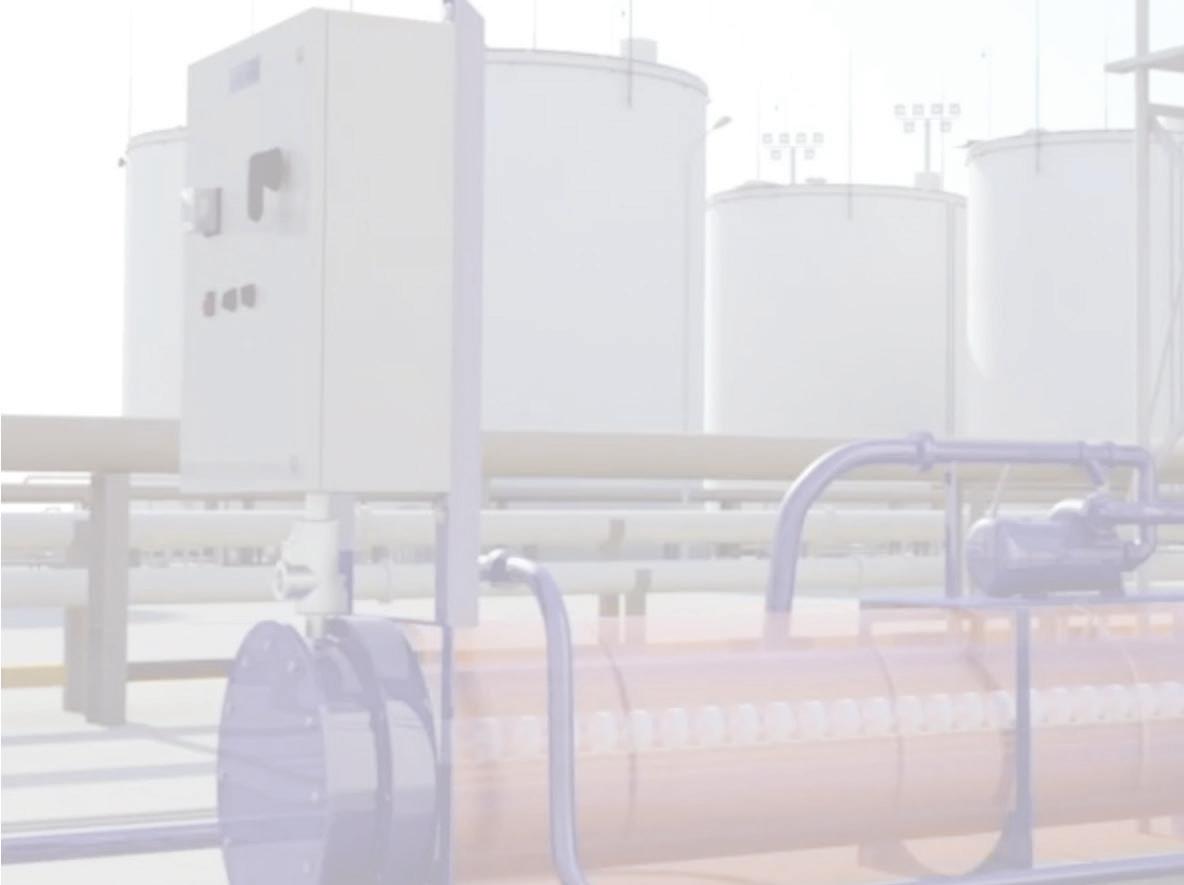
8 minute read
The Heat Is On
The
Supplied by PHCo
Is On
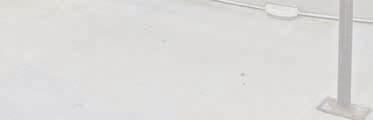
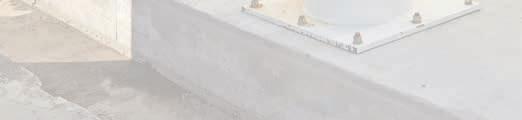
When choosing energy for asphalt heating, it’s important to look at the entire picture. Cost-per-unit of energy to heat asphalt and oil is certainly part of the puzzle — but it is not the only cost. Also important is the heater’s thermal efficiency. A small difference in efficiency can make a big difference in how much fuel a heater burns over its lifetime.
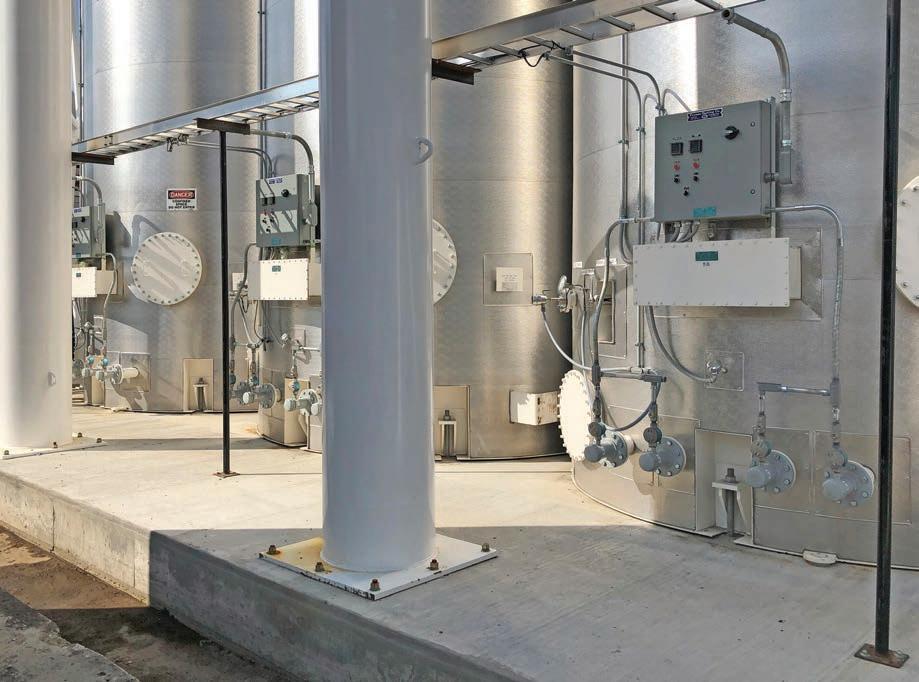
Supplied by PHCo
Get Current with Efficient and Cleaner Heat Sources at Your Plant
With fuel and material prices on the rise, asphalt producers are finding it more challenging than ever to keep operating costs under control. Add new environmental regulations and initiatives into the mix, and they have what might seem like an impossible mission — to not only find the most efficient and costeffective ways to run the plant, but also reduce or eliminate its emissions. There is an oft-overlooked aspect of asphalt production, however, that can make a difference in both realms — that of energy choices for heating asphalt and emulsions.
There’s no denying that energy costs contribute significantly to the operating costs of an HMA plant. But fuel choices can impact producers in more ways than just cost. And the form of energy they choose to heat their asphalt tanks, hot oil circulating systems and fuel oil preheaters can actually help producers reach their goals.
Typically, the first question operators have is what’s the cheapest form of energy for heating? The answer, unfortunately, isn’t simple — and it is dependent on several variables, including local energy costs and the age of the equipment. Operators often make energy choices for heating their plant’s components based on current energy pricing trends. But the cost of natural gas, LP gas, fuel oils and electricity have all fluctuated over the years.
Electric heaters are simple to install in most asphalt plants: A complete installation of the heater, plumbing, piping and electrical hookup can be completed two days or less. Low-watt-density electric heaters not only provide 100 percent efficient heat, but they also require little to no maintenance, further reducing a plant’s operating costs.
Supplied by PHCo

Supplied by PHCo

FUEL COST TABLE
In an initial assessment, looking at operating cost in Year 1, it would seem that natural gas, followed by LP propane gas, are the cheapest forms of heat energy. But we already know that fossil-fuel burners operate at only 80 to 85 percent efficiency at best — and their efficiency drops over time. When true efficiencies are considered, along with aging burners and poor maintenance practices, the cost gap narrows dramatically — especially keeping in mind that electric heaters operate at 100 percent efficiency throughout their lifetime. Add the cost of an annual per-heater stack permit, where electric heat requires no stack, and electric heat suddenly becomes the least expensive option.
Costs Per-Day and Per-Ton
Process Heating Company (PHCo) performed tests over a 3-week period, the electric tank heater consumed 192 kilowatt hours (kWh) per day. Using current industrial electric cost of $0.08 per kW (see Table 1), the cost for heating the tank over 192 kWh is $15.36. The hot oil system used 422 actual kWh per day during the same period, thus the cost per day to heat the plant’s hot oil is $33.76. The cost per ton of output can be determined using: $28.99 / 2,400 tons produced per day, or $0.014 (1.4 cents per ton). The plant had two identical asphalt storage tanks and the hot oil system, the total electricity costs per day using electric heaters would be $15.36 x 2 = $30.72 + $33.76 for a total of $64.48. Total cost per ton of output is $64.48 / 2,400 tons produced per day, or $0.0268 (2.7 cents per ton).
A Little More Math
An average drum mix asphalt plant using a PHCo hot oil heater will require a 140 kW heater, which is adequate for two 30,000-gallon asphalt tanks and associated jacketed pumps, meters and asphalt lines running ~4 hours a day in the summer and ~6 hours a day in the winter. The same plant would use ~20 gallons of diesel fuel per day in the summer and ~27 gallons per day in the winter.
At current industrial electricity costs of $0.08 per kW, a 140 kW heater running 4 hours per day would accrue $44.80 in daily costs, and 6 hours per day would accrue $67.20 in daily costs. Alternately, with diesel fuel costs of $3.36 per gallon, daily asphalt heating costs would total the following: 20 gallons of diesel fuel at $67.20/day and 27 gallons at $90.72/day. [At time of print, diesel costs avg. $5.82]
The Emissions Enigma
Electric heat eliminates some need for expensive permits because it operates without combustion or emissions. Adding a single stack at a plant can increase the annual permit cost by $5,000 or more, and No. 6 Oil produces high emissions. This type of fuel often requires preheating, and typically uses special burners. LP propane gas produces greater levels of NOx. And while today’s No. 2 Oil produces lower emissions than it has in the past, that energy source, as well as natural gas, both create some level of emissions at the plant — with associated stacks, permits and expenses. Electric heat can help producers meet ustainability goals, and also eliminates a source of fuel spills.
Additional Advantages of Electric Heat
Low-watt-density, drywell-style electric heaters not only provide 100 percent efficient heat, but they also require little to no maintenance. Because they typically last more than 30 years, electric-powered plant heaters also enjoy a lifespan that lasts three to four times longer than fossil-fuel burners, which must be replaced every eight to 10 years — reducing capital costs.
Better product quality is another benefit to using electric heat. Low-watt-density heaters, which dissipate controlled heat as low as 3 watts per square inch on the heater’s sheath, can prevent the coking and damaging of temperature-sensitive materials that often occurs with fossil-fuelfired burners. In hot oil systems, this reduces or eliminates the need to change out expensive heat transfer oil.
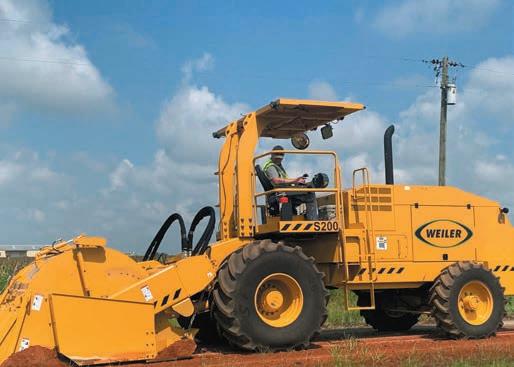
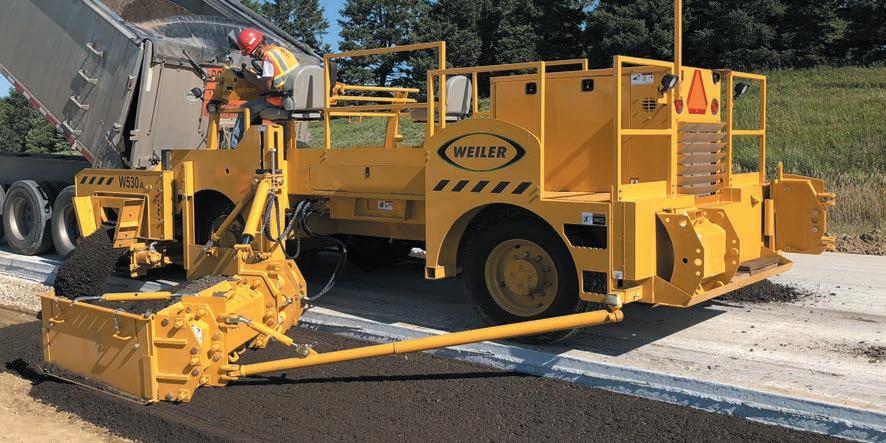
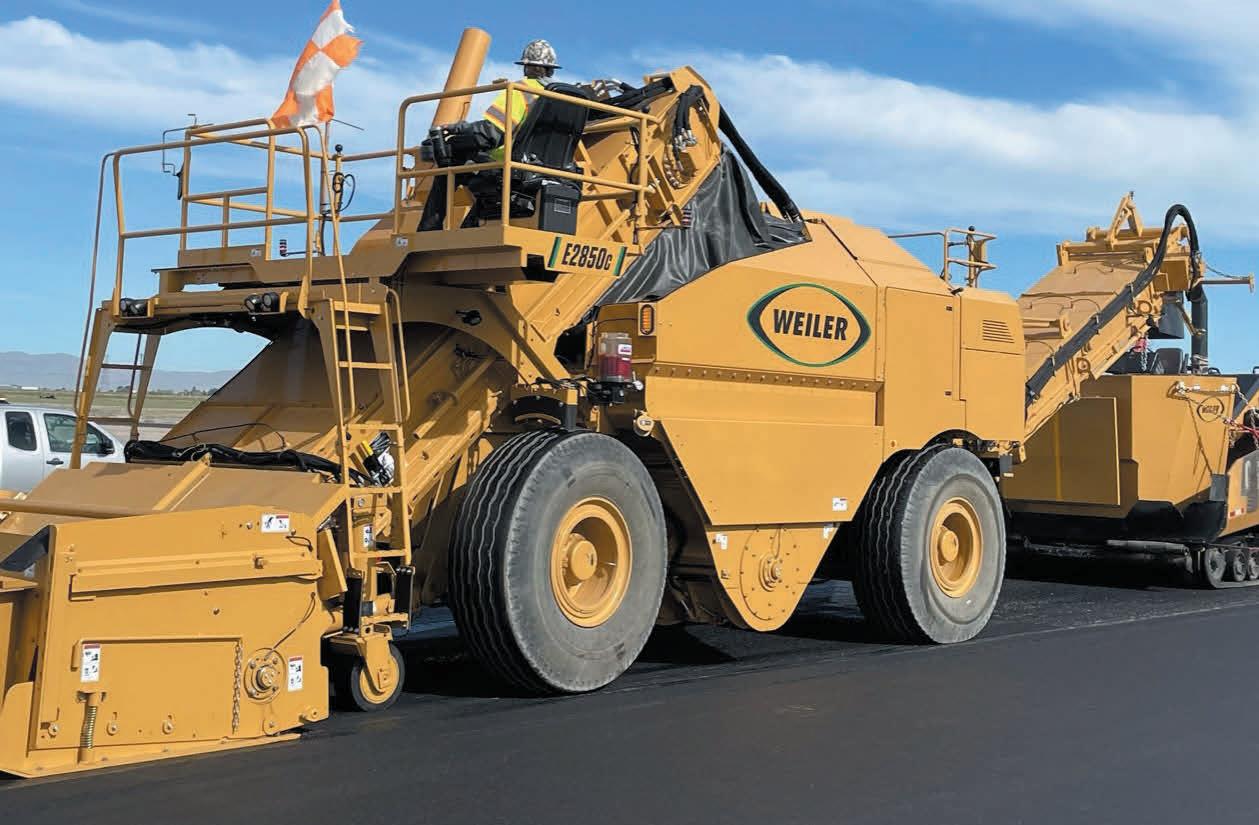
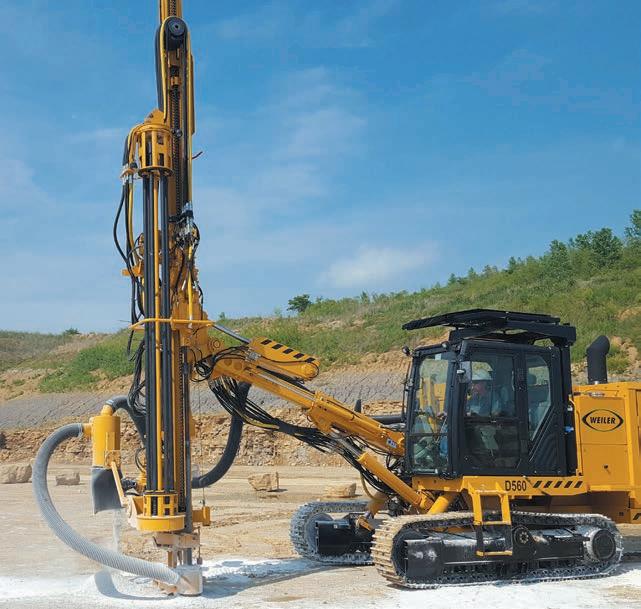
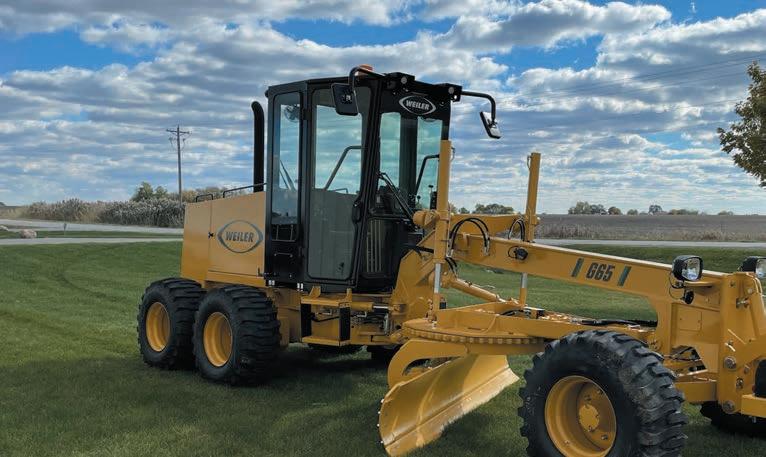
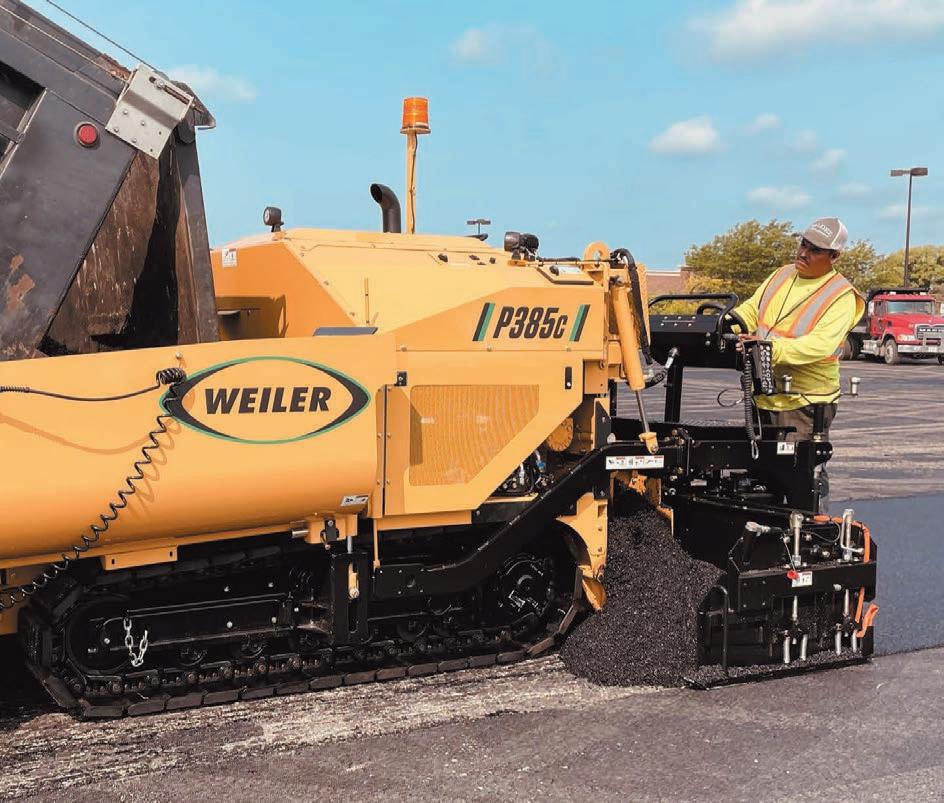
From innovative designs to Caterpillar dealer service and support, Weiler is paving the way to success for contractors across North America. Weiler material transfer vehicles, commercial pavers, road wideners, windrow elevators, compactors, soil stabilizer, rock drills, grader, screeds and tack distributors are engineered with proven features to increase productivity while reducing operating costs. Weiler equipment is sold and serviced exclusively at Caterpillar dealers throughout North America, providing unmatched support with factory trained technicians and readily available parts to keep your operation up and running.
In order to achieve optimal electric rates, electric heaters can be interfaced with other large electric-using equipment to avoid adding to demand charges. By utilizing time clocks to operate during off-peak hours, producers can take advantage of the lowest possible electric rates without impacting performance or operation of the plant.
Supplied by PHCo
At one time, fuel oil was the cheapest form of energy for heating. By the late 1990s, electricity became far less expensive than fossil fuels to use for heat. In the past 10 years, natural gas has become the least expensive energy choice for heat — if you’re looking only at energy prices.
But producers often overlook the fact that their energy choices create impacts that go beyond operational costs, and what seems to be a simple challenge actually requires additional considerations to reach optimal efficiency. When choosing energy for asphalt heating, it’s important to look at the entire picture. Cost-per-unit of energy to heat asphalt and oil is certainly part of the puzzle — but it is not the only cost. Also important is the heater’s thermal efficiency. A small difference in efficiency can make a big difference in how much fuel a heater burns over its lifetime.
THE ISSUE WITH EFFICIENCY
It is widely accepted that most fossilfuel-fired burners only operate at 80 to 85 percent efficiency when new. What this means is on its best day, a burner is actually wasting 15 to 20 percent of its heat, which goes into the air as heat, exhaust, and burner emissions. Then, as the burner ages, its efficiency drops. And because fossil-fuel-fired asphalt heaters are maintenanceintensive, if they are not properly maintained and tuned, their efficiency drops even more significantly. In fact, by the time a fossil-fuel burner is 7 to 8 years old, its efficiency can easily have dropped to just 50 to 60 percent — meaning that up to 50 percent of the heat is wasted, going into the air as exhaust.
In comparison, an electric-powered asphalt tank or hot oil heater operates at 100 percent efficiency from day one — 100 percent of the heat is applied to the product, with no heat or emissions exhausted into the air. And over the lifetime of the heater, the electric efficiency never drops.
Table 1 on page 30 shows a recent fuel cost comparison between different forms of energy per 1 million BTUs, which is the approximate number of BTUs required to maintain 30,000 gallons of asphalt cement at 300˚ F over 24 hours in a tank with 3 inches of insulation.
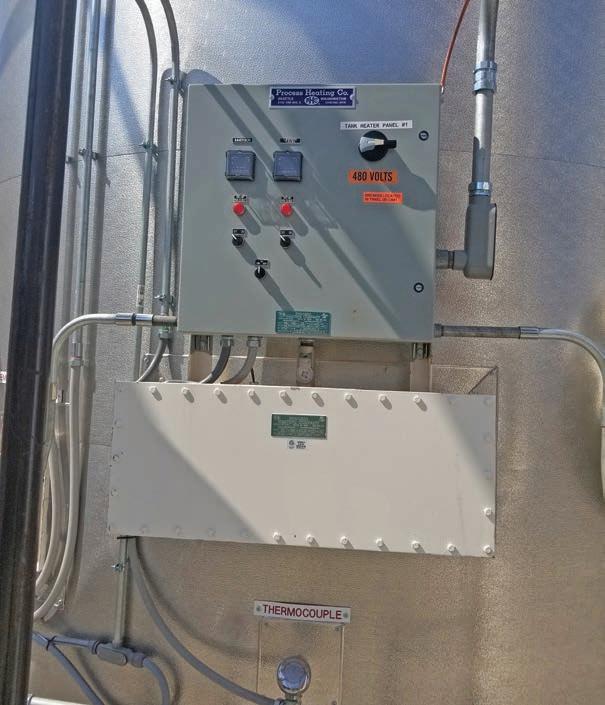
For more information visit https://myfc.pro/30gvaa
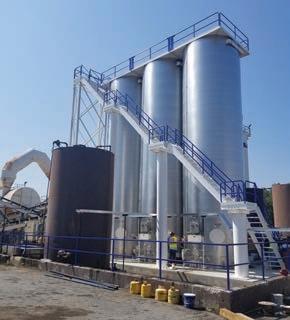
Electric heat eliminates some need for expensive permits because it creates zero emissions. A single stack at an asphalt plant can cost upwards of $5,000. But beyond costs, and with increasing emission regulations across the country, electric heat can help producers meet regulations and their sustainability goals — including NAPA’s “The Road Forward” climate action plan.
Supplied by PHCo