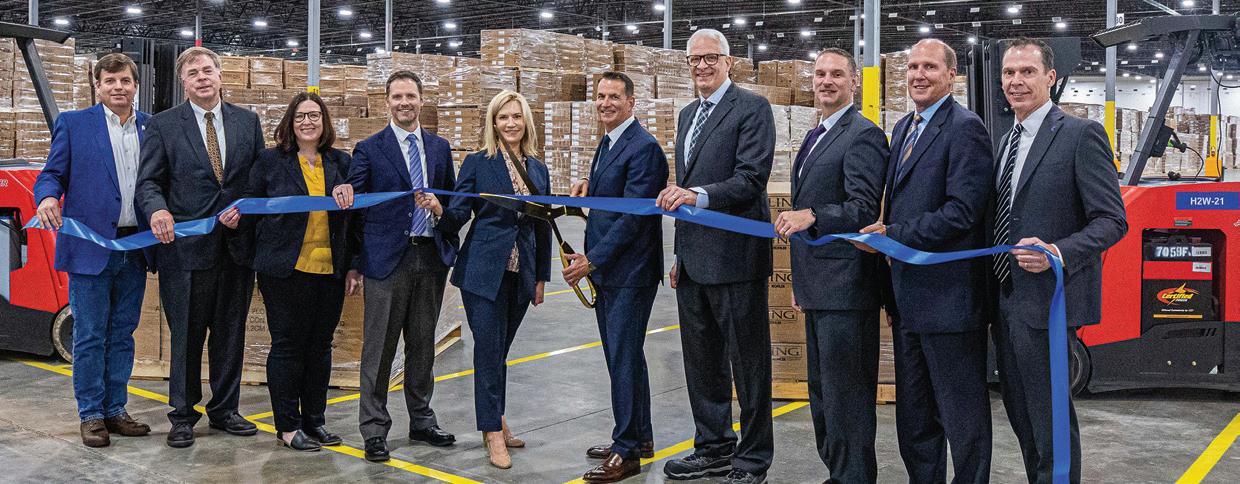
11 minute read
By Mike Easterling
from HBJ 2022 Issue
Kohler Company Adds New Warehouse to Huntsville Facilties
By Mike Easterling / Photos courtesy of Kohler Company
Advertisement
The city of Kohler in America’s Dairyland – Wisconsin – is known for its cheese and beer. But in the city of Kohler, it’s also home to a well-known name in kitchen and bath products. And golf.
Kohler Co., founded in 1873 in its namesake city in the Badger State, is owner/operator of two five-star hospitality and golf resort destinations in Kohler and golf’s birthplace at St. Andrews, Scotland.
Kohler’s Whistling Straits golf course hosted the 43rd Ryder Cup in 2021.
But Kohler’s calling card is the local company’s products that line shelves worldwide. Tuesday, May 10, it expanded its footprint in the Tennessee Valley.
A ribbon-cutting ceremony was held to celebrate the completion of what Kohler billed as a “state-of-theart’’ warehouse in Huntsville that will house STERLING Vikrell bath and shower fixtures.
The building was erected near Kohler’s existing manufacturing plant off Wall Triana Highway at 176 Cochran Road, which according to Kohler produces STERLING Vikrell products that are popular among the nation’s top single-family homebuilders, home improvement retailers, and a vast number of multi-family developers, plumbers, and remodelers.
“In the past, our business has been constrained by a lack of warehouse storage, which challenged us in providing the level of consistent quick delivery our customers expect,” said Norb Schmidt, senior vice president-Kitchen & Bath Operations.
“The new warehouse and enhanced stocking strategy will greatly reduce lead times and improve delivery efficiency. We are pleased to expand our presence in Huntsville and Madison County and contribute to the local economy.’’
The warehouse totals 546,000 square feet.
The ribbon-cutting ceremony included Kohler Co. CEO David Kohler, and Senior Vice President-HR, Stewardship & Sustainability Laura Kohler. Also present were Kohler associates, representatives of design-build contractor Burns & McDonnell and local officials including mayors Tommy Battle of Huntsville and Paul Finley of Madson along with Madison County Commission Chairman Dale Strong.
In a press release, Kohler said it has more than 50 manufacturing locations worldwide. The company is a global leader in the design, innovation and manufacture of kitchen and bath products; luxury cabinetry, tile and lighting; engines, generators and clean energy solutions.
The company also develops solutions to address pressing issues, such as clean water and sanitation, for underserved communities around the world to enhance the quality of life for current and future generations. For more details, visit kohlercompany.com. w

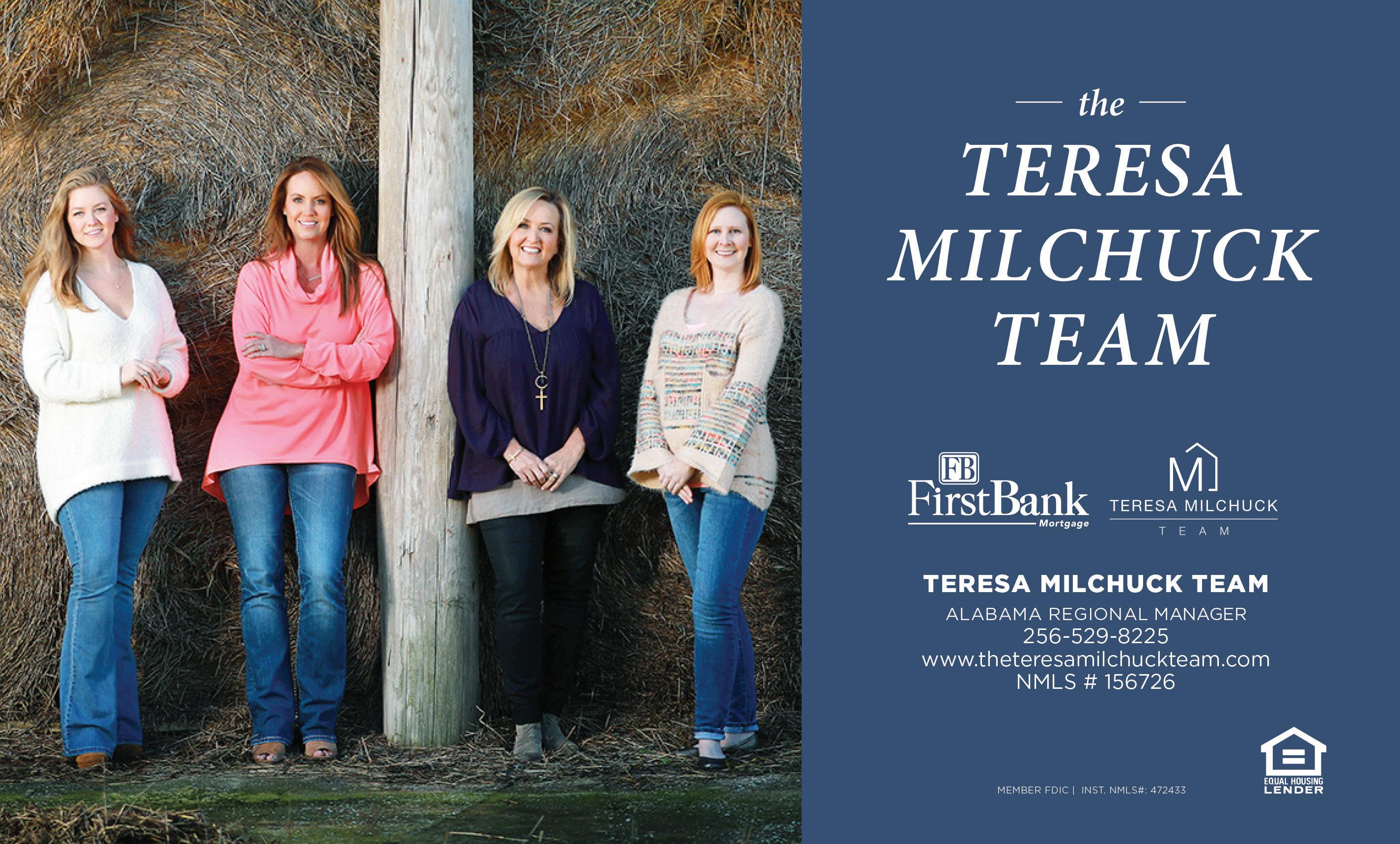
Blue Origin’s Overhaul of Historic NASA Test Stand Presented Challenge
By Mike Easterling / Photos courtesy of NASA/Blue Origin
Longtime city residents will recognize the thundering sounds and the shaking of area structures when NASA’s historic 4670 Test Stand at Marshall Space Flight Center is once again ready to play a key role in the country’s space exploration.
The 300-foot tall stand, first employed in 1965 to support the Apollo program’s Saturn V rocket and later in service for the Space Shuttle and RD-180 Atlas rockets into the coming decades, has been inactive since 1998.
But 4670 will once again roar to life when Blue Origin, Jeff Bezos’s space rocket venture, completes a refurbishment project of the stand through a deal with NASA.
Boosters have been tested at MSFC as America gets ready to return to the Moon and beyond. But the rockets that will do the heavy lifting – BE-3U and BE-4 – have yet to be fired at 4670.
David Helderman, a Purdue University alum and aerospace engineer, is director of Alabama Test Operations for Blue Origin and leads the Test Stand 4670 Project. He said the BE-3U and BE-4 engines, which will support both Blue Origin’s New Glenn and United Launch Alliance’s Vulcan space flight vehicles, are on schedule for testing later this year.
“The Saturn V was a seven-and-ahalf million pounds of thrust that was tested on the test stand, so that definitely shook windows and everything a long distance away,’’ Helderman said. “Then in the eighties, the space shuttle main engines and RD-180 were an order of magnitude much more powerful.
“So that’s kind of what people often remember from the ’80s and ’90s. When we get into testing the BE-4 we’ll be at five hundred-and-fiftythousand pounds of thrust. So it’ll be loud and people will hear it, but it won’t be near as loud as the Saturn V was back in the 60s.’’
Bob Smith, president of Blue Origin, previously promised the company would “provide for the refurbishment, restoration and modernization of this piece of American history – and bring the sounds of rocket engines firing back to Huntsville.’’ Getting the stand back into shape is no small task. “The challenge that we’ve had is just dealing with the age of the test stand,’’ Helderman said. “Some parts of the test stand haven’t aged as well as others. We found some corroded steel and things like that that we’ve had to go into in-depth evaluation and then the re-
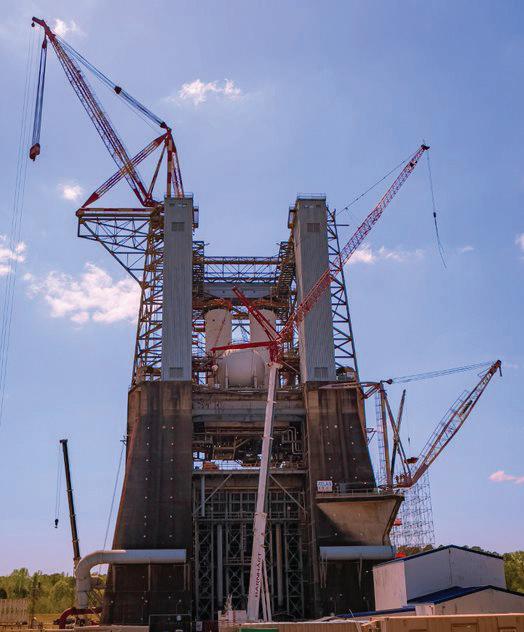
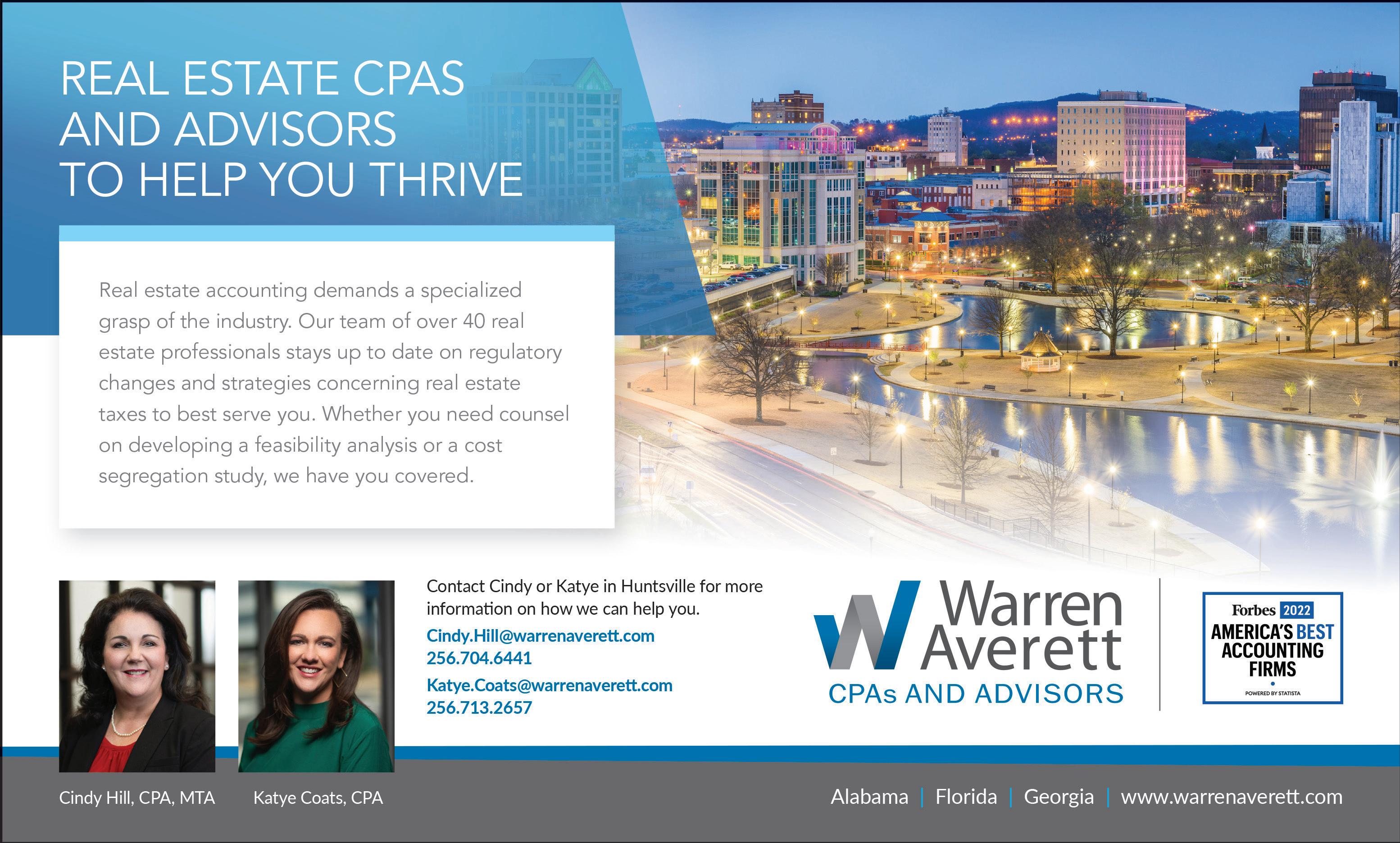
pair or replacing in some cases some of those corroded steel members and things like that.
“So by and large our biggest challenge was just dealing with the age of the test stand and bringing it up to current standards and modernizing it.’’ According to Helderman, the 4670 team has embraced the history of the test stand since the start of the project. “One of the coolest things about this whole project is the history,’’ he said. “We love that we’re building our history on history. It’s a cool, long history of America’s Space Program. “I can tell you that the team out here, we love the history that goes with a test. And one of the big attractions for people to come work out here is being able to be a part of that history and carry on that legacy.’’ The BE-4 is the engine that engineers and explorers envision taking men, and women, to an eventual trip to the Red Planet and more.
“This is the rocket that’s going to enable our vision of millions of people living and working in space,’’ Helderman said. “That’s kind of the building block. It’s the first step of that situation that allows us to get a lot of things into space.
“It’ll allow us to build a space station like an orbital reef and will allow us to put people back on the moon. It will enable many many things beyond that fundamentally. It’s the heavy lift vehicle that’s going to allow us to put all sorts of things in space, which will open up space to generations to come and many things we haven’t even thought of yet.’’
Helderman wouldn’t hesitate to live in space, or on Mars.
“If I had the chance I would definitely go into space and I would I would live in pretty much anywhere in space as long as it was habitable,’’ he said. w
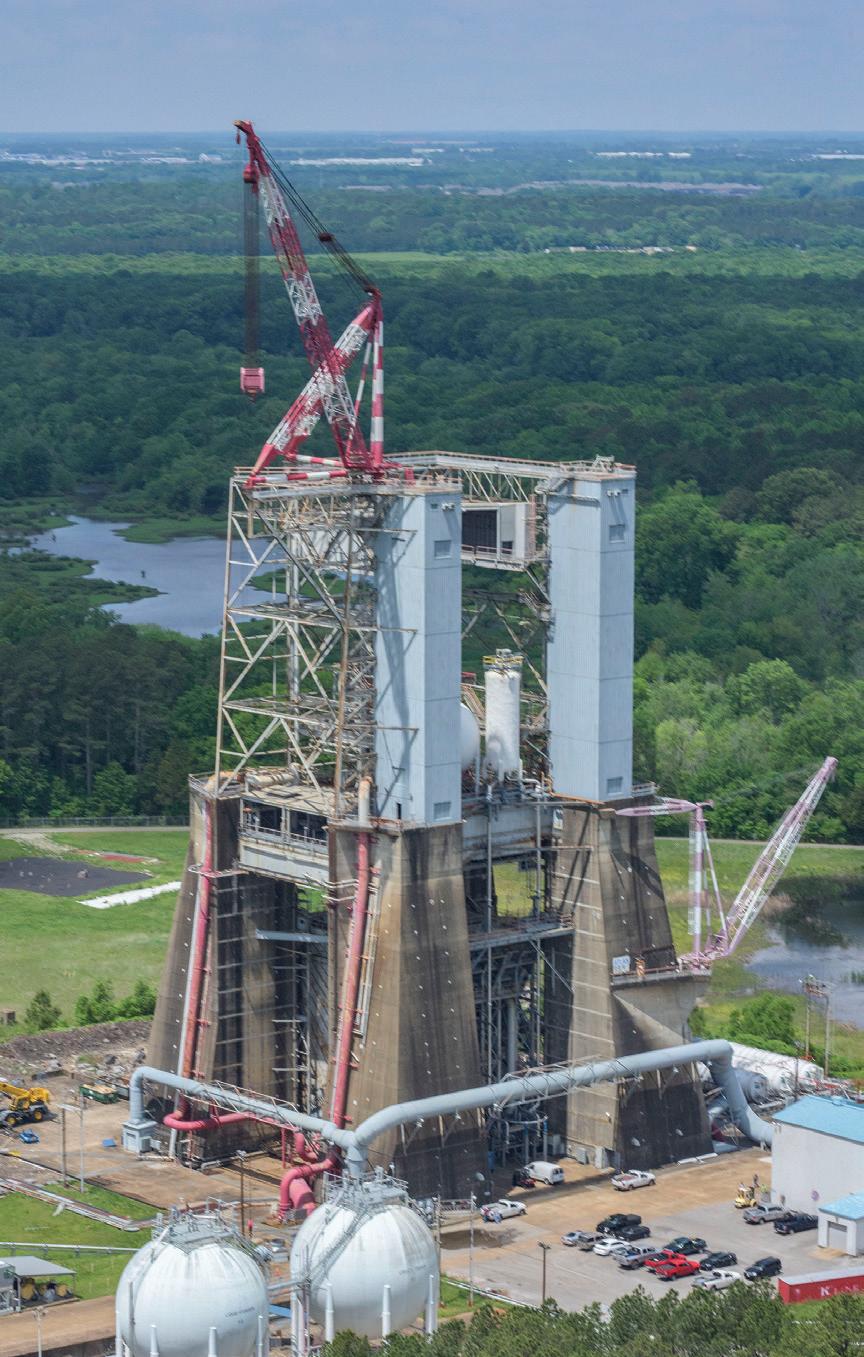


Third Time’s the Charm: Boeing Starliner Heads to ISS
After two failed previous attempts, Boeing’s CST-100 Starliner spacecraft successfully entered orbit on Thursday night after separating from the United Launch Alliance (ULA) Atlas V rocket.
An excited crowd gathered in the U.S. Space & Rocket Center’s exhibition hall for the viewing event. Prior to the countdown, guests explored the USSRC’s newest exhibit, “Planet Pioneers,” before settling in to watch the launch.
Robert La Branche, Special Assistant to the Chief Executive Officer of the USSRC, acted as emcee for the event. During his remarks, La Branche noted that the OFT-2 marks the 675th launch of the ULA Atlas rocket and the 375th to launch from Cape Canaveral.
As the Atlas rocket lifted off, the Huntsville audience erupted in loud cheers, followed by another with the Solid Rocket Booster (SRB) separation milestone. Although two of Starliner’s thrusters didn’t fire as expected during the spacecraft’s orbital insertion burn and a backup failed after 25 seconds, redundancy failsafes kicked in, allowing Starliner to complete the crucial burn without incident.
The Starliner Orbital Flight Test-2 (OFT-2) is the second uncrewed flight of the Starliner that will demonstrate the spacecraft’s human transportation capabilities. This test flight is the last major step before the Atlas V and Boeing’s Starliner capsule take American astronauts to the International Space Station (ISS) as part of NASA’s Commercial Crew Program.
Built in Decatur, the Atlas V Starliner configuration was modified specifically for the Boeing CST-100 Starliner spacecraft and does not include a standard payload fairing. Instead, the Starliner’s insulated surfaces take the place of the fairing to protect the uncrewed spacecraft during ascent.
While this mission is uncrewed, it does contain a special passenger: “Rosie the Rocketeer,” Boeing’s first anthropometric test device. During OFT-1, Rosie was outfitted with 15 sensors to collect data on what astronauts will experience during crewed flights on Starliner.
For OFT-2, spacecraft data ports previously connected to Rosie’s 15 body sensors will be used to collect data from sensors placed along the seat pallet, or the infrastructure that holds all crew seats in place. This test run will enable Starliner to maintain a proper center of gravity during ascent, docking, undocking, and landing.
The Starliner spacecraft is scheduled to dock to the ISS at 6:10 a.m. CST on Friday, May 20. The crew of Expedition 67 will open Starliner’s hatch about 10:45 a.m. on Saturday, May 21. Starliner is scheduled to depart the Space Station on Wednesday, May 25 and will land in the desert in the western U.S.
Starliner carries with it over 500 lbs. of NASA cargo and crew supplies and will return to Earth with nearly 600 lbs. of cargo, including reusable Nitrogen Oxygen Recharge System (NORS) tanks that provide breathable air to station crew members. The tanks will be refurbished and returned to the station on a future flight.
“I am so proud of the NASA, Boeing, and United Launch Alliance teams who have worked so hard to see Starliner on its way to the International Space Station,” said NASA administrator Bill Nelson. “Through adversity, our teams have continued to innovate for the benefit of our nation and all of humanity. I look forward to a successful end-to-end test of the Starliner spacecraft, which will enable missions with astronauts aboard.” w
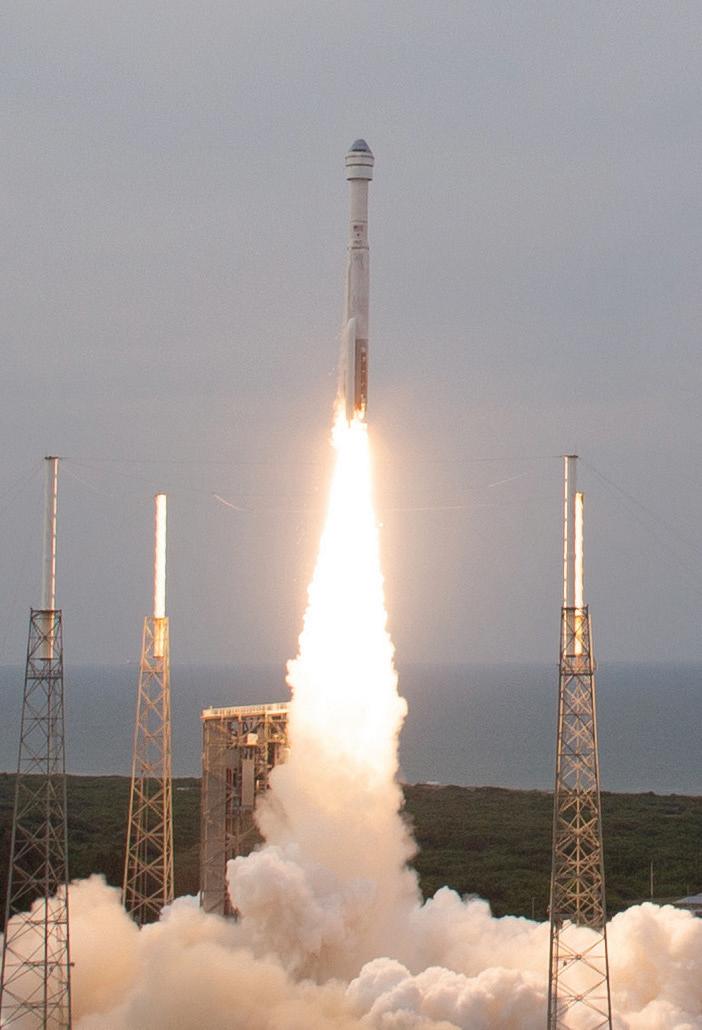
By Dawn Suiter / Photos courtesy of NASA/Joel Kowsky
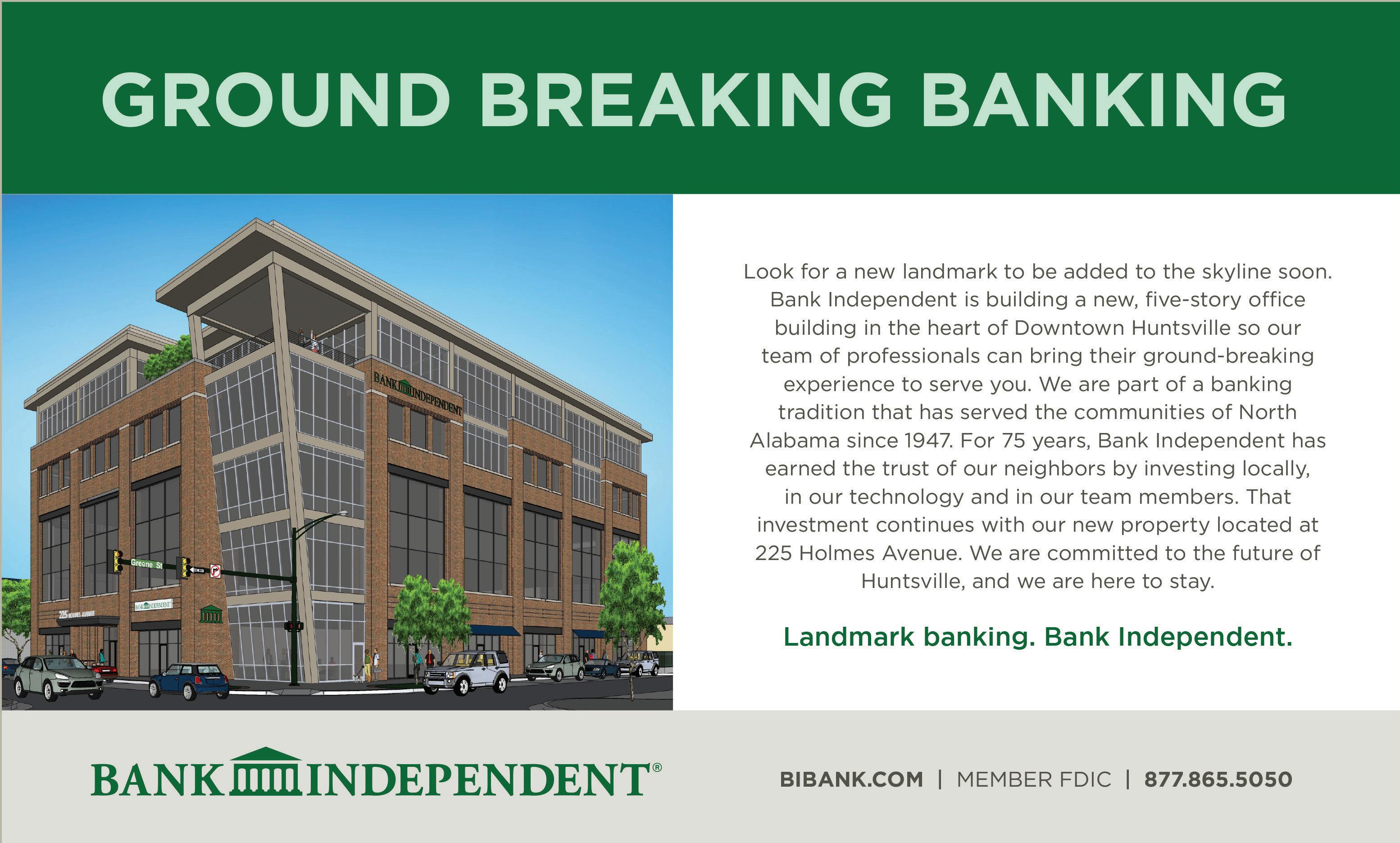
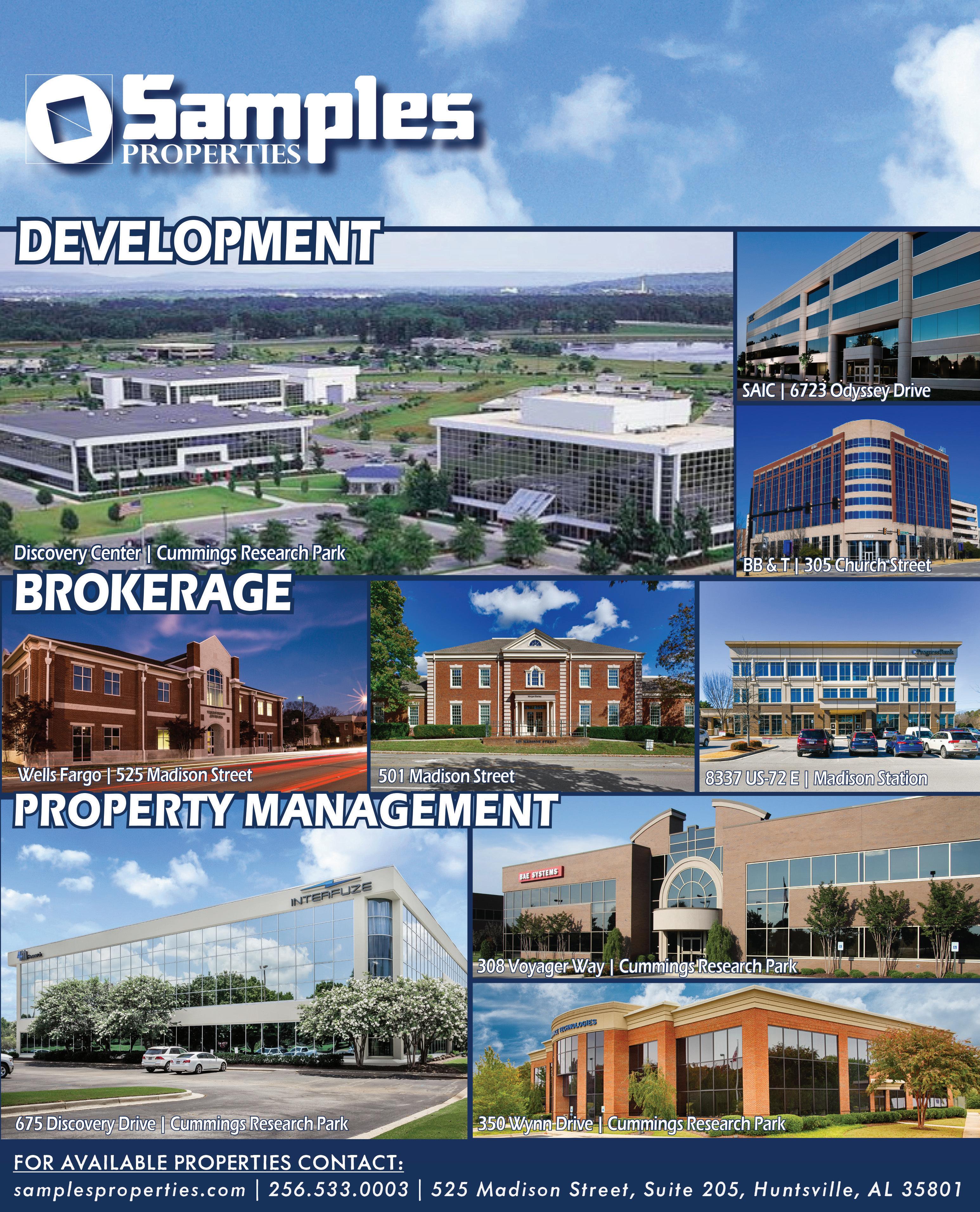
Huntsville Based Aerobotix Reaches 40th Installation for Missile Manufacturers with More to Come
By Noah Logan
The Huntsville based robotic solutions and metrology company Aerobotix reached a significant landmark in its service to the missile manufacturing industry. On May 18, the company installed its 40th robotic system for the United States Defense Department.
Over the course of recent months, Aerobotix has delivered robotic systems to support surge production at several missile manufacturing sites for various defense contractors. These robotic systems are supporting interceptor, cruise, air-to-air and hypersonic missile production on multiple levels.
“Automation is often the smartest strategy when defense contractors really need to increase production,” said Ricky Schwartz, Principal Engineer at Aerobotix. “Contractors are realizing it’s time to ‘tech up.’ That’s why we’ve now installed 40 robotic systems for U.S. missile manufacturing and are already on our way to No. 50.”
His prediction to reach their 50th instillation could come sooner than expected given the increase in federal spending towards missile defense. The Missile Defense Agency (MDA) is seeking $9.6 billion in 2023 to expand defenses against increasingly complex missile threats.
The MDA requested $8.9 billion in 2022, but received an additional $1.5 billion from Congress for a total of $10.4 billion. Congress has now increased funding for the MDA for two years in a row, arguing that the agency hasn’t requested sufficient funds for it to meet the requirements of the National Defense Strategy. Industrial-grade robots integrated by Aerobotix are capable of providing more than 10 years of operation, or 60,000 hours, before major failure. This level of durability ensures contractors a strong return on investment and gives investors confidence that they can answer the call for more product. Aerobotix robots also remove human workers from dangerous or difficult manufacturing environments, making the work environments safer.
Aerobotix is actively working with these defense contractors to identify missile manufacturing processes that are best suited to the automation their installations provide.
“Recent demand has focused around the automation of testing, scanning and quality operations,” explained Schwartz. “We’re able to transform these manual – and sometimes even subjective – inspections into fully-automated processes that just crank out products. Our robots can perform a perfect inspection every time and record the data so that the customer then has a digital twin of the missile.” w

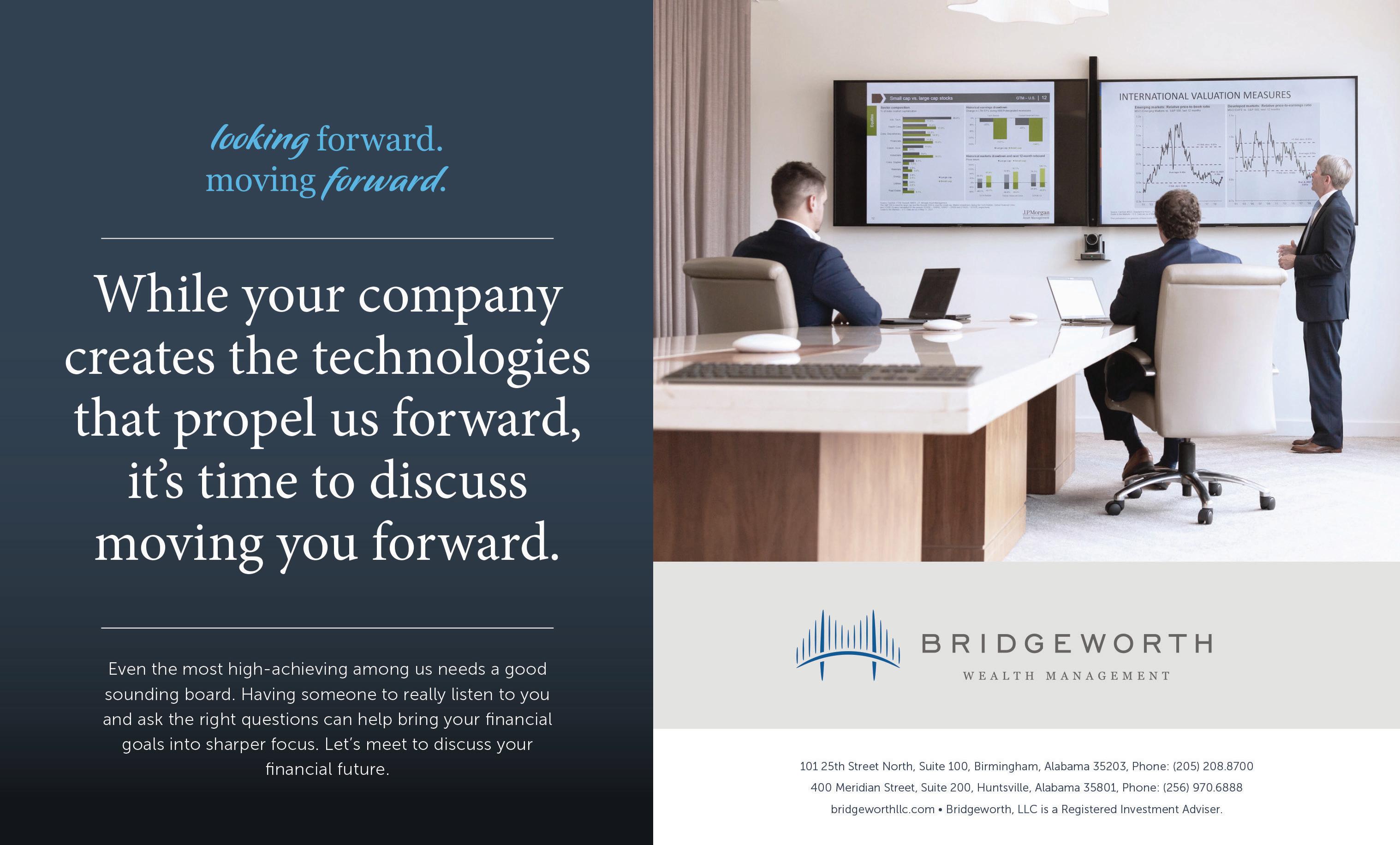