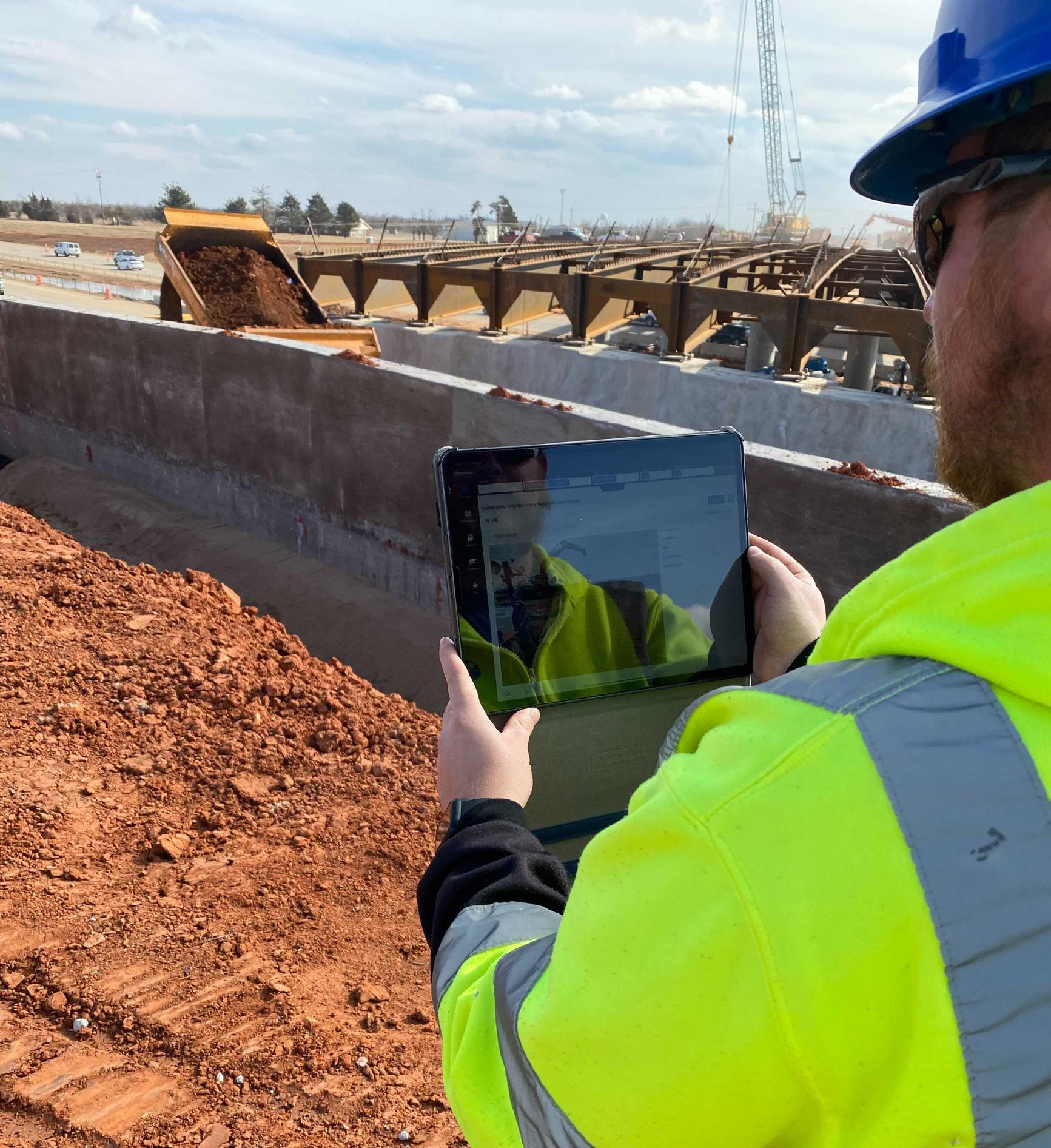
53 minute read
MOBILE TECHNOLOGY IMPROVES JOBSITE PRODUCTIVITY
A project inspector at a state DOT utilizes HeadLight as part of the inspection process.
As the industry evolves to do more work with fewer resources, technology is adapting to help achieve better results in less time.
The construction industry has historically been slow to adopt technology. While this may have been acceptable in the past, the increasing amount of challenges infrastructure projects are facing requires the use of advanced technologies to ensure both project accuracy and jobsite efficiency.
Si Katara, president and cofounder of HeadLight, started his company recognizing the challenges the industry faces. He and his team spent months meeting with construction business owners, DOTs and municipalities to look at what their existing processes were and what they needed to do to deliver projects. The team found that many existing processes were still predominantly paper based.
“We really wanted to understand what the business challenges were so we spent six months in the field,” Katara says. “Before we wrote a line of code or designed a single interface, we really wanted to learn what was the process and the communications up the stack — from inspectors to chiefs to project engineers to management — to complete the project delivery. And we saw just an incredible opportunity to apply technology to help solve that problem.”
From their research, the team developed HeadLight, a photobased inspection technology that can be used on projects to quickly and efficiently capture project data. This encourages greater collaboration between stakeholders, quickly resolves problem areas, minimizes disputes, and ultimately ensures successful, ontime project completion.
HOW IT WORKS
The majority of information collection on construction projects is still done using a notebook. The notes are then hand entered into a computer at the end of the day in a time-consuming and inefficient process.
“Paper-based operations are not only inefficient, but it’s almost impossible to integrate and share all that information in a timely manner,” Katara states. “HeadLight flips this form-based mentality on its head, allowing field staff to capture events as they occur naturally, not as the paper-based form is laid out.”
According to Katara, what comes from this method of data entry is close to a Facebook feed for your project, with photos being a core pillar of the technology. These photos are used to help project stakeholders communicate quickly and with all of the information wrapped in the context of the project.
“You get automatic location information, automatic time stamping and you can tie all that information directly to contractrelevant items,” Katara explains. “This also allows the information that’s collected in real time on a project to be used for many different purposes. That information is now available for state DOTs or public owners so they can share it directly with contractors for real-time issue resolution and things can get fixed much more quickly.”
The time savings can add up fairly quickly and in monetizable ways.
“With HeadLight, they can literally push a button and be done and go home after they’ve been collecting information throughout the day, which saves them almost an hour and a half of extra time each day as opposed to hand entering the information. So, there’s a big administrative savings there,” Katara points out.
“On the flip side, with the owners using it, they can share the information the state is collecting and allow contractors to see it in real time, as well,” he continues. “As a result, there’s no extra work for the contractor. They get access to a whole rich set of information and they know what the state is seeing and what they are noting as items that need to be addressed. And what it does is it basically creates a second set of eyes for the contractor through the state’s eyes.”
IMMEDIATE IMPACT
The technology was recently put to the test by the Louisiana Department of Transportation and Development (DOTD). The state’s research department found that
inspectors using the HeadLight photo-based inspection technology experienced a 28% increase in productivity when creating and submitting daily work reports that provide an overview of project progress. The increase in productivity for departmentwide adoption is estimated to produce 117,000 hours per year that can be leveraged to accelerate additional projects for the taxpayers of Louisiana.
In addition to supporting infrastructure projects across the state, the partnership between Louisiana DOTD and HeadLight also played a critical role in addressing the devastation caused by Hurricane Laura and a historic hurricane season in 2020.
According to Entergy, the DOTD faced thousands of miles of impacted roadways and more than 360,000 people in Louisiana were without power after Hurricane Laura hit. The power outages across the state disrupted legacy systems, making it impossible to access them.
Because HeadLight is a cloud-based solution, DOTD employees were able to access the system and view real-time updates from their colleagues across the region. DOTD’s strategic use of advanced cloud-based technology and HeadLight’s ability to customize its platform enabled the agency to complete 1.1 million cu. yds. of debris cleanup following Hurricane Laura even with Hurricane Delta bearing down on the state.
The study also revealed that inspectors using HeadLight collected and shared 1.9 times more jobsite information while increasing the number of photo and other media observations, which contributes to a more complete record of the project. With more details about projects, employees and contractors can collaborate more effectively and readily address challenges, as well as easily prevent issues, disputes and claims made in relation to a project.
Since adopting the technology, DOTD has reduced claims by more than 75%, ensuring the agency’s funds are spent on the development of projects, and issues are addressed quickly and in partnership with contractors.
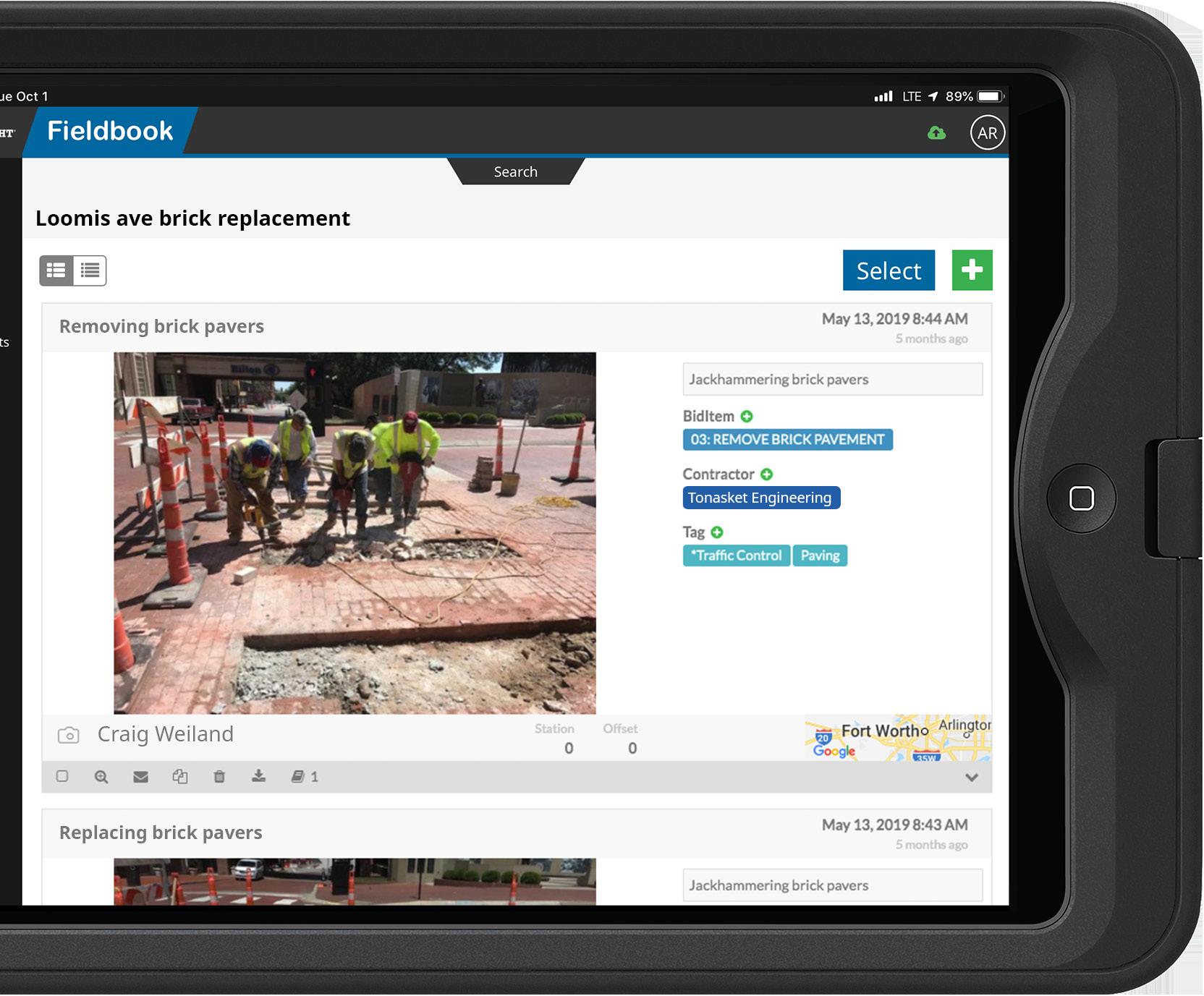
CHANGE IS GOOD
Change in the construction industry has been slow and difficult, but as solutions like HeadLight are proving, processes can and should be completed more efficiently with the technology available.
“We’ve been doing things in a certain way for so long, that just changing whatever it is —whether it’s a technology-based or process-based change — is just a difficult thing to make happen, especially at the organization level,” Katara acknowledges. “No matter what change you make, you have to communicate... in a way that creates a very clear understanding to contractors, or to whomever the stakeholder is, on what is the benefit and the practical impact of the change that you want to make.
“On the DOT side, if we can say this change is going to save you an hour and a half a day and you get to go home and see your kid’s softball game, that resonates,” he adds. “And that helps with getting through change.”
Any technology-based change being made in this industry needs to be accompanied by proper training, Katara emphasizes. HeadLight first works to identify the problems a specific organization wants to solve; maps out how to use the product to do it; and then takes the technology out in the field where they validate it with the end user.
“This isn’t an industry where you can just throw technology at people and then walk the other way,” says Katara. “We take a very hand in glove approach to be on jobsites in the field with them, to help them make that connection of what’s the practical business problem that they are dealing with every day and how does the HeadLight technology rise to the occasion to help them meet that and do it better. And it’s that environment on the jobsite that really makes those connections occur. When you do it that way, it really helps to ease that burden of change, because you’re doing it all the way to the ground level.”
The company also created a Best Practices Guide to help train and create consistency across the organization for everyone that uses the technology.
While change can be hard, it will be essential to success in an evolving construction environment.
“If we are able to secure a long-term investment in infrastructure, there’s going to be a flood of work and activity that will come with a long-term plan,” Katara comments. “With that raised level of activity, it’s going to be really hard to deliver
StreetsLA is using online technology to speed up the inspection process on street projects. what we’re going to be required to deliver as an industry without innovation, without technology and without really thinking about creative solutions to be much more effective and much more efficient.” ET HeadLight Photos are used to help project stakeholders communicate quickly, with all of the information wrapped within the context of the project.
“They know what the state is seeing and... noting as items that need to be addressed... it basically creates a second set of eyes for the contractor through the state’s eyes.” — Si Katara
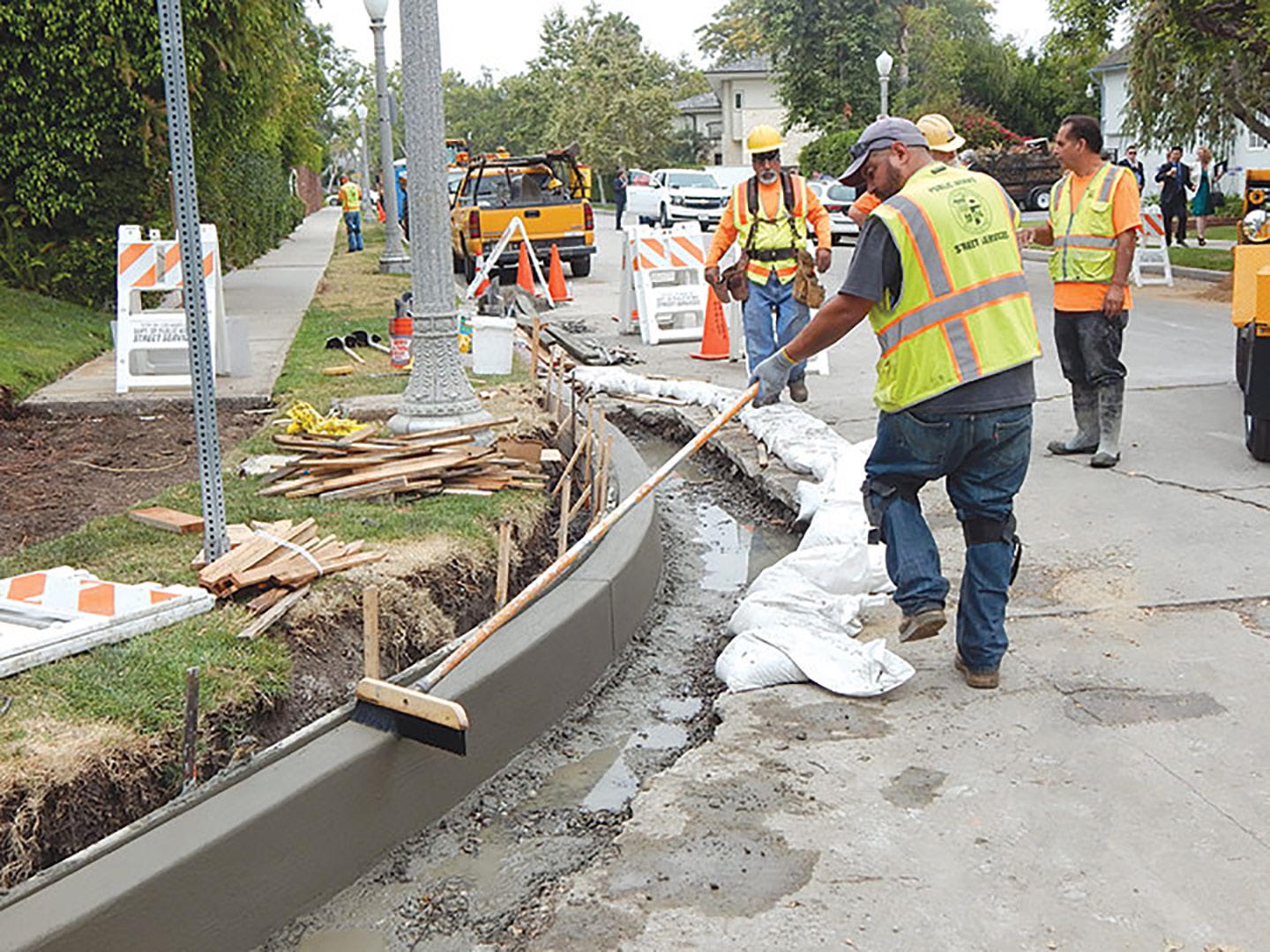
Barton Malow Tests Technology to TRACK TOOLS ON JOBSITES
Barton Malow is incorporating tool tracking technology into its projects to improve efficiency and cut tool costs.

The ability to capture data on how a tool is being used and how it’s performing on a project can provide useful insights that can be used to enhance both tool and operator productivity. DeWalt just recently introduced the Tool
Connect Construction Asset Gateway, which can be deployed in jobsite boxes, vehicles and tool cribs to automatically audit inventory and provide total jobsite visibility in its Site Manager platform.
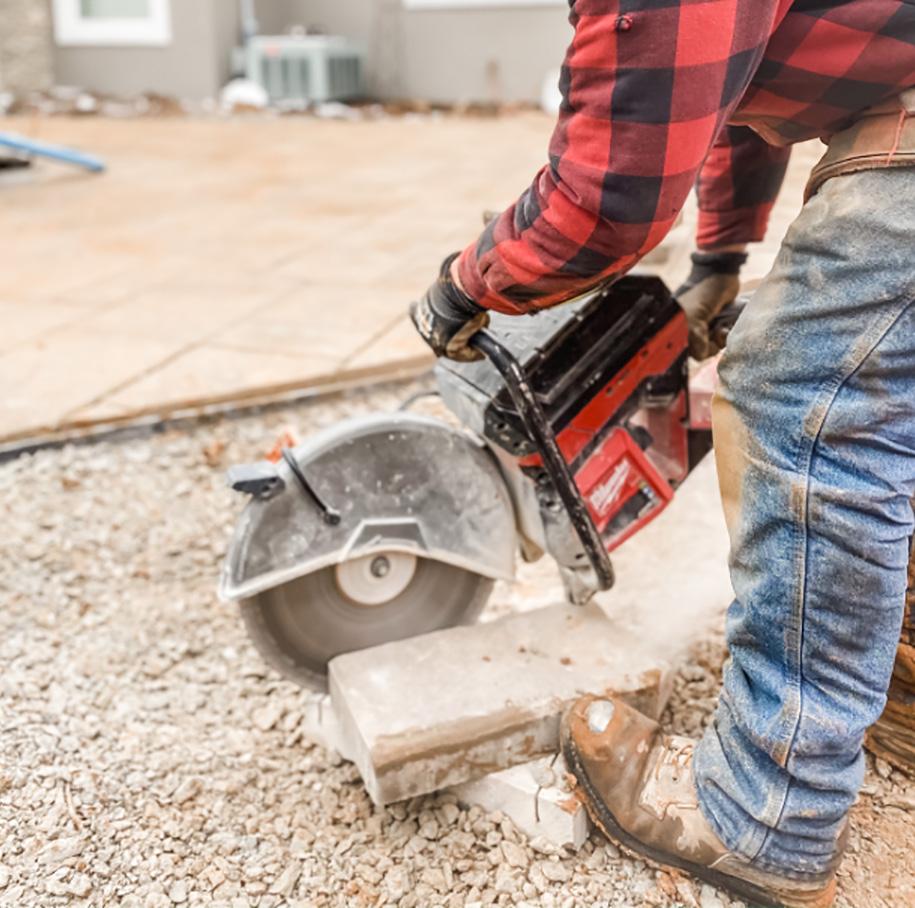
As tool technology continues to advance, the price of items such as concrete drills, cutoff saws and other powered hand tools found on construction projects tends to grow along with it. So, each time a tool disappears or is misplaced, it’s a further expense to replace it. A tool here, a tool there — the costs can add up to a lot during the course of a project or over an extended period of time.
To combat such cost creep on its construction projects, Ohiobased Barton Malow is testing available technology to see how it can help improve management of tool tracking and logistics and potentially save on tool costs long term.
MANY, MANY ITEMS TO TRACK
Barton Malow has been in business for nearly 100 years and has 15 offices throughout the East Coast, with projects scattered across the country. Employing more than 2,000 workers, it operates in the commercial, institutional, industrial, energy and manufacturing sectors, as well as self-performs civil operations, concrete — including walls, foundations and flatwork — rigging, structural steel, interiors, refractory, boilermaker and other work.
“One of the things that we pride ourselves on is that diverse market,” says Matt Hedke, director of virtual design and construction. “We try to have a pretty equal portfolio. Operating in all those different markets gives us flexibility. We don’t want to have too much work in one specific area.”
Working on projects throughout the U.S. means equipment and tools are distributed to several disparate locations at any one time. Tracking those resources is a primary challenge, according to Ryan Tow, operations manager. Tow oversees the equipment yard in Oak Park, MI, which supports all of the self-performed trades. Nearly all the equipment, tools and accessories Barton
Malow requires on projects are moved in and out of yard operations, so each item must be carefully tracked and managed. This adds up to a lot of individual items. “All of the [concrete] accessories, all the panels... are tracked and managed and rented out of our yard operations,” Tow notes. “Some of the things that are the most challenging, I would say, are a lot of the smaller items that we have where there tends to be a huge inventory. Formwork is one of them... because we have multiple formwork systems and there are a lot of accessories that go along with them.
“Being able to track and manage those from project to project and at the same time keep our inventory up to our standard, and then be able to redeploy to the next job — there’s a lot of stuff that goes on behind the scenes,” he comments.
Consequently, it’s not the heavy equipment that is typically the biggest issue on large jobs. “It’s hand tools like the cordless impacts, saws, stuff like that. We have more of an issue as a company tracking those specific items than we do our equipment,” Tow acknowledges. “For the most part, we have a pretty good handle on all of our [heavy] equipment.”
Barton Malow uses a sizable number of small tools. If they go missing, costs mount. “Everybody knows the price of everything just keeps climbing and climbing,” Tow says. “It was a $60 drill. Now, it’s a several hundred-dollar drill and then you have a $150 battery, two or three of them. So, you have a good amount of capital tied up into a cordless power drill.
“We’ll walk away from a yearto-year job and there’s a huge dent. There’s a lot of missing stuff on certain projects, especially the further out we get where they’re not our ‘regular’ staff,” he notes. For example, laborers brought on for these jobs may not fully understand the company’s processes, there may be theft, tools may be picked up by other contractors, etc. “There’s a bunch of different scenarios, so we have more issues on that end.”
“As we get further and further away from that centralized hub, a lot of those things get more complex and harder to manage,” says Hedke. “There are all these moving parts that, over time, we have evaluated and refined. And we continue to try to figure out how do we leverage technology to help drive that process and educate not only our own people on our projects but our trade partners, as well.”
TOOL MANAGEMENT, COST CONTROL AND MORE
To enhance tool management, Barton Malow has been using DeWalt’s Tool Connect on select projects. “I’ve been pretty heavily involved in the DeWalt portion of it for about two years. We’ve used it on a few projects, smaller jobs,” says Tow.
A more recent addition has been Milwaukee Tool’s Tick, a
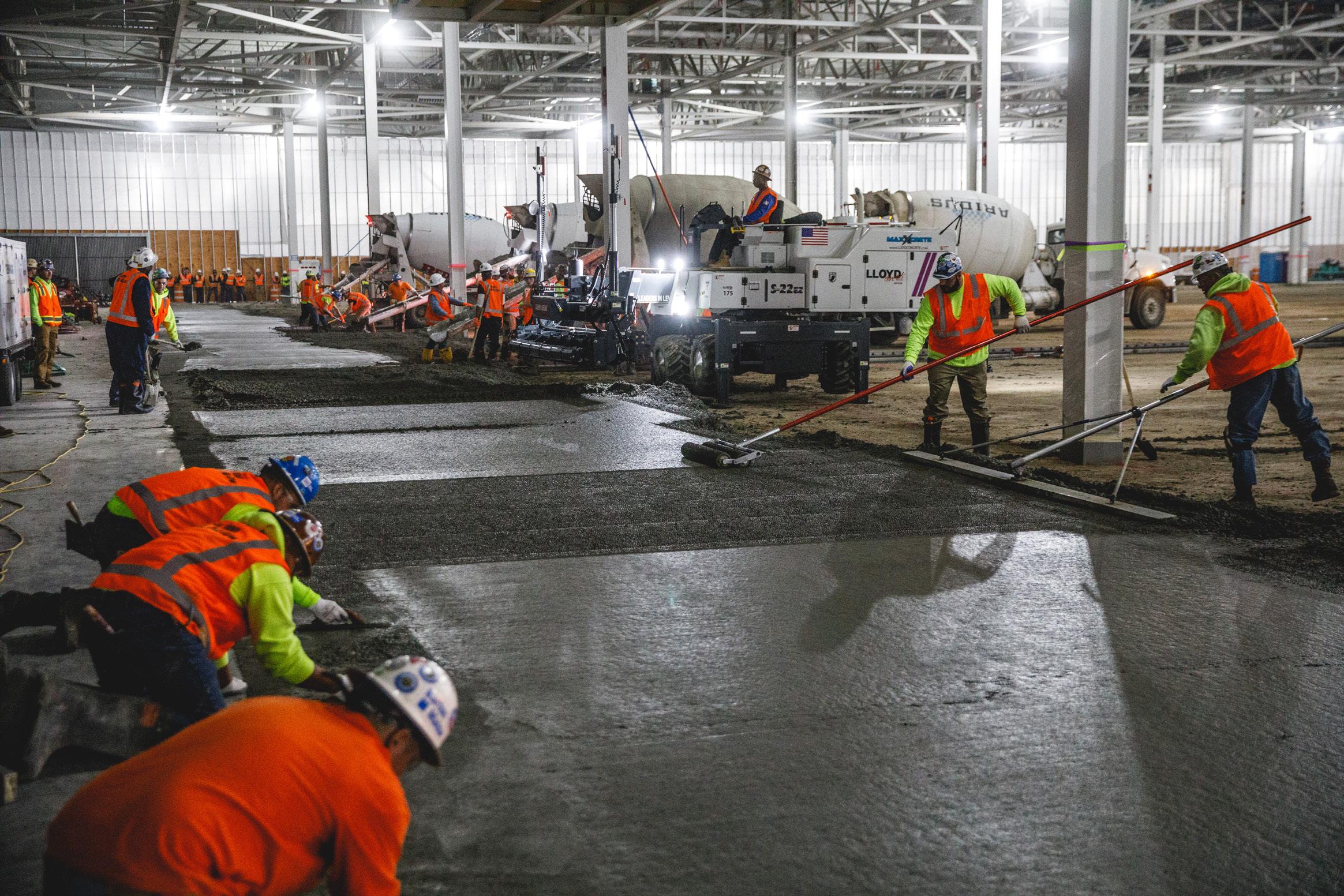
Nearly all of the equipment, tools and accessories Barton Malow requires on projects are moved in and out of yard operations, so each item must be carefully tracked and managed.
Bluetooth tracking device that provides location updates when the tool comes within 100 ft. of a phone that has the One-Key app installed. “We use it on our small power tools — SDS-plus hammer drills, 1/4-in. impacts, 1/2-in. drill drivers,” says Tow. “There’s an assortment of smaller cordless power tools that we have those on.”
The potential advantages in logistics management have proven readily apparent. In the past, when a tool couldn’t be found on the jobsite, the crew would simply order a new one. With tool tracking, that’s no longer necessary.
“You have the capability to be able to say, ‘All right, I know I [had] a tool that was here this morning,’ and then be able to pull up some software, look on a map and know it’s over in the southeast corner [of the jobsite],” Tow explains. “When you can say, ‘Let’s go get it’ instead of having to buy another one, you’re saving resources and capital.”
Also offering significant advantage is the ability to create geofences. “From a theft perspective, by creating that geofenced perimeter, that tool shuts off if it leaves or you get a notification that it’s left [the specified area],” Hedke says. “Those are all things that I think we, as an industry, can see huge benefits in.”
The ability to capture data on how a tool is being used and how it’s performing on the project offers benefits, as well. “From my perspective, Milwaukee Tool and others started to look at opportunities to get data out of their tools,” says Hedke. “That [opened the door] for us to... try to figure out, ‘How do we make that connection between the user and that data and learn from that data? How can we start to look at the data holistically and use it as a way to learn and get insights on tool utilization?’”
“If a grinder pulls, if the brake e-clutch is engaging — the same with the hammer drill — being able to pull those analytics off for safety and being able to train your staff is a benefit,” Tow agrees. “Some people aren’t necessarily going to be trained correctly in how to use power tools from a safety standpoint, so you can use that information.”
The data could also be used to assess the type and number of tools that will be needed to complete a project or task. “Tools have a useful life. You can figure out how many tools you’re going to need by how many dowel holes you’re going to be drilling, or whatever it might be,” says Tow. “A lot of it is just to be able to get that information off of that tool and use it in a productive manner.”
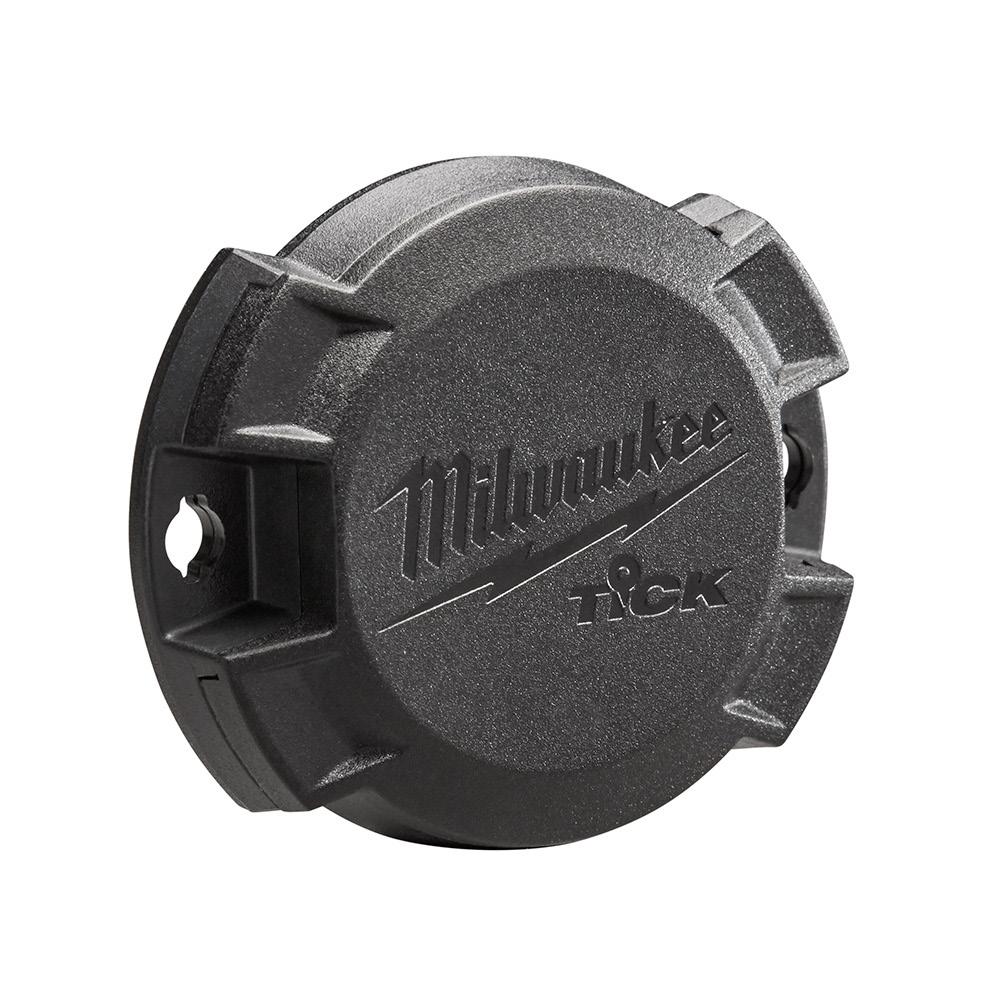
LEARNING THROUGH PARTNERSHIPS
Setting the stage to maximize the overall benefits of tool tracking technology is an ongoing process for Barton Malow, involving input from multiple sources.
“The only way that we’re going to learn is if we get plugged into it and we start to identify and partner with the tool manufacturers and partner with our project teams to set up a roadmap to say ‘Here’s our basis for a pilot and here’s some low-hanging fruit that we think we can get. If we can achieve that first step in just capturing this data, here’s some benefits that we see,’” Hedke comments. “And I think, organically, you’re just going to learn that there are other benefits that maybe we’re not yet seeing.”
As such, Barton Malow continues to partner with more than one supplier and test the systems’ performance. “We haven’t really kicked things off on a single source because it does take a yard operation, staff behind the scenes and the project team to actually use it and [determine] what the capabilities are,” says Tow. “And not every job is structured to where it marries up perfectly. Sometimes, there are too many moving pieces, it’s too large a job, they don’t have the staff on the jobsite, etc.”
There’s also the matter of whether data can reach where it needs to be. “When you start to have... all these smart tools out in the field, there’s certainly a jobsite connectivity concern,” says Hedke. “I think that’s an industry-wide problem.”
Then there’s the issue, and opportunity, with software integration. “There are a lot of different project management solutions out there,” says Hedke. “We’re a big Autodesk user; we use BIM360. [We’re learning] how we get that data and that tool tracking technology integrated into our project management solution. That’s another opportunity that we’ve been having a lot of discussions with the folks at Milwaukee Tool about.
“Again, it just brings up a lot of really, really cool opportunities that we’re excited about that we want to be a part of coming up with a solution for, and certainly looking to partnerships with Milwaukee and others to try to solve them,” he continues. “I think the technology is going to allow us to really open the door for how we track and manage our tools, use the data we get from them and integrate it with other solutions.”
Still, there is value in taking a measured approach. “There’s an endless amount of data that it can probably be overwhelming if we’re not careful,” Hedke acknowledges. “But I think if we’re smart, we can start to use it in a smart way and learn from it and better ourselves for years to come.” ET
Milwaukee Tool
Milwaukee Tool’s Tick is a BlueTooth tracking device that provides location updates when a tool comes within 100 ft. of a mobile device that has the OneKey app installed.
Leica Updated BLK3D 3D Handheld Imager
The BLK3D updated handheld imager has doubled its operating range and in-picture measurement accuracy for many indoor and outdoor applications, such as exterior building measurements for scaffolding, façade, roofing and architecture projects.
•Can capture image with centimeter accuracy in seconds •Enhanced image processing algorithms and workflow adaptation allow for capturing multi-shots with up to four shots •BLK3D with Publisher license enables seamless collaboration among teams with increased accessibility to published 3D images through the cloud www.ForConstructionPros.com/21045087



Milwaukee Tool One-Key Asset ID Tags Tenna Equipment Fleet Management App
The Equipment Fleet Management app provides access to asset information from Tenna’s One Platform at your fingertips.
•Scaled-down version of online platform is synced to the cloud and allows user to create new assets, edit existing assets and connect installed trackers to the platform •Access and update pertinent asset details such as status, condition, location, assignee and more •Scan assets and inventory with QR codes to automatically update location and edit details •View utilization data on individual assets or assets by projects •Enables working offline if out of range www.ForConstructionPros.com/21092158
The Fleetwatcher Materials Management Solution is a wireless telematics system for paving contractors that uses load cycle analysis to allow users to see where problems are occurring and correct them in real time.
•Enables users to identify traffic problems in real time and reroute trucks on the fly •E-ticketing modules eliminate points of contact •Transponders can be hardwired into trucks or installed via cigarette lighter adapter •Mobile app accessible via cell phone or tablet •Integrates with popular accounting and payroll applications and scale systems www.ForConstructionPros.com/12294134
ConcreteDirect Concrete Order Management App
The ConcreteDirect app helps you manage orders, track deliveries and monitor performance of concrete pours from the palm of your hand.
•Can be used across various technology platforms (iPhone, Android and PCs) •Follow truck positions live on GPS and message customer care representatives within the app •Share tickets, view active orders and order history, correct order mistakes in real time and monitor crew performance from any location •Includes touchless tickets, contactless delivery, QR code tracking system, pins as signature replacement, GPS routes and Field Level Risk Assessment www.ForConstructionPros.com/21576997
Soil Connect eRegulatory Module
Available through the Soil Connect digital marketplace, the eRegulatory module automatically captures and saves essential truck, load and route data, allowing users to easily share with regulatory bodies and other stakeholders.
•Includes documentation settings for both clean fill and contaminated dirt •Turn-by-turn GPS tracking provides an end-to-end record of the truck and material route •Enables contactless e-signatures •Digital database for manifests provides a record of all routes and deliveries in one place •Information can be easily shared with local regulatory bodies in a PDF format www.ForConstructionPros.com/21521485
Durable ONE-KEY Asset ID Tags allow users to easily manage smaller tool and equipment inventories by providing instant documentation as assets are transferred between jobsites and users.
•Scan tags to record time and location data using a smart mobile device with an integrated camera and ONE-KEY app •Come in small (.69” x 1”) and large (1.5” x 2”) and in sets of up to 200 designed to adhere to plastic or metal surfaces •Offer water and chemical resistance, fade protection from UV light, scratch resistance and maintain adhesion through significant temperature fluctuations www.ForConstructionPros.com/21220313
Command Alkon TicketPro Digital Ticketing Solution
The TicketPro solution digitizes 100% of material and haul tickets that enter a production facility or a jobsite.
•Ticket signer simply selects a project, chooses the material being hauled and snaps a picture of the paper ticket •Can utilize scanner integration or capture tickets directly from a scale printer •Allows for job cost reporting, accruals reporting, invoice reconciliation, tracking quantities delivered and more •Takes all data on the invoice and matches it against actual ticketing data www.ForConstructionPros.com/21562995
Skyward Mapping & Modeling with Pix4D
Skyward Mapping & Modeling, powered by Pix4D, enables customers to create, view, measure and export 2D orthomosaic maps and 3D photogrammetric models right from Skyward’s web app.
•Plan flights, receive approval to fly in controlled airspace with LAANC, fly with Skyward’s InFlight ground control station and process data using Pix4D from within the Skyward platform •Provides access to business-ready data sets via a seamless plan, fly, process workflow www.ForConstructionPros.com/21563134

Contextual Mobile Device Management automatically adjusts access to mobile apps and features based on a given work environment and additional contextual indicators.
•Includes a web-based Management Console, mobile app and available Beacon technology that can detect movement or be used to define boundaries •Employer defines how to protect employees based on location or proximity to high-risk areas or equipment, movement including speed, time of day or day of week and user or work group •Apps and functions that help employees are kept front and center, while those seen as distracting are temporarily hidden www.ForConstructionPros.com/21295111
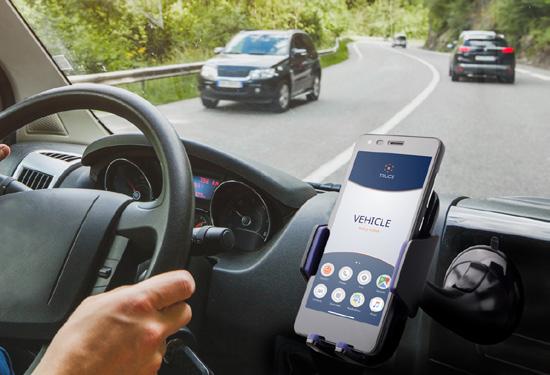
Mecalac MyMecalac Fleet Management System
The MyMecalac telematics solution comes standard on the company’s excavators and loaders.
•Simply log in to the web portal or app to access all machine data in real time •Delivers high-level summaries to specific machine details to empower fleet managers to boost efficiency and machine uptime •Alerts can be set up to notify user when maintenance is required or when a fault code appears, as well as if the machine moves from a designated zone or operates outside of designated hours •Enables dealer technicians to remotely diagnose machine issues www.ForConstructionPros.com/21521665
Lytx Badge Driver Identification Solution

The Lytx Badge driver identification solution detects driver ID using a QR code without requiring any additional hardware.
•Driver scans a unique QR code from a badge or cell phone using the installed DriveCam Event Recorder •Driver’s name recorded along with vehicle data for visibility into driver hours, how much time the vehicle is moving during each shift and how much idle time occurs •Automatically assigns events captured by DriveCam to the appropriate driver •Works with Driver Safety, Risk Detection and Fleet Tracking modules www.ForConstructionPros.com/21159835
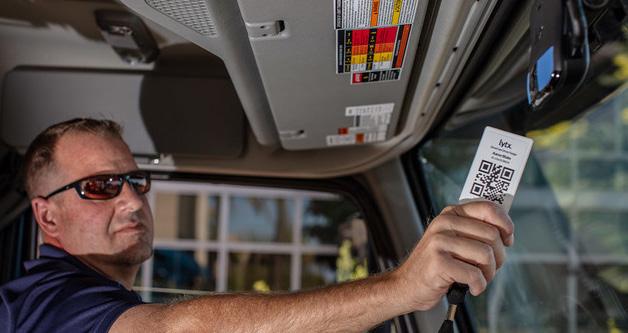

Zonar Next-generation EVIR Solution Senzit Predictive Maintenance Platform
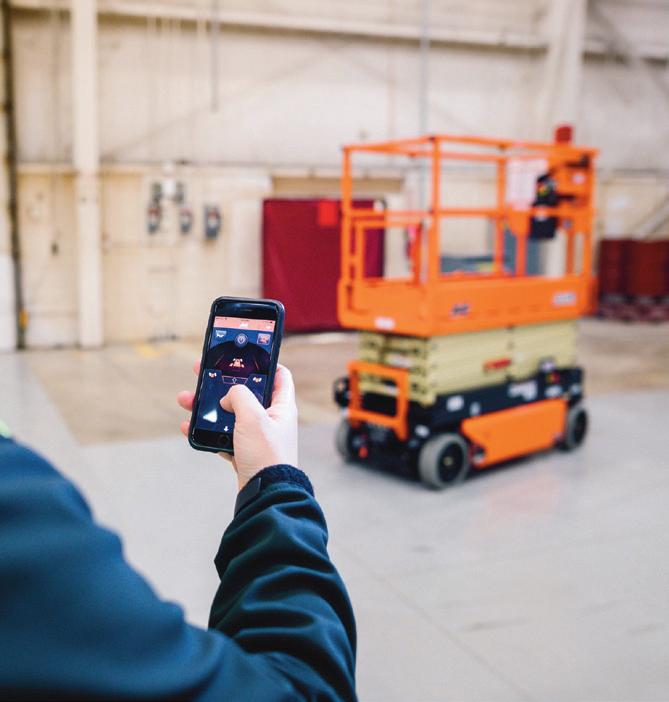

ezNova ezClocker
ezClocker is a simple to use time tracking and scheduling software solution for small construction companies with crew members who work at different locations.
•Online job scheduling feature allows employer to create shifts for crews and assign them to a location •Timesheet export feature sends hours to accounting for payroll or enables calculation of how much each job cost in labor •Cloud-based time clock app enables employees to use their own phone to clock in and out and supports multiple smartphone devices •GPS stamp automatically saves employee location when they clock in or out so employer can verify they were at the correct location www.ForConstructionPros.com/21590576
The mobile version of the electronic verified inspection reporting (EVIR) solution improves and verifies Federal Motor Carrier Safety Administration mandated pre- and post-trip inspections.
•Includes features of the original EVIR in a mobile-friendly app with additional features and functionality •Inspections can be completed quickly and accurately and results digitally stored without the need for extra hardware •Intuitive Asset Map View shows aerial views of vehicles and equipment with guides for tag placement, plus training videos and links within application •Inspection history and data can be accessed through the Ground Traffic Control web-based platform www.ForConstructionPros.com/21710769
This subscription-based predictive maintenance platform for heavy-duty fleets consists of a user-friendly mobile app and web portal that enables remote monitoring of the health and location of equipment.
•Allows users to remotely monitor air filter dust load percentage and remaining hours of use, view engine hours, optimize routes and prevent theft with machine trip history and more •Use digital log book to record service and maintenance with notes and photo documentation •Utilizes predictive machine learning and smart AI to notify user of filter changes before breakdowns occur •Viewable via a desktop or mobile device www.ForConstructionPros.com/21614846
JLG R Series Scissor Lift Mobile Control App
The JLG Mobile Control app enables users to drive, steer and load R Series scissor lifts while in a stowed position from an iOS mobile device.
•Available as an option on new lifts or as an aftermarket option •Assists operators in positioning lift into areas with low clearances and to the best location to see jobsite obstacles •Allows machines to be loaded onto trucks without the need for an operator in the platform or walking next to the machine •Easy to use and equipped with an intuitive user interface that displays all essential features to run the machine •Displays battery and machine status plus includes a horn symbol that allows operators to easily alert jobsite personnel when the machine is operating nearby www.ForConstructionPros.com/21048175
TRUX Contactless Ticketing Solution
TRUX Contactless Ticketing is a robust e-Ticketing solution that integrates sales orders and scale tickets directly into technology solutions for all participants in the material supply chain.
•Allows contractors, dump truck drivers and material producers to safely and digitally record and track data from construction projects •Leverages unified digital dispatching, hauling and site contact load tracking and resolution software •Meets established requirements from the leading state DOTs across the country for digital ticketing www.ForConstructionPros.com/21139310
Core LaborOS/Crews by Core Pro
The Crews by Core Pro Labor Operating System (LaborOS) offers the capability to hire and manage crews with a task and labor management tool that syncs with existing systems.
•Connects teams across the field and office via a single system on a desktop or mobile device •Desktop control center (C4) can be used to manage project status, real-time updates and communication, tasks, subs and crews •Easy to use app for workers to see which tasks are most important and chat using real-time messaging •Provides reports and insights on task completion and labor workload www.ForConstructionPros.com/21563101
HCSS myField Mobile Time Tracking and Engagement App
myField is a mobile employee engagement and time tracking solution for heavy construction operations.
•App allows crew members to directly clock in or submit their time and information, as well as review their hours logged •Foreman receives a copy and can review events and times per employee •Can also be used for individual time tracking, quick equipment safety inspections, cost code work, documentation, safety observations and maintenance requests •All clock in/out locations stamped with longitude and latitude www.ForConstructionPros.com/21330877
Trackunit Kin Asset Tracker
Trackunit Kin enables all on-site machines and equipment to be tagged and connected, tracked and managed using a single, easy to use application.
•Compact, robust tags can be attached to any small, medium or large asset and activated, installed and onboarded in seconds via a mobile device •Cloud-based IoT platform offers real-time intelligence to precisely locate equipment, accessories and tools •Users can track the utilization of attachments and tools including the correct attachmentto-machine pairing •Up to 400m of line-of-sight detection •Connects to the RAW (TU600) installed network of devices via the Trackunit Go app www.ForConstructionPros.com/21319393
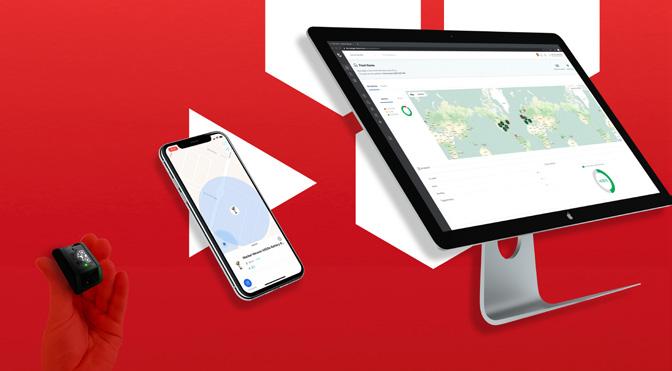
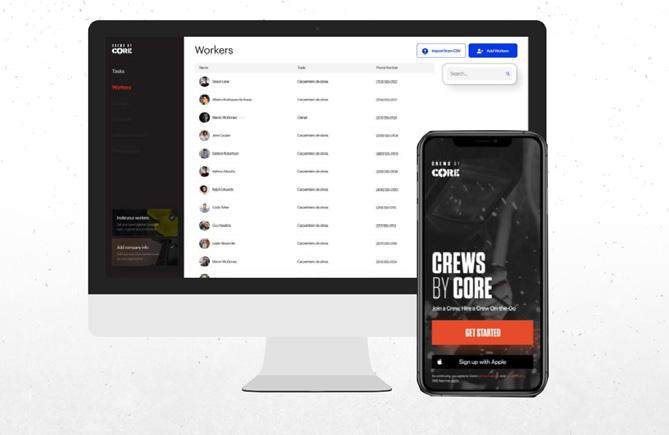
What Does Workforce Management Mean for CONSTRUCTION?
How construction workforce management can help you more effectively engage with your people.
People are a company’s most important asset and that’s why it’s important to focus on them when building a strategy for your construction business. One of the most noticeable differences between companies that thrive and those that fail is usually workforce management — or a better way to say it is how contractors engage with their people.
While most people think construction workforce management is the same thing as scheduling labor, labor scheduling is only a portion of the full definition. Yes, you have to schedule your people, but workforce management means managing your roster beyond a schedule.
From data management and communication, to people management and planning, a cloud-based workforce management platform can open new doors for your people and business. Let’s break each of these areas down by what they mean for the construction industry: ˜ Data management: Organizing and housing all of your people and project data in a secure manner that creates time savings and new efficiencies. ˜ Communication: Efficiently sharing project, scheduling and additional updates on an individual or workforcewide basis to ensure everyone stays in the know and has all of the information they need to be successful. ˜ People management: Ensuring your roster stays motivated, develops new skills and stays up to date on certifications so your organization can tackle any project at any given time. ˜ Planning: Having information you can depend on to ensure your company can forecast ahead for new projects and know when to ramp up your workforce.
When paired with labor scheduling, the elements listed above help paint the full picture of what workforce management entails. BENEFITS OF DIGITAL SOLUTIONS
Like others, you want to optimize the productivity of your staff and effectively forecast labor needs for future jobs. From a basic point of view, it’s simply knowing where your people are today and where you need them in the future.
By identifying and onboarding workforce management software, you can gain direct and actionable insight into your workforce. The platform can provide realtime information about people’s skills, certifications, location and more, while also communicating project updates to your entire team, or only to those who need to know. In addition, the nature of scaling up and scaling down on construction projects means the size of your labor pool will fluctuate; a digital workforce management platform can help you manage those fluctuations.
With a better understanding of your needs and a definitive labor plan, you will be better positioned for growth because
LIFTING SOL UTIONS
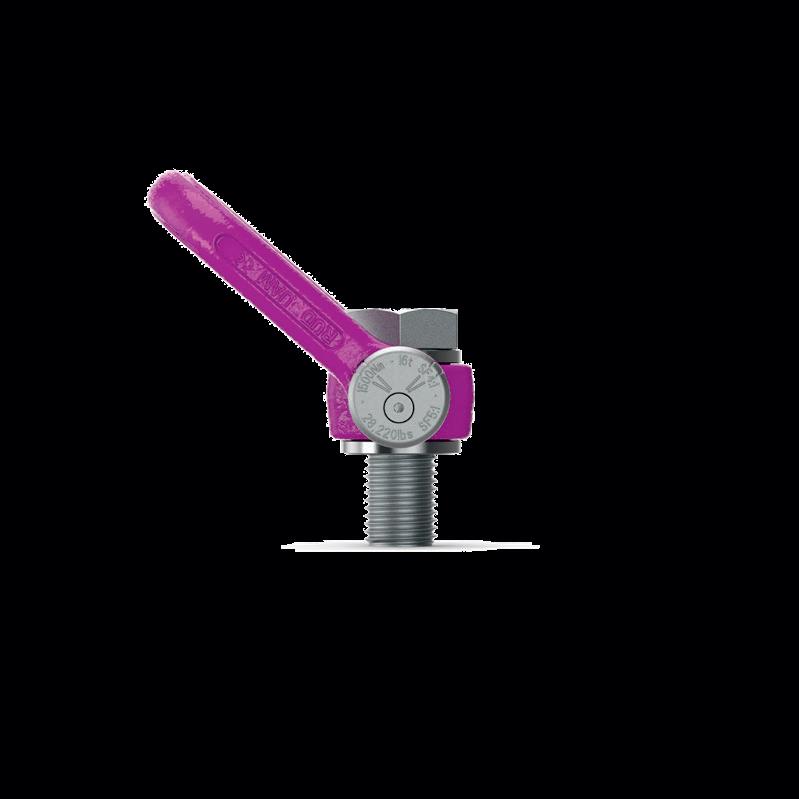
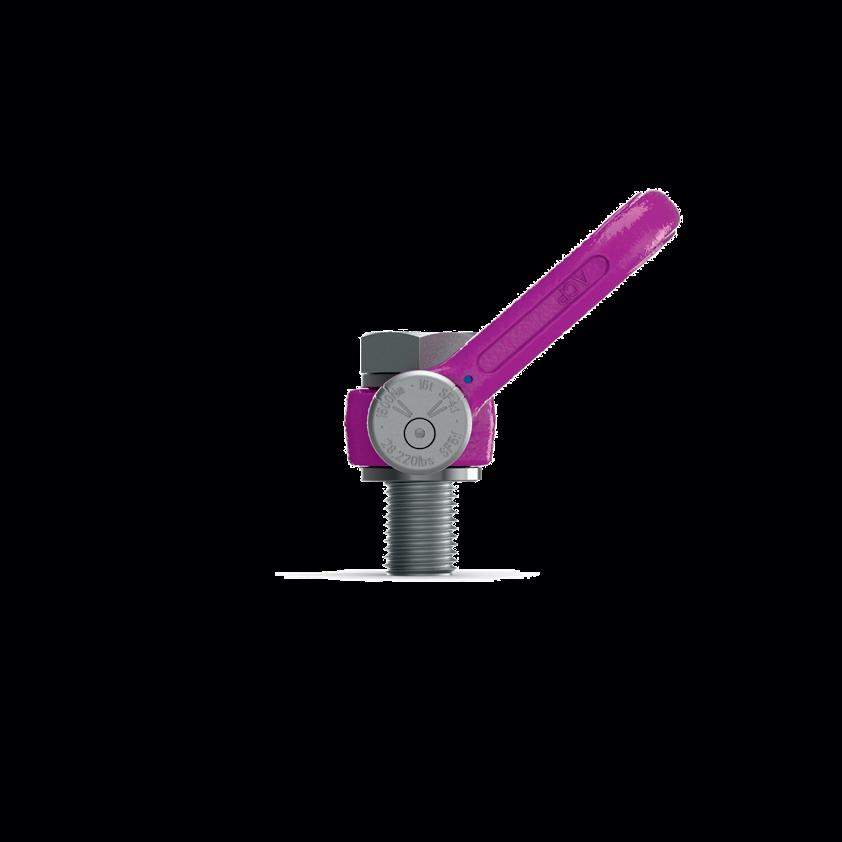
SMARTER. BIGGER. STRONGER.
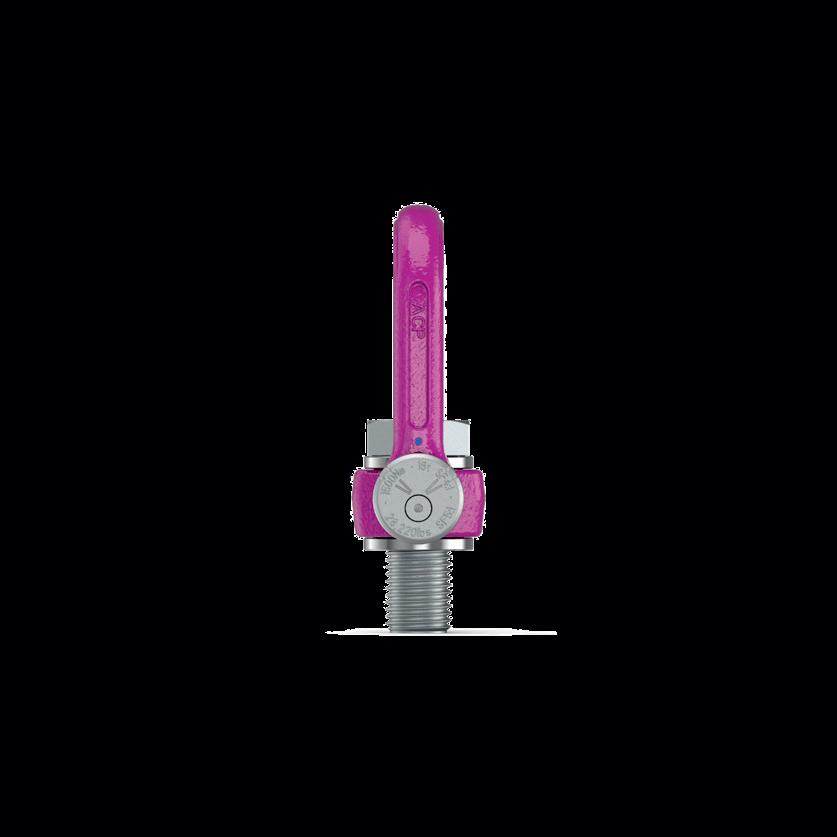
THE NO-WORST-CASE POSITION LIFTING POINT
RUD ACP-TURNADO
NOW IN M36 AND M42 AS WELL AS 1½” + 1¾” FOR LIFTING HEAVIER LOADS. you will be able to identify exactly what is required to take on additional projects. This single source of truth builds confidence within your organization, makes bidding future jobs more accurate and gives you extra insight into what makes sense for your business.
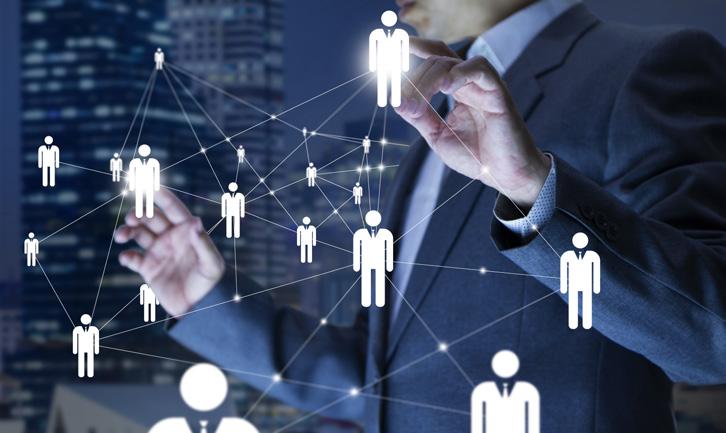
MEETING NEEDS FOR THE FUTURE
No matter the industry, workforce management can play a vital role. You can only schedule, not manage, your workforce on a spreadsheet, whiteboard or piece of paper. There’s no planning ahead, active communication or real-time information available.
Construction companies from Slotegraaf Construction in Ontario, Canada, to P2K in Atlanta, GA, are already using digital tools to learn from the past and plan for the future and win future jobs. For example, P2K, a civil contractor founded in 1998, previously spent hours going over Excel spreadsheets, under-utilizing staff in unproductive labor meetings and misplacing worker information in its files. By implementing the LaborChart workforce management platform (https://bit. ly/2UwUPOb), it is now able to: ˜ input new employee information and track certifications; ˜ effectively forecast how many workers will be needed with any given project throughout the year; ˜ provide project managers with a holistic view of each worker, jobsite and overall costs; ˜ and “tag” workers who are certified to work on certain tasks and those authorized to work on government projects.
There is a risk that companies who aren’t adopting new technology will slowly fall behind. Workforce management can help them to optimize their workforce and identify new management efficiencies in order to realize their full potential. ET
Here is a collection of products designed to enhance jobsite efficiency, productivity and/ or safety. For more information, use the URLs shown or visit the New Product Directory at www.ForConstructionPros.com.
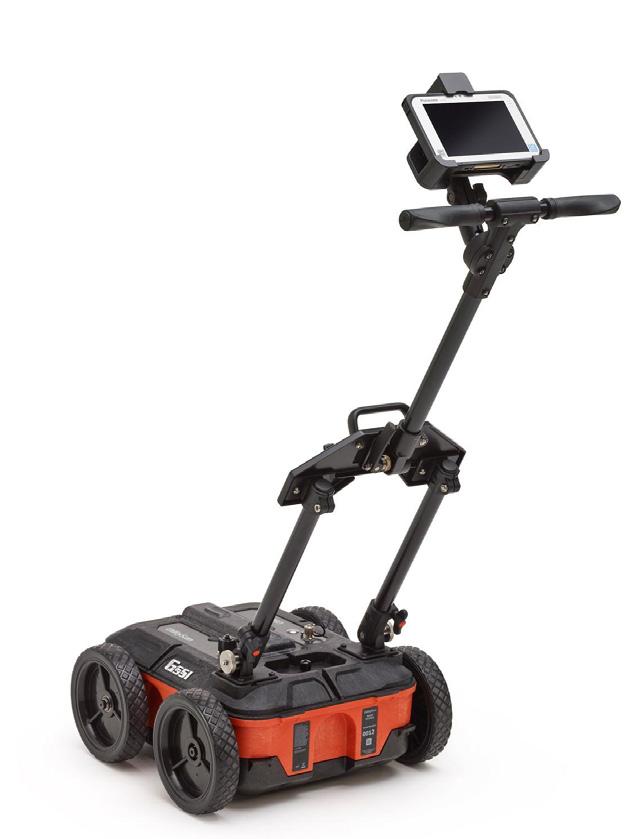
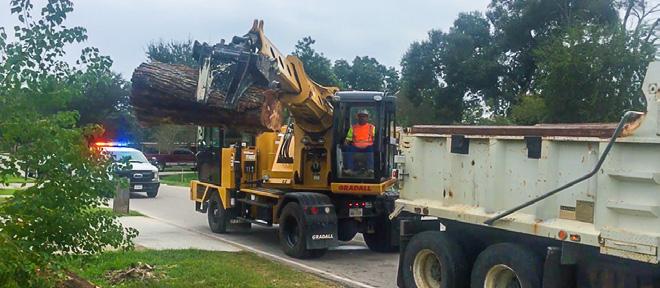
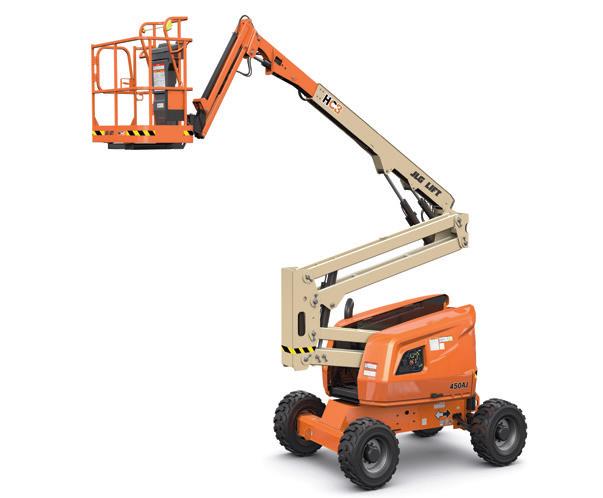
Gradall Fixed Thumb Grapples
Fixed thumb grapple attachments expand the capabilities of Gradall excavators in emergency applications after severe weather, as well as for routine jobsite cleanup and demolition.
•Can be used to reach out and remove brush, debris and tree limbs that may block roadways •Able to move bulky, irregularly shaped objects, waste and building materials •Maintain a strong, positive grip on loads and can be precisely positioned with the excavator boom •Available for Storm Recovery Series wheeled excavators, Series V excavators and Discovery Series models www.ForConstructionPros.com/21244754
JLG 450AJ HC3 Hi-Capacity Boom Lift
The 450AJ HC3 boom lift has a 45-ft. platform height and 25 ft. of horizontal outreach.
•660-, 750- and 1,000-lb. capacity zones provide ability to carry up to three occupants and tools to height in every zone •Zero calibration, automatic loadsensing system keeps machine within the allowable work envelope by limiting range based on platform load •Chassis tilt alarm alerts operator when the machine is on a slope greater than 5° •LED display and ground controls improve visibility by sensing ambient light conditions and adjusting brightness www.ForConstructionPros.com/21354791
Komatsu Expanded Hydraulic Breaker Range
This line of breakers is compatible with PC78 to PC490 excavators.
•Accumulator eliminates hydraulic pump cavitation •Blank firing protection standard •JTHB-G line uses hydraulic flow and pressure plus a nitrogen-filled chamber to provide striking energy and features only two moving parts, a patented tie-rod design, hydraulic cushion at the cylinder base and key slot dampers (larger models) •JMHB-H accumulator-type models don’t require nitrogen recharge, have a single power cell instead of tie-rods and offer sound-dampening housings, a pressure regulator valve, vibration dampening system and automatic lubrication www.ForConstructionPros.com/21415750
MBW AP/GP18 Vibratory Plates

The GP12, GP15 and GP18 singledirection vibratory plates weigh 130 to 184 lbs. and are available with or without a water tank.
•Suspension system reduces hand-arm vibration and better isolates all upper mass components from vibrations produced by the exciter •Optional UHMW paving pad •GP18 includes a modified spray bar, added clearance to allow use of a paving pad, standard Honda GX160 engine and side plate handles •Designed to be easy to lift and maneuver around the jobsite www.ForConstructionPros.com/21354560

Carlson Paving EZIV Front Mount Screed
The EZIV Screed provides a reliable, heavy-duty screed platform for commercial, municipal and highway-class applications.
•Available in 8- and 10-ft. models •Can be mounted to all current North American asphalt pavers offered by major manufacturers •Can be retrofitted onto most previous North American highway-class pavers www.ForConstructionPros.com/21342414
GSSI UtilityScan GPR System
The UtilityScan compact GPR unit is highly portable, easy to maneuver in tight survey areas and ruggedly built to withstand challenging field conditions.
•Features a robust wireless antenna that can handle required data rates •Electrical design uses HyperStacking technology to increase depth penetration in challenging soils while providing high near surface data resolution •Includes backup Ethernet connection if WiFi is not desired or allowed on a particular jobsite or facility •Can be used with the LineTrac accessory to help locate specific underground power sources including AC power and induced RF energy present in conduits www.ForConstructionPros.com/12008564
Crary Bear Cat CH1015H Chipper
The CH1015H engine-powered chipper has a 10-in. capacity to allow for chipping larger trees and less pruning of smaller trees.
•57-hp Kubota gas engine equipped with a block heater for cold environments •Rotor includes six reversible blades and four paddles for efficient chipping and discharge •Digital Display Controller (DDC) offers push-button control, in-field troubleshooting and hydraulic system diagnostics •Self-contained hydraulic system with flow control to allow optimization of feed rate •Easily towable trailer with a four-position, 18-in. telescoping hitch pole www.ForConstructionPros.com/21565151
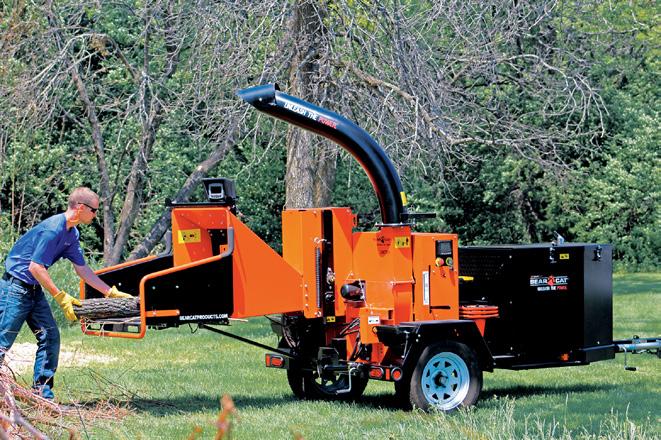
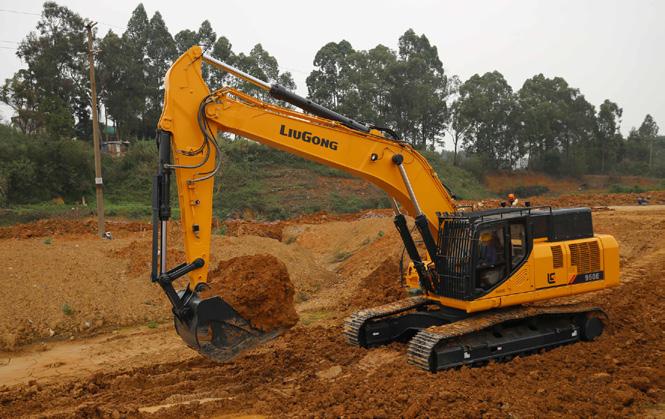
LiuGong 950E Crawler Excavator
The 950E has an operating weight of 108,467 lbs. and a bucket capacity of 2.88 cu. yds.
•Maximum digging depth of 25 ft. 9 in. •Features a 64,745-lbf. arm digging force and 71,939-lbf. maximum drawbar pull •400-hp (gross) Cummins QSG12 Tier 4 Final diesel engine with 1,500 lbs.-ft. of torque •Optimized load-sensing hydraulics •Cab includes ergonomically designed controls, clear and informative displays, increased visibility and enhanced comfort www.ForConstructionPros.com/21205490
RimRiser Bolt-adjusted Manhole Leveling Solutions
The RimRiser adjust-to-grade systems for manholes, catch basins and precast tops make the process of leveling cast iron manhole rings, inlet frames/grates and precast concrete tops simpler, faster and more accurate.
•More than 35 RimRiser-ready castings available including models specified for 15 states •Eliminate hazards from lifting with prybars, overhead machines or slings and prevent accidental drops on hands or fingers •Bolts are small enough to fit in a pocket, making them easy to store and carry •Castings all utilize the same boltadjustable system so there’s no need to order special sizes in advance www.ForConstructionPros.com/21603084
CLC Work Gear Molded Base Tool Bags and Tool Carriers
This line includes a Molded Base Tool Backpack, Technician’s Tool Bag, Open-Top Toolbox, Contractor’s Closed-Top Tool Bag, BigMouth Tote Bag and Electrical/HVAC Tool Carrier.
•Durable 1680D ballistic polyester with extra webbing around pockets and handles •Molded bottom base attached with double-stitched tape binding •Include a padded shoulder strap, ergonomic carrying handles, large metal zipper pulls, heavy-duty hardware and multiple pocket arrangements •Different configurations of sizes, zippered compartments and pockets depending on trade-specific needs www.ForConstructionPros.com/21603312
HOW TO USE DRONES TO IMPROVE CONSTRUCTION SAFETY
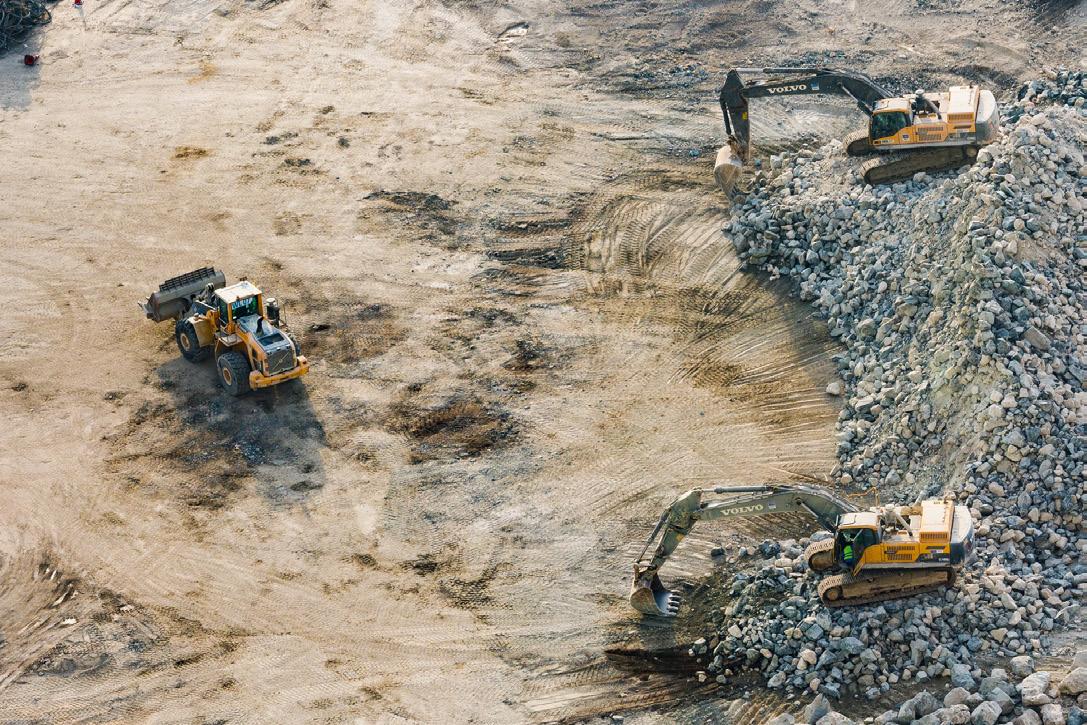
Contractors are leveraging drone technologies to minimize risk and keep workers safe, which involves keeping them away from worksites as much as possible. www.ForConstructionPros.com/21627001
Statement of Ownership, Management, and Circulation
(Requester Publications Only)
PODCAST: WHAT IS A DIGITAL TWIN IN CONSTRUCTION?
Dave Burns, vice president of project delivery and emerging tech at McCarthy Building Companies, talks about digital twins and how they work in the construction industry.
LISTEN IN: www.ForConstructionPros.com/21648101
1. Publication Title Equipment Today
4. Issue Frequency
1. Publication Title1. Publication TitleJan, Feb, Mar, Apr, May, Jun, Equipment TodayEquipment TodayJul, Aug, Sep, Oct, Nov, Dec
2. Publication Number
3. Filing Date
Statement of Ownership, Management, and CirculationStatement of Ownership, Management, and Circulation 369-290 September 15, 2021
5. Number of Issues Published Annually (Requester Publications Only)(Requester Publications Only)
6. Annual Subscription Price
2. Publication Number2. Publication Number 12 369-290 369-290
3. Filing Date3. Filing DateFree to Qualified September 15, 2021September 15, 2021Subscribers ADVERTISER INDEX
4. Issue Frequency 5. Number of Issues Published Annually4. Issue Frequency 5. Number of Issues Published Annually7. Complete Mailing Address of Known Office of Publication (Street, City, County, State, and Zip+4)
Jan, Feb, Mar, Apr, May, Jun, Jan, Feb, Mar, Apr, May, Jun, AC Business Media Jul, Aug, Sep, Oct, Nov, DecJul, Aug, Sep, Oct, Nov, Dec201 North Main St., 5th Floor Fort Atkinson, WI 53538-1807 12 12
7. Complete Mailing Address of Known Office of Publication (Street, City, County, State, and Zip+4)7. Complete Mailing Address of Known Office of Publication (Street, City, County, State, and Zip+4) 6. Annual Subscription Price6. Annual Subscription Price Contact Person
Free to Qualified Free to Qualified Angela Franks SubscribersSubscribers
Telephone
Contact PersonContact Person(920) 542-1259
AC Business MediaAC Business Media
201 North Main St., 5th Floor201 North Main St., 5th Floor8. Complete Mailing Address of Headquarters or General Business Office of Publisher Fort Atkinson, WI 53538-1807Fort Atkinson, WI 53538-1807AC Business Media, 201 North Main St., 5th Floor, Fort Atkinson, WI 53538-1807
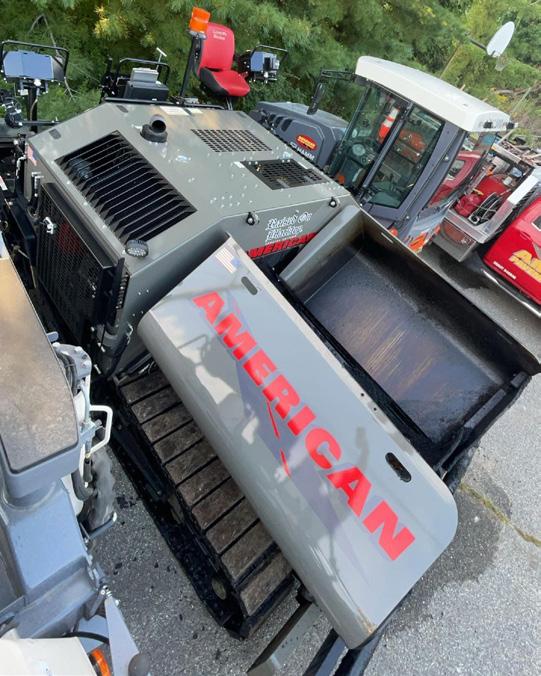
9. Full Names and Complete Mailing Addresses of Publisher, Editor, and Managing Editor 8. Complete Mailing Address of Headquarters or General Business Office of Publisher8. Complete Mailing Address of Headquarters or General Business Office of Publisher Publisher (Name and Complete Mailing Address)
AC Business Media, 201 North Main St., 5th Floor, Fort Atkinson, WI 53538-1807AC Business Media, 201 North Main St., 5th Floor, Fort Atkinson, WI 53538-1807 Sean Dunphy, Group Publisher 201 North Main St., 5th Floor 9. Full Names and Complete Mailing Addresses of Publisher, Editor, and Managing Editor9. Full Names and Complete Mailing Addresses of Publisher, Editor, and Managing Editor Fort Atkinson, WI 53538-1807
Publisher (Name and Complete Mailing Address)Publisher (Name and Complete Mailing Address)Editor (Name and Complete Mailing Address)
Sean Dunphy, Group PublisherSean Dunphy, Group Publisher Becky Schultz, Editor 201 North Main St., 5th Floor201 North Main St., 5th Floor201 North Main St., 5th Floor Fort Atkinson, WI 53538-1807Fort Atkinson, WI 53538-1807Fort Atkinson, WI 53538-1807
Editor (Name and Complete Mailing Address)Editor (Name and Complete Mailing Address)Managing Editor (Name and Complete Mailing Address)
Angela FranksAngela Franks
Telephone
Telephone
(920) 542-1259(920) 542-1259
Becky Schultz, EditorBecky Schultz, Editor VIDEO: GET AN 201 North Main St., 5th Floor Fort Atkinson, WI 53538-1807 Managing Editor (Name and Complete Mailing Address) 201 North Main St., 5th Floor Fort Atkinson, WI 53538-1807 Managing Editor (Name and Complete Mailing Address) 10. Owner (Do not leave blank. If the publication is owned by a corporation, give the name and address of the corporation immediately followed by the INSIDE LOOK AT THE names and addresses of all stockholders owning or holding 1 percent or more of the total amount of stock . If not owned by a corporation, give the names and addresses of the individual owners. If owned by a partnership or other unincorporated firm, give its name and address as well as those of each individual owner. If the publication is published by a nonprofit organization, give its name and address.) 10. Owner (Do not leave blank. If the publication is owned by a corporation, give the name and address of the corporation immediately followed by the names and addresses of all stockholders owning or holding 1 percent or more of the total amount of stock . If not owned by a corporation, give the names and addresses of the individual owners. If owned by a partnership or other unincorporated firm, give its name and address as well as those of 10. Owner (Do not leave blank. If the publication is owned by a corporation, give the name and address of the corporation immediately followed by the names and addresses of all stockholders owning or holding 1 percent or more of the total amount of stock . If not owned by a corporation, give the names and addresses of the individual owners. If owned by a partnership or other unincorporated firm, give its name and address as well as those of Full Name Complete Mailing Address ACBM, LLC, Ron Spink, CEO 201 North Main St., 5th Floor, Fort Atkinson WI 53538-1807RAISED ON BLACKTOP ASPHALT PAVER each individual owner. If the publication is published by a nonprofit organization, give its name and address.) Full Name Complete Mailing Address ACBM, LLC, Ron Spink, CEO 201 North Main St., 5th Floor, Fort Atkinson WI 53538-1807 each individual owner. If the publication is published by a nonprofit organization, give its name and address.) Full Name Complete Mailing Address ACBM, LLC, Ron Spink, CEO 201 North Main St., 5th Floor, Fort Atkinson WI 53538-1807 11. Known Bondholders, Mortgagees, and Other Security Holders Owning or Holding 1 Percent or more of Total Amount of Bonds, Mortgages or Other Securities. If none, check here. None
Full Name Complete Mailing Address
With a Kubota turbocharged diesel engine, a 9-ton hopper 11. Known Bondholders, Mortgagees, and Other Security Holders Owning or Holding 1 Percent or more of Total Amount of Bonds, Mortgages or Other Securities. If none, check here. None 11. Known Bondholders, Mortgagees, and Other Security Holders Owning or Holding 1 Percent or more of Total Amount of Bonds, Mortgages or Other Securities. If none, check here. None and its exclusive gray paint job, Full Name Full Name Complete Mailing Address Complete Mailing Address the Leeboy 8520B Raised on 12. Tax Status (For completion by nonprofit organizations authorized to mail at nonprofit rates) . (Check One) Blacktop Edition asphalt paver is The purpose, function, and nonprofit status of this organization and the exempt status for federal income tax purposes: Has Not Changed During Preceding 12 Months one you don’t want to miss. 12. Tax Status (For completion by nonprofit organizations authorized to mail at nonprofit rates) . (Check One)13. Publication Title 14. Issue Date for Circulation Data Below12. Tax Status (For completion by nonprofit organizations authorized to mail at nonprofit rates) . (Check One)13. Publication Title 14. Issue Date for Circulation Data Below Has Changed During Preceding 12 Months PS Form 3526-R Facsimile, July 2014 The purpose, function, and nonprofit status of this organization and the exempt status for federal income Equipment Today The purpose, function, and nonprofit status of this organization and the exempt status for federal income Equipment Today September 2021September 2021 SEE VIDEO: tax purposes: 15. Extent and Nature of Circulation tax purposes: 15. Extent and Nature of Circulation Has Not Changed During Preceding 12 Months Has Changed During Preceding 12 Months Average No. Copies No. Copies of Single Has Not Changed During Preceding 12 Months Has Changed During Preceding 12 Months Average No. Copies No. Copies of Single No. Copies of Single www.ForConstructionPros. PS Form 3526-R Facsimile, July 2014PS Form 3526-R Facsimile, July 2014 Each Issue During Issue Published Preceding 12 Months Nearest to Filing Date Each Issue During Issue Published Preceding 12 Months Nearest to Filing Date Each Issue During Issue Published Preceding 12 Months Nearest to Filing Date com/21648026 a. Total Number of Copies (net press run)a. Total Number of Copies (net press run) 75,580 75,580 68,342 68,342 68,342
WHAT YOU’LL FIND ONLINE
➊ All the latest news impacting the construction industry ➋ Exclusive articles on equipment, business management, safety and more ➌ New Product Directory hosting over 19,000 products ➍ Video Network with thousands of videos covering equipment, industry trends, applications and more ➎ Podcasts on equipment, technology, trending topics and more ➏ Profit Matters channel to help build profits in your construction business ➐ Blogs by the industry’s leading construction editors ➑ Current issues from five of the nation’s top construction industry publications ➒ AND MUCH MORE...
Outside County Paid/Requested Mail Subscriptions stated onOutside County Paid/Requested Mail Subscriptions stated on
(1) PS Form 3541. (Include direct written request from recipient, telemarketing and (1) PS Form 3541. (Include direct written request from recipient, telemarketing and b. Legitimateb. Legitimate
Internet requests from recipient, paid subscriptions including nominal rate subscriptions, Internet requests from recipient, paid subscriptions including nominal rate subscriptions,
Paid and/orPaid and/or
employer requests, advertiser's proof copies, and exchange copies.) employer requests, advertiser's proof copies, and exchange copies.) Requested (2)Requested In-County Paid/Requested Mail Subscriptions stated on PS (2) In-County Paid/Requested Mail Subscriptions stated on PSIn-County Paid/Requested Mail Subscriptions stated on PS
DistributionDistribution Form 3451. (Include direct written request from recipient, telemarketing and internetForm 3451. (Include direct written request from recipient, telemarketing and internet (By Mail (By Mail and Outsideand Outside
requests from recipient, paid subscriptions including nominal rate subscriptions,requests from recipient, paid subscriptions including nominal rate subscriptions, employer requests, advertiser's proof copies, and exchange copies.)employer requests, advertiser's proof copies, and exchange copies.) the Mail) the Mail)(3) Sales Through Dealers & Carriers, Street Vendors, Counter (3) Sales Through Dealers & Carriers, Street Vendors, CounterSales Through Dealers & Carriers, Street Vendors, Counter
Sales, and Other Paid or Requested distribution Outside USPS.Sales, and Other Paid or Requested distribution Outside USPS. (4) Requested Copies Distributed by Other Mail Classes (4) Requested Copies Distributed by Other Mail ClassesRequested Copies Distributed by Other Mail Classes
Through the USPS. (e.g. first-Class Mail)Through the USPS. (e.g. first-Class Mail)
c. Total Paid and/or Requested Circulationc. Total Paid and/or Requested Circulation [Sum of 15b(1), (2), (3), (4)] [Sum of 15b(1), (2), (3), (4)] (1) Outside County Nonrequested Copies stated on PS form 3541. (1) Outside County Nonrequested Copies stated on PS form 3541.Outside County Nonrequested Copies stated on PS form 3541.
(include sample copies, requests over 3 years old, requests induced by a premium,(include sample copies, requests over 3 years old, requests induced by a premium, d. Nonrequested bulk sales and requests including association requests, names obtained fromd. Nonrequested bulk sales and requests including association requests, names obtained from DistributionDistribution
business directories, lists, and other sources)business directories, lists, and other sources) (By Mail (By Mail (2) In-County Nonrequested Copies stated on PS form 3541. (2) In-County Nonrequested Copies stated on PS form 3541.In-County Nonrequested Copies stated on PS form 3541. and Outsideand Outside (include sample copies, requests over 3 years old, requests induced by a premium,(include sample copies, requests over 3 years old, requests induced by a premium, the Mail) the Mail) bulk sales and requests including association requests, names obtained frombulk sales and requests including association requests, names obtained from business directories, lists, and other sources)business directories, lists, and other sources)
(3) Nonrequested Copies Distributed Through the USPS by (3) Nonrequested Copies Distributed Through the USPS by Nonrequested Copies Distributed Through the USPS by
Other Classes of Mail.(e.g. First-Class Mail, nonrequestor copies mailed in Other Classes of Mail.(e.g. First-Class Mail, nonrequestor copies mailed in excess of 10% Limit mailed at Standard Mail or Package Services Rates)excess of 10% Limit mailed at Standard Mail or Package Services Rates)
(4) Nonrequested Copies Distributed Outside the Mail (4) Nonrequested Copies Distributed Outside the MailNonrequested Copies Distributed Outside the Mail
(include pickup stands, trade shows, showrooms, and other sources)(include pickup stands, trade shows, showrooms, and other sources)
e. Total Nonrequested Distribution (Sum of 15d (1), (2), and (3))e. Total Nonrequested Distribution (Sum of 15d (1), (2), and (3))
f. Total Distribution (Sum of 15c and e)f. Total Distribution (Sum of 15c and e)
g. Copies Not Distributedg. Copies Not Distributed
68,460 68,460 68,460
0 0 0
190 190 190
0 0 0
68,650 68,650 68,650
6,140 6,140 6,140
0 0 0
0 0 0
31 31 31
6,171 6,171 6,171
74,821 74,821 74,821
759 759 60,221 60,221 60,221
0 0 0
165 165 165
0 0 0
60,386 60,386 60,386
6,993 6,993 6,993
0 0 0
0 0 0
154 154 154
7,147 7,147 7,147
67,533 67,533 67,533
809 809 809
h. Total (Sum of 15f and g)h. Total (Sum of 15f and g)
75,580 75,580 75,580 68,342 68,342 68,342
i. Percent Paid and/or Requested Circulation (15c / 15f x 100) *if you are claiming electronic copies, go to line 16 on page 3. If you are not claiming electronic copies, skip to line 17 on page 3.
91.8% 89.4% Statement of Ownership, Management, and Circulation i. Percent Paid and/or Requested Circulation (15c / 15f x 100) *if you are claiming electronic copies, go to line 16 on page 3. If you are not claiming electronic copies, skip to line 17 on page 3.
91.8% 91.8% 89.4% 89.4%
PS Form 3526 -R Facsimile, July 2014PS Form 3526 -R Facsimile, July 2014 (Requester Publications Only)
Average No. Copies No. Copies of Single
16. Electronic Copy Circulation
Each Issue During Issue Published
Preceding 12 Months Nearest to Filing Date
a. Requested Electronic and Paid Electronic Copies b. Total Requested and Paid Print Copies (Line 15C) + Requested/Paid Electronic Copies (Line 16a) c. Total Copy Distribution (Line 15F) + Requested/Paid Electronic Copies (Line 16a) d. Percent Paid and/or Requested Circulation (Both Print & Electronic Copies) (16b divided by 16c X 100)
2,448 71,098 77,269 92.0%
9,797 70,183 77,330 90.8%
x I certify that 50% of all my distributed copies (electronic & print) are legitimate requests or paid copies
17. Publication of Statement of Ownership for a Requester Publication is required and will be printed in the October issue of this publication. 18. Signature and Title of Editor, Publisher, Business Manager, or Owner Date
ADVERTISER PAGE
Bobcat.........................................................21, 52 The Caldwell Group .........................................46 ChevronTexaco ................................................2-3 Dominion Equipment Parts LLC......................22 Doosan Infracore...............................................13 Eager Beaver Trailers .........................................51 Fecon LLC........................................................17 IGNITE Construction Summit ........................47 Iron Capital Group .............................................6 JCB Inc.............................................................20 JLG Industries Inc.............................................23 John Deere Construction Equipment..................5 LDJ Manufacturing ..........................................35 Milwaukee Electric Tool Company ..............26-27 Premier Manufacturing Co. ..............................34 Schweiss Doors .................................................49 Uline.................................................................33 Wacker Neuson Corp..........................................7
This index is provided as a service. The publisher does not assume liability for errors or omissions.
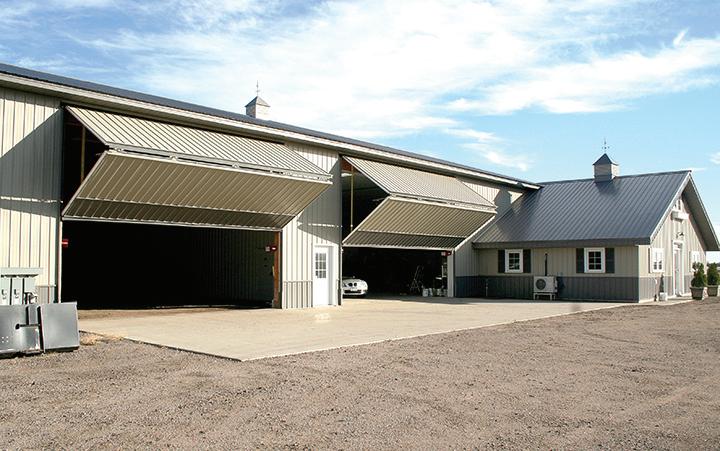
How to Max Out Your Company’s Tax Benefits
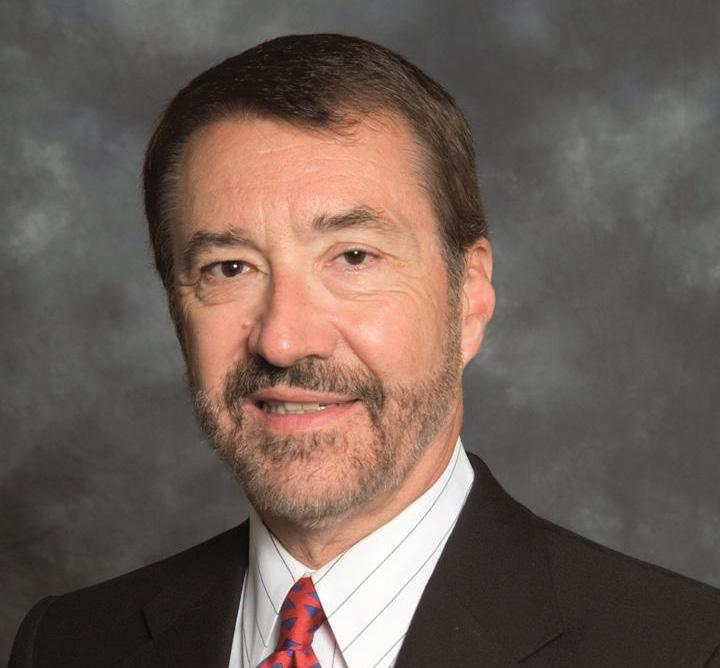
How the proposed tax bill may impact tax risks, plus two options that could provide major tax deferrals.
Garry Bartecki is the managing member of GB Financial Services LLP and a consultant to the Independent Equipment Dealers Association. He can be reached at (708) 347-9109 or gbartecki@comcast.net.
While I planned to continue the own vs. rent commentary this month (and plan to do so in the near future), with the release of President Biden’s proposed tax bill, I believe now is the time to discuss the changes it contains so you have time to plan out the rest of this tax year, as well as 2022 and 2023.
To keep you from chasing around trying to find the tax proposals, you can download a review of the bill at www.ForConstructionPros. com/21722633 that covers just about everything you need to know. It was compiled by Steve Pierson, a CPA at Seldon Fox (www.seldenfox.com), who has been working with me for at least 20 years and specializes in the issues I normally come across with dealers, rental companies and contractors. He can deal with just about any tax issue that comes up, especially those related to equipment and other types of depreciable assets.
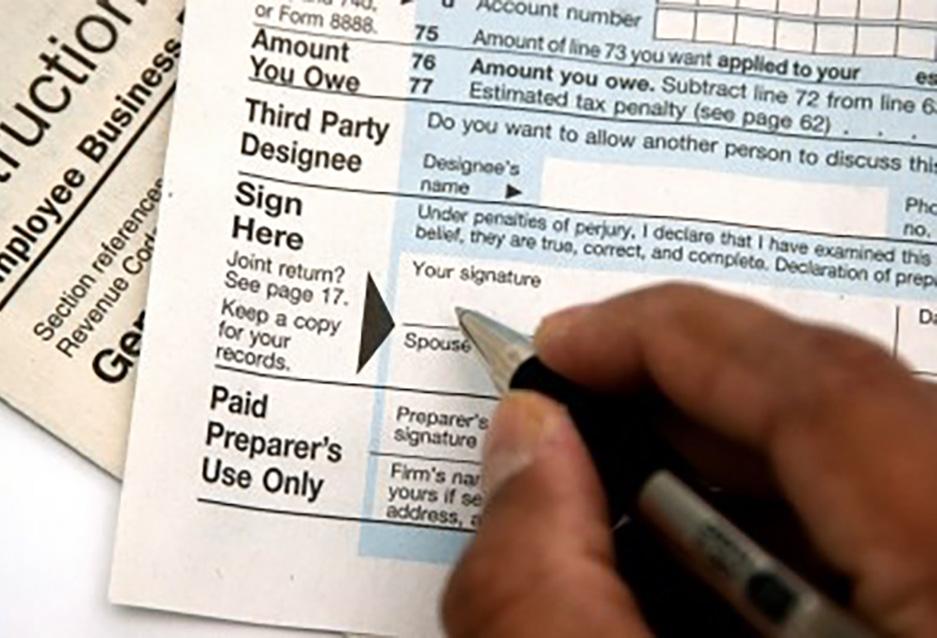
What you will find in the memo is a discussion about how Bonus Depreciation and Sec 179 will change and the impact to expect for 2022-27. Bonus Depreciation will be phased out by 20% per year starting with 2023, going from 100% deduction to 80% deduction and so on. In other words, the tax benefits related to new and used equipment purchases will decline and thus raise taxable income compared to what you can do today.
This change in the deprecation deduction increases your risk of higher tax bills and thus a use of cash you were able to avoid with the 100% Bonus deduction. This new risk is a result of owning assets with a zero tax basis (the cost was deducted) which, when you sell them, will be 100% taxable at the new proposed higher income tax rate. Up to this point, many contractors were able to mitigate this tax issue because they had Bonus Depreciation to cover taxable profits.
Read the review for more information.
TAKE ADVANTAGE OF TAX DEFERRALS
tax deferrals as well as dollars from the government similar to the PPP loan programs. They include the Employee Retention Credit (ERC), and Cash Basis accounting available for contractors. (Steve is also quite conversant about these topics in case help is needed.)
If you qualify for the ERC, you can receive a refund of a percentage of the employment taxes paid for each quarter in 2020-2021. In order to qualify for 2020, your total sales for the quarter had to be 50% less than the same quarter in 2019, which was a little tough to do. But with a change to 20% for 2021, your chances of having a positive outcome increase when comparing each quarter of 2021 against the same quarters of 2019.
For 2020, the max credit per employee under the ERC was $5,000. For 2021, it is $7,000 per employee. If you have 100 or fewer employees, all wages are eligible. ERC is taxable but the overall result is still very positive. Steve’s partner Paul Rozek knows this area very well and can help guide you through the process.
Cash Basis accounting really helps conserve cash because taxable income is based on funds received vs. accrued income where your funds are sitting in accounts receivable (AR). So, if you have a good year and wind up with a significant AR balance, you could wind up straining cash because collections are slow. On the other hand, if your AR and work in progress (WIP) go down, you may have a higher taxable income on a Cash Basis compared to what it would have been on the accrual basis. In short, Cash Basis accounting is a deferral of tax due that could reverse if AR and WIP balances fall compared to the prior tax year.
Both of these tax-related concepts should be reviewed as a way to build cash and reserves to mitigate any pandemic or economic pitfalls that may come your way.
REVIEW YOUR TAX POSITION
Steve, Paul and I and our colleagues make it a point to meet in the fall with clients to review the tax planning from the prior year and how that turned out, and then estimate the tax position for the current year and the related tax requirement. This gives us three to four months to work out ways to reduce the tax burden.
This takes a little work but keeps management informed about both former and current tax planning results. Management then knows what to expect for a tax liability and can gather the cash to cover the amount due.
There is one other tax program I want to review with you, as well, and will do that next month. These topics will also be covered at the Ignite Construction Summit program in November. ET
Interested in learning more on financials? Attend the Ignite Construction Summit — the construction industry’s only conference and networking event for construction business owners and high-level managers — November 3 to 5, 2021, to hear from Garry Bartecki on these issues and more!
201 N. Main Street, 5th Floor Fort Atkinson, Wisconsin 53538 (800) 538-5544 www.ACBusinessMedia.com
Publication Staff
Publisher SEAN DUNPHY, sdunphy@ACBusinessMedia.com Editor BECKY SCHULTZ, bschultz@ACBusinessMedia.com Senior Field Editor CURT BENNINK, cbennink@ACBusinessMedia.com Contributing Writers GARRY BARTECKI, JESSICA LOMBARDO, ALEXIS SHEPRAK, VICKI SPEED, GIGI WOOD Art Director DAVE HAGLUND Senior Production Manager CINDY RUSCH Audience Development Manager ANGELA FRANKS Advertising Sales (800) 538-5544
SEAN DUNPHY; NIKKI LAWSON; KRIS FLITCROFT; TADASHI SOMA
ForConstructionPros.com
Editor-in-Chief WAYNE GRAYSON Editor LARRY STEWART
AC Business Media
Chief Executive Officer.............RON SPINK Chief Financial Officer..............JOANN BREUCHEL Chief Digital Officer .................KRIS HEINEMAN Chief Revenue Officer ..............AMY SCHWANDT VP Audience Development........RONDA HUGHES Director, Demand Generation & Education ............................JIM BAGAN Dir. of Digital Operations & IT ..NICK RAETHER Group Content Director............JON MINNICK
Change of Address & Subscriptions
PO Box 3605, Northbrook, IL 60065-3605, Phone: (877) 201-3915 • Fax: (847) 291-4816 circ.EquipmentToday@omeda.com
List Rental
Bart Piccirillo, Sr. Account Manager, Data Axle Phone: (518) 339-4511 bart.piccirillo@data-axle.com
Reprints
Reprints — For reprints and licensing please contact Sean Dunphy at 920-542-1252 sdunphy@acbusinessmedia.com
Published and copyrighted 2021 by AC Business Media Equipment Today makes every effort to report manufacturers’ product news accurately, but is not responsible for validity of news claims. All rights reserved. No part of this publication may be reproduced or transmitted in any form or by any means, electronic or mechanical, including photocopy, recording or any information storage or retrieval system, without written permission from the publisher. SUBSCRIPTION POLICY: Individual subscriptions are available without charge in the U.S. and Canada to management, engineering, supervisory, equipment maintenance and other personnel who have buying influence in the construction equipment industry. Subscribe online at www.ForConstructionPros.com. Publisher reserves the right to reject non-qualified subscribers.
One year subscription to non-qualified individuals: U.S. $50; Canada/Mexico $70; all other countries $100 (payable in U.S. funds, drawn on U.S. bank). Single copies available (prepaid only) $10.00 each (U.S., Canada & Mexico), $15.00 each (International). For change of address or subscription information call (847) 559-7598 or fax (847) 291-4816. Equipment Today (USPS 369-290, ISSN 0891-141X) is published is published 12x with issues of January, February, March, April, May, June, July, August, September, October, November and December by AC Business Media, 201 N. Main Street, 5th Fl., Fort Atkinson, WI 53538. Periodicals postage paid at Fort Atkinson, WI, and additional entry offices. POSTMASTER: Please send change of address to Equipment Today, PO Box 3605, Northbrook, IL 60065-3605. Printed in the USA.
Canada Post PM40612608. Return Undeliverable Canadian Addresses to: Equipment Today, PO Box 25542, London, ON N6C 6B2.
Vol. 57 No. 10 October 2021