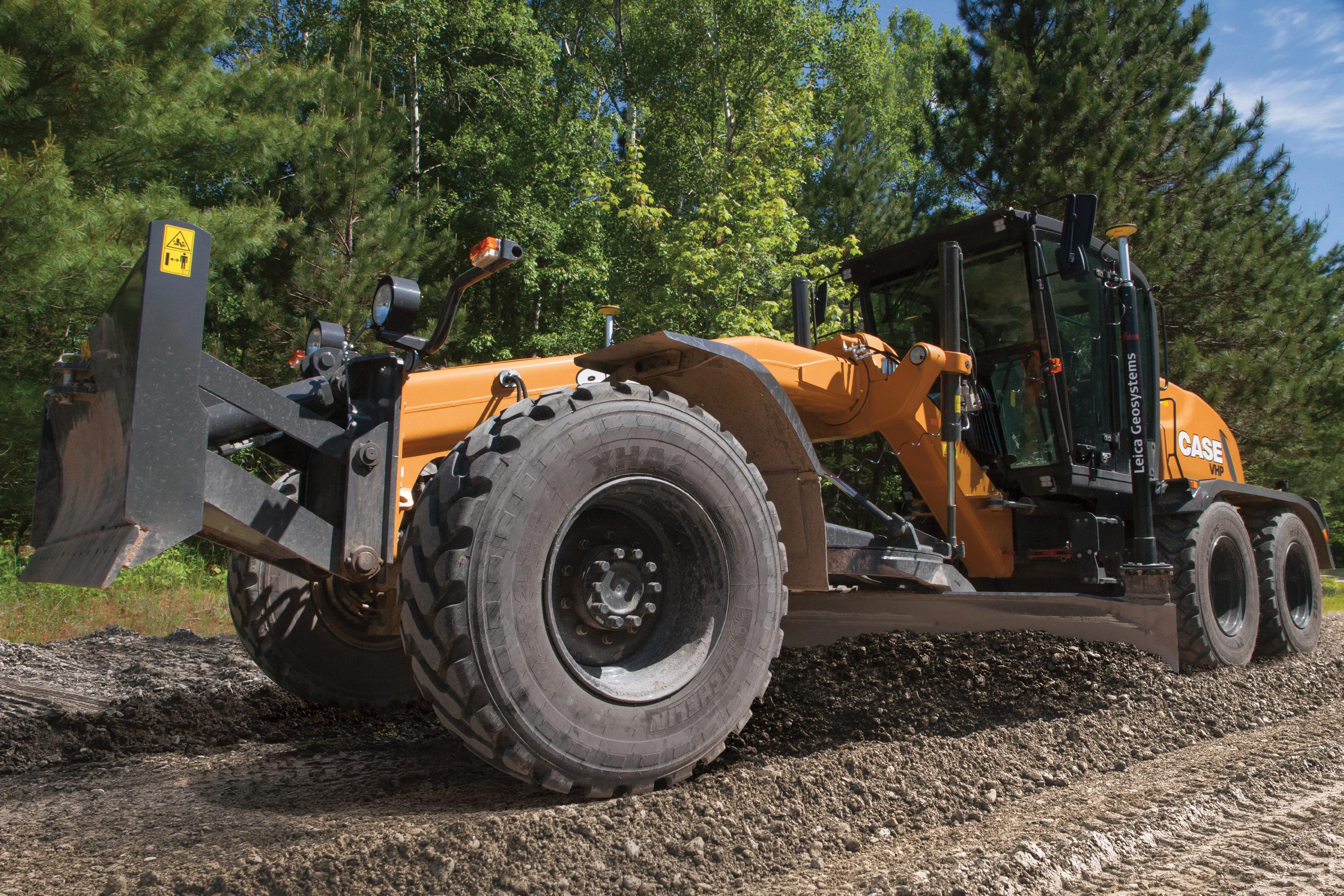
38 minute read
MACHINE CONTROL STREAMLINES EARTHMOVING OPERATIONS
Use machine control to increase productivity, slash operating costs, reduce labor and eliminate staking.
By now everyone is familiar with machine control technologies utilized in earthmoving applications. But as the costs continue to drop and the technology continues to advance, make sure you are not one of the contractors who gets left behind.
“There are very few earthmoving applications that won’t benefit from machine control in one way, shape or form,” says Jeremy Dulak, product manager, Case Construction Equipment. “As acceptance and adoption is increasing, the contractors you are bidding against on a regular basis may already be using it to streamline their operations and make their bids more aggressive.”
Before adopting any technology, you need to develop an understanding of what it can do for your operation. In the case of grade control, there are many competing technologies, ranging from indicate-only systems to full automation.
There are important differences between guidance and automation. “Many of these solutions are guidance or indicate-only solutions,” says Richie Snyder, marketing manager, CE Digital and Precision Solutions & Telematics, CNH Industrial. “This means that it is providing the operator with feedback on the screen that helps guide his or her actions. The solution still relies entirely on the input of the operator. It is simply letting them know where they are as it relates to their desired result and helps them dial in their work from there.”
Many of the recent advancements are being made in automation. “The automatic solutions are where true machine control takes place,” says Snyder. “This is where the system actually takes over the hydraulics of the machine and the blade to automate that performance. This is particularly helpful when working in a 3D world and trying to build complex grades and site profiles.”
Automation helps level the playing field by elevating the performance of less experienced operators while also improving the performance of your best operators.
BUILDING BLOCK APPROACH MAKES TECH ACCESSIBLE
Many systems will allow you to invest in lower cost 2D and use the components as building blocks as you move up to 3D. “It’s important to note that many of the components are the same for 2D; the foundational building blocks are already there,” says Snyder. “When you are ready, you can easily transition to 3D.
“2D grading is machine control at its simplest form,” he continues. “Its tools work in two dimensions: plane and slope.” This is accomplished through basic technologies like lasers and sonic tracers.
The capabilities expand as you progress into more advanced systems. “3D is where things get really fun and it allows you to expand beyond working with just a slope or a plane,” says Snyder. “These machines can be indicate only, but reach the full potential of machine control when they are automatic. You do need to add some additional geospatial technologies to make it work, such as a GPS or a GNSS receiver or a universal total station. These systems still allow you to do plane and slope work, but really simplify those more complex curves and site plans.”
You need to choose the correct technology for your worksite. “2D is great for those jobs that are consistent in nature and are often very simple,” says Nathanial Waldschmidt, product manager, Case Construction Equipment. “If you’re typically working on a single slope away from a fixed point of reference — which is often to ensure proper drainage — then a 2D system Your choice for acquiring machine control technology depends on if you already own the grading equipment or if you are purchasing a new unit. Options include aftermarket, aftermarket at time of purchase or factory fit.
MacMor Construction was one of the first contractors to take delivery of a Case factory fit dozer. The goal with adding machine control was to be more competitive with production on jobs. If you are going to add more complex work in the future, you may want to look at systems that can be easily adapted to 3D.
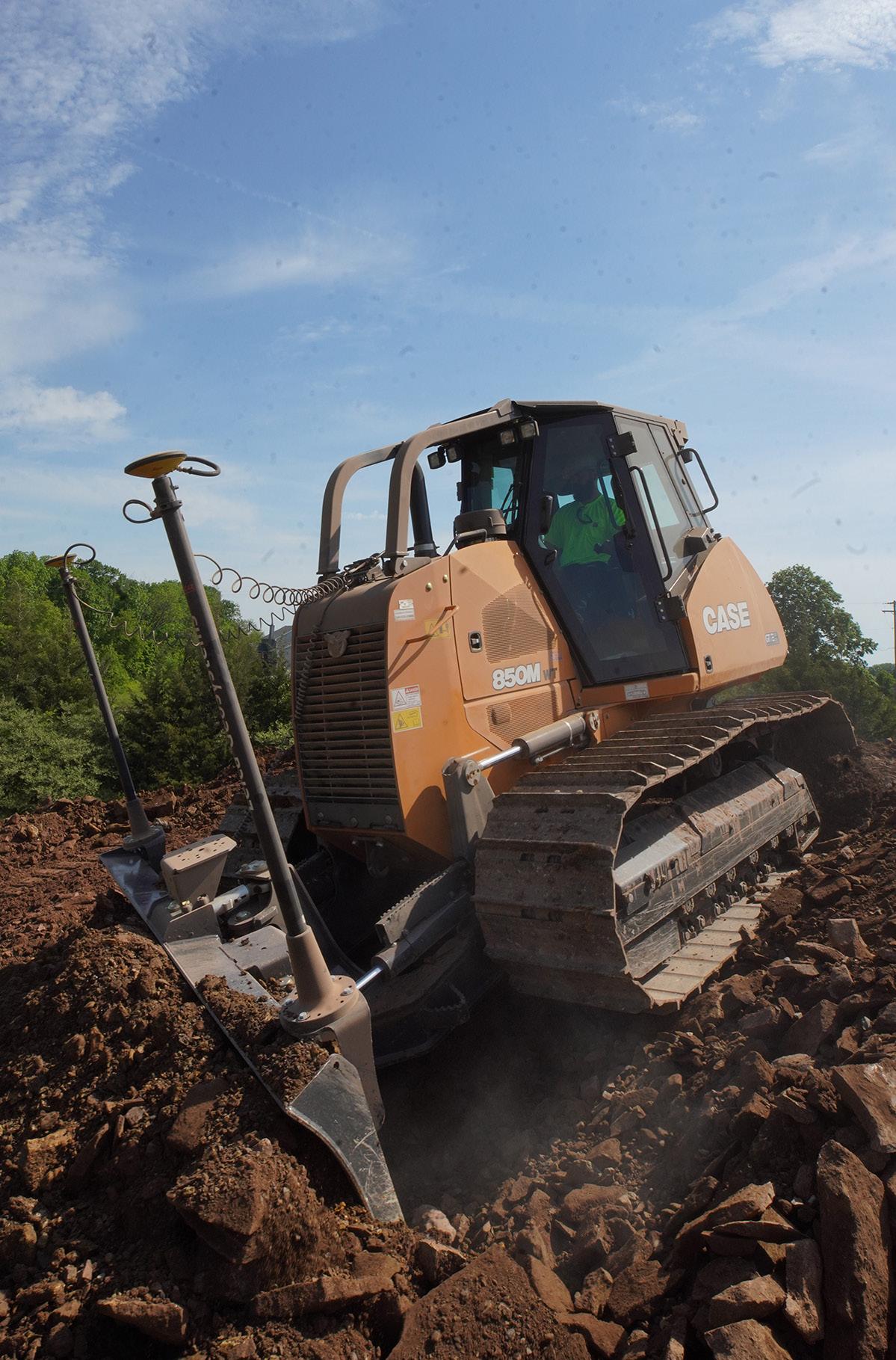
is going to be more than adequate. If you are doing driveways or parking lots, or simple final grading in residential neighborhoods where all you are doing is making sure the grade is pitching away from the home or building, 2D will work. If you are only creating building pads and doing flatwork, 2D will definitely work for you and help you ensure that you have that flat, clean plane that you are looking for.”
If you are going to add more complex work in the future, you may want to look at systems that can be easily adapted to 3D. “As your business grows, you evolve and the solution can grow with you to add on to that the next step,” says Waldschmidt. You can step up the capability of the machine control solution as you grow your business. 3D is for more complex projects, including large infrastructure projects where there are countless points of reference throughout the site that must be hit. It makes contouring and more complex designs considerably easier.
Some 3D systems can perform in both 2D and 3D modes. This is important when you want to shift between simple plane surfaces and more complex 3D designs.
Consider a Leica Geosystems solution matched with a Case machine that
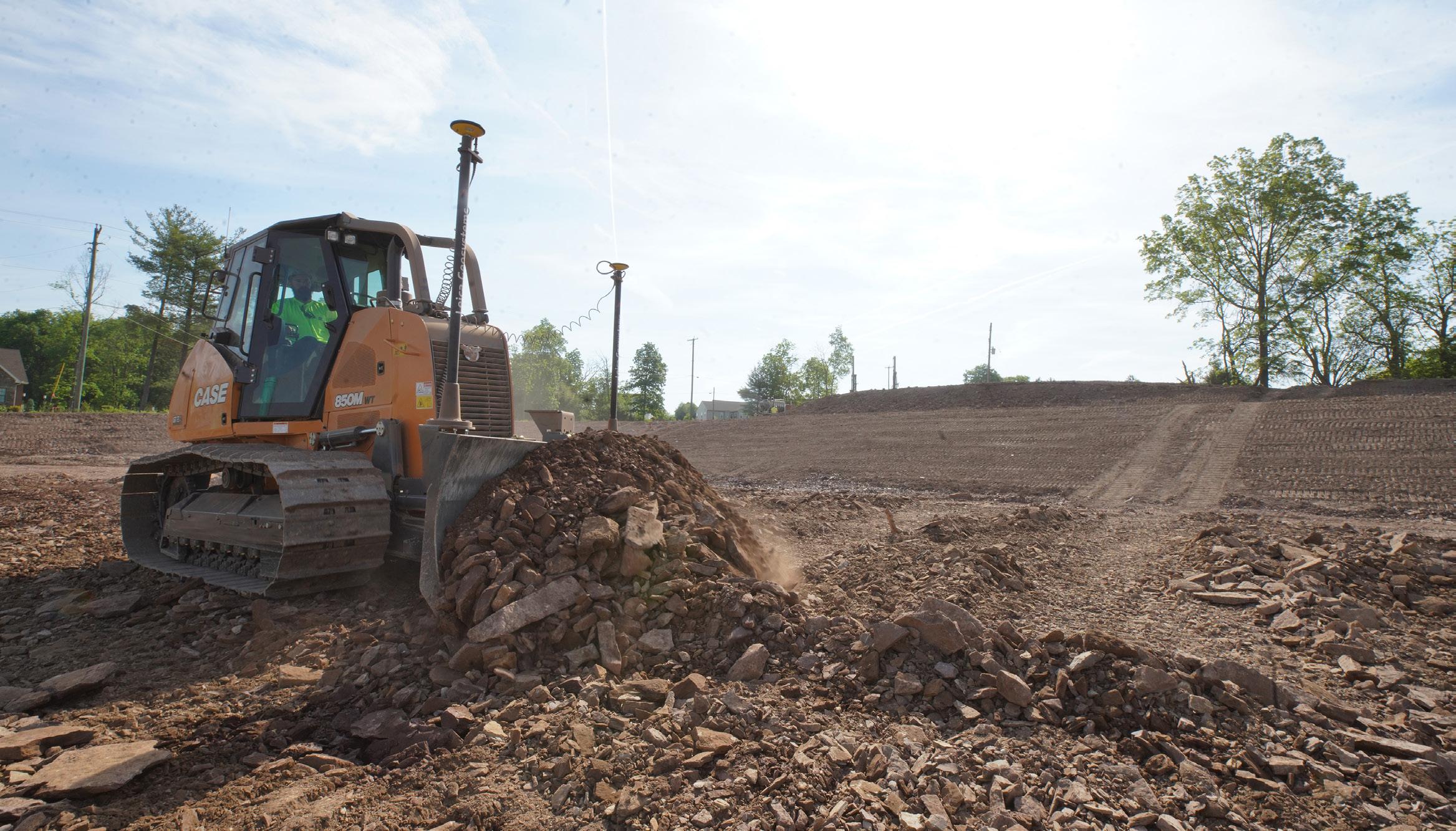
π
SHIPPING SUPPLY SPECIALISTS
IT'S ALL IN STOCK
OVER 40,000 ITEMS IN 12 LOCATIONS ACROSS NORTH AMERICA
ORDER BY 6 PM FOR SAME DAY SHIPPING

COMPLETE CATALOG 1-800-295-5510
uline.com
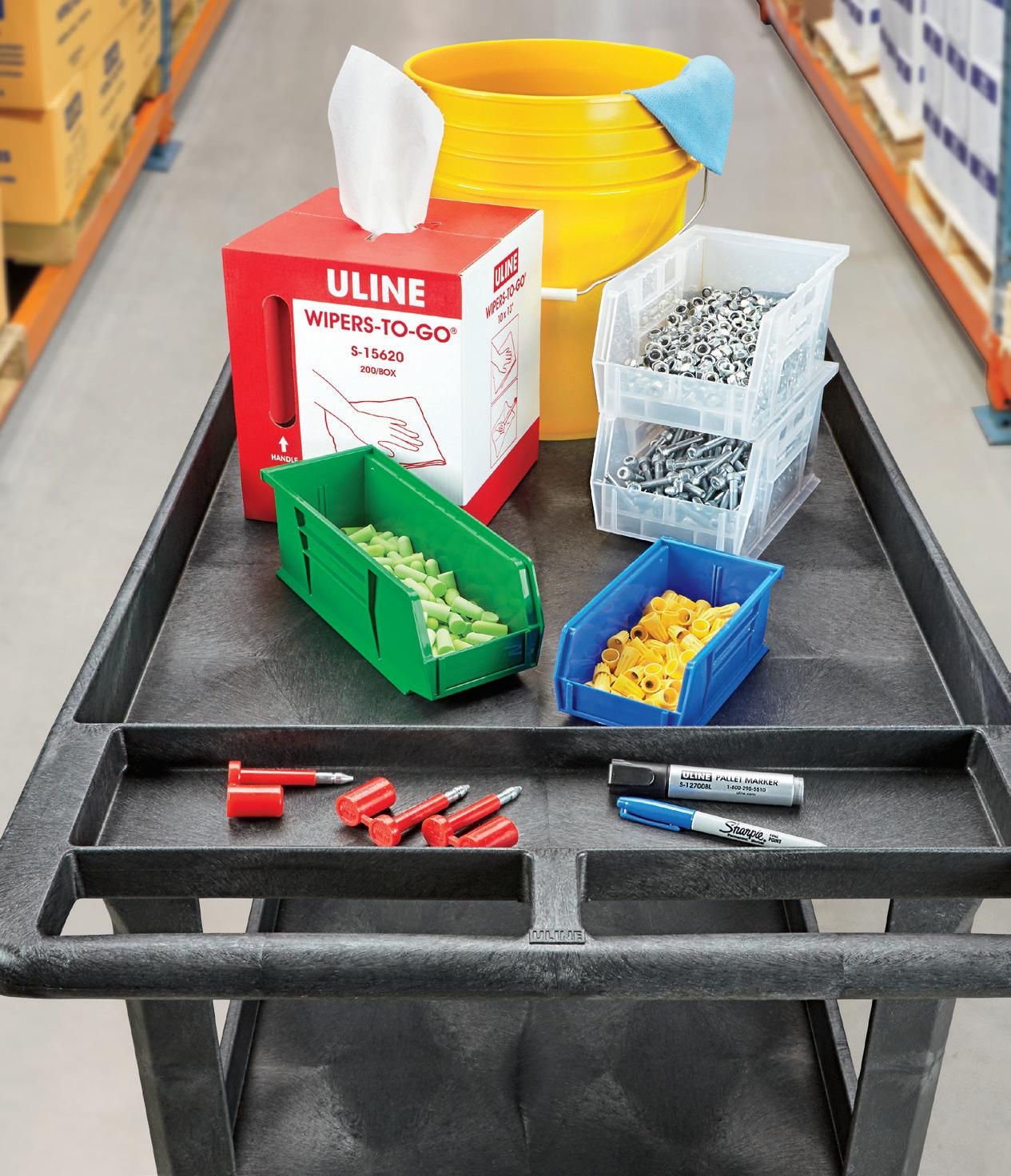
can easily go between 2D and 3D. “[On a] machine that is running 3D, that 3D panel also allows you to turn it into 2D mode,” says Snyder. “You absolutely can switch to 2D, even though it is a 3D system.” For example, you can replace the GPS antenna that’s on top of a mast with a laser receiver. “Now we are operating that 3D machine in a 2D environment.”
“It is important to note that not all manufacturers can offer that solution of scaling back down and operating in a 2D situation,” Waldschmidt points out.
Another consideration for machine control technology is the ability to increase jobsite safety. “Any machine control solution that we have running a 3D panel with the current software, we actually have the ability to put a sensor on a safety vest or on a vehicle so the operator is aware of someone coming in close proximity,” says Snyder.
UNDERSTAND YOUR OPTIONS
You have a few choices for acquiring machine control technology depending on if you already own the grading machine or if you are purchasing a new unit.
“With machine control, you really have three options when you are adding it to your fleet,” says Snyder. “You can do it aftermarket, at the time of purchase with an aftermarket solution or at the time of purchase with a factory fit solution.
“Aftermarket is pretty self-explanatory,” he notes. “You own a machine or you bought a machine and then you decide after purchase that you want to add machine control to that machine.”
You will want to work with your dealer to determine the best solution. There will be some downtime for that machine to be equipped and calibrated with the technology.
“You will need to work that into your schedule,” says Snyder.
If you know ahead of time that you want machine control outfitted on a new dozer or motor grader, you can consult with the dealer during the machine purchase. “The advantage here is that at the time of purchase, you’re analyzing the combination of that machine and solution and working with an expert to ensure they are all wellsuited to work together,” says Snyder. “We focus a lot on scalability. If you start out with a 2D system as an initial investment, you’ll have the building blocks to expand into more advanced systems as your business grows.”
Some OEMs offer pre-installed solutions that remove the hassle of installing an aftermarket solution. “We recently introduced factory fit machine control on our dozers,” says Dulak. “The factory fit provides a few strong advantages. The first is simplified ordering. You can group the system to best fit your needs with the purchase of the machine. This combines all elements in the investment into a single payment, a single financing package and a single interest rate. It also reduces paperwork and administrative time, making it all very seamless.
“The factory fit solution also ensures that when the machine arrives at the dealer, it’s just about ready to go,” he continues. “The machine and system are purpose built together, ready to work. Ordering or buying the dozer with a factory fit machine control will also increase the residual value of the machine.”
Rental can provide a way to test machine control before making the decision to purchase. “We’re seeing more dealer and independent rental operations making machine control available to their customers,” says Dulak. “Your local rental house may be a great way to dip your toes into machine control for a project or two without making a big first investment.”
DON’T OVERCOMPLICATE THE SOLUTION
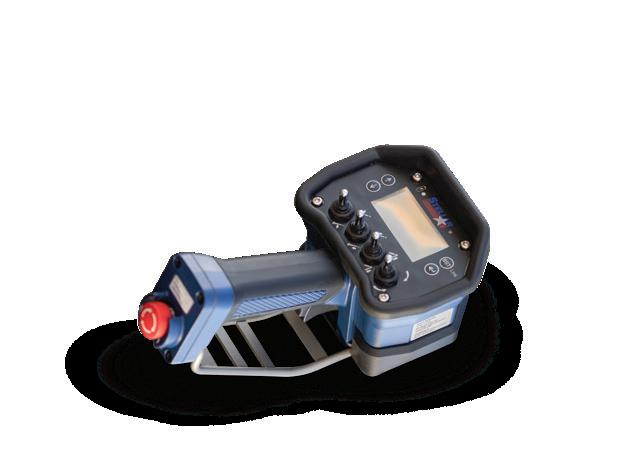
Not every machine in your fleet requires a separate machine control solution. “Machine control is very versatile,” Dulak comments. “You can have multiple machines, but you don’t have to have the finishing kits on every single machine.”
If machines are wired and the mounting points are installed, the technology can be transferred between machines. “You can transfer the hardware from one to the next. When one job is done, you can take those pieces of hardware and put it on another dozer,” Dulak explains. “It is a very flexible system tailored to your needs.” You can even use the technology on rental machines that are pre-wired for the technology.
Benefits can be immediately realized. “Machine control will give you much better control over your job costs,” reports Snyder. “It’s going to make your work schedules much more predictable and it’s really going to help you out when you’re being competitive on your next bid.”
There is also less wear and tear on your equipment. “If you can complete a job in half the passes, you can complete a job with half the wear and tear on the equipment,” says Dulak. “The amount of work doesn’t change. That is constant. You know what you have to do to complete the job. Machine control lets you do it with significantly less time on the equipment, which has huge lifetime implications.”
This also allows better equipment utilization. “We had a contractor in the Carolinas who was able to go from two dozers on each site to one because the company was able to complete both the cut and the final grade with the same machine,” recalls Dulak. “The second dozer was able to be off on the next job working instead of sitting idle, which allows contractors to be smarter about how equipment is deployed.”
There are definite labor benefits that need to be considered. “First off, you typically have a person that’s checking grade for you,” says Snyder. “You can have that person off doing some other work that’s more productive.
“Depending upon the size of the site, many contractors will set aside a whole portion of their budget to account for re-staking. Stakes either get moved, they get run over, designs change and so on. This can get very costly,” he states. “With machine control, the data points don’t change and the design remains consistent within the system unless you do a design change, at which point a new design is simply uploaded rather than re-staking the whole site.”
Leica Geosystems has built out an ROI calculator that lets you input real jobsite metrics and statistics to help you calculate realistic payback on a machine control system. This isn’t a guarantee on ROI, but it definitely helps paint the picture of what is possible. ET

MACHINE CONTROL ADDS VALUE FOR CONTRACTOR AND PROJECT OWNERS
MacMor Construction began operations in July of 2013 and has grown to specialize in heavy highway construction along with site work. According to Bryan Golden, owner, “Basically, we have everything to do with the complete site excavation. We will do clearing, grubbing, site work and then all of the utilities.”
Unknowns are among the trickiest complexities when performing site work. You may think that there is a 2-ft. layer of shale and it turns out to be 8 ft. deep. An open line of communication with the project owners helps cope with these surprises. “We try to keep as open line of communication with folks as we can,” notes Golden. “We don’t try to hide anything.”
To offset any surprises, MacMor is always on the lookout for different ways owners can save money on projects. “We do some value engineering with them,” says Golden.
Machine control offered the ideal opportunity to add that value, though Golden wasn’t 100% sure about the technology at first. But the goal with adding it was to be more competitive with production on jobs. So MacMor became one of the first contractors to take delivery of a Case factory fit dozer.
The benefits have proven to reach beyond production. “It’s on the cost side, as well,” says Golden. “It takes us from having a surveyor out on a project putting in stakes that had the potential of getting knocked over. We always use a rule of thumb that each stake costs you about $75. If you knock over 100 of them, that is $7,500.” Machine control eliminates this cost.
Operators also have greater vision of the site. “It takes the question out of what is it supposed to look like,” Golden explains. “[Operators] can see it more with the screen and see what they have going vs. a guy putting in a bunch of grade stakes.”
Machine control also provides peace of mind during production. “I’ve seen no issues with this machine on any application we put it on,” says Golden. “It does a great job. Whether you run a 3:1 or a 2:1 slope with it, you know you are going to hang on. The ability to track in slopes... everything works very well on it. It doesn’t give me any worries about that machine doing what it is supposed to do.”
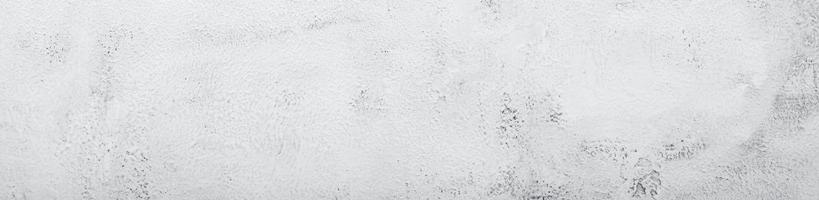
Productively.
Handle maintenance in the field in less time with Stellar’s innovative new CDTpro™ crane control system. The industry-only Range Finder™ technology provides realtime max lifting capacity from any point without unstowing the crane, so there’s no more time lost to unnecessary re-setups.
Learn more about this and other innovations at stellarindustries.com
Mobile Crushing Saves Time and Money
Recycling of virgin or waste concrete and asphalt on the jobsite eliminates transportation fees and lowers costs.
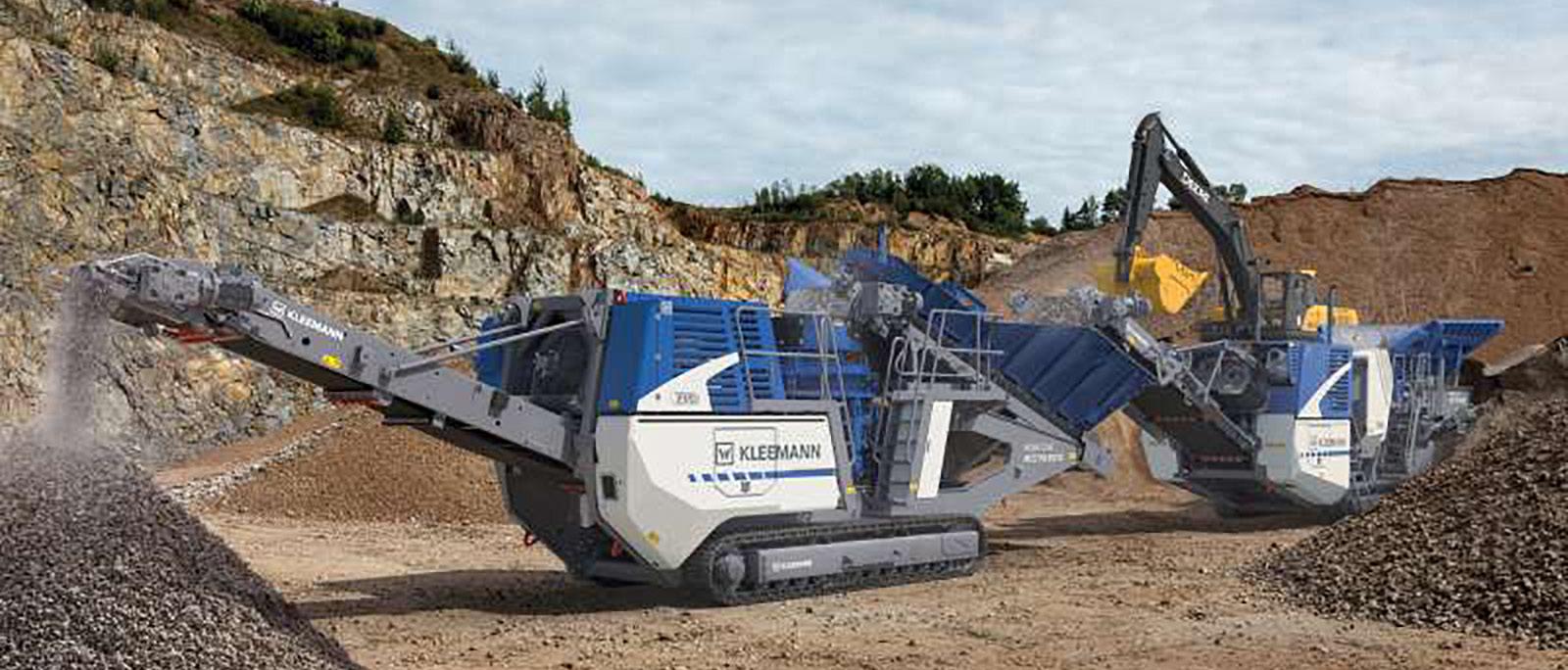
Today’s mobile crushers are ideal for use in a wide range of applications, including as a mobile recovered concrete crusher, or for asphalt and mixed C&D waste.
The construction industry is one of the largest recyclers in the country, recycling and reusing asphalt and concrete in massive amounts. Today’s mobile crushers are suited for use in a wide range of applications, including for asphalt and concrete or for mixed construction and demolition waste.
For larger road construction or demolition projects, on-site recycling and crushing of materials can be beneficial to the project bottom line. Processing, screening and crushing existing concrete and asphalt on-site eliminates unnecessary transportation costs and hassles. The recycled product may be used on the project at hand, sold to another job or transported and stored for future work — saving space in landfills and saving money.
Recycling on the jobsite also mitigates the cost of buying virgin stone, and it can be stockpiled to build something else on the property. Other advantages of recycling concrete and asphalt right at your location include: ˜ Eliminating or reducing tipping fees and disposal costs ˜ Eliminating usage demand for much needed landfill space ˜ Eliminating or reducing transportation costs ˜ Helping preserve virgin deposits and protect the environment ˜ Lowering aggregate material cost for construction projects ˜ Lowering traffic impact and reducing energy costs

Every time material is moved around or off the jobsite, labor and expenses are involved. Mobile crushers bring the machine right to the pile and allow for efficient material processing. HOW MOBILE CRUSHING WORKS
Screening and crushing plants receive the material from the initial crushing process and are small enough to be mobile. Additional crushing further reduces large particle sizes, while the screener sorts out material, allowing the right size material to pass through and returning the larger particles back to the crusher for further processing. In order to smooth out the gradation of the crushed particle and ensure a higher quality material, the new aggregate can be fed into the crusher hopper and mixed with the recycled material.
Recycled aggregate materials can offer superior compaction, better yield and greater durability over virgin (quarry or pit) aggregate bases. The use of recycled aggregates is typically authorized by State Transportation Departments for use in roadbeds and drainage projects.
To perform on-site crushing, contractors need to either own or rent specialized equipment. For smaller projects, a crushing attachment or small portable crusher can be useful for turning concrete into usable aggregate. For larger jobs, mobile crushing units are ideal.
The stand-out feature of the mobile crusher or tracked impactor for recycling applications is its mobility combined with high productivity per hour. Units are fully self-contained on a tracked undercarriage and can be easily driven off a trailer by one operator and quickly put to work, with the capability for moving directly to materials. Some models are even capable of tracking (moving about on their tracks) while crushing.
Every time material is moved around or off the jobsite, labor and expenses are involved. Mobile crushers bring the machine to the jobsite, right to the pile and allow for efficient material processing.
CRUSHERS: RENT VS. OWN
When it comes to investing in crushing equipment, buying vs. renting can offer distinct trade-offs. Buying crushing equipment usually requires a larger investment than renting, though financing options are able to ease the acquisition. Renting can allow for a smaller initial investment; but depending on the job length and frequency of use, rental costs could add up over time.
Larger volumes of material will require a dedicated crusher, which is not only a large capital investment but a heavy time and space commitment, as well. Crushers require a substantial amount of room and take time for setup. When you fold out a screen plant and set up a jaw crusher, you need to plan for their footprint on project sites. You will need room for the stockpiles, as well.
Large crushers also require support equipment, such as an excavator to feed the crusher and a dozer to move the recycled material to the stockpile. In addition, your crew will need to be trained on how to use the equipment and how to troubleshoot the machine in case of a breakdown. For these and other reasons, renting this equipment or hiring a specialized crushing subcontractor may be beneficial.
If you employ well-trained team members, buying and maintaining crusher equipment may be no more costly than renting regularly serviced equipment. Employing team members on site could also resolve unexpected problems more quickly than waiting on service from your rental partner.
Carefully consider the economics before committing to on-site crushing. Justifying this expense requires that you have sufficient material to crush. Many say having a crusher on site is not worth the expense unless there is 3,000 tons of material or more. Ultimately, it will come down to how much you will use the equipment and if you can keep it busy. ET
Leica 3D Machine Control for Swing Booms
The MC1 one-for-all software platform now provides a 3D machine control solution for compact excavators and backhoes with a swing boom.
•Provides flexible data flows and easy to use interfaces •MC1’s portable control panel can be used across multiple machines •Cloud-based collaboration platform Leica ConX can be used to share and report as-built documentation with office and field stakeholders •Utilize a swing boom sensor or manually defined angles •Prism and total station configurations possible for high-accuracy jobs www.forconstructionpros.com/21563118
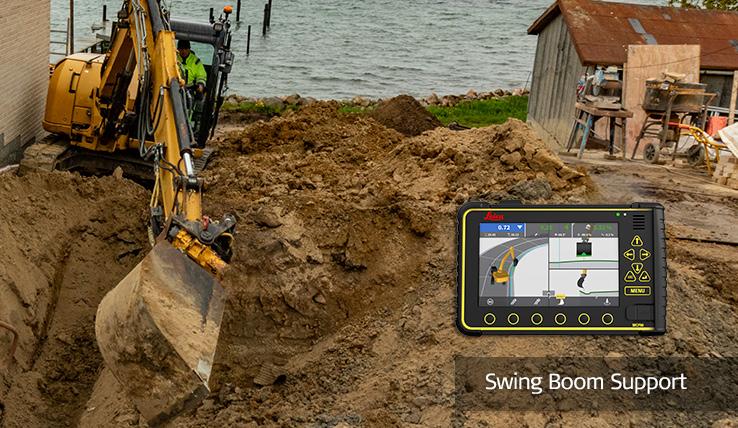
LBX Link-Belt Precision Grade
The Link-Belt Precision Grade powered by Trimble Earthworks upgrade kits are available for the LinkBelt 145 X4 excavators.
•Provide all necessary components, hardware and software required to upgrade a standard machine to 2D/MG (Machine Guidance) or 2D/MC (Machine Control) •Can also upgrade a machine with 2D/MG already installed to a 2D/MC-capable machine •Integrated into the excavator’s Spool Stroke Control hydraulic system to deliver enhanced accuracy and controllability www.forconstructionpros.com/21747158
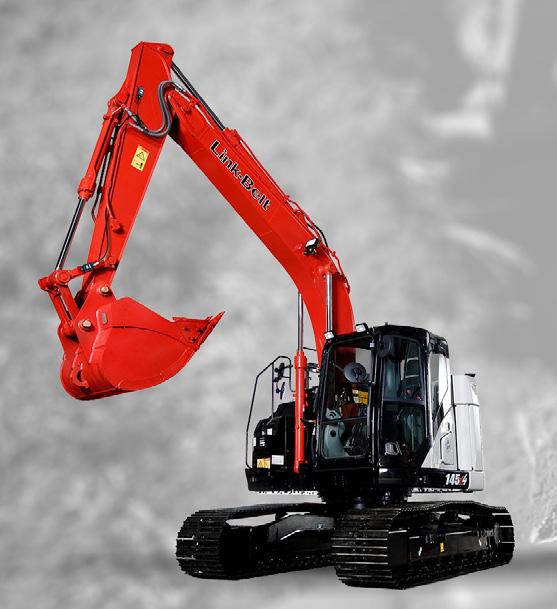
Liebherr PR 736 Generation 8 Hydrostatic Drive Dozer
The 56,218-lb. PR 736 G8 dozer has a 217bhp Liebherr Tier 4 Final diesel engine with Eco mode.
•Straight, semi-U and six-way blade options available in capacities ranging from 5.36 to 7.27 cu. yds. •Electronically pilot-controlled work hydraulics for swift, precise work cycles •Liebherr OAS – Operator Assistance Systems offers a “Free Grade“ level for active blade stabilization during fine grading, “Definition Grade“ level for automatic blade positioning when creating 2D grades and “3D Grade“ option to model complex terrain shapes •Roof-mounted GPS/GNSS antennas standard along with onboard Active Sensor Control to stabilize all blade axis www.forconstructionpros.com/21063560
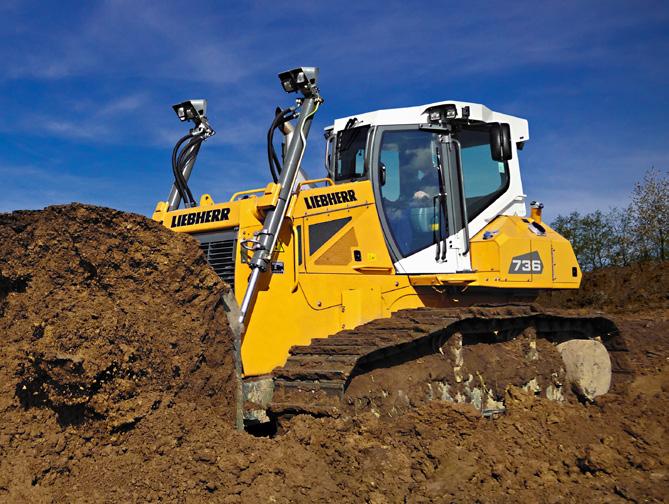
Topcon MC-Mobile Machine Control for Compact Equipment
The MC-Mobile portable machine control solution provides the user experience and performance benefits of full-size machine control guidance solutions for compact excavators, skid steers and compact track loaders.
•Provides design, build and check functionalities and a feature-rich Topcon software experience •Operators can use modular components for a range of applications, including grade checking, creating designs on the fly and self-performing site layouts •Displays and other components can be easily shared across numerous machines and moved from grade checking/layout rover pole to machine and back •Easy to set up and use www.forconstructionpros.com/22093795

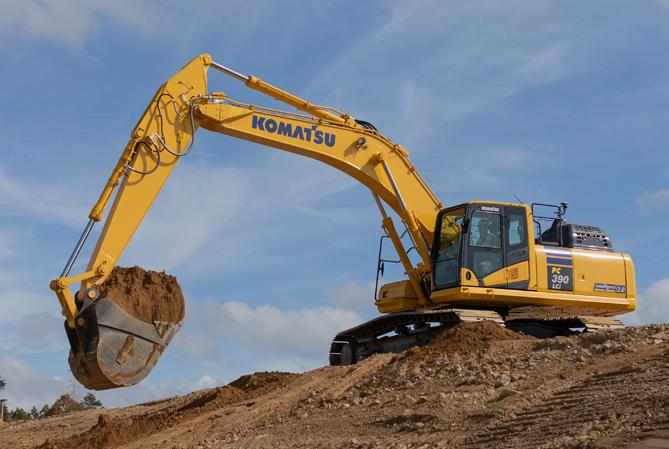
Komatsu PC290LCi-11, PC360LCi-11 and PC390LCi-11 with iMC 2.0
The intelligent Machine Control 2.0 (iMC 2.0) is now available on the mid- to large-size PC290LCi-11, PC360LCi-11 and PC390LCi-11 excavators.
•Updated, factory-integrated systems help to minimize over-excavation and empower operators to dig straight to grade quickly and accurately •Auto tilt bucket control assists operators by aligning bucket parallel with the slope so finish grading can be accomplished without needing to align the machine with the target surface •Bucket angle hold control automatically holds bucket angle to the design surface during arm operation to enable finish grading using only arm input www.forconstructionpros.com/22056661
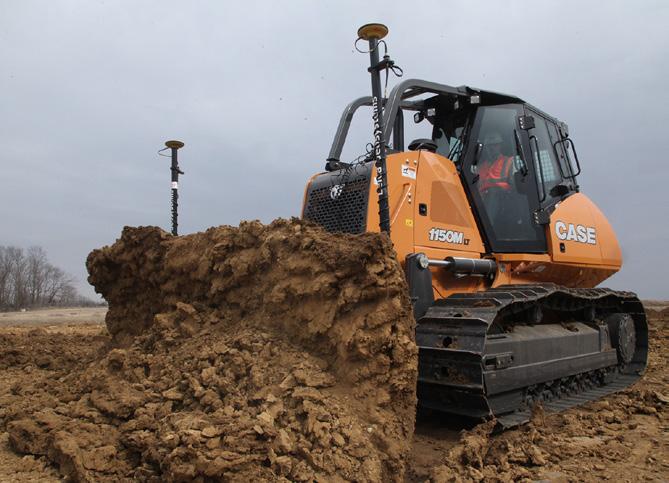
Case M Series Crawler Dozers
The M Series dozers range from the 68-net-hp 650M to the 214-net-hp 2050M, offering operating weights from 16,405 to 45,398 lbs., blade capacities from 2 to 7.29 cu. yds. and maximum drawbar pull from 39,086 to 80,979 lbs.
•FPT Tier 4 Final engines with selective catalytic reduction technology •Hydrostatic transmissions •Optimized cab-forward design, sloped hood and floor-to-ceiling glass ensure optimal visibility to the blade edge •Soft, medium and aggressive reversing and steering mode settings •750M to 2050M available with factory installed and calibrated Leica 2D, dual mast 3D and SiteControl CoPilot precision machine control solutions www.forconstructionpros.com/10920461
Trimble Earthworks Grade Control Platform Version 2.0
Trimble Earthworks 2.0 includes Horizontal Steering Control for dozers, which automatically controls the machine to follow any horizontal alignment without operator assistance.
•Augmented Reality for excavators enables users to easily understand 3D models, cut/fill information, slope data and other bench points and reference points on the in-cab display in context •Mastless motor grader configuration provides an improved range of blade motion •Integrated LOADRITE Payload Management displays grade control and accurate payload data on one screen www.forconstructionpros.com/21035976
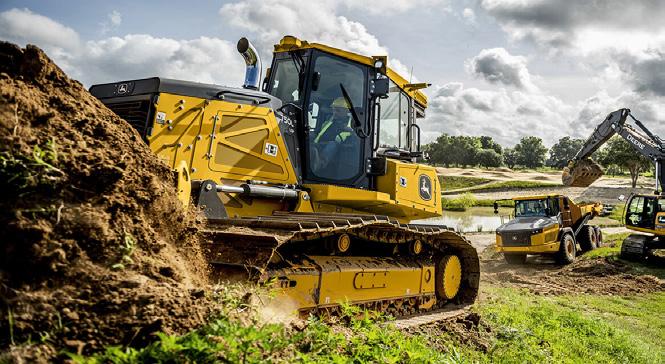
John Deere SmartGrade Remote Support
John Deere offers SmartGrade Remote Support on its newest SmartGrade dozers, motor graders, excavators and compact track loaders.
•Includes Remote Display Access and Wireless Data Transfer and will be available on most SmartGrade products for six years from factory invoice date •Available on 700L/750L/850L SmartGrade dozers, SmartGrade motor graders, 210G LC and 350G LC SmartGrade excavators and compact track loaders •Enables remote transfer of project files to machines and troubleshooting of any grade control-related issues www.forconstructionpros.com/21808923
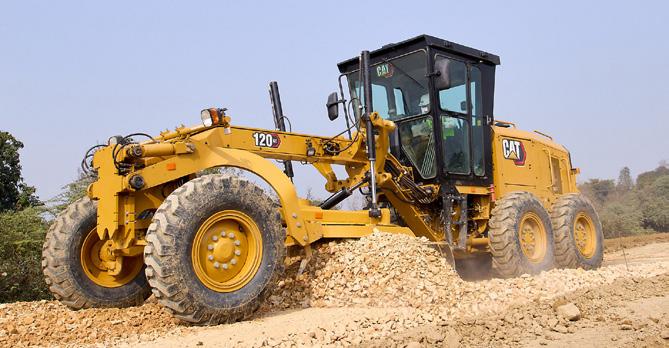
Caterpillar 120 GC Motor Grader
The 120 GC features a powershift transmission and balanced machine design that ensure appropriate drawbar power to the ground with the fuelefficient C4.4 engine.
•Electronic throttle control adapts engine power and torque to application demands •Standard rear-wheel drive and optional all-wheel drive •Transmission with torque converter eliminates need for an inching pedal •Drive system’s no-spin differential automatically unlocks in the turn to eliminate required operator input •Standard drawbar circle moldboard includes hardened circle teeth and replaceable wear inserts www.forconstructionpros.com/21928339
Over 18 years, K&D Land Improvement’s services have expanded to all types of work, including land and water conservation; field tile repair; septic and sewer work and demolition (pictured here).
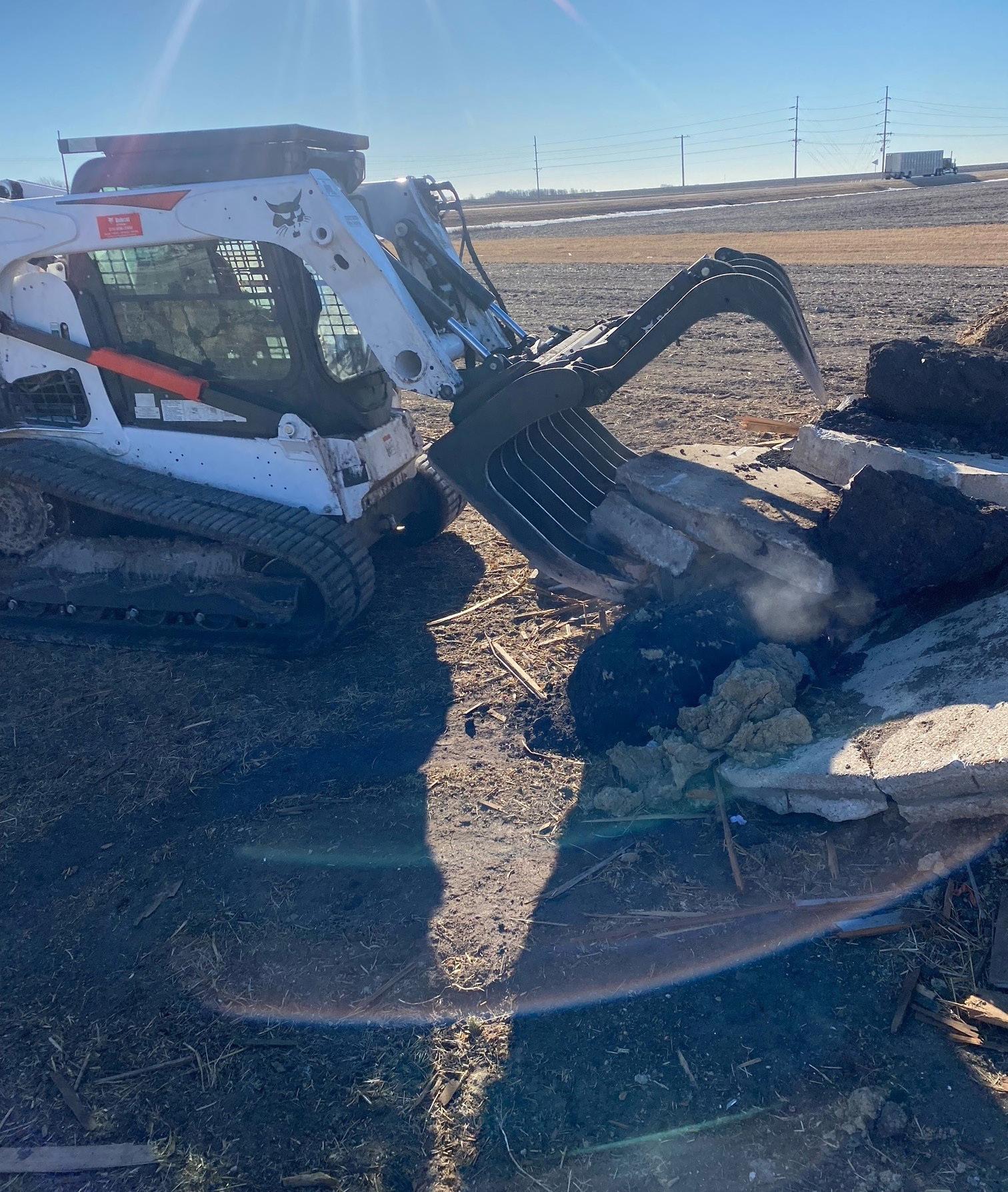
CTL HELPS LAND IMPROVEMENT COMPANY Conserve Business Growth
K&D Land Improvement has built its business around compact equipment and attachments.
For Iowa contractor Dan Hansen, a love of the land was strong enough to motivate him and his wife to start K&D Land Improvement, a business largely focused on timber and prairie preservation. And even though the company provides a broad range of services, it is the conservation-focused work that Hansen enjoys most.
Hansen and wife Karen (the “K” in K&D Land Improvement) started the business in 2003. Over the next 18 years, K&D’s services expanded to land preservation and restoration, including tree and brush clearing for private landowners and the Department of Natural Resources; field tile repair; implementing water and soil conservation practices, such as saturated buffers and bioreactors; septic tank installation; demolition; street sweeping; and sewer work.
Although Hansen is committed to any project K&D takes on, the conservation work strikes a different chord. “I literally grew up in the woods not far from here,” he says, while working on a timber improvement job in his hometown of Lehigh, IA, where the business is based. “We’ve found a niche being versatile, and services like sewer work are a necessity, but I’d much rather be working in the timber. It’s who I am.”
BUILT TOUGH FOR TIMBER AND LAND CLEARING
The Hansens have a son, Zach, who has been completing jobs with his dad full-time since graduating college; their two daughters are not part of the business.
“It’s just my wife and me and our son. You don’t get much smaller than that,” Hansen says. “But we have nice equipment that truly is our livelihood. It’s my business; it’s my desk.
Hansen started out using a competitor’s skid-steer loader before developing a relationship with Capital City Equipment Co. He rented, then leased and eventually purchased a Bobcat 773 skid-steer loader. Now, the company has a T770 compact track loader (CTL), which is its 10th Bobcat loader, as well as an E63 compact excavator and MT50 mini track loader.
K&D’s services run the gamut of what Bobcat machines and their attachments can support, resulting in a fleet of 20 Bobcat attachments for the contractor’s three machines. The Hansens believe their root grapples are the most versatile attachments they own because they can be used for so many types of work.
In timber restoration and land clearing, the forestry cutter and application kit for the T770 has proven extremely efficient. “The forestry cutter is perfect for this type of work,” Hansen says. “Safety and protection wise, you get the cab with the special door and windows and different guards... This is a really tough attachment doing work that can be brutal on a machine.”
Specific to the T770 loader’s size and strength, he adds, “We cannot have a big, heavy footprint on most of our sites, and for this class of machine, Bobcat is definitely the toughest.”
Hansen calls Bobcat engineers and dealer salespeople “understanding” when it comes to machine and attachment innovation, especially for his primary types of work. “They are continually updating and getting better,” he says, “but they ‘get’ my business and get what I need.”
Hansen realizes, however, that getting the most out of any machine requires a commitment from its owner and operator. As such, he is adamant about preventive maintenance on the equipment. “Considering the investment and how important they are to the business, you’ve got to take good care of them,” he emphasizes. PRESERVING THE FUTURE
K&D Land Improvement has earned a strong reputation in the area without formally advertising. In fact, it has a lot of repeat business, particularly related to timber improvement and restoration.
One landowner near the Brushy Creek State Recreation area in Lehigh has been hiring the company to help clear and maintain his land for 15 of K&D’s 18 years in business. Although the customer marks trees and brush to be removed, as a Natural Resources Conservation Service commissioner, Hansen can help select trees and brush to remove or keep based on state forester standards. Karen, a conservationist for Webster County, IA, can help, as well.
Hansen appreciates the fact that many of his neighbors and customers care as much about the land as he and Karen do.
“I’m not a political guy but conservation is important,” he states. “We’ve got to pay attention to our natural resources and protect and preserve what we have. We can all do this together, but everyone needs to do their thing.” ET
Dan Hansen (right), who co-owns K&D Land Improvement with his wife Karen, has his son Zach (left) working alongside him on jobs.
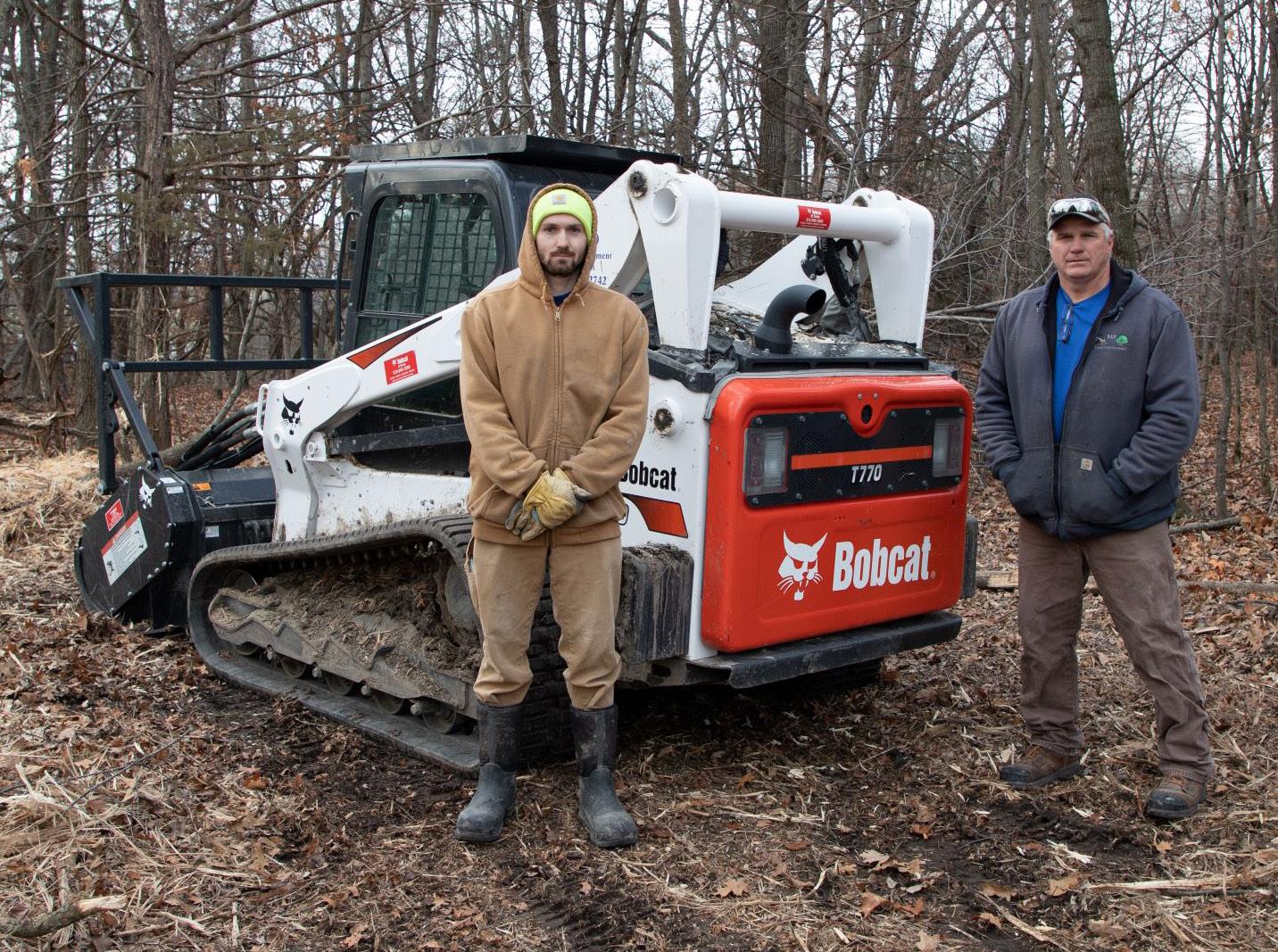

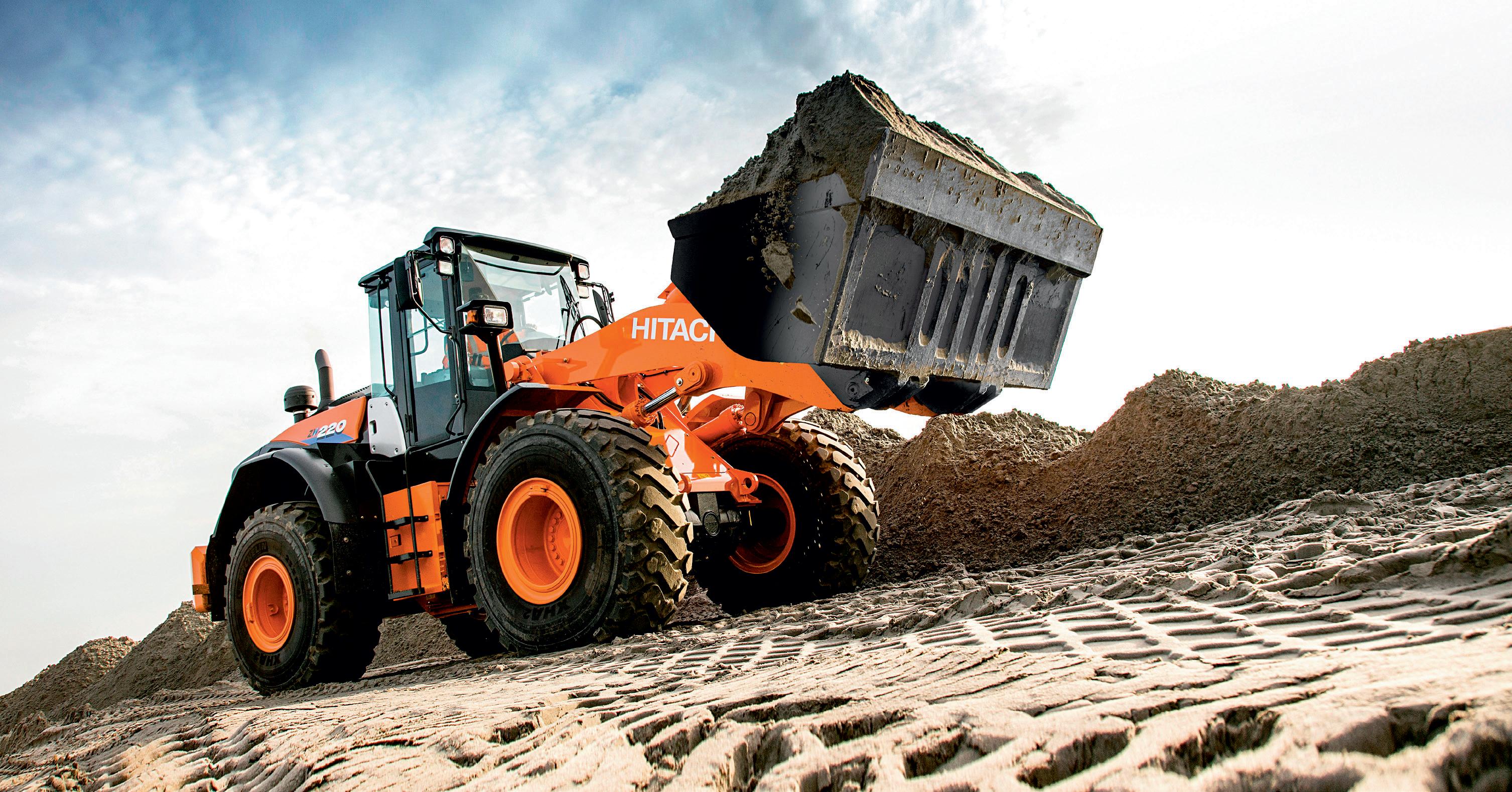
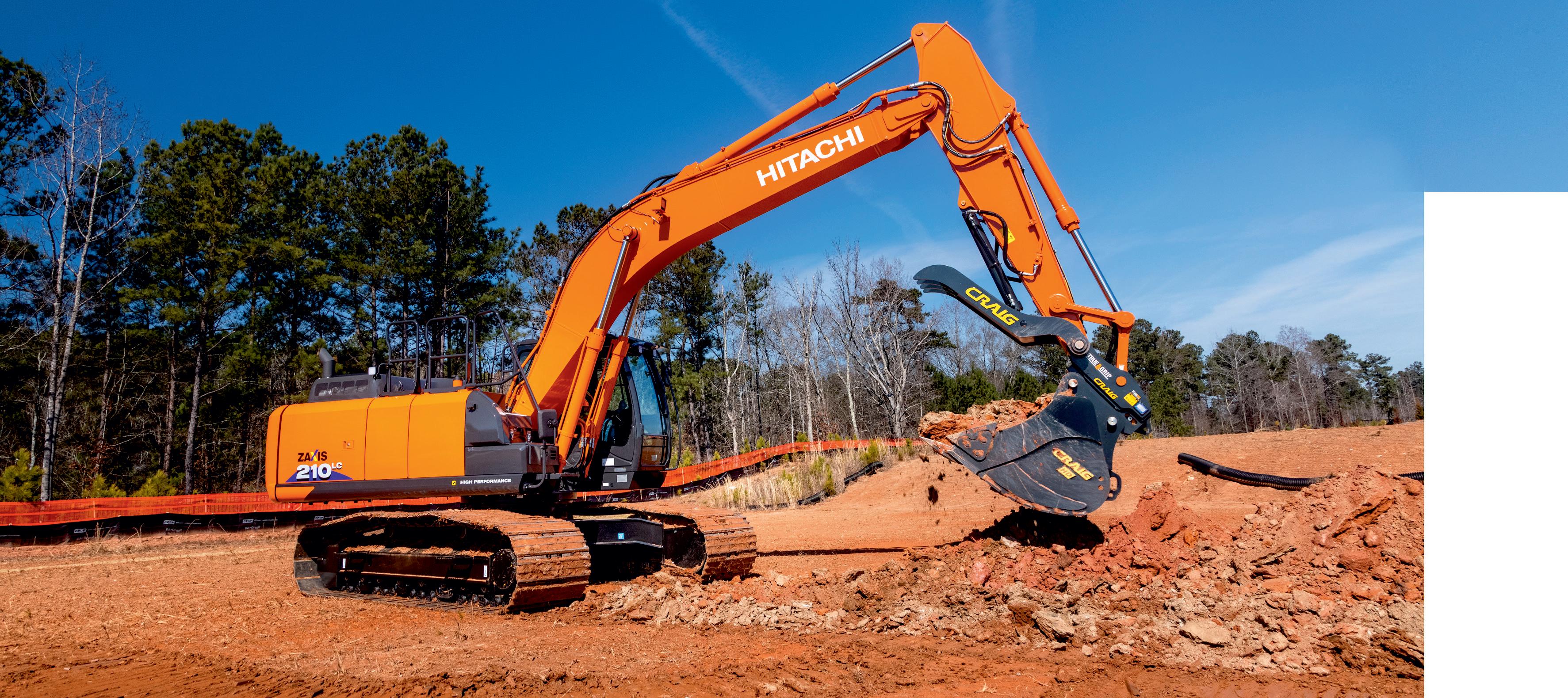
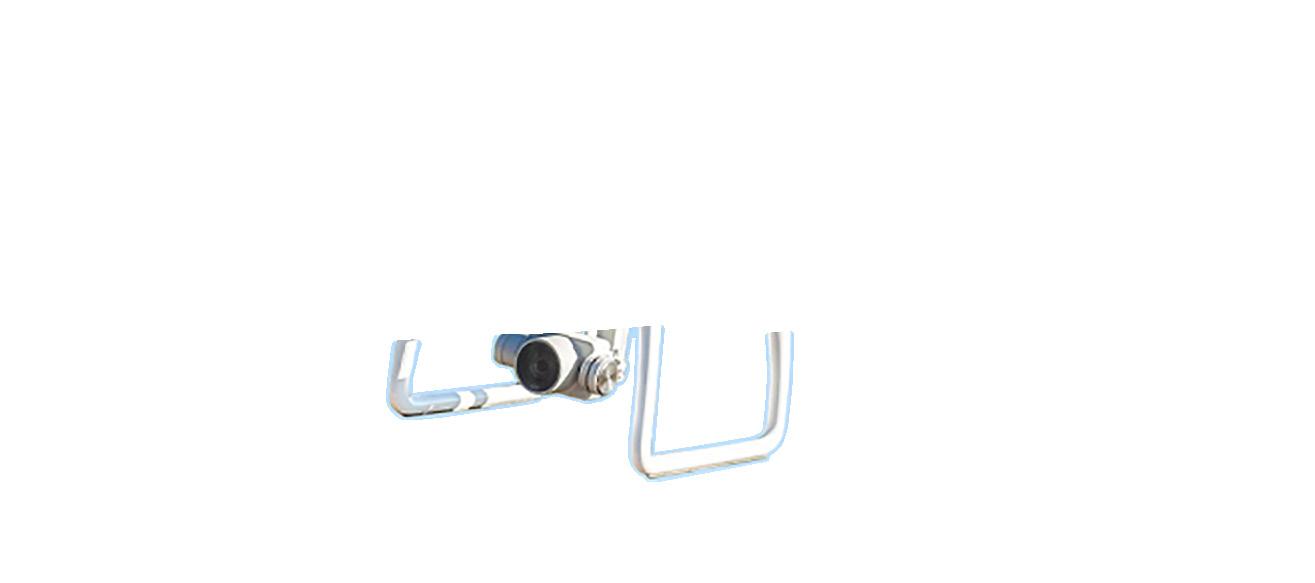

Drone surveying is one of the most effective ways to upgrade your construction workflow, but it’s important to understand a few key laws and processes.
A key best practice is to always check the rules surrounding the airspace in which you intend to fly so you can conduct your flight without issue.
Switching from traditional base and rover surveying to drone surveying is one of the most effective ways to upgrade your construction workflow, setting you and your team up to make better, datadriven decisions.
Drones are more efficient, shaving days or weeks off typical surveying time. Since today’s drones are cheaper and simpler to use, you’ll be able to capture on-site data more effectively without expensive surveying equipment. Drone imaging allows you to collect and analyze data whenever you need it and, with the right processing software and ground control, you can achieve survey-grade accuracy throughout your site.
One of the biggest perceived obstacles to starting a drone program is airspace and flight regulations. These regulations are actually easy to follow, and by understanding a few key laws and processes, you’ll be collecting survey-grade data with drones in no time.
To that end, this article will cover the following: ˜ What makes something a drone ˜ Registering your drone ˜ Getting licensed to fly ˜ Licensing resources (study guides, where to take the test) ˜ Understanding where you can fly ˜ Airspace restrictions ˜ Special waivers
COMMERCIAL DRONE REGULATIONS
A drone is a type of aircraft, albeit a tiny one. All unmanned autonomous vehicles (UAVs) are regulated by a country’s aviation authority, and rules around how, when and if you can fly differ by country.
Each country and region has different UAV rules and regulations, with Australia and the EU introducing new regulations in 2021. For locations in the Asia Pacific region, refer to the International Civil Aviation Organization’s guidelines.
In the United States, each drone must be registered with the Federal Aviation Administration (FAA) on the FAADroneZone website (https://faadronezone.faa.gov), and every commercial drone operator must hold a current FAA Remote Pilot Certificate (https://www.faa.gov/uas/ commercial_operators/). This certificate is for anyone who makes money by flying a drone, including survey teams and photographers, and is meant to ensure drone pilots have a basic understanding of what other commercial pilots are doing in the surrounding airspace.
The “Unmanned Aircraft General – Small (UAG)” test to obtain the certificate is straightforward and involves a multiple-choice test with 60 questions centered around keywords and understanding a sectional chart, a specialized airspace map that doesn’t require GPS to be read. There are free practice tests online (https://bit. ly/3uTCzhX), as well as multiple study guides you can use along the way. To take the actual test, simply establish an FAA tracking number (https://bit.ly/3v0t6Wl) and schedule a test time on the FAA website. Once you pass, fill out the FAA Form 8710-13, obtain your certificate and renew every two years. (Access the full breakdown on how to become a drone pilot at https://bit. ly/3GVSnDk.)
Licensees operate under the FAA’s Part 107 Small Unmanned Aircraft Rule, which has two major tenets: a drone must be kept within the operator’s visual line-of-sight and below 400 ft. in altitude. These requirements can become difficult to follow when surveying large sites that may have dangerous topography or small spaces that are challenging for surveying teams to navigate.
Luckily, the FAA can grant Part 107 waivers to individual surveyors or surveying teams, allowing them to bypass these requirements. To apply for a Part 107 waiver (https://bit. ly/3rTwCQj), applicants simply include a full description of how they use their drone and how the pilot will comply with specific performance-based standards. This waiver unlocks much more freedom in equipment use and is instrumental for larger construction sites.
A key best practice is to
All images courtesy Propeller Aero
Since today’s drones are cheaper and simpler to use than traditional surveying options, you’ll be able to capture on-site data more effectively without expensive surveying equipment.
always check the rules surrounding the airspace in which you intend to fly (https://bit. ly/3LEi1Qw), so you can conduct your first flight without issue. Finally, keep in mind that these regulations will differ between countries, so make sure to stay informed on the latest restrictions in your region.
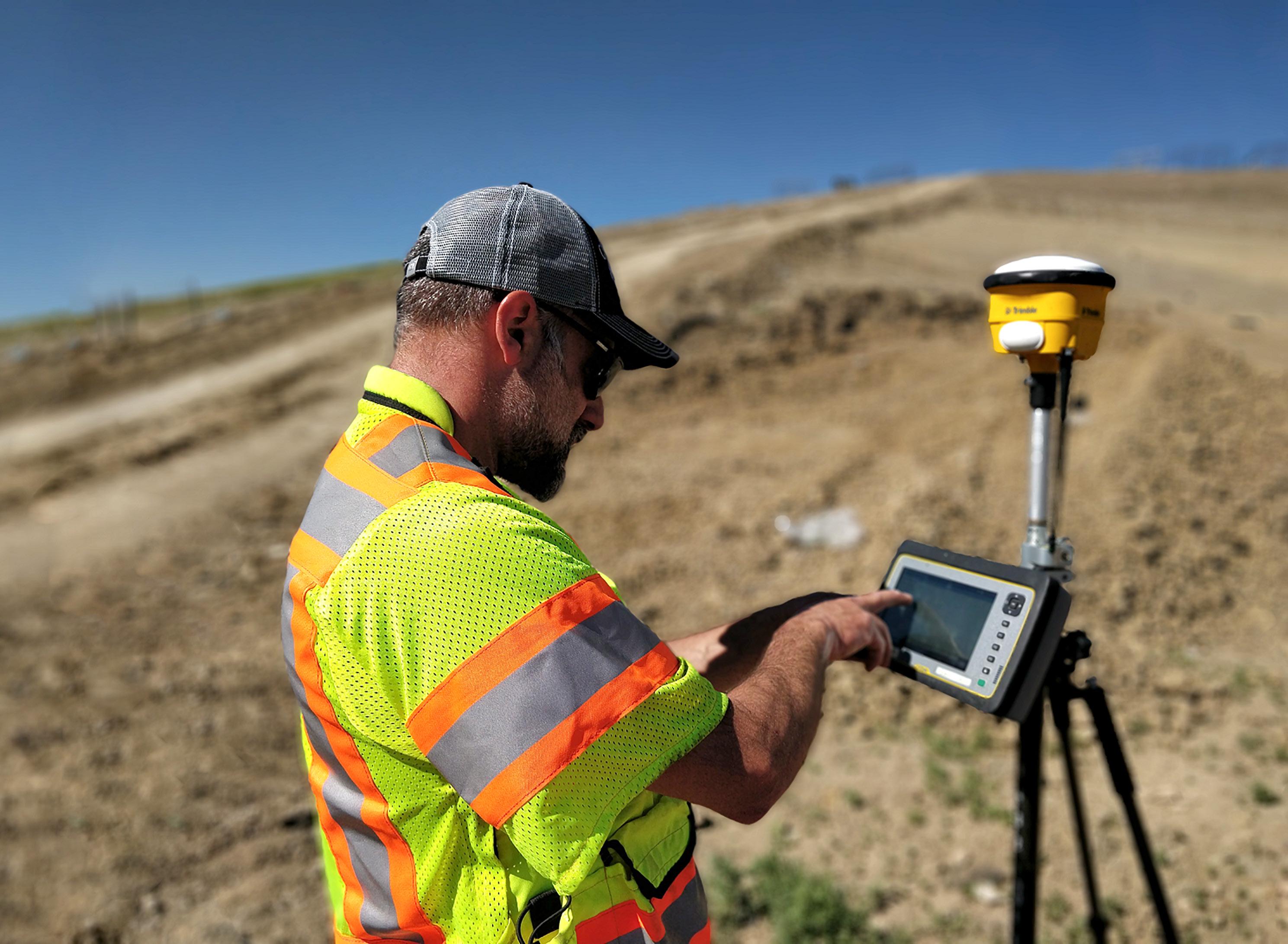
NAVIGATING RESTRICTED AIRSPACE
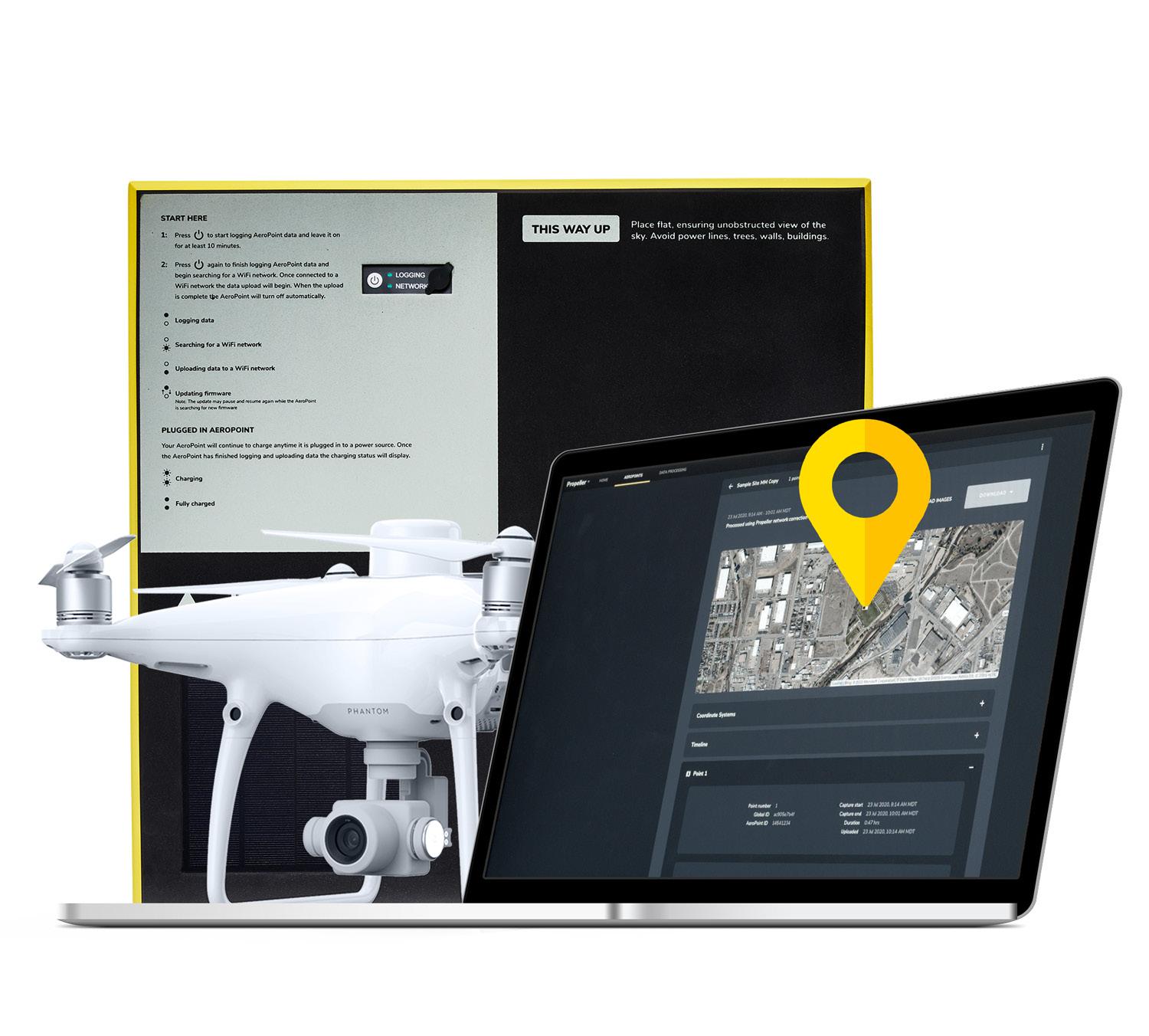
Once you obtain the necessary license and comprehend national regulations, understanding whether the airspace in which you intend to fly is restricted is another important step before beginning a drone program.
Airspace is the portion of the sky that’s controlled by a country above its territory. In the U.S., airspace is divided into six classes, which indicate its use and restrictions. For example, airspace at or below 2,500 ft. near airports with control towers is Class D and it’s controlled, so you would need authorization before attempting to fly in this area.
Without getting into the many airspace nuances and allowances, make sure you stay vigilant for the following when assessing your construction site: ˜ If your site is near an airport or helipad ˜ If your site is near a military base ˜ If your site is in an urban environment
If you discover the airspace you need to fly in is controlled, you’ll need to gain additional authorization, usually from the airport or military.
If you’re looking to fly near one of 500 participating airports, you can get authorization via the Low Altitude Authorization and Notification Capability (LAANC) program, which will drastically cut down on the time spent waiting for authorization to fly drones in controlled airspace. All you need is to prove you’re operating within Part 107 regulations and flying under a certain height within a square mile of the airport, and you can get authorization immediately. You can obtain LAANC authorization through several FAA-partnered companies and apps, like AirMap.
Finally, if you’re using a DJI drone and have obtained a hardware unlock (which will tell the hardware of the drone it’s okay to fly) and an airspace authorization waiver such as the LAANC, you can use the DJI Fly Safe portal to streamline the process of requesting to unlock restricted airspace, especially if you often fly in these zones.
TAKING FLIGHT
Navigating drone licenses and regulations might seem daunting at first, but the steps to reach your first flight are clearly laid out and the restrictions are straightforward. With your remote pilot license and a knowledge of the space in which you’ll be flying, you and your team can confidently take to the skies to obtain survey-grade site data in a fraction of the time. ET
Margaret Farmakis is the vice president of customer solutions for Propeller Aero.
If you’re using a DJI drone and have obtained a hardware unlock (which will tell the hardware of the drone it’s okay to fly) and airspace authorization waiver such as the LAANC, you can use the DJI Fly Safe portal to streamline the process of requesting to unlock restricted airspace, especially if you often fly in these zones.
Concrete Contractor Forms Advantage with ROBOTIC SURVEYING
Contractor benefits from robotic total station on a $400 million research center expansion project.
Orlando, FL-based Universal Forming, Inc. (UFI) offers a wealth of services ranging from preconstruction to formwork to complete concrete structures. While the formwork facet of the job has long relied upon total station technology, the company recently upped its game with the addition of a robotic solution.
The decision fits perfectly into Bill Nagele’s penchant for getting better results while minimizing manpower-intensive efforts and reducing the risk of error. That’s a key reason his company relied heavily on a Topcon robotic total station on the recent $400 million expansion of the Moffitt Cancer Research Center in Tampa.
FOCUS ON PRODUCTIVITY
UFI was formed in 2005 when Nagele and Todd Volheim decided to combine their 40 years of successful concrete construction experience and establish a company that could expertly build and provide construction management of large, complex concrete structures. Today, the company employs more than 400 people, has weathered downturns that others couldn’t and has established itself as one of the leading concrete structure builders in the state of Florida.
“I own the company, but at heart, I am a production person and always have been,” says Nagele. “When I was younger, I would watch guys work and instantly spot ways in which they could improve their efforts. If they were putting two nails per foot, I could see that putting one nail every 10 in. could save time without forsaking quality. And I think that’s why we’ve been successful as a company; we are far more productive than our competition.”
That focus on productivity extends to Nagele’s choice of instrumentation used for layout. He notes that he’s been doing work of this type since he was 15 years old starting out with ABOVE: Getting better results while minimizing manpower was a key reason UFI used a Topcon robotic total station on the $400 million expansion of the Moffitt Cancer Research Center. LEFT: While construction survey/layout efforts have traditionally been a two-person operation, robotic total stations have opened the door to those tasks being performed by a single individual.
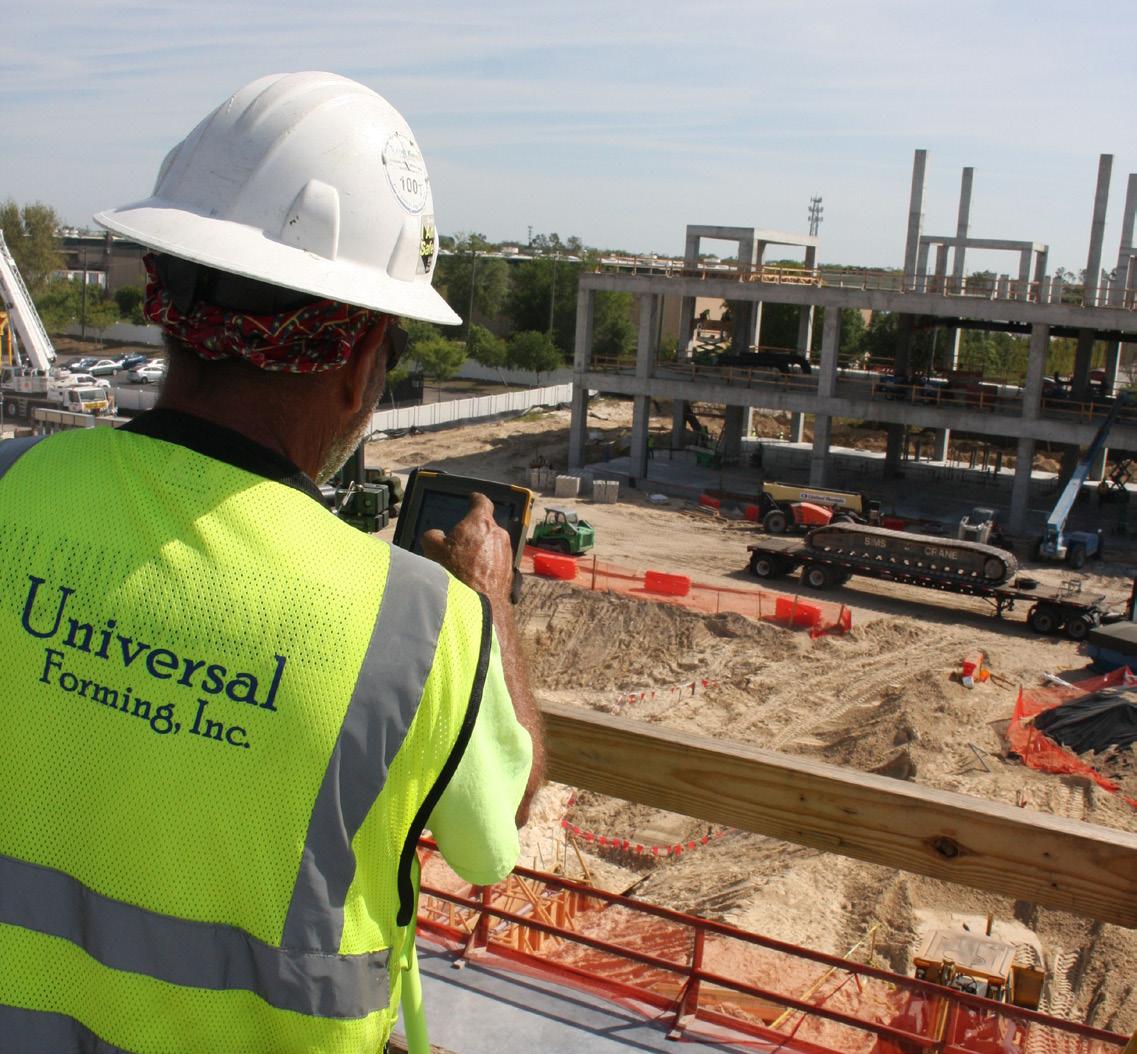
a Wild T-1 theodolite, and has seen an impressive evolution of survey technology along the way. His survey gear preference leans toward those that can provide the accuracies demanded on the jobsite but are easy for his crews to understand. That’s what led him to Topcon.
“I liked the fact that Topcon solutions were designed for simple operation, which meant I could easily train my staff,” he says. “That helped us really get going in the early days. Once we got into it, however, we went full bore into total stations, then added a prism-less capability. As a company, we evolved right along with the technology.”
RESISTANCE TO CHANGE
That evolution hit something of a speed bump when robotics entered the scene as a means to further enhance total station performance. While many of UFI’s younger and more tech savvy personnel embraced the technology and saw the benefits it could provide, a good many of the
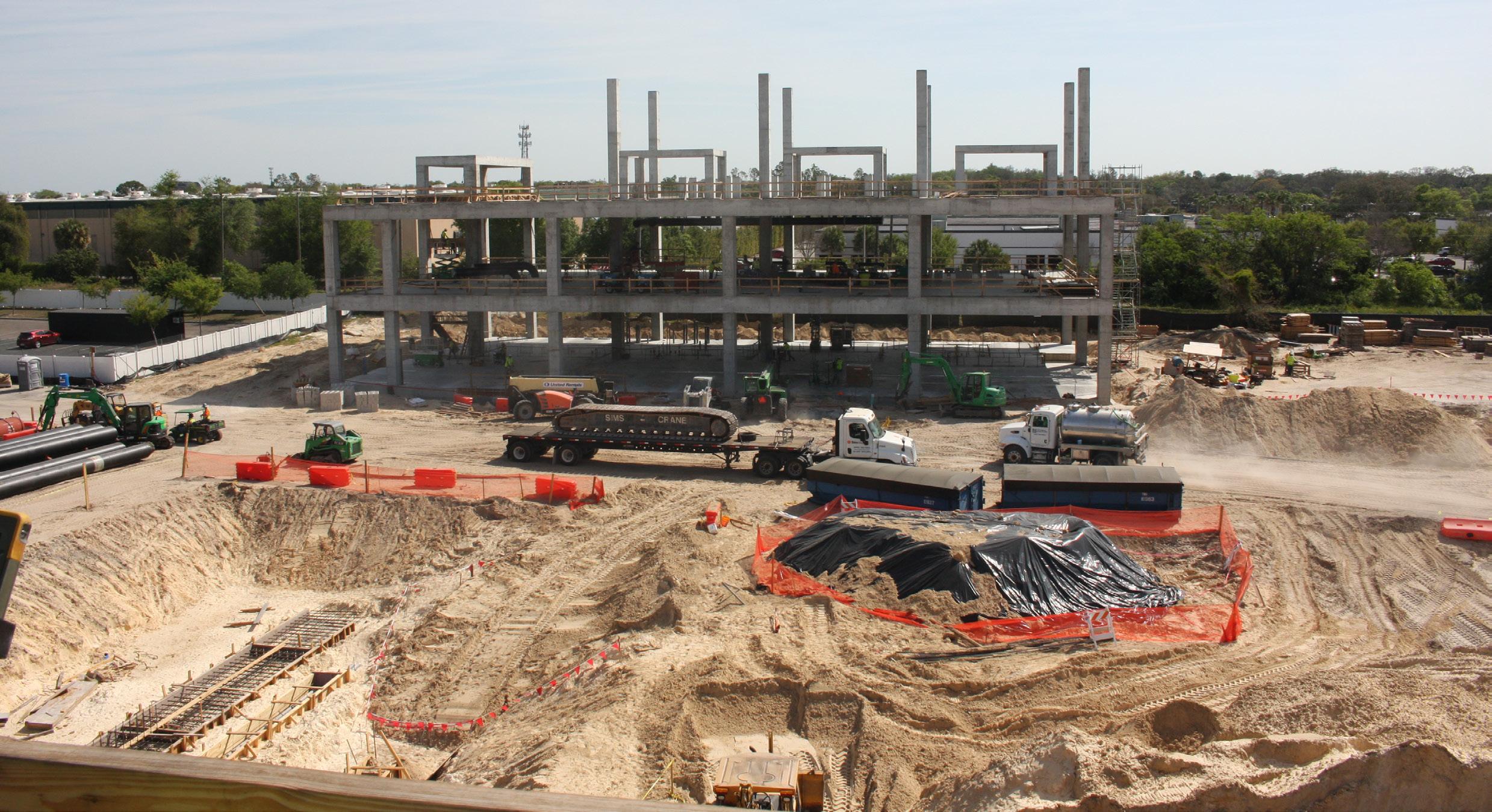
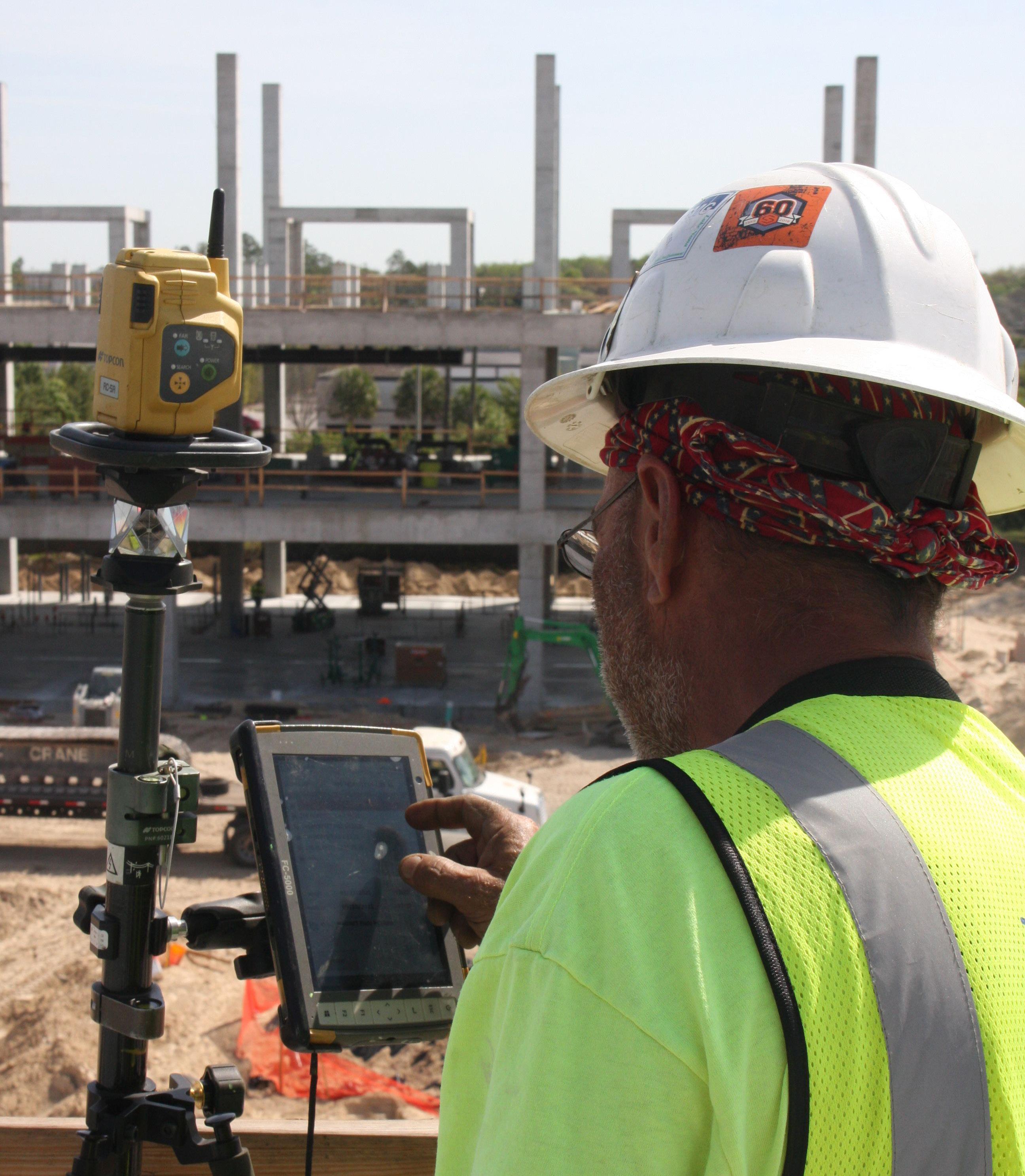
ABOVE: UFI is responsible for creating the shell for the structure. In that capacity, surveyors appreciated the speed and ease of use of the Topcon GT-503V robotic total station. LEFT: The robotic total station takes some of the heavy reliance on math skills out of the equation, broadening the labor pool.
“seasoned” crew members were resistant — and remain so to this day, says Nagele.
“It’s a tough sell to a person who will not even use the simplest of data collectors,” he comments. “What I see as streamlining the workflow, they see as threatening to take their jobs away. However, I currently have a little more than half of my people embracing the solution and that number will continue to climb as the older personnel retire.”
Because Florida is such a transient state, getting workers to buy into construction as a career is challenging enough. Getting people who are capable of tackling some of the math associated with layout is another matter entirely.
“The robotic unit takes some of that heavy reliance on math skills out of the equation, broadening the labor pool for us,” Nagele points out. “And the simplicity of the solution makes it much easier to train a person in layout work. The ones who use this robotic total station on a regular basis swear by it. Unlike the older crew members, there’s no need to convince them of its value.”
FAST, EFFICIENT SOLO SOLUTION
Dave Yanna, one of UFI’s layout/survey technicians, got his training with the U.S. Forest Service in Michigan before entering the private sector in 1986. Since then, his life has revolved around layout work for building construction.
Yanna’s most recent layout effort was at the Moffitt expansion project where UFI is responsible for creating the shell for the structure. In that capacity, he appreciated the advantages of the Topcon GT-503V robotic total station.
“The biggest and most obvious benefit is the speed of the gun,” he says. “I’ve used many other total stations over the years and this, by far, is the fastest. Even when I’ve been several floors below the instrument and laying out for the adjacent power plant building, it tracks me and holds me better than anything I’ve ever used. And should something come between me and the gun, it quickly reacquires my prism and resumes tracking.”
While construction survey/ layout efforts have traditionally been a two-person operation, the advent of robotic total stations has opened the door to those tasks being performed by a single individual in many cases. Yanna does occasionally work alongside another person but sees working alone as far more efficient.
“Bill has asked me in the past if I needed a helper and I said I’d take one if I had to, but I really don’t need anyone else,” Yanna comments. “On this Moffitt job, working alone with the robot, I am placing hundreds of points on each floor. I am doing things faster, better and more accurately than if I was working with someone on the other end of a radio telling them to go left 1 ft., right 6 in. and so on. I have all the [information] right on my data collector, so as fast as I can move, I can mark a point.”
And although other trades such as plumbers and electricians still have to gather their own layout points for water lines, waste and gas lines, pass-throughs, etc., they are doing it based off Yanna’s control points, resulting in a savings to them, as well.
“I love the robotic approach because I tend to know exactly what I want to stake and where I want to do it,” Yanna says. “If I have a rodman who’s not in tune to the project, there will be a delay. And because many facets of this job are repetitious, I can often put the rod down and be within an inch of where I need, which is much faster than explaining to someone what needs to be done, then doing it.
“In fact, if I had a helper right now, the only help he would provide is carrying my gear up six stories,” he adds. “For me, this is the only way to work.”
MORE EFFECTIVE TEAMWORK
It’s important to note that while some of UFI’s people, like Yanna, function well as a solo act, there is just as much value to be derived when the robotic solution is used as part of a team effort.
“One-person crews are great from a layout perspective, but our work is about more than just shooting forms,” says Nagele. “There are elevations, inbed locations and so on that have to be done. So, in those cases, we still utilize a team — but it is a far more efficient team with the robot.
“When robotic total stations first hit the market, I was admittedly skeptical,” he acknowledges. “However, once I saw the accuracies the GT-503V could get us, I was totally on board with the solution. In this business, if you lag behind, you’re left behind. And lagging behind anything has never been an option for me.” ET
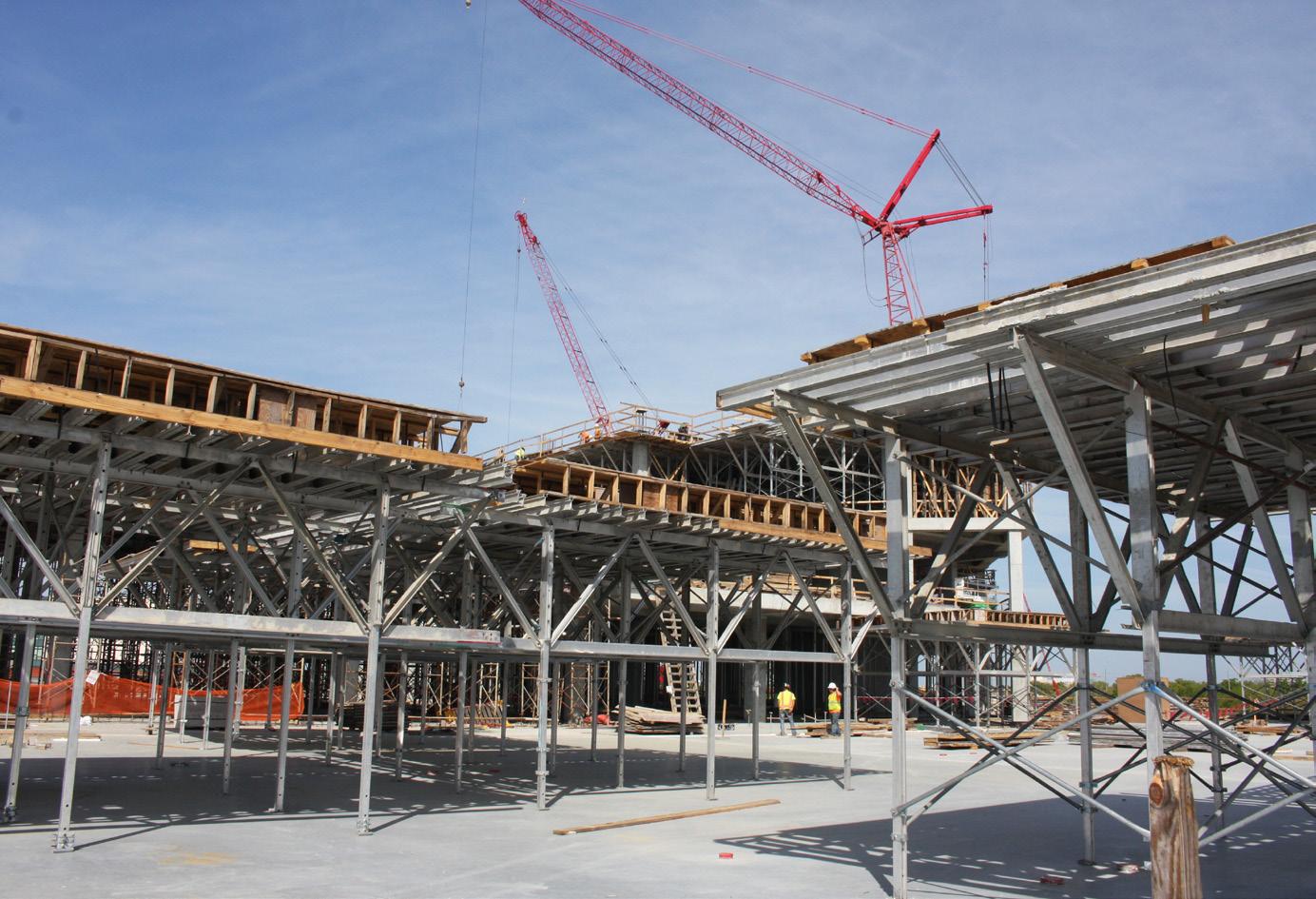