9 minute read
Manufatura aditiva e o novo paradigma da produção de peças de reposição
Por Paulo Roberto dos Santos
Já ouviu falar em Manufatura Aditiva, ou em inglês AM – Additive Manufacturing? Talvez tenha ouvido falar em impressão 3D. O que talvez muitos não tenham visto ainda, é como a manufatura aditiva está evoluindo rápido, especialmente na fabricação de peças em metal. Sim! Peças de metal, fabricadas totalmente a partir da adição de materiais.
Ao contrário do processo de usinagem convencional, em que o material deve ser removido, a impressão em 3D ou MA constrói um objeto tridimensional a partir do modelo CAD ou arquivo AMF, adicionando sucessivamente material camada a camada.
São processos usados para criar um objeto tridimensional, em que camadas de material são formadas sob controle de computador. Os objetos podem ser de quase qualquer forma ou geometria e são produzidos usando dados de modelo digital 3D ou outra fonte eletrônica de dados, como um arquivo AMF (Additive Manufacturing File).
Imagine este cenário: Um elevador quebra em uma cidade no interior de um estado remoto no Brasil. O provedor de serviços precisa substituir a peça o mais rápido possível para restaurar o serviço. A empresa de manutenção, em sua oficina local baixa os arquivos de peças necessários de um servidor central de nuvem e os envia para produzir em uma impressora 3D interna, ou de um fornecedor que concentre a produção local. O elevador deve estar funcionando novamente em breve, certo?
Esse poderá ser um cenário comum nos próximos anos. É evidente que continuaremos mantendo peças de maior demanda em estoque, e assim minimizamos o custo de
reparo. Mas, em muitos casos as peças necessárias são caras demais para mantermos em estoque, sem uma garantia de que serão necessárias. Por outro lado, quem estiver mais bem preparado para atender com agilidade, se tornará mais competitivo.
A manufatura aditiva está ganhando tanta importância, que já existe uma Norma ISO sobre o tema: A ISO / ASTM52900-15, que define sete categorias de processos MA no seu significado: • jato de aglutinante • deposição de energia direcionada • extrusão de material • jato de material • fusão de pó • laminação de folhas • fotopolimerização em cubas
A seguir a descrição de cada processo.
Jato de aglutinante
O processo de jato aglutinante utiliza dois materiais; um material à base de pó e um aglutinante. O aglutinante geralmente está na forma líquida e o material de construção na forma de pó. Uma cabeça de impressão se move horizontalmente ao longo dos eixos X e Y da máquina e deposita camadas alternadas do material de construção e do material aglutinante, até formar a peça final. Após cada camada, o objeto que está sendo impresso é baixado em sua plataforma de construção.
Devido ao método com jato aglutinante, as características do material nem sempre são adequadas para as peças estruturais e, apesar da velocidade relativa da impressão, o pós-processamento adicional pode adicionar um tempo significativo ao processo geral.
Como em outros métodos de fabricação à base de pó, o objeto que está sendo impresso é autossustentável no leito de pó e é removido do pó não ligado depois de concluído. A tecnologia é geralmente chamada de tecnologia 3DP e possui direitos autorais sob esse nome.
Deposição de energia direcionada
O DED (Directed Energy Deposition) abrange uma variedade de terminologias: ‘Moldagem de rede projetada a laser, fabricação de luz direcionada, deposição direta de metal, revestimento a laser 3D’. É um processo de impressão mais complexo, comumente é usado para reparar ou adicionar material adicional aos componentes existentes (Gibson et al., 2010).
Uma máquina DED típica consiste em um bico montado em um braço de vários eixos, que deposita o material derretido na superfície especificada, onde solidifica. O processo é semelhante em princípio à extrusão de material, mas o bico pode se mover em várias direções e não é fixo a um eixo específico. O material, que pode ser depositado de qualquer ângulo devido a máquinas de 4 e 5 eixos, é derretido mediante deposição com um laser ou feixe de elétrons. O processo pode ser usado com polímeros, cerâmica, mas normalmente é usado com metais, na forma de pó ou arame.
As aplicações típicas incluem reparo e manutenção de peças estruturais.
Extrusão de material
A modelagem de deposição por fusível (FDM) é um processo comum de extrusão de material e é registrada pela empresa Stratasys. O material é puxado através de um bico, onde é aquecido e, em seguida, depositado camada por camada. O bico pode se mover horizontalmente e uma plataforma se move para cima e para baixo na vertical depois que cada nova camada é depositada. É uma técnica comumente usada em muitas impressoras 3D domésticas e de baixo custo.
O processo possui muitos fatores que influenciam a qualidade do modelo final, mas possui grande potencial e viabilidade quando esses fatores são controlados com sucesso. Embora o FDM seja semelhante a todos os outros processos de impressão 3D, à medida que cria camada por camada, varia no fato de o material ser adicionado através de um bico sob pressão constante e em um fluxo contínuo. Essa pressão deve ser mantida constante e a uma velocidade constante para permitir resultados precisos (Gibson et al., 2010). As camadas de material podem ser ligadas pelo controle de temperatura ou pelo uso de agentes químicos. O material é frequentemente adicionado à máquina na forma de carretel, como mostrado no diagrama.
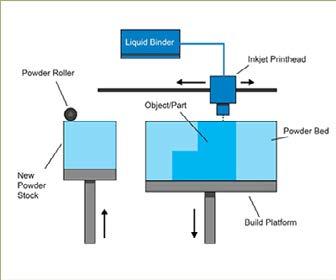
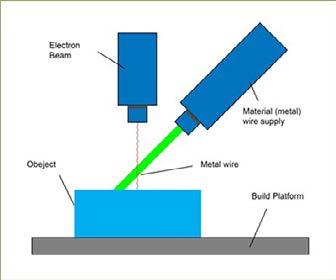
Jato de material
O jateamento de material cria objetos em um método semelhante a uma impressora a jato de tinta bi-
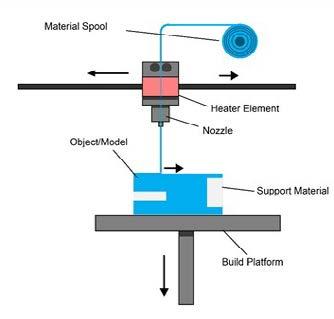
dimensional. O material é injetado em uma plataforma de construção usando uma abordagem contínua ou Drop on Demand (DOD). O material é jateado na superfície ou plataforma de construção, onde solidifica e o modelo é construído camada por camada. O material é depositado a partir de um bico que se move horizontalmente através da plataforma de construção. As máquinas variam em complexidade e em seus métodos de controle da deposição de material. As camadas de material são então curadas ou endurecidas usando luz ultravioleta (UV).
Como o material deve ser depositado em gotas, o número de materiais disponíveis para uso é limitado. Polímeros e ceras são materiais adequados e comumente usados, devido à sua natureza viscosa e capacidade de formar gotas.
Fusão de pó
O processo de fusão do leito de pó inclui as seguintes técnicas de impressão comumente usadas: sinterização direta a laser de metal (DMLS), fusão por feixe de elétrons (EBM), sinterização seletiva por calor (SHS), fusão seletiva a laser (SLM) e sinterização seletiva a laser (SLS).
Os métodos de fusão do leito de pó (PBF) usam um laser ou feixe de elétrons para derreter e fundir o pó do material. A fusão por feixe de elétrons (EBM), os métodos requerem vácuo, mas podem ser usados com metais e ligas na criação de peças funcionais. Todos os processos PBF envolvem a dispersão do material em pó sobre as camadas anteriores. Existem diferentes mecanismos para permitir isso, incluindo um rolo ou uma lâmina. Uma tremonha ou um reservatório abaixo da cama fornece suprimento de material fresco. A sinterização direta a laser de metal (DMLS) é igual à SLS, mas com o uso de metais e não de plásticos. O processo sinteriza o pó, camada por camada. A sinterização seletiva por calor difere de outros processos ao usar uma cabeça de impressão térmica aquecida para fundir o material em pó. Como antes, as camadas são adicionadas com um rolo entre a fusão de camadas. Uma plataforma reduz o modelo de acordo.
Laminação de folhas
Os processos de laminação de chapas incluem manufatura aditiva por ultrassom (UAM) e manufatura de objetos laminados (LOM). O processo de fabricação aditiva por ultrassom usa folhas ou fitas de metal, que são unidas por meio de soldagem por ultrassom. O processo exige usinagem cnc adicional e remoção do metal não ligado, geralmente durante o processo de soldagem. A fabricação de objetos laminados (LOM) usa uma abordagem semelhante de camada por camada, mas usa papel como material e adesivo em vez de soldar. O processo LOM usa um método de hachura cruzada durante o processo de impressão para facilitar a remoção após a compilação. Objetos laminados são frequentemente usados para modelos estéticos e visuais e não são adequados para uso estrutural. A UAM usa metais e inclui alumínio, cobre, aço inoxidável e titânio (Visão Geral da Fabricação de Aditivos Ultrassônicos, 2014). O processo é de baixa temperatura e permite a criação de geometrias internas. O processo pode unir diferentes materiais e requer relativamente pouca energia, pois o metal não é derretido.
Fotopolimerização em cubas
A polimerização em cuba, usa uma cuba com resina líquida de fotopolímero, da qual o modelo é construído camada por camada. Uma luz ultravioleta (UV) é usada para curar ou endurecer a resina quando necessário, enquanto uma plataforma move o objeto que está sendo feito para baixo após a cura de cada nova camada.
Como o processo usa líquido para formar objetos, não há suporte estrutural do material durante a fase de construção. Diferentemente dos métodos à base de pó, onde o suporte é fornecido a partir do material não ligado. Nesse caso, as estruturas de suporte geralmente precisam ser adicionadas. As resinas são curadas usando um processo de fotopolimerização (Gibson et al., 2010) ou luz UV, onde a luz é direcionada através da superfície da resina com o uso de espelhos controlados por motores (Grenda, 2009). Onde a resina entra em contato com a luz, cura ou endurece.
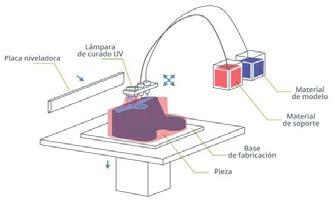
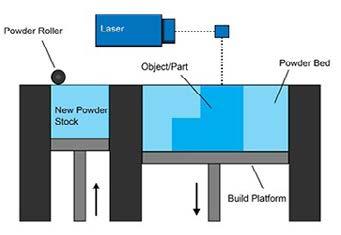
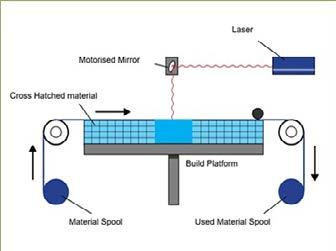
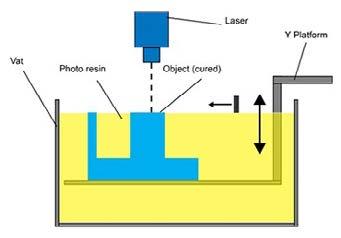
Conclusão
Essa é uma das tecnologias habilitadoras da Indústria 4.0, está apenas no começo das aplicações industriais, embora muitos componentes, inclusive aeroespaciais, já se beneficiem da tecnologia.
O tempo e o custo das peças produzidas estão caindo drasticamente, mês após mês. Novos métodos de manufatura aditiva estão surgindo rapidamente, com mais possibilidades e capacidades, é uma rápida evolução que está substituindo processos convencionais.
Acompanhe de perto a evolução dessa tecnologia, porque ela será um dos principais processos de produção em poucos anos.
Sobre o autor
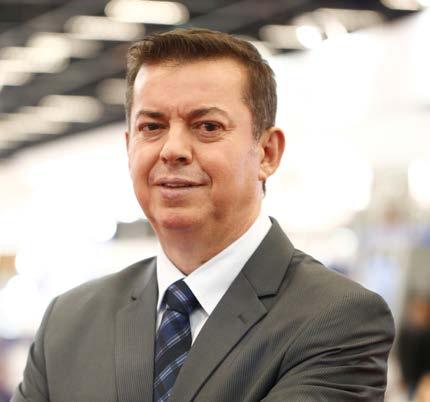
Paulo Roberto dos Santos
Sócio Diretor da Zorfatec, consultoria em Inovação Tecnológica, Engenheiro Industrial Mecânico, MBA em Gestão e Engenharia do Produto pela Escola Politécnica da USP, Especialista em Industria 4.0. Durante mais de 25 anos atuou na Festo Brasil, sendo responsável por P&D e pela Estratégia de Produtos na Região Américas. Tem Especialização em Administração de Empresas, Gerenciamento do Desenvolvimento de Produtos, e Dinâmica Organizacional e Gestão de Pessoas pela Fundação Getúlio Vargas. Especialista em Gestão da Inovação, posicionamento estratégico da empresa para novas tendências como Industrial IoT e Indústria 4.0 (Manufatura Avançada). Com mais de 25 anos de experiência na Gestão de Projetos de Inovação, Engenharia e Automação. Mentor dos principais projetos de demonstradores de Indústria 4.0 apresentados na FEIMEC 2016, Expomafe 2017 e FISPAL 2017. Um dos pioneiros na introdução do tema Industria 4.0 no Brasil. Palestrante sobre temas de Inovação, Automação Industrial, Internet das Coisas (IoT) e Indústria 4.0. Apresentando os temas em congressos, seminários e eventos especializados no Brasil e América do Sul.