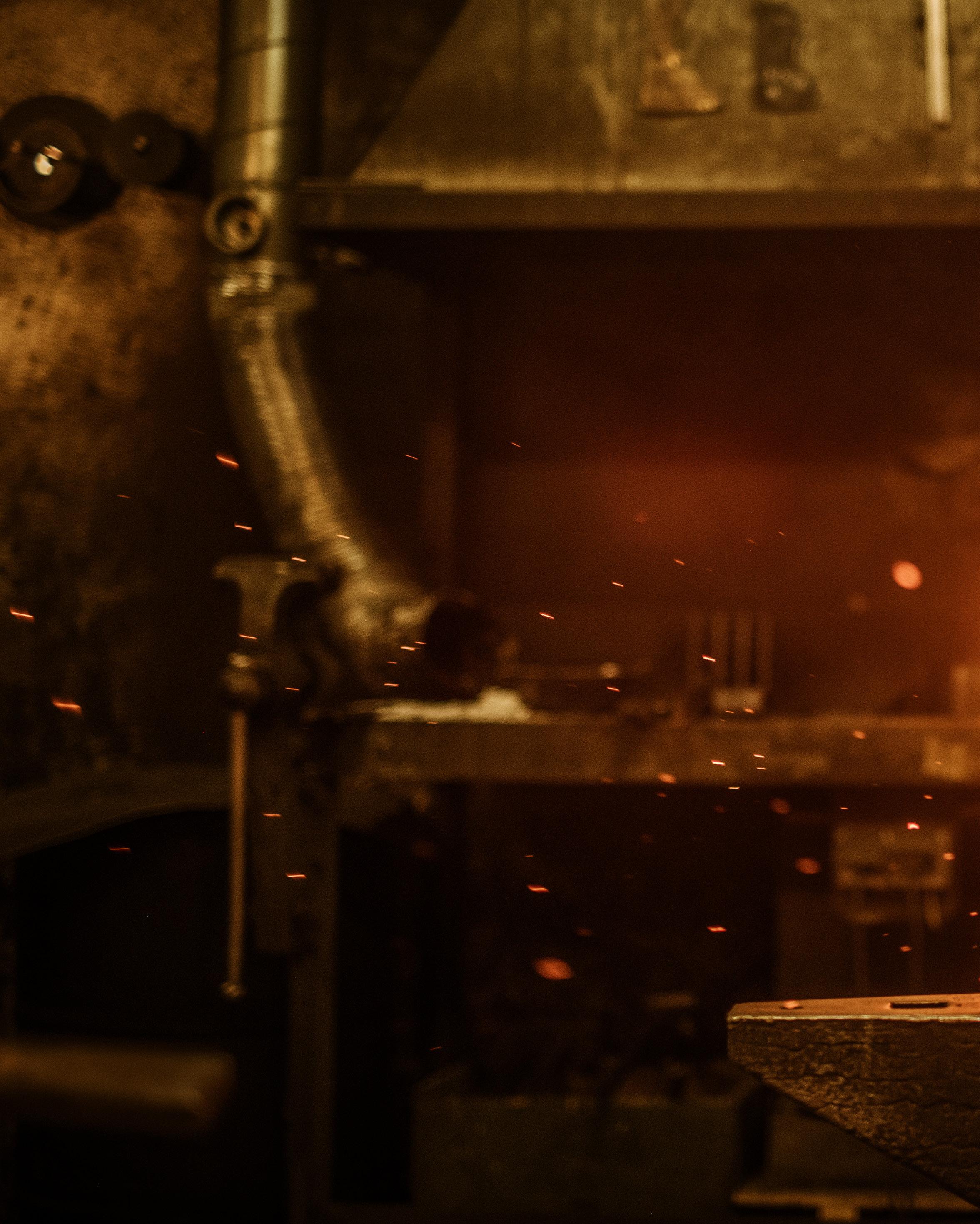
3 minute read
The Modern Blacksmith
from Entering The Flame
by Seubkj
Photograph by Alfa27
Chapter Two The Modern Blacksmith
Advertisement
The art of blacksmithing, beginning before recorded history, had changed very little over the centuries. In the recent past it reached such a peak of perfection that it will be difficult to attain that excellence again. But the very fact that our present society has entered into a renaissance of handcrafts now places the skill of working at the forge in a most promising light.
Modern equipment and trends have introduced new elements into this age-old art of hammering iron into various shapes on an anvil. For instance, that very useful new device, the visegrip pliers, is a very welcome additional tool in the modern blacksmith shop, not replacing traditional tongs, but supplementing them.
The utilization of salvaged steel material is a modern phenomenon. The present “economy of waste” had created an abundance of discarded, high-quality steel from scrapped automobiles and a variety of mechanical and industrial equipment. This give the contemporary blacksmith excellent material at almost no cost. In addition, modern power-tool equipment (secondhand or new) can be repaired or converted to meet specific tasks. Soon, an ideally equipped workshop comes about. No matter how “junky” it may seem in the eyes of others, it enables the modern blacksmith to forge useful and beautiful things from a seemingly endless variety of salvaged scrap.
The modern blacksmith must learn to do by himself that which the old-time blacksmith and his helper did as a team. They must learn how to resort to whatever he may invent, improvise, and construct in order to reduce the handicap of not have an apprentice helper. The machine plus modern hand tools becomes their assistances. Hand-filing, hand-drilling, and sledging can easily be replaced with the

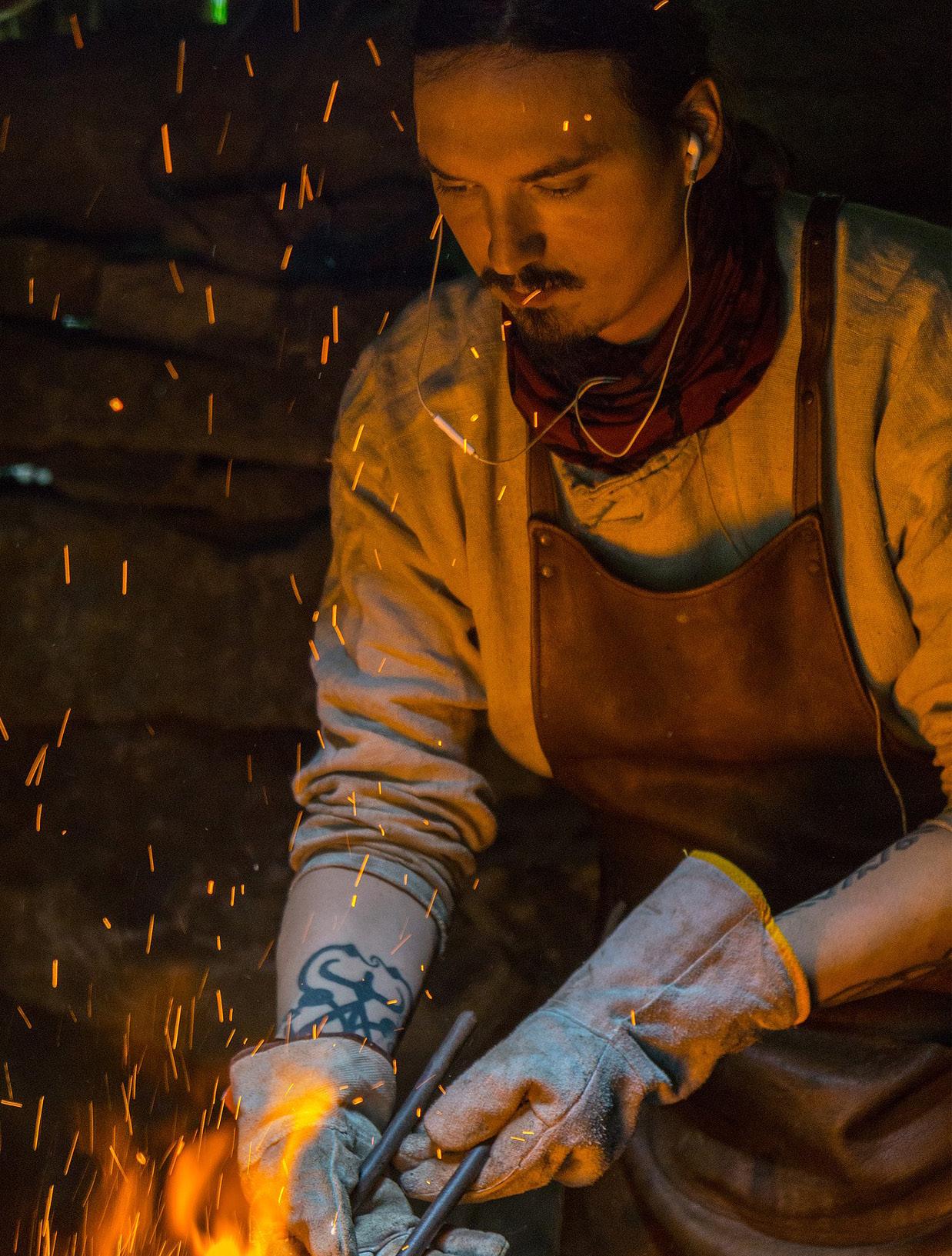
Photograph of a modern day blacksmith, and his forge and plugged into his headphones by Peter Bösken
power grinder, table power drill, and power hammer. Nevertheless, the forgings do not necessarily need to assume a mechanized look. If the machine remains strictly the helper, the overall results remain hand-rendered in appearance. The modern blacksmith who truly loves his craft will scrupulously want to perfect his skills in pure forging. Machine “hypnosis” must always be held at bay so that the craftsman will remain in full control of the machine and not the other way around.
The decorative-wrought-iron industry employs a few workers who call themselves blacksmiths, but their skill frequently could have been surpassed by a three-month apprentice a hundred years ago. There is a growing number of farriers. A good farrier working at a race track can make more money than most corporation executives in the United States, and a six-week course in horseshoeing costs about $1500 — no negligible tuition for a trade school. Farriers, however, while they use hammer and tongs, forge and anvil, are not general blacksmiths.
One can expect to see the general blacksmith disappear over time. His fire however, has been passed to the artist. For the young modern blacksmiths of the late twentieth century, the artists who have rediscovered the fascination and psychic satisfaction of ironworking, are growing in numbers. The enthusiastic band will save the sounds, the smells, the visual joys of the blacksmith shop as a human heritage for generations to come.
Photograph by Anna Volotkovska

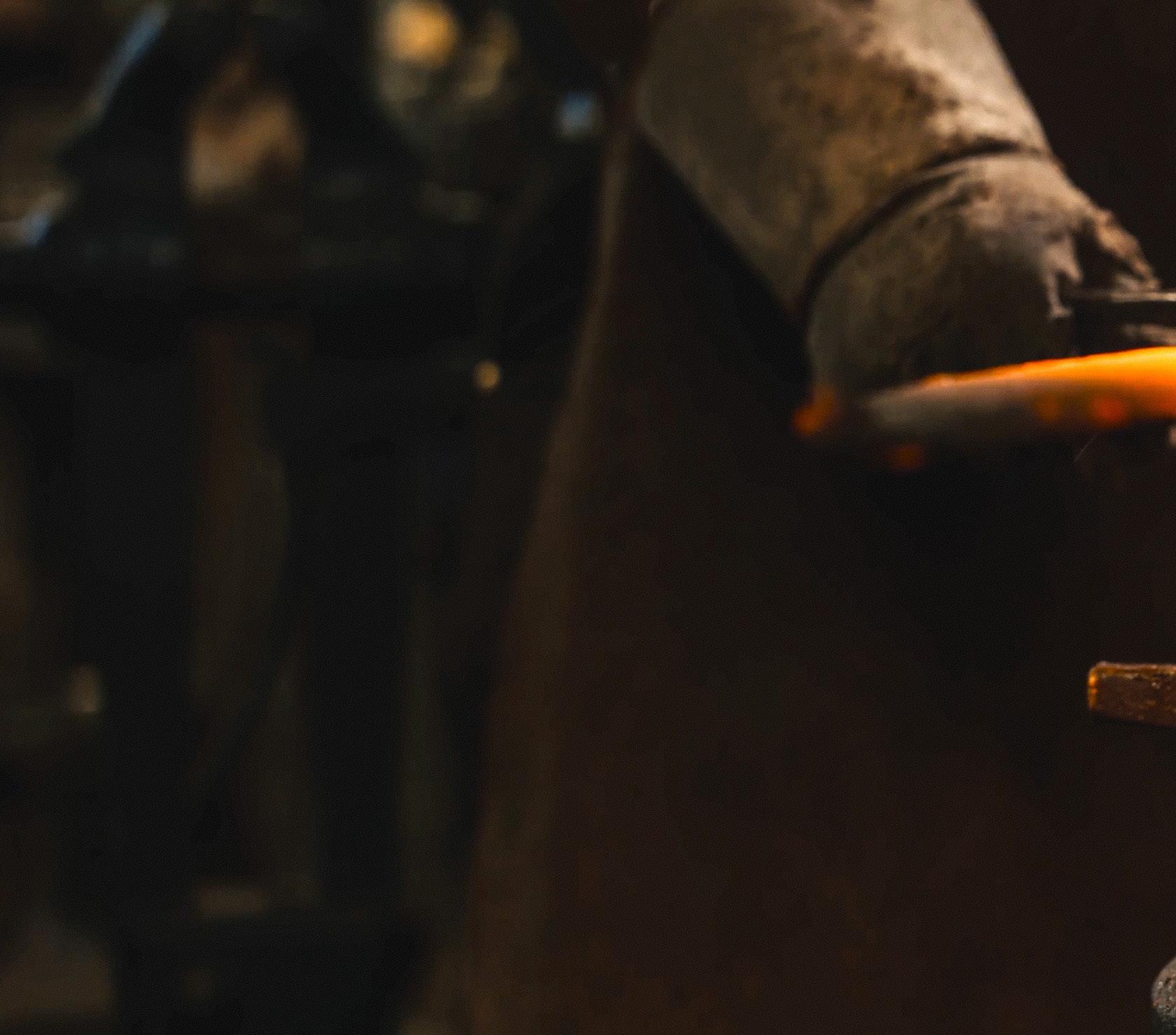
Photograph by Isaac74
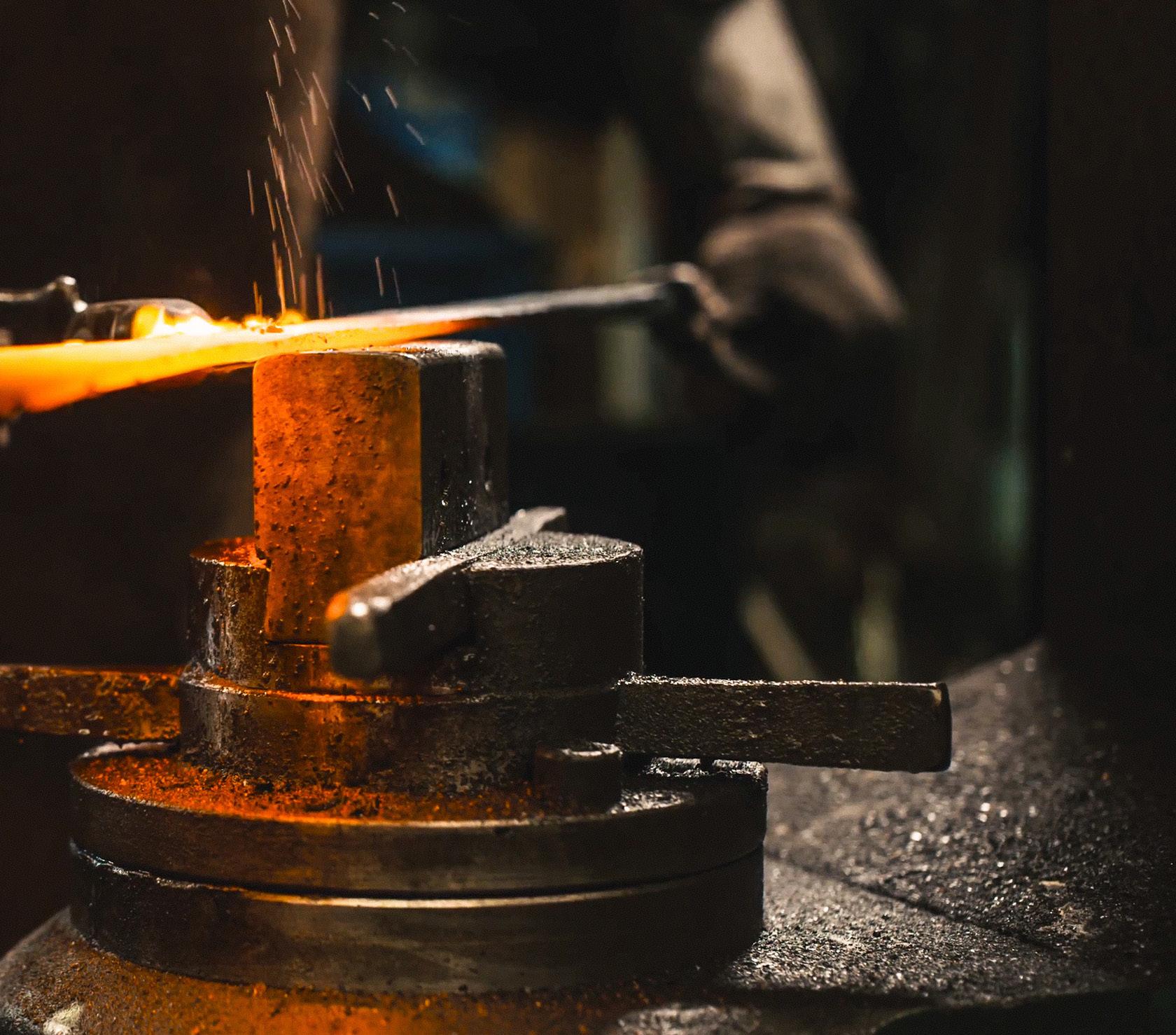
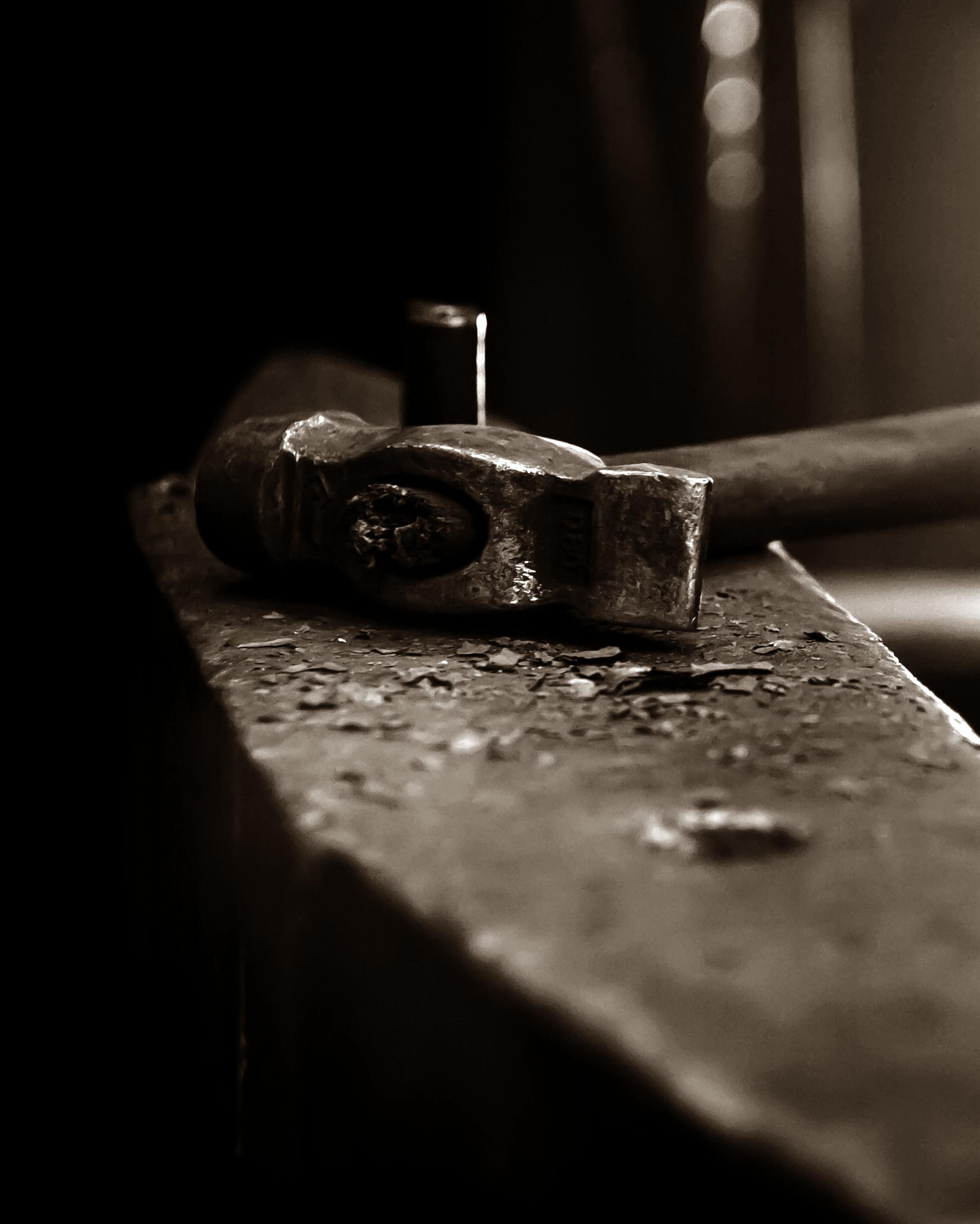

W orkshop
