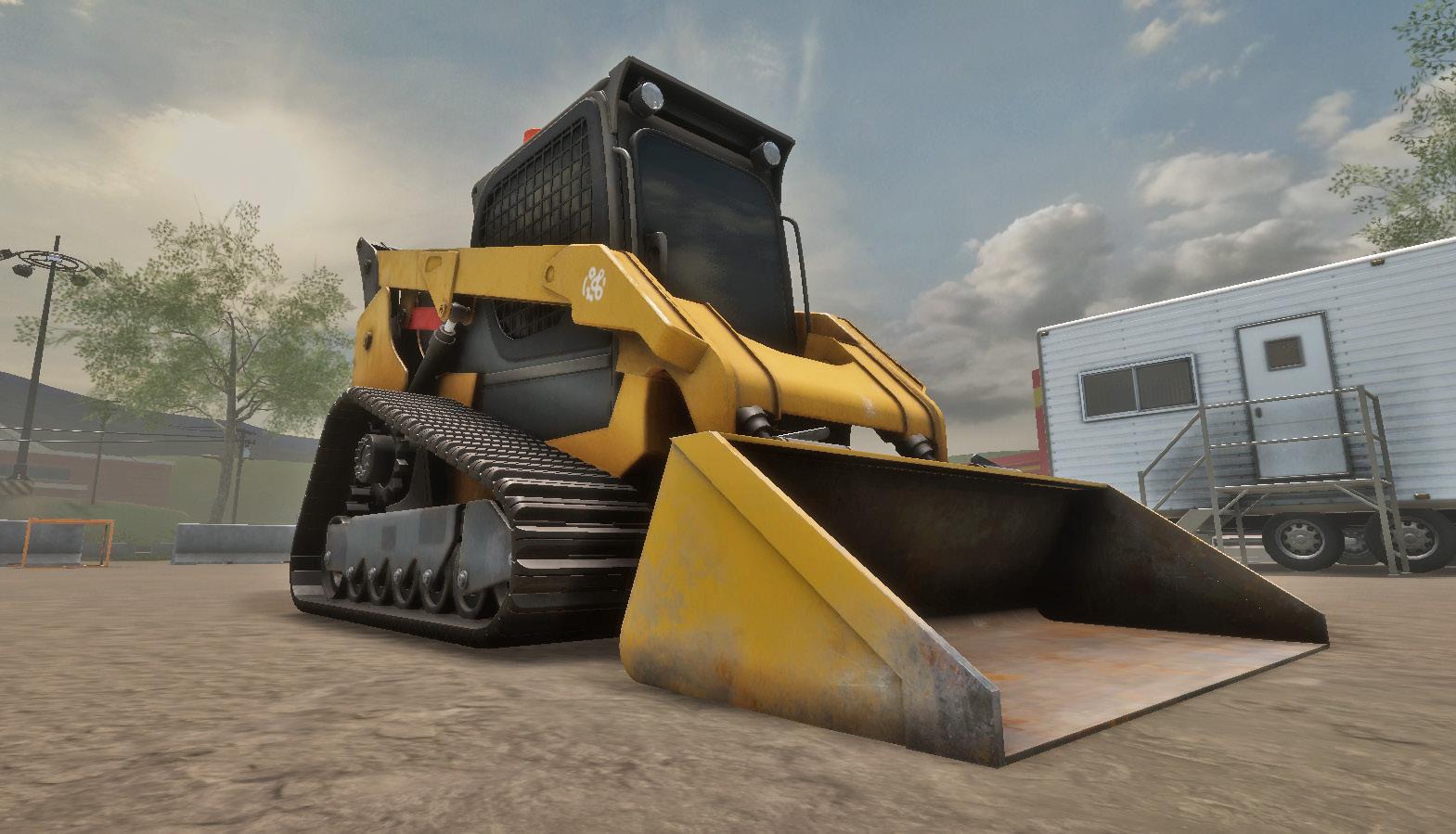
12 minute read
Does Training in a Simulation Translate to Real- World Skills?
Does Simulation Training Translate to Real-World Results?
The ROI for simulation training shows broad benefits to both workers and employers who need skilled people on the job quickly. CM-Labs uses cutting-edge technology to level-up your business
The integration of personal computers into the normalcy of daily work and life is so ubiquitously intertwined now, that we hardly notice or pay much attention to it. It is everywhere. Smart technology is in every corner of our homes, our cars and even our job sites. While this can be a shock and a challenge, at times, as some struggle to adapt to these digitalchanges, the truth is that ultimately the benefits outweigh the growing pains. This is especially relevant at a time like the one we are living through.
Worker shortages are something every industry is currently facing, and this is an even more critical problem where the know-how for the job traditionally required hundreds of hours of hands-on experience to do them. In the past, perhaps, a new employee would start on a construction style job as a general laborer, and slowly work their way up over a number of years, operating more complex machines and more precise tasks. It took a long time to earn the kind of experience needed.
That kind of process was gradual, and it allowed employers and production managers to test and select candidates at a relatively slow pace. It allowed for job-seekers time to size-up the work expected of them in those roles too, and decide if continuing on that path was right for them. Just as an example, some crane operators had to log 400 hours of experience before being considered fully certified. To speak in very broad and general terms, this is no longer a viable option in the post-pandemic reality.
Now emerges an increasingly large gap between the previous paradigm, and the one faced today by companies eager and, in some places, desperate for people who can do the job both safely and skillfully. If you're going to stay competitive, not only in the terms of labor, but also in terms of overall business success, a new approach must be adapted. Thankfully, there are a host of new solutions for employers in order to radically and safely change the way new-hires are trained, properly tested and made real-world ready.
WHY IS THIS HAPPENING?
According to the Schwartz Center for Economic Policy Analysis, older adults (aged 55 and up) left the labor force and stopped looking for new work in record numbers since the start of the COVID-19 pandemic in March of 2020. The American Association of Retired Persons reports that more than 2 million workers were forced into an early retirement due to either health or economic reasons, or in a lot of cases, due to a combination of both.
A whole generation's worth of technical skill and know-how has disappeared from the labor force much more rapidly than normal. Skilled laborers, heavy machine operators, and the varying array of support workers that make infrastructure jobs like asphalt paving and road-building functional aren't there to do the jobs anymore, and they
A decidedly human touch to plant automation.
Designed around real people.
“The plant control system that MINDS designed for us has worked very well. The graphics depict the plant almost identically as built and are very easy to follow from the control room. Each value is shown with its position indicated by colours that make identifying issues, such as a stuck valve, extremely easy. The materials that we have produced with the system have been very consistent from the fi rst production run.”
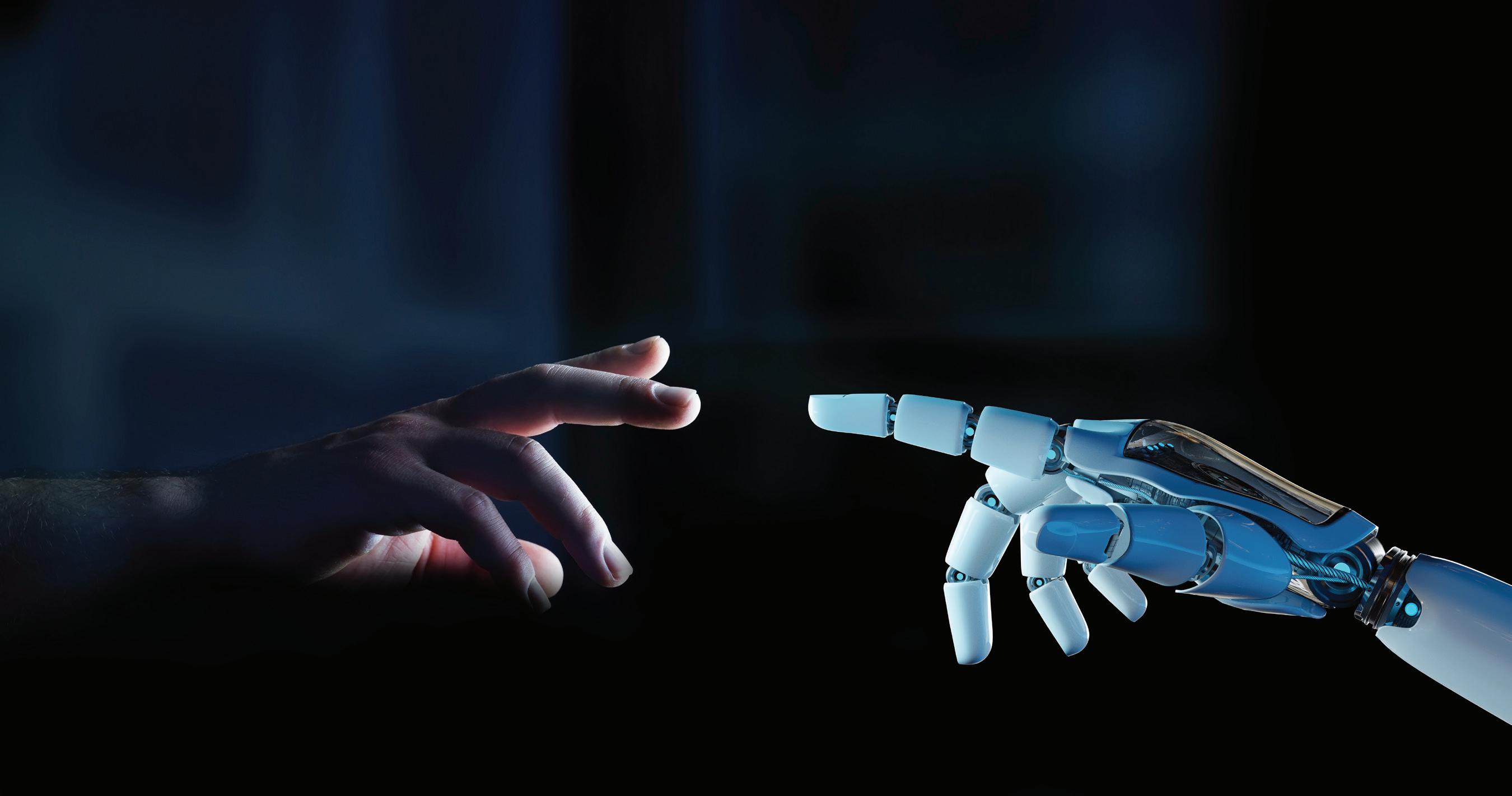
Allen Hendricks, Vise President, Asphalt Divisions Manager Blythe Construction, Inc.
For the past 25 years, MINDS has built a reputation for user-friendly, advanced, customizable plant automation control systems. As of April 2022, we became part of the Astec family to add to their Rock to Road solution for asphalt road building. MINDS provides award-winning desktop software, mobile apps, and hardware for many applications:
Drums, Batches, Combo/hybrid hot mix plants,
Emulsion plants, Liquid Terminals. Silo load-out, Ticketing, and Cloud-based data management for the Rock to Road industry.
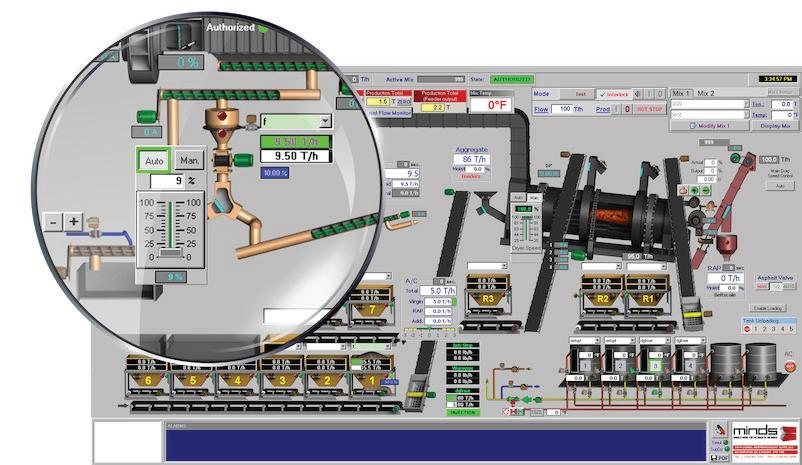
Better data. Increased control. Higher profi ts.
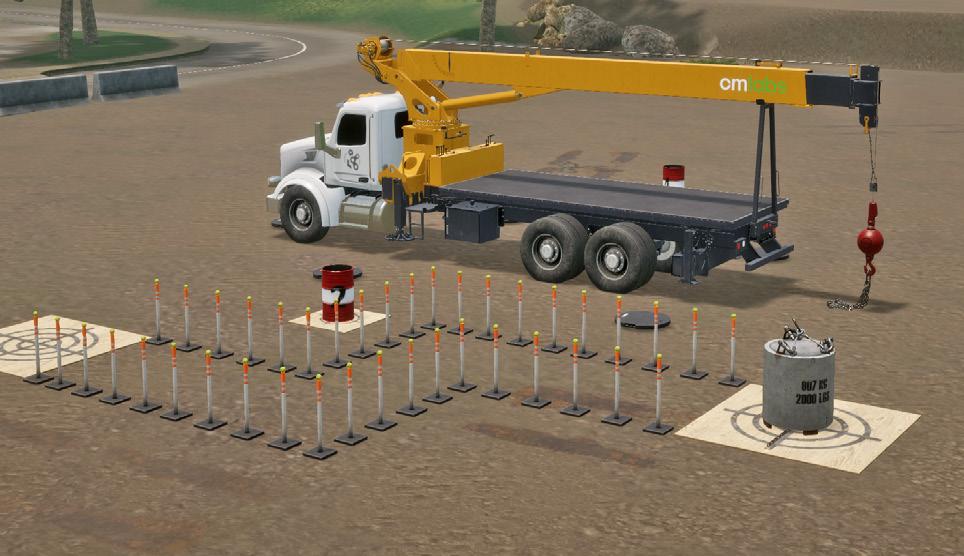
Provided by CM-Labs aren't there in as great a numbers to pass on the knowledge that they have.
Last year, an analysis by the Nation League of Cities (NLC) reported that 3 out of every 10 infrastructure jobs (those related to design, construction or maintenance) were have more difficulty finding someone to fill the open position, compared to other industries. NLC determined while 19 days was estimated as the median time between job posting and hiring a candidate, in the case of infrastructure, it was taking 23 days 30% of the time.
“Labor shortages, misalignment between workforce systems and industry needs, a large wave of retirements and lack of education...creates significant employment challenges for the infrastructure industry. Moreover, many workers do not have access to the skills training and development programs necessary to build experience for higher-level positions, limiting career pathways to higher and more stable employment and pay.” -NLC Press Release
When we put these realities together, a clear picture of the problems faced by businesses emerges. Large losses of established labor. A void in personnel qualified to train others on-the-job. Difficulties finding and placing new workers in available employment opportunities. This is the domino effect that CM-Labs, a software and simulations development company, steps into the middle of. They offer customizable solutions for infrastructure based companies, and they back them up with measurable results.
ENTER THE SIMULATION
Originally founded as Lateral Logic in 1994, then CM-Labs in 2001, the company was focused on ground vehicle simulations. Christa Fairchild, product marketing manager from CM-Labs insists that, despite the outer appearance looking very similar to an arcade video game, these are very serious machines. "It was a very academically founded company," she said, "Lots of patents and research, academic research that was invested in developing the secret sauce, shall we say, in our systems."
The "secret sauce" she refers to is the company's proprietary software and physics engine that makes the simulations possible. It's the unique code that sets the "rules" for the simulation’s gravity, space, lighting and more. They call the engine "Vortex" and it is the essential component to the success of their training modules. A collaboration with Trimble GPS means high fidelity, realistic earth-moving physics and accurate immersion.
Fairchild continued, "Objects are simulated in a realistic manner. When you sit in the simulators, they react in a way that would reflect what would happen in real life. That's really important, because if you're going to train on a piece of equipment that doesn't reflect what happens in the real world, you're setting yourself up for some surprises, both efficiency wise and safety wise."
A DANGEROUS GAME
Alan Limoges, product manager at CM-Labs, added to this sentiment, explaining more about the benefits of creating custom training scenarios, "We look at vehicles that have a lot of accidents. What role can simulation play to help prevent these accidents? And where is there a need in training? These are heavy pieces of equipment that are not the first piece of equipment a new, green operator would sit on. Simulation comes into play so they can get exposed to these machines early on. Then when they see them in real life, when they hop on the real machine, they have the confidence and it's much safer."
According to the Occupational Health & Safety Administration (OSHA), the construction industry suffers from one of the highest incident rates among high-risk industries. Statistics from the Department of Labor indicate that, in a single year, construction workers accounted for 1,008 or 21.1% of work-related fatalities. In the simulation, these incidents can be better trained for and avoided, as a new or novice operator can get hands-on experience in realistic environments and situations. Instructors can trigger weather conditions and randomized events to test how the trainee handles them.
Using simulators is also a huge savings, over the long-term, considering all the metrics previously involved with traditional training methods. If you needed to train someone on a piece of heavy machinery, you needed access, fuel, good weather, proper insurances, instructor time, and more. It starts to add up. With the simulation platforms like what CM-Labs created, it doesn't matter what the weather is like. You don't need to waste costly fuel, and you don't have to stage a setting for them to practice in. It's all self contained.
So, the simulation addresses two of the current problems, but what about the staffing shortages? The best training in the world isn't any good if there's no one to train, right? Well, the CM-Labs platforms are beneficial here, as well.
READY, PLAYER ONE?
Even though CM-Labs didn't start out in the video game industry, the video game industry has grown so ubiquitous that it is having a positive side-effect on the use of their training platforms. That is because of the general familiarity that people, especially younger generations, have with similar hardware and software as they are exposed to it when they play video games. They share certain commonalities, and it has an impact.
Limoges said, "with regards to
Provided by CM-Labs
recruitment and targeting younger workers, those people are much more familiar with interfaces like screens and joysticks, which are part of the actual equipment that's being used. They're learning very quickly, but it is also attractive to them, because the simulation and the simulators are just awesome to look at. They can create the tone of what you are going to expect working for the company, and can be a symbol for the recruitment process. They're also very mobile, which means you can bring them to schools and job fairs and actually get people started on them right away. It's a great way to connect with the next generation." However, it isn't exclusive to young people. A demographic report on video game usage by Newzoo, a market research group for game companies, found that time spent playing video games is higher across the board. Even the Baby Boomers are getting in some screen time. Here's a breakdown by generational group that shows what percentage of those surveyed play any video games, and how many hours they play on average per week: • 42% of Baby Boomers / 2.5 hrs • 60% of Gen X / 4.5 hrs • 77% of Millennials / 7 hrs • 81% of Gen Z / 7.5 hrs
Even though these numbers aren't directly tied to the way employment interests will play out, it is significant to see just how invested the contemporary work-force is in spending time each week in simulated environments. No matter what demographic you’re targeting, the CM-Labs platforms have a high ceiling when it comes to their training potential.
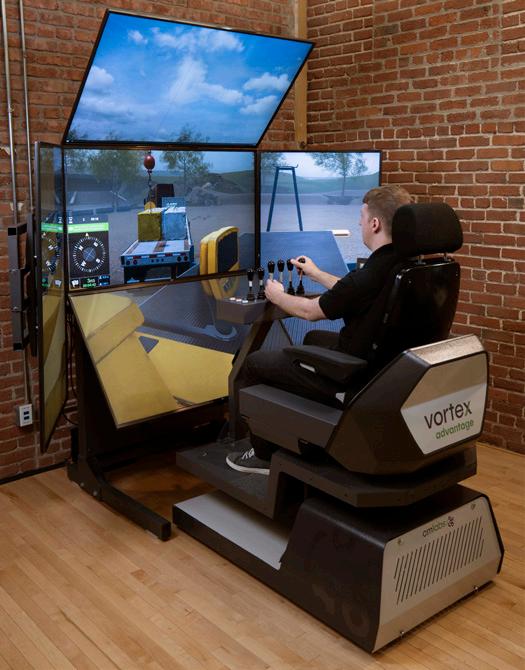
THE HARDWARE
We discussed a lot of things so far: the market conditions, as well as the software that makes the CM-Labs’ simulators tick behind the scenes. Now, let's take a moment to look at the three off-the-shelf physical simulator platforms that CM-Labs offers, how they are different, and which situations they are individually suited for.
Vortex: Edge Plus
The Vortex Edge Plus simulator is a complete training solution that can run CM Labs’ full fleet of earthmoving, lifting and forestry equipment training packs. It's an off-the-shelf platform, meaning you can buy and use it with a minimal amount of set-up. This version is literally a "desktop" piece of equipment, with a giant screen, laptop computer, table mountable joy-sticks and steering wheel, as well as a variety of foot pedals that rest on the floor. It also comes with a carrying case for all the pieces, making it a truly idea option when space is at a premium, or if the training location needs to be relocated frequently. This iteration is great for the beginner as it contains the same proprietary simulation software and realistic physics, but it does not include the chair motions or feedbacks that can tilt or shift weight, providing that great depth of immersion and realism. Edge Plus is helpful in gauging interest, teaching skill and testing basic competencies.
Vortex: Edge Max
With a rugged, stripped-down design that minimizes simulator costs, the Vortex Edge Max includes the same heavy-duty controls an operator would use on the actual equipment. The single, large forward screen rotates to provide an optimal field of view for every piece of equipment. This unit is its own space. Instead of needing the desk or table, the chair and the display are built as a single piece of equipment. The chair is a fully functional motion platform, its biggest upgrade over the Edge Plus, and is capable of meeting a large percentage of a contractor's training needs.
Vortex: Advantage
This version of the CM-Labs hardware is fully immersive, and it is designed to scale and grow with a company's potential or changing needs. It has options for one, three, or five screens, and added motion-platform to reproduce the feel of real machinery, including vibration, impact, acceleration and overload conditions. It also features equipment-specific swappable control sets and pedals, so that it can be retooled in as little as 30 seconds to another simulation pack. It's an adaptable piece of hardware that can mimic whatever is in your fleet.
In addition to these diverse off-theshelf, ready to use products, CM-Labs is capable of working directly with its clients to specifically design, fine-tune and customize the simulations used on any of the platforms to meet the needs of the client. Limoges goes on to say, "we have PhD qualified mechanical engineers that work at CM-Labs that create the models, tune the hydraulic systems, and even the transmissions of all these vehicles. We work with our customers until the specifications and the feel are exactly right. We do this to avoid any sort of 'negative training', where the real machine and the simulation don't behave in the same way."
In the face of staffing shortages and training gaps, one of the ways forward is certainly through immersive technologies. Whatever your needs as a company or contractor, if it involves the operation of heavy machinery in specific environments, a simulation platform like the ones offered by CM-Labs provides a lot of potential upside.

For more information visit
http://asphalt.com/ p8pqe5
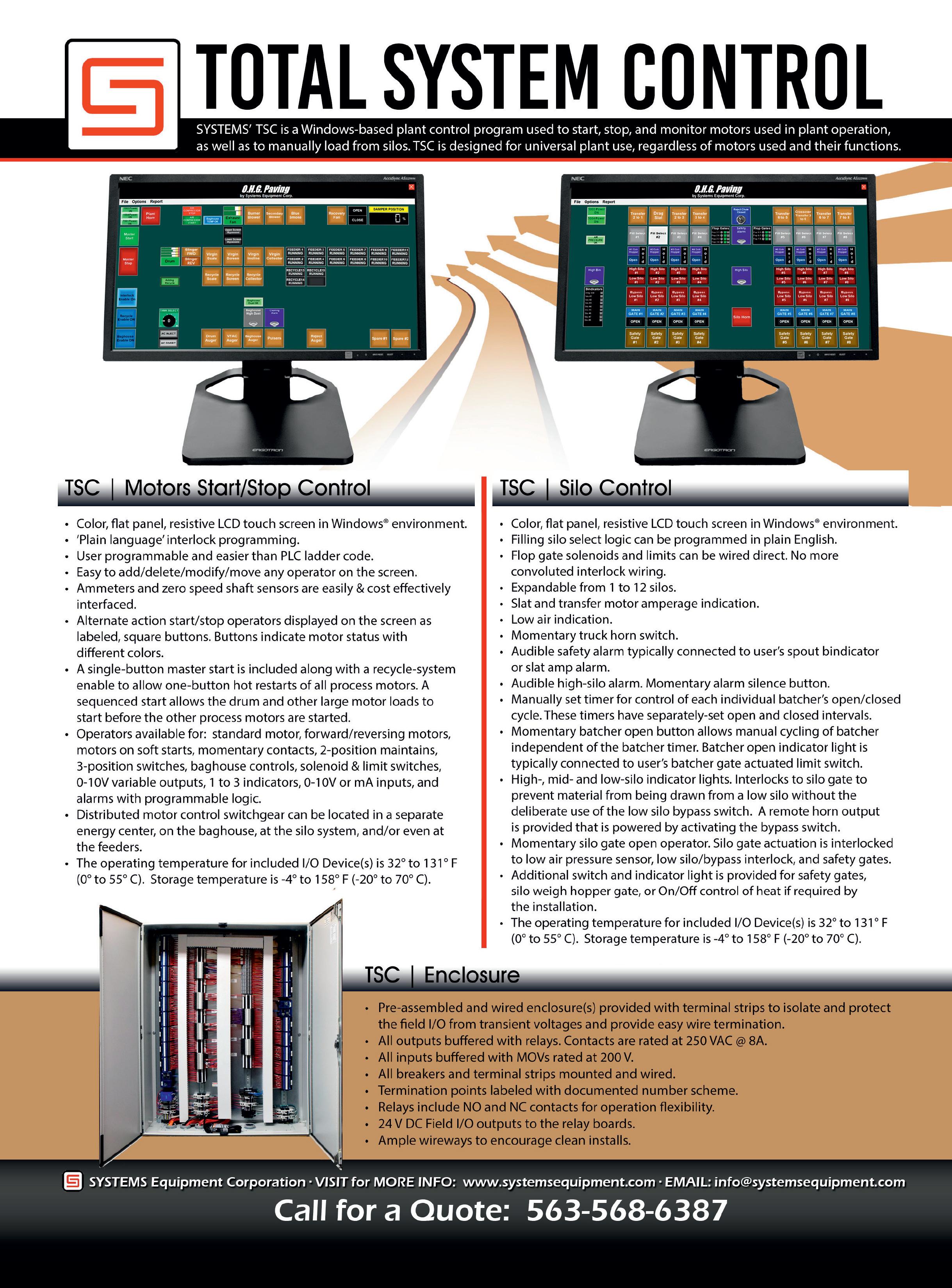