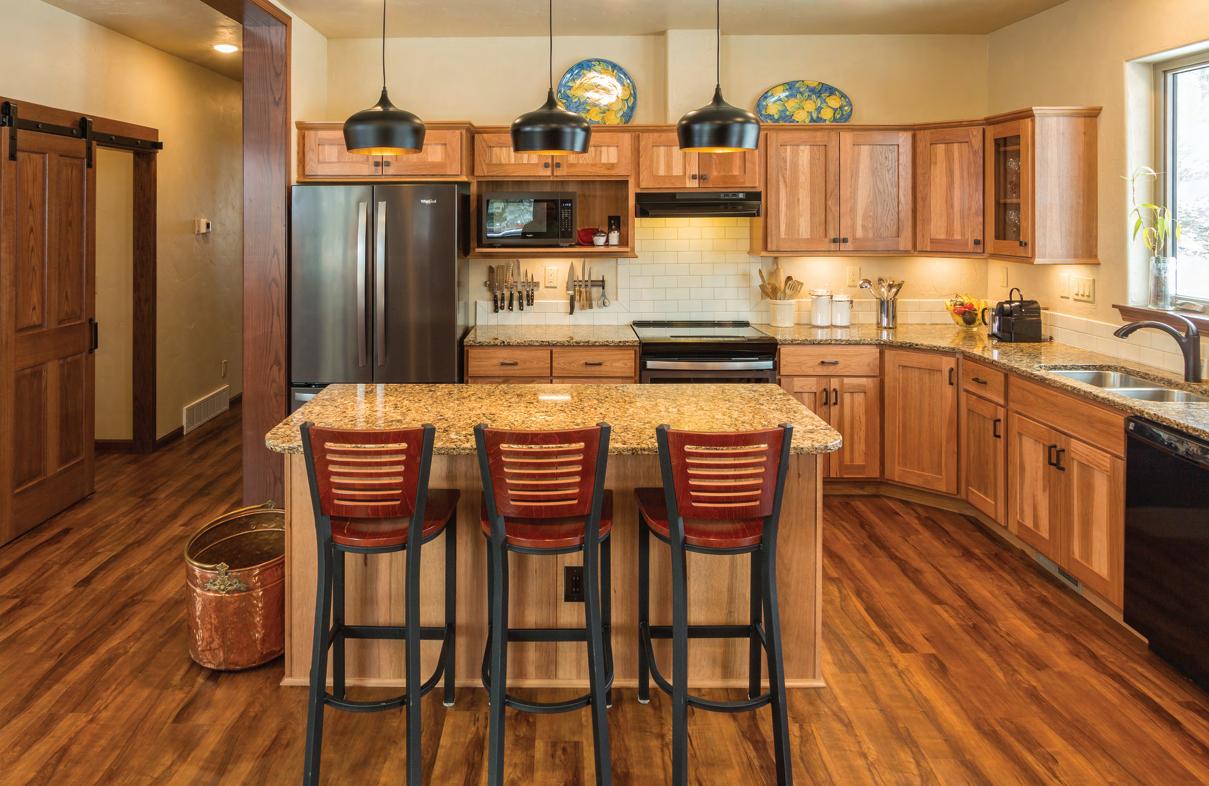
7 minute read
THE MAKING OF MODULAR HOMES

FAIR AND SQUARE CONSTRUCTION MODULAR HOME INTERIOR
Advertisement
SMARTPADS MODULAR HOME
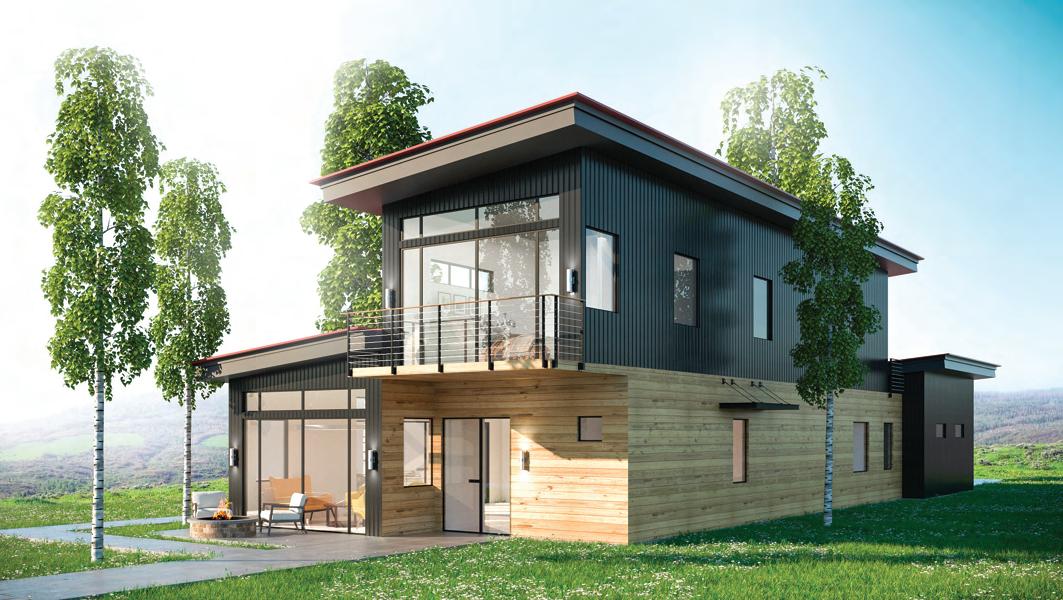
SYSTEM-BUILT MODULES REDUCE CHALLENGES OF LOCAL CONSTRUCTION
BY SUZIE ROMIG
Homebuyers in Routt County are increasingly interested in modular construction to save building time and money.
At the local Sustainable Home Tour in September, frequent comments from tour attendees were “which one is the modular?” and “I want to be sure to see the modular.”
With the tight local labor market, harsh winters that shorten the building season, and higher land and construction costs in an area popular with second home owners, homes built with systembuilt modular or hybrid modular construction are helping to reduce some of the challenges of residential construction.
“Construction will continue to move in this direction because there are too many benefits,” said Ron Davies, CEO of Fair & Square Construction in Steamboat Springs. “I think there is a growing interest because of the challenges with weather and labor resources here.”
“People are looking for ways to save money,” said Davies, who can operate a smaller crew to finish a modular home. “In the end, there is no difference between this modular and a fully sitebuilt home.”
With a degree in civil engineering and 26 years of construction experience in Routt County, Davies believes modular construction will become more of a norm except for the “ultracustom high-end homes” with complex designs
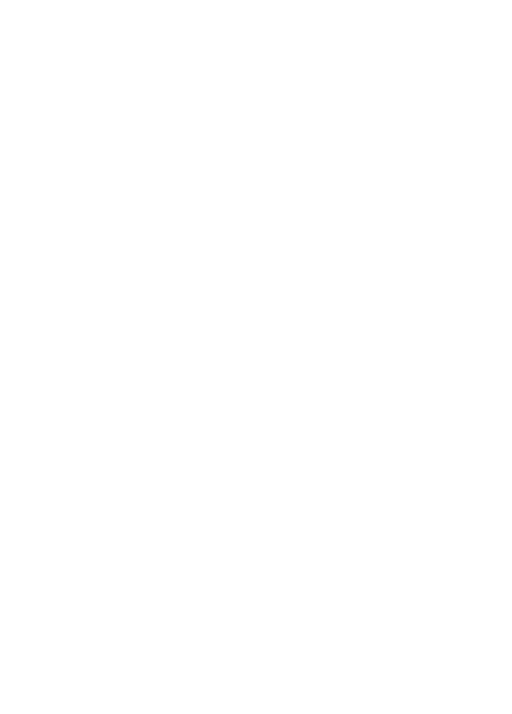
匀吀䔀䄀䴀䈀伀䄀吀 䄀刀䌀䠀䤀吀䔀䌀吀唀刀䄀䰀 䄀匀匀伀䌀䤀䄀吀䔀匀
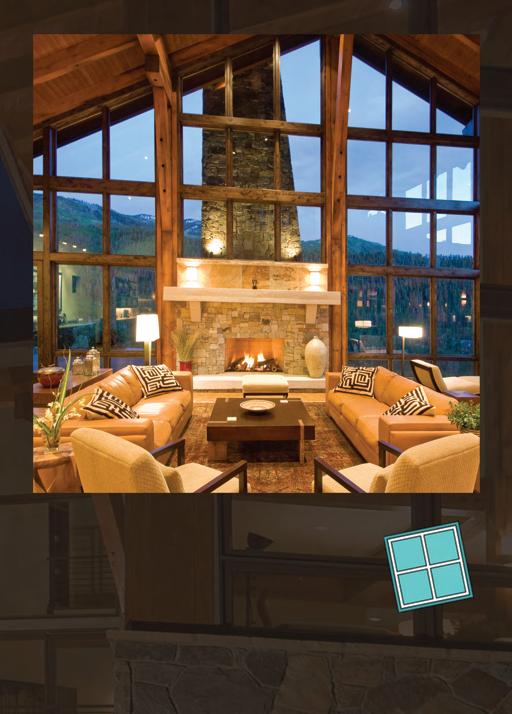
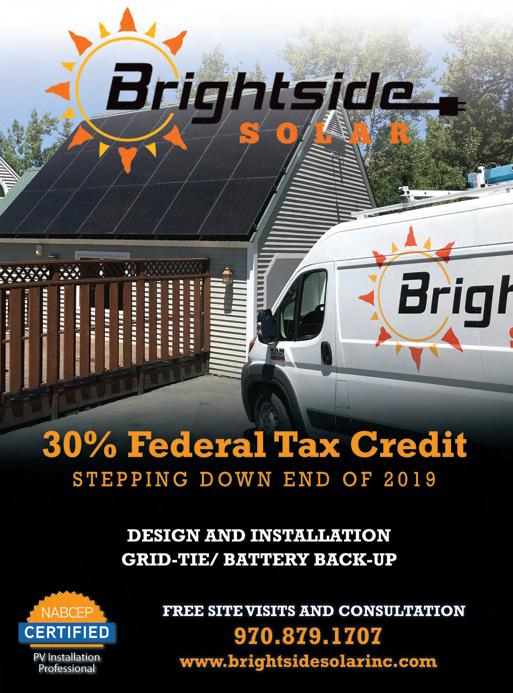
and large volume great rooms. Modular homes can be placed almost anywhere except very steep sites, he said.
The modules are built in climate-controlled factories that limit damage to materials from weather and water that can add to mold and durability concerns. The assembly-line process and simpler designs create some 50 percent less waste of construction materials. Modular homes have less cost overruns, can save 15 percent on hard costs with bulk purchased construction materials, and can cut construction time in half, Davies said.
Since 2010, Fair & Square (www.FairandSquare.org) has been an authorized representative for Heritage Homes of Nebraska that started in 1978 and serves an 11-state region in middle America. Fair & Square has used Heritage Homes modules for six homes in Steamboat Springs, Oak Creek, Rangley and Clark, including one for second home owners Bessie and Dimitri Zgourides.
“I went to Nebraska (to tour the factory) and was impressed with the quality of work and materials,” said Bessie Zgourides, an artist who has a background in architecture. “We were really happy with the end product.”
While the modules are being constructed in the Heritage factory – requiring about five weeks per module – a local crew can simultaneously construct the foundation or first floor. The standard modules arrive 80 to 85 percent complete, said Heritage Homes co-owner Jon Meyer, needing some final steps such as plumbing connections and floor tile grout.
Meyer said Heritage has sold more than 200 modular homes in Routt County since 2000, working previously with builder Dave Combs for a decade. Heritage has 14 authorized dealers in Colorado, has experienced 20 percent year-over-year sales growth since 2010 and records the highest concentration of sales in Summit, Clear Creek, Park, Chaffee, Grand, Routt and Eagle counties.
“We have had incredibly stable growth in Colorado since the bottom of the recession in 2010,” said Meyer, noting that 38 percent of Heritage business in 2018 was in Colorado.
The move by Heritage to more customizable modular layouts and finishes in 2002 contributed to sales growth. Modular homes help customers control costs of the livable space, which represents some 60 percent of the overall residential project costs, Meyer said.
Knowledgeable contractors can point out the wider 8-inch connecting wall that give off-site prefabricated home modules away, but house guests do not notice the difference. Homeowner Zgourides said when guests learn the top floor of her two-story home was built with two rectangular modular units transported 672 miles from Wayne, Neb., they turn their
heads inquisitively and ask “really?” or “where does it connect?”
The 2,580-square-foot home in Clark used a hybrid modular style with foundation and lower level built on site while the living room was pushed out and up on the second floor. Through this method, the shorter timeline saved significantly on construction loan costs that have a higher interest rate than mortgages. The garage, porch and patio were built on site after the modules were hoisted into place by a crane.
“Modular can be less stressful for the homeowner with less decisions,” said Davies, a sustainably focused builder. “We believe that people tend to build smaller with the modular system, not bigger.”
Downsizing retirees Donna and Joe Russo utilized Heritage and Fair & Square for their simple, well-built and energy efficient 1,500-square-foot, single-story home in Old Town Steamboat Springs that was completed in five months.
“I am really sold on the modular after living here a couple of months,” Donna Russo said, noting the home was warmer, tighter and “just as sturdy as can be.”
Davies said three of the modular homes that his company most recently completed earned a final Home Energy Rating System (HERS) score of 50 to 55 on the nationally recognized scoring system for measuring a home’s energy performance. This means the modular homes performed as well or better than completely site-built current homes the company has built.
Steamboat Springs-based SmartPads company (www. SmartPads.co), founded by local realtors Ryan Cox and Darrin Fryer, partner with Zip Kit Homes, a prefabricated modular home company headquartered in Idaho. SmartPads and Zip Kit collaborated to open a building facility in April 2018 in Vernal, Utah, that employs an eight-person construction crew. SmartPads works with local general contractors Drury Construction and Petra General Contractors to complete projects in Hayden and Steamboat Springs.
“There is a growing demand for a different approach to building,” Cox said. “Our goal is to bring affordable home solutions that are stylish, efficient and smart. Our homes are stick-framed just like most site-built homes.”
SmartPads got off to strong start with a 10-unit townhome development in Hayden with one-bedroom, one-bath units at 572 square feet listed for $168,000. Four of those small townhomes were set in November 2018, with six units to be set in April 2019.
The SmartPads homes range from 840-square-foot, twobedroom, two-bath single family homes in Leadville and Buena Vista to three single-family homes ranging from 1,900 to 2,855
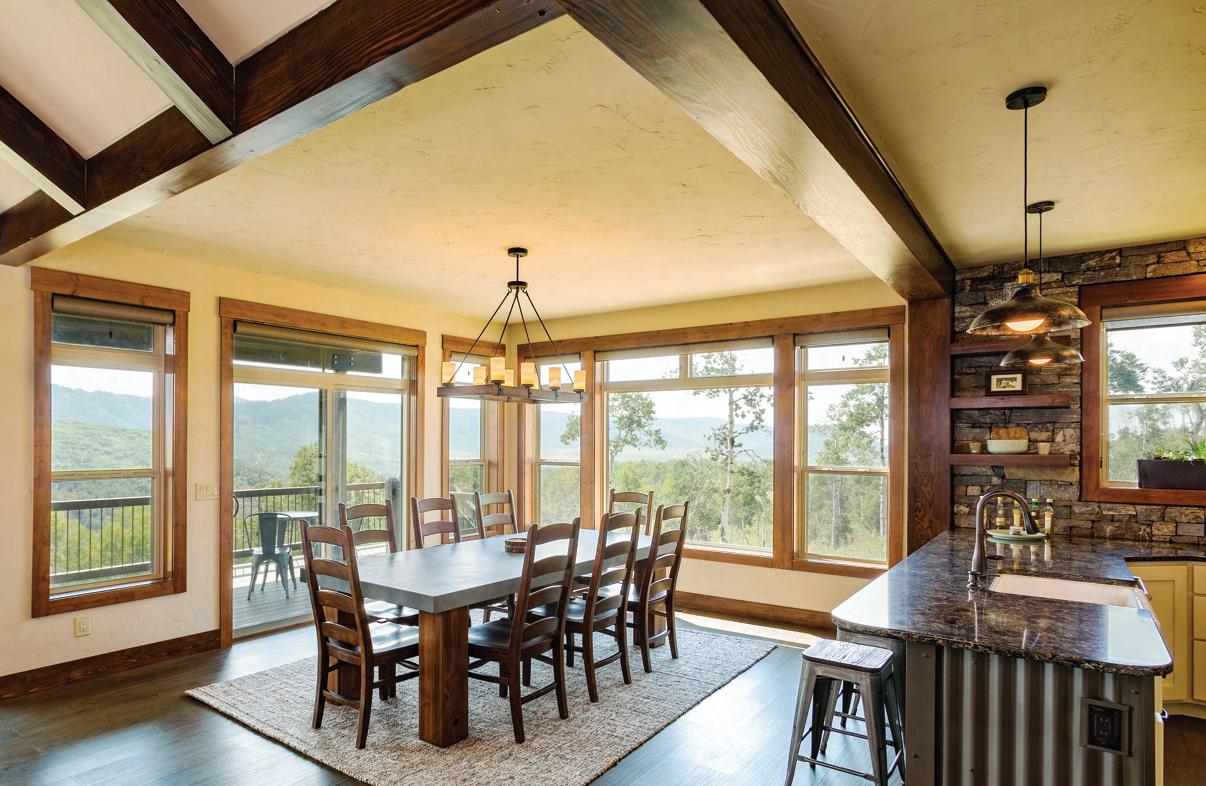
FAIR AND SQUARE CONSTRUCTION MODULAR HOME INTERIOR
FAIR AND SQUARE CONSTRUCTION MODULAR HOME
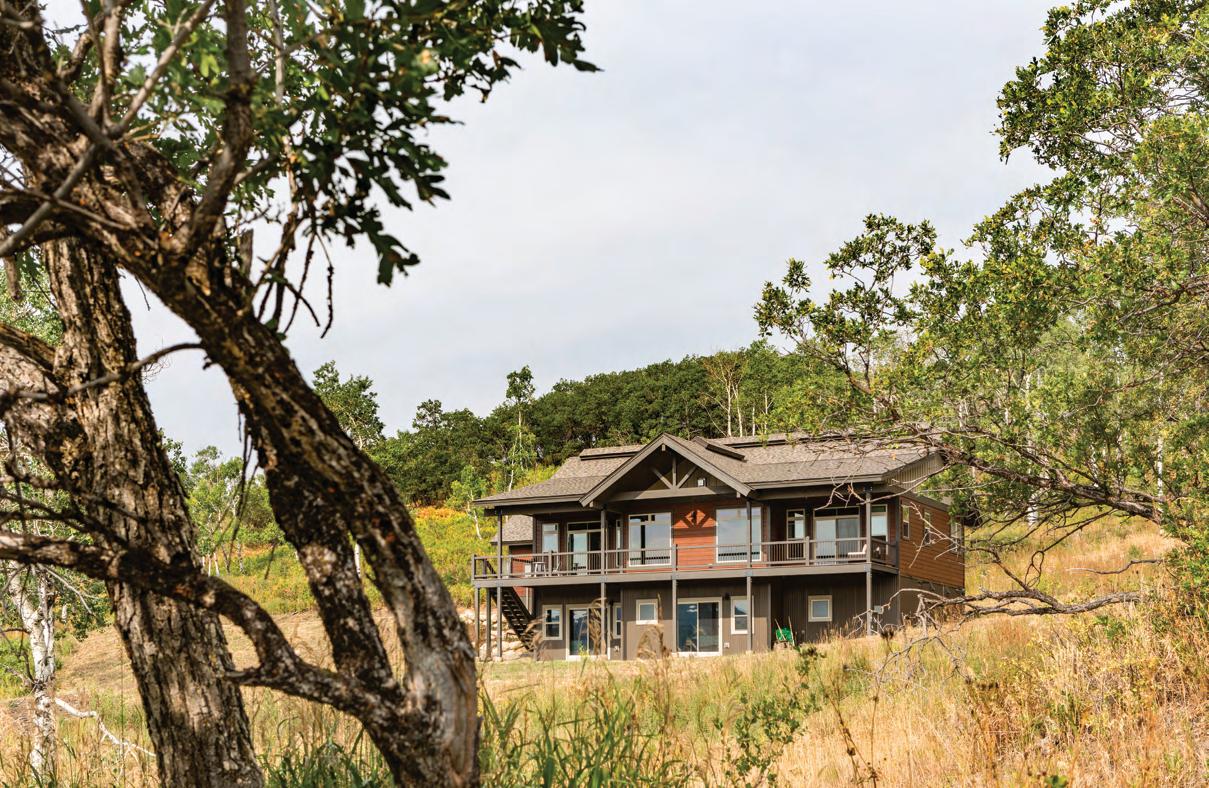
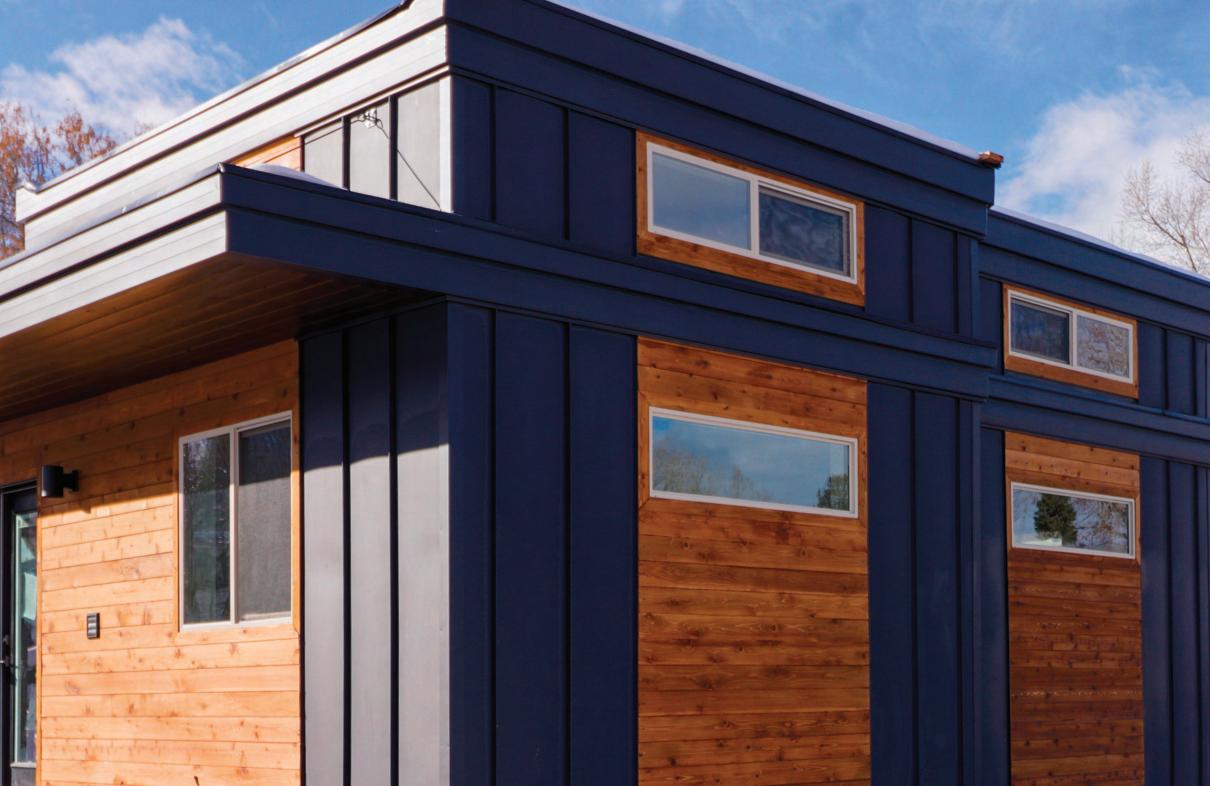
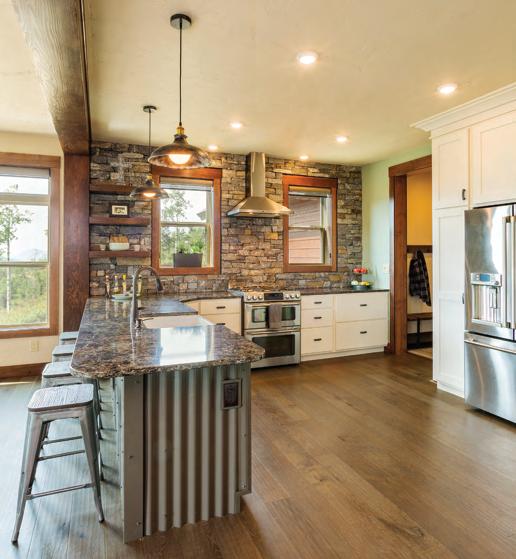
FAIR AND SQUARE CONSTRUCTION MODULAR HOME INTERIOR
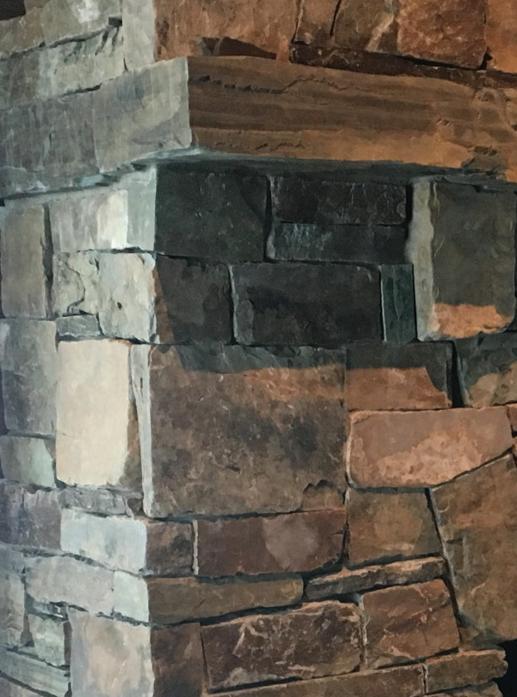
square feet in the new Sunlight Steamboat subdivision. Those homes in Sunlight are prefabrication homes or a hybrid product with a site-built lower level and prefabricated upper level.
Sunlight homebuyer Bonnie Glover said she chose SmartPads because it was “a simple and efficient process.”
Cox said if a customer purchases an existing design when SmartPads has open capacity, the product could be delivered on site in as quick as three months.
Modules can also reduce costs for commercial construction. Fair & Square completed a business building in Oak Creek that was 6,750 square feet with two stories above a basement. The two modular levels were 2,250 square feet each and were built from six modules. For the truck shipping, the maximum dimensions for the Heritage modules can be up to 17 feet wide, 66 feet long and 12 feet 10 inches tall.
Another use for modules is for simpler expansion projects at existing homes. Davies said Fair & Square is completing a modular addition on two homes in Milner and Clark, which can “cut disruption of construction on site in half.”
Modular home partners are all quick to point out that modules are built to current state and local building codes and are inspected at the factory and on site. The construction style is not to be confused with mobile homes found in trailer home parks that have steel frames, thinner walls, lesser insulation levels and follow federal HUD guidelines.
“We get several leads reaching out to us each week,” Cox noted. “Based on interest, we are confident that there is a demand for this type of product.”
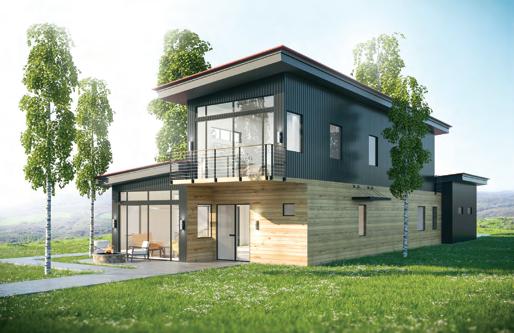

TRADITIONAL MASONRY FIREPLACES
209 RIVER RD, STEAMBOAT SPRINGS, COLORADO | 970-846-6535
3BD / 3.5BA • 2,150SF • $395K
stylish, modern, efficient prefab home solutions.
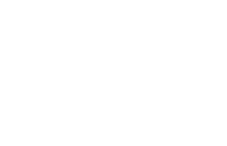
970-819-5359 www.SmartPads.co | ryan@smartpads.co