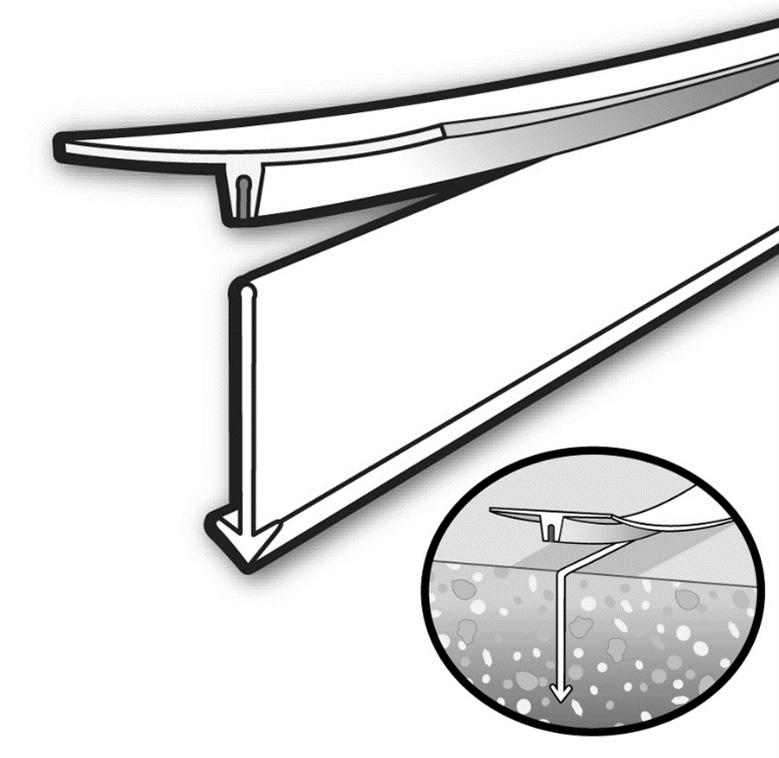
2 minute read
INSIDE THE ACI CONT
Insert Joints
Insert joints have a rigid or flexible material embedded into the fresh concrete. In the past, Masonite strips were inserted into the concrete. Today, rigid plastic strips (Zip Strips) are more common and typically 10-ft. long. Workers walk in the fresh concrete to insert the strips by hand. Sometimes a long metal angle is used to make a groove prior to inserting the strips. This assists in establishing a straight line and assuring that the insert has a vertical orientation in the slab. Without the prior groove, problems can arise with lack of straightness of the joints or the inserts may not be vertical. Strips, which are installed at a slant, have a top edge that is less than 90 degrees. The thin edge is vulnerable to breaking off. These inserts are used in relatively small slabs, such as residential houses, retail stores, and utility slabs.
The new insert method, called Trak Joints, are installed using a tool called a Traker. The Traker is used to embed a continuous, folded, flexible plastic strip into fresh concrete—either before or immediately after bull floating. The plastic strip is pulled off a roll and then folded in half by an insertion disc, just as it is embedded in concrete. A long-handled pole or rope is used to push or pull the Traker across the slab. The strip remains in the slab as concrete finishing operations occur over the strip. The appearance of the Trak Joint, after the joint activates, is a relatively straight crack in the slab.
Applications for Trak Joints are limited to uses where straight-crack joints are acceptable. Such applications are residential house slabs (where floor coverings are used), utility slabs, pathways, parking lots, and roads. A few advantages of Trak Joints are: no silica dust is created; the embedded plastic tape adheres to the walls of the crack, so curing of concrete in the joint is effective; rainwater is deterred from entering the joint and wetting the subbase soil; and, after the slab is in use, moisture vapor emissions are prevented from rising through the joint. The most significant advantages are reduction in random cracks and reduced cost over that of other joint methods.

Conventional Sawcuts
Conventional sawcut joints have been used for a long time so the equipment and blade technology are well understood. These joints can be cut dry or wet. The appearance of the joints is neat and clean. The main disadvantage is that due to the wait time for the concrete to become sufficiently strong, so that aggregate particles are not dislodged by the sawblade, the timing for joint installation can easily occur too late. For certain jobs, sawcutting needs to occur after workday hours, so a decision is made whether to wait until the following morning to cut. This overnight delay can result in the formation of random cracks.
Harvey Haynes established Haynes & Associates LLC in 1982 to provide concrete consulting services to the construction industry and legal firms. He focused his career of over 55 years on the study of concrete as a construction material and applies his knowledge to the investigation of concrete problems. Mr. Haynes is a Fellow of the American Concrete Institute.