixiviación, que es enviado a la instalación de estériles de corta.
La necesidad de operación en estos filtros es similar al proceso original por cuanto la cantidad total de material tratado, alrededor de 1,3 a 1,5 millones de toneladas, se mantiene.
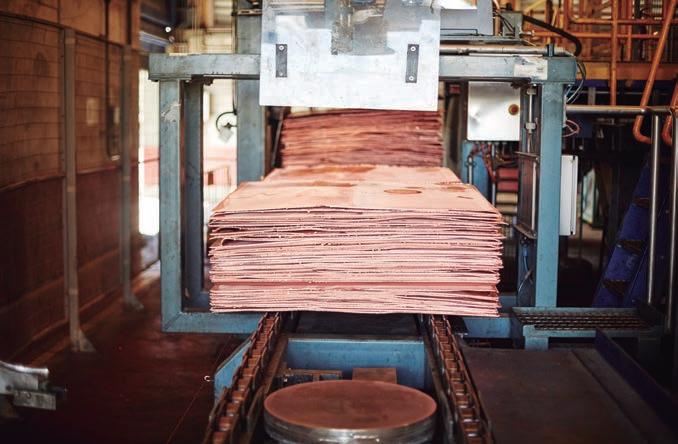
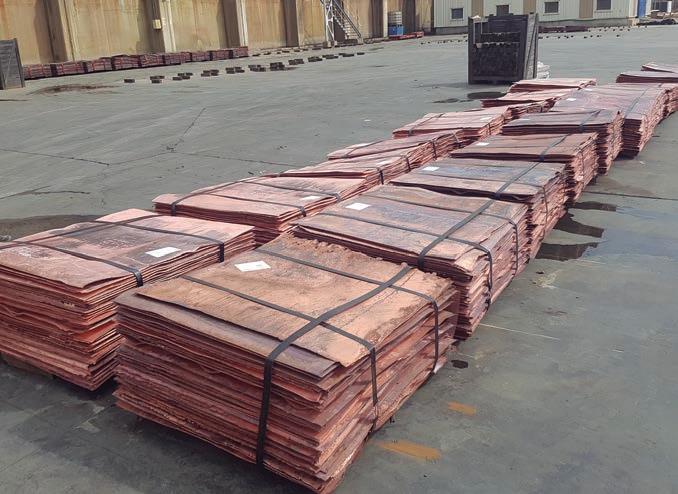
Con este proceso de tratamiento de colas, Cobre Las Cruces ha sabido seguir obteniendo cobre mientras se tramitaban todos los permisos para su nuevo proyecto minero y metalúrgico, por el que operará una nueva mina subterránea y una refinería polimetalúrgica de cobre, zinc, plomo y plata. La producción de cobre procedente de las colas en 2021 fue de 13.600 toneladas anuales, cifra que en 2022 se aproximó a las 10.000 toneladas, siendo enviada toda la producción a la provincia de Córdoba a una fundición de cobre.
Agradecimientos
Quisiera agradecer a Luis Vega, director de mina, las gestiones pertinentes para poder visitar la mina y realizar este artículo, así como la visita VIP que tuvo el gusto de ofrecerme por toda la explotación minera. A Miguel Ángel Muñoz, jefe de control de procesos, por su explicación y visita a la planta; a Ángela Cañal, responsable de relaciones públicas, por su acompañamiento y las gestiones pertinentes para la obtención de toda la información; a Juan Manuel Escobar, jefe de geología, por su explicación del modelo de gestión de los tailings; y a Pedro Soler, director general de Cobre Las Cruces, por autorizar la visita. Muchas gracias a todos.
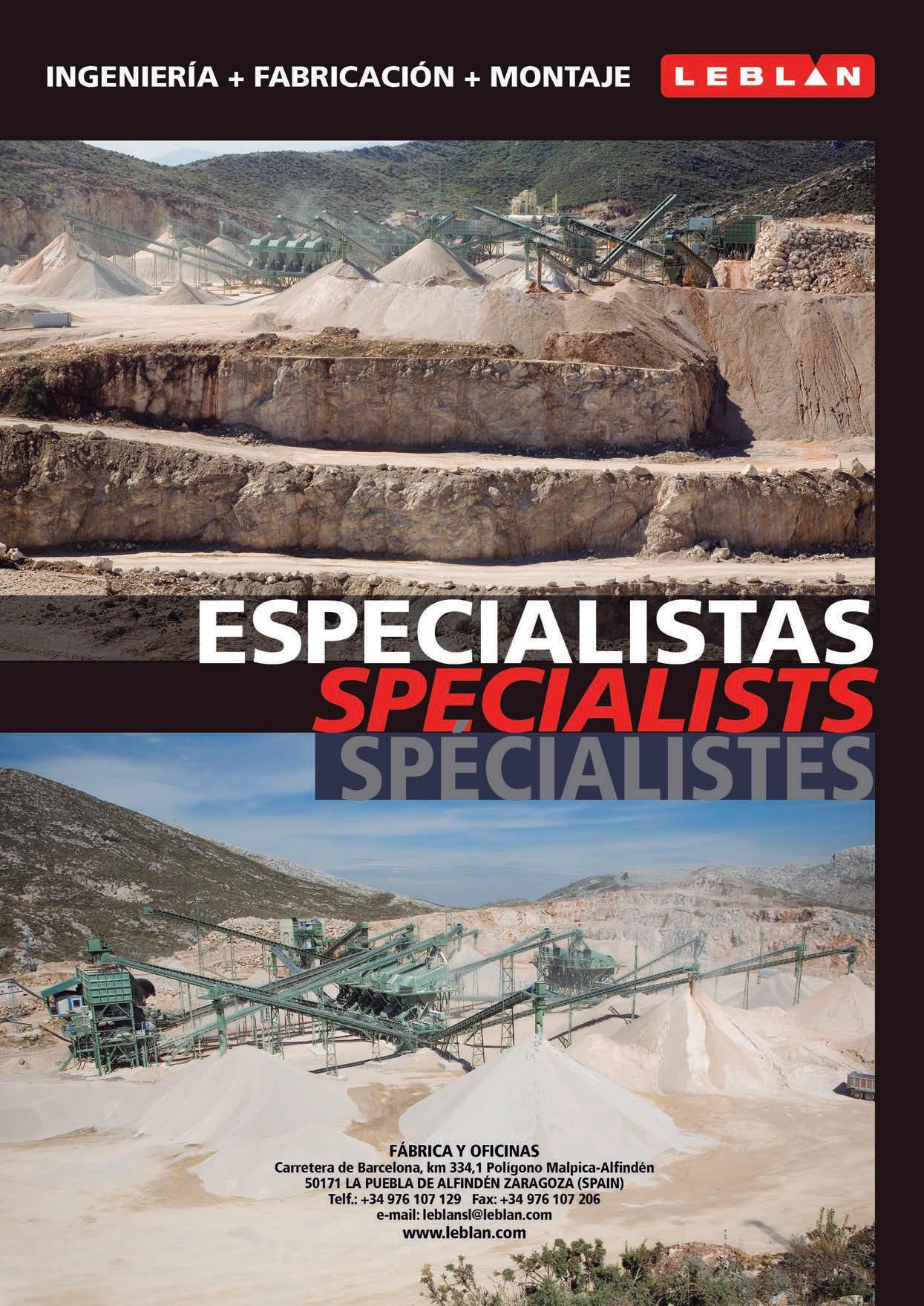
Quien piense en Implaser como una simple empresa fabricante de pegatinas para maquinaria está muy lejos de la realidad. Implaser 99, S.L.L. es mucho más que eso, es una compañía dedicada a la señalización luminiscente y de seguridad, al diseño y fabricación de pegatinas técnicas para entornos industriales, y a la investigación y desarrollo de soluciones de accesibilidad, todo ello basado en tres pilares fundamentales como son la confianza, el compromiso y la innovación.

IMPLASER, LÍDER EN SEÑALÉTICA, ACCESIBILIDAD Y PEGATINAS
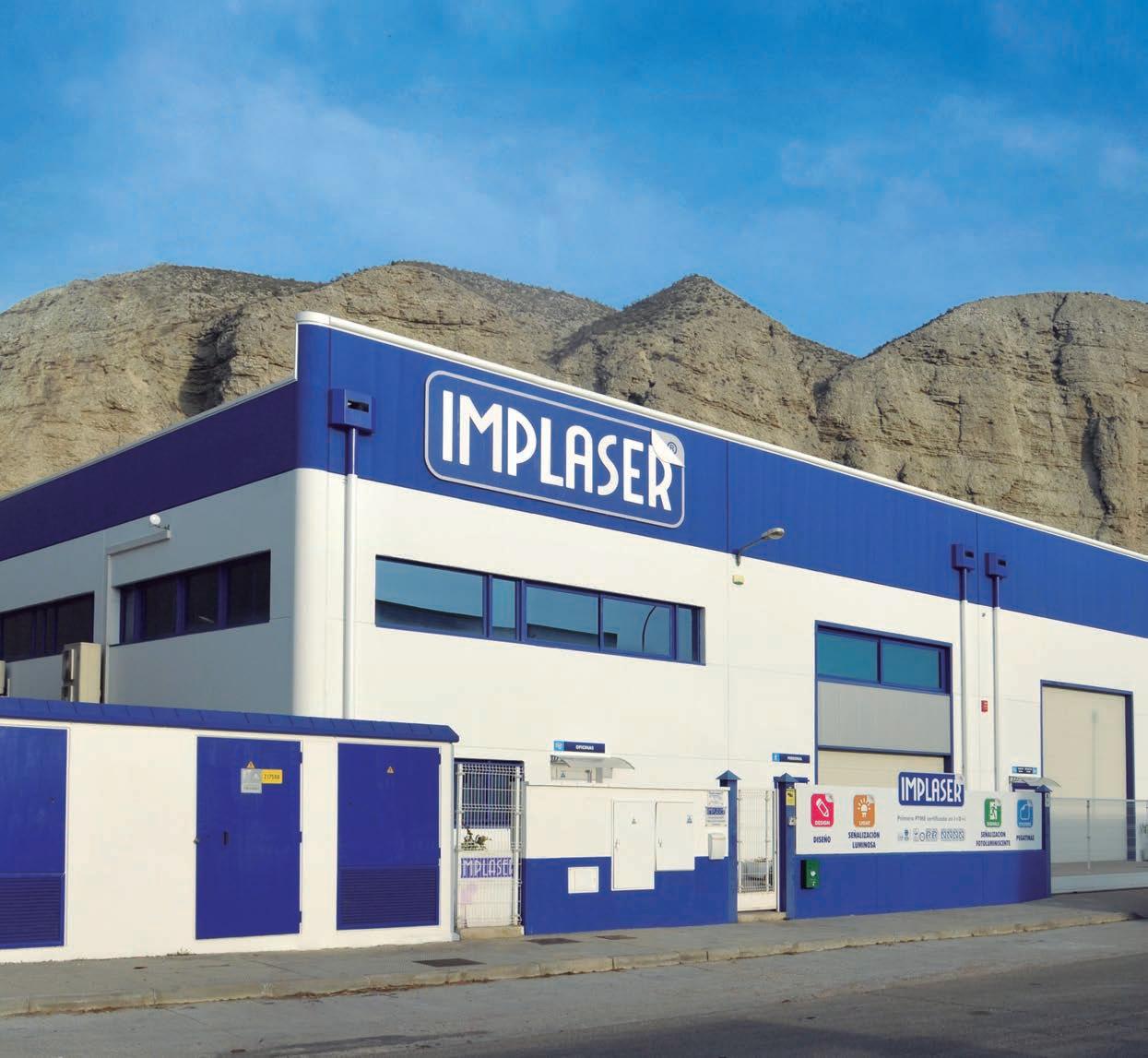
En el polígono industrial Borao Norte, en el término municipal de Alfajarín, en la provincia de Zaragoza, en las estribaciones del desierto de Los Monegros, se encuentra ubicada la mayor empresa española de señalética, pegatinas técnicas y accesibilidad. Implaser, conocida en el sector de la maquinaria por ser el mayor proveedor de pegatinas, es una empresa con más de 38.000 referencias, que provee más de 12.000 pedidos al año a 25 países diferentes y cuenta con una facturación anual que se acerca a los 8 millones de euros.

Sus orígenes se remontan al año 1999 cuando cuatro socios con mucha visión de futuro crearon una empresa basada en el compromiso con las personas, la apuesta por la sostenibilidad, el desarrollo I+D+i, el fomento de la solidaridad y la generación de alianzas. 24 años más tarde esta compañía cuenta con un conjunto de tres naves que suman 4.000 m2, 7 líneas de producción con equipos de última generación, 80 empleados entre los que se encuentran ingenieros, doctores y arquitectos, y un compromiso por la innovación y por la calidad que le ha llevado a ser la primera PYME certificada por AENOR en I+D+i en España. En definitiva, se trata de una empresa líder en la fabricación de señalización luminiscente, soluciones de accesibilidad y pegatinas técnicas.
Esta compañía tan avanzada técnicamente tiene como objetivo conectar personas y entornos, creando espacios más seguros, integradores y ha- bitables por todos. Además, revierte a la sociedad parte de sus beneficios empresariales, apostando por el cumplimento de los Objetivos de Desarrollo Sostenible de la Agenda 2030 de las Naciones Unidas, con políticas implementadas que abarcan la mayoría de todos ellos.
Para ello, Implaser comienza buscando el bienestar de sus trabajadores y su seguridad. La plantilla de 80 trabajadores está formada por un 75% de mujeres y un 25% de hombres, contando actualmente con 19 horarios diferentes que buscan la conciliación familiar. Además, la empresa reparte entre sus empleados el 10% de los beneficios anuales, y cuenta con un gimnasio en sus instalaciones y con varios puntos de descanso. En definitiva, se trata de una empresa que busca el máximo compromiso con sus trabajadores, algo muy similar a lo que ocurre con sus clientes.
Pero, ¿tan necesario es el sector de la accesibilidad y las pegatinas técnicas? Si se analiza la cantidad de pegatinas que lleva una excavadora o cualquier equipo industrial, no hay más que pensar en el consumo, por ejemplo, que tienen las empresas de alquiler, que buscan llevar siempre sus equipos perfectamente señalizados garantizando la seguridad de los operarios. A partir de ahí, la señalización en las oficinas respecto a los extintores, zonas de salida, áreas de emergencia, etc., y algo a mayor escala en las estaciones de metro, autobuses, edificios públicos, restaurantes, etc., permite conocer la importancia de la señalética para la seguridad.
Para ello, Implaser comienza buscando el bienestar de sus trabajadores y su seguridad. La plantilla de 80 trabajadores está formada por un 75% de mujeres y un 25% de hombres, contando actualmente con 19 horarios diferentes que buscan la conciliación familiar. Además, la empresa reparte entre sus empleados el 10% de los beneficios anuales, y cuenta con un gimnasio en sus instalaciones y con varios puntos de descanso
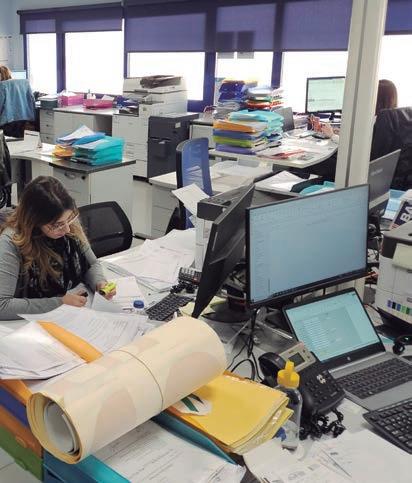
Implaser es líder nacional en la fabricación de pegatinas técnicas así como de productos accesibles para lugares de pública concurrencia y sistemas inteligentes para la seguridad y trazabilidad de personas y activos en entornos públicos e industriales.
Proceso De Producci N
Si se tiene en cuenta que Implaser a nivel nacional provee a empresas como El Corte Inglés, Mercadona, Sánchez Romero, Mercedes Benz, Adidas, Caterpillar, Ausa, Atlas Copco, Securitas, Nissan o Mitsubishi, entre otras muchas, el proceso de producción debe cumplir con unos estándares de calidad muy ele- vados. Implaser acaba de realizar toda la señalética en cinco estaciones ferroviarias de Emiratos Árabes Unidos, se encuentra certificada por ADIF para todas las estaciones españolas, y es proveedora de señalética para la IMO, la Organización Marítima Internacional, de ahí que el exhaustivo control de la calidad, de la fabricación, de la materia prima y del producto final en laboratorios propios sea un aspecto de primer nivel en la compañía. Actualmente Implaser cuenta con certificado AENOR de gestión de calidad ISO 9001 y el certificado AENOR de gestión I+D+i ISO 166002.
El proceso de fabricación comienza con un estudio pormenorizado de las materias primas y elementos necesarios para la fabricación. Para ello cuenta con un laboratorio muy completo con los últimos equipos y procesos, así como personal cualificado, que permite conocer si la calidad suministrada por los proveedores es la exigida por la empresa
El proceso de fabricación comienza con un estudio pormenorizado de las materias primas y elementos necesarios para la fabricación. Para ello cuenta con un laboratorio muy completo con los últimos equipos y procesos, así como personal cualificado, que permite conocer si la calidad suministrada por los proveedores es la exigida por la empresa. Entre todo el proceso de fabricación, lo más llamativo es que Implaser es la única empresa en España que fabrica su propia pintura fotoluminiscente, a través de una mezcla de pigmentos con mineral de aluminato de estroncio procedente en su totalidad de China.
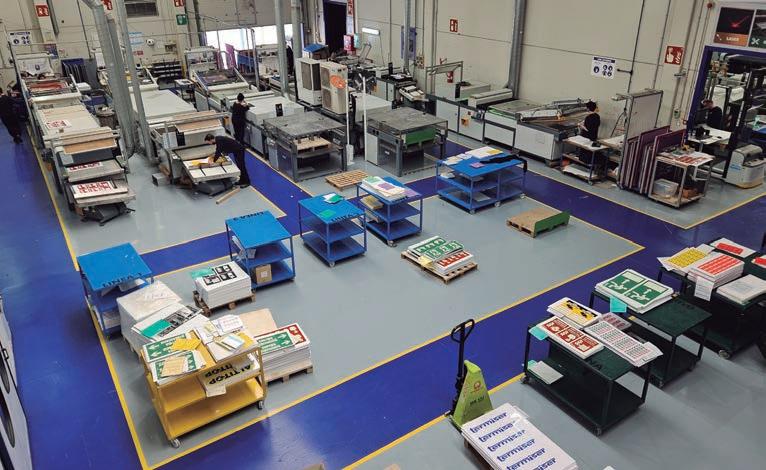
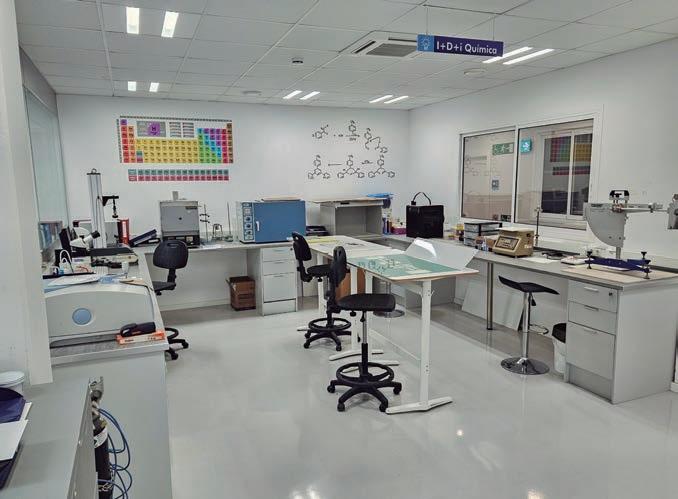
Zona de producto terminado.
Hay que tener en cuenta que Implaser fabrica elementos de accesibilidad y pegatinas en diferentes tipos de soportes, entre los que se encuentran el aluminio, acero, glaspack o PVC de alto agarre, para lo que necesita diversos tipo de maquinaria para garantizar su adhesión a estas superficies.
Por ello, en sus instalaciones dispone de varias líneas de serigrafía e impresión digital que le permiten obtener productos con múltiples acabados, lo que le ha llevado a contar actualmente con casi 40.000 referencias. La zona de serigrafía ocupa 2.500 m2 y la de impresión digital 250 m2, donde maquinaria de última generación trabaja a dos turnos para abastecer a un mercado mundial de 25 países.
Uno de los éxitos de Implaser es su gran stock de material, lo que hace que si el pedido entra antes de las 12:00 h, se entregue en 24 horas. “Al día salen de Implaser entre 3.000 y 5.000 señales solo para España”, matiza José Ignacio Aparicio, director comercial y uno de los cuatro socios fundadores de la empresa.
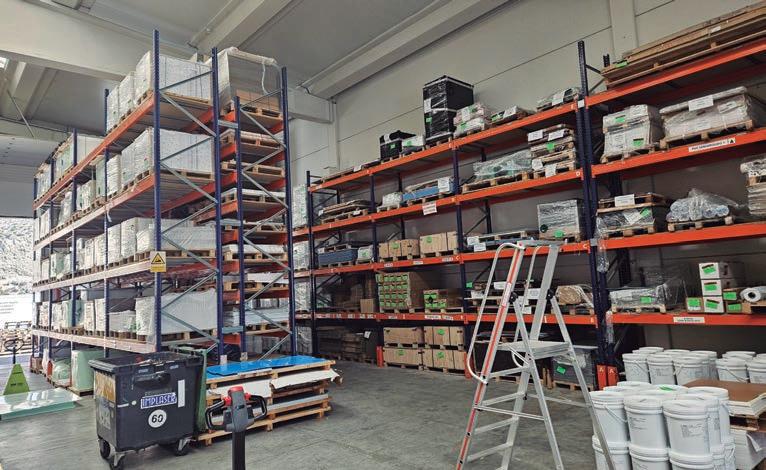
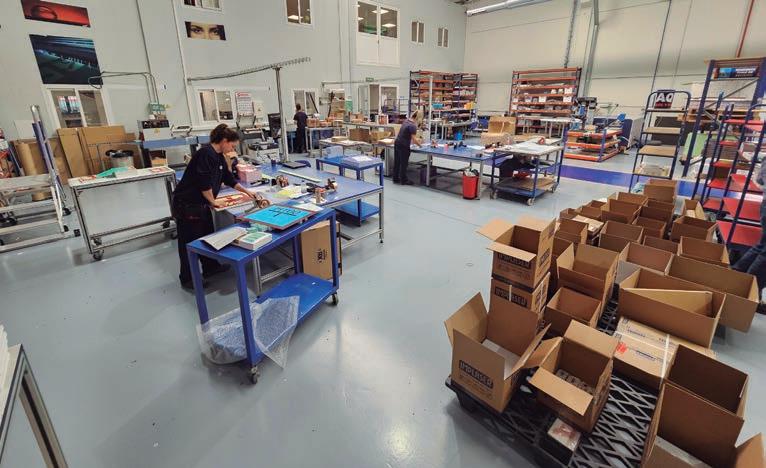
El producto final, antes de su despacho, es también sometido a un riguroso examen de laboratorio para
El producto final, antes de su despacho, es también sometido a un riguroso examen de laboratorio para conocer en todo momento la calidad del elemento terminado. Por ejemplo, a las pegatinas técnicas se le hacen pruebas de adhesión y ensayos de calor para conocer en todo momento su comportamiento conocer en todo momento la calidad del elemento terminado. Por ejemplo, a las pegatinas técnicas se le hacen pruebas de adhesión y ensayos de calor para conocer en todo momento su comportamiento.
Por si no fueran pocos todos los controles de calidad que aplican, todas las pegatinas y señalética de Implaser incorpora un código QR que alberga la información relativa a esa señal. Es la única empresa que lo hace y eso habla muy bien de una empresa donde la calidad existe de principio a fin del proceso de fabricación.
Además de la accesibilidad y señalética, Implaser colabora con empresas importantes de su sector y con Centros Tecnológicos y Universidades a nivel nacional e internacional. Así, ha participado en distintos proyectos de desarrollo tecnológico con financiación propia y externa.
La inversión en todos esos proyectos supera los 61.000.000 de euros, donde Implaser ha participado con 4.000.000 de euros aproximadamente.
En definitiva, Implaser es uno de los grandes fabricantes mundiales de fabricación de señalización luminiscente, soluciones de accesibilidad y pegatinas técnicas, todo basado en el compromiso con la calidad, con el bienestar de sus trabajadores y con las exigencias de sus clientes.