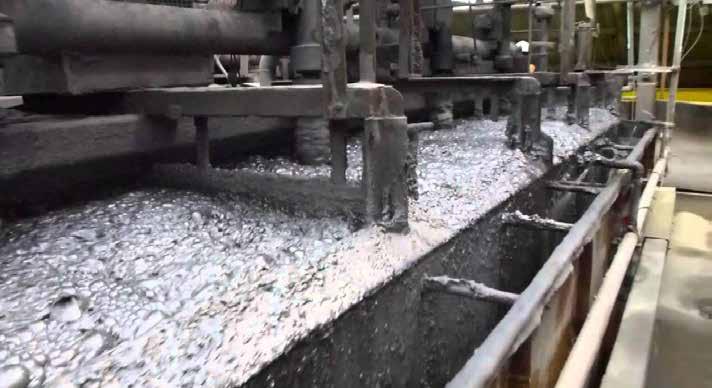
16 minute read
Flotation reagents in the mineral processing
Flotation reagents in the mineral processing industry
Flotation is the most flexible and adaptable mineral beneficiation technique. Mineral separation by flotation works on physicochemical surface properties of valuable and unwanted gangue minerals. It is being continuously modified for low-grade complex sulfide ores like lead-zinc, leadzinc-copper, nickel-platinum-gold, tin, fluorite, phosphate, fine coal and iron ore at a lower cost with better recovery. The processes are known as froth and column flotation.
Advertisement
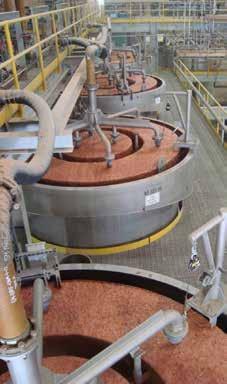
Froth flotation
Froth flotation process produces froth of selective mineral agglomerates and separates them from other associated metallic components and gangue minerals. The physicochemical surface properties of optimum fine size fraction make some specific minerals hydrophobic. The particles turn into water repellent by coming in contact with moving air bubbles in the presence of certain reagents. The forth portion moves up leaving other metallic minerals and gangue (tailing) below, stabilizes for a while and collects as concentrate for further cleaning.
The mineralized concentrate stabilizes for a while at the top of the cell, overflows and moves to cleaner, filter and dryer in sequence to form mature salable product. The concentrate is the raw material for extracting metals by smelting and electro and chemical refining. There are three main types of reagents used in flotation, namely, collectors, frothers and regulators. Each individual set of reagents plays a specific role in mineral processing.
Collectors, also known as “promoters”, are organic compounds which make the surface of certain selected minerals water repellent. These reagents are added to the pulp in the conditioner tank and ball mill. The mineral surface
absorbs the collectors during conditioning period making them hydrophobic. Froth is formed when they come in contact with flowing air bubbles and float to the surface. Sodium Isopropyl Xanthate and Potassium Amyl Xanthate are the commonly used collectors.
Frothers are surface-active chemicals that concentrate at the air-water interface. It prevents air bubbles from coalescing or bursting by lowering the surface tension of the slurry. Frothing properties can be persistent or nonpersistent depending on the desired stability of the froth. Pine oil and alcohols such as MIBC are most commonly used frothers.
Regulators or “modifiers” are used to modify the action of the collector by intensifying or reducing water-repellent effect of mineral surface conditions. This is done to assist in the selective flotation of minerals. Regulators can be classed as activators, depressants, or pH modifiers. Regulators may activate poorly floating minerals such as sphalerite by adding readily soluble copper sulfate. Similarly, regulators can depress certain minerals rendering it hydrophilic and preventing their flotation. Minerals like pyrite and arsenopyrite can be depressed by adding sodium cyanide or lime, so that a differential flotation can be performed on a complex ore. Nigrosene reagent is used for maximum depression or elimination of graphitic carbon from zinclead sulfides in graphitic host rock.
Separation of graphitic carbon aids in producing high-quality clean zinc and lead concentrates. Chemicals that change the pH of the slurry are also used as modifiers. An alkaline condition of medium is preferable in the flotation process where most of the collectors are stable. Alkaline environment minimizes the damage done by corrosion of cells and pipelines. pH modifiers include lime, soda ash and sulfuric acid. It can act as activators and/or depressants by controlling the alkalinity and acidity of the slurry. Modifiers can also counteract interfering effects from the detrimental slimes, colloids, and soluble salts that can absorb and thereby reduce the effectiveness of flotation reagents.

The design of mineral processing circuit requires integration and assembly of various unit operations. It starts from crushinggrinding-flotation with generation of valuable concentrates and rejection of tailing in continuous process. It is desirable to conduct laboratory, bench and pilot plant scale test works at the appropriate stages of exploration and mine development activities. It is done before adopting a commercial plant flow diagram of complex mineral assemblages.
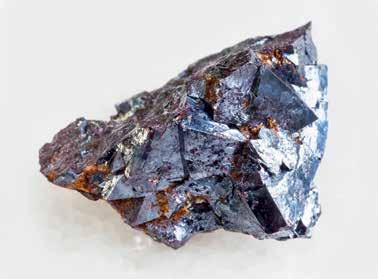
The representative sample is obtained by compositing duplicate mineralized core covering the characteristics of entire deposit and bulk sample collected from initial mine development. The grind size, concentrate grades and other quality, recovery of valuable minerals, type of reagents and cost parameters are optimized.
Productivity up by 17%, noise levels down by 75% - Atlas Copco Surface Rock Drills rock!
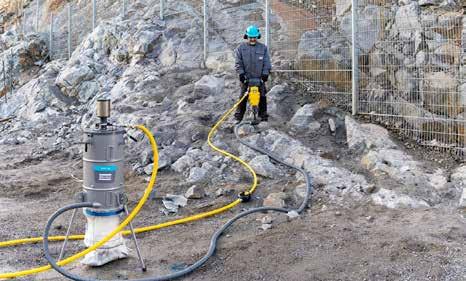
“Atlas Copco’s new Surface Rock Drills, the SRD range, is everything you want from a tool – reliability, efficiency, minimum maintenance, rapid service and low operating costs,” says Atlas Copco Power Technique’s Business Line Manager for Portable Products, David Stanford.
Owing to an ergonomic design, these powerful pneumatic rock drills are light-weight, versatile and easy-tohandle, getting the job done seamlessly, productively and safely. Engineered to perform optimally even under the toughest of working environments, these robust tools are ideal for drilling and breaking applications in construction and quarrying. Fitted with eco-friendly power packs, several drills can be conveniently and cost-effectively operated with a single compressor.
Thanks to the smart Solid / Single Body design, the pneumatic tools which are available in 20kg and 25kg versions, boast a world-class power-to-weight ratio making them well-balanced for easy, comfortable operation. The solid housing eliminates leakages and increases cylinder lifecycle while fewer moving parts means less wear. In addition, these one-piece machines are easy to assemble and disassemble, facilitating service and maximising up time.
The SRDs are equipped with Assisted Flushing Technology which is activated by opening the flashing valve to allow an additional flow of compressed air through a pathway in the cylinder to flush the drill hole while operating. “This technology can improve productivity by up to 17%!” notes Stanford.
Stanford draws attention to Atlas Copco’s a zero-compromise approach when it comes to operator safety and comfort, stressing that Atlas Copco places operators at the core of its tool design. The two-step SOFTSTART™ trigger gives operators full control enabling them to start a cut with surgical precision even under difficult conditions. In addition, these tools are HAPS™ (Hand and Arm Protection Systems) enabled which lessens the impact of vibrations, making it possible to extend working hours up to six-fold.
In order to further shrink vibration and wear, the tool’s piston switches on aircushions on both ends of the cylinder,
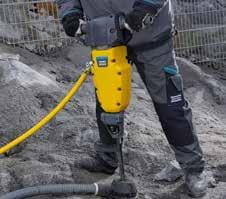
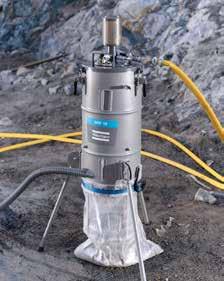
almost fully eliminating metal-to-metal contact when working off-load. The vibration level of the SRD 25 is 50% lower compared to previous generation tools.
Atlas Copco has developed a pneumatic dust collector to protect operators from the large amounts of silica dust produced during drilling and breaking. Powered by compressed air and utilising vacuum technology, the dust collector efficiently removes dust directly at the source, maintaining levels below the permissible exposure limit. The semi-automatic filter cleaning mechanism requires minimal maintenance, the dust collector consumes no more than 12 litres of air per second and its recyclable collection bags will last for an 8-hour shift. The unit is suitable for indoor and outdoor use.
High noise levels can affect an operator’s hearing and lead to fatigue. Atlas Copco has developed an improved wear-resistant polyurethane silencer that diminishes the noise levels of the SRDs by up to 75%. “This equates to a 2dB reduction in noise which makes a substantial difference, especially when several drills are operating simultaneously.”
Atlas Copco supports the SRD handheld pneumatic tool range with a professional after-sales service portfolio that includes high-quality Air Line accessories such as air hoses, hose nipples, couplings, water separators and Air Oil lubricants.
Real-time fleet and mine management systems in mining

Monitoring the company’s activity in real-time has many assets and advantages not to be ignored. This instant management allows us to visualize and know the real situation of the company as well as to monitor its objectives, key figures and performance indicators; it facilitates decisionmaking, manages its daily life more effectively and improves its reactivity and competitiveness. Regardless of the structure size, any good manager must be equipped with the appropriate resources to manage his activity effectively. This means that the positioning of carried out actions and committed budgets should be monitored, for both, quantitative and qualitative objectives.
The Fleet Management System (FMS) is a term used to refer to a wide range of solutions for different fleet applications in the fields of transport, distribution and logistics. It includes targeted planning, supervision and control of fleet operation ac-cording to available transport resources and application constraints. The FMS aims to reduce risks, increase service quality and improve a fleet’s operational efficiency while minimizing costs.
FMS is easy to control and optimize, its foundations date back to the 1980s when the computer was integrated with the vehicle and connected to different wireless networks by satellite and terrestrial. In the mining sector, the main objective of the fleet management system is to optimize mine production and efficiency based on real-time data. More specifically, the FMS aims to maximize mine production, minimize stock handling, feed the processing plant at the planned rate and meet quality mixing constraints.
The implementation of operational research techniques as the main means of addressing the high cost of transporting equipment to mines has attracted researchers and laid the foundation for FMS used in different types of mining. They considered the FMS as a real-time decision-making system for materials handling in mining. FMS obtains the required information about mining operations from the database and makes decisions accordingly. These decisions are then implemented in the operation and the FMS is recalled whenever a new decision is required.
Commonly, the primary objective of the mine fleet management system is to optimise mine production and efficiency based on real-time data. More specifically, the fleet management system intends to maximise mine production, minimise stockpile rehandle, feed the processing plant at the targeted rate and meet the grade blending constraints.
The common approach is a multistage optimisation, where the solution of each step is used in the next step and where the problem is divided into

three sub-problems: (1) shortest path model, (2) truck-and-shovel allocation optimisation – upper stage and (3) realtime truck assignment optimisation – dispatching – lower stage. The best path model determines the shortest route for travelling between every pair of locations in the mine. The truck-and-shovel allocation optimisation allocates haulage resources to excavating activities based on truck-dependent loading rates and maximisation of overall truck productivity.
A static scheduling algorithm is implemented to determine the optimal configuration of loaders over the mining faces as well as optimum production rates for each route connecting loading points to dumping points and allocation of truck resources to meet production target. The truck assignment problem in mining operation has been dealt with most as an assignment problem or sometimes as a transportation problem.
This programming algorithm assigns the trucks to a proper destination by the time the truck asks for a destination at an assignment beacon in a way that minimises the deviation from the production target.
The fleet management system mainly works based on two different set-ups: (1) fixed truck allocation and (2) flexible truck allocation. In fixed truck allocation, at the beginning of each shift, a group of trucks is locked to each transportation route. The trucks allocated to the paths are to work on the same path over the shift period based on several criteria, such as production requirement, availability of the trucks in the fleet, etc. The paths to which trucks have been allocated will not change until a shovel breaks down or a critical event happens.
Congratulations to our customers for OPTIMISING
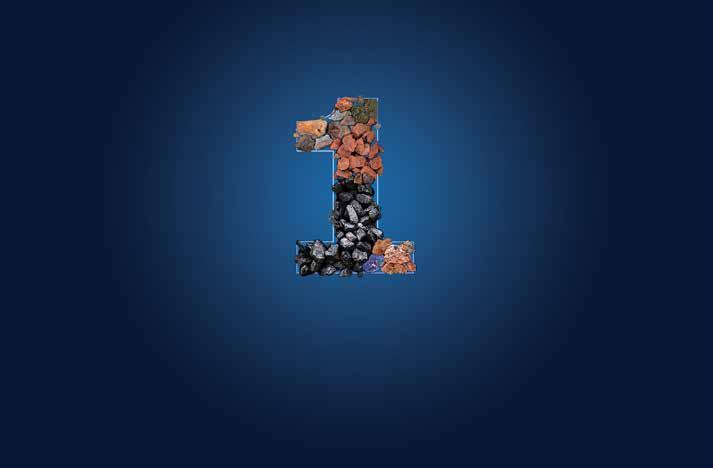
TRILLION TONNES of HAULAGE over the last 40 years
Leveraging Data and Innovation to Optimise the Mining Value Chain in Real Time
Contact Us
East Mining Company and Zyfra presented a digitalization project at Solntsevsky coal strip mine
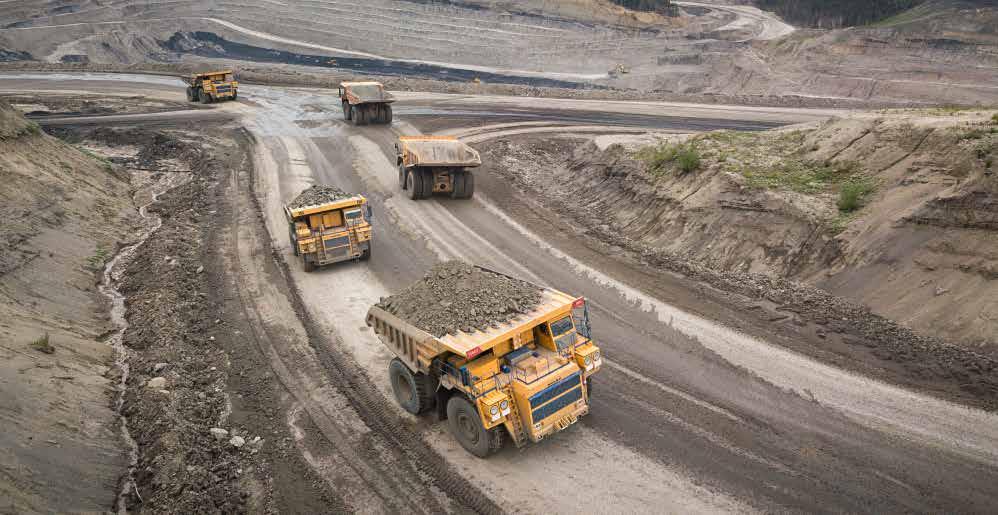
The East Mining Company (EMCO), one of major Russian exporters of brown coal, in cooperation with Zyfra, Finnish-Russian industrial digitalization leader, held a webinar on digitalization in the coal mining industry. The event addressed the current trends in the development of digital technologies in the coal industry, as well as the data culture, i.e. introduction of the data-based corporate culture.
The key point of the webinar was the presentation of the project to implement and customize the Zyfra OpenMine Fleet Management System (FMS) at the Solntsevsky coal strip mine in Sakhalin, the largest island of the Russia, situated in the North Pacific Ocean. The East Mining Company was represented by Stanislav Ploshchenko, Deputy CEO for Business Efficiency, Ruslan Karimov Deputy CEO for IT and Digital Transformation, and Evgeny Grabar, Project Manager for ERP System Implementation.
The EMCO specialists presented the first results of the Zyfra Open Mine FMS customization for the needs of the Solntsevsky coal strip mine. The system was put into commercial operation at the mine in December 2019. Almost 9 months of work resulted in a one-time increase of dump truck load by 10%. With the installation of on-board sensors, it is now possible to control violations of the security zones. Introduction of a modern fast fuelling system for mining haulage equipment helped to reduce fuelling time per unit by 2.5 times and increase the equipment performance.
“The main challenges we faced in implementing the system were the size of the company and a large fleet of equipment with almost 150 units inside the mine and about 120 units outside used to deliver the coal from the strip mine to the company’s port facilities of Shakhtersk. So far, all operation modes and procedures have been recorded and most of them are already automated. The next step will be to commission the latest version of the system, which will help to minimize the equipment downtime inside the open-pit and eliminate the lost time of backshovels. We also plan to introduce process KPIs for the dispatchers and operators of the equipment,” commented Stanislav Ploshchenko, EMCO’s Deputy CEO for Business Efficiency.
“Efficient operation of modern coal mining companies is impossible without a well-developed transport complex. For this reason, considerable attention is paid to improving equipment productivity, ensuring savings in all types of material resources, optimising vehicle loads and streamlining the coal grades. These challenges cannot be solved without using modern digital technologies,” noted Pavel Rastopshin, Managing Director at Zyfra.
About East Mining Company
East Mining Company is the major producer of thermal coal in Sakhalin region, Russia. The company is a among major Russian exporters of brown coal to the countries of Asia-Pacific region.
EMCO controls the full cycle from the extraction to the shipment of the products. The Sakhalin coal reserves have more than 300 million tons, and a prospected reserve in Magadan region of more than 100 million tons.
About Zyfra
Zyfra Mining (formerly – VIST), a mining division of Zyfra Group, Finnish-Russian industrial digitalization leader, has been successful in the mining industry for 30+ years with 80+ mines using the company’s products. The main solutions developed by Zyfra Mining include mine fleet management system, which collects and manages real-time information from mining equipment, autonomous mining dump trucks and drill rigs.
Komatsu 730E Haul Truck, photo courtesy of Komatsu

Modular Mining helps iron ore operation increase revenue through payload optimization
Introduction
Modular Mining introduced its nextlevel support offering, the Performance Assurance (PA) program, to ensure each customer receives maximum sustained value over the life of their Modular Mining technologies. With each PA engagement, a dedicated team of experts collaborates with a cross section of mine personnel to develop tailored, flexible, and proactive solutions to address each operation’s specific challenges.
Participating mines have seen numerous benefits, including enhanced truck productivity, shorter queue times, reduced equipment maintenance costs, and more.
Challenge
In accordance with a high-level performance improvement initiative, the mine sought to maximize equipment effectiveness and increase the rate of material moved, without expanding the existing fleet.
As part of the corporate program, the mine’s Integrated Control Systems (ICS) team identified that the payload size distribution of the fleet’s Komatsu 730E trucks exhibited an unacceptably high zero-payload count, per day. It was further determined that the zeropayload instances were attributable to the absence of data being sent from the trucks’ onboard payload systems to the DISPATCH® Fleet Management System (FMS).
In addition, a significant number of loads under 135t were being registered in the DISPATCH System; a value far less than the planned payload capacity of 190t. As a result, the same hauling effort
The DISPATCH Payload Optimization solution presents loading equipment operators with target payload information. The information conveyed is based on Komatsu PLM IV-OLS data (if present) or a pre-configured target payload that factors truck carryback into its calculations.
Once the truck is stopped and loading, the truck sends the PLM IV-OLS target payload to the DISPATCH FMS for display on the shovel system.
In addition, for each production record, the target payload, carryback, and measured payload values, are recorded, which further improves the payload data analysis. consistently yielded fewer-than-expected payload tonnes, per truck, upon arrival at the tipping point.
Resolution
The PA, ICS, and Mine Operations teams, along with support from Komatsu, collaboratively analyzed and evaluated the payload distribution inconsistencies, which led to the joint decision to implement Modular Mining’s DISPATCH Payload Optimization solution in conjunction with Komatsu’s Payload Meter IV® and Optimized Loading Software (PLM IVOLS) solution.
Working together, the teams performed the following actions: • Reviewed the health and configuration of the Komatsu PLM
IV payload sensors on all applicable trucks, and made repairs or adjustments, as needed • Updated the original equipment manufacturer (OEM) auxiliary software driver version to enable carryback polling functionality • Implemented the PLM IV-OLS solution on the Komatsu 730E trucks and the DISPATCH Payload
Optimization solution on the mixedmanufacturer shovels running the
Modular Mining ProVision® Shovel
System
Figure 1. Komatsu 730E TKPH before PA (Jan - Jun 2020) vs. after PA (Jul - Aug 2020) Data Source: DISPATCH FMS

Reviewed, updated, and configured the PLM IV-OLS Sprung Weight and Frame Torque parameters to calibrate the trucks’ suspension and control the effects of the empty vehicle weight on payload values
Results
As a direct effect of the implemented solution, the site realized the following measurable improvements:
The TKPH (Tonnes x Kilometres / Hour) value for Komatsu 730E trucks improved by almost 19%, increasing from 1888t to 2240t, as shown in Figure 1 above: Zero-payload counts reduced by 88%, down from 392 instances to 47* instances, per day, as shown in Figure 2 below:
Summary
Through the collaborative teamwork of Modular Mining PA, mine personnel, and Komatsu, the site’s payload accuracy increased dramatically – a significant step toward meeting the continuous improvement goals defined at the corporate level. Also, with the near-19% TKPH gained through payload optimization, the mine anticipates an equivalent revenue uplift of nearly $50 million (USD), per annum.
About Modular Mining
Founded in 1979, Modular Mining is the market-leading provider of powerful information management solutions for surface and underground mining operations, addressing the key areas of production, machine guidance, equipment health, and operator safety. Employing over 800 employees in 10 globallydistributed offices, Modular Mining has successfully deployed its solutions at more than 270 sites, worldwide.
For more information, visit: http://www.modularmining.com/
