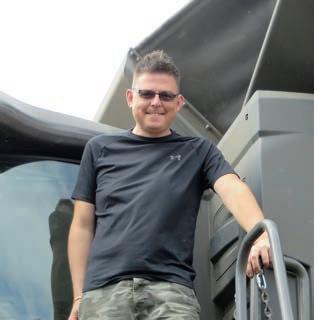
8 minute read
alking combines improves harvesting effi ciency for
Big claims have been made for Agco’s multibrand Ideal combine, but with a radical new design, has the gamble paid off for early customers? Jane Carley catches up ith one company using the combine to fi nd out more.
Ideal for the future
Replacing two New Holland CR9080s with a pair of Fendt Ideal 8T combine harvesters is described by Lincolnshire Field Products (LFP) senior farm manager Paul
Langford as a ‘leap of faith’, but it as also a move made ith specifi c business goals in mind.
With 1,750 hectares of combinable crops just one part of the Spaldingbased enterprise, the cereal harvest has to be fi tted in to a tight indo between vegetable work and the potato and sugar beet harvests.
Mr Langford comments that the opportunity to increase capacity and save fuel were two factors in considering the deal.
He says: “We were looking to go from . to . metre ft to ft headers and the direct drive and improved crop fl o of the deal as promised to match the improved output ith fuel savings.
The combines tend to work in pairs, so to take advantage of this the two 8Ts have been set up with machineto machine communication. ne has the manufacturer’s full Ideal Harvest settings software package, with the second machine taking all its settings and A lines from the fi rst.
They are also equipped with ‘Fendt Connect’ telemetry, using Agco’s server to transfer harvest results into Gatekeeper and send machine data such as fuel and AdBlue consumption direct to the farm offi ce.
Harvest data is uploaded as soon as the operator confi rms that the fi eld is completed, and is separated from other information so that it can be accessed by invited third parties such as an agronomist.
Yield maps
“This enables us to study yield maps promptly and act on information such as lower yielding patches located in areas shaded by trees or subject to pigeon damage, e plains r angford.
“Also, we have already been able to assess fuel savings, with the Ideals using some litres a day each less than their predecessors.
Mr Langford points out that the Ideal design means many of the features were familiar to the drivers
BEN WALKER
as it uses established components such as the Vario Terminal and joystick used in the Fendt tractors and sprayers in the company s fl eet.
‘Combine A’ operator Ben Walker comments that Ideal Harvest gives him the ability to visualise crop fl o for the fi rst time, using readings from sensors in the threshing and separation areas which are displayed on a tablet in the cab.
“I input my required settings and deal arvest confi rms them, and can then view where the crop is along the rotor and sieves at any time and quickly make adjustments to solve
Wider tracks – sourced from Agco’s Challenger plant at Jackson – proved to be benefi cial in wet harvest conditions. any issues. reviously had to use my e perience and make assumptions using only what was in the tank and loss monitor readings.
The variable wheat crop in 2019 has also made good use of the fi rm s Harvest Plus cruise control, set to maintain the intake rate at the feeder housing at a pre-determined level by adjusting forward speed according to crop density. r alker can also fi ne tune his preset rate on the move, as conditions change. r alker says An e treme rain event in une fl attened much of the heat in the area, but the o erfl o header’s belt design has tackled that and this year s diffi cult oilseed rape with aplomb – an improvement on e tendible type tables.
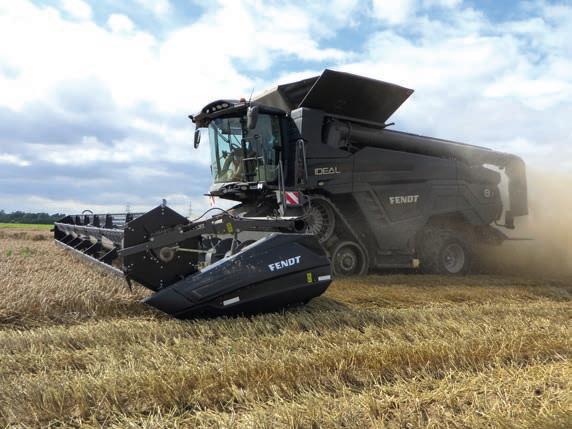
Conditions
utputs have been about to tonnes/hour in testing conditions, with Mr Walker noting that in the peak of the wheat crop he was getting some hours on half a tank of diesel
“The combine’s twin rotors compact the crop less and only run at 800-1,000rpm, compared to the , rpm of the s rotors. You get the same separation but ith lo er fuel consumption.
All straw is baled, going to a variety of markets, Mr Walker says: “Because of the action of the rotors, straw quality is decent. As ith any rotary combine, the crop-on-crop threshing means that
The combines have 10.7-metre headers, increasing capacity and matched with high output from a double helix rotor threshing system.
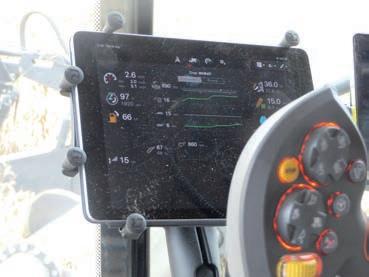
Ideal Harvest technology uses data from using sensors in the threshing and separation areas, with information displayed on a tablet in the cab.
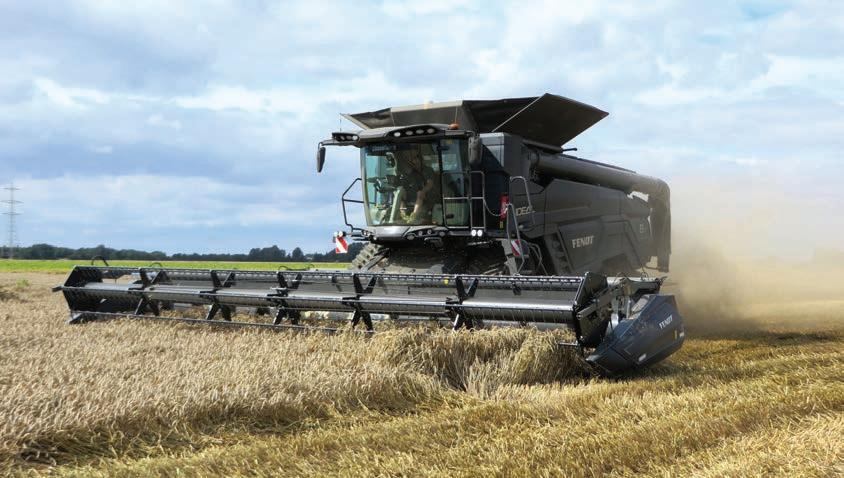
grain quality is also good, with no splitting.”
Mr Walker has also enjoyed his time in the cab.
“The Variterminal is on a rail so that you can position it to suit your preferences; I have it right at the back, with the smaller tablet at the front so I have got an unimpeded view of the end of the header.”
However, he says there are some improvements to be made to the Variterminal’s screen layout. hen fi nding fi elds for e ample it is necessary to fl ick through numerous pages, whereas on the tractors, there is a ‘quick jump’ setting which would be a great help if it was added. That said, the harvest settings are a lot easier to get into.”
Another item on his wish list is longer mirrors to help judge the position of the combine body better.
“I use the 360 degree camera to keep an eye on traffi c and potential ha ards on the road, but fi nd that the image quality is not that good, even when the camera is clean.
“The reversing camera also produces a fi sh eye image hich can distort perspective and make judging distances tricky.”
FENDT IDEAL 8T Z
● Engine: MAN 12.4 litres 538hp ● Fuel tank: 1,250 litres ● Transmission: two-speed Motionshift 40kph ● Header: 10.7 metres ● Rotor: Double helix ● Total separation area: 4.06sq.m
BEN WALKER
Suspension
He notes that while the tracks follow ground contours well enough in the fi eld and allo the header to ride accurately, their lack of suspension can make them bounce on the road.
“They are slightly wider than the ones we had before so give a larger footprint which has proved its worth in this wet harvest,” says Mr Walker.
“However, the combine itself is narrower so we are no wider on the road. I was keen that the axle width should not be too narrow to maintain the turning circle, and avoid the need to shunt backwards and forward on corners which increases compaction.”
Mr Walker is also impressed by the cooling and emissions management packages.
“The exhaust and manifold are well positioned and the engine bay is one of the cleanest that I have seen – there are no dust traps anywhere.
“The reversing fan is very effective – I have not had to blow out the air fi lters, and in general the simple drive makes it easy to service, with just three chains to oil.”
So is it the ‘ideal’ combine?
“We are not quite there yet but with the improvements in fuel savings, stra uality and effi ciency it could be fantastic. In two or three years it will be excellent.” says Mr Walker.
Paul Langford points out the potential benefi ts for ith the wider header we are getting 15 to 20 per cent more output, which given that we have a harvest season of 30 days could shorten it by four to fi ve days, giving us peace of mind in a catchy season such as this.
“The simpler design also means less wear and tear and less downtime, plus we are also using 350 litres of fuel less per day per machine. At this early stage, we can say that it is starting to prove itself.”
● Total sieve area: 5.4sq.m ● Grain tank capacity: 12,500 litres ● Unloading speed: 140 litres/second ● Cameras: rear view/360 degrees optional ● Price: £477,440 including 10.7m header
MACHINE-TO-MACHINE COMMUNICATION Z
THE combines share settings via Fendt’s server using Fendt Connect telemetry, explains Fendt harvest specialist Ant Risdon: “When several machines are working together, ‘Combine A’ sends its settings to the server and they are then transferred to all combines in the user group. The operators of ‘Combine B’ and so on accept the data and the A-B lines and settings are transferred to the machines.”
Fendt Connect also allows data to be sent to the farm manager and other parties as required, using VarioDoc Pro to produce records which can be integrated into Gatekeeper or Farmworks software.
In the case of LFP, before each fi eld is harvested, the agronomist sends job specifi cations to Combine A via Fendt Connect – A-B lines, crop type, variety and any fi eld obstacles. Using fi eld recognition, the operator accepts the fi eld and harvesting can begin.
After the fi eld is completed, a harvest record is transferred back to the offi ce and into Gatekeeper.
Mr Risdon points out that there are no distance limits and machines do not have to be within line of sight as the data transfer is via the phone network, although they should ideally be in the same fi eld.
Functionality is built into all combines so the system could easily be adopted or extended if adding another machine to the fl eet; ultimately Agco plans to extend machine-to-machine communication to tractors, matching the movements of grain cart operation to the harvester.
“The ability to share waylines when two combines are harvesting the same fi eld is most important for LFP as they have experienced operators who can work to their own settings. We can see that sharing settings to a whole group will be very useful in Eastern Europe for example, where there is less skilled harvest labour,” says Mr Risdon.
Combines generally work in the same fi eld, so machine-to-machine communication is used so that the two machines can share waylines, and if required, harvest settings.
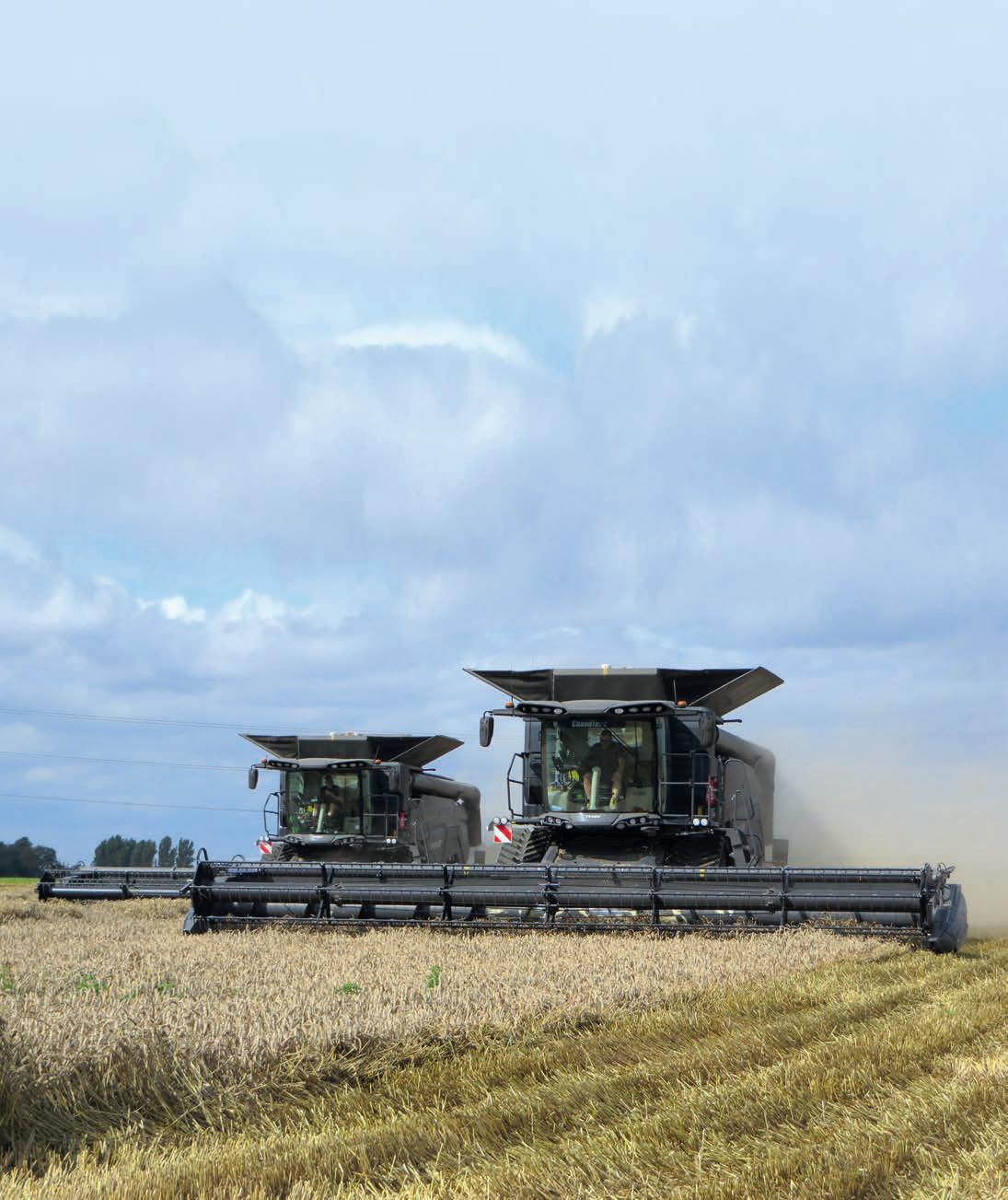