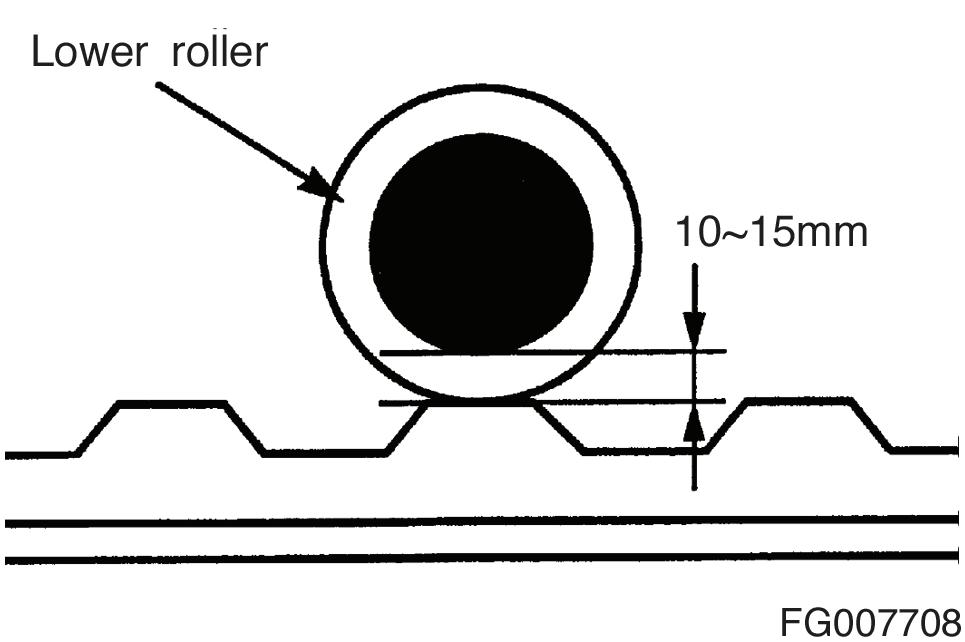
1 minute read
TRACK TENSION
from Daewoo Doosan DX85R-3 Excavator Service Repair Manual Instant Download (Serial Number 1001 and Up)
by fkms89dio8sk
Warning
AVOID DEATH OR SERIOUS INJURY
Advertisement
Measurement of track tension requires two people. Always follow these instructions:
•One person must be in the operator's seat operating the controls while the other person makes dimensional checks.
•Block frame to make sure the machine won't move or shift position during service.
•Warm up the engine to prevent stalls.
•Park the excavator in an area that provides level, uniform ground support and/or use support blocks when necessary.
The track adjusting mechanism is under very high-pressure. NEVER release grease pressure too fast. The track tension grease valve should never be backed off more than one (1) complete turn from the fully tightened down position. Bleed off grease pressure slowly. Always keep your body away from the valve. Always wear eye and face protection when adjusting track tension.
Track shoe link pins and bushings wear with normal usage, reducing track tension. Periodic adjustment is necessary to compensate for wear and it may also be required by working conditions.
Inspection
1.Turn upper body so it is at a 90° angle to tracks. NOTE: On rubber tracks, move machine body so seam of tracks pad is on axle centerline, then turn body.
2.Use the boom and arm to raise the machine.
3.Place blocking underneath the machine.
4.Raise the boom until the weight of the machine is resting on the blocks.
5.Stop the engine.
Turn the track backward 1 - 2 turns.
6.Measure clearance between track roller and track contact surfaces. Clearance must be approximately 10 - 15mm (0.39 - 0.59in)
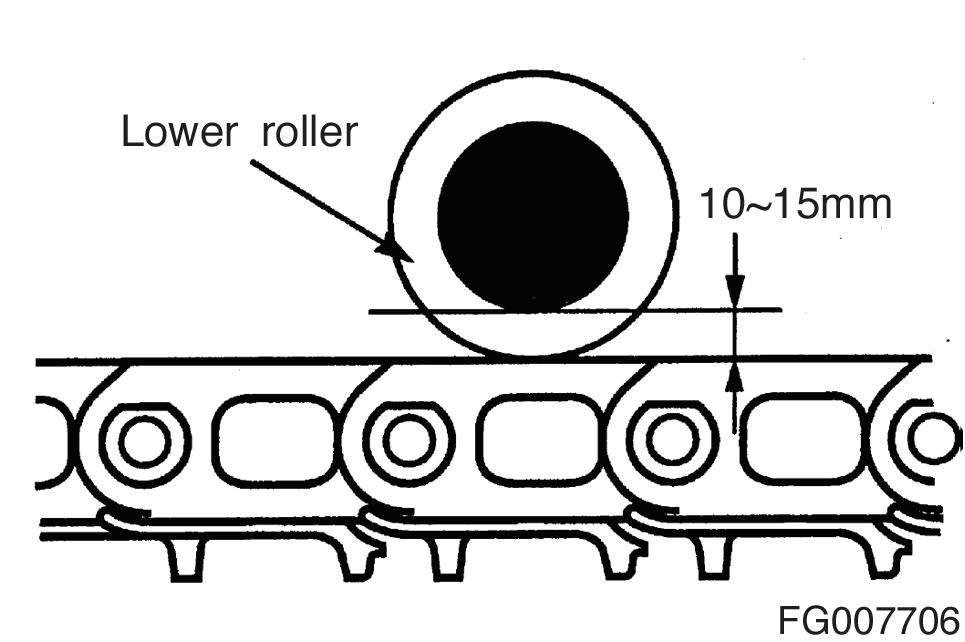
Figure 3
10 ~ 15 mm
Avoid Death Or Serious Injury
The track adjusting mechanism is under very highpressure. NEVER release pressure too suddenly. The track tension grease valve should never be backed off more than one (1) complete turn from the fully tightened down position. Bleed off grease pressure slowly. Always keep your body away from the valve. Always wear eye and face protection when adjusting track tension.
How to Increase Tension
1.Apply grease through grease fitting.
2.Move track forward and backward to distribute grease and readjust tension if necessary.
3.If tension cannot be increased, replace pin and bushing, or, on rubber tracks, replace cylinder seal or tracks.
To Reduce Tension
1.Loosening track tension grease valve causes grease to drain out and track tension to decrease. Loosen valve slowly to a maximum of 1 turns.
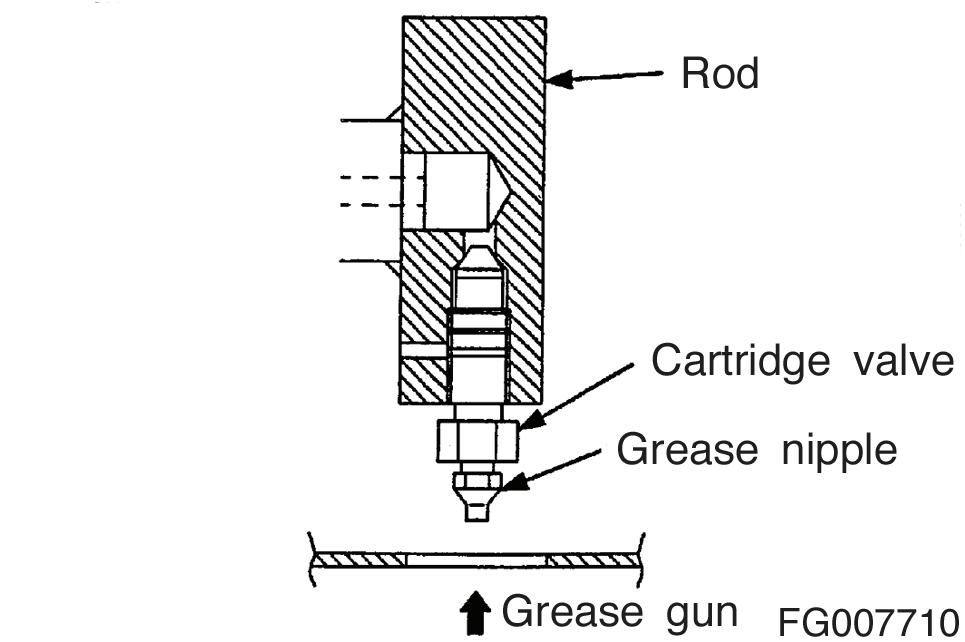
2.When track tension is correct, tighten track tension grease valve to 59 - 88Nm/6 - 9kg•m (43 - 65ftlb)
3.Recheck tension by moving track forward and backward.
4.Recheck tension and adjust as necessary.