
9 minute read
Increased investment and a host of new products
Tyre manufacturer BKT is growing its product o ering and investing heavily in its already impressive Bhuj, India manufacturing plant. The company’s global sales exceeded $1Bn last year, and there are plans to double that gure within just three years. David Williams visited the factory and met the owners to nd out why the brand is so successful.
Balkrishna Industries Ltd (BKT) is a relative newcomer to the agricultural tyre market. The company was formed in 1987 to supply o -highway tyres lling a gap between expensive, premium brands and budget versions, to suit the average user. Since then, continued investment in research and development and meticulous attention to detail has paid o . Now the company’s huge range of more than 3,400 sizes of tyre includes high speci cation IF and VF radials capable of competing with other premium brands, and BKT tyres are listed as OE tment options by many leading tractor manufacturers.
Recent additions to the BKT o ering include rubber tracks, and tyres for special applications. Sales of over one billion US dollars were achieved for the rst time last year, and the company aims to double that gure by the end of 2026.
Successful investment
BKT has ve tyre factories in India, and the newest plant is at Bhuj, 850km north of Mumbai. The plant’s construction began in 2010 with a traditional site blessing and, by 2012 the rst solid tyres were produced. The plant is in an arid desert area, away from centres of population.
The area’s road and rail links are poor, there was no infrastructure to support the new plant and no local workforce. However, the 125ha needed was available there and two main sea ports nearby make it easy to ship tyres worldwide. Reservoirs were constructed supplying water for production and an 8km pipeline brings drinking water to the site. An electricity supply was connected from 13km away, although an onsite 40MW power station and solar panels currently provide all the power needed. Up to 7m depth of volcanic soil was removed and replaced by soil suitable for foundations and groundwork.
Labour supply issues were solved by an on-site village for workers and their families comprising modern, well-equipped ats accompanied by sports and social facilities as well as a supermarket and a medical centre. Approximately 900 families currently live on-site.
Research and development
One of BKT’s strengths is that the company builds its own tyre moulds, shortening lead times when adding new tyres to the range. Minor adjustments to optimise tread patterns can be achieved almost immediately, allowing tyres to be produced meeting speci c requirements.
A state-of-the-art 10ha research and development centre at the Bhuj site was completed in 2017, allowing intensive testing of new tyres and technology, and contributes to the short lead times for new tyres. Compounds, carcase and tread designs are all thoroughly evaluated. “Having a testing centre at the factory is crucial,” explained joint managing director, Rajif Poddar.
A tour of the testing centre included simulators – developed with Volvo, where operators sit at the ‘controls’ of earthmovers and dumpers and ‘drive’ them around work sites. Impacts and loads are assessed, and the data helps the development team design tyres ideal for the intended tasks.
Testing systems include huge steel rollers which rotate with the tyres, applying pressure and resistance, allowing a long working life to be simulated within just a few weeks, and including side loads to replicate operation on uneven ground and slopes.
An outside test area comprises six types of tracks and allows tyre evaluation on vehicles before nal testing by customers.
The thorough testing results in an extremely low failure rate of less than 0.25%, even though the radial tyres come with a six-year warranty.
Tyre manufacturing is complex, and the factory tour included explanations of how rubber
…from previous page compounds can be created to optimise ride quality and tyre durability, and how combinations of layers achieve the desired results.
BKT president and director of technology, Dilip Vaidya explained previously to Farmers Guide that the company’s fastest development of a completely new tyre took just 45 days, but the average time taken is six months from start of design to supply – far quicker than most other manufacturers.
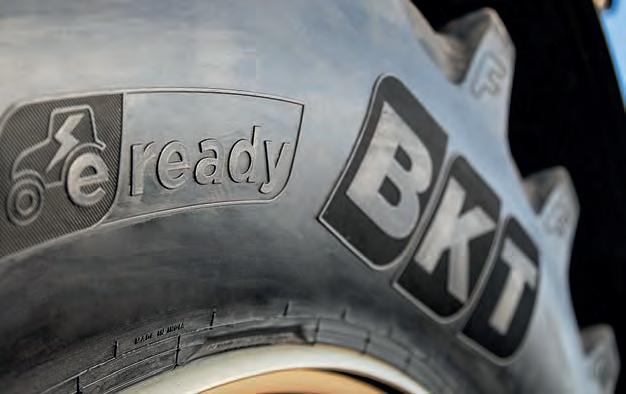
Catering for the future
Advanced construction techniques were used to create a new range of tyres for electric-powered tractors. The new tyres carry an E-Ready logo and BKT explained that reasons special tyres are needed include up to 30% additional unladen weight due to the heavy batteries; additional drive torque – especially when pulling away – so beads must achieve a rm grip to the rim and tread sections have to be optimised in terms of design and compound. Also, to achieve maximum working time between battery charging, the rolling resistance had to be minimised. This can account for as much as 20% of energy consumption, so the tread pattern, compound and sidewall structure were optimised. Noise levels are a ected by the tread pattern, compound composition and tyre size, so these were also designed for quiet operation.
Track range imminent
BKT has also added Agriforce rubber tracks to its range – with general availability due later this year. There are three types for di erent applications – construction, harvesters and agricultural.

Harvester tracks available initially will include 450-90-60 and 450-90-51. Agricultural tracks come in 18-644, 18-6-53, 18-6-54, 18-6-58 and 18-6-59. Product manager, Hemant Sawant explained that current track production is ve tonnes, or 20–25 units per day, but by 2024 production up to 50 tonnes of tracks per day will be possible, and a new dedicated track manufacturing facility is under construction to meet anticipated demand. “Development started in 2017, and ve years later we have tracks being evaluated by customers who report excellent performance,” Hemant continued. “When we are satis ed by every aspect of their operation, then we will o er them on the open market and eventually for OE tment by machinery manufacturers.”
Rajif Poddar said he has been thrilled by the amount of interest already shown by machine manufacturers. “It exceeded our most optimistic expectations,” he said. “The reason for the interest is due to the success and reputation we already have for our tyres.”
Heavy-duty solid rubber tyres
BKT also used the event to announce that solid rubber tyres will be available from the second half of this year. For industrial applications including forklifts and materials handlers, the tyres have holes through the pro le to provide cushioning and reduce shock loads and vibration. Three sizes will be available initially including 20.5-25, 23.5-25 and 26.5-25.
Specialist forestry tyres
A range of dedicated forestry tyres is also being added. “The key challenge is navigating forest terrain,” explained Mr Vaidya. “Our current agro-forestry tyres are suitable for use o - and onroad, on tractors and other specialist machinery, but the forestry tyres are exclusively for use o -road on forwarders, skidders and harvesters.” Designated ForestMax, the new tyres have eight plies and three steel belts and a special tread compound which withstands the high wear and tear typical in forestry applications.
Largest tyres
Larger tyres from BKT include its earthmover range. The biggest size currently is 46/90R57 – weighing 4,139kg per unit and standing 3,575mm tall. Each tyre is made from 28 separate components and each bead weighs 140kg. The tyres take 12 hours to cure in the moulds. Each tyre carries 63t, providing total weight carrying capacity of up to 240t across four tyres on a rear axle. BKT explained that the tyres not only achieve excellent load carrying ability; they are also designed for operator comfort which is essential in demanding quarry situations. Tyres with an even larger 63in rim diameter and weighing 7,000kg each are under development and due to be available shortly. Moulds will be ready by May, and the tyres will be available to purchase from August, with a 5,000hour warranty and an 8,000-hour predicted working life.


Meeting demand
Recent completion of a new radial tyre production facility in 2021 has increased total capacity to 700 metric tonnes per day. Within the new 9ha building, tyres are manufactured from scratch, and the optimised working environment includes cooled air increasing comfort for employees. Automation includes robots performing repetitive actions including cutting rubber sheets to size, and for painting. Cameras automatically check production quality throughout the process. Like the other BKT buildings, a digital gallery displays production gures and real-time power consumption.
Rapid growth
When tyre production started at Bhuj, the site was just 123ha and represented a $500M investment. The current site is 258ha, but land recently purchased adjacent to the plant increases the area by almost 30% – to 323ha. The additional $0.5Bn planned investment includes tyre production facilities, but also a move into Carbon Black manufacturing on a massive scale. Carbon Black is essential for
The McCormick X6.4 has evolved, so much so that it received the “Tractor of the Year 2023 Best Utility” award. Confirming itself as the best tractor in its class. It features a more powerful and efficient engine, P6 Drive 6-speed powershift transmission, and new McCormick High Visibility Cab. Demonstrating the strength, e ciency and quality that makes a McCormick tractor.
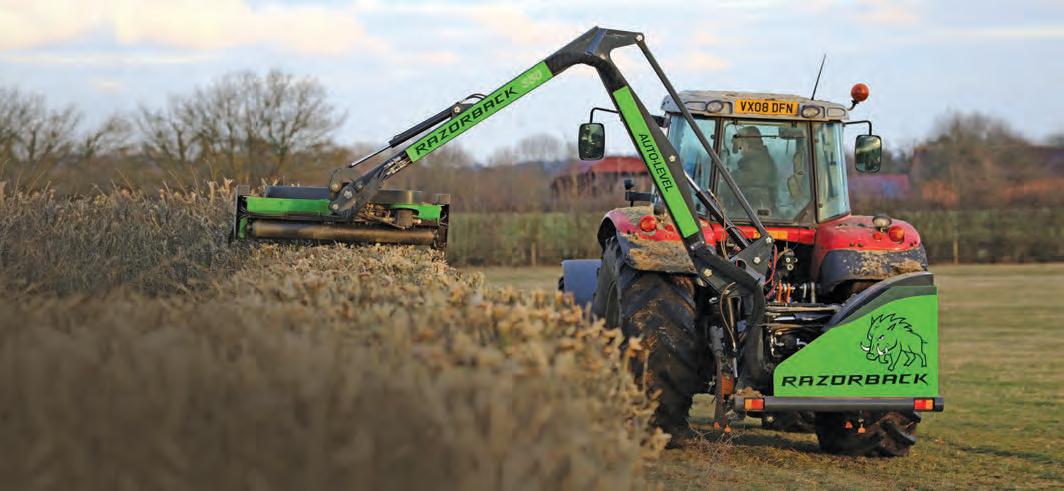
A NEW CHAPTER IN NO-TILL FARMING AVATAR SD
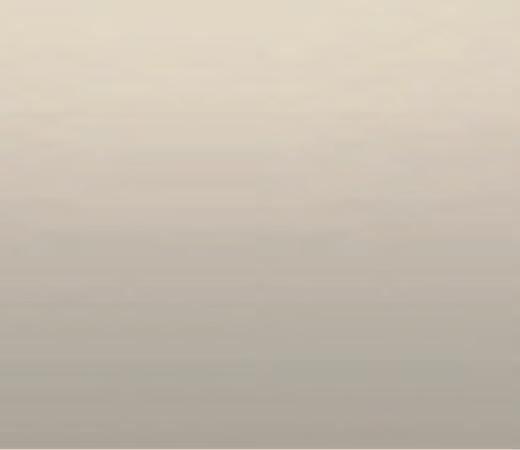
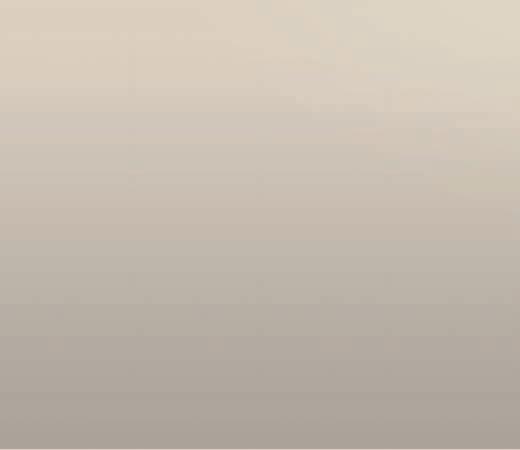
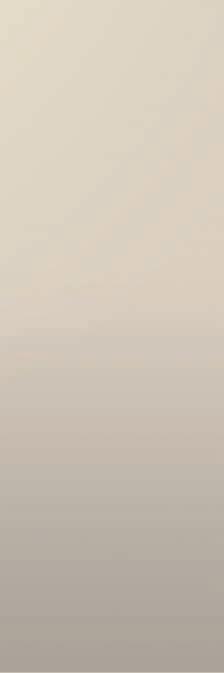

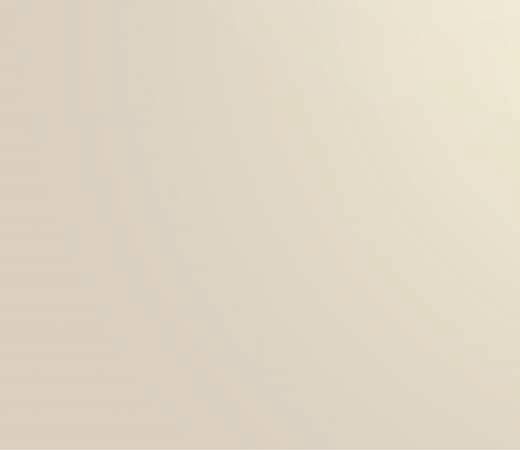
High performance direct drill with single disc coulter for no-till farming, with versatile hopper systems including grain & fertiliser and micro-granular. A compact machine with working widths from 3m to 8m, 12m and 18m, Avatar SD can be used universally from direct drilling to cultivated soils.
tyre manufacturing, and accounts for up to 25% of a tyre’s construction. The current Carbon Black production plant started operation in 2017, when 65,000t of the hard grade Carbon Black for tyre tread was produced. Production increased to 110,000t in 2018 with the addition of soft grade Carbon Black, and in 2020 with the combined production of both types reached 138,000t, increasing again to 165,000t last year. Almost 200,000t will be made this year, including Speciality Carbon Black suitable for use in paints, plastics and inks.
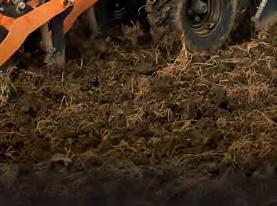
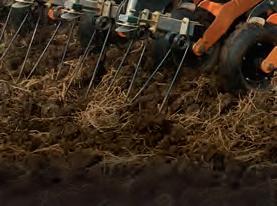
BKT has invested in a new approach to production at its plant –making the process more sustainable and reducing CO2 emissions. Energy produced as a by-product during manufacture helps power the plant. Approximately 70% of the Carbon Black produced is used by BKT, and the rest is sold to external customers including tyre manufacturers.
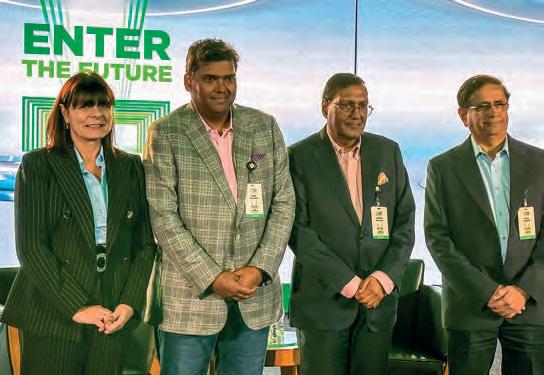



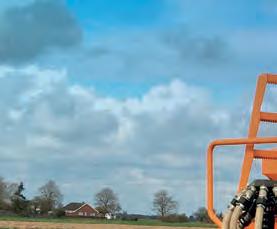
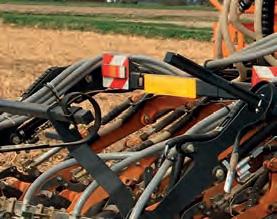
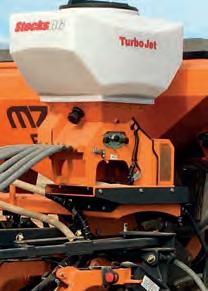
Managing environmental impact
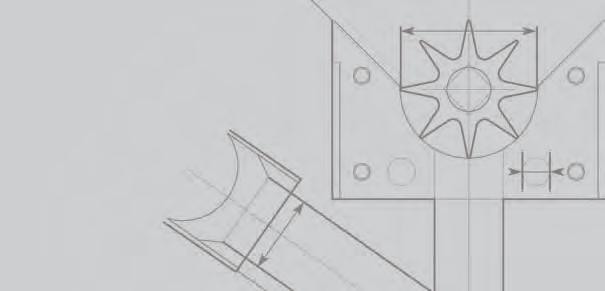
BKT is proud of its environmental credentials. Approximately 30% of the site area is green, and an onsite nursery produces bushes and trees for the plant. The environmental impact of tyre and Carbon Black production is monitored, and particulate and emissions gures are available to view at monitoring stations at the site. Emissions are approximately half the legal limits – which a spokesman explained are stricter in India than in most other countries. “When the plant is operating then we are creating emissions,” he acknowledged. “The key is managing the emissions to operate as cleanly as possible.” All water used is recycled and nothing is
…from previous page discharged outside the plant.
BKT also acknowledges its responsibility to the local population and con rmed investment in a school for up to 1,800 pupils to be built adjacent to the plant, and which will also be available for use by adults out of school hours.
Future growth
In 2022, the BKT Bhuj plant achieved total tyre production averaging 436t per day, contributing to the company’s total sales of $1Bn. Development of the additional land and construction of the new tyre and Carbon Black production facilities is due to start soon, and Rajif Poddar expects them to be operating within just two years and by 2026 the company’s plan is to produce 600,000 metric tonnes of tyres annually. Up to 1,240 families and 400 apprentices recruited from colleges and seeking practical experience will be living in housing provided at the Bhuj site.
“We are not just a tyre company,” concluded Rajif Poddar. “Global tyre demand is growing, and we see no signs of it slowing down over the next ve years. Our vision is simple which is why it is certain.” FG
Sustainable farming
Farming in north-west India tends to be on a small scale. Agriculture employs 45% of the country’s workforce – equivalent to 230 million workers, but the average farm size is only 1.08ha, compared to 14ha across the EU.
Farmers Guide visited two farms approximately 200 miles north of Mumbai, both of which have diversi ed to remain successful.
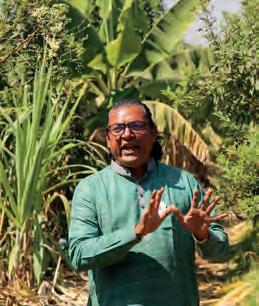
The Va Vagdo SPK Farm at Olpad, near Surat produces 60 di erent crops at its 1.25ha site. Farmer Mr Raj Deep struggled to produce good crops when farming the saline soils using conventional methods, and eventually gave up, but tried again a few years later using an organic production regime recommended by an advisor, with the land ridged and complementary crops grown side by side. The ridges were created manually and no machinery is used except for a small tractor and trailer to move goods around the site. Up to 127cm of rain falls each year – all between July and September – which creates a challenge. Drip irrigation ensures e cient use and e ective take-up by the plants. Nutrients including cow manure and sugar cane by-products are sourced from local farms, and the crops self-seed so there is no need to replant each year. Mr Deep farms single-handed most of the time, with help from two neighbouring farmers during busy periods. The three farmers help each other with no payments exchanged.
The organic salad, fruit and vegetable crops are sold direct to customers, and achieve prices more than twice that of similar crops grown using arti cial fertilisers and chemicals in the area. “This is my ATM,” Mr Deep explained as he plucked a g from a tree.