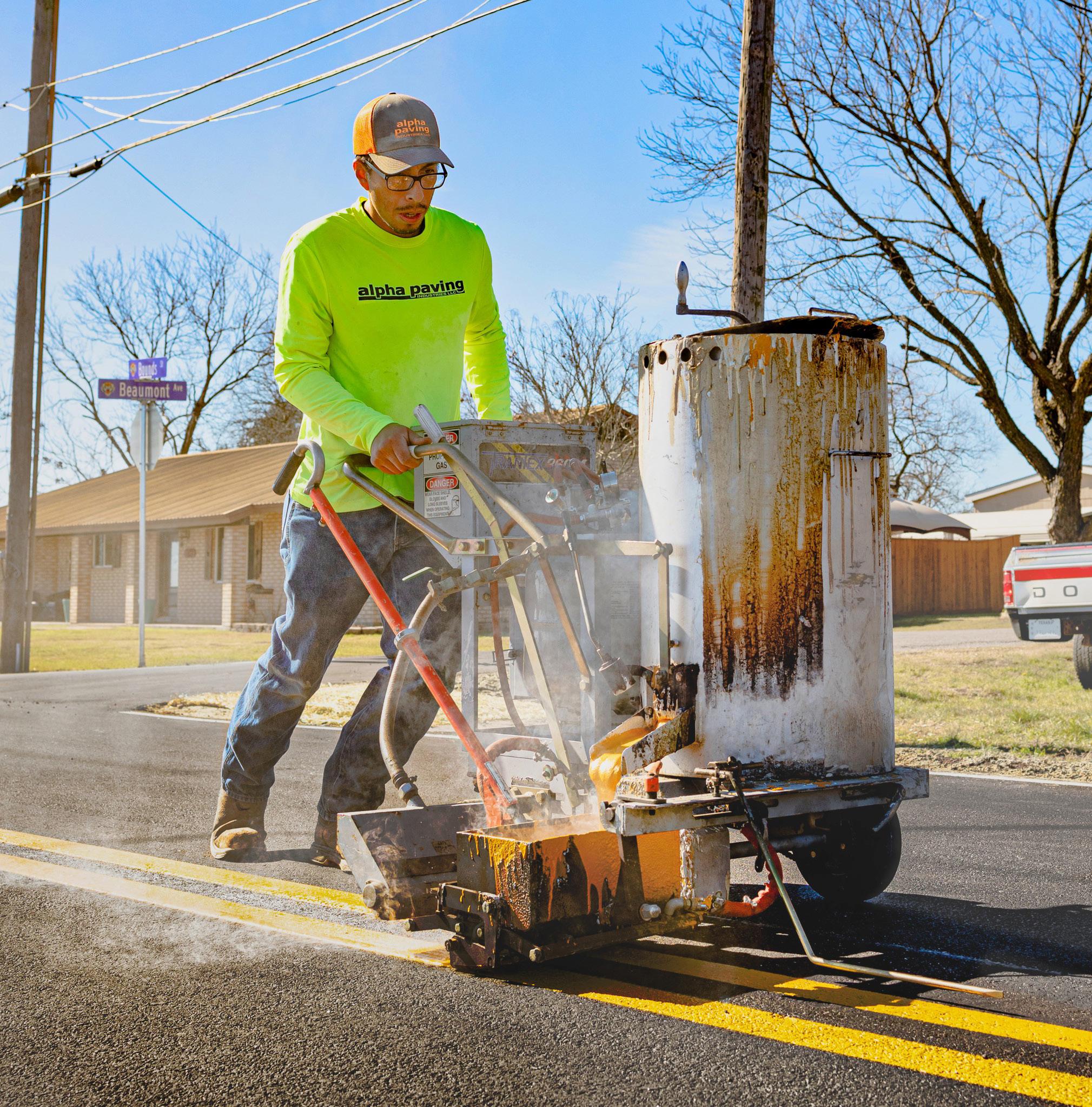
6 minute read
How to Incorporate Thermoplastics Into Your Service Offerings
Thermoplastic pavement markings are used as paint, also known as hot melt marking paint.
Alpha Paving | Facebook
How to Incorporate THERMOPLASTICS
Into Your Service Offerings
Diversifying services to be a resource to customers can be a smart business move for your company
Contractors are diversifying services to become a one-stop shop for their customers, which isn't new, this has been happening for many years. If you are already performing paint striping services on parking lots or municipal work, the natural next step would be to include thermoplastic offerings to reach a broader customer base looking for a more durable, longer-lasting marking.
Thermoplastic markings, when applied to pavement, is a molten material created from melting either plastic granules or a pre-mixed material that is heated, cooled and formed into a block or powder which is then melted before application. The material is heated to 400°F - 425°F before it is applied to the pavement. "It's one of those things that everything has to be lined up correctly," said Josh Ross Schnelting, striping manager for Alpha Paving. "The pavement needs to be at a certain temperature which typically you want to see at 50 degrees and rising. Your material needs to be a certain temperature too, otherwise it comes out and big clumps. It looks like cake batter."
The learning curve with thermoplastic is fairly easy, especially if the contractor is already in the pavement marking segment. The material must reach the proper heat before application. Also, like Schnelting said, contractors should consider the surface temperature of the pavement. Applying thermoplastics at proper application temperature 400°F+ is one of the most critical factors affecting the bond to the pavement. If the road temperature is too cold, the material may fail and not adhere properly.
These lines can be thicker than a paint line, increasing the likelihood of removal by snow plows when the blade comes in contact with the thermoplastic marking, thus thermoplastic tends to be used more in warmer environments. However, there has been advancements to feather the line's leading edge making the technology more attractive in colder climates.
EQUIPMENT Thermoplastic markings require specialized equipment to heat and hold the hot material before being placed on pave-
ment which can be applied by handwork or long line applications.
Walk-behind handliners are small, portable pieces of equipment that hold the molten material and maintain it at the proper temperature long enough to let the operator apply it. Handliners are pushed by the operator and are made of either steel or aluminum. Some manufactures are creating efficiencies like ride-on attachments that can either connect to the handliner or kettle, or have built ride on stripers to help drive productivity.
Walk-behind handliners can weigh between 275 and 300 pounds, manufacturers suggest testing them out before buying. Also, set up a test drive for any long line or ride on stripers to understand what the machines capability.
For contractors doing mostly intersections, parking lots or smaller jobs, a handliner will be the equipment choice. Handliners are preferred for jobs requiring detail work where a larger, long line trucks will not be mobile enough to achieve the desired details.
Pre-melting kettles are essential as well. The kettle is used to heat the thermoplastic material to the required temperature before application. Some trucks or ride on stripers have an integrated pre-melting kettle.
Keep the die system, the container the thermoplastic material flows through to reach the pavement surface, in mind as well. Different sizes of dies are available depending on the mil thickness of the material being applied. Know which size you'll need so you're not purchasing more than necessary or the wrong size.
Just like maintenance on other equipment, thermoplastic machines need
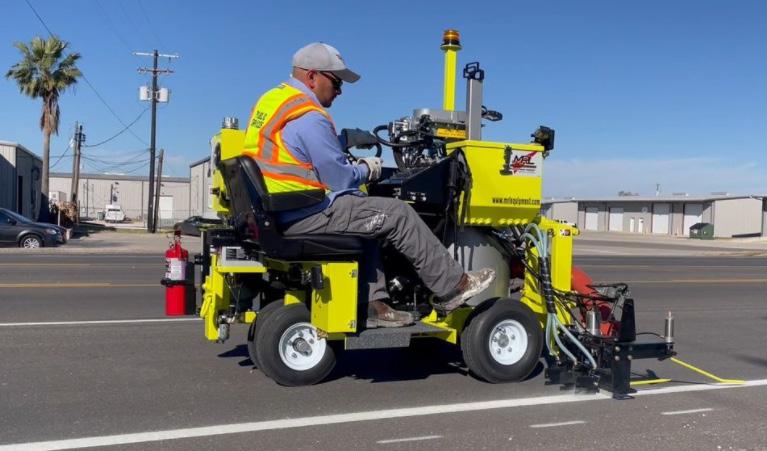
Pavement surfaces must be clean, debris free and dry before application as moisture on the surface can decrease the bonding ability.
MRL Equipment | Instagram
to have scheduled maintenance intervals as well. Draining the kettle daily, remove excesses material from the die and checking the burners should be done on a regular, if not daily basis.
SAFETY FIRST AND FOREMOST Just like any other service, training and safety measures for crew members are important. Especially when working with dangerously hot materials and equipment in thermoplastic applications. • Operators should wear proper clothing; long-sleeve shirts, long pants, hard-soled shoes, hat, heatresistant gloves. When adding or transfering the material to the kettle, a face shield and protective apron will
protect workers from any splash back that may occur. • Keep a fire extinguisher readily available and train all crew members on its proper use. • Have a first aid kit near, and know how to treat burns. • Add small amounts of material at regular intervals. Try not to drop an entire bag or block into hot material already in the kettle. Doing so will cause the molten material to splash up and in some cases out. • Try not to leave kettle or application unattended when lit. • Do not leave burners on when the kettle is empty. • Don't overheat material, overheating can cause fumes to ignite and cost more because the product can become scorched and unusable. • Operators need to understand the operation of the equipment before attempting to perform any striping or maintenance. Read the operator's manual fully and familiarize yourself with the thermoplastic equipment and striping process.
Before diving into thermoplastic application, make sure you and your crew are well educated on the product and the market. It is important to know the acceptable application methods in your area. Also, understand who your competition is. Be sure to take the time to practice and get the feel for it as well as understand the equipment and the process. "Anyone that wants to get into it has to be patient," said Schnelting. "If you have no experience, it will take a little research and due diligence to try to find your best price. But once you've figured out how long it takes to do a job and the temperature factors that go along with thermoplastic, it will become natural and you can successfully complete jobs you might have previously sub contracted out." ■
Thermoplastic paint dries quickly and can be walked on or driven on shortly after application.
Graco
ADVANTAGES OF THERMOPLASTIC MARKINGS:
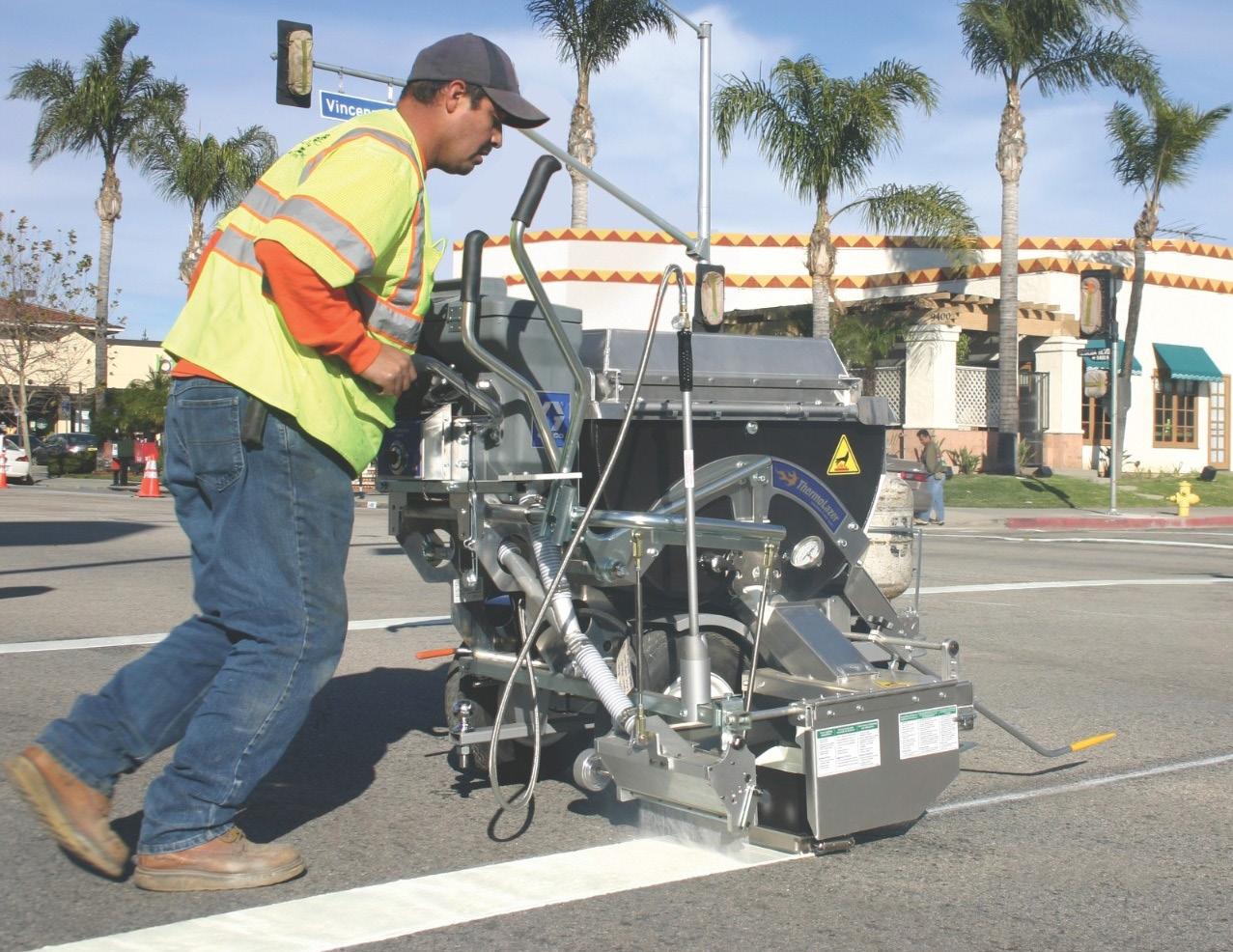
• Durability: Thermoplastic striping is created by combining glass particles and resins, which are then heated within a specially designed applicator and bonded to the pavement. • Visibility: The glass beads used for the application of the striping provide a built-in reflectivity. Thermoplastic striping is required marking material for most major roadways in southern United States. • Long Lasting: The unique blend combines with specialized application to create a long-lasting bond that is more resistant to fading, cracking and skid marks than other paint striping methods. • Quick Dry Time: Thermoplastic markings require the extra step of heating the material however, it does not extend the project time because the paint sets quickly, without losing texture, color, durability or finish. • Enhanced Safety: The markings are highly reflective allowing for optimal sight during the dark and stormy/ wet conditions when visibility is poor when drivers and pedestrians need it most.
For more information on striping technology, visit