
2 minute read
RETROFIT DRIBBLE BAR
• 7.5m working width, 2.2m transport width
• Choice of Vogelsang or Mastek macerator
• Full lighting board is fitted as standard
• Can be used with a splash plate in place
• Parking stand and lighting board supplied as standard
• Retro-fits to the tanker back door
The trailing shoe system separates the grass sward to place slurry on the soil surface at the grass root for immediate nutrient uptake.
Within four to ve days after the grass has been harvested, Victor applies slurry at the rate of 2,500 gallons/acre. Within 25–30 days, the crop is ready for harvesting and feeding again. The surplus grass at peak growth times is taken out for bales which are fed during the winter months.
“The grass responds well to the slurry applied with the trailing shoe with minimal grass contamination and we are soon round to harvesting again," explained Victor. “Because it applies the slurry right where it’s needed, it helps to avoid losses from both evaporation and surface run-o , which is nancially bene cial as well as being environmentally considerate.”
Ruairi Delaney changed from suckler to dairy farming in 2014 and opted for a robotic system. He milks 130 cows with two robots in a grassbased system in Co Mayo, Ireland. He installed a Lely grazeway to allow him to graze in an AB system, where cows move to freshly allocated grass every 12 hours. This exibility gives him time to focus on grassland management on the family’s 130-acre plot. The land around his farm is hilly, so a 2300 Alpine Major tanker with 7.5m dribble bar slurry applicator is used to recycle farm waste. The dribble bar applies slurry directly on top of the grass sward thus minimising nutrient losses and allowing stock to return more quickly to grazing.
Both the Major Dribble Bar and Trailing Shoe systems can be retro tted onto any tanker make or model and can be used with an existing splash plate.
For more information about Major Equipment’s slurry handling solutions, visit www.majorequipment.com or contact the company directly. FG
“Strength, longevity and superior cutting”
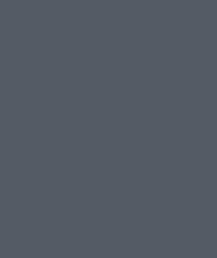
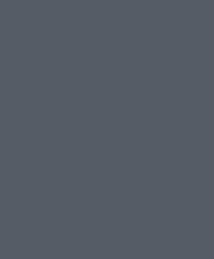
The Albutt Shear Grab range is designed to give users a strong, reliable option for cutting clamped silage. Trusted all over the world, the Albutt name is synonymous with a quality shear grab product, the company says. High-capacity rams, strategically placed, o er “unrivalled cutting power” with a Hardox blade leaving a smooth clamp face.
For maximum durability and strength, choose the Hardox tine models, says Albutt, the pioneer for using genuine Hardox tines in shear grabs. They provide 2–3 times better wear than mild steel, lengthening the life of the product and, as they are welded into the shear grab, eliminate the requirement to tighten tines as a part of routine maintenance.
The Albutt range varies from capacities of 0.7m3, ideal for skid steers and tractor loaders, right up to the 2.5m3 mighty shear king, which is ideal for loading shovels. Whether you are trying to load your diet feeder or anaerobic digester, Albutt reckons it has the right shear grab for you. For ease of ejection, a hydraulic push o is also available.
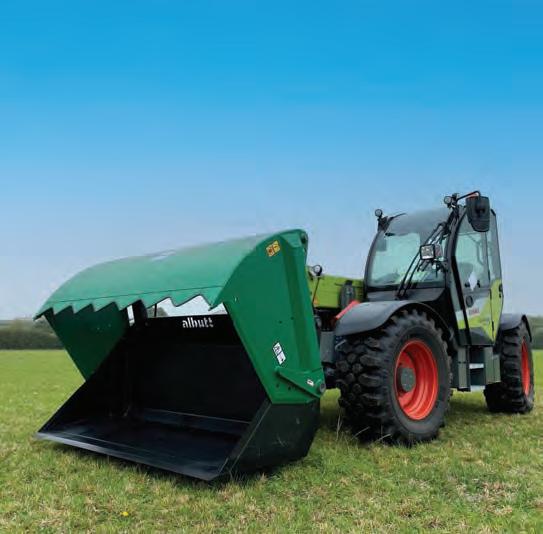
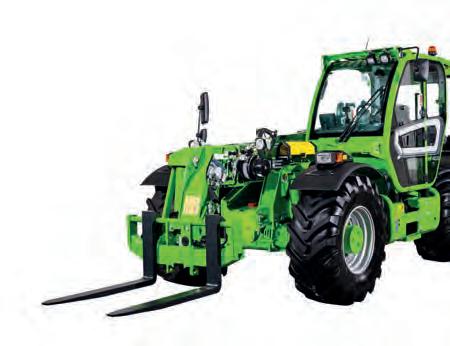
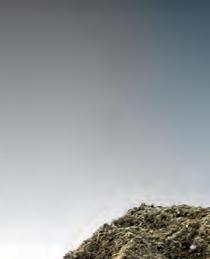
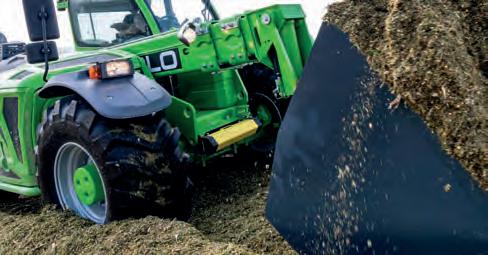
Albutt also produces a range of shear buckets; the rst created in 2017, based on the Shear King Mini. It featured Strenx Steel throughout the body, Hardox blades, bolt on wear pads and retained Hardox tines to support the bucket. Following its success the range expanded to 1m3 capacity right up to 2.5m3. FG
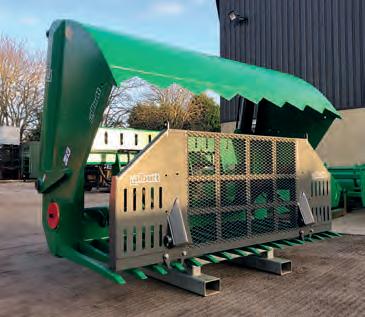