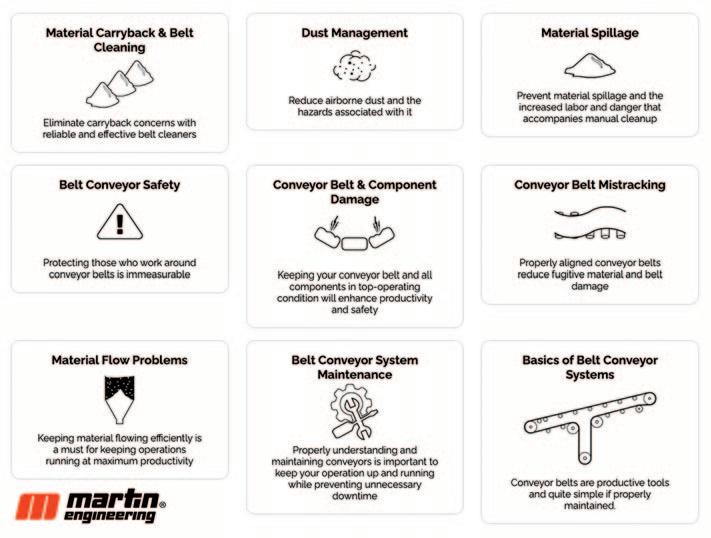
12 minute read
Kocks Ardelt Kranbau: engineering art from Eberswalde back to Brunsbüttel
subject from beginning to end with text information, topical webinars, videos and related articles.
“Our goal is comprehension and retention,” Heitzler pointed out. “Visitors might be pressed for time or may become distracted. While an experienced live instructor can see that and overcome it in a face-to-face training session, online learning is a different animal. So by providing visitors with options for learning and ways to break up the information rather than hours of reading or long videos, we’re able to better engage them, improving their experience and their learning.”
Once the Learning Center has been fully explored, users should have the foundation needed to operate belt conveyors safely and effectively. If managers choose, they can refer their employees to the Learning Center to gain professional development credits toward their certification to become qualified as maintenance technicians, operators, foremen, millwrights/fitters and so on.
The feedback from people who have already used the Learning Center has been excellent. Users find it informative, easy to
Topic categories are easy to find and understand, and lead to an entire collection of learning resources. use, engaging, and an overall enjoyable experience. Managers and supervisors say they like having a trustworthy and costeffective source for quick, unbiased information. Resource volumes are “Of course, nothing replaces hands-on available as free downloads to training and on-the-job experience, so provide in-depth information that’s why the training system is called (all photos: © Foundations,” Heitzler said. “We provide 2022 Martin the basic knowledge needed to work safely Engineering). and efficiently in a platform that they can easily access when they need it.” ABOUT MARTIN ENGINEERING Martin Engineering has been a global innovator in the bulk material handling industry for more than 75 years, developing new solutions to common problems and participating in industry organizations to improve safety and productivity. The company’s series of Foundations books is an internationally-recognized resource for safety, maintenance and operations training — with more than 22,000 print copies in circulation around the world. The 500+ page reference books are available in several languages and have been downloaded thousands of times as free PDFs from the Martin website. Martin Engineering products, sales, service and training are available from 17 factoryowned facilities worldwide, with wholly owned business units in Australia, Brazil, China, Colombia, France, Germany, India, Indonesia, Italy, Mexico, Peru, Russia, Spain, South Africa, Turkey, the USA and UK. The firm employs more than 1,000 people, approximately 400 of whom hold advanced degrees.
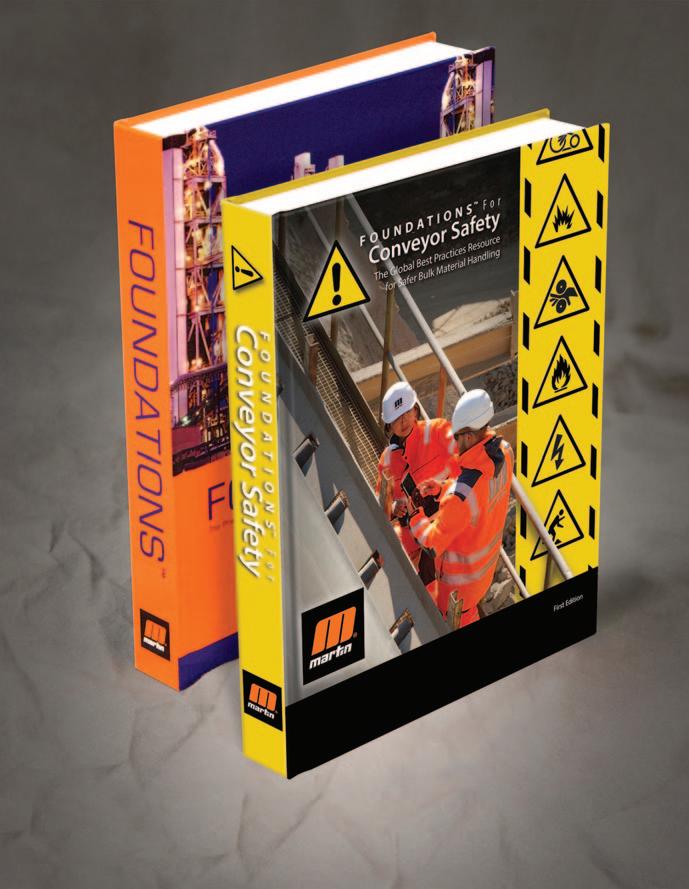
Two Alimak rack and pinion elevators were installed on new ship unloader cranes at the port of Kaohsiung in Taiwan.
The grab-type ship unloader gantry cranes will serve China Steel Corporation with bulk materials delivered from vessels. These types of cranes are often applied in bulk material discharging with high efficiency and wide usability.
The Alimak rack and pinion elevator gets the crane driver to the crane’s driver cabin at a height of 35 metres in less than a minute, improving the efficiency and productivity further. Safety is also improved as hazards, such as slipping on the stairs or objects falling from height, are greatly reduced.
The Alimak elevators provide reliable and efficient access to three different levels of the cranes for men, tools and repair parts facilitating frequent preventive maintenance and minimizing costly downtime resulting from breakdowns. By allowing operators to access the crane’s cabin more quickly, an elevator also substantially increases the crane’s overall productivity per shift.
50 YEARS’ EXPERIENCE IN THE PORT INDUSTRY Alimak has provided industrial elevators based on the rack and pinion drive technology to the port industry for more than 50 years. Alimak delivered its first shipyard crane elevator in 1971 and since then, has emerged as the world’s leading supplier of elevators to this industry.
In fact, the company has an installed base of over 23,000 rack and pinion elevator solutions for different industries worldwide, including close to 3,000 in ports. Alimak has developed extensive engineering knowledge on a wide variety of industrial applications. Industrial elevators from Alimak are designed to withstand the harsh environments and abrasive conditions in ports, providing reliable vertical access, anytime and anywhere it is needed, from intermodal container terminals and storage yards to shipyards, and dry docks.
IDEAL FOR PORT CRANE ACCESS The rack and pinion elevator has proven to be easy to install and maintain and compared to accessing cranes via stair towers, rack and pinion elevators significantly increase efficiency, productivity, and safety.
Rack and pinion elevators are ideal for accessing port cranes for crane operators and maintenance personnel. They effectively reduce the risk of falls from height, eliminate exertion from climbing, and provide the ability to quickly transport injured personnel from any height.
CRANE REFURBISHMENTS Rack and pinion elevators can easily be installed on any crane structure, and perfectly lends itself to retrofitting. Alimak has participated in a wide range of modernization projects. It offers a wide and versatile range of vertical access solutions also for temporary use whether for retrofitting, upgrades or larger refurbishment programs at the port.
RACK & PINION PIONEER In 1962 Alimak pioneered the rack and pinion drive system that, within a few years, established the company as a world specialist in this technology. The rack and pinion elevator proved to be simple, reliable and cost-effective compared to other revolutionized passenger and material transportation options on construction sites.
The rack and pinion concept has since been developed and refined, subsequently opening up new markets in the industrial
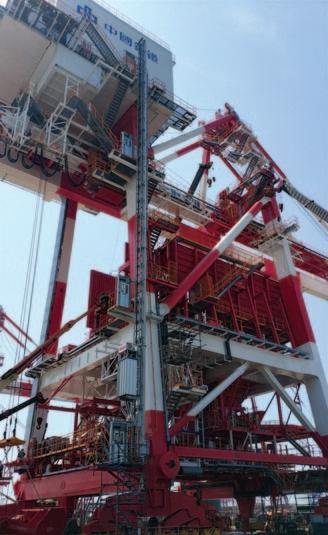
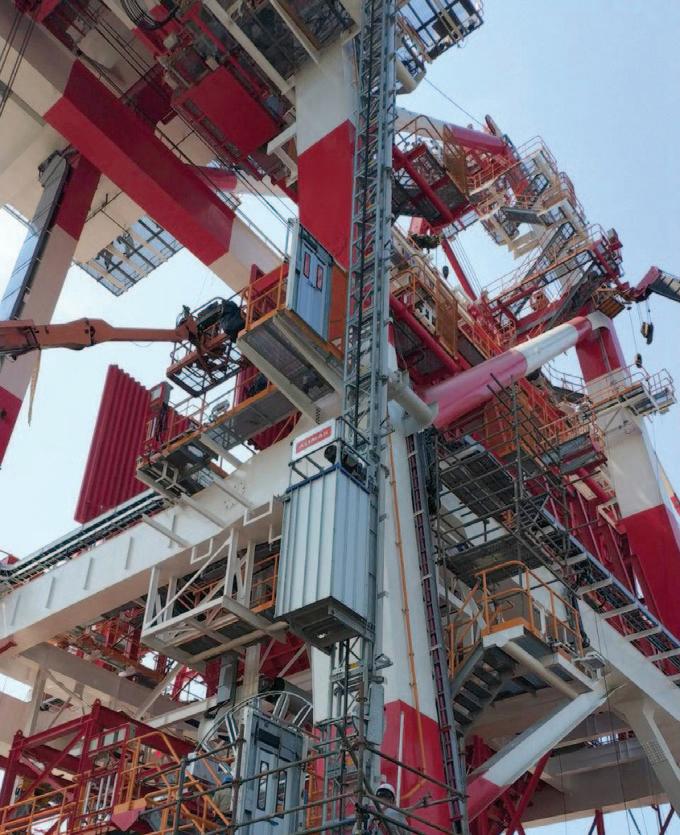
elevator sector. Today Alimak’s activities are concentrated on the design, manufacture and distribution of permanent industrial elevators, construction hoists, mast climbing work platforms and transport platforms, all based on the rack and pinion principle.
ABOUT ALIMAK Alimak is a global market pioneer in the design and manufacture of vertical access solutions for industrial and construction industries. The company provides high-quality rack and pinion and traction elevators, construction hoists and work platforms. Alimak has a well-established global sales, service and distribution platform across over 90 countries with a strong market presence. It has a large global installed base of over 23,000 units which provides unique knowhow of all industrial application areas. Alimak was founded in 1948 and employs over 1,200 people across the world. Alimak is part of Alimak Group which is headquartered in Stockholm, Sweden.

Kocks Ardelt Kranbau GmbH: engineering art from Eberswalde finds its way back to Brunsbüttel
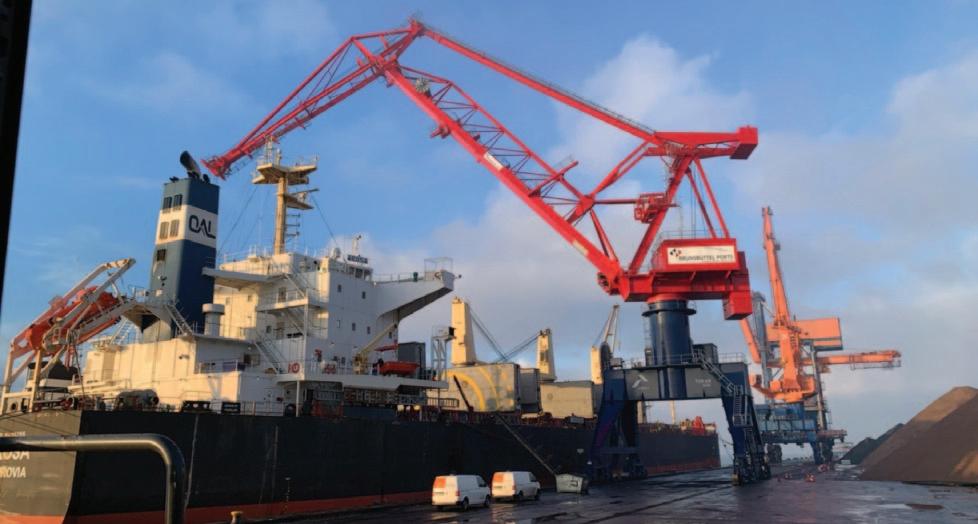
Brunsbüttel Ports GmbH, a loyal customer of Kocks Ardelt Kranbau for many years, has once again placed its trust in the proven German crane manufacturer based in Eberswalde/ Brandenburg. It has ordered a new Tukan-type crane with grab and hopper, measuring 35/50/120 t x 63/40/30m for the Elbehafen. This order was placed during the Covid-19 pandemic.
Kocks Ardelt Kranbau GmbH, the crane construction company from Eberswalde/ Brandenburg, provided the port with the equipment for cargo handling only a year after the contract was awarded. In close co-operation between the customer and the crane builder, the crane’s parts were delivered by sea, and on-site assembly went smoothly.
This new crane handles both bulk and general cargo and makes the port even more efficient and flexible, which further increases the performance of this port which now has seven cranes, five of which are manufactured by the Eberswalde company.
This new Tukan crane is characterized by high energy efficiency and low noise emissions, making it particularly environmentally friendly. The lifting capacity in the Elbehafen is doubled by the new crane from currently 120 tonnes to 240 tonnes in tandem lift. The high lifting capacity and the crane’s long reach of maximum 63 metres will enable even heavier goods to be handled in future, including from shipto-ship in transshipment operations.
Brunsbüttel Ports GmbH has found a reliable partner in Kocks Ardelt Kranbau GmbH, because the name Kocks Ardelt stands for customer advice, design and manufacture, commissioning, assembly, the execution of tests and services from a single source, as well as modernizations on its own and thirdparty crane systems and, in particular, the supply of customized customer solutions in addition to the existing standard crane range.
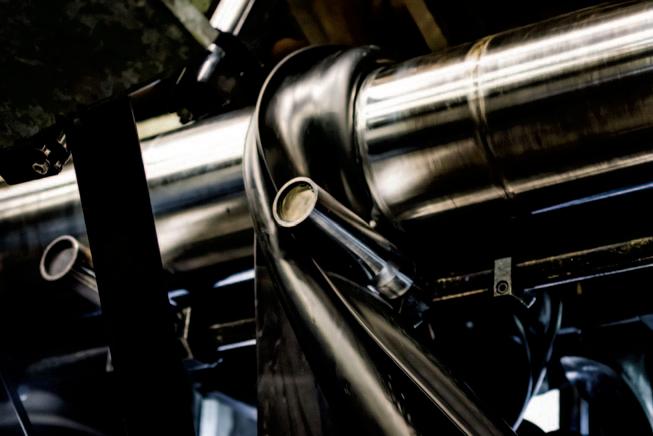
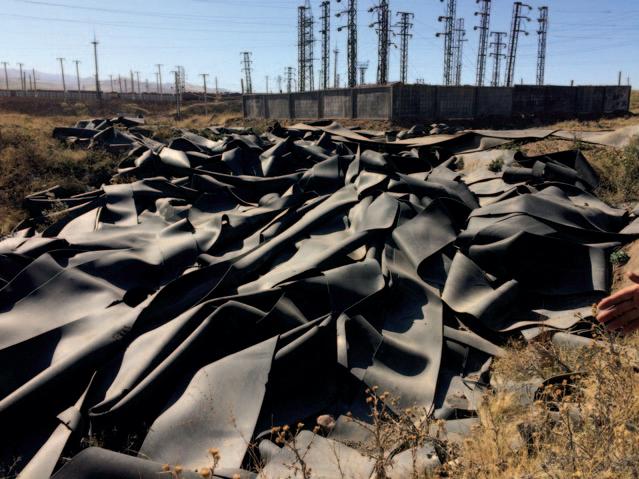
How the Russia–Ukraine conflict is affecting the European conveyor belt market
CONVEYING ADVICE
Just when we thought that we were beginning to see the light at the end of the tunnel as far as the Covid 19 crisis was concerned, the world around us has again changed dramatically because of the Russian–Ukrainian conflict. The post-pandemic surge in demand for virtually all kinds of products created severe inflationary pressures. As Covid restrictions lessened, raw material prices began to spiral rapidly. At the same time, huge supply chain problems were being experienced — caused by shortages in shipping containers and the sheer capacity available to move the huge volumes required. Before those pressures had a chance to subside, an arguably even bigger second wave of pressures as a direct result of the terrible events in Ukraine has made matters a whole lot worse. As with almost every type of manufacturing industry, European conveyor belt manufacturers are being hit and, as a consequence, so are the multitude of conveyor belt users.
Because of its adaptability, most of the rubber used to make conveyor belts is synthetic. Dozens of different chemical components and substances are used to create the numerous different synthetic rubber compounds needed to cope with the different demands that may be placed upon them. These raw materials can constitute up to 75% of the total cost of producing a conveyor belt. The conflict has caused shortages in the supply of many of these raw materials and, as a logical consequence, additional price increases on top of what were already record high levels. Alongside these issues are the huge increases in the price of oil, which is the basic ingredient of many of the raw materials used to manufacture conveyor belts plus the increased cost of gas and electricity, which in some cases is five times higher than last year. Added to that, the cost of both road and sea transport has seen further massive increases.
In terms of volume, low-grade conveyor belts imported into Europe from South East Asia were already dominating the market when these problems began. Non-European manufacturers have a significant added advantage in that they are not subject to EU regulation concerning the use of hazardous chemicals or the use of Persistent Organic Pollutants (POPs). This means that they are free to use unregulated raw materials that cost much less on the global market, even though those same materials may be entirely prohibited or at least have strict usage limitations within the European community. This helps them to keep their prices low at the expense of quality, safety and the impact on the environment.
As belt manufacturers have been forced to increase their prices in order to survive the storm, it has created a natural but extremely risky temptation for end-users to seek lower-priced imported belt as an alternative. There are numerous well-proven technical reasons why imported belt can be priced lower than European made belts of apparently the same specification. All of these reasons relate to such huge differences in reliability, performance and operational longevity that good quality European-made belts can quite easily last as much as three or four times longer than their imported counterparts. The message is clear; price is what you pay but cost is what you spend.
Raw materials can constitute up to 75% of the cost of producing a conveyor belt.
Price is what you pay but cost is what you spend. Bob Nelson
REMA TIP TOP AG has acquired HEMPEL Industrievulkanisation GmbH & Co. KG, a major conveyor technology company based in Neu-Ulm, thus further expanding its service network in southern Germany.
For 45 years, Hempel Industrie vulkan isation has been a force to be reckoned with in the field of conveyor technology in southern Germany, focusing on the installation, repair and splicing of conveyor belts made of rubber and PVC. The company is also a service partner for the maintenance and renewal of conveyor systems, coating and repair of conveyor belt drums and idlers, and wear protection technology.
“Both companies are linked by a longstanding partnership, which will be taken to the next level with the acquisition,” says company owner Roy Hempel, who started his career at REMA TIP TOP. “Service and solution orientation will continue to be the unrestricted focus of our thinking and business in the future,” emphasizes Bodo Wein of REMA TIP TOP, who will support Roy Hempel on the management board.
The REMA TIP TOP Group has acquired HEMPEL Industrievulkanisation GmbH & Co. KG as of 1 April 2022, and is thus further expanding its service network in the field of materials processing technology in southern Germany.
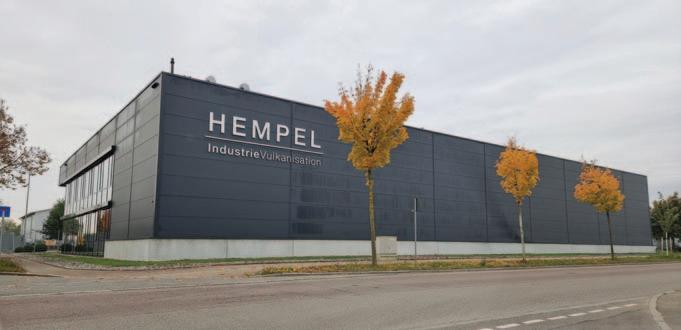
ABOUT REMA TIP TOP
REMA TIP TOP is a globally operating system provider of services and products in the field of conveying and treatment technology as well as tyre repair. The company has a global service network and offers a wide range of rubber products, linings and coatings for both the industrial and automotive sectors.
Over almost 100 years, the company has built up unique expertise in materials development and industrial services and is active in the belting, material processing, surface protection and automotive sectors. At the end of the 2020 financial year, REMA TIP TOP generated sales of about €1 billion.
Worldwide the company employs 8,000 employees and has more than 180 subsidiaries and associated companies — including well-known brands such as Dunlop Belting Products South Africa and Asplit.
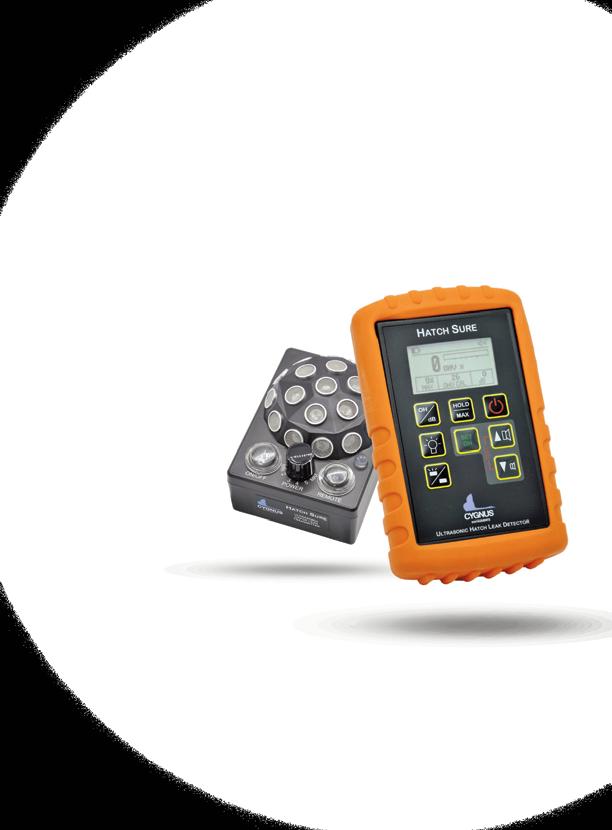

WEATHERTIGHTNESS MATTERS
CYGNUS HATCH SURE ULTRASONIC HATCH COVER TESTER
• Reliable Solution For Hatch Cover Weathertightness Tests • Accepted By P&I Clubs And ABS Type Approved • Powerful And Robust Transmitter