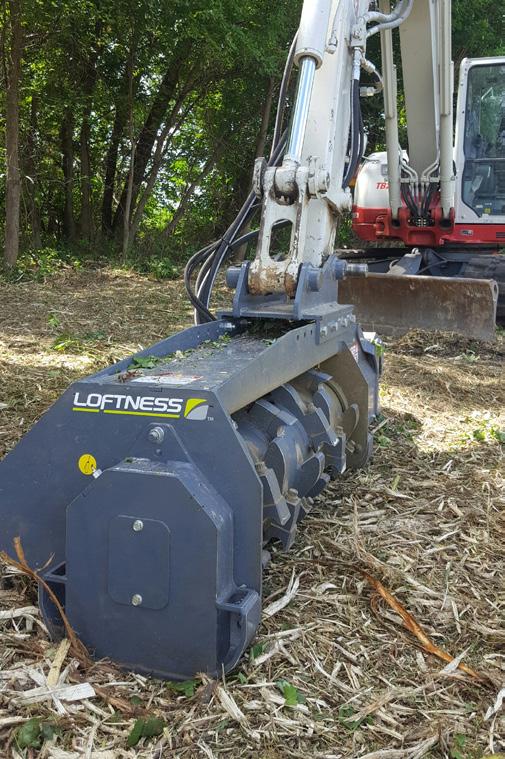
22 minute read
Excavator Attachments
Loftness Battle Ax Excavator Mulching Attachment
The Battle Ax mulching attachment for 4.5- to 20-ton excavators features a rotor with unique depth gauges to maximize the productivity of both knives and carbide cutting teeth.
•Two-stage cutting chamber capable of processing material more thoroughly by cutting material twice •Powerful direct drive with a variable displacement piston motor capable of turning the rotor between 1,600 and 2,500 rpm •Staggered spiral tooth pattern with single-bolt tooth mounting for easily reversing or replacing cutting teeth on the jobsite •Adjustable skid shoes for cutting up to 1.5 in. below grade
Read more at: https://eqtoday.co/t8kfv3
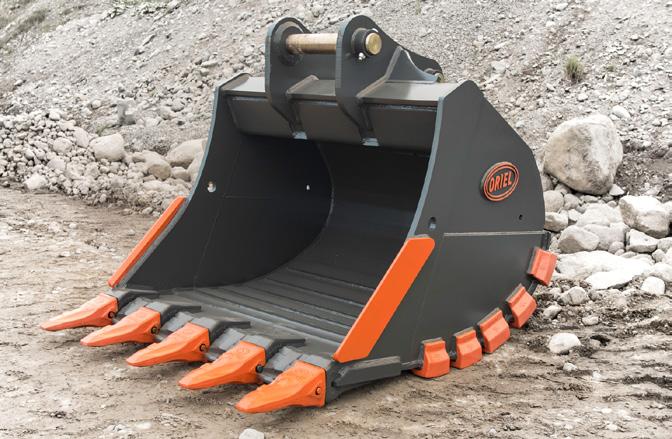
Oriel Attachments Heavy-duty Excavator Buckets
These buckets are built for heavy-duty applications with a main body built using AR 450 wear-resistant steel in all critical areas.
•Designed to maximize capacity and reduce drag, extending the life of the bucket •Folded top section gives greater structural strength and allows a greater opening for ease of loading and unloading material •Available in a range of widths and capacities for excavators from 4,500 to 112,000 lbs. •Manufactured to the relevant safety standards with high-strength steels for quality and performance Read more at: https://eqtoday.co/2qf5fm
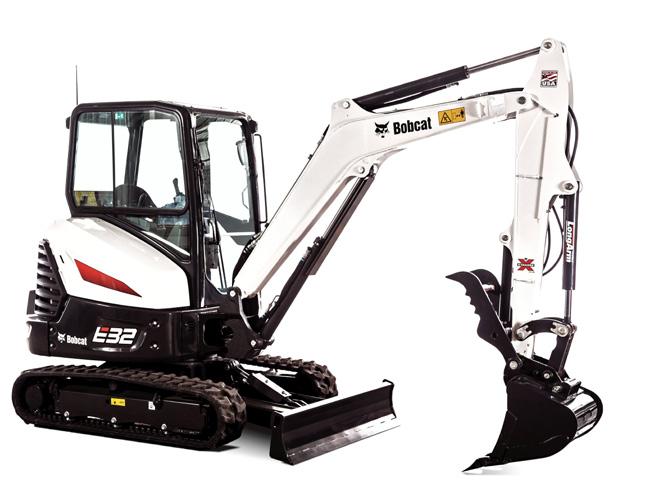
Bobcat Grading and Trenching Buckets
Redesigned trenching buckets and new grading buckets are available for Bobcat E26 through E85 compact excavators.
•Grading buckets available in 36-, 48- and 60-in. widths and equipped with waffle plates to add extra strength and rigidity to the bottom •Trenching buckets come in 12-, 16-, 18-, 20-, 24-, 30- and 36-in. widths with replaceable cutting edge or toothed versions available •Optimized to fit the standard clamp and optional Pro Clamp System •Easily interchanged using the X-Change attachment mounting system Read more at: https://eqtoday.co/4dh98b
Caterpillar H190 S and H215S Performance Series Hammers
The H190 S and H215S fit in the 13,000- and 18,000-ft.-lb. impact energy class and deliver 370 to 530 and 300 to 520 bpm, respectively.
•Switchable power mode from high frequency/low power to low frequency/high power to fine tune power to the material being broken •Buffering material dampens vibration feedback to the carrier •H190 S sized for use on 349 through 374 excavators and the larger H215 S is designed for the 374 and 395 •Auto Stop instantly terminates hammering when tool breaks through material, preventing damage to the carrier and hammer
Read more at: https://eqtoday.co/dahtj2
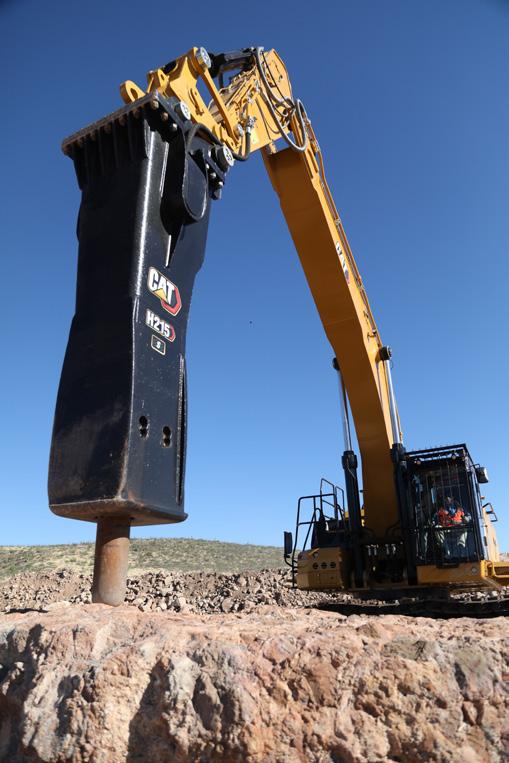
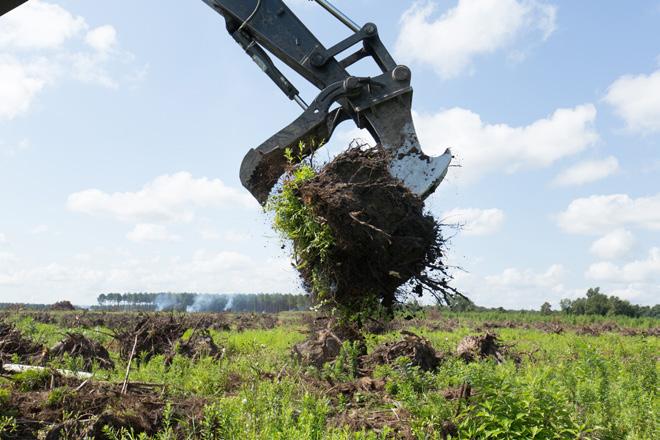
Solesbee’s Excavator Stump Puller
The excavator Stump Puller ("Stumper") fits 15- to 40-ton excavators and is designed for efficient stump removal and land clearing.
•High-strength alloy steel and replaceable wear tips for extended service life •Can increase production by as much as 30% percent •Two shanks cut through roots to enable removal with minimal soil disruption •Shank’s curved design increases breakout force for slicing through tough surfaces when extracting forestry material •Can be paired with the company's excavator thumbs and is compatible with Solesbee’s Quick Coupler Read more at: https://eqtoday.co/zyhyzd
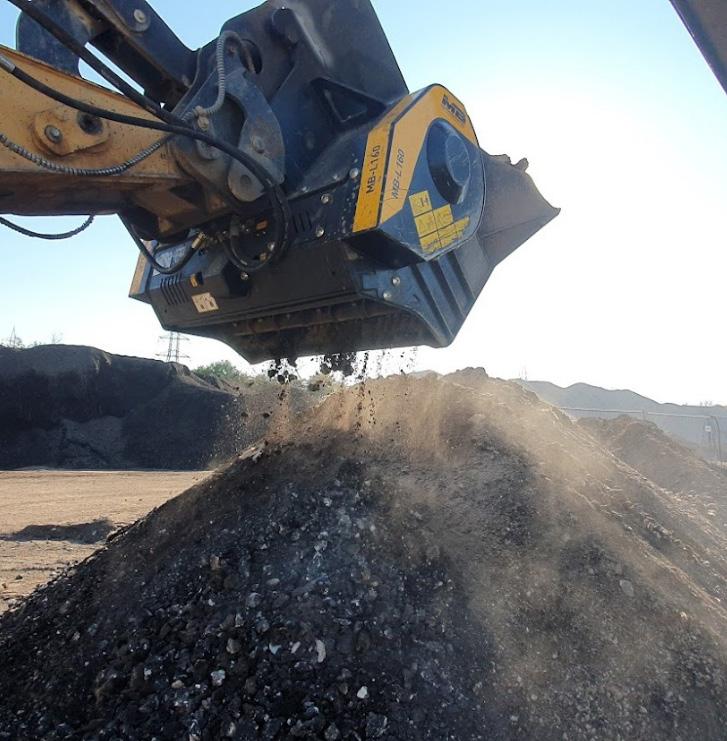
MB America MB-L 160
Designed for a skid steer or backhoe, the MB-L 160 model offers a production rate up to 25 tons per hour.
•Jaw Crusher •Separate concrete from rebar •Adjustable output from 2 to 0.5 in. minus •Crush material from concrete to granite •Weight: 3,000-lbs. •Goes onto a 3.8 ton excavator •Low maintenance
Read more at: https://eqtoday.co/4ycqth
Werk-Brau PowerGrip Bucket
This multi-purpose bucket has 120° of enhanced clamping force that is consistent throughout the jaw's full range of motion. Its design includes an enclosed rotary actuator hinge in a cross-tube. There are no exposed cylinders or other external moving parts. The unit is available in various sizes and widths to fit up to 50,000-lb. machines with customization options available. Two different cutting edges allow the operator to switch between ditching and digging without changing buckets. High-strength steel is used throughout the weldment and hardened, greaseable bushings are utilized at all pivot points. Tapered side plates reduce wear on bucket sides and allow easier dumping. A variety of tooth options or bolt-on cutting edge are available.
Read more at: https://eqtoday.co/58gzeb
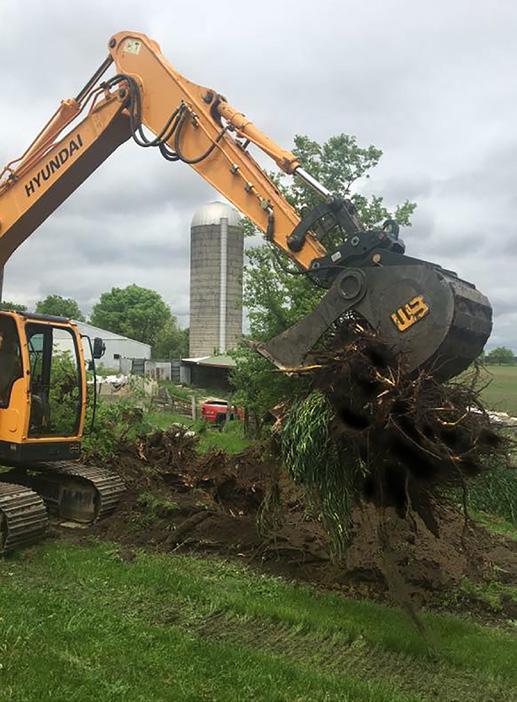
Epiroc CB 5500 and CB 7500 Concrete Busters
The CB Concrete Busters have wide jaw openings and high cracking forces suited for demolishing thick foundation walls and cracking girders and heavy concrete at extreme heights.
•CB 5500 and CB 7500 suited for carriers in the 50 to 85 tons weight class and for use with high reach or long front carriers. •Two powerful hydraulic cylinders deliver virtually continuous closing force •Offer cracking forces of up to 190 tons depending on the model •Two moving jaws with cutting blades •360° endless hydraulic rotation Read more at: https://eqtoday.co/548e3c
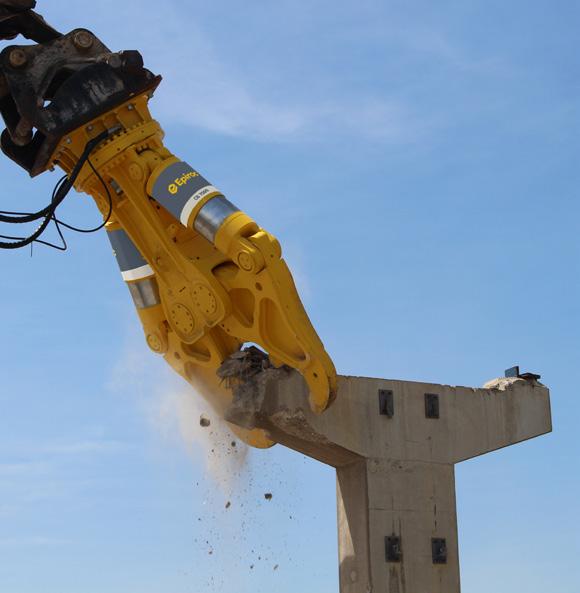
The diamond grinding operation.
Courtesy Kevin Harvill, City of Baytown, TX
CASE STUDY:
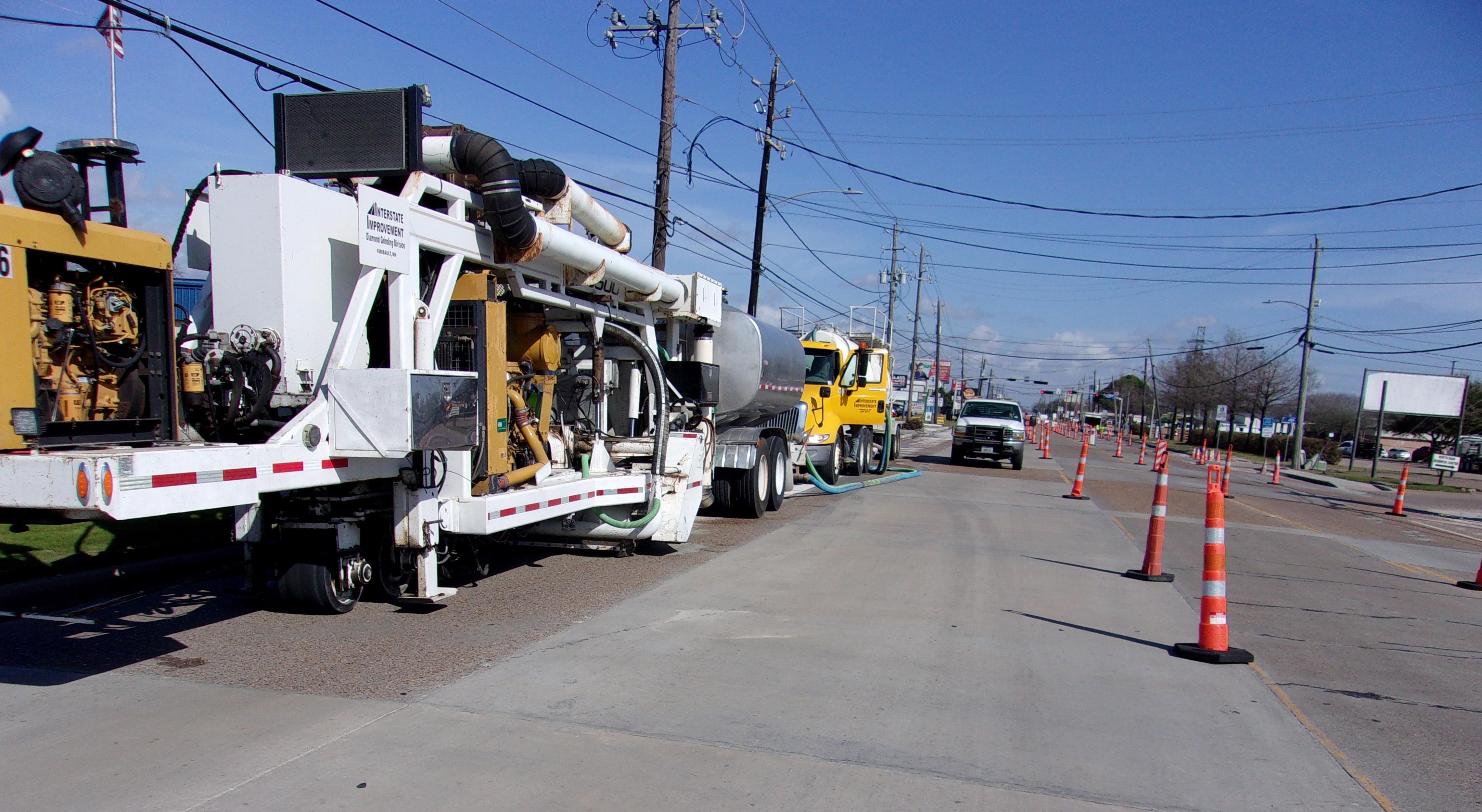
How Concrete Pavement Preservation Saved $10 Million in Road Repairs
Concrete roads are durable and long-lasting, requiring only targeted rehabilitation and diamond grinding every 25 years or so. With repairs on concrete roads being performed infrequently, however, cities may face a learning curve when it comes to understanding the available repair tools.
When the City of Baytown, Texas, faced ride-quality issues on its North Main Street in 2015, the Public Works and Engineering Department needed to find a cost-effective repair strategy that would perform well, considering the unique properties of the street’s pavement. By working with educational institutions and industry experts, the department identified challenges and came up with a solution that resulted in a project that was dramatically lower in cost—by 80%—than initial estimates.
North Main Street is a concrete road that was installed in the 1980s. It serves as a major right-of-way in the Houstonarea City of Baytown, with two lanes in each direction, as well as a turn lane. It’s also a truck route that serves nearby industrial areas.
The aggregate used in the original construction was river rock, an exceptionally hard material. Measurements from hardness tests on the North Main Street aggregates were an 8 on the Mohs scale of mineral hardness (diamonds measure at 10). Some of the ride-quality issues that had developed on the roadway were due to the wearing away of the cement paste layer and consequent exposure of the rock.
On the section of street in need of repair, located between Baker Road to the north and State Highway 146 to the south, pavement condition index (PCI) measurements averaged 43, with four sections being in the low 20s to mid-30s. The PCI scale is based on a 100-point range, with 0 representing the worst conditions and 100 representing the best.
Reconstruction was considered, but with an estimated cost of $12-13 million, the city didn’t have adequate funding for a project of that scope. Through word of mouth, the Public Works and Engineering Department learned that concrete pavement preservation (CPP) was an option.
MEETING WITH EXPERTS
program, one of the first steps was to meet with experts to learn more. The Public Works and Engineering Department consulted with states who had experience with CPP, including Minnesota and Kansas.

The Public Works team took online training classes through Iowa State University, whose National Concrete Pavement Technology Center (CP Tech Center) offers courses delivered via webinar, video and other channels (cptechcenter. org/webinars-and-videos). The department also worked with the International Grooving & Grinding Association (IGGA), a trade association that serves as a technical resource for pavement preservation and restoration.
The relationships the department formed were maintained throughout the North Main Street project and guided the CPP process from its earliest phases through to project completion. During project planning, IGGA experts and Baytown officials conducted an in-person inspection of the roadway, confirming that the pavement showed adequate structural integrity and was a good candidate for CPP. They then worked together to develop specifications, gleaning insights from the states with detailed specifications already in place, and collaborated during the contractor search and bidding processes. When Interstate Improvement (a highway
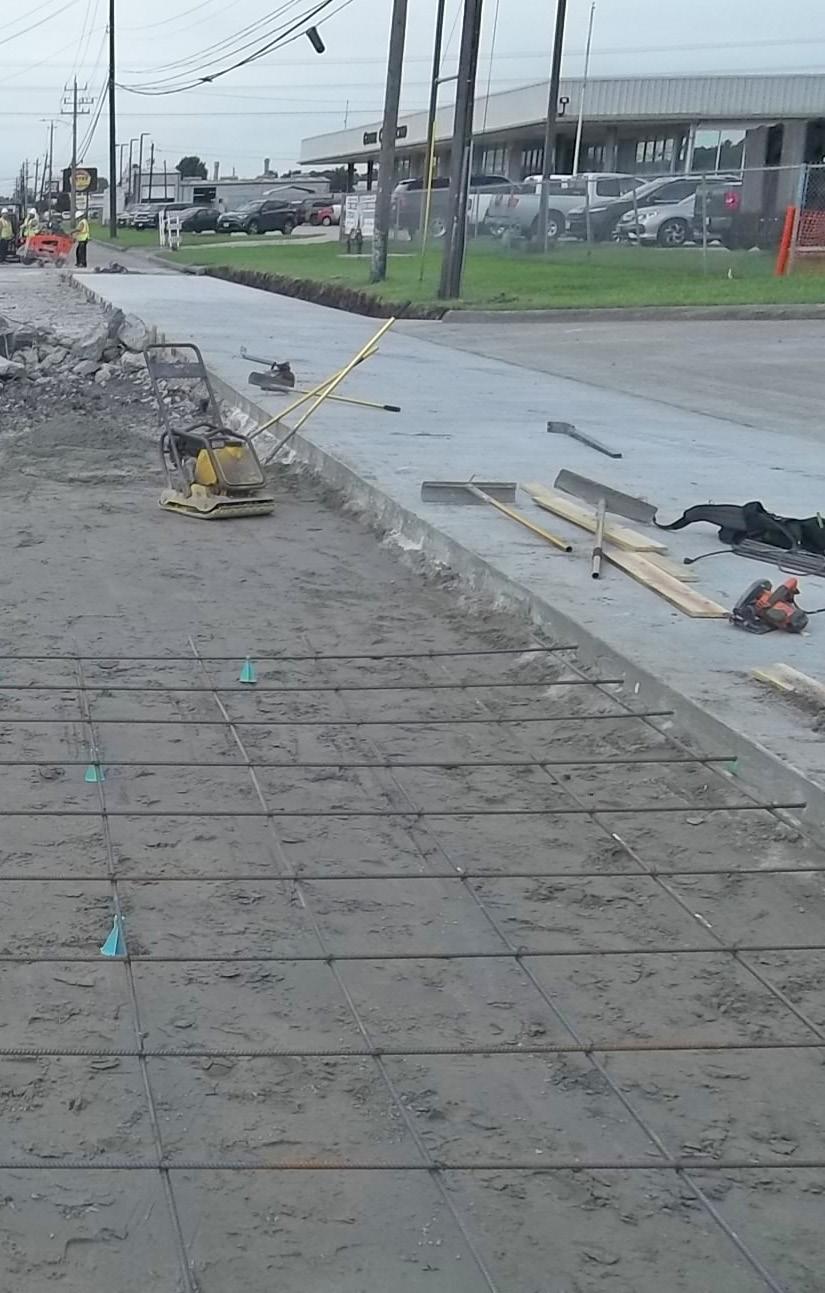
contractor based in Faribault, Minn. who performs work nationwide) was selected to perform the CPP, that company also became involved at an early stage, with project manager Nathan Sirek visiting the city and consulting with department officials prior to the start of work. Together with Interstate Improvement and with the IGGA, the city identified the proper repair procedures for individual distressed areas.
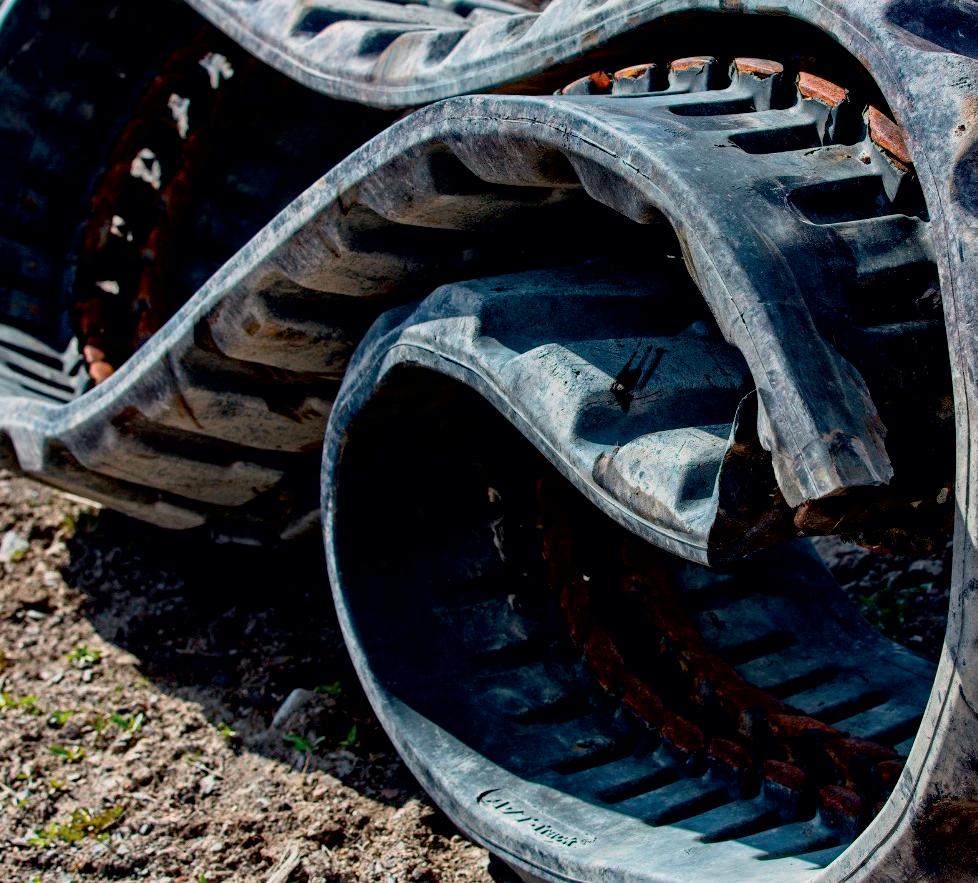
Full-depth repairs of the concrete road.
Courtesy Kevin Harvill, City of Baytown, TX THE WORK DONE
Construction began in 2020 and was completed in spring 2021. The City of Baytown replaced approximately 20% of the road surface on the North Main Street section, with work including: ˜ Full-depth panel replacement ˜ Approximately 47,000 sq. yds. of diamond grinding, at 1/8 to 1/4 in. ˜ Dowel-bar retrofit (using 300 dowel bars) for transverse cracks ˜ Cross-stitching (using 2,500 deformed rebars) for longitudinal cracks and joints ˜ Replacement and resetting of manholes ˜ Crack repair and sealing
The project was a success by all measures. Cost savings were enormous, with CPP treatments being completed for $2.2 million—less than 20% of the cost of reconstruction—saving the city approximately $10 million. PCI measurements improved to an average of 75-80. Department officials and residents were pleased with the rideability of the finished road surface.
In the upcoming 2022 construction season, the City of Baytown expects to continue its successes with CPP. Work will be performed on several residential streets, with approximately 1,200 dowel bars being placed to repair transverse cracks and 3,500 dowel bars used to crossstitch longitudinal cracks and joints. The city will optimize its return-on-investment by ensuring that involved personnel receives the proper training and by selecting future projects using lessons learned on the North Main Street project. For example, considering the hard aggregates used on many of the city’s concrete streets, project sizes will be limited due to the fact that grinding goes more slowly on hard surfaces. Projects will also be timed to occur when PCI scores are in the 50s-70s, thereby controlling the scope of repairs needed and keeping the project in line with pavement preservation (as opposed to full reconstruction). Streets targeted for CPP will ideally require 10% or less in panel replacements and panel settlement will be corrected with panel lifting prior to grinding. When determining the number of panels needing replacement, crews will perform surveys by walking the project, since exposed aggregates can make cracks difficult to see. Finally, while the North Main Street project conducted some half-lane repairs to save time and money, in the future, wider repairs will be performed because they impart greater consistency to the finished surface.
Project scheduling is also critical to success. Dowel bar retrofit should begin at least a week before grinding is scheduled but it’s equally important to have grinding work completed in a timely manner, to maintain good ride quality for the public.
CPP provides a cost-effective repair option for concrete streets while returning the pavement surface to a like-new condition and improving ride quality. It keeps roads in good structural condition and ensures durability for decades to come. For cities looking to stretch their budgets, achieve sustainability benchmarks, and have high-quality roads, CPP is a wise approach. ET
A photo of one of the manholes reset followed by diamond grinding.
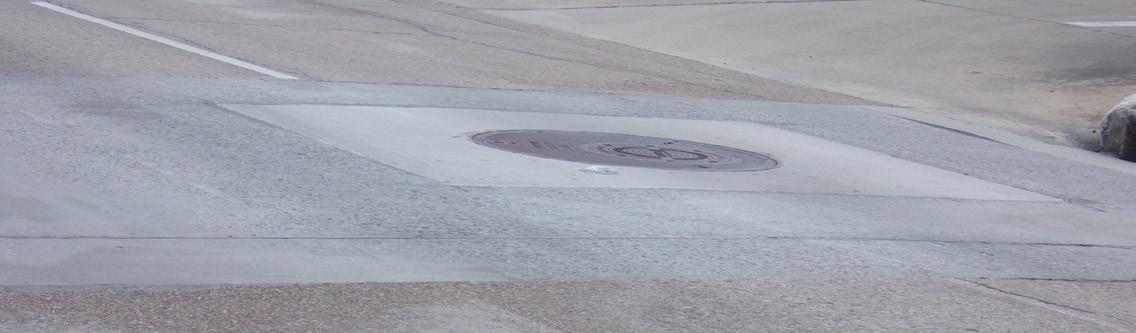
Courtesy Kevin Harvill, City of Baytown, TX
WHAT IS CONCRETE PAVEMENT PRESERVATION?
Unlike overlays, CPP fixes underlying sources of pavement distress. It consists of targeted treatments such as full- or partial-depth panel replacement, dowel bar retrofit, cross-stitching, crack repairs, and more. By addressing problems at their source, CPP prevents ongoing deterioration, reducing the need for more costly repairs in the future. Pavement condition after CPP is close to or better than that of the original.
Cost savings were enormous, with CPP treatments being completed for $2.2 million— less than 20% of the cost of reconstruction— saving the city approximately Kevin Harvill is the assistant $10 million. director for the Public Works and Engineering Department of the City of Baytown, Texas. Read more at: https://eqtoday.co/g3638t
ARE YOU IN NEED OF REPLACEMENT TRACKS?
We’re proud that Dominion Rubber Tracks are the
#1 SELLING RUBBER TRACK BRAND IN AMERICA! DEPPARTS.COM 800-365-7260
Your Competitors Are Adopting 3D Asphalt Paving and So Should You
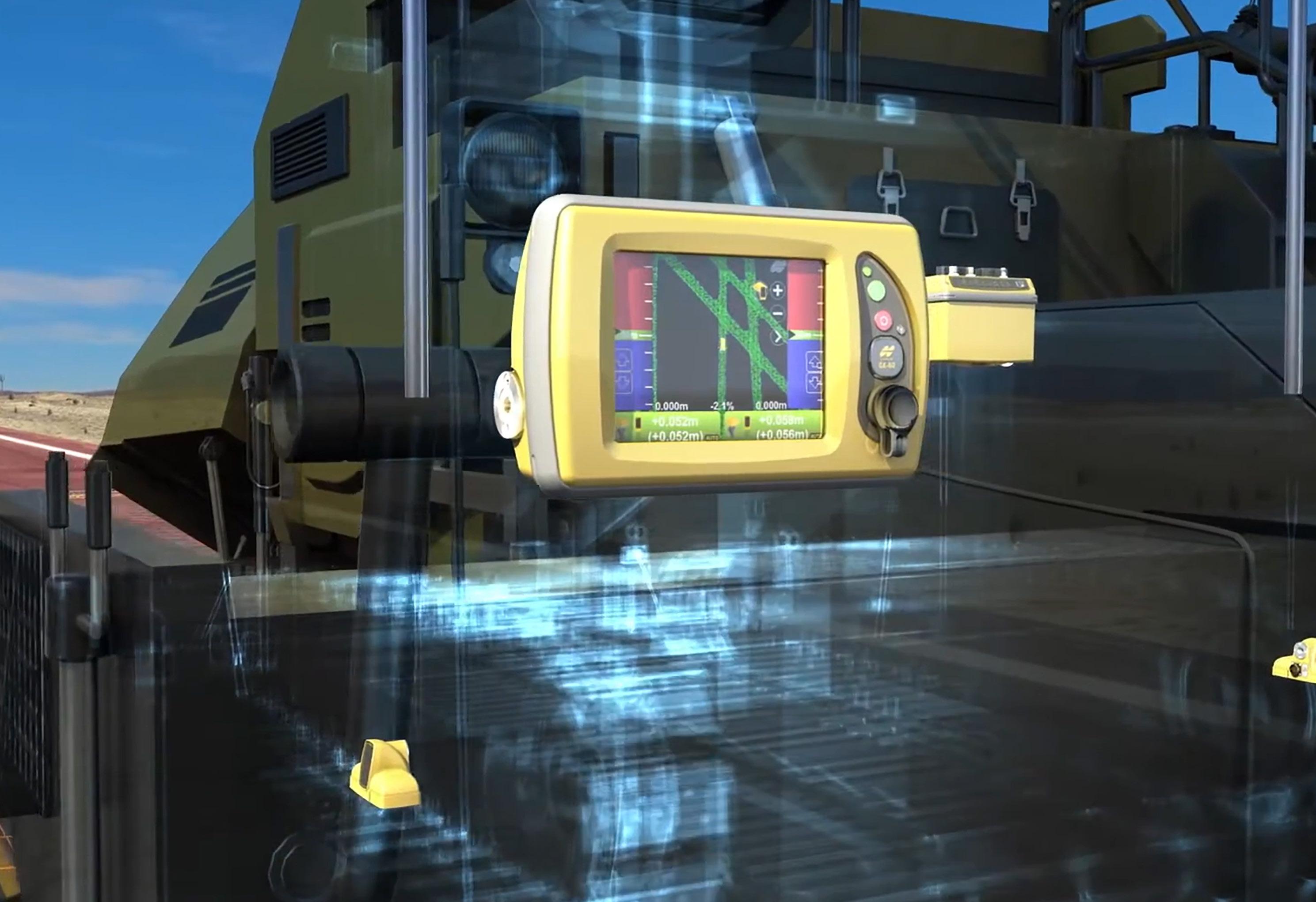
Conditions are pushing asphalt paving contractors to adopt automation widely in order to meet federal mandates, cope with a labor shortage and complete the volume of work that will come as a result of the Infrastructure Investment and Jobs Act (IIJA).
The IIJA increases the national investment by 55% over and above the 2015 Fixing America’s Surface Transportation Act baseline, and the National Asphalt Pavement Association projects that each state will receive more than $1 billion total in Federal Highway Administration (FHWA) funding to repair and improve roads and bridges. Within the IIJA is the Surface Transportation Reauthorization Act of 2021, that allocates a record amount of highway and bridge funding. These dollars will be heavily loaded toward repair of existing assets, making blacktopping and resurfacing core disciplines that will be in demand. The IIJA also includes verbiage that makes clear work performed under the bill should use advanced construction technologies:
“The Secretary shall establish and implement a program under the technology and innovation deployment program established under paragraph (1) to promote, implement, deploy, demonstrate, showcase, support, and document the application of advanced digital construction management systems, practices, performance, and benefits … The goals of the accelerated implementation and deployment of advanced digital construction management systems program established under subparagraph (A) shall include-(i) accelerated State adoption of advanced digital construction management systems applied throughout the construction lifecycle (including through the design and engineering, construction, and operations phases) that-(I) maximize interoperability with other systems, products, tools, or applications; (II) boost productivity; (III) manage complexity;
(IV) reduce project delays and cost overruns; and (V) enhance safety and quality;”
Even before passage of the IIJA though, longstanding guidance from the FHWA advocated for the use of automated screed control whenever possible on thin hot-mix asphalt overlay. Recent requests for proposals for highway projects at all levels of government are increasingly also mandating use of pavers with automatic screed controls and sensors on both sides of the paver. The controls, according to some of these mandates, should sense the grade from an outside reference line, sensing the transverse slope of the screen and provide automatic signals that operate the screed to maintain the desired grade and transvers slope within plus or minus 0.1%.
What this means is that 2D automated screed control is almost a no-brainer, as each time you adjust the screed manually, it takes several paver lengths to get to the new level. And the operator may not get it right at first, and some titration up and down causes waves in the pavement, which in turn results in expensive grinding and rework. 2D screed control on asphalt pavers has become commoditized, and in order to differentiate themselves, paving contractors may need to adopt even more advanced technology that limits waste and reduces labor requirements as inputs are constrained and rising in cost. Asphalt binder costs have increased 100% between 2020 and 2021, even before the current embargo of Russian oil sent crude prices well over $100 per barrel. A 2021 U.S. Chamber of Commerce study found that 88% of contractors are facing a labor shortage, forcing them to pull back from projects they otherwise would accept.
3D PAVING AUTOMATION IS THE ANSWER
3D stringless paving is one way asphalt contractors are going one better than their field of competitors, while cutting costs and shaving days off the project timeline. 3D paving is now reliable and mainstream, with the technology having been proven in earthworks and then seeing early adoption on highvalue paving projects in the early 2000s.
In a 3D paving environment, an array of total stations typically lock onto receivers on 3D paving-equipped machines—pavers, rollers and milling machine— through a prism mounted on each machine. 3D paving controls on each machine contain a digital model of the job, enabling the equipment to deliver on the model automatically, including slope, crossfall and even compaction density.
The trailing gate of the paver is also typically sensored, automating as-built inspection and reporting.
“2D grade control is now relatively common,” Trimble General Manager of Civil and Specialty Solutions Kevin Garcia said. “Asphalt paving contractors come to us now to learn about 3D … there is a big

- Jason Hogue, vice president, automation and machine control, Flores differentiator between 3D and things past. With 3D, we are talking about variable depth paving, and it can very quickly change the depth of the pavement and conceivably the cross slope if needed, if you are going into a superelevated curve. It does not require paint markings on the ground and is taking the human error of that process out.” 3D paving will become the standard on large or high-value paving projects, according to Flores Automation and Machine Control Vice President Jason Hogue.
“We see it now on big and small projects, just depending on the application,” Hogue said. “Some airports have asphalt 6 inches deep—so in that setting, square footage may not be that great, but accuracy is everything in the world. We are also seeing 3D paving mentioned in RFIs. I have taken calls from a number of DOTs about specifications of our accuracy—some states are thinking about stating these in their state standard provisions. We have already seen this done in a couple projects in Minnesota, but they are only the first. There will be more.”
3D PAVER OPTIONS
Paving contractors have a few options when it comes time to outfit their paving, compaction and milling equipment for 3D paving.
Topcon Positioning Systems has a line of 3D automation tools that can be moved from one machine to the other. Their Millimeter GPS GNSS technology, combined with a land-based laser and the PZS MC compact sensor on the paver toe arm, provide vertical accuracy within a few millimeters. The Topcon 3D-MC machine control unit attaches to pavers, compactors and other equipment and the 3D-MC Milling system to millers for grinding or cold planing. Topcon’s C53 System intelligent compaction system captures stiffness, temperature and pass count. When using multiple pavers, millers and compactors on a site, the units connect to the Sitelink 3D product, which captures cumulative pass count data on all rollers on the project to streamline the workflow and ensure multiple operators do not inadvertently over-compact.
The Trimble Roadworks 3D Paving Platform, meanwhile, combines automated 3D screen control accessed through the Trimble TD520 Display and PCS900 3D with the Trimble SPS930 Total Station. Trimble Roadworks transfers 3D designs from the office to the machine via the cloud so the operator is always using the latest design. Trimble Hot Spot automatically transfers control from one total station to another, preventing stops as a paving line moves along the linear project. Productivity data collected from the machine is automatically synced back to the office. Paving and compaction machine performance data can be seamlessly transferred to front office applications with the SNM941 Connected Site Gateway, passing on design updates, GNSS corrections, production reporting and enabling in-field support.
Leica Geosystems originated 3D mobile control for paving in 1999, and goes to market in North America through Flores Automation & Machine Control, (FAMC), which maintains a sales and technician network nationwide.
The Leica MCP80 machine control panel pairs with a Leica MDS docking station that stays with the machine and retains all machine-specific performance data. So even if the MCP80 is moved from one machine to another, the data for the specific machine remains segregated for later analysis, reporting and decision support. All 3D machine control software solutions are compatible with the MCP80 panel, which serves as the universal interface across all 3D machine control applications, making it interchangeable between any heavy construction machinery. Machine-specific data such as calibration values and hydraulic parameters are stored in the docking station. In this way, the panel can be used on any other machine without the risk of losing machine data even as the MCP80 is moved from one machine to the other. This also means operators need to be trained only on one interface.
Availability of the hardware for 3D paving seems to be fairly good, despite current supply chain challenges.
“I make sure we are ordering a quarter to a quarter-and-a-half ahead to make sure we are ready to meet demand,” Hogue said. “If someone calls right now and wants 200 units, which might be a challenge, but for most orders, we can fulfill them and schedule installation for one or two weeks out.”
“Prior to the problems we are seeing now, lead time to delivery was five to 10 days,” Garcia said. Now it is in weeks or longer—a lot of people are placing orders to get in line. Fortunately, most components are ready, so install could be 80% complete and then just wait for final hard-to-find components. And our biggest challenge has not been chips, radios or displays, but connector ends—the simple connector at the end of a cable.”
LOWER COST, HIGHER QUALITY
What 3D paving does, and why it’s appealing to both contractors and project owners like
federal and state governments, is enable a paving contractor to increase quality, increase margin, lower cost and shorten the timeline simultaneously.
“Most of the time, the hourly rate of an asphalt paving crew is a shockingly high number,” Garcia said. “Every little hiccup is costing you a lot of money— and it takes a lot of coordination to get the paving train moving at the right pace. That includes the plant loading out the mix at the right rate, the trucks coming at the right intervals and not having to stop and park so the mix cools off or getting segregation.”
The goal is to keep the paver moving at a consistent rate as part of a smooth and stable process. “You want to avoid stops as much as possible and changing speeds is nearly always better than stopping,” Garcia said. “The screed floats but a stop lets it sink, driving out the air voids with the weight of the screed. Every time you stop there is a discernable bump in the road. Oftentimes, you will have to come back and grind that bump—bring out the diamond grinder and grind a high spot, particularly if it is next to a low spot. These are incurred costs that you may not have budgeted for and may cause you to exceed your buffer.”
The compactor’s job would seem simpler, but also benefits from 3D technology to monitor the number of passes, degree of compaction and temperature of the asphalt. Too little compaction and the asphalt will contain air pockets, which lead to premature erosion. Too much compaction, as can happen when an operator loses track of the number of passes they have completed, leading to the operator completing more than is necessary in order to be thorough, can crush and break down the aggregate in the asphalt. Overcompaction also, according to Garcia, can have a knock-on effect, where the paver pulls further and further ahead of the compactor, which must do its job when asphalt is at the correct temperature. This causes the paver to stop, which again results in uneven spots that must be milled out. DIFFERENT 3D PAVING STROKES FOR DIFFERENT FOLKS
While 3D paving gives the contractor a great deal of control over quality, it also puts them in the driver’s seat when it comes to how they go about bidding and planning the job. And exactly how this control is leveraged depends on a number of things, including how a contractor is incentivized.
“It differs depending on whether a contractor is responsible for their own mix,” Hogue said. “If you are the sub purchasing the asphalt, you can use 3D paving to keep the general contractor honest. You have the capability to shoot elevations and grade before you pave— killing any argument on the volume of the job.”
“Is this a pay-by-the-ton job or is there a different incentive on this job?” Garcia said. “What sort of technologies do your crews already deploy? And what is the most important thing for your paving crew to achieve when you are on the job site? Do you need to meet the specs of the project, maximize margins on the bid— people tend to act like those things are mutually exclusive, but they don’t have to be. You can still do a really good job and put money back in your pocket if you are deploying things in the right way.”
But Garcia stresses that the contractor should consider their own needs, as well as those of the project owner.
“Is this a pay-by-the-ton job, and if so, what is the max allowable overrun?” Garcia said. “You want to design for the exact tonnage. You want to maximize pay and not place tonnage you will not get paid for. If you produce your own asphalt, maybe want to maximize tonnage.”
Often, exceeding smoothness criteria can bring financial incentives that by themselves can make the technology attractive—over and above other incentives for maintaining the timeline.
“On the job site you have huge savings in the timeline, which is important because you cannot go over without paying a huge penalty,” Hogue said. The biggest no brainer is in smoothness. If you are getting your ride numbers, you are saving time and dollars for not having to grind after the fact. The second no-brainer is yield—keeping that yield below or under budget.”
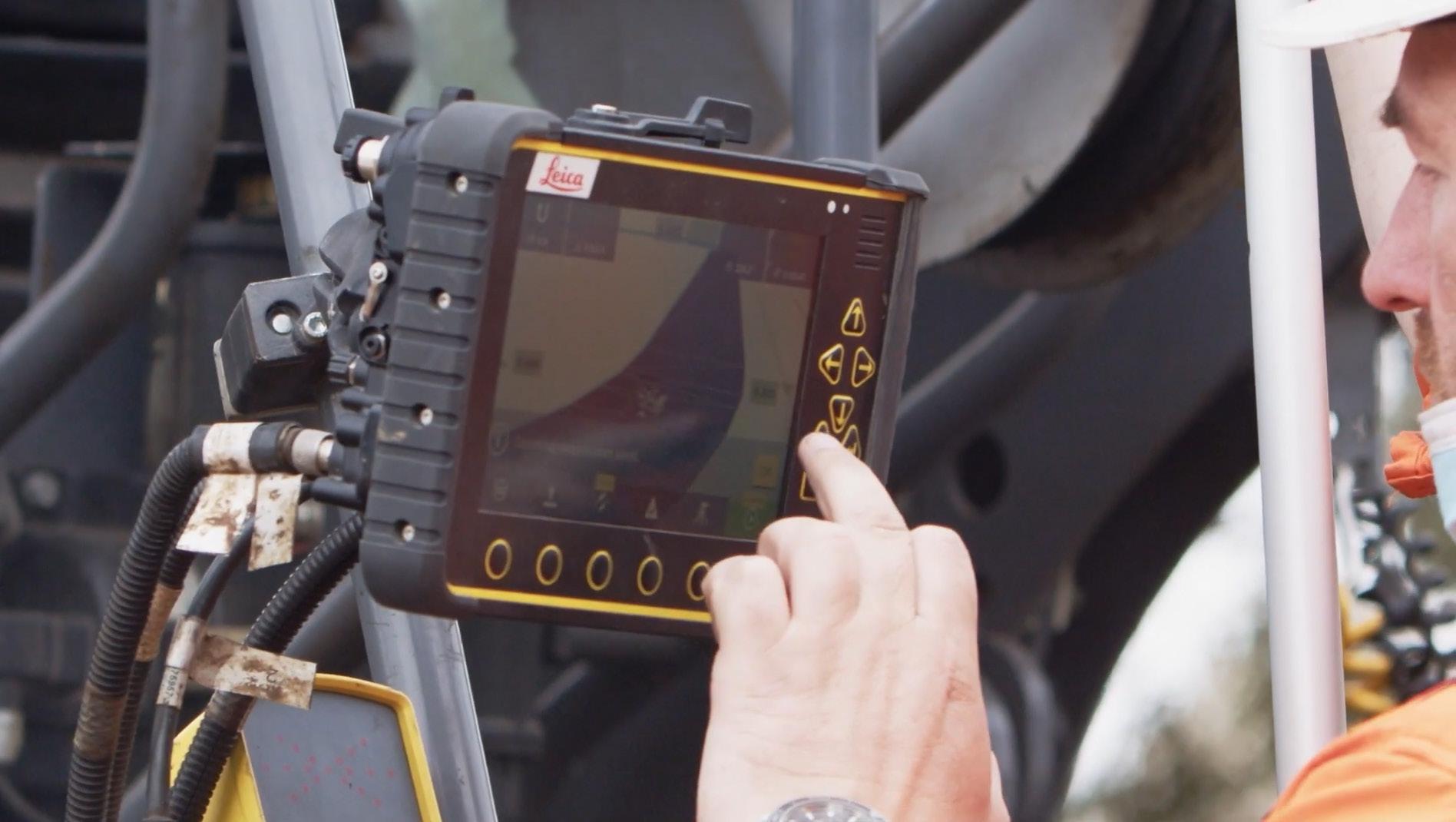
NOW IS THE TIME
3D asphalt paving will become as mainstream as 2D paving is today. The good news is 2D asphalt paving systems you have already installed are a prerequisite for achieving 3D control. Automation is advancing, and doing so in a way that rewards earl adopters. ET
Read more at: https://eqtoday.co/js4gh3
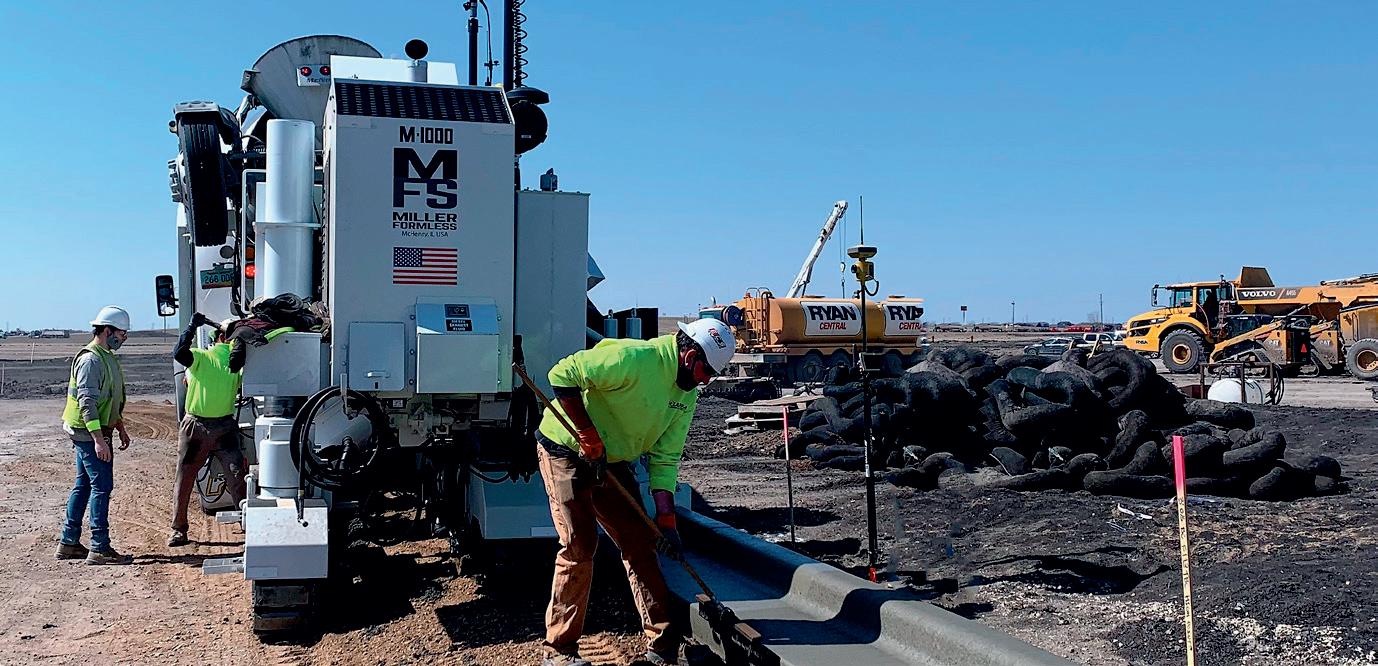
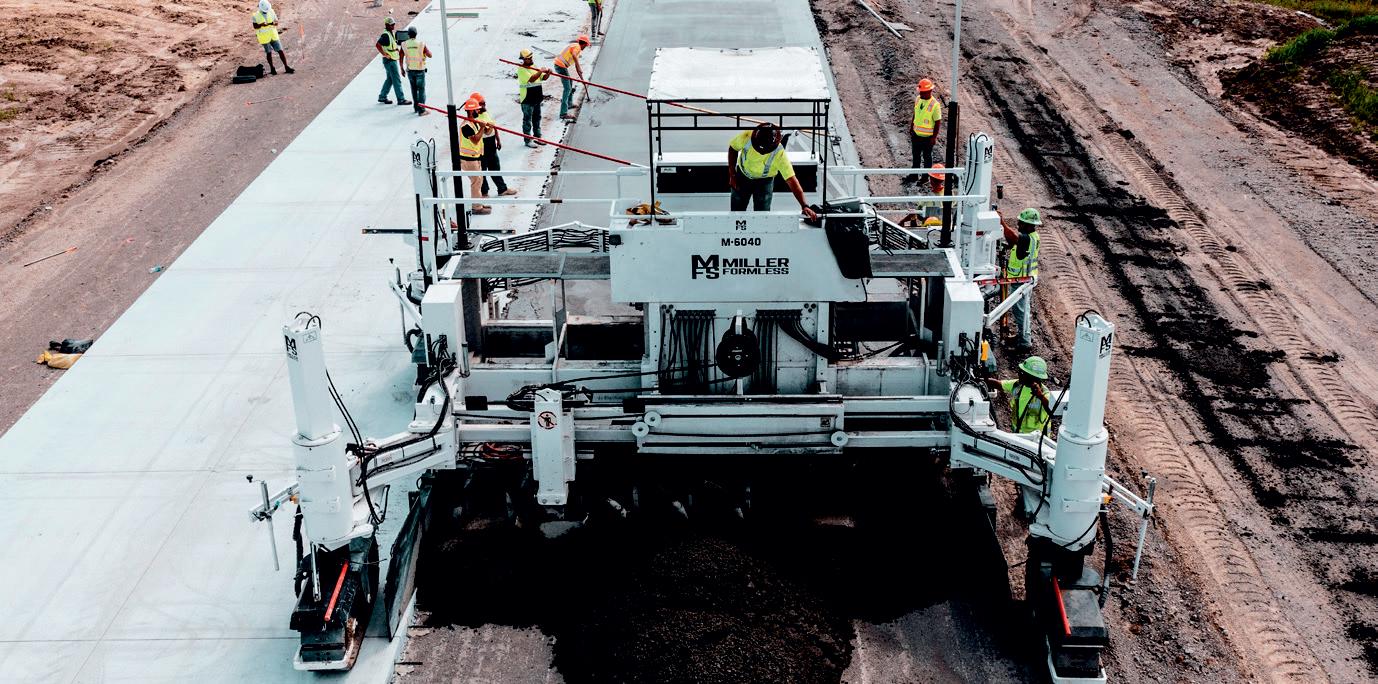
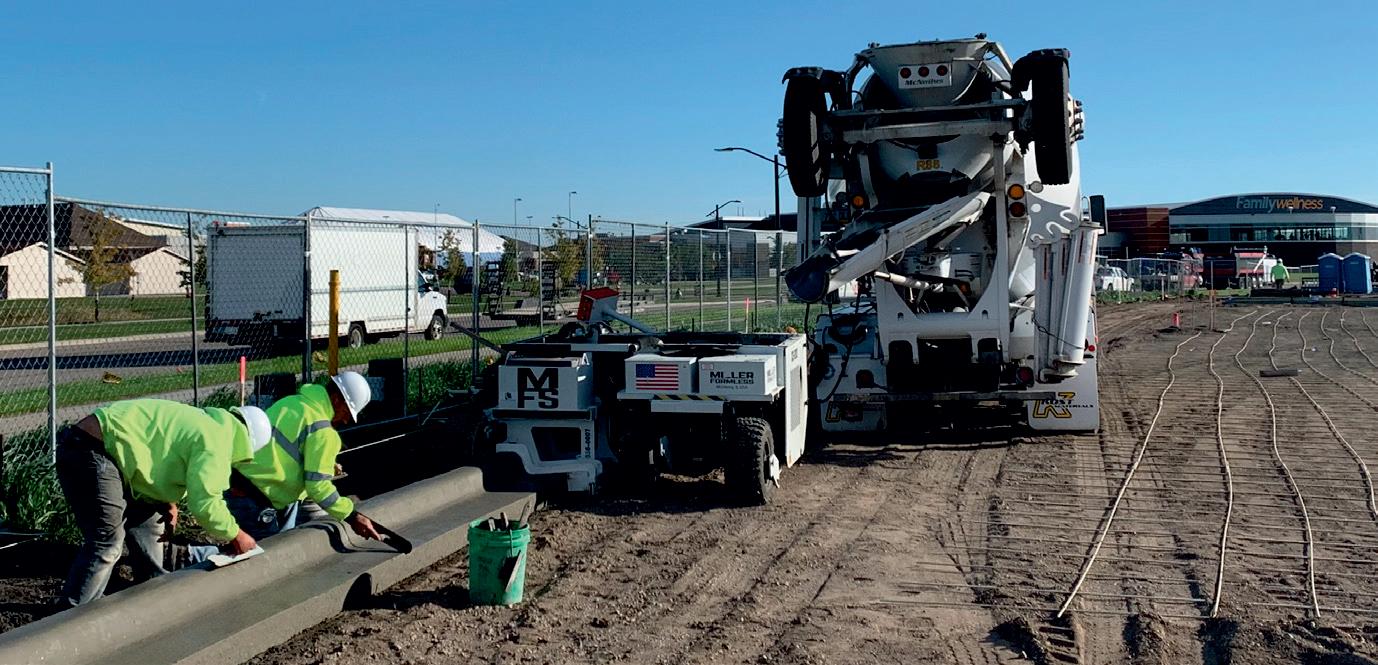