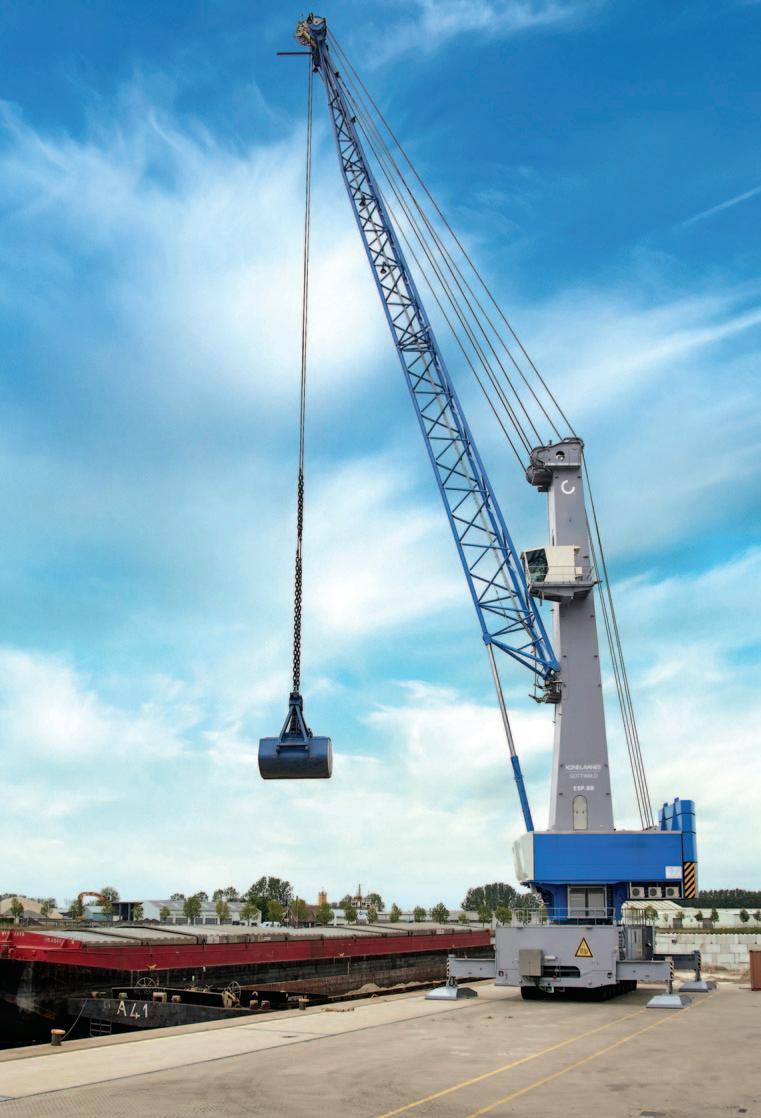
19 minute read
CLOSE-UP ON CRANES: THE BULK MARKET’S WORKHORSE
ENGINEERING & EQUIPMENT Closeup on cranes
the bulk market’s workhorse
ESP.8B Konecranes Gottwald mobile harbour crane for continuous-duty bulk handling.
Jay Venter
Konecranes instills new Generation 6 mobile harbour cranes with a genetic code for the future
ESP – Electric, Smart, Powerful:
Konecranes Gottwald Generation 6 mobile harbour cranes are built on this genetic code. They combine technology proven a thousand times over with innovation, and offer not only high performance and ecoefficiency but a high level of intelligence, too.
With its new Generation 6 mobile harbour cranes, Konecranes has transformed industrial megatrends and current port developments in ports and terminals into high-performance cargohandling technology. The initial six crane models with maximum lifting capacities of 200 tonnes and radii up to 64m stand for sustainability, de-carbonization and ecoefficiency, in addition to ergonomics, digitalization and automation. They provide terminal operators with mobile cargo handling machines that not only reduce the ecological footprint, but also impress with robust design and distinct dynamics, as well as particularly smart equipment. To meet all requirements for handling performance, productivity, safety and serviceability, Konecranes has been in close communication with customers around the world throughout the development of Generation 6.
PREMIUM LEGACY, COMBINED WITH INNOVATIVE STRENGTH Konecranes’ more than 60 years of experience as the inventor and premium manufacturer of mobile harbor cranes, plus its R&D strength as a global player, are evident in Generation 6. Heribert Barlage, Senior Vice President Business Unit Mobile Harbor Cranes, said: “Generation 6 combines pioneering spirit with the innovative power of the technology leader Konecranes. Our mobile harbour cranes have always stood for performance and dynamics, and they have always been electric.
“We have once again enhanced these features for Generation 6, while at the same time providing a high level of intelligence. The result is a total package with which we make our customers well prepared to meet today’s requirements and at the same time provide them with the code for the challenges of tomorrow, ESP.”
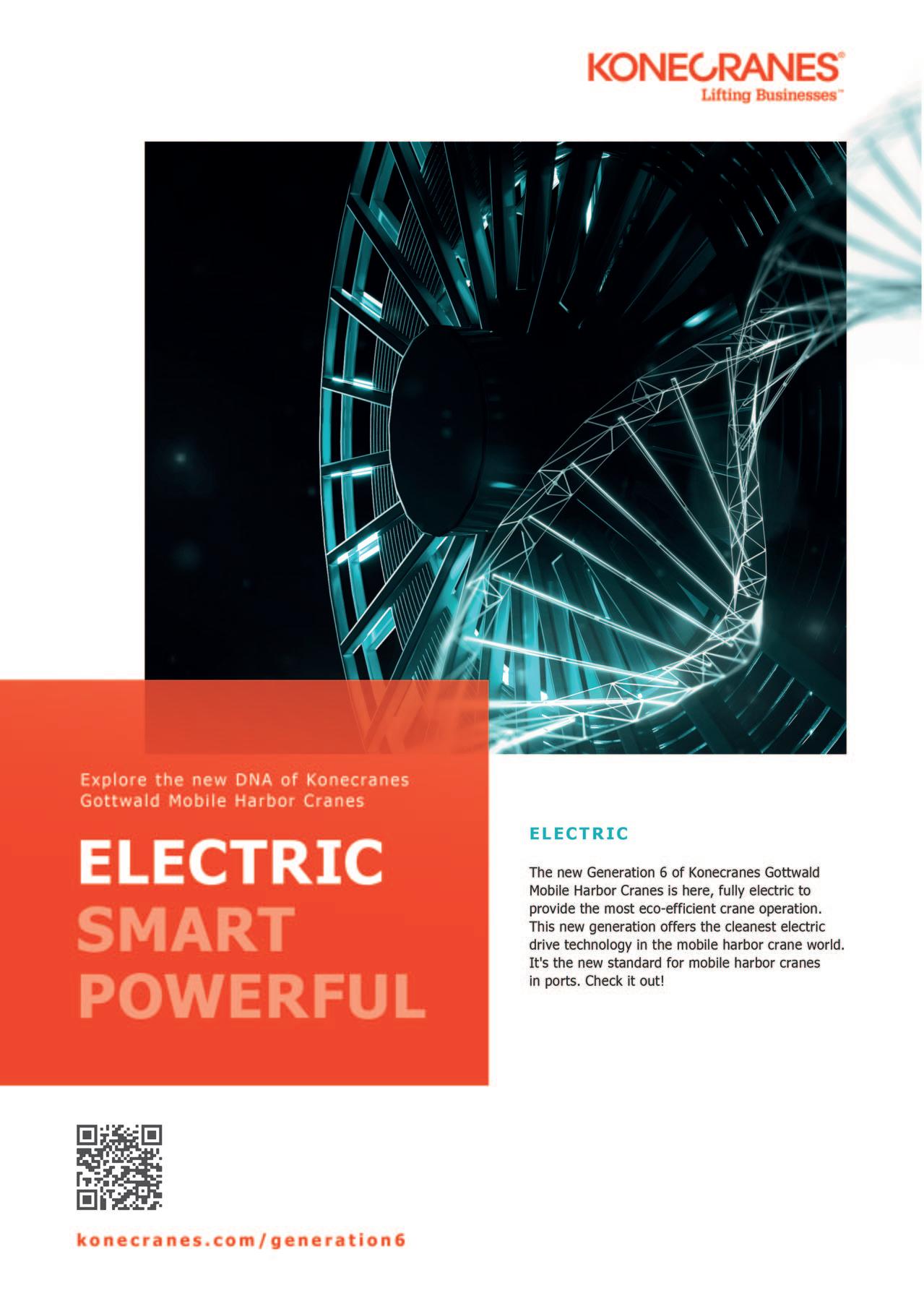
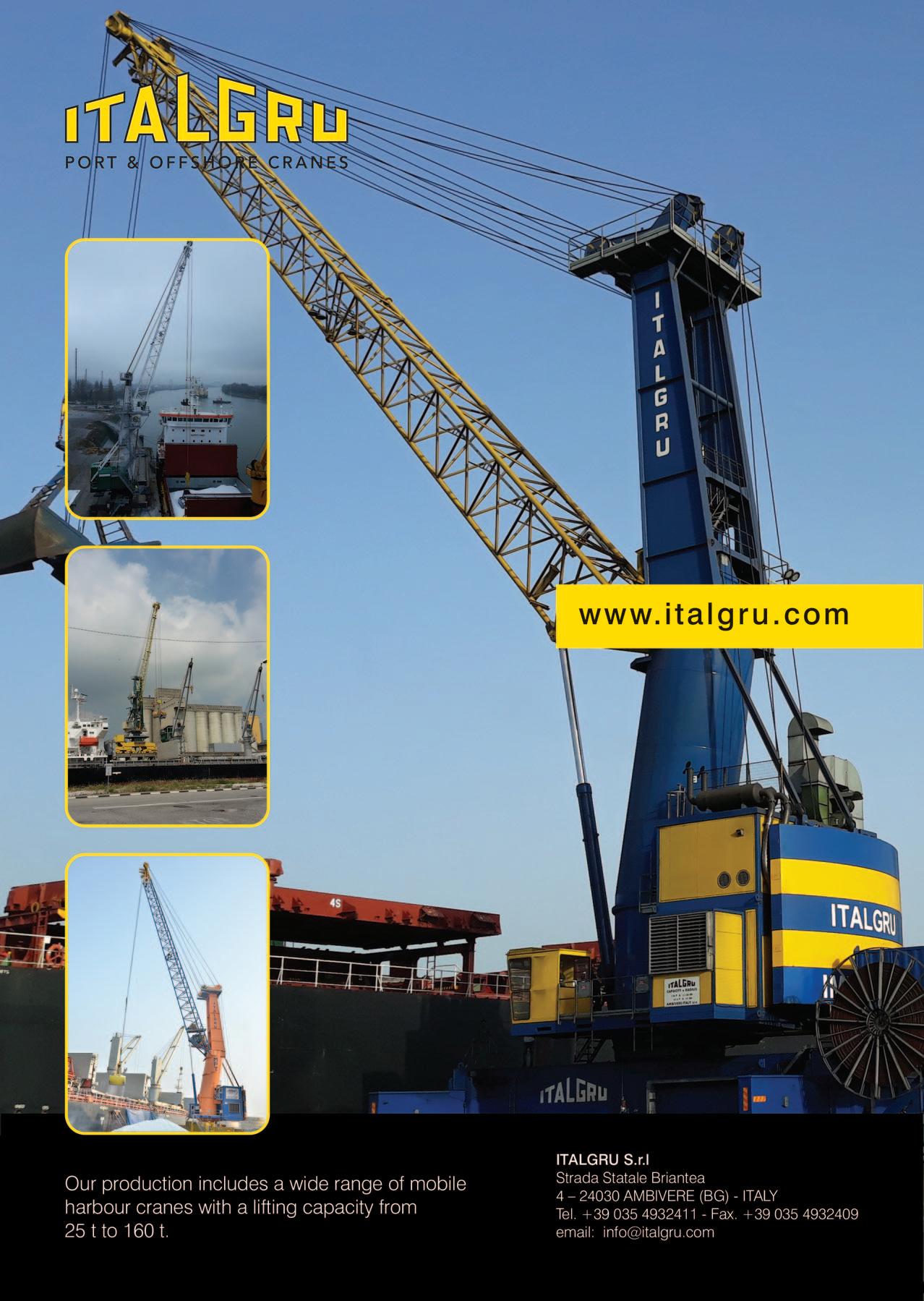
E FOR ELECTRIC: THE GENE FOR SUSTAINABILITY E for Electric denotes the electric drive systems of Konecranes Gottwald mobile harbour cranes, in use since 1956. Generation 6 is designed so that customers can choose from several electric drive variants. Power can be supplied via the onshore power grid or an on-board generator. If a crane always works on the same quay where shore power is available, customers can rely on using the appropriate equipment from the outset. If cranes need to be disconnected from the grid for journeys between quays with shore power supply, a battery pack ensures mobility — a first for Konecranes. For quays both with and without access to power from the on-shore grid, the combination of shore power equipment and diesel-generator set is the solution. For quays without power supply, the latest hybrid drives are available.
S FOR SMART: THE GENE FOR SUSTAINABILITY S for Smart stands for the added smart features that Konecranes has given its Generation 6 cranes. The interpretation of Smart has been particularly versatile here, for example ergonomics: this is where the new cranes impress with a stateof-the art cab, from which the crane operator has everything perfectly under control. This is due not least to the completely revised Visumatic® crane management system, which also controls all smart crane features, supporting the crane operator with even more productive and safe handling options. Based on smart crane features, Konecranes is also gradually paving the way for further crane automation. Additional focus has been placed on transparent crane operation, too. This is achieved via the YourKonecranes customer portal with cloud-based connectivity solution Truconnect® , which gives terminal operators access to a wealth of process and operating data as well as maintenance and service information.
P FOR POWERFUL: THE GENE FOR RELIABLE DYNAMICS P for Powerful is the crossgenerational original gene of all Konecranes Gottwald mobile harbour cranes. P means: dynamics and maximum performance in continuous-duty operation — serving all types of vessels in all terminals and in all applications. Ecoefficient with its type of drive and smart with its crane operator assistance systems, Generation 6 cranes are also improved in their core characteristic: More robust steelwork doubles the service life in container operation, up to 30% more powerful four-rope grab curves ensure optimum operation of vessel hatches and up to 18% higher working speeds ensure fast vessel turnaround.
GENERATION 6 COMES WITH A POWERFUL RANGE Generation 6 is being launched with six high-performance models. This compre hen sively diversified range of cranes starts with the ESP.6 model and extends to the ESP.9 high-performance crane; customers can choose between two-rope and fourrope grab crane versions with numerous options; all cranes offer a homogeneous product face. With lifting capacities up to 200t, radii up to 64m and 63t grab load curves, the range of performance is extensive — as are the possible applications.
Barlage concludes: “Generation 6 covers our complete crane modular system, including portal harbour cranes and cranes on barge. This means that the new cranes fit into any infrastructure, which makes the ESP code successful and future-proof not only on the quay, but also beyond the quayside”.
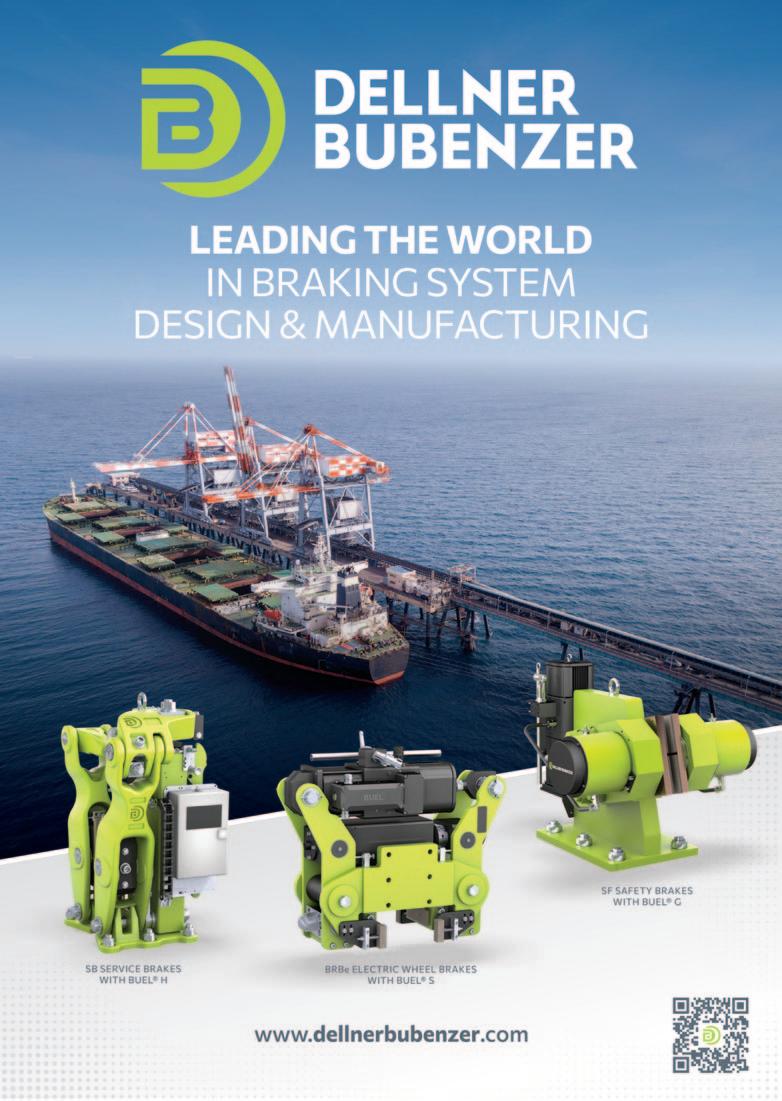

Engbergs operates at Östrand pulp mill, about 12 kilometers from Sundsvall port on the Swedish East Coast. Engbergs operates mostly with vessel offloading of round wood and woodchips, and last year it also started bark-handling. Engbergs has a long history with Mantsinen Group, going back over 20 years. During this time, it has witnessed the development of Mantsinen to the size the company is today. It was therefore easy to choose new material handlers from Mantsinen that were needed in order to increase production capacity by 100%. Choosing Mantsinen material handlers comes naturally to Kjell Arne Engberg, CEO of Engbergs.
“Our relationship with Mantsinen has deepened over the years. In 2003, our first Mantsinen machine was put to use and we were very satisfied with the machine, not to mention the service support we got. No matter where in the world our contact was, they always answered the phone.”
In 2009 Engbergs ordered another Mantsinen material handler, and in 2017 the co-operation was taken to a new level when discussions about Mantsinen’s latest innovation started; the Mantsinen Dualpower is the first real dual power concept within large material handlers utilizing twin engine technology. It combines the best features of an electric motors and a diesel engine, resulting in a union of mobility, productivity and advanced environmental friendliness.
FORTUNE FAVOURS THE BOLD Engbergs was the first customer to acquire a Mantsinen’s Dualpower machine, in this case a Mantsinen 120 with crawler gantry undercarriage.
“I am very open minded towards development of products. We purchased one diesel Mantsinen 120 and one Mantsinen 120 with Dualpower. The reason for the machine renewal was that the pulp mill decided to increase production by 100% and we needed to solve the logistics accordingly. In all our investments, we look into the possibility of reducing carbon emissions. We wanted this solution because it combines two benefits: when you reduce emissions, you also reduce costs. It is a win-win situation. However, we still needed a diesel-driven machine too, because we could not access electrical power all around the pulp mill area. The pulp mill was luckily very interested in helping us build the power grid solution.”
PERFORMANCE AND EASY MAINTENANCE One of the benefits of the Dualpower is easy maintenance. The technology is based on standard components, allowing easy service and standard spare parts availability. Pairing this technology with the Mantsinen Insight allows for smooth operation and fewer unexpected surprises.
“The material handler works well, and it has much fewer maintenance needs. I believe that the maintenance in these kinds of machines will be more and more remote. The Mantsinen Insight lets the machine tell you if something is not right. In the future I think we could even solve some problems remotely and not on the site.”
In addition to maintenance needs, the Mantsinen Insight also records all the important data on the machine’s performance and efficiency. Engbergs has achieved the production increase they wanted with the help of the Mantsinen 120 Dualpower.
“Looking at the last seven days, we have lifted 23,000 tonnes mainly with electric motor. Our production has been in average 435 tonnes per hour.”
INNOVATION CYCLES GAIN SPEED Megatrends of intelligent data and environmentally friendly solutions are unstoppable. Development cycles gain speed and companies are more willing to try new solutions.
“The speed of development is very interesting. This is mostly seen in cars, but also in industrial machines — there is a need to get away from the fossil fuels. Even in the financial markets, there will be a trend of environmental friendliness, for example interest rates being depended on how much your investments affect the environment. Also reusing materials and components will develop further.”
Other suppliers were also considered during the purchasing process. Engbergs has a habit of a meticulous background investigation before seeking quotes. Mantsinen was selected as the competitors did not quite meet Engbergs quality standards.
“With our investigation looking into the investment, it was very clear to us what we needed from the machine. It seems this material handler with both diesel and electric drive is the right solution for us.
“We have reduced the emissions enormously,” Engberg sums up.
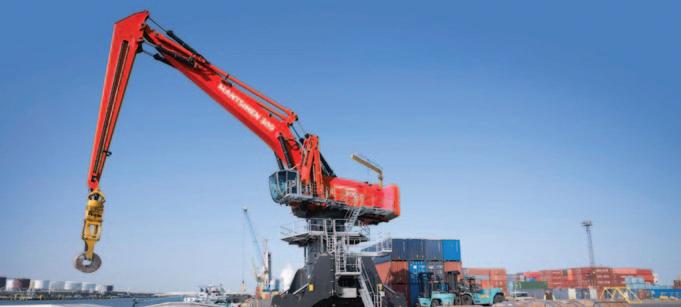
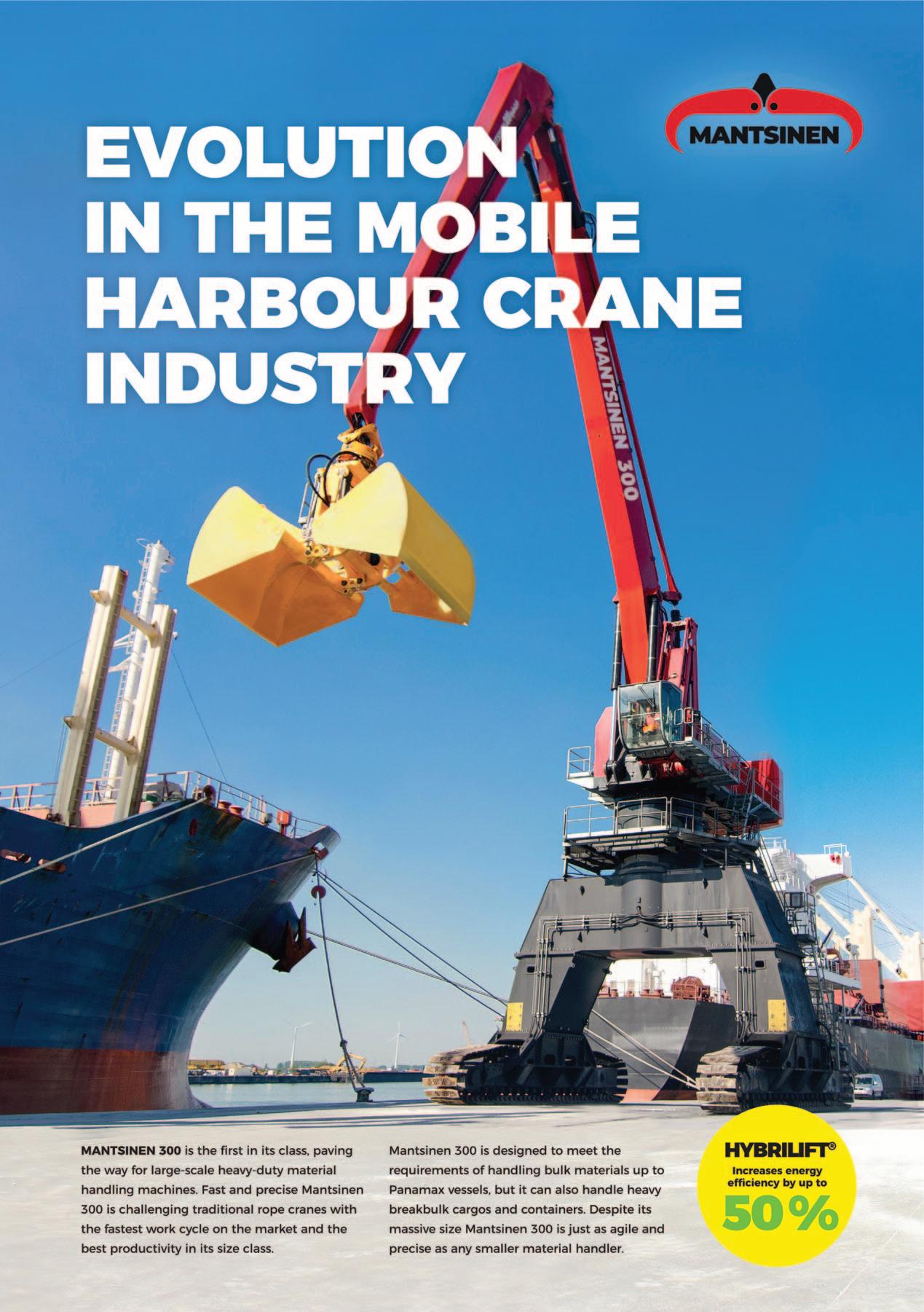
ENGINEERING & EQUIPMENT 1,300 maritime cranes – from Rostock to the world
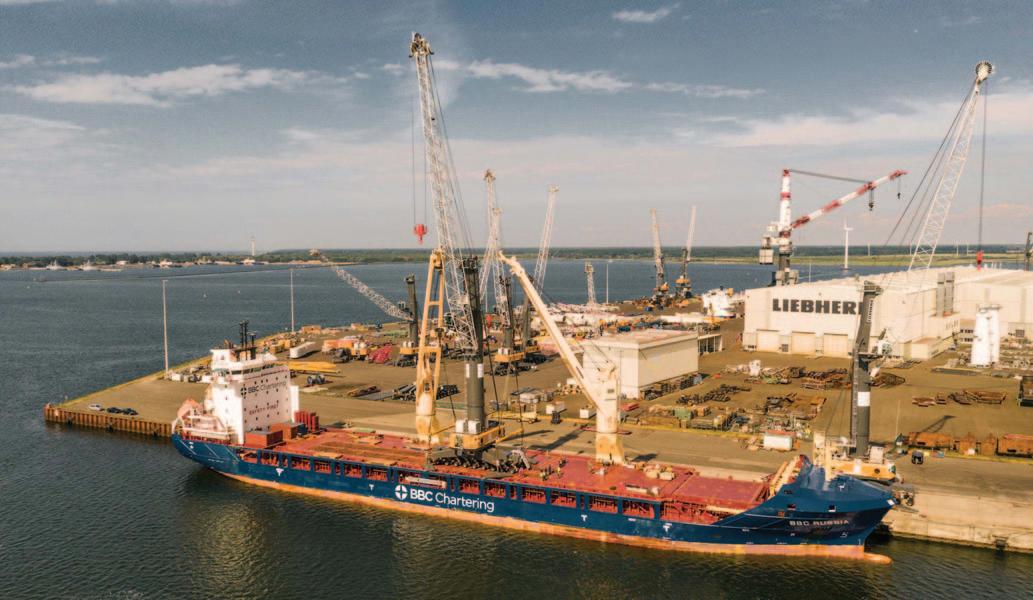
Liebherr Rostock has manufactured and delivered 1,300 maritime cranes since 2005.
Since the start of production in 2005, Liebherr-MCCtec Rostock GmbH has manufactured and delivered well over 1,000 maritime cranes. Today, the numerous mobile harbour, ship and offshore cranes are in use in over 100 countries on all continents. Now the 1,300th crane has left the Rostock premises to its destination in Ghana.
Slowly, ship cranes on the heavy-lift vessel BBC-Russia raise the new machine over the quay edge. The LHM 550 is one of two Liebherr mobile harbour cranes that will, in a few hours, begin the 5,500km journey to Ghana. On receiving its new machines, the West African Port of Tema is expanding its fleet of cranes for container handling. This delivery marks the eighth mobile harbour crane from Rostock to the port operator: Ghana Ports and Harbours Authority (GPHA).
“We have a long-standing partnership with Liebherr. We are impressed with both Liebherr products and their service. It is not only the individual consulting but also the fast delivery that has promoted an expansion and increase of our business,” says Ing. Stephen Kwamina Owiah, Port Logistics Manager GPHA.
The berths adjacent to the Liebherr factory in Rostock’s port are accessible to ships with a draught of up to 13 metres and are free from shipping obstacles such as locks and bridges. The factory’s direct connection to the Baltic Sea makes it possible to load the fully assembled cranes, in working order. As such, the two machines boarding the BBC-Russia are timeously ready for use after arrival at the port of destination.
“The Rostock international port offers us ideal conditions for shipping the often large-dimensioned equipment. We now load 60-65 percent of the cranes in fully assembled condition,” says Gregor Levold, General Manager – Shipping and Heavy Lift Handling at Liebherr-MCCtec Rostock GmbH.
An experienced team makes use of various loading options when shipping the cranes. An example is the roll on/roll off (RoRo) procedure on board special ships which enables the machines to travel independently from the quay onto the vessel. The loading onto the BBC-Russia was carried out in the lift on/lift off (LoLo) procedure. The LoLo procedure involves cargo being lifted up onto the ship using on-board cranes. However, road freight also offers advantages for many customers due to the immediate proximity of the Liebherr factory to the German motorway network.
GLOBALLY RESPECTED MANUFACTURER OF MOBILE HARBOUR CRANES It is not only the good infrastructural links that ensure the success of LiebherrMCCtec Rostock GmbH. One of the reasons Liebherr has enjoyed its prominent position in the mobile harbour cranes market for so many years is its commitment to high customer satisfaction. Through worldwide customer service Liebherr takes care of customer machines, even in times of crisis, to ensure that ports are able to provide supplies to their people. Despite the worldwide lockdown as a result of the Covid-19 pandemic, Liebherr mobile harbour cranes remained functional in ports across the world.
“More than 1,000 colleagues are close to our customers every day in our numerous service companies around the world. Together we are continuously developing our cranes,” says Andreas Muller, Sales Director for Mobile Harbour Cranes at Liebherr-MCCtec Rostock GmbH.
INNOVATIONS AS A CONSTANT COMPANION In addition to the worldwide customer service network, it is the continuous technical development of the cranes and assistance systems that gives Liebherr’s customers a decisive edge. In future, the mobile harbour crane series is set to run on the fossil-free HVO 100 diesel. The diesel reduces emissions by up to 90% and is derived from renewable raw materials. Additionally, a fundamentally revised hybrid drive for the mobile harbour crane will be introduced shortly. The revision will allow users to switch between two different modes: the boost mode which provides extra power for faster handling, and the eco mode which significantly reduces fuel consumption. The future-oriented hybrid
drive offers the user a high degree of flexibility. Depending on the individual situation, the innovative system can be individually tuned and thus delivers optimal performance in every situation.
ABOUT LIEBHERR-MCCTEC ROSTOCK GMBH Liebherr-MCCtec Rostock GmbH is one of the foremost European manufacturers of maritime material handling solutions. The product range comprises ship, mobile harbour, and offshore cranes. Reachstackers and components for container cranes are also included in the product portfolio.
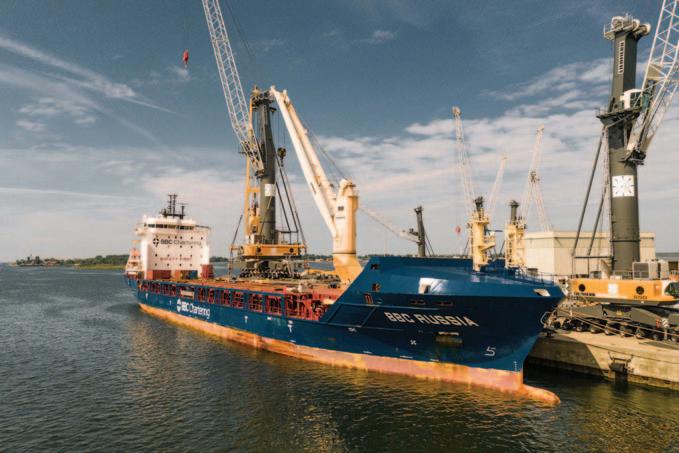
ABOUT THE LIEBHERR GROUP The Liebherr Group is a family-run technology company with a highly diversified product portfolio. The company is one of the largest construction equipment manufacturers in the world. It also provides high-quality and user-
Crane number 1,300 was shipped from Rostock, Germany to Ghana in June.
oriented products and services in a wide range of other areas. The Liebherr Group includes over 140 companies across all continents. In 2020, it employed around 48,000 staff and achieved combined revenues of over €10.3 billion. Liebherr was founded in Kirchdorf an der Iller in Southern Germany in 1949. Since then, the employees have been pursuing the goal of achieving continuous technological innovation, and bringing industry-leading solutions to its customers.
Everything remote: distance not an issue for Liebherr
Remote Service App in use for remote assembly of a mobile harbour crane. crane control via an encrypted mobile phone connection. So they could support the customer by troubleshooting the issue. Both remote tools allow issues with the machine to be identified more quickly, avoiding unnecessary journeys for maintenance — an especially important factor in times of corona and travel restrictions. Precise fault diagnosis allows the correct parts to be ordered so that the crawler crane, rope excavator, maritime crane, deep foundation machine or mobile crane can quickly be put back into operation.
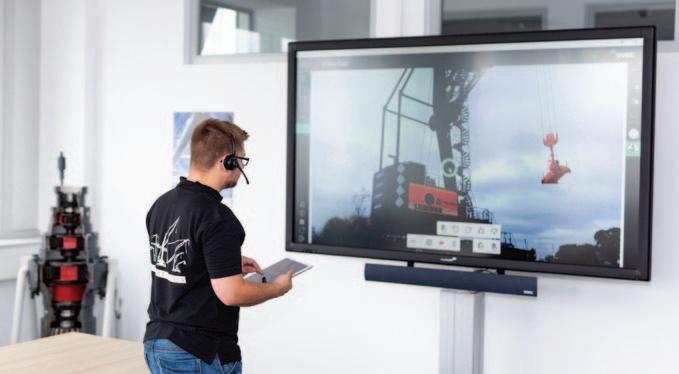
Remote products are the topic of the hour and due to the Covid-19 pandemic in greater demand than ever. All the better that the Liebherr Group has been working for a long time on such innovative solutions and is able to offer its customers appropriate products for various applications — for remote maintenance as well as for collaboration with local technicians.
The coronavirus pandemic has given the digital transformation extraordinary impetus over the last year, demonstrating that there most certainly are solutions for performing work without being present on site. Such remote applications have many benefits and are currently experiencing a veritable boom. Liebherr has been working for many years on various remote products, now allowing the company to make use of these and to further expand its innovative technologies. Besides the application examples listed below, Liebherr also offers different solutions covering all product lines for making daily work easier and more efficient.
REMOTE MAINTENANCE AT THE PUSH OF A BUTTON Liebherr’s Remote Service app is especially well suited as a diagnosis tool for repairs or for remote maintenance on cranes, excavators and construction machines. It can be used around the world in real time and can transmit visual information, allowing fast and efficient customer support when it is needed. Liebherr also offers remote diagnostics for its cranes of the latest generation. If a problem occurs, a service engineer would connect to the
SMART GLASSES FOR THE RIGHT PERSPECTIVE Smart glasses are a practical tool for providing fast assistance to customers in faraway places without having to send a technician around straight away. The glasses allow pictures to be simply shared and discussed. So this remote tool not only avoids the need for travel, but also saves substantial costs and makes customer service more efficient.
Liebherr also uses smart glasses for earthmoving machines and material handling technology. This enables digital remote support for service and maintenance cases: the customer wears the smart glasses and a live image is transmitted directly to a Liebherr service technician. They then carry out a fault diagnosis and, ideally, find a solution to the problem.
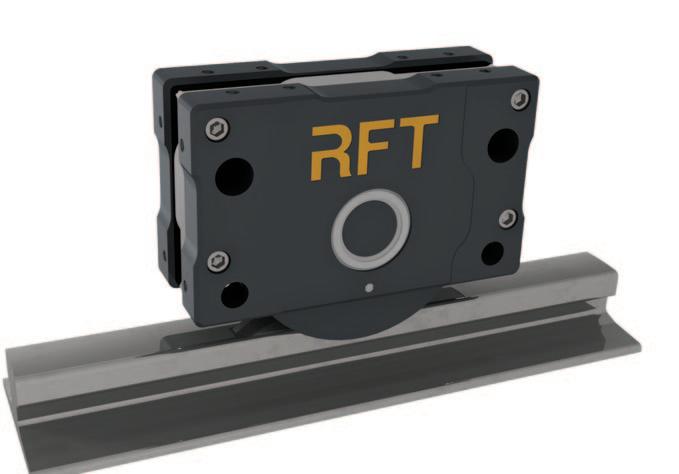
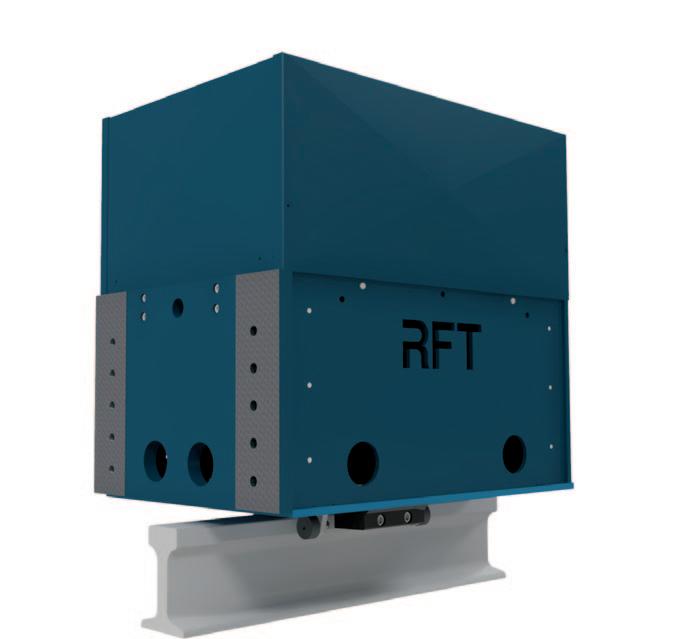
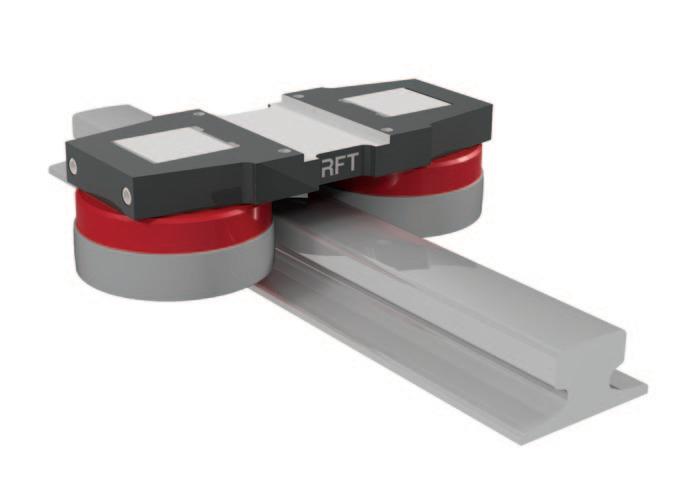
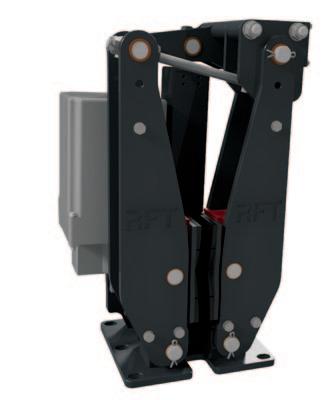
Römer Fördertechnik GmbH (RFT) based in Wetter/Ruhr, Germany, is a direct manufacturer of crane and industrial components such as industrial brakes, couplings, hydraulic end stop buffers, storm brakes/rail clamps, guide roller systems, wheels, wheel block systems, bottom hook blocks and sheaves. All RFT components find their application in the fields of port-, mining-, conveyor and materials handling technology. The products feature the latest technology, highest safety and quality level. RFT successfully co-operates with international crane manufacturers, operating companies and consultants. Hydraulic buffers, dampers, brakes, couplings, storm brakes, guide rollers, bottom hook blocks and many other products are designed, manufactured, assembled and tested in RFT’s own facilities in Germany. The products feature the highest safety and quality level in the market of materials handling and safety technology.
RFT is focused on improving standard components to avoid system failures and reduce follow-up and service costs. Current improvements are: v Storm brakes type VZFH-HVZ with lifting and lowering solution — no contact with the rail during crane travel, therefore no wear during crane travel.
These are especially suitable for fast moving systems and transverse travels. v Guide roller systems type SFRS-SV in strong design with integrated damping solution. Up to 490kN load rating per guide wheel. The integrated and patented damping solution protects the bearing against unwanted impacts. In addition to that, the reinforced guide roller system features larger guide wheels where a double bearing solution is integrated. v Disc brake type RSTN in new design with synchro lifting mechanism. v Wheel block systems type RRB with integrated bearing protection.
All RFT components are exclusively manufactured in Wetter, Germany.
Disc brake RSTN. RFT wheel block RRB.
Storm brake VZFH-HVZ in lowered position.
RFT guide roller system SFRS-SV.
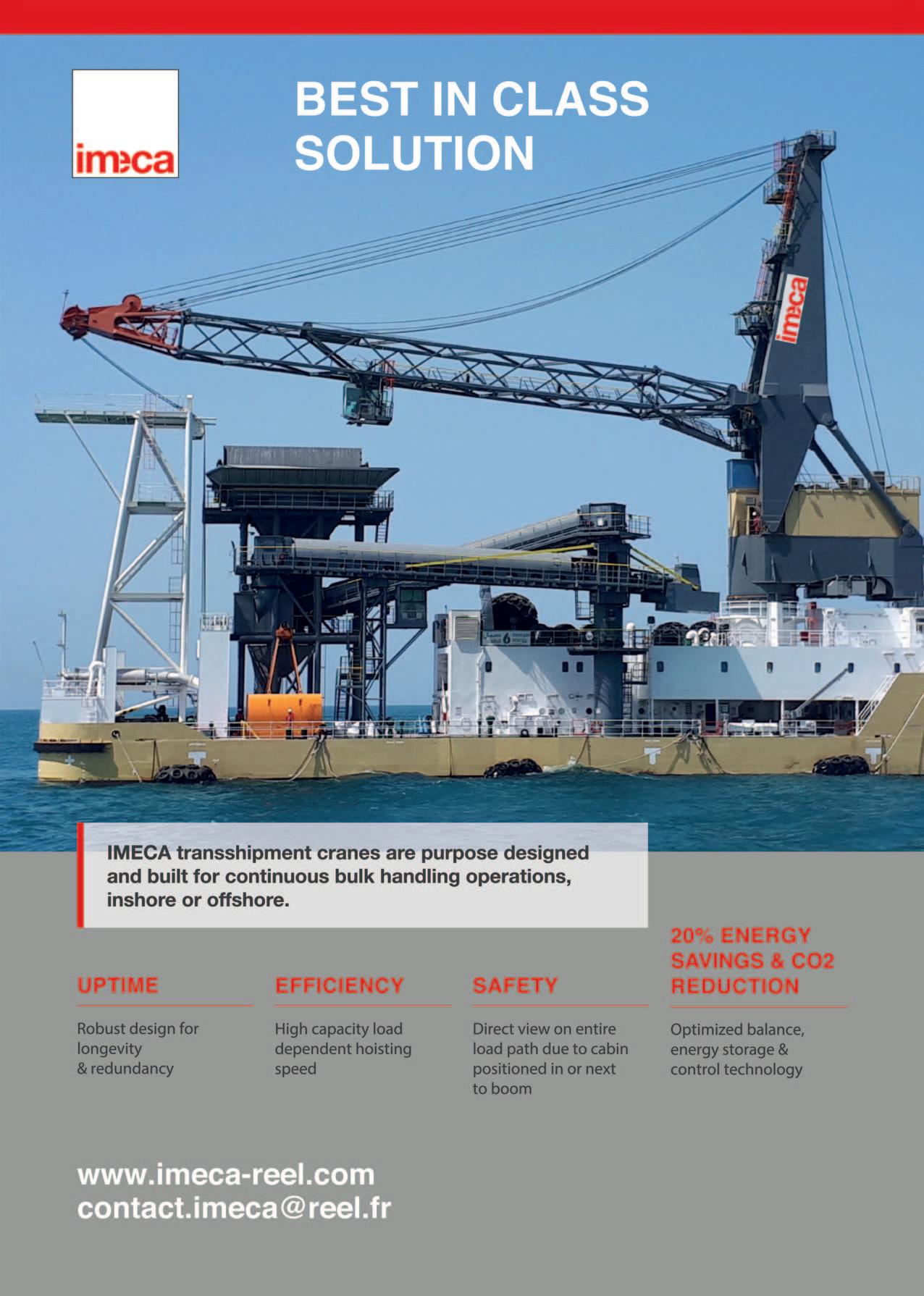


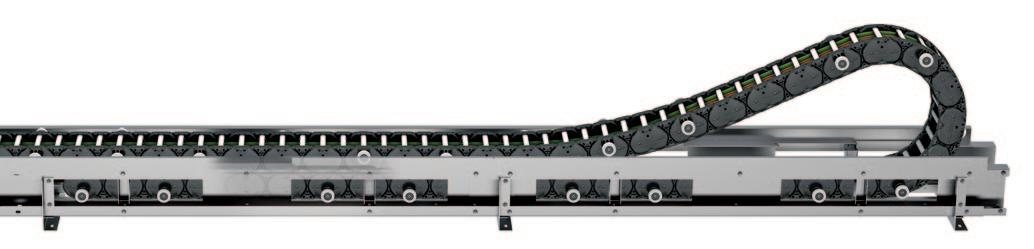
High velocities and acceleration, long travel lengths and — last but not least — extreme weather conditions: cable carriers that are deployed for port cranes must be able to meet the wide range of requirements this application demands. The robust and durable systems from TSUBAKI KABELSCHLEPP can do just that. In many ports around the world, they ensure reliable, trouble-free crane operations, and have therefore established themselves as a safe and modern alternative to conventional festoon systems.
Cable carriers for cranes is a key business segment for TSUBAKI
KABELSCHLEPP. The experts have been raising awareness in the industry that cable carrier systems on cranes are a viable option — also and especially for port cranes, which have previously been the domain of traditional festoon systems. Users are increasingly rethinking their approach here, and for good reason. First, a cable carrier can be used to route all types of media at the same time — cables, hoses, and fibre-optic lines. Another key benefit is the space-saving design: the cable carrier is installed directly under the main girder and has a system height of less than one metre. There are no loops of suspended cables that could get caught up in the crane’s steel structure. And, talking of loops: the drag cable also has to have an extra steel structure to house it, whose length needs to be about ten percent of the travel length. This isn’t needed in the case of cable carrier systems: the end of the crane girder is also the end of the cable carrier. This also means that much shorter cable lengths are needed for cable carriers.
SAVING TIME AND MONEY WITH CABLE CARRIER SYSTEMS A cable carrier is pushed and pulled by the crane trolley. The additional drive system required by many festoon systems is therefore not needed here. Controllers are also not needed to synchronize the crane trolley with the cable management system. This lets users save both time and money: cable carrier systems requires less maintenance and requires less often relubrication — and there are no rollers or bungee ropes to replace, either. If necessary, cables can simply be swapped out without any complicated threading-in. The new cable is then simply pulled into the carrier with the old cable. None of this requires the dismantling of threaded assemblies.
Last but not least, cable carriers also place less mechanical stress on the cables. Even if a crane isn’t moving, festoon cables are always in motion — caused by the trolley, the gantry movement and of course the wind. This represents a constant
Since commissioning in September 2015, the system has been running successfully at the Pupuk Kaltim port on the island of Borneo (all pictures: TSUBAKI KABELSCHLEPP).
The sturdy design of the TKHD cable carriers ensures that they offer a long service life even when used in dirty and harsh environmental conditions.
Roller-supported chains are an ideal solution for high additional loads and long travel lengths.