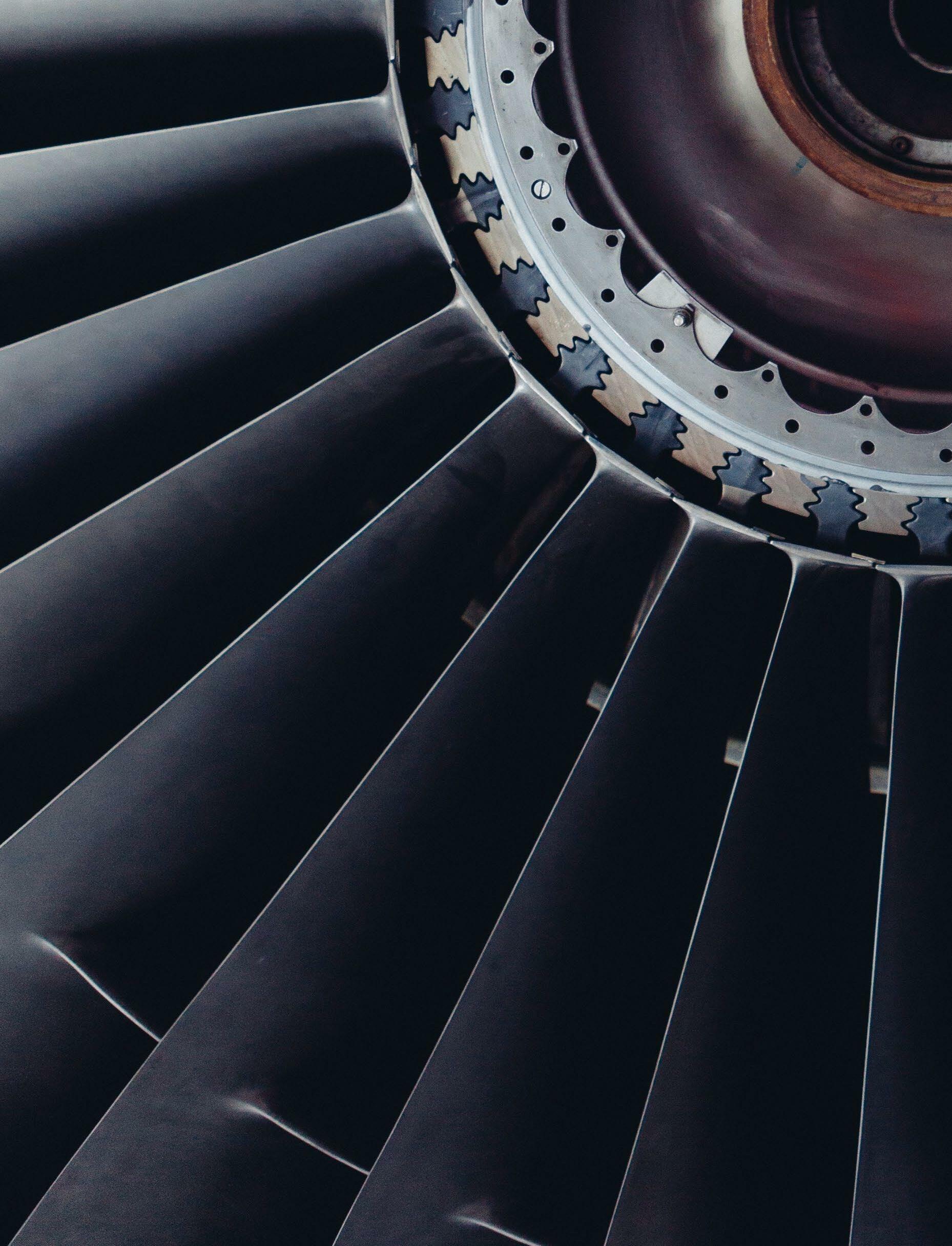
7 minute read
I²MPECT
Powering the future of aviation
Reducing carbon emissions is an increasingly urgent priority for the airline industry, while operators are also investigating ways to improve operational efficiency and reduce maintenance costs. The I²MPECT project aims to develop an innovative power converter which could have a significant impact on the airline industry, as Karl Weidner and Oliver Raab explain
The airline industry is under pressure
to reduce its carbon footprint and improve efficiency in line with wider goals around limiting the impact of climate change. Making greater use of electrical technologies could have a significant impact in these terms, an issue that researchers in the I²MPECT project are investigating. “One of the core aims of the I²MPECT project is to improve the efficiency of the airline industry. One possible way to achieve this is by moving away from burning fossil fuels towards greater use of electrical power,” explains Oliver Raab, the project’s coordinator. Funded under the Horizon 2020 programme, the project brings together nine partners from across Europe, aiming to develop next generation power electronic converters for use in aircraft. “We’re looking at the components of the converter itself and how we can improve the efficiency of those parts,” says Karl Weidner, principal engineer at Siemens.
A number of factors need to be taken into consideration into this work, with researchers in the project looking at each of the building blocks of the electrical converter. The shared goal is to develop efficient power converters and demonstrate their effectiveness even in harsh environments, while also looking to reduce the cost of production. “In reducing the cost of these building blocks, we can reduce the cost of manufacturing the system overall,” points out Raab. Based himself at Siemens, Raab says one of his company’s key roles within the project is to investigate the reliability of each of the different components within the power converter, which is of course a key issue in terms of their potential applicability in aircraft. “We compare different semiconductors, as well as packaging and assembly techniques in terms of their performance and durability,” outlines Raab. “Coming from that point, we’re looking to make the power modules, the heart of a converter, more efficient, more safe and more reliable.”
Semiconductor components
The project’s agenda also includes research into novel semiconductor components for the power module, especially silicon carbide (SiC). These offer some significant benefits in comparison to conventional silicon chips, according to Weidner. “The main reason for using these new semi-conductor technologies is that they are much more efficient than conventional silicon chips. You can drive those chips at a much higher frequency – so you can transform electrical energy in a much smoother way, and therefore improve the efficiency of the overall energy conversion system,” he outlines. A third key point is that these chips can withstand higher temperatures, leading to a less heavy cooling system, which is an important issue in terms of the eventual application of a power converter in an aircraft. “A converter has to be very reliable, very safe and lightweight to be used in an aircraft. This is something that we are working on – together with Safran Electrical & Power who are furthermore responsible for assembling and testing the overall converter system,” Raab states.
The project’s work in developing an innovative planar technology holds clear potential in these terms. Raab and his colleagues are closely involved in building up a planar interconnect technology, part of the wider goal of developing a compact and intelligent power electric converter. “The modules which we at Siemens and Dynex Semiconductors are developing are very compact, offer low inductivity and a good thermal behaviour” he explains. Different circuit topologies will be considered as researchers look to identify the best approach in terms of power density, efficiency and robustness. This down-selection process is supported by specialists of Airbus Group
Innovations, central R&T entity of Airbus Group. All this is done bearing in mind the challenging requirements that have been defined by Airbus and that have to be met for an eventual use in the target application onboard aircraft. “A further thing to consider is that the control and driving circuits have to be very specialised and very precise. They have to be very close to the switching elements – otherwise you get inductive disturbances,” outlines Raab. “We have to integrate the electronic components with each other very effectively – there’s a lot of research at the project partner ETH Zürich on precisely triggering those wide band gap chips.”
A high level of symmetry in the system is essential to achieving efficient switching, which is the basis for transforming a voltage to another voltage, and a frequency to another frequency. The switching characteristics also offer a means to monitor the health and functioning of the power module, a core element of the project’s work, which is being investigated at the University of Sheffield. “When you switch a semiconductor chip you get a response, and from this answer you can derive insights into the health status of the SiC chips and the power module itself,” explains Raab. This has important implications in terms of monitoring the state of the converter, and also can help reduce maintenance costs. “For example you can calculate the remaining life time of a power module by combining simulation models and experimental results together with profound calculation algorithms. Such a so called life time model is being developed by the Institut national des sciences appliquées de Lyon (INSA) in close collaboration with the other project partners,” outlines Raab. “From there, you can assess the likely performance lifespan of the power module.”
This leads into an enhanced ability to forecast when a converter will come to the end of its lifecycle, and hence predict maintenance intervals, which will have a significant impact on the expenses for aircraft operators. Accelerated reliability tests are being applied in the project to assess the performance of the converter. “In the project we’re using both physical methods and simulations to speed up the aging process of power modules,” says Raab. These tests, such as driving the power modules at very high temperatures, in some ways expose them to harsher conditions than the actual operating environment, which allows researchers to find defects in the modules in a very short period of time. “Together with our partner INSA, we are trying to identify failure mechanisms, and from that learn how we can modify the manufacturing process to prevent them if possible,” continues Raab. “If this is not possible, then we aim to find out after which period of time, and under which conditions, those failures will occur and how we can prevent those conditions.”
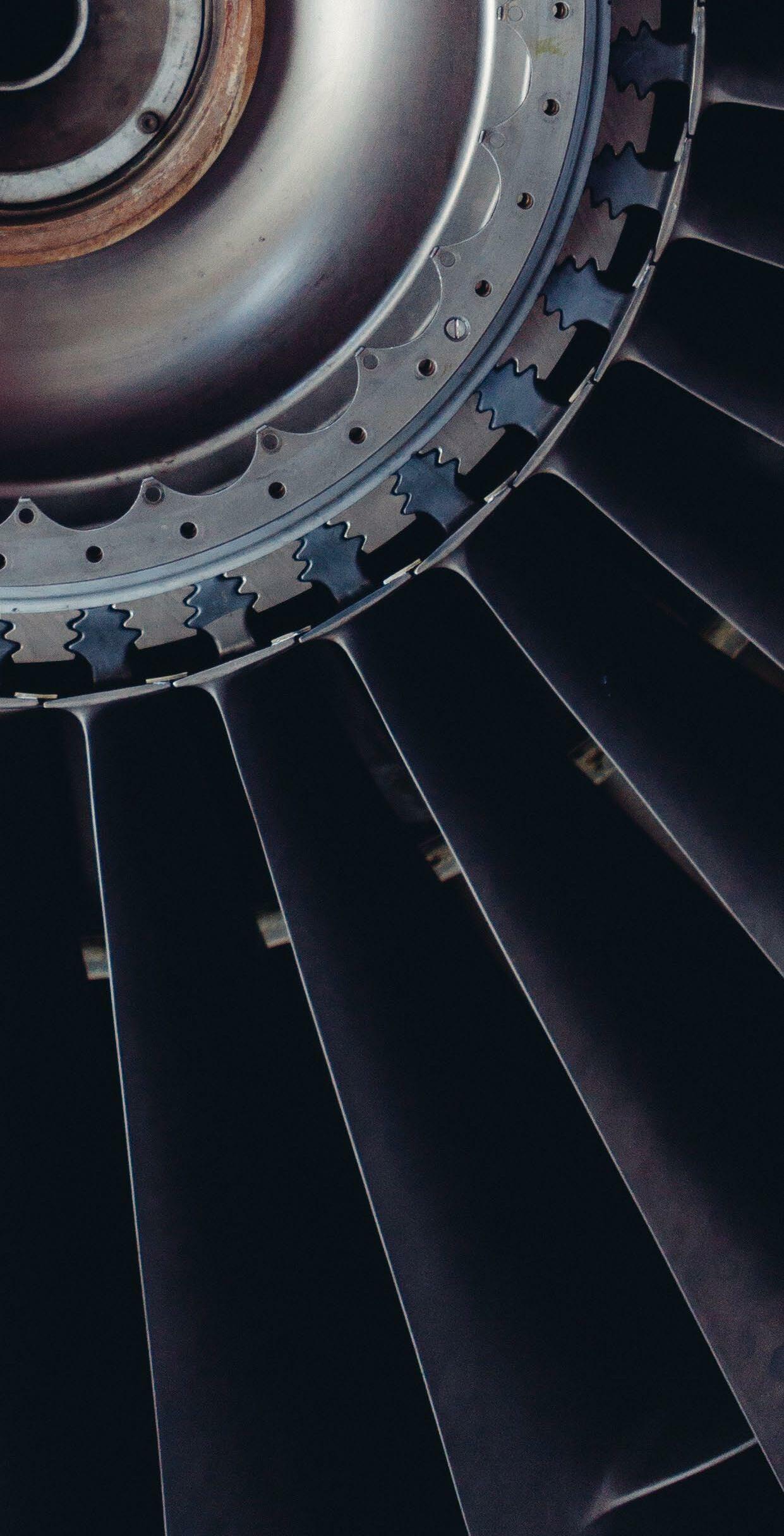
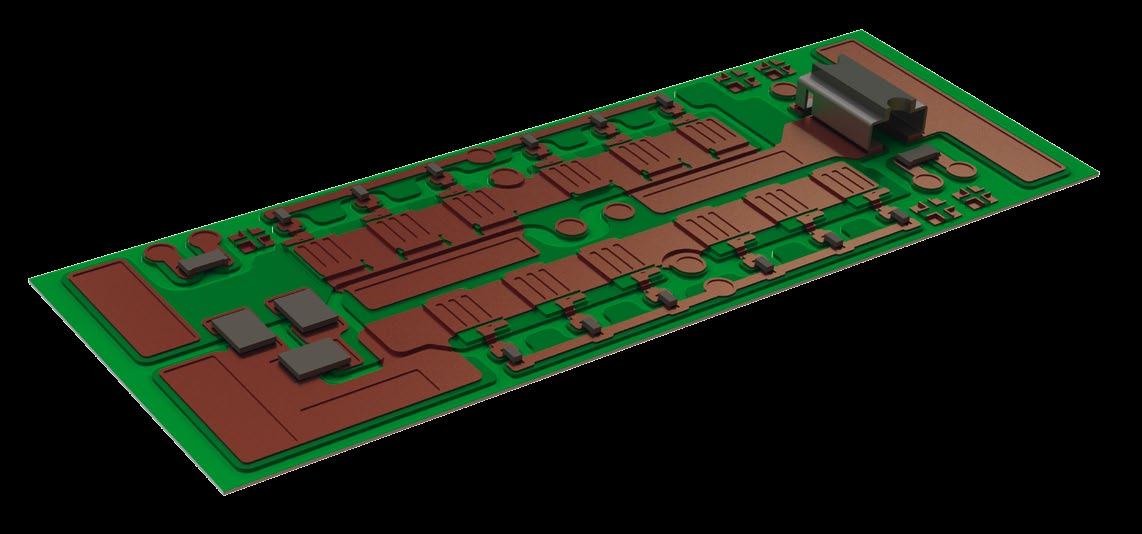
I²MPECT Siemens wirebond-less planar power module.
Full Project Title
Integrated, Intelligent Modular Power Electronic Converter (I²MPECT)
Project Objectives
Modular power electronic converters are the key technology enabling a “more electric” aviation. A more electrically driven aircraft has the potential to significantly reduce the airplane weight and therefore to reduce fuel consumption and the carbon footprint of today’s airplanes. The I²MPECT project will demonstrate important advances in power converters for harsh environments. Innovative 3D device packaging based on planar interconnect technologies with new integrated cooling technologies will be implemented for wide band-gap wire-bond free power semiconductor devices.
Project Funding
Funded by the European Commission Grant No. 636170: 6,734,627.00 euros.
Project Partners
Airbus Group (FR/DE), Dynex Semiconductor Ltd. (UK), Eidgenössische Technische Hochschule Zürich (CH), Institut national des sciences appliquées de Lyon (FR), K&S Projektmanagement (DE), Safran Electrical & Power (FR), Siemens AG (Coordinator, DE), University of Sheffield (UK).
Contact Details
Project Coordinator, Oliver Raab Siemens AG Corporate Technology CT REE PEM SPT-DE Otto-Hahn-Ring 6 81739 München, Deutschland T: +49 89 636-634366 E: oliver.raab@siemens.com W: http://www.i2mpect.eu/
Karl Weidner Oliver Raab
Oliver Raab is project manager and research scientist at Siemens Corporate Technology with his background lying in micro-electro-mechanical systems. Before he has put his research focus on power electronics he has been developing assembly solutions for different areas of application ranging from photovoltaics and printed electronics to detectors for computed tomography. Karl Weidner is a Principal Key Expert Engineer and experienced project leader in the field of future packaging technologies and innovative products for a broad range of technology fields. He has 27 years of experience and is focused on creating specific solutions in the area of electronic packaging and system integration.