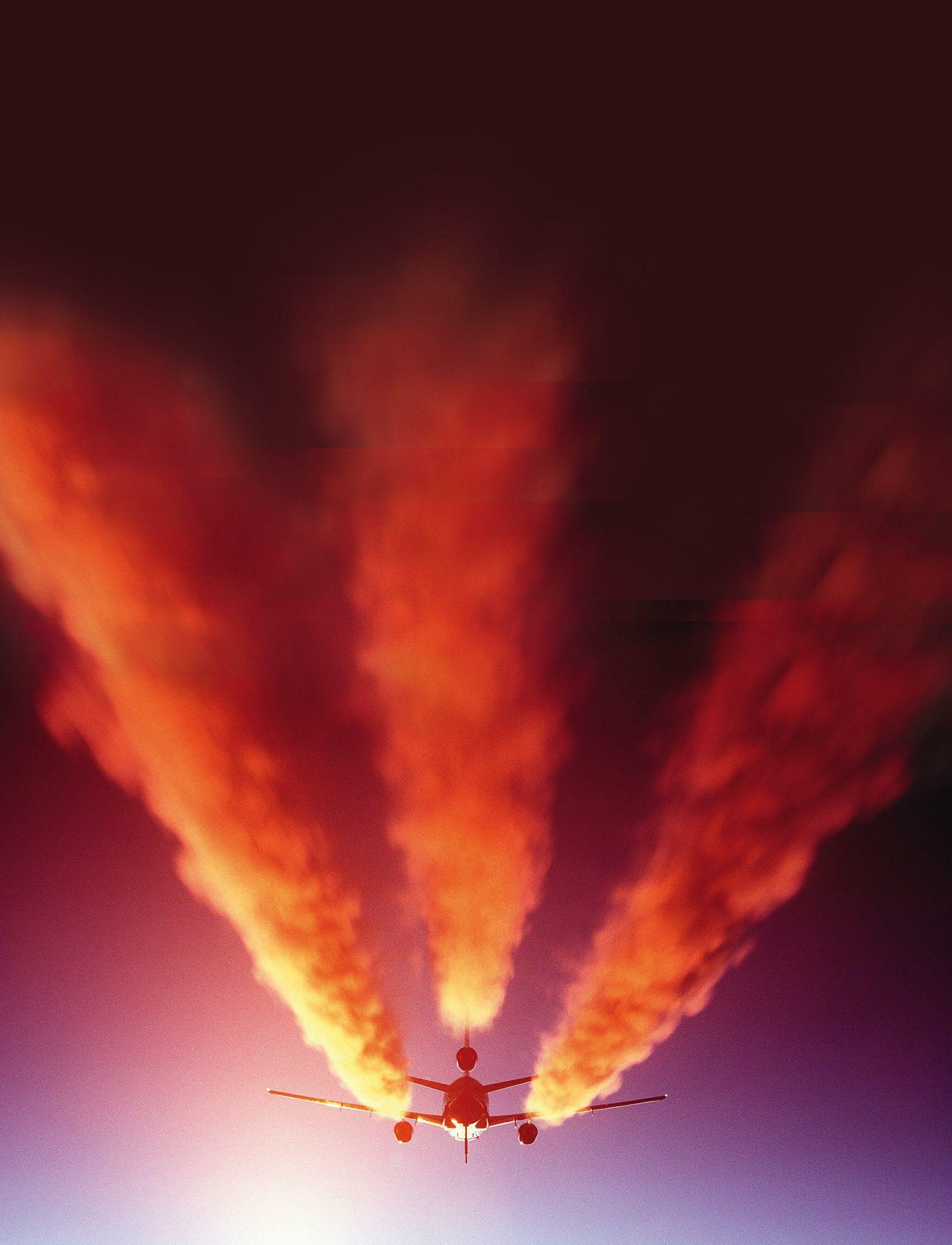
9 minute read
X-Plane Aviation
The Next Generation of Green Planes is About to Take Off
The aviation industry is a major contributor of the pollutants responsible for climate change. There is now a high demand to focus on innovative aircraft designs that would not only cut emissions dramatically but would create more efficient and quieter airplanes for us to fly in. This is why NASA is now leading the way to ‘greener’ designs, by funding an exciting new range of X-Plane projects
Let’s start with the problem. Look up, almost anywhere in the world and sooner or later you’ll see long sunlit contrails diffusing out into the sky. The emissions from an airplane will carry in them a cocktail of carbon dioxide, hydrocarbons, carbon monoxide, water vapour, nitrogen oxides, sulphur oxides and black carbon – all of which have an impact on the atmosphere.
Air travel has been a very successful growth industry, so emissions have escalated on a tremendous scale. In the EU countries alone, gas emissions from aviation ramped up by 87% from 1990 to 2006.
In 2015, worldwide, a total of 781 million tonnes of C02 was produced from flights alone, not surprising perhaps, when 8.3 million people fly every day. What’s more, civil aviation consumes more than 5 million barrels of oil per day. This is therefore a major commercial sector that’s causing significant environmental pollution and is impacting on natural resources – but let’s face it, we are not prepared to give up air travel any time soon. In fact, air travel is predicted to double in size within the next 10-15 years. So what can be done?
Luckily, the problem is on the radars of key stakeholders. Everything from light weight composite materials, improvements for better propulsion systems and techniques for reducing noise have become the subjects of research by academics and companies working together to make aviation cleaner and greener.
NASA invests in X-planes
NASA, in particular, is working on creating new experimental aircraft and technology that will dramatically reduce fuel consumption, emissions and noise too. The overarching aim is to cut emissions by more than 50 percent and reduce noise levels to half of the current level of the quietest aircraft currently in operation.
NASA has launched the New Aviation Horizons programme – which is a 10-year accelerated research plan. Part of this is to
investigate new design concepts, which has led to the organisation investing its substantial budget into six month long contracts, handed out to four companies that can contribute, each tasked to work out the technical details, cost and approach of making new super-efficient, subsonic *‘X-Plane’ designs based around green objectives.
Those four companies are now engaging in work that is rewriting the script on plane designs, which in turn could herald a new era of air travel.
So, what are these new plane concepts that could reduce emissions and transform the industry?
Not just flights of fancy
Here’s an insight into each new conceptual design, currently on the drawing board:
• The Aurora D8 ‘Double Bubble’ – By Aurora Flight Sciences Corporation of Manassas, VA.
With an investment from NASA totalling $2.9 million, the D8 is a twin hulled aircraft, proposed by Aurora Flight Services and Massachusetts Institute of Technology (MIT). In 2015, the US Federal Aviation Administration (FAA) also contributed funding for the D8’s Lower Energy, Emissions and Noise Program.
Aurora has been a pioneering company in manufacturing and innovative technology in the aerospace industry for nearly 30 years and the D8 is a conceptual commercial aircraft that is tantalising the sector with possibilities for future changes in airliner design.
Aurora claims to have ‘rethought and reconfigured every part of the air vehicle to maximise efficiency and minimise operating costs as well as improve passenger experience’. There is an expectation that it could go into service by 2027.
The design is a departure from the traditional way of putting a plane together. Instead of making the plane a composite of thousands of parts, with a traditional tube and wing design, it will have one integrated system and a ‘double bubble’ fuselage with twin lobes and aisles within them, with small wings and jet engines mounted on the top near the tail.
As the jets are mounted at the rear, thrust requirements are less than usual from something known as Boundary Layer Ingestion (BLI) – which increases propulsive efficiency. Tests in the wind tunnel for the D8 suggest 15% fuel savings just for having the engines embedded in the aft of the fuselage.
The radical integrated design means that there is more lift which reduces drag, resulting in less fuel required for flight.
It’s proposed that the D8 configuration could achieve a 71% reduction in fuel burn, a 60 EPNdB reduction in noise, and an 87% reduction in LTO NOx – all relative to a best-in-class Boeing 737-800 narrow-body aircraft. This aircraft would typically fly at speeds estimated at 582mph / 936kmph.
Analytical tests have been conducted by the team that have verified the design benefits. Next up in the panning, is to conduct flight research using a demonstrator that can simulate accurate flight conditions.
• Blended Wing Body (BWB) – Dzyne Technologies Incorporated of Fairfax, VA.
There is a similar focus on the aforementioned lift to drag ration design advantage here, this time geared toward a smaller aircraft than the D8. The wing and body act as one component – seamlessly joined together with an improved aerodynamic shape to traditional aircraft, thus reducing drag and increasing lift. There will be no clear dividing line between the body and the wings. This plane design will not look conventional – it has a sciencefiction feel to it – like all those planes you see on movies about the future. Interestingly – BWB has usually been seen to be a design that suits larger planes and is not so suited for smaller jets but Dyzne’s design has changed this stance.
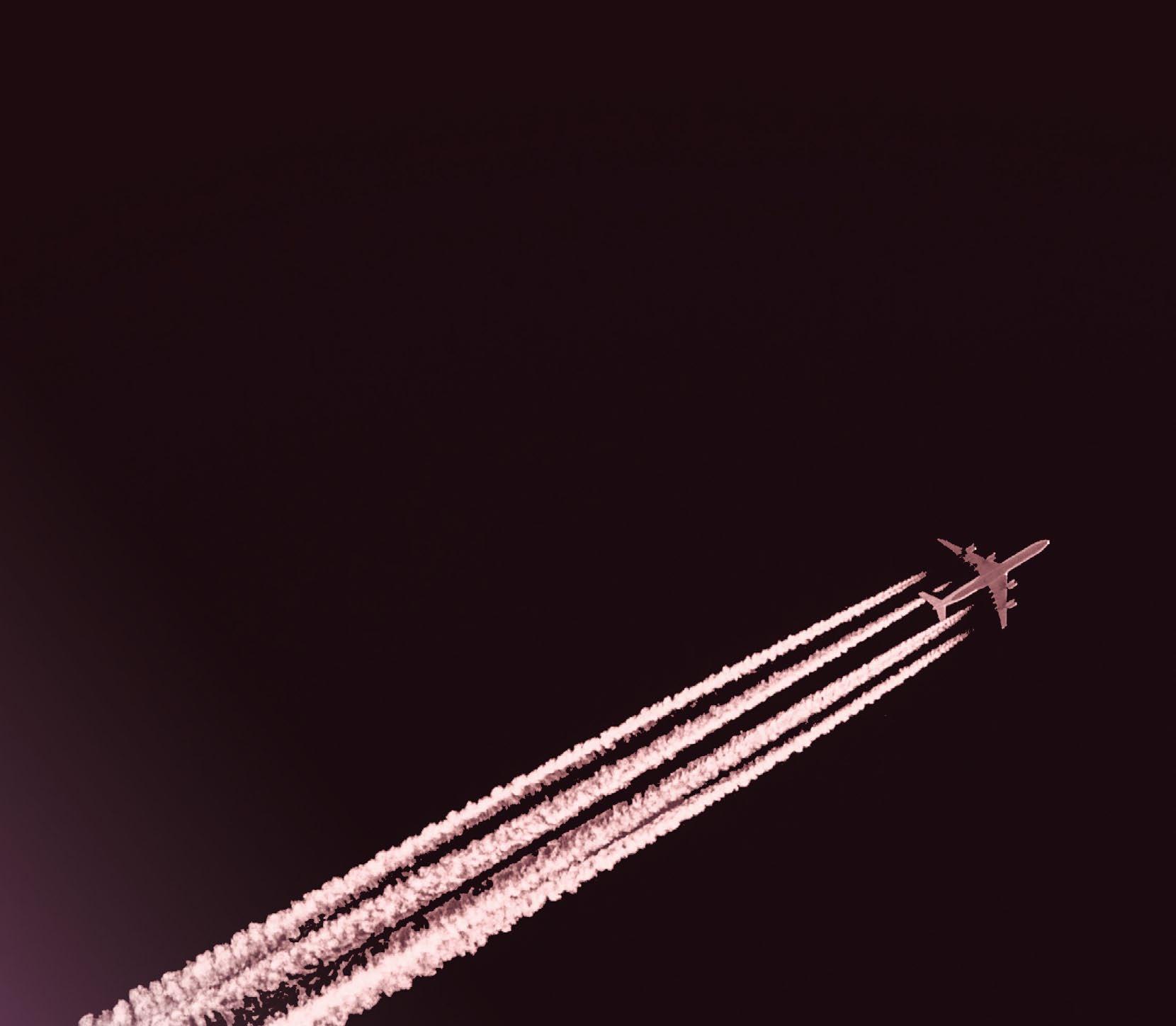
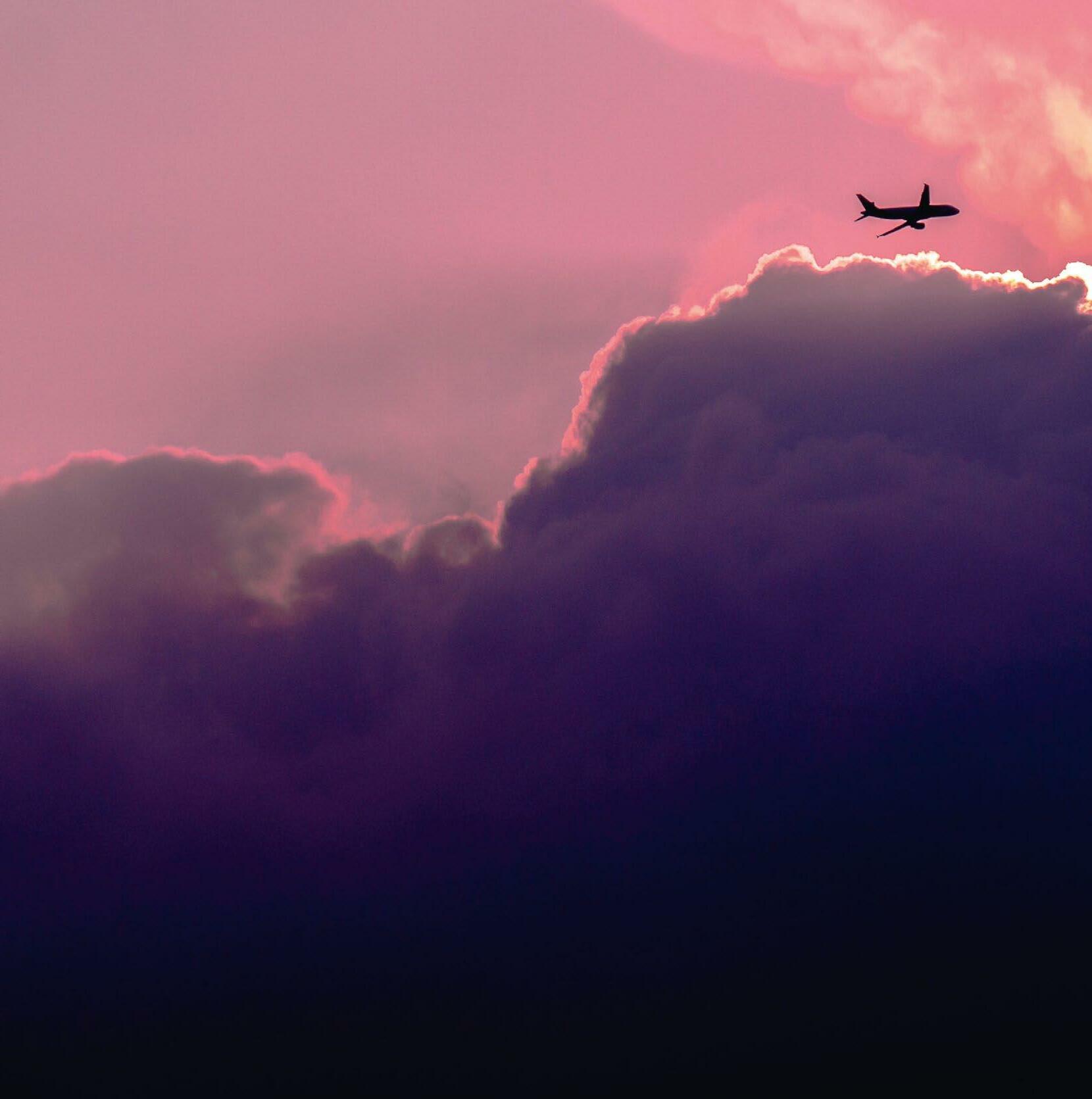

Dyzne is looking at the potential for a lightweight material called Prseus composites technology for the structure of the plane. The plane design (we’re talking about a 110-130 seater regional plane) has a single deck, centralised body with thin wings. The landing gear is stored outwards (not under the cabin) and the cargo and baggage is held in the wing roots. The way the plane is put together will create a 20% saving on fuel burn.
• Hybrid Wing Body (HWB) – Lockheed Martin Aeronautics Company of Ft. Worth, TX.
The design for this Hybrid Wing Body concept will be capable of carrying the same cargo as the giant Lockheed C5 plane with the advantage of burning 70% less fuel. Over-wing nacelles make it possible to install large, fuel efficient very-high bypass engines – which prove 5% more aerodynamically efficient than underwing engines. The overall design is a little more conventional than that proposed by Dzyne – more T shaped in the tail.
The hybrid wing body would have a combination of blended wing and fore-body which would be a benefit for aerodynamic efficiency but it would have a conventional aft fuselage as well as the tail, in order to be compatible with standard cargohandling equipment. This design should have a bright future as a basis for a commercial plane and it could also be used in the military for airlifts.

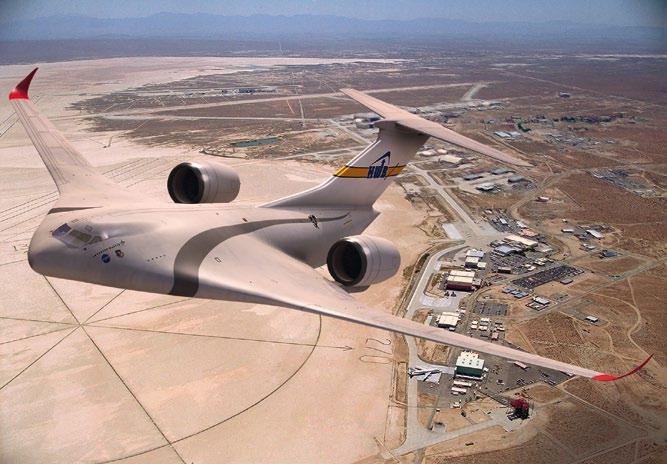
• Blended Wing Body (BWB) & Truss-Braced Wing Concept – The Boeing Company of Hazelwood, MO.
There are two concepts that Boeing is looking into. Firstly, Boeing’s very own BWB design – some versions of which have already been flight tested. The other is a Truss-Braced Wing concept. This is a long wing that performs very aerodynamically – the wing is held up by trusses connected to the fuselage. To look at this, it is perhaps the most conventional looking of the X-Plane concepts presented here.
The plane has a wing not unlike a glider’s in appearance that spans a lengthy 170 ft (as opposed to the norm of 118ft) and is attached to the tubular fuselage. Wind tunnel tests have been promising according to NASA. This design can reduce fuel burn by up to 10% compared against traditional 180 seat narrow body airliners.
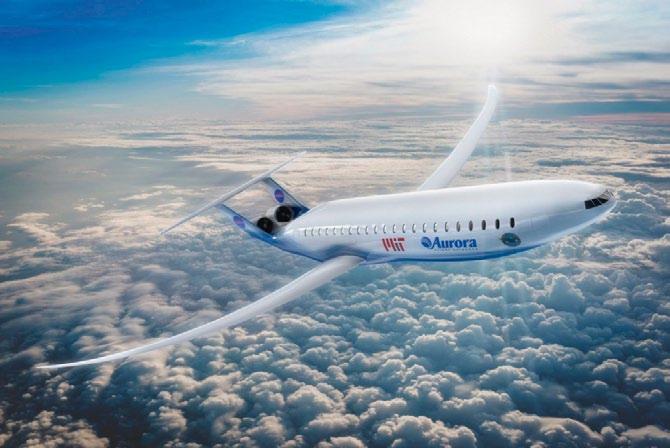
From design to reality
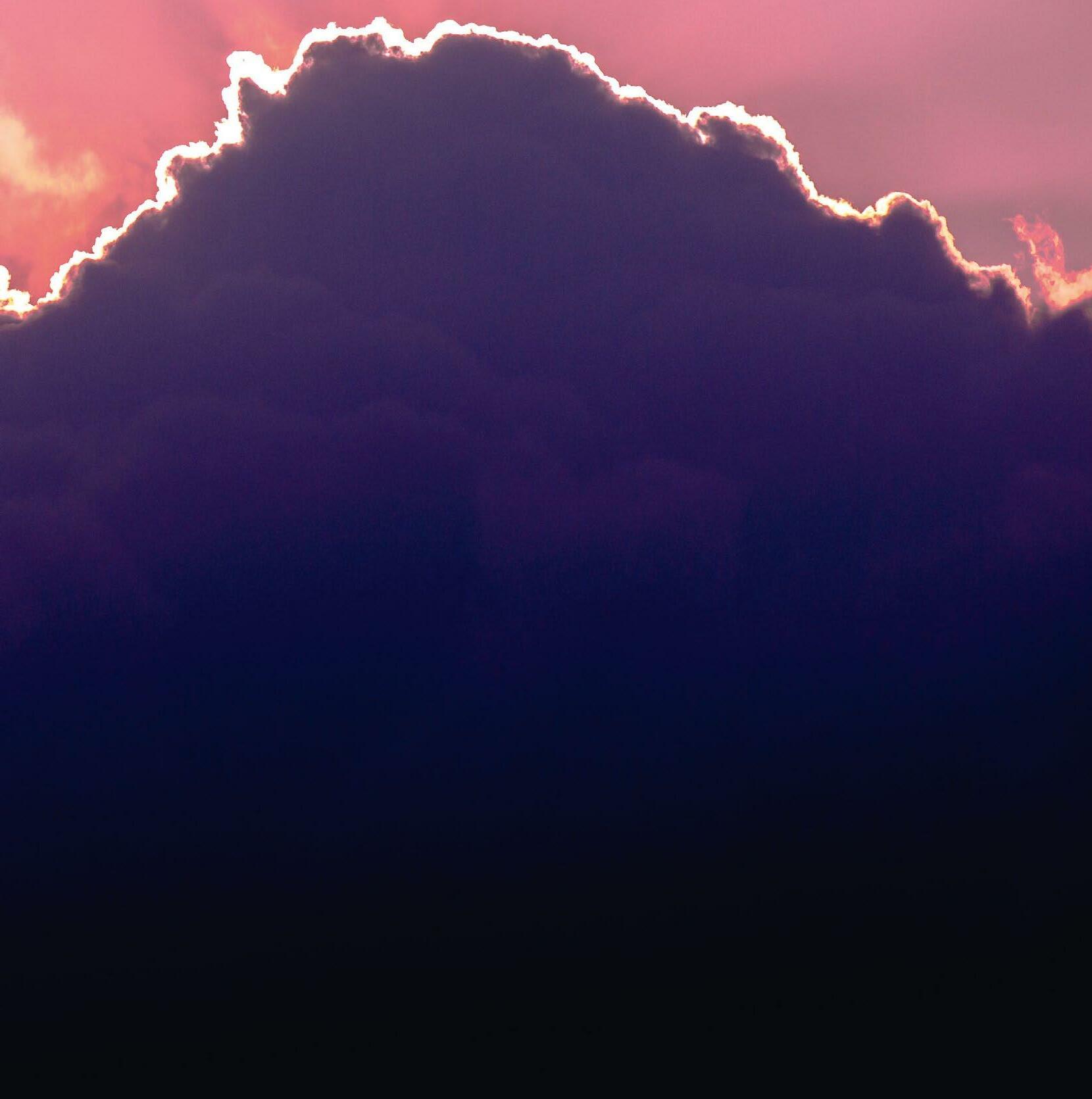
The challenge for each of these company’s research teams is to come up with a detailed technical plan demonstrating how to pilot one of these planes for up to two to three hours in subsonic flight.
Ed Waggoner, NASA’s Integrated Aviation Systems Program Director, explained in a statement: “Engaging these contractors now to gather this information will help us move forward efficiently and expeditiously when we’re ready to commit to building the X-planes themselves.”
In as little as five years’ time from now, the first experimental aircraft could be built from the research that is currently taking place in facilities around the US, into how these X-Planes would behave.
It’s highly likely we may see versions of these kinds planes in our skies in the future and they would make our current airliners look dated by comparison. There will be so many benefits from using them, from less noise pollution, more comfort, less costs for carriers but most of all it is essential that the industry acts on cutting emissions and burning less fuel. We are now at the beginning of a new age for aviation. * X-Planes is a term for a class of experimental aerospace plane model that requires research.
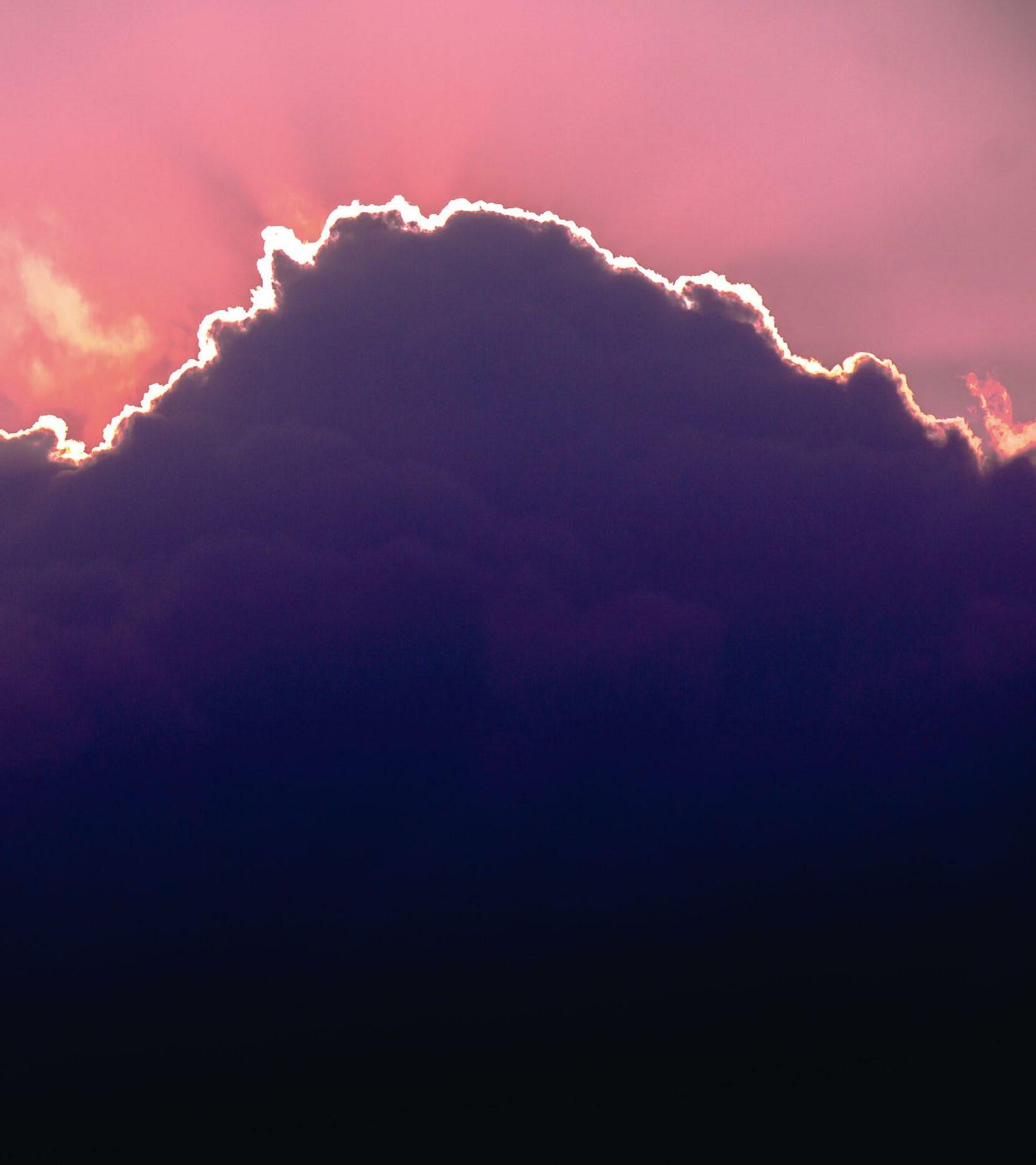
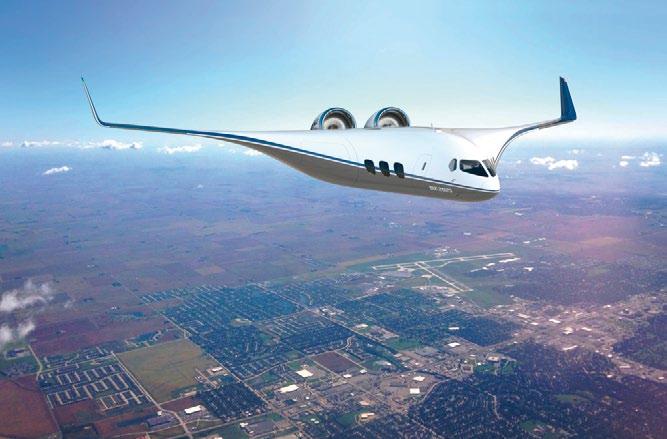
New Measures Agreed in International Aviation for Emissions Reduction
On 6 October 2016 in Montreal, Canada, at the 39th meeting of the International Civil Aviation Organisation, a total of 191 countries came together to reach a landmark agreement, to take measures to alleviate global climate change, by reducing emissions from the aviation industry.
More specifically, Government, industry and civil society representatives have agreed on a new global market-based measure (GMBM) to control CO2 emissions from international aviation.
“It has taken a great deal of effort and understanding to reach this stage, and I want to applaud the spirit of consensus and compromise demonstrated by our Member States, industry and civil society,” said ICAO Council President Dr. Olumuyiwa Benard Aliu. “We now have practical agreement and consensus on this issue backed by a large number of States who will voluntarily participate in the GMBM – and from its outset. This will permit the CORSIA to serve as a positive and sustainable contributor to global greenhouse gas emissions reduction.”
ICAO’s Carbon Offsetting and Reduction Scheme for International Aviation (CORSIA) is designed to complement the basket of mitigation measures the air transport community is already pursuing to reduce CO2emissions from international aviation. These include technical and operational improvements and advances in the production and use of sustainable alternative fuels for aviation.
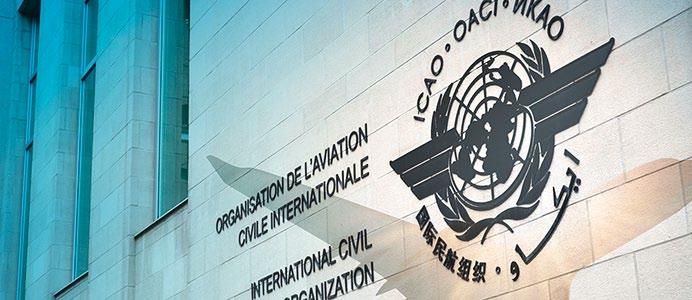