
5 minute read
It’s in the Mix When it Comes to Concrete, What’s Submitted Isn’t Always What You Get
Anthony Perrello, Jr. Principal Sullivan Construction Group
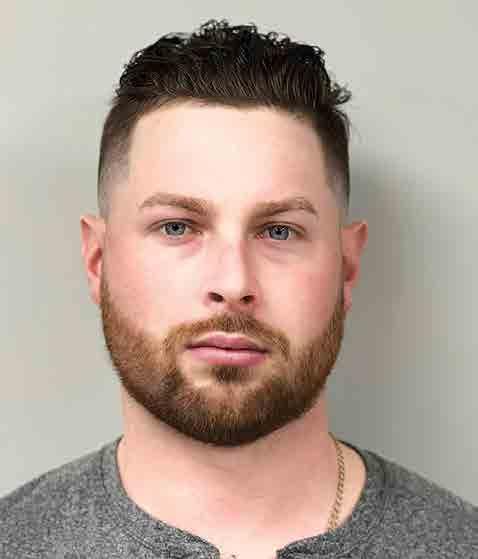
Concrete is the world’s most widely used building product with a history dating back to 6500 BC, and whether you’re a developer, an accountant, or a librarian you interact with concrete every day. It’s in the bridges we cross, the homes we live in, the buildings we work in and the schools our children learn in.
Concrete’s basic ingredients are cement, water, sand and stone. Simple, right? But as the world grows those ingredients change, deplete or are targeted by government policies, creating a very delicate balancing act.
Those of us in the industry are well versed in the pre-construction submittal process. You pick a vendor and request the material submittals sheets. We, in turn, submit them to the design team, get approval, and place the materials order.
Usually, you verify that the materials match the submittal. But how do you really know what you got? There are no on-site ingredient tests other than batch weight comparison to the submitted design mix but even that won’t prove that the specified ingredients were used. This is a systemic problem everywhere, and the Hudson Valley is no exception.
The submittal managing process is key to project success. The Sullivan Construction Group has developed strategies to navigate and mitigate these challenging issues, allowing us to become a leading concrete contractor in the region for complex concrete structures, specialty floors and industrial paving and parking lots.
Not All Mixes are Created Equal
Concrete mixes come in all shapes, sizes and usages. Think you call the concrete plant and order a 4000PSI and that’s the end of it? It’s just the beginning.
Foundations mixes are often based on functionality and strength design, so if the mix results in the appropriate strength, provides the proper coverage for reinforcement or embeds, and can handle the regional climate fluctuations, it will work for the job.
But placing the concrete can complicate things, and depending on distance, the concrete may need to be pumped or conveyed to the location. But is your mix pumpable? You must also hope that your ready-mix supplier used approved materials from the mix design.
“Slab-on-Ground” - or metal deck - falls under the same strength and functionality parameters with one caveat: Finishability, which is single-handedly the biggest issue in the industry for every flat work contractor. The ready-mix supplier is bound only by compressive strength or, at times, flexural requirements, neither of which tell you if the surface can handle the manipulating (floating, trowelling, etc.) during finishing. Meanwhile, if that finished surface peels or delaminates, the ready-mix supplier will shrug and say, “Well, the breaks came back good.”
So why does the philosophy of compressive strength not hold up? When finishability issues arise or aesthetics are challenged, the owner will often insist the contractor remove the floor and bear the cost. The comments are often made, “The finishers got on it late (or early),” but can you really tell without costly testing? Then the questions start. What was the cement Type I/II or Type IL? Was it natural sand? What was in the mix that was placed and finished? Did someone change the mix design?
The Usual Suspect (Hint: It’s Sand)

With the Hudson Valley developing as quickly - and for as long - as it has, our natural resources are being depleted.
Natural sand is a key ingredient of good, finished floors, and it’s commonly found near old riverbeds and lakes. As a result of natural erosion, natural sand is rounder and softer than other sands. It’s mined from the ground, screened and washed, used in concrete and other products. Its quality is measured by angularity, type, absorption rate and gradations (there is much more but these are the basics), and it’s often the best sand for good, finishable concrete. But clean and consistent natural sand is becoming more expensive and harder to find, causing many local ready-mix producers to turn to manufactured “man sand.”
“Man sand” is made by crushing stone to make coarse aggregates and is, in some ways, a byproduct. The stone is run through crushers to create the small particles used in concrete production. Quality is measured the same as natural sand, but it is usually far more angular.
Man sand isn’t all bad - it works great in most structure concrete, like footings, walls, and piers - but it does have its downfall in the use of slabs of any kind requiring a machined troweled finish. (It can be used, if treated correctly and tested for finishability with mockup “test” slabs and adjusted as needed.)
Your mix design may say natural sand from “ABC Sand and Gravel,” but that doesn’t mean that’s the sand in your mix. ABC may have run out and your ready-mix producer, in a scramble to make the pour, used an alternate sand supplier. Often you won’t be informed of these adjustments until there’s a problem (if they tell you at all.) If the breaks come back in spec, you are left with an expensive problem. The owner blames the contractor, and the ready-mix supplier doesn’t take any responsibility if the mix met strength.
Keep it Simple
Owner/developers, general contractors, construction managers, and design teams should understand these constructability issues ahead of time. If they do, they can play an integral role and help concrete subcontractors mitigate all the possible issues (and at the end of the day it’s their issues, too.)
Hire contractors that are committed to quality and continuing education with American Concrete Institute (ACI) certified personnel. Professional concrete contractors will be up-to-date on these issues and use things like preslab meetings to make sure these items are identified and coordinated. They’ll stay in front of issues and ask the tough questions, have the ready-mix suppliers re-submit mix designs with current materials used, and send the third-party inspection agency to make a plant inspection to guarantee the mix is what was approved.
Really, when you think about it, these upfront discussions are cheap insurance policies. You only get one chance to finish concrete correctly.
Cement Talk
Here’s a quick primer in cement types:
Type I/II
The cement typically used in the everyday construction operations in the Hudson Valley and Catskills regions are usually Type I/II, a general-purpose cement most often used for foundations, slabs, precast concrete products, bridges and pavements. It provides a moderate sulfate resistance to exceed the applicable ASTM and AASHTO chemical and physical requirements, ASTM C150 and AASHTO M 85.
Type IL
The new cement on the block that will replace Type I/II is the challenging Type IL, a blended portland limestone cement (PLC) that permits an interblending of naturally occurring limestone to a maximum allowance of 15 percent.
Type IL cements are more environmentally friendly than other types and have similar performance to Portland Type I/II, and is a sustainable cement building solution that significantly reduces carbon footprint. Although Type IL meets ASTM C595, AASHTO M 240 and ASTM C1157 it is also creating issues for concrete contractors across the country. The limestone blended into the cement is ground much finer in the cement clinker and has resulted in low breaks, set differentiation, and an array of finishing nightmares, including peeling and delaminations.
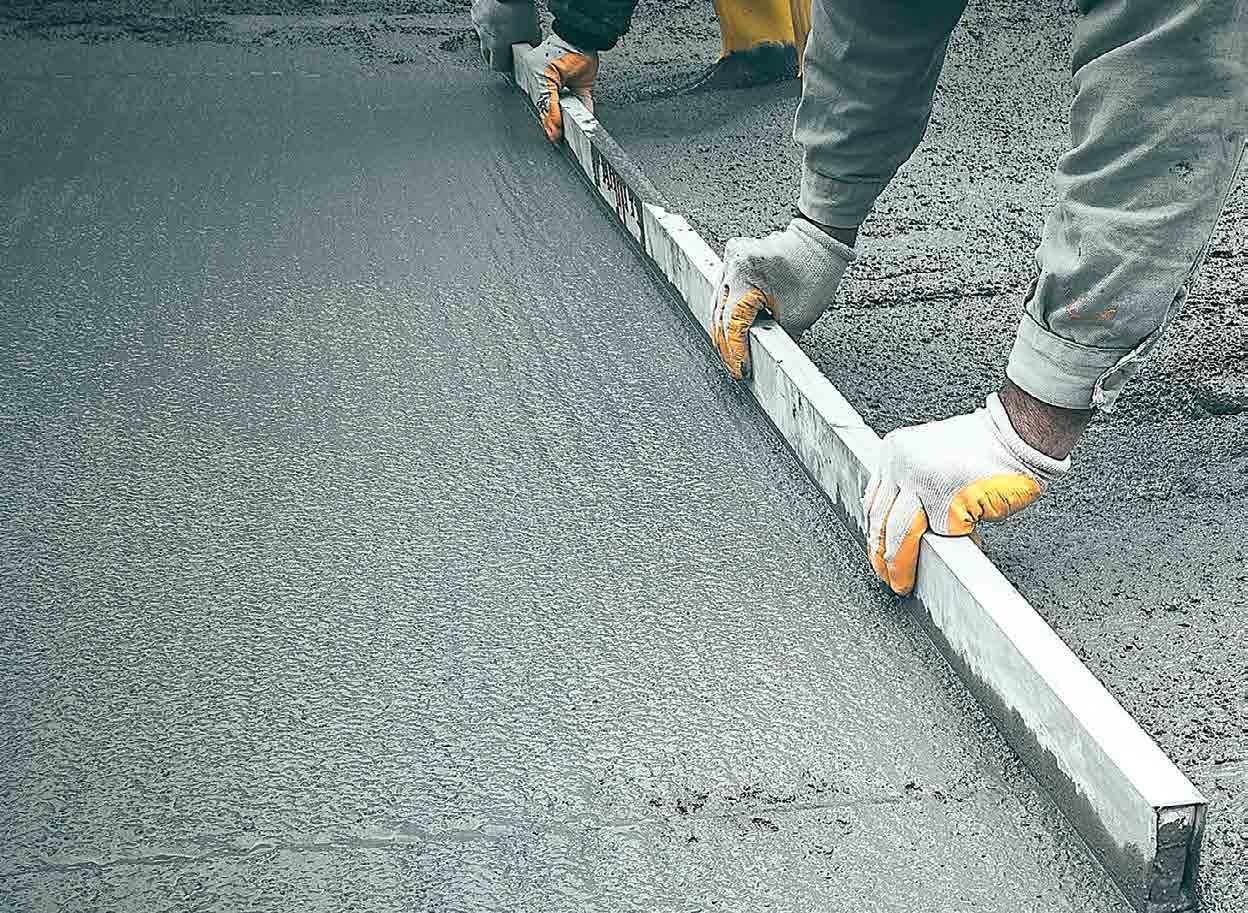
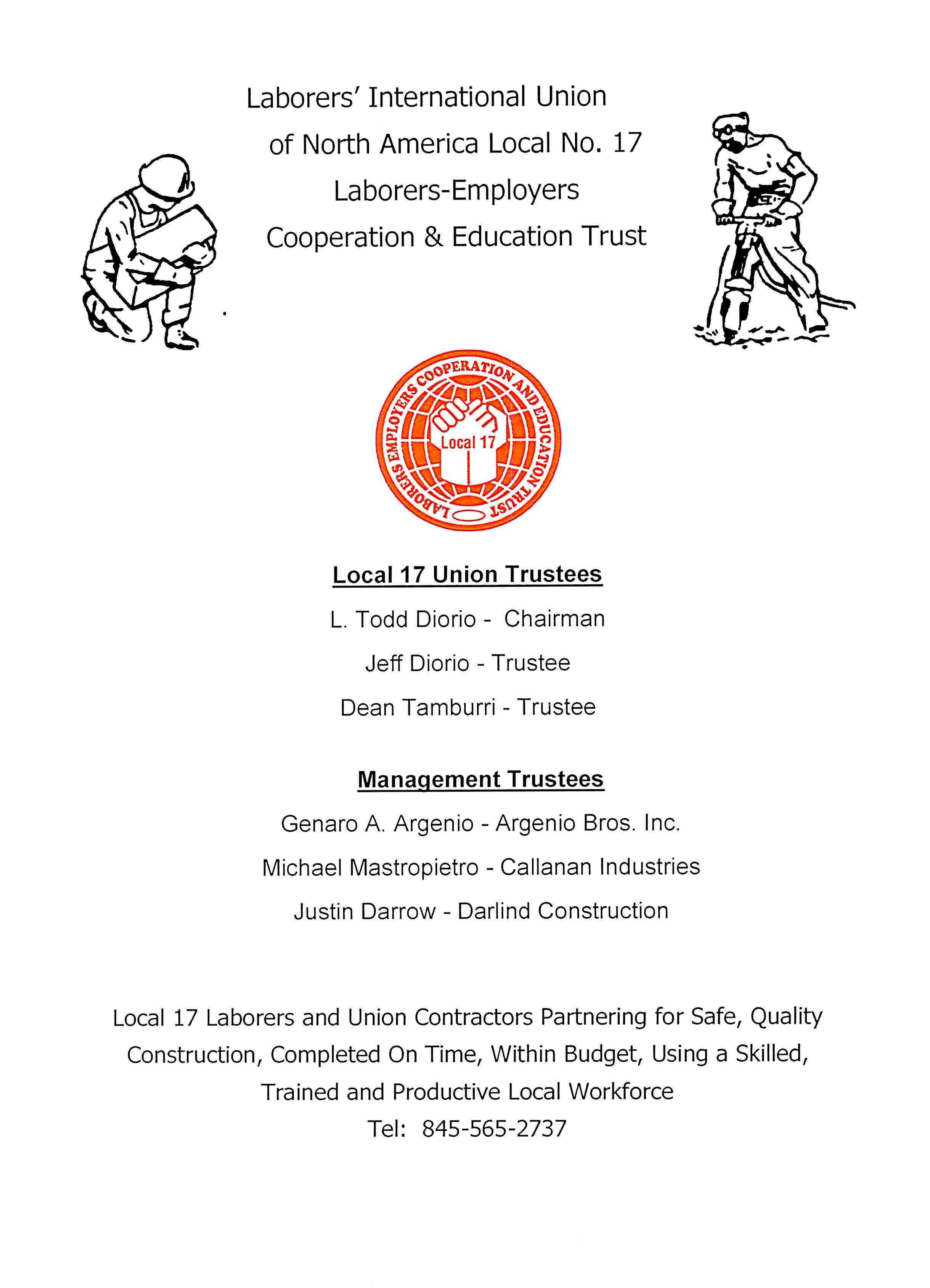