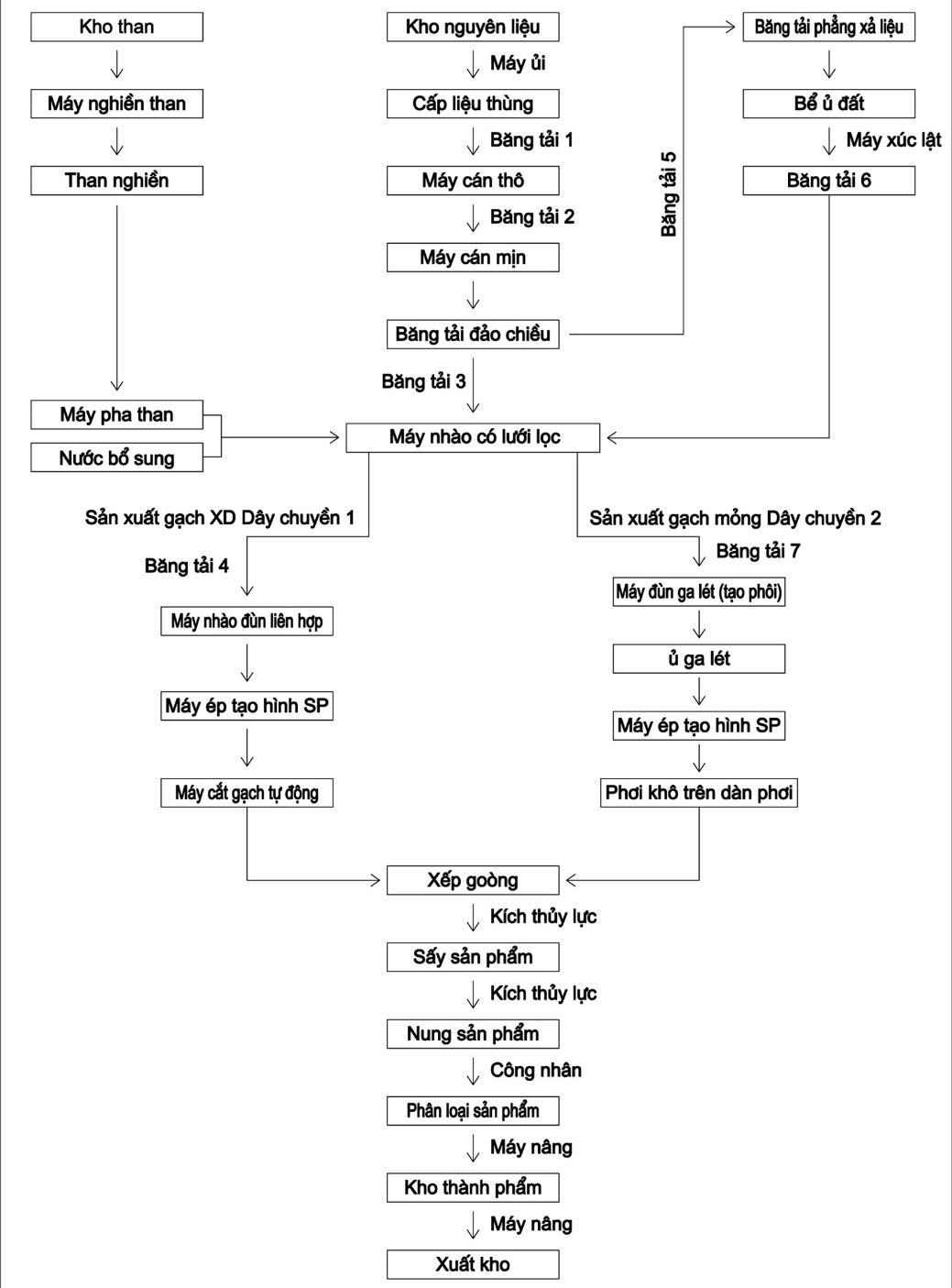
4 minute read
Hình 4.3: Sơ đồ công nghệ sản xuất
from Đánh giá hiện trạng môi trường nhà máy SX gạch nung Tuynel và đề xuất biện pháp giảm thiểu ô nhiễm
4.2.2. Sơ đồ quy trình công nghệ của nhà máy sản xuất gạch nung Tuynel tại huyện Đông Triều, tỉnh Quảng Ninh
4.2.2.1. Sơ đồ công nghệ sản xuất - Xuất sứ công nghệ sản xuất của dự án từ Châu Âu (Đức). Sản xuất theo kiểu lò nung theo công nghệ nung liên tục với buồng đốt cố định. - Công suất của nhà máy: 80 triệu viên QTC/năm. Sơ đồ công nghệ của dự án được mô tả theo hình dưới đây:
Advertisement
Hình 4.3: Sơ đồ công nghệ sản xuất
* Quy trình công nghệ của dự án Gia công nguyên liệu và tạo hình sản phẩm - Nguyên liệu tại kho ngoài trời sau khi đã phong hóa được ủi vào kho có mái che → đưa vào cấp liệu thùng, qua hệ thống cắt, thái được thái nhỏ và làm tơi → rơi xuống băng tải cao su lõm số 1 → máy cán thô, tại đây, đất được ép, phá vỡ cấu trúc ban đầu và được → băng tải cao su số 2 → máy cán mịn, với khe hở giữa hai quả cán 2mm, tại đây phối liệu được phá vỡ cấu trúc một lần nữa → đất từ băng tải đảo triều được đưa sang băng tải số 3 và băng tải số 5. - Đối với dây chuyền 1 (sản xuất gạch xây dựng): Đất từ băng tải số 3 → máy nhào trộn có lưới lọc, tại đây các tạp chất (cỏ, rác, sỏi, sạn) được giữ lại tại lưới lọc còn đất được đùn ra khỏi máy, mặt khác nước được cấp vào máy nhào lọc để điều chỉnh độ ẩm cho phù hợp (khoảng 22%). + Đồng thời than cám từ kho được nghiền mịn (cỡ hạt 0,8 mm) được máy pha than tự động rải đều xuống băng tải cấp vào máy nhào lọc để trộn với đất tạo thành phối liệu giảm tối đa nồng độ bụi gây ra, với lượng pha than khoảng 80-100kg/1000 viên gạch mộc tiêu chuẩn. + Sau khi ra khỏi máy nhào lọc, cấp liệu pha trộn → băng tải số 4 → máy nhào đùn liên hợp có hút chân không, sau khi qua hệ thống nhào trộn của máy, phối liệu được đưa vào buồng hút chân không, nhờ hệ thống bơm chân không, không khí được hút ra khỏi phối liệu, làm tăng độ đặc chắc của gạch mộc, tạo ra cường độ ban đầu nhất định, giúp quá trình vận chuyển đem phơi không bị biến dạng. Sau khi qua máy đùn ép hút chân không, nhờ khuôn tạo hình và máy cắt, các sản phẩm được tạo hình theo kích thước và hình dáng đã định. - Đối với dây chuyền 2 (sản xuất sản phẩm trang trí (gạch mỏng các loại)):
+ Đất từ băng tải đảo triều được đưa sang băng tải số 5 → băng tải xả liệu vào bể ủ (bể ủ có tác dụng ngâm ủ và làm tăng tính dẻo, đồng nhất hoàn toàn cơ tính của đất, giảm tối đa mức độ co ngót của sản phẩm trong quá trình nung đốt, nâng cao mỹ quan và chất lượng sản phẩm) → hố cấp liệu bằng máy xúc lật → băng tải số 6 → máy nhào lọc → máy đùn ép chân không → ủ ga lét → Máy ép tạo hình, nhờ khuôn tạo hình và máy cắt, các sản phẩm được tạo hình theo kích thước và hình dáng đã định → phơi khô sản phẩm trên dàn phơi. - Sản phẩm mộc sau tạo hình, phôi khô được công nhân xếp lên xe goòng theo tỷ lệ 70% là sản phẩm mỏng (gạch ốp, lát), 30% sản phẩm gạch xây dựng. *Sấy và nung sản phẩm: - Sản phẩm mộc sau khi được xếp lên goòng sẽ được đưa vào hầm sấy nhờ kích thủy lực đặt ở đầu hầm. Không khí lạnh dần được đốt nóng lên sau khi làm nguội sản phẩm và được chuyển sang vùng nung tham gia quá trình cháy. Không khí nóng được chuyển sang vùng đốt nóng sấy khô sản phẩm mộc và đốt nóng dần chúng lên trước khi chuyển sang vùng nung. Vật liệu được nung di chuyển đi qua lò, nhiệt độ của nó thay đổi phù hợp với biểu đồ nung đất sét tạo gốm silicat. Đặc tính này thuận lợi cho kiểm sát chế độ nung, năng suất chất lượng tốt. Khói lò được thải ra ngòai qua ống khói nhờ quạt hút. Sự tuần hòan của khí thải cho phép tạo ra chế độ nhiệt và chế độ ẩm dịu hơn, làm cho nhiệt độ đồng đều trên tiết diện lò, giảm tác động có hại của không khí lạnh lọt vào. - Nhiên liệu sử dụng cho lò là bột than. Bột than được tra từ nóc lò xuống và cháy trong nhiệt độ có sẵn trong lò (800÷1.050oC), là môi trường đốt cháy hết nhiên liệu.