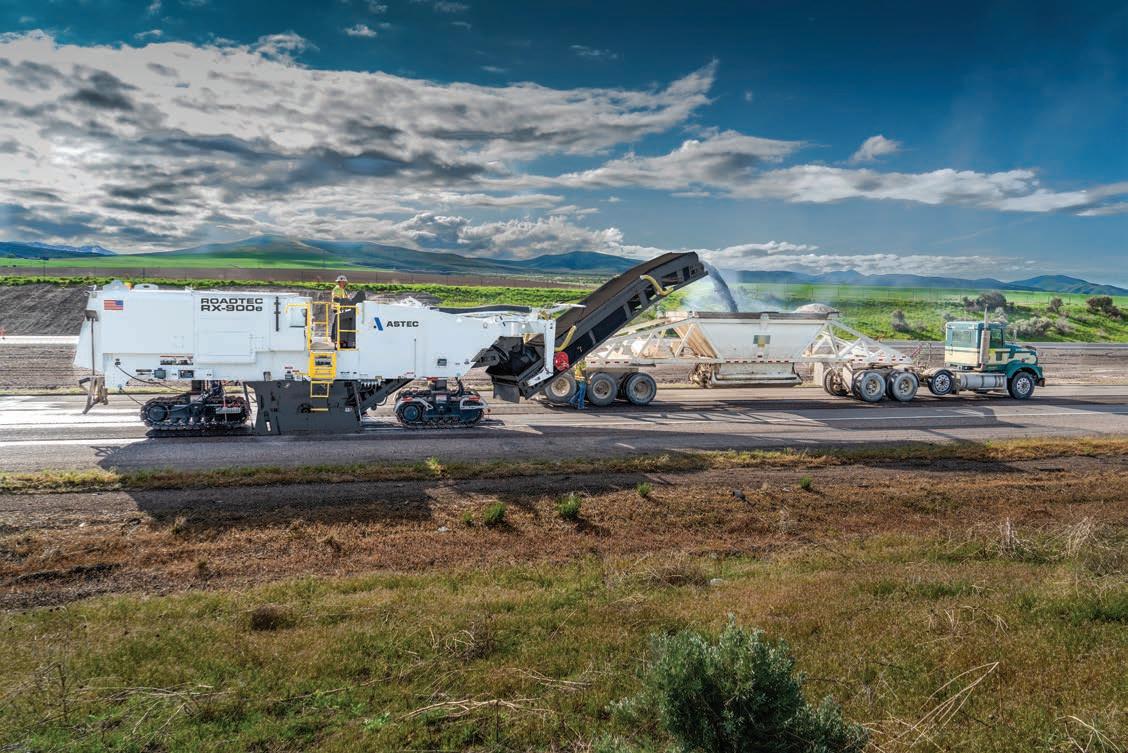
16 minute read
Milling Best Practices Improve the Quality of RAP
Milling Best Practices Improve the Quality of
Many factors will determine the quality of the recycled asphalt pavement materials being produced
The use of recycled asphalt pavement (RAP) is continuing to grow in the United States. In 2020, the National Asphalt Pavement Association reported that the industry reclaimed 97 million tons of RAP for future use, saving about 58.9 million cubic yards, or enough landfill space to fill up the dome of the U.S. Capitol 1,223 times. This massive reclamation effort also saved $5.3 billion in gate fees for disposal in landfills.
Our country’s most diligent recyclers are in fact asphalt mixture producers, who utilize more than 94 percent of old asphalt pavements in new pavement construction. But are they doing the best they can to ensure these materials are being recycled properly?
“Sizing of RAP can have a dramatic effect on how well RAP goes through asphalt plant," Kyle Neisen roadbuilding product manager at Astec Industries says. “A more consistent size coming in off the milling machine will be more efficient for everyone involved.”
By maintaining RAP quality in the field, the asphalt plant can achieve a faster turnaround using the RAP in a new mix design. Here are some ways to do that.
IMPACT OF OPERATOR
Operators play a huge role in the success of your operations, but this is especially true when milling where the operator plays the biggest part in ensuring quality.
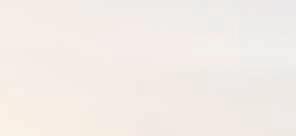
Maintaining milling best practices across the board can be better than changing the drum, both in terms of quality and productivity.
Get the Most from Your RAP
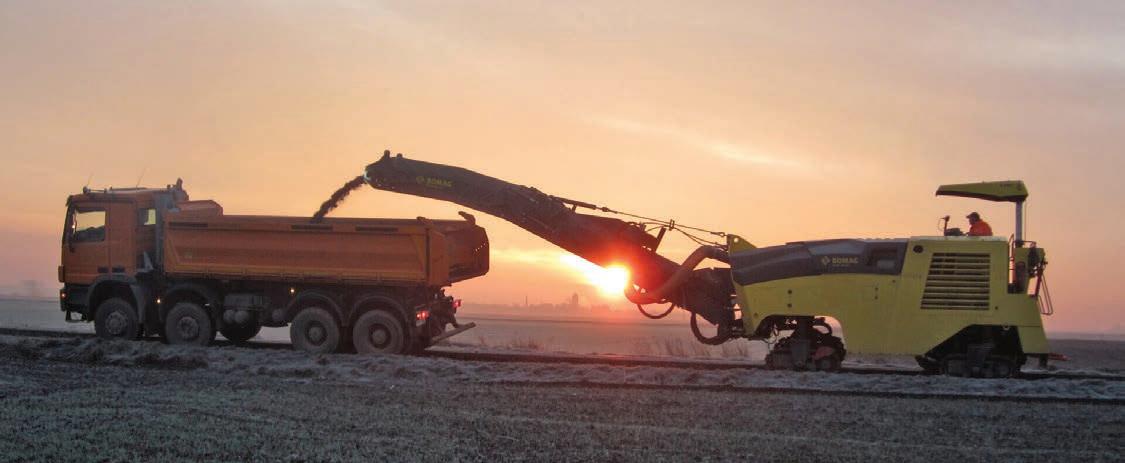
The main purpose for using RAP is to recover the oil so less virgin oil is used in the new asphalt. Making sure you’re getting the most out of this material is important to the success of your milling operations.
“The level of AC (asphalt content) in milled RAP has a big impact on the quality and the final AC content of the new asphalt it’s used in,” Dave Peterson, market professional with Caterpillar Cold Planers says. “That’s one reason why mill and fill applications are so effective, because they simply remove the top wearing course of a road where the oil content is typically the highest, and least likely to be contaminated with base aggregates. That RAP material is then very good for use in making new asphalt.”
To be the most successful at this, you need to know exactly what you’re milling up.
“Asphalt is placed in lifts and each lift has different rock and oil content,” Miller with BOMAG says. “Depending on how deep you are cutting, you may want to do this in lifts to separate the usable RAP with good oil content from the older material that may not have any oil left.”
Contamination is also a big factor in ensuring proper RAP quality.
“Operators should be aware of contamination and try to avoid major contamination, such as picking up dirt from the shoulder,” Niesen with Astec Industries adds. “Dirt can damage a mill head and results in poor quality RAP.”
Frequent contamination points also include the shoulder, going into the base layer and debris around intersections.
Contamination can also happen by accident, but can be easily managed through communication on the jobsite.
“Periodically, RAP material could encounter foreign oil or fuel leaks, either from the milling machine or one of the support vehicles (water truck, fuel truck, dump truck),” Chastain with Wirtgen America says. “Once we establish where the leak is coming from, we need to get that machine off the road in safe spot to address the problem. ”You also need to let supervisor know about what has happened. This communication allows all involved to know we may have contaminated material. If we catch it, the plant may be able to separate that contaminated material from the quality RAP. Also, throwing garbage, old cutting tools, etc. under the machine to put into the truck is not a good practice as well.”
“How an operator runs the machine will absolutely determine the quality of the RAP,” Austin Miller, paving development manager at BOMAG Americas says. “If he runs too fast or raises the front moldboard too high, it can produce large slabs that will have to be processed through a crusher and screen and stacked for use at a later date. If the operator can produce a consistent material with minimal deviations, the material can be processed during the making of the new mix with a small grinder or RAP wrangler prior to being put into the material bin on the asphalt plant.”
Therefore, consistency is key to RAP quality control.
“By maintaining a consistent pace of milling, and not going too fast, operators can help control quality,” Niesen adds. “If the operator slows down a few feet per minute it can help the machine get consistent size material.”
Machine controls can help with this.
“Properly setting things like rotor speed, travel speed, front antislab and rear moldboard position all contribute to achieving the desired pattern or surface finish behind the mill,” Jameson Smieja, global sales consultant with Caterpillar Cold Planers says. “Also proper setting and use of an automatic grade and slope
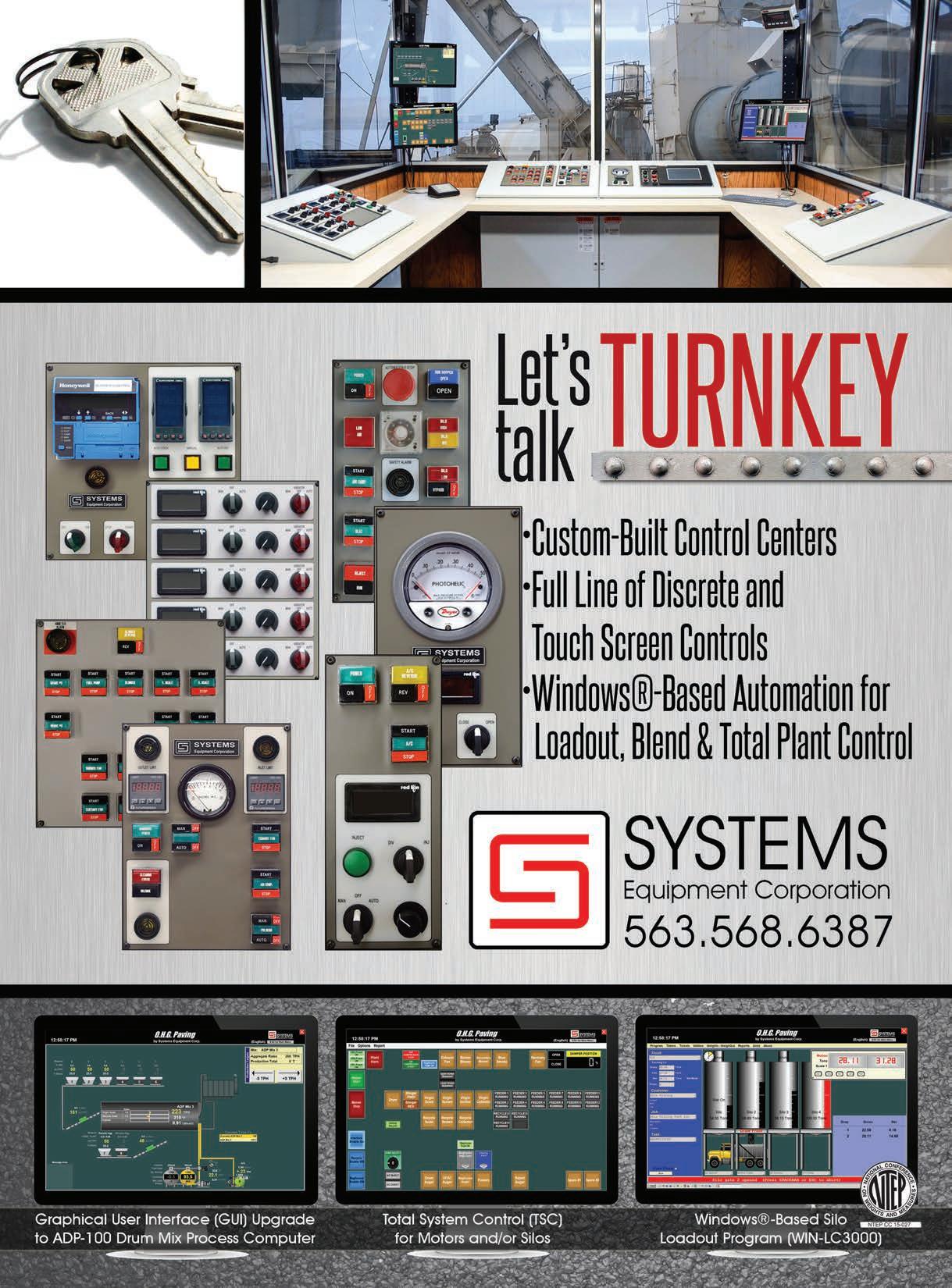
systems significantly improves the profile of the milled surface to be repaved.”
Operators also need to be aware of other factors outside of their control like the material being milled which impacts their water usage.
“The material does have something to do with quality,” Tom Chastain, milling product manager at Wirtgen America says. “How much water we are running can affect the RAP once it hits the plant due to how much water consumption the material has. Too much water consumption could mean we need to run the RAP through the dryer to bring that down some.”
IMPORTANCE OF THE DRUM
The drum you choose will obviously determine the size of material being processed and that is usually influenced by the desired spec of the job.
“Different cutting tools will affect sizing of material,” Chastain says. “Different sized carbide or diamond tools can either cut the material in small sizes or larger flakes.”
The finer the drum pattern, the finer the material will be.
“That is not always good as you don’t want to create more fines which is counterproductive in most cases,” Miller cautions. “Bottom line, pick the drum for the surface texture you desire, not for the RAP quality.”
“In general, you can hit any smoothness spec with any drum if know how to control machine,” Niesen says. “Not frequently do you have to go to micro-milling or quad wrap but doing either can help maintain production speeds while also achieving desired smoothness.”
One you have that drum in place, making sure it’s properly maintained is paramount to the success of your milling application.
“The maintenance of the drum is key in the quality of the RAP produced,” Miller says. “With good tooling, you will get a cleaner cut and less breakage of the aggregate. Once the teeth reach stage 4 or 5 of wear, they will tend to break the material or crush it instead of cutting. Watching your cut pattern and checking your teeth on a regular basis will ensure you are getting quality material.”
Last but not least, monitor the milled surface and make adjustments as necessary, including the replacement of cutting teeth. This will help maintain the best quality throughout the job.
“Cutting tools affect not only RAP sizing, but machine performance and pattern quality,” Chastain says. “Operators need to keep an eye on what the pattern looks like, how is the machine performing and look at the material that is being loaded into the truck. As


Top: Sizing of RAP can have a dramatic effect on how well RAP goes through asphalt plant. A more consistent size coming in off the milling machine will be more efficient for everyone involved. Bottom: Monitor the milled surface and make adjustments as necessary, including the replacement of cutting teeth. This will help maintain the best quality throughout the job.
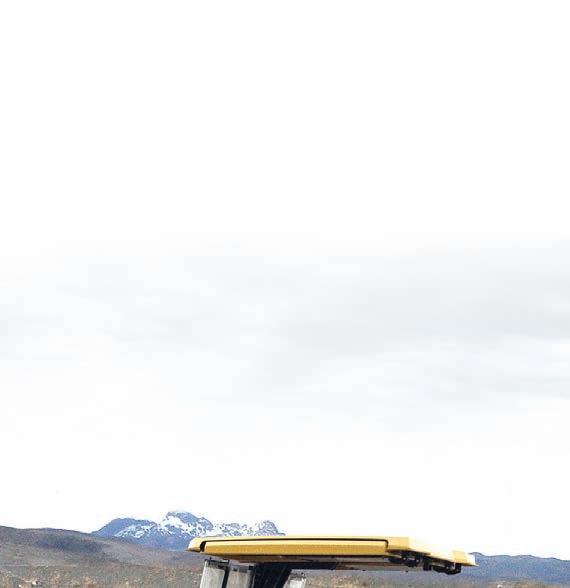
cutting tools wear, pattern quality can go down, then the machine performance goes down, then we see the RAP sizing start to be affected. If the cutting tools are wearing evenly, maybe we just need to slow the machine down, or possibly change what working parameters or drum speed we have the machine in.”
Maintaining best practices across the board can be better than changing the drum, both in terms of quality and productivity.
“At the end of the day, control the factors you can control,” Chastain says. “Machines need to be maintained properly and drum maintenance is extremely crucial. We need to have a cutter drum that is well maintained, and the proper cutting tools installed to achieve higher quality. Water spray systems also need to be in proper working order to make sure we are getting proper spray to the key areas.”
PROPER STORAGE & PROCESSING
Once RAP is transported back to the plant, the importance of quality control continues. The transportation, storage and utilization of RAP is always a logistical challenge, but the single most important best practice is to treat RAP the same way you treat virgin materials. This means always keeping the RAP clean and dry before it’s reprocessed and put back on our roadways.
When possible, store processed RAP stockpiles under cover, or at least in an area with a sloped surface and good drainage. NAPA recommends paving underneath stockpiles to allow for proper drainage.
“Storing processed RAP in a covered building is the most desirable,” Miller says. “It will keep the direct sun off the material which can heat the material

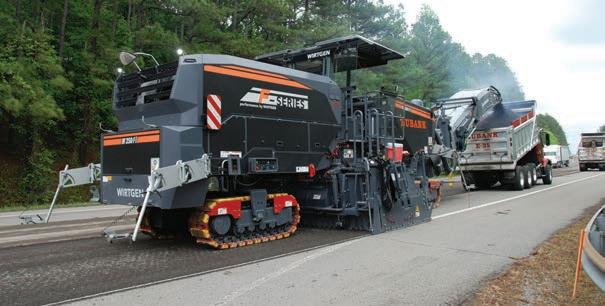
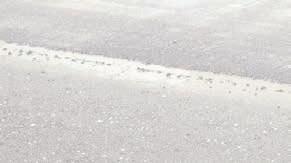

Properly setting things like rotor speed, travel speed, front antislab and rear moldboard position all contribute to achieving the desired pattern or surface finish behind the mill.
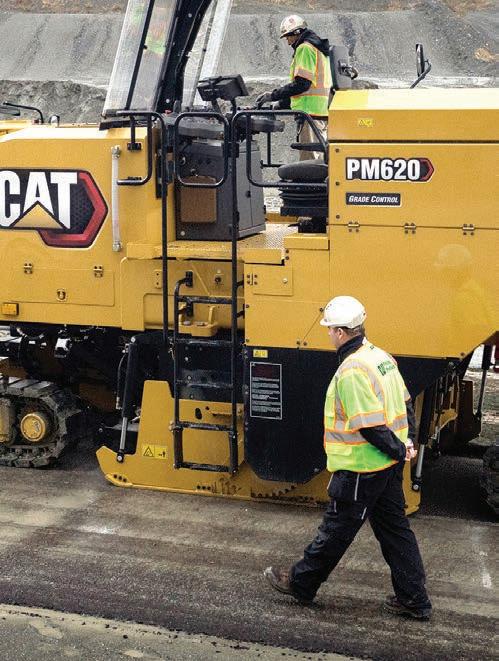

up and cause it to stick back together. If you have to store out in the open, try and process just enough for your job as close to the start of the job as you can so it has less time in the sun.”
One practice that makes higher percentages of RAP more successful is fractionation of the material. A producer should separate the material into two or more stockpiles based on the size of the RAP particles. It's becoming more common to separate RAP into a coarse pile, with particles of more than 1/2-in. or 3/8-in. in size, and a fine pile with particles of 1/2-in. minus or so. That lets contractors use fine RAP in finer asphalt mixtures and coarse RAP in coarse mixtures.
Crush only what you need for a two- to three-month period. Re-use of the RAP material is recommended within two-to-three-month period. Longer storage periods may be expected when the material is under cover. Also, avoid driving loaders on RAP stockpiles, which leads to premature compaction of the processed RAP.
The use of RAP is not going away. Follow these best practices for processing and stockpiling the material and you’ll be sure to produce a better-quality product.
For more information on the latest milling machine technology, visit
ForConstructionPros. com/21563294
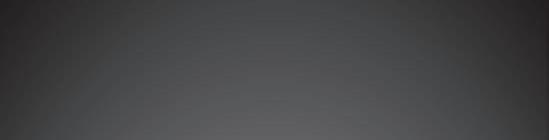
WE HAVE
YOU COVERED
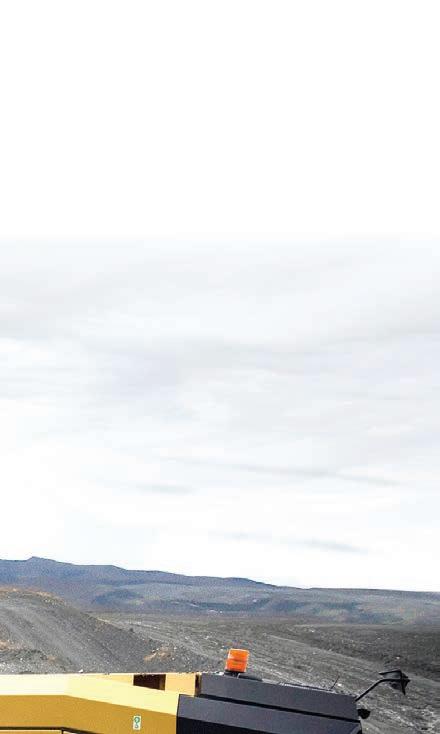
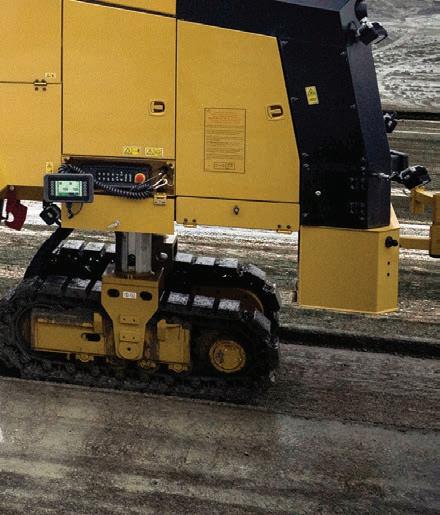
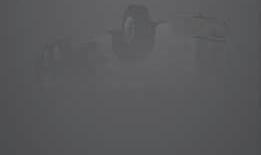
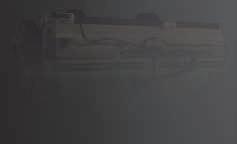

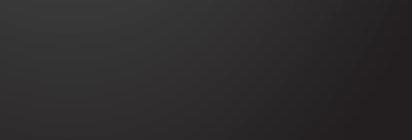
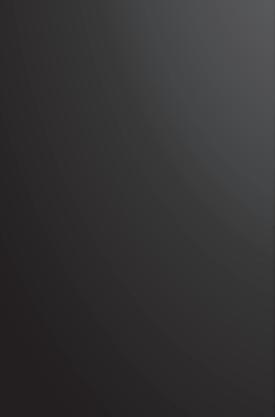
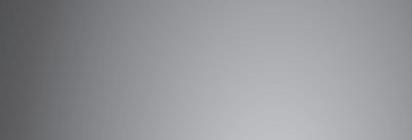

Etnyre International’s three companies work in tandem to supply you with the equipment you need to get the job done. With SUPERIOR building materials and expert engineering, our products are of the highest quality. Whether it is Bearcat, Etnyre, or Rayner, we are able to meet a wide number of specs to fulfill your needs.
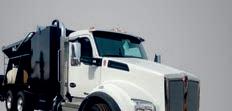
Contact our factory to see how we can help you.

INTERNATIONAL
bearcatmfg.com etnyre.com resroadsaver.com
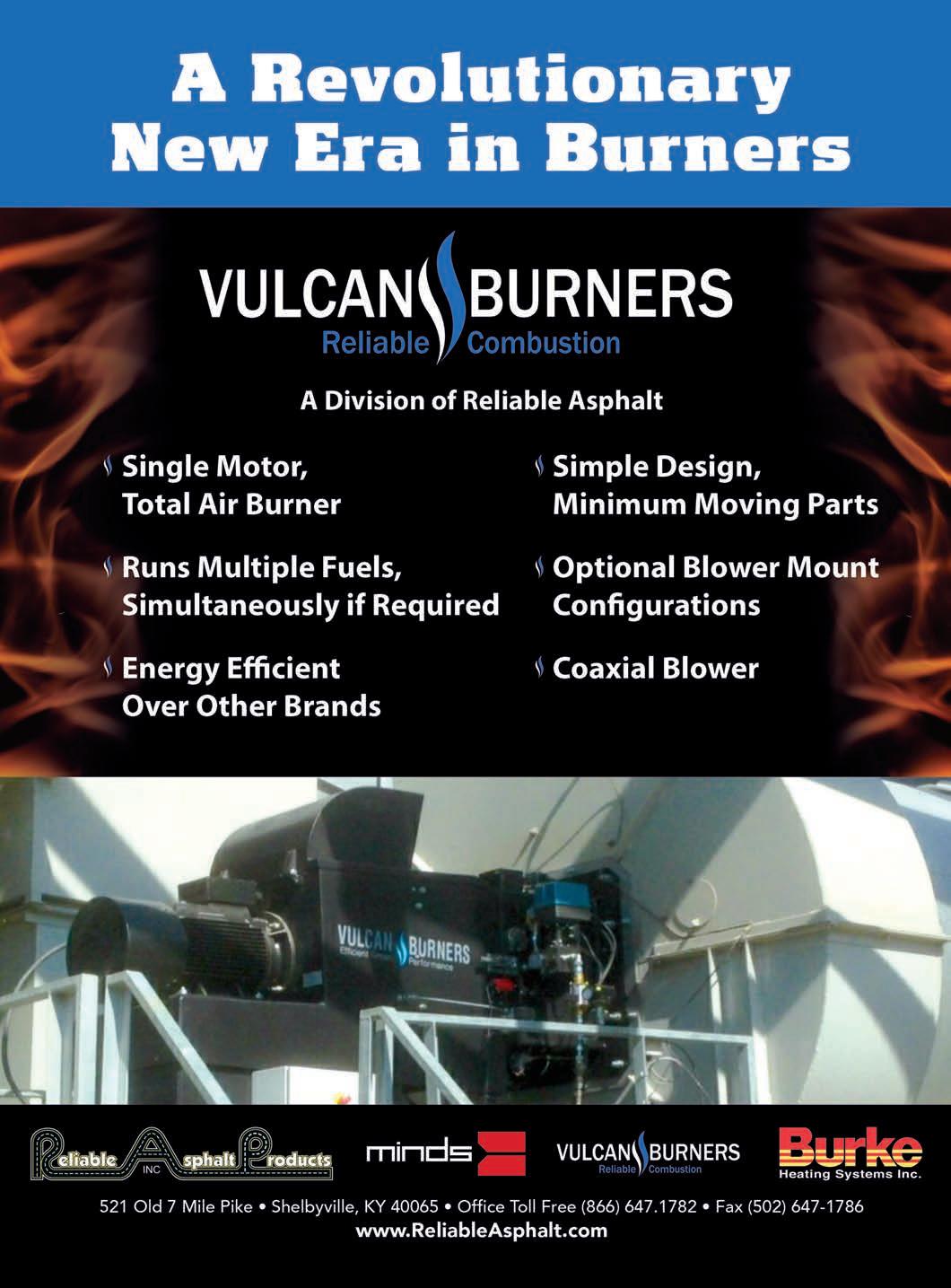
SAFE AND EFFICIENT
Lo Riser Inclining Platform Trailers Get the Job Done.
With a Lo Riser you’ll see: Lower labor costs✔
- one man loading offers more deliveries daily Lower GVWR✔
The 4 degree load angle is ideal for low ground clearance or reduced - four-to-one payload-to-trailer weight ratio gradeability equipment. - high strength steel safely handles the rated payload while keeping the trailer weight to a minimum Lower specialized equipment costs✔
- no rollback truck required, just a pickup truck Lower worker's comp claims✔
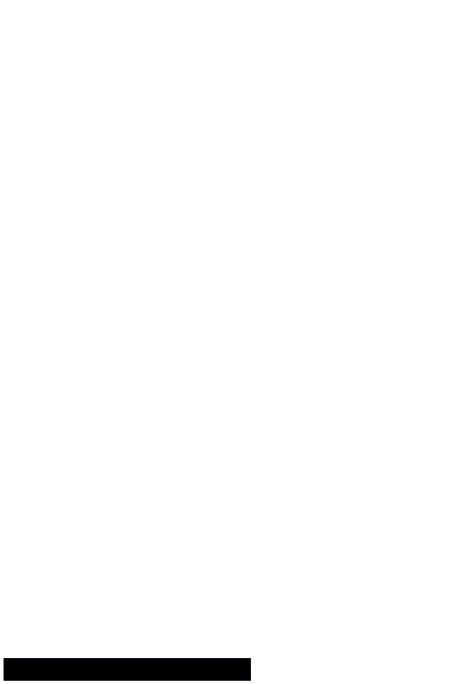

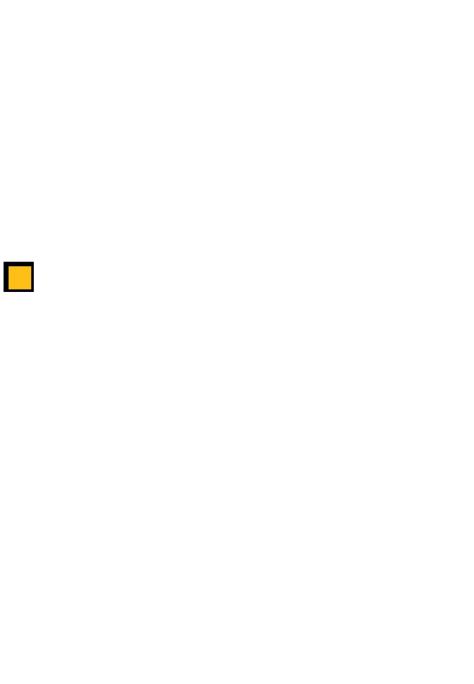
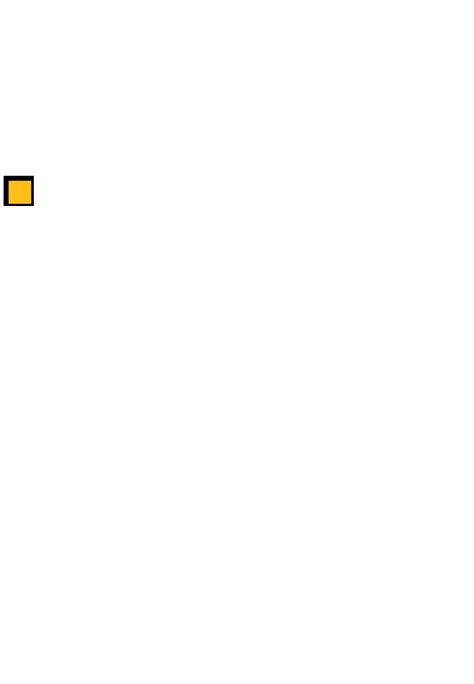

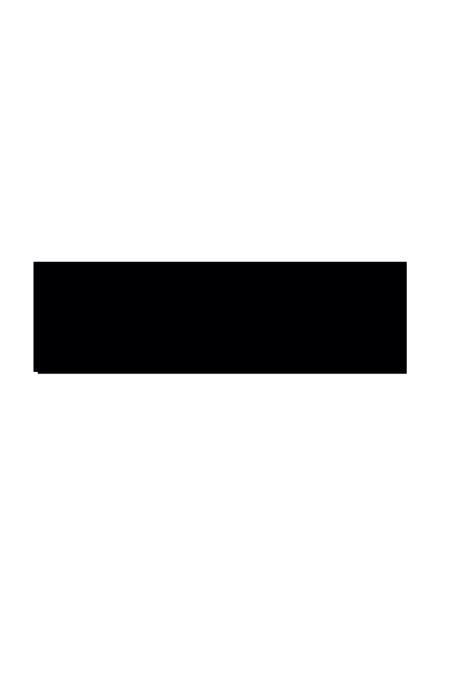
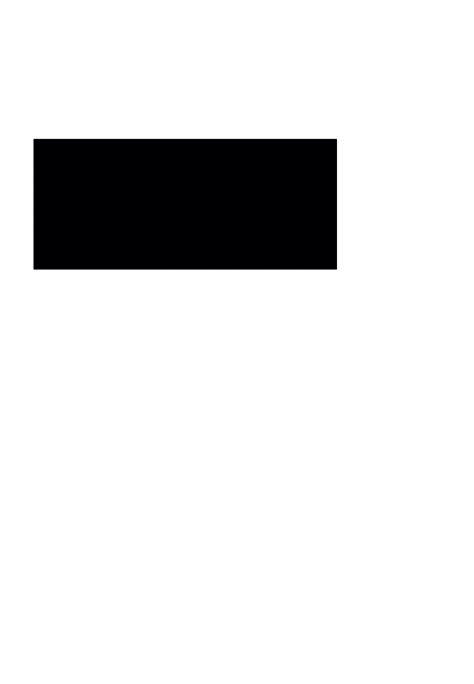

- enhanced safety features eliminate most opportunities for injuries - no heavy tailgates and no more dangerous, slanted ramp boards



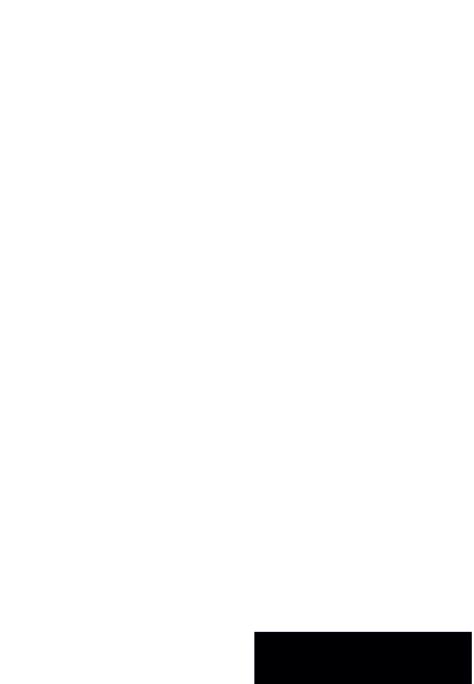

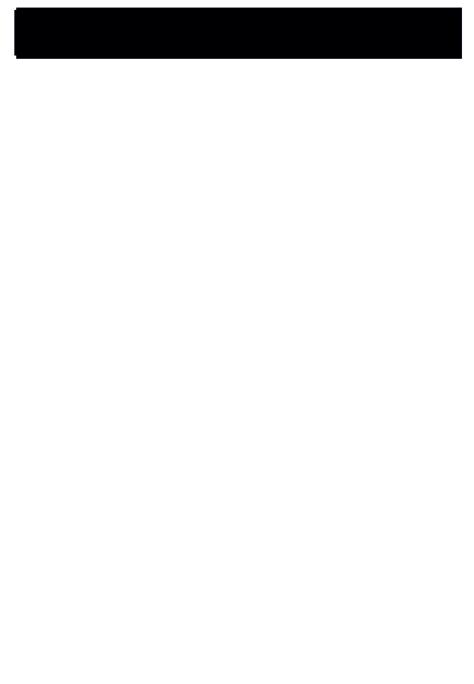
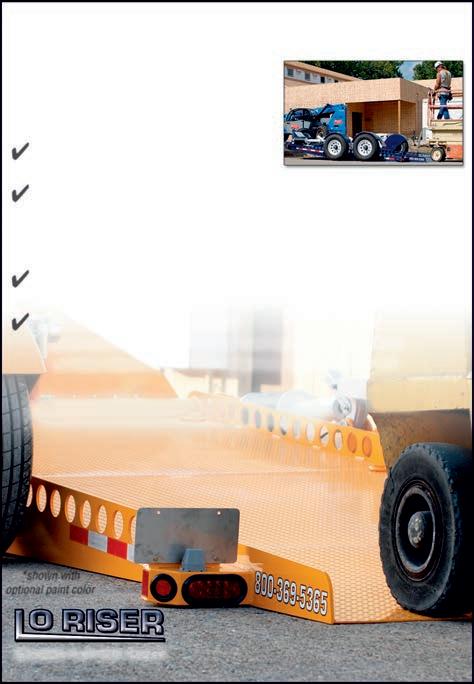
Get a Lo Riser working for you.
*shown with optional paint color
INCLINING PLATFORM TRAILER
Manufactured by: The Advance Metalworking Company, Inc.
1-800-369-5365
www.advancemetalworking.com
PUMP PACKING
Stop your pumps from leaking!
Pre-cut packing sets proven within the Asphalt Industry. Viking®, Roper, Rotan, etc. Call Scott at 1-800-231-4209 www.rainsflo.com
Contact Tadashi Soma Print and Digital Advertising 920-542-1267
tsoma@ACBusinessMedia.com
Advertiser Index
ALMix
Asphalt Drum Mixers Inc. (ADM)
Astec Inc.
Bomag Americas
Eager Beaver Trailers
Etnyre
Gencor Industries Inc.
IGNITE Construction Summit
LeeBoy, Inc.
Meeker Equipment Co. Inc.
Minds, Inc.
Pegasus Vans & Trailers, Inc.
SealMaster
Systems Equipment
Tarmac International, Inc.
TransTech Systems, Inc.
Weiler Products
Wirtgen America Inc.
Index
9 PAGE
17
26-27, 51, 52
13
45
47
3, 5
22
2
35
37
41
7
29, 43
39
33
31
19, 21, 23, 25
Contractors Need More Resources to Move Infrastructure Projects Forward
How will the industry accomplish the influx of work headed our way? These tools can help
As discussions continue on the Infrastructure Investment and Jobs Act, contractors are readying themselves to scoop up as much of the incoming business as possible. In their excitement however, many construction businesses are neglecting the fact that they don't have the manpower or equipment they will need to complete these projects.
In order to not only compete with this influx of work, but succeed in completing these jobs, contractors are going to need to rethink how they hire, bid and work and technology will be key to that. According to a new survey, construction technology can provide a 15-20% cost reduction on road, bridge, airport, mass transit and other infrastructure construction projects. The time to act is now.
HEAD COUNT
According to recent data from the U.S. Chamber of Commerce, 88% of contractors surveyed report moderate to high levels of difficulty finding skilled workers and over one-third (35%) are turning down work due to the labor shortage. An insufficient number of workers will make it difficult to complete projects in a timely and cost-effective manner.
Here are some solutions for hiring and labor management: • LaborChart
• Core LaborOS/Crews by Core Pro • TraLaMa • ProCore • TradeHounds While it's impossible to completely avoid the impact of a labor shortage that affects the entire country, it's possible to combat this with innovative technological advances. More people may be inclined to join the industry if they understand that it is an environment that embraces technology.
CASH FLOW
Estimating and project delivery issues are additional problems contractors need to be prepared to address. To gain and maintain public confidence, projects need to deliver the Jonathan Byer/ Teichert Construction results that owners promise, within the timeframes they set. That means projects need to be completed more efficiently and cost-effectively. Cost overrun is a common problem that construction companies experience for a number of reasons. Contractors are going to need to consider investing in estimating and bidding software that can manage the elements of project overruns. Here are a few technologies: • Briq • ProEst • B2W • HCSS A cloud-based project management solution is also necessary. According to Trimble, siloed processes and systems create a domino effect of miscommunication and inefficiencies. Rework, change orders, duplicate models and manual data entry drastically impact profitability. Here are a few construction project management platforms to help you streamline your operations: • Trimble FieldLink • YellowBird • TraceAir • Propeller Platform • HeadLight
By taking the proper steps to put a sufficient project budget in place and automate various processes, construction companies can effectively avoid cost overrun.
ON-SITE TECHNOLOGY
Between the pandemic, mounting climate concerns and the rapid, ongoing digitization of society, the stakeholders involved in building and operating America’s road and bridges can no longer resist change. There are many ways to work smarter, not harder in order to complete the work that will be required of our industry.
Here are some solutions for increasing productivity on road building jobsites: • BOMAG BOMAP Connect • Trimble 3D RoadWorks • Witos for Paving • Caterpillar eRoutes Mobile App • Topcon PaveLink App
You have an opportunity right now. A refusal to adapt to accommodate this influx of work will worsen performance, while developing new business and operating models could allow companies to generate more value and profit. The choice is yours.
For more information on technology for the asphalt industry, visit
ForConstructionPros. com/21119160
BUILT TO CONNECT
Guided by a customer-centric approach
We help you build the roads that connect goods to markets, people to communities and families to one other. Astec pavers, screeds, mills, stabilizers and MTVs are designed with a customer-centric approach that yields innovative and reliable rock to road solutions that create value and connection.
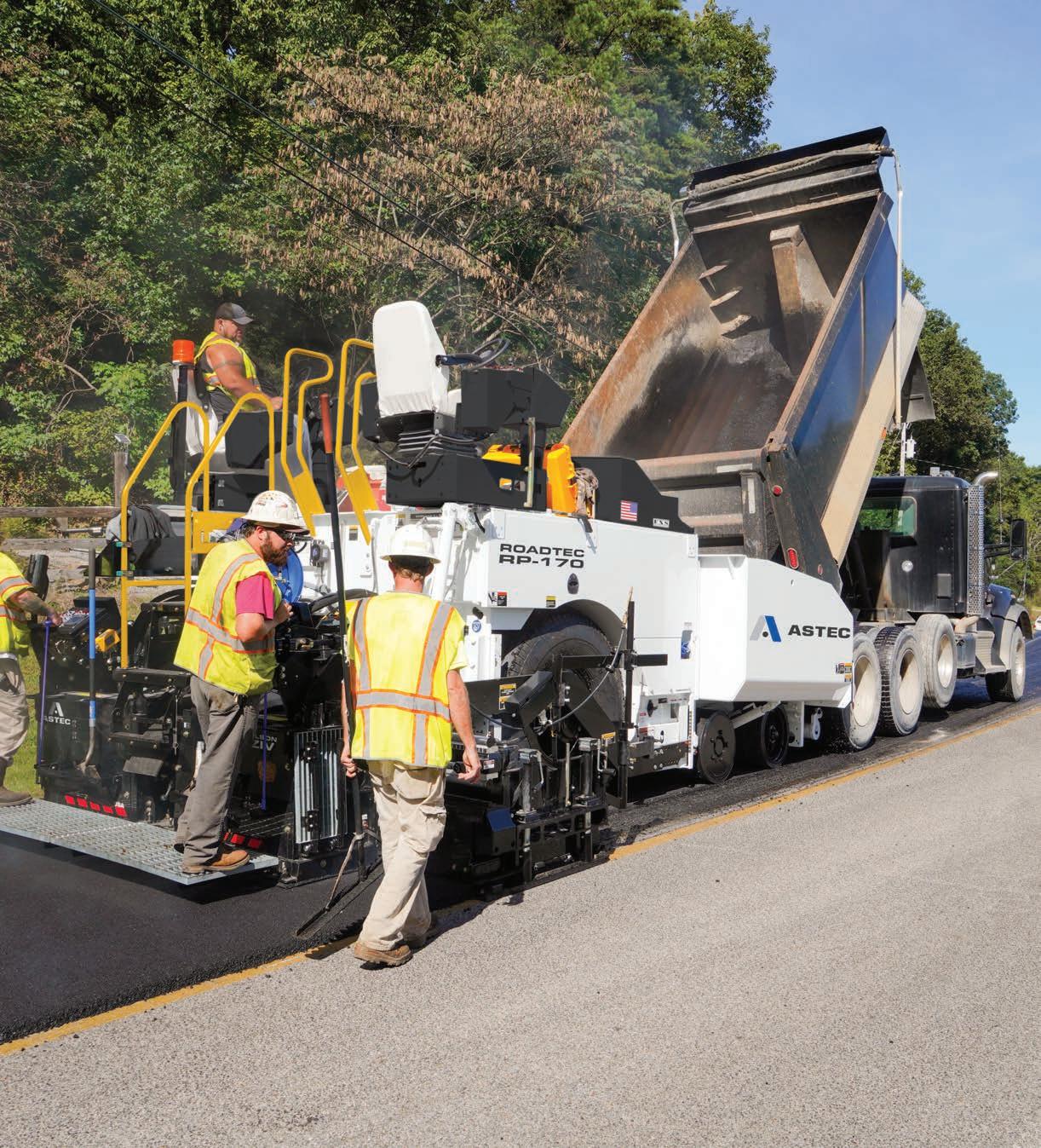
We are inspired to connect with our customers through inventive design that creates safe and reliable roads.
BUILT TO CONNECT
Efficiency and Productivity

Designed with safety and operator comfort in mind, the Shuttle Buggy® SB-3000 material transfer vehicle features adaptive cruise control, bright LED lighting, four-wheel steering for easy transport and groundlevel maintenance access for added convenience. Operators can rely on clear sightlines and the ground operator is safely protected inside the structure of the machine. The Roadtec SB-3000 is the perfect blend of traditional craftsmanship and modern technology.