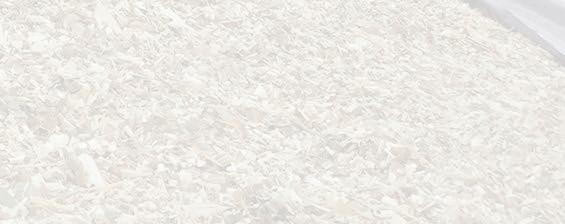
6 minute read
SILAGE STORAGE
Building a new clamp rather than relying on baled silage can help dairy farmers reduce costs, minimise use of plastic on-farm and lower their carbon footprint signi cantly, according to forage production specialists.
Over a 20-year period, costs of ensiling each tonne of silage would be halved, use of plastic would be nearly 20 times less and associated
CO2 production would be reduced by nearly 95%, says Will Wilson, of forage systems specialists
ARK Agriculture.
He says: “Modern high oxygen barrier lms combined with the latest technology in clamp building are giving producers a real opportunity to move their forage production forward and make the most e cient use of home-grown feed materials while minimising environmental impacts.
“It is a great example of new technology making established practices signi cantly more e cient and more aligned with processors and consumers’ desires to see farming reduce its carbon footprint.”
He adds that many of the practices producers have relied on are becoming ‘increasingly unacceptable’ in the era of more sustainable production and he says excessive plastic use is just one of those.
Looking at the construction of a 10-metre by 45m by 3m clamp reveals some interesting comparisons to baled silage, he says.
“Such a clamp is going to cost about £80,000 to build and, at 0.7t/ cu.m, it will hold about 1,000t of grass silage, so every 1t stored costs about £80 in build costs. Over 10 years, that is going to be £8/t stored and, over 20 years, it will be £4/t.
Charges
“Wrapping a 700kg bale including contractor charges is about £7/bale, which equates to about £10/t – signi cantly more than the £8/t over the rst 10 years of the newly built clamp.
“Over a 20-year period, well within the serviceable life of a modern silage clamp, you will be storing your silage for much less than the same operation using big bales.” e numbers get even more a ractive when you factor in plastic use, says Lucy Johnson, of silage lm specialists Silostop.
“You should be able to cover 22 x 700kg bales with six layers of lm for every 24kg roll of wrap, so that is about 1.09kg of plastic per bale or 1.54kg/t; 1,000t of wrapped bales will require 1,540kg of plastic per year, costing about £4,500/year at £75/roll.
“Looking at the clamp situation, a roll of 50m orange high oxygen barrier lm weighing 26kg will cover our 1,000t of clamped silage.
“Side wall lm will add a further 44kg, so that is 70kg.
“You will also need two 12m anti-UV covers weighing 120kg in total, but these will last for six years, so that is 20kg/year of plastic.
“ is is a total of 90kg of plastic used to produced 1,000t of forage in a clamped situation, compared to 1,540kg of plastic for the equivalent weight of baled silage – over 17 times more.”
Cost-wise, Ms Johnson says the plastic required for the big bales will cost £4,425/year at £75/roll, whereas the high oxygen barrier lm and covers for the clamp will cost about £870 for 1,000t of silage at current prices.
She says: “Assuming both types of lm require the same amount of energy to produce and release the same amount of greenhouse gases in the production process, the lm will have a carbon footprint about 95% less than for the plastic required for the big bales.”
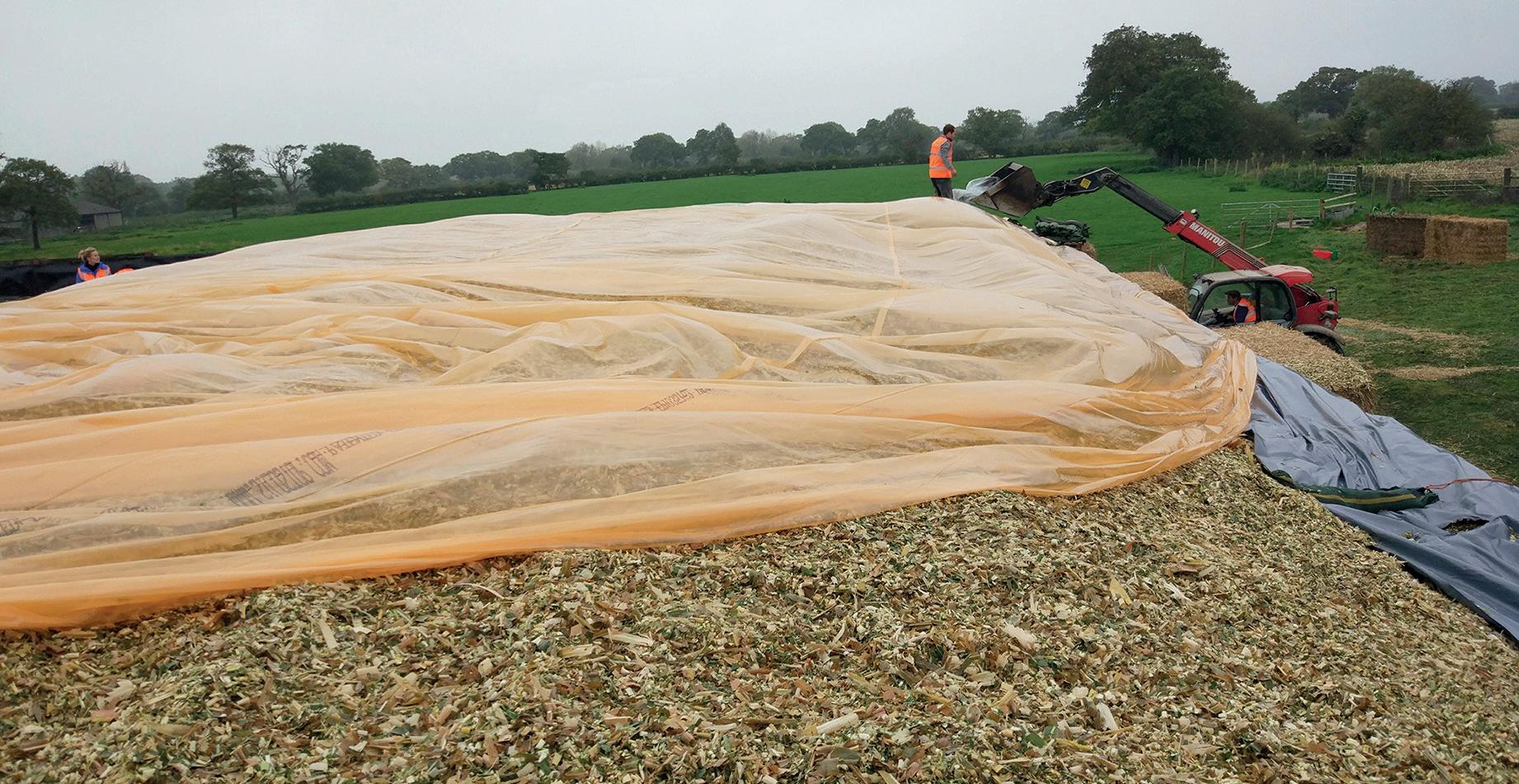
Developments in silage clamp construction and coverings are increasing the efficiency of silage production significantly while minimising waste and the associated carbon footprint of milk production. Dairy Farmer reports.
Silage storage choice has environmental and financial impact
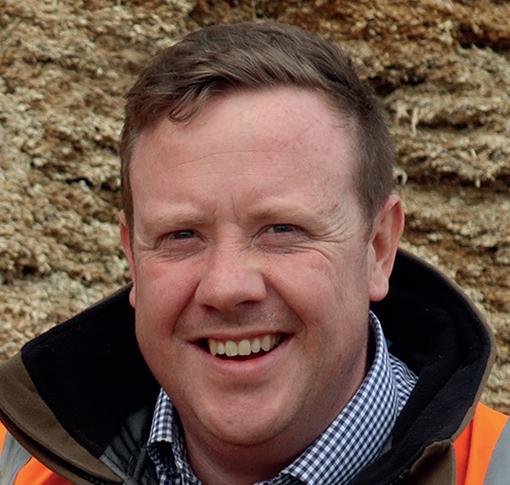
Will Wilson
To clamp 1,000 tonnes of forage, about 90kg of plastic is required, compared to 1,540kg of plastic for the equivalent weight of baled silage. Lucy Johnson
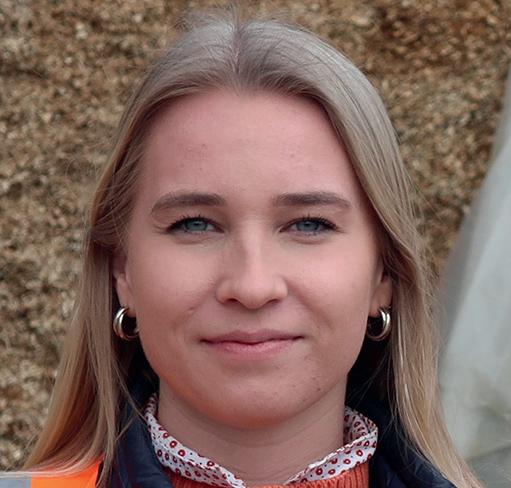
e numbers associated with clamped silage over the baled equivalent are impressive, but they are not the only advantages, she says.
“ e general direction of travel in dairying is for be er use of resources and proper management of waste, so unnecessary use of big bale silage is contrary to this.
“Bales are normally stored on porous hard-standing or soil, so e uent management is more di cult than with a properly designed and managed clamps.
“Baled silage also takes up more space on the ground as they can only really be stored three-high as a maximum. Even at three high, the bo om bales are compressed and this can allow air ingress and e uent leakage as the wrap moves.
“Baled silage also has more variability in terms of quality and is harder to evaluate for rations unless each separate eld is marked and fed accordingly. Clamped silage has more even quality as the forage is mixed thoroughly during the ensiling process.
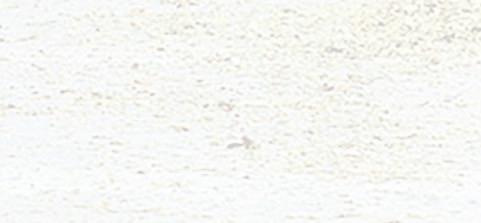
Vulnerable
“Wrapped bales are very vulnerable to bird damage both in eld and in the stack and do not forget all waste plastic on-farm must now be recycled by law.
“Waste companies do not tend to like bale wrap as it is thin plastic with high contamination levels due to the silage and soil contained, so it can be very expensive to deal with.”
Mr Wilson agrees, saying with more dairy companies factoring the carbon footprint of the milk they are buying, high energy, high input practices will come under greater scrutiny in the future.
“A farm’s carbon footprint is increasingly being benchmarked by dairies and milk buyers with plastic use guring in these totals more and more. Historically, such things have been fairly low on the agenda for many milk producers, with other important management decisions taking priority.
“ e expansion in herd size over recent years has meant cow accommodation and manure storage have o en been seen as more important than the extra forage storage capacity needed for this, but things are changing.”
Home-grown forage is becoming even more important in the dairy pro tability equation and is seen as one of the most important ways to reduce input costs in the future with poor forage management less tolerated than ever, Mr Wilson says.
“Over lled clamps or poor compaction levels, for example, are not only bad news for cows, they are dangerous to operators and shorten the longevity of the clamps themselves. I think this is being recognised.
“We are de nitely starting to see be er producers realising good clamps are as important as any other piece of infrastructure on-farm and are critical to the economics of production.
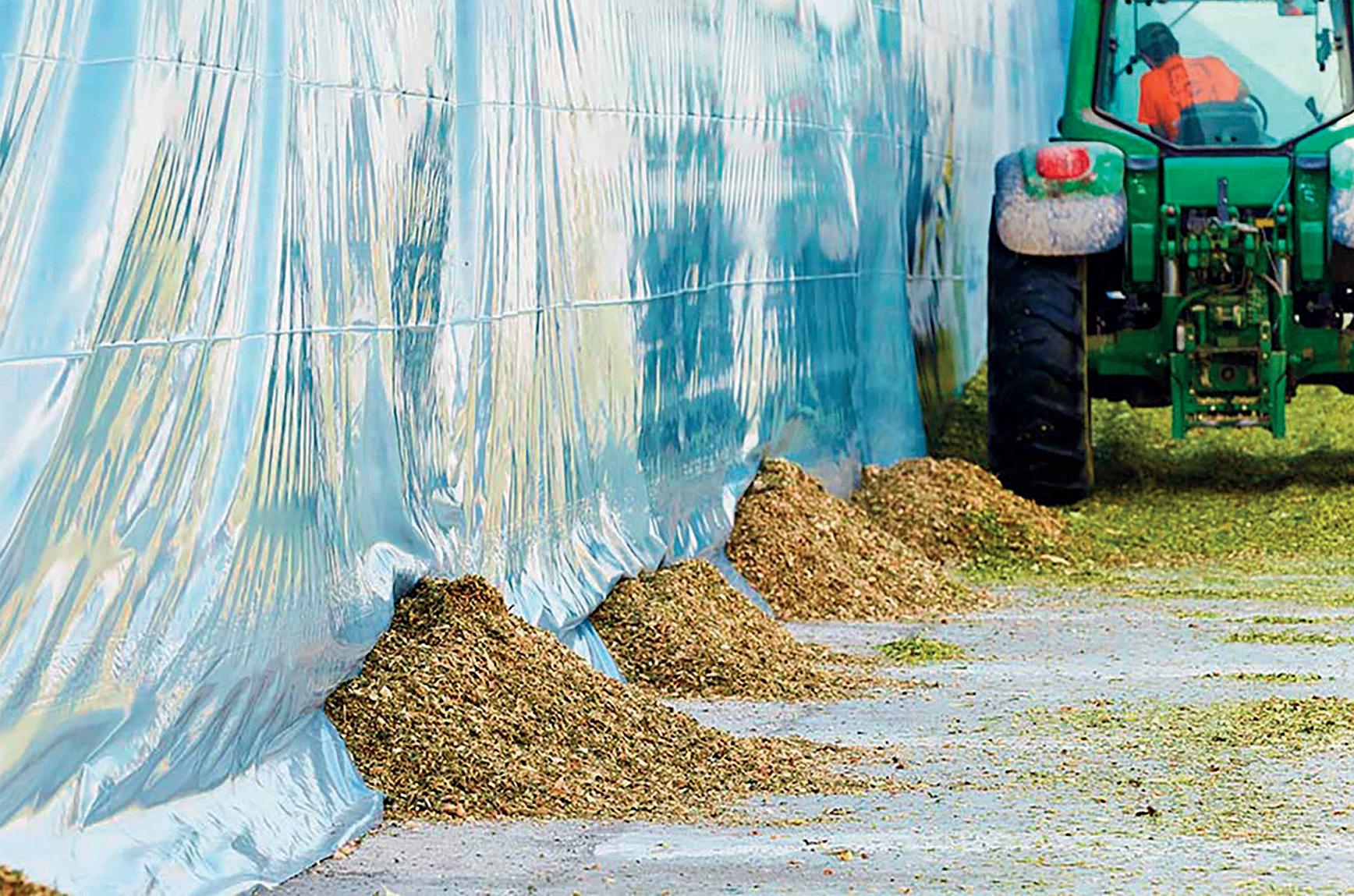
Investment
“ ey represent a longer term investment than bagged silage, but the return on investment is signi cant and quickly achieved, particularly when used with the newer technology lms which reduce plastic use signi cantly and improve forage quality.
“Add in the tax e ciency of using Capital Allowances for construction and Countryside Stewardship grants available for roo ng silage clamps and I think we are going to see construction of new clamps becoming increasingly popular in the future.”
Will Wilson says clamps are as important as any other piece of infrastructure and are critical to the economics of production.
